一种快速定位的辊环锥套液压拆卸工具的制作方法



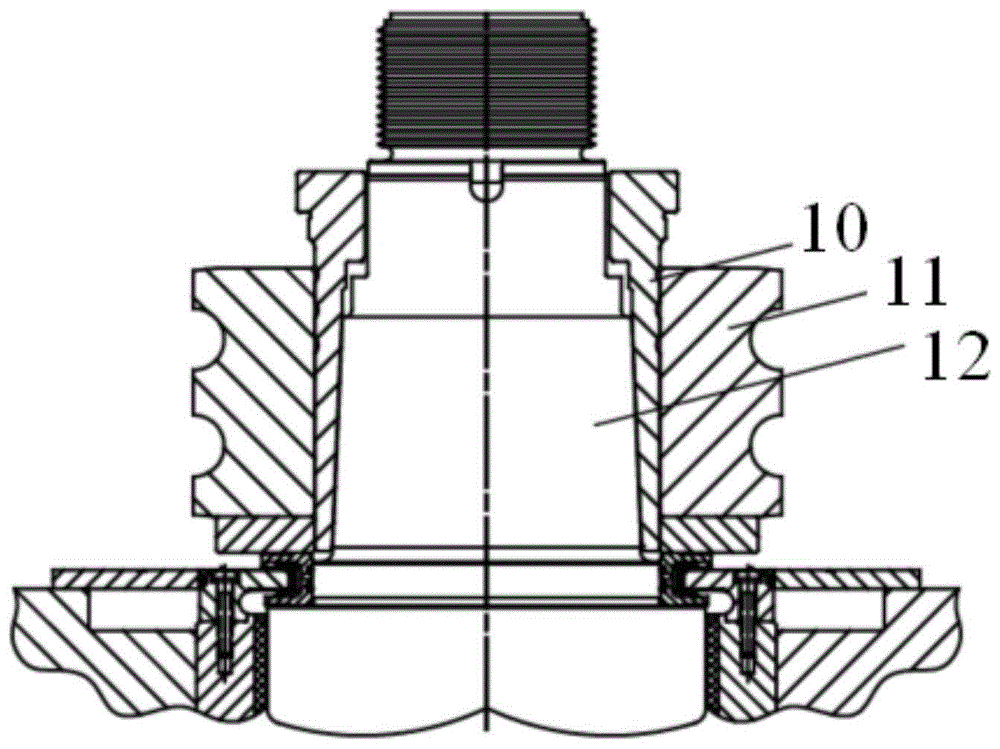
本实用新型涉及一种快速定位的辊环锥套液压拆卸工具,用于高速线材预精轧机组10寸、9寸辊环锥套,精轧机组8寸、6寸辊环锥套和夹送辊机组5寸辊环锥套的液压拉拔拆卸,属于高线材轧机液压换辊工具领域。
背景技术:
高速线材轧制生产线轧制区域的预精轧机组、精轧机组和吐丝机前端的夹送辊机组中,在线材轧制方向上布置有多组辊环,其作用是逐步轧制线材直至其达到工艺所需的线径,在轧制过程中,需要定期对以上机组中的轧制辊环进行周期性更换,以保证所轧制产品的质量稳定性。
如图1、图2所示,辊箱轴12的外侧套有锥套10,锥套10的外侧套有辊环11,三者之间均为过盈配合。锥套10的顶部设有耳环9。
在更换辊环时,首先需要将固定辊环的锥套进行拆卸。拆卸过程中,需要将拆卸工具的卡爪1.1与锥套10的耳环9相互重合,再用换辊打压小车向拆卸工具输出压强。拆卸工具中柱塞伸出后顶住辊箱轴12的端面,卡爪1.1在柱塞顶推的作用力下将固定辊环11的锥套10拔出。
由于辊环11与锥套10采用过盈配合,拆卸所需的拉拔力也相对较大。(数值)所以耳环9与卡爪1.1的接触面积至关重要。现有技术中卡爪1.1是否与耳环9的重合度取决于现场作业人员的操作熟练程度,缺乏一种简单、可靠及快速的判断方法。现场作业人员操作的熟练程度决定正常换辊的生产节拍,如卡爪1.1与耳环9不完全重合的情况下进行拉拔,会造成耳环9因局部区域受力过大而断裂损坏。这会导致锥套10无法通过液压拉拔的方式被正常取下,需要通过动火气割的方式进行破坏性拆卸,同时还延长了机组辊环作业时间,造成非计划停机。
目前,国内大多数生产高速线材的钢厂拥有不止一个品牌的轧机设备,不同品牌的轧机品牌的精轧机使用各自规格尺寸辊环锥套,相应的也就需要不同规格的拆卸工具。该拆辊工具不能实现一种规格拆辊工具对多个品牌精轧机组辊环锥套的兼容,造成高速线材厂拆辊工具备件种类的增加,不利于降本增效。
同时,现有的拆卸工具因为材质及制造工艺的因素,导致了其自身重量较重的现象,比如:用于8寸辊环锥套拆卸的工具重约20公斤。对于采用手提式操作的拆卸工具而言,需要通过人工的方式将其套在辊轴上,对于操作者的提拿造成了较高的工作强度,会造成操作上的不便。
技术实现要素:
本实用新型要解决的技术问题是:解决了如何快速确定拆卸工具的卡爪与锥套的耳环是否完全重合的问题。
