一种预埋件自动安装装置的制作方法



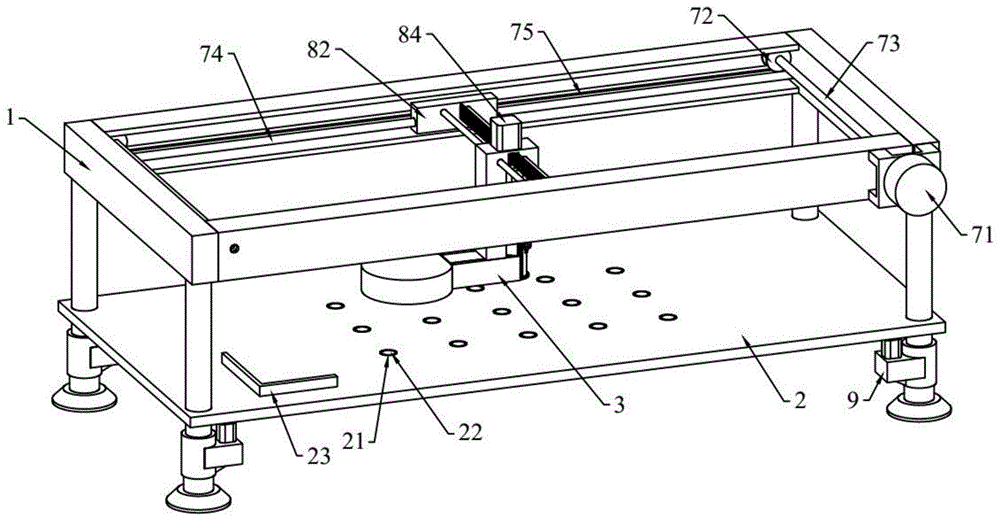
本发明涉及自动化装置技术领域,尤其涉及一种预埋件自动安装装置。
背景技术:
预埋件是家具板材中常用到的部件,为三合一连接件中的一个,其主要是预先安装在板材的预留孔内,板材安装时通过预埋件上的螺孔与螺丝相连接,从而实现板材间的快速、便利安装。
传统方式的预埋件安装主要是通过手工安装,工人通过锤子等将预埋件敲入预留孔内以实现安装,这种方式费时费力,效率差、效果差,准确性不高,且对工人不友好,已经不推荐使用。
中国专利cn207840615u公开了一种膨胀预埋件自动安装设备,其采用对料箱中预埋件进行逐个分离,并推送至喷嘴部分,利用外部高压气体进行推送预埋件至木板预留孔,以实现预埋件的安装,这种方式大大提高了预埋件安装的效率。但是,由于预埋件整体呈圆柱状,且预埋件为从料箱中依靠重力向下掉落,虽然有小齿轮波动,但是依然会存在因预埋件翻转等造成的安装前预埋件偏斜或未与预留孔对中的问题,从而影响预埋效果,影响产品质量。
技术实现要素:
针对以上不足,本发明提供一种预埋件自动安装装置,能够通过定位圆筒来实现预埋件与预留孔之间的对中以实现预埋件的高效、精准定位,以提高预埋效果。
为达到上述目的,本发明采用如下技术方案:
一种预埋件自动安装装置,包括有机架以及安装在所述机架上的支撑固定板、x向驱动机构和y向驱动机构,所述y向驱动机构上设有推料定位机构,所述推料定位机构包括有固定梁、固定安装在所述固定梁底端的进料通道,所述进料通道的一端口连通用以放置预埋件的料盘,另一端口处设有上下敞口的定位圆筒,所述定位圆筒包括有各为半圆弧形的第一定位切割半弧板和第二定位切割半弧板,所述第一定位切割半弧板固定设置于远离进料通道的一侧,所述第二定位切割半弧板由第一气缸驱动上下移动,所述第一定位切割半弧板与进料通道的端口正对的侧壁上开设有通槽,所述通槽的底部设有刃口,所述第二定位切割半弧板与进料通道的端口正对的侧壁的底部向上开设有底槽,所述底槽的顶部设有刃口;所述定位圆筒的上方设置有第二气缸以及由所述第二气缸驱动上下移动的顶压套筒;所述进料通道上设有用以驱动所述预埋件往定位圆筒内移动的预埋件驱动机构。
进一步地,所述预埋件驱动机构包括有第三气缸、连接板、第四气缸和推爪,所述进料通道的侧壁沿进料通道延伸方向开设有贯通进料通道内部的爪槽,所述第三气缸固定安装在进料通道的外侧壁上,所述第四气缸安装在第三气缸上并由第三气缸驱动沿爪槽长度方向运动,所述连接板安装在所述第四气缸上并由第四气缸驱动往靠近或远离进料通道的方向移动,所述推爪安装在连接板上并与所述爪槽相对设置。
进一步地,所述定位圆筒的下方设有导向软环,所述导向软环的内侧沿周向均匀分布有多个齿片状弹性软齿。
进一步地,所述定位圆筒内还设有激光定位传感器,所述激光定位传感器位于所述定位圆筒的轴心上,所述激光定位传感器通过支杆与所述第一定位切割半弧板的顶部固定连接,所述顶压套筒的侧壁上开设有沿轴向延伸的延伸槽,所述支杆穿过所述延伸槽。
进一步地,所述x向驱动机构包括有安装在所述机架上的第一驱动电机、同步带轮、以及位于机架两侧的第一导轨,所述同步带轮为多个,位于所述机架同侧的同步带轮之间套设有同步带,所述y向驱动机构安装在所述第一导轨上并与同步带固定连接,位于所述机架端部的相对设置的两个同步带轮之间连接有转轴,所述第一驱动电机与所述转轴相连接以带动所述转轴转动。
进一步地,所述y向驱动机构包括有安装块、第二驱动电机、齿轮、齿条和第二导轨,所述安装块为两块,分别滑动安装在机架两侧的第一导轨上并与所述同步带固定连接,所述齿条和第二导轨设置在两块安装块之间,所述固定梁的顶部滑动安装在所述第二导轨上,所述第二驱动电机安装在固定梁上,所述齿轮安装在第二驱动电机的输出轴上并与所述齿条向啮合。
进一步地,所述支撑固定板通过顶升气缸安装在所述机架上。
进一步地,所述支撑固定板上开设有多个真空吸盘孔,所述真空吸盘孔内设置有吸盘,所述吸盘通过管路与真空发生器相连通。
进一步地,所述支撑固定板上设有l型的原点定位板。
进一步地,所述第一定位切割半弧板和第二定位切割半弧板其中一个在相向的侧边上开设有轴向设置的滑槽,另一个相应设置有位于所述滑槽内的滑轨。
与现有技术相比,本发明的有益效果是:本发明提供一种预埋件自动安装装置,通过设置推料定位机构来实现预埋件的安装时的精确对中,保证预埋件在安装前不偏斜,以最终保证预埋件安装的高效、高质,提高预埋件安装的效果,保证板材产品质量。
附图说明
为了更清楚地说明本发明实施例的技术方案,以下将对实施例描述中所需要使用的附图作简单地介绍。
图1为本发明优选实施例的结构示意图;
图2为y向驱动机构和推料定位机构的结构示意图;
图3为推料定位机构的局部剖视图;
图4为推料定位机构的局部示意图;
图5为推料定位机构的局部剖视图;
图6为推料定位机构的部分部件的爆炸示意图;
图7为第二定位切割半弧板和第一气缸的局部剖视图;
图8为顶压套筒的结构示意图。
具体实施方式
下面将结合本发明实施例中的附图,对本发明实施例中的技术方案进行清楚、完整地描述。显然,所描述的实施例仅仅是本发明一部分实施例,而不是全部的实施例。基于本发明中的实施例,本领域普通技术人员在没有作出创造性劳动前提下所获得的所有其他实施例,都属于本发明保护的范围。
实施例
请参照图1,本发明优选的实施例提供一种预埋件自动安装装置,包括有机架1以及安装在机架1上的支撑固定板2、x向驱动机构、y向驱动机构和推料定位机构3。机架1为框架结构,包括有四个支脚,支撑固定板2安装在机架1的四个支脚上。x向驱动机构安装在机架1上以实现一种x向的运动,y向驱动机构安装在x向驱动机构上以实现y向的运动,推料定位机构3安装在y向驱动机构上,由y向驱动机构驱动y向运动,也即推料定位机构3能够在x向驱动机构和y向驱动机构的驱动作用下实现x向和y向的运动,以实现推料定位机构3位于板材的预留孔的正上方。
请参照图1至图8,推料定位机构3包括有固定梁31、固定安装在固定梁31底端的进料通道32,进料通道32为水平设置,进料通道32的一端口连通用以放置预埋件10的料盘33,另一端口处设有上下敞口的定位圆筒。本优选的实施例中,料盘33为整体为圆盘状,内部中空,具有开口与料盘进料通道32的端口连通。本优选的实施例中,预埋件10优选采用两个相邻的预埋件10之间互相通过连接条101相连接的形式,相邻的两个预埋件10之间采用两根横向设置的、互相平行的连接条101来连接,连接条101分别连接在预埋件10的外周上,多个预埋件10竖立设置,卷成盘状结构并放置在圆盘状的料盘33内,部分预埋件10位于进料通道32,并在安装时由预埋件驱动机构4驱动逐一进入定位圆筒内。
定位圆筒包括有各为半圆弧形的第一定位切割半弧板34和第二定位切割半弧板35,第一定位切割半弧板34和第二定位切割半弧板35组成的定位圆筒的内径等于或稍大于预埋件10的最大处的外径,以当预埋件10进入定位圆筒后定位圆筒能够对预埋件10实现一个基本的定位。第一定位切割半弧板34固定设置于远离进料通道32的一侧,为了实现第一定位切割半弧板34的稳固,在本优选的实施例中,进料通道32的端部设置有一具有贯穿顶面和底面的通孔的安装板117,安装板117的通孔正对定位圆筒的底部并大于预埋件10的最大处的外径,第一定位切割半弧板34的底部固定安装在安装板117上,第一定位切割半弧板34的顶部固定安装有固定块118,固定块118通过连接杆116与固定梁31的顶部固定连接。第二定位切割半弧板35由第一气缸36驱动上下移动,第一气缸36固定安装在安装板117,其活塞杆与第二定位切割半弧板35的顶部固定连接。第一定位切割半弧板34与进料通道32的端口正对的侧壁上开设有通槽37,通槽37的底部设有刃口38,刃口38为外侧低内侧高的形式,以尽可能地往靠近预埋件10的侧面的位置切割连接条101,预埋件10朝向第一定位切割半弧板34的外周上的连接条101进入通槽37;第二定位切割半弧板35与进料通道32的端口正对的侧壁的底部向上开设有底槽39,刃口38为外侧低内侧高的形式,以尽可能地往靠近预埋件10的侧面的位置切割连接条101,底槽39的顶部设有刃口38,底槽39由第二定位切割半弧板35的底部向上设置,为下大上小的形式,以使得当第二定位切割半弧板35向下时能够让两个预埋件10之间的连接条101顺利进入底槽39内,且底槽39具有一定的深度,以使得第二定位切割半弧板35的底部部分低于预埋件10的顶部时,第二定位切割半弧板35上的刃口38才与连接条101相接触。第一定位切割半弧板34和在于第二定位切割半弧板35相向的侧边上开设有轴向设置的滑槽114,第二定位切割半弧板35相应设置有位于滑槽114内的滑轨115,通过设置滑槽114和滑轨115,保证第二定位切割半弧板35的平稳、平滑移动并保持定位圆筒的圆度。定位圆筒的上方设置有第二气缸310以及由第二气缸310驱动上下移动的顶压套筒311,第二气缸310固定安装在固定块118上,其活塞杆向下设置,顶压套筒311的顶部与第二气缸310的活塞杆的底部固定连接,顶压套筒311与定位圆筒同轴设置,在第二气缸310的作用下顶压套筒311能够实现上下运动。
进料通道32上设有用以驱动预埋件往定位圆筒内移动的预埋件驱动机构4,在优选的实施例中,预埋件驱动机构4包括有第三气缸41、连接板42、第四气缸43和推爪44,进料通道32的侧壁沿进料通道32延伸方向开设有贯通进料通道32内部的爪槽312,爪槽312为两个,并排设置在进料通道32的侧壁的上部和下部,第三气缸41固定安装在进料通道32的外侧壁上,第四气缸43安装在第三气缸41的活塞杆的端部上并由第三气缸41驱动沿爪槽312长度方向运动,第四气缸43为无杆气缸用以节省空间,连接板42安装在第四气缸43上并由第四气缸43驱动往靠近或远离进料通道32的方向移动,连接板42竖立设置,推爪44安装在连接板42上并与爪槽312相对设置,推爪44为杆状结构,其为两个,分别安装在连接板42的两个端部上。实施时,在第四气缸43的驱动下,连接板42做靠近或远离进料通道32的方向移动,当连接板42做靠近进料通道32的方向移动时,两个推爪44可以分别插入两个爪槽312内,并可在第三气缸41的带动下,随着第四气缸43一起沿着爪槽312延伸方向的方向(也为进料通道32的通道方向)移动;当连接板42做远离进料通道32的方向移动时,推爪44随之一同远离并离开爪槽312。
实施时,开设有预留孔的板材放置在支撑固定板2上,x向驱动机构和y向驱动机构带动推料定位机构3移位以对准待安装预埋件10的预留孔,此时定位圆筒与预留孔相对,也即定位圆筒位于预留孔的正上方;预埋件10放置在料盘33内,第二定位切割半弧板35处于升起状态或者通过第一气缸36驱动使第二定位切割半弧板35升起,以使得第二定位切割半弧板35不挡住进料通道32靠近定位圆筒处的端口;第四气缸43运转带动连接板42及其上的推爪44插入爪槽312,并插在两个预埋件10之间,第三气缸41运转带动第四气缸43往靠近定位圆筒的方向移动,此时连接板42及其上的推爪44一同移动,推爪44推动预埋件10往定位圆筒的方向移动,并使得一个预埋件10进入定位圆筒内并顶在第一定位切割半弧板34的内侧壁上,此时该预埋件10与板材的预留孔对中;进入定位圆筒的预埋件10在靠近第一定位切割半弧板34的侧面上的连接条101进入第一定位切割半弧板34上的通槽37内,此时第一定位切割半弧板34及其上的通槽37对预埋件10有一个定位和限位的作用;然后第一气缸36驱动第二定位切割半弧板35往下移动,第二定位切割半弧板35的底槽39与预埋件10远离第一定位切割半弧板34的侧面上的连接条101相对准,随着第二定位切割半弧板35不断往下移动,第二定位切割半弧板35套设在预埋件10的顶部,底槽39套住该侧的连接条101,然后不断往下的刃口38向下切割连接条101使得两个预埋件10之间的连接条101被切断,由于底槽39具有一定的深度,以使得第二定位切割半弧板35的底部部分低于预埋件10的顶部时,第二定位切割半弧板35上的刃口38才与连接条101相接触,使得在切割连接条101,第二定位切割半弧板35以及另一侧的第一定位切割半弧板34一起对预埋件10有一个定位、限位的作用,从而不会偏斜而影响对中;第二定位切割半弧板35完全落下并与第一定位切割半弧板34一同形成一个圆筒状的结构,此时第二气缸310驱动顶压套筒311往下,往下的顶压套筒311顶住预埋件10的顶部并带动预埋件10不断往下直至预埋件10被完全顶入板材的预留孔,此时完成预埋件10的自动安装,整个过程中,预埋件10在第一定位切割半弧板34和第二定位切割半弧板35的作用下,不会偏斜,与预留孔对中准确,从而使得安装效果良好,也即实现预埋件10的高效、精准定位,并提高预埋效果。且在预埋件10被顶入预留孔的过程中,第一定位切割半弧板34上的通槽37底部的刃口38,会与该侧的预埋件10的连接条101相作用,以切掉部分连接条10,从而在预埋件10被顶入预留孔时,其两侧的连接条101被切短,不会影响预埋件10的安装以及破坏板材的预留孔。当一个预埋件10安装完成后,第二气缸310驱动顶压套筒311往上复位,第一气缸36驱动第二定位切割半弧板35往上复位,x向驱动机构和y向驱动机构带动推料定位机构3移位以使得定位圆筒位于下一个安装预埋件10的预留孔的正上方,第四气缸43运转带动连接板42及其上的推爪44离开爪槽312,第三气缸41运转带动第四气缸43往远离定位圆筒的方向移动,并使得爪槽312正对两个预埋件10之间,第四气缸43运转带动连接板42及其上的推爪44插入爪槽312,并插在两个预埋件10之间,第三气缸41运转带动第四气缸43往靠近定位圆筒的方向移动,此时连接板42及其上的推爪44一同移动,推爪44推动预埋件10往定位圆筒的方向移动,并使得一个预埋件10进入定位圆筒内并顶在第一定位切割半弧板34的内侧壁上,然后再参照上面的方式通过驱动第二定位切割半弧板35、顶压套筒311等,可实现又一个预埋件10的安装。基于此,本发明可以实现连续作业,安装效率高,效果好。值得注意的是,待安装预埋件10的板材的厚度是已知的,因此,可事先调整支撑固定板2的高度或者推料定位机构3的高度,以使得在进行预埋件10的安装时,预埋件10的顶部高度与推料定位机构3的底部高度基本一致或者推料定位机构3的底部高度稍高于板材的顶部高度,以便于预埋件10被顶压时能够直接进入板材的预留孔,从而保证安装效果。
在一些优选的实施例中,定位圆筒的下方设有导向软环5,导向软环5的内侧沿周向均匀分布有多个齿片状弹性软齿51。本优选的实施例中,导向软环5设置在安装板117上,与定位圆筒同轴设置,在第二定位切割半弧板35向下并切割预埋件10的连接条101时,预埋件10受力稍微偏斜,预埋件10的底部与导向软环5的齿片状的弹性软齿51相接触并挤压弹性软齿51,当第二定位切割半弧板35向下完成后,由于弹性软齿51具有弹性并可恢复,且均匀分布在导向软环5的内侧周向上,因此恢复的弹性软齿51能够驱动预埋件10的底部摆正并与导向软环5对中,也即与定位圆筒,也即与预留孔对中,从而助于对中安装。
在优选的实施例中,定位圆筒内还设有激光定位传感器6,激光定位传感器6位于定位圆筒的轴心上,激光定位传感器6通过支杆61与第一定位切割半弧板34的顶部固定连接,顶压套筒311的侧壁上开设有沿轴向延伸的延伸槽313,支杆61穿过延伸槽313并位于顶压套筒311内,设置延伸槽313使得在顶压套筒311往下或往上移动时,不会与支杆61相接触,不干涉支杆61和激光定位传感器6,通过设置激光定位传感器6,激光定位传感器6工作时依靠不同的反光率来检测是否与预留孔相对,以实现辅助找孔、对中。
在优选的实施例中,请参照图1,x向驱动机构包括有安装在机架1上的第一驱动电机71、同步带轮72、以及位于机架1两侧的第一导轨74,同步带轮72为四个,分别位于机架1的四角上,位于机架1同侧的同步带轮72之间套设有同步带75,位于机架1端部的相对设置的两个同步带轮72之间连接有转轴73,第一驱动电机71与转轴73相连接以带动转轴73转动。实施时,第一驱动电机71带动转轴73转动从而带动其上的同步带轮72转动,同步带75随之传动。通过第一驱动电机71不同方向转动从而可以实现同步带75的两个方向传动,也即实现x向传动。
请参照图1和图2,y向驱动机构包括有安装块82、第二驱动电机84、齿轮85、齿条81和第二导轨83,安装块82为两块,分别滑动安装在机架1两侧的第一导轨74上并与同步带75固定连接,齿条81和第二导轨83设置在两块安装块82之间,固定梁31的顶部滑动安装在第二导轨83上,第二驱动电机84安装在固定梁31上,齿轮85安装在第二驱动电机84的输出轴上并与齿条81向啮合。在第一导轨74以及同步带75的作用下,同步带移动时,可带动安装块82随之一同移动,也即实现安装块82的x向移动,即实现y向驱动机构的x向移动。第二驱动电机84转动带动齿轮85转动,在齿条81和第二导轨83的作用下,第二驱动电机84和固定梁31一同移动,这种移动与x向垂直,且均为水平移动,称为y向移动,通过第二驱动电机84的不同方向转动,可实现固定梁31的两个方向移动,也即实现y向传动。
通过上述x向驱动机构和y向驱动机构,可带动推料定位机构3的x向和y向移动,从而可以实现将推料定位机构3移动到待安装预埋件10的板材预留孔上方,以实现预埋件10的安装。
在优选的实施例中,请参照图1,支撑固定板2通过顶升气缸9安装在机架1上,顶升气缸9为四个,分别安装在机架1的四脚上,通过设置顶升气缸9,能够实现支撑固定板2的整体上下移动,以及实现整体移动板材升降,以调节板材与推料定位机构3的距离,便于适用于不同的厚度的板材,且相对采用其他的z轴运动方式要方便控制,精度要求也不高。
在优选的实施例中,支撑固定板2上开设有多个真空吸盘孔21,真空吸盘孔21内设置有吸盘22,吸盘22通过管路与真空发生器(图中未示出)相连通。通过设置吸盘22,在真空发生器的帮助下,真空发生器负压时吸盘22吸气,从而可以吸附住支撑固定板2上的板材,保证板材不会意外移动。
支撑固定板2上设有l型的原点定位板23,方形的板材一角顶在l型的原点定位板23的内侧上时,实现原点定位,整个板材实现一个定位,从而有助于实现板材上预留孔的位置定位,有助于安装时预留孔的位置查询以及推料定位机构3的对位、找正。
以上所述,仅为本发明的具体实施方式,但本发明的保护范围并不局限于此,任何熟悉本技术领域的技术人员在本发明揭露的技术范围内,可轻易想到的变化或替换,都应涵盖在本发明的保护范围之内。因此,本发明的保护范围应以所述权利要求的保护范围为准。
起点商标作为专业知识产权交易平台,可以帮助大家解决很多问题,如果大家想要了解更多知产交易信息请点击 【在线咨询】或添加微信 【19522093243】与客服一对一沟通,为大家解决相关问题。
此文章来源于网络,如有侵权,请联系删除