为了解决上述技术问题,本实用新型的技术方案是提供了一种快速定位的辊环锥套液压拆卸工具,包括缸体,缸体的顶部设有进油口,缸体内设有可以上下滑动的活塞,活塞顶部与缸体顶部之间形成与进油口接通的密封腔体,缸体下部的内壁上设有端盖,端盖的中间设有可供活塞下部穿过的通孔,缸体上位于端盖的下方设有用于放置锥套上耳环的凹槽,缸体的底部位于凹槽的边缘上均布有多个用于卡住耳环且与耳环位置相对应的卡爪,其特征在于,至少一个所述的卡爪一端的位置所对应的凹槽侧壁上设有用于挡住耳环的凸起,凸起固定在缸体的内壁上。
优选地,所述的缸体的外侧固定有用于转动缸体的手柄;缸体的材质为高强度合金(例如,42crmo);活塞的材质为铝合金。
优选地,所述的活塞上部的侧面与缸体的内壁密封接触。
优选地,所述的活塞上部的侧面与缸体的内壁之间通过密封组件密封连接。
优选地,所述的活塞上部的侧面设有卡槽,密封组件套在卡槽上。
优选地,所述的活塞的下部套有复位压簧,复位压簧设于端盖与活塞上部之间。
优选地,所述的活塞的下端固定有可替换为不同规格的垫圈。
优选地,相邻两个所述的卡爪之间的间隙大于耳环的长度;所述的卡爪的长度不小于耳环的长度。
优选地,当耳环与卡爪重合时,至少一个所述的耳环一端与凹槽侧壁上的凸起接触连接。
优选地,所述的凸起为定位螺钉,缸体上开有螺纹通孔,定位螺钉设于螺纹通孔内。
本实用新型可以使得现场操作人员无需再凭借经验及每次关注拆卸工具的转动角度,继而就能快速实现拆卸工具的卡爪与锥套的耳环完全重合,保证其在拆卸时的均匀受力,最大程度地降低因锥套的耳环断裂而造成轧制机组的非常停机。
本实用新型通过在活塞端面上放置针对不同品牌机组辊环锥套尺寸量身定制的垫圈,可以实现一个基本型号拆辊工具通过增减垫圈的方式,实现了一个型号拆辊工具适用于多个不同品牌机组辊环锥套拆卸的目的,有限降低了现场使用单位备件存储的重量和数量,对于降本增效起到积极的作用。
本实用新型降低了现有技术拆辊工具的总量约25%,最大将原先20公斤的换辊工具通过制作材料的优化降至16公斤,有效降低了现场作业人员的劳动强度。
附图说明
图1为辊环与锥套装配关系的示意图;
图2为耳环的示意图;
图3为一种快速定位的辊环锥套液压拆卸工具的结构示意图;
图4为一种快速定位的辊环锥套液压拆卸工具在定位前的使用状态图;
图5为一种快速定位的辊环锥套液压拆卸工具在完成定位后的使用状态图;
图6为活塞的结构示意图(一);
图7为活塞的结构示意图(二)。
附图标记说明
1为缸体;1.1为卡爪;2为复位压簧;3为端盖;4为定位螺钉;5为活塞;
5.1为第一垫圈,5.2为第一垫圈固定螺钉,5.3为第二垫圈固定螺钉,5.4为第二垫圈;
6为手柄;7为密封组件;8为进油口;9为耳环;10为锥套;11为辊环;12为辊箱轴;13为凹槽。
具体实施方式
为使本实用新型更明显易懂,兹以优选实施例,并配合附图作详细说明如下。
本实用新型为一种快速定位的辊环锥套液压拆卸工具,如图3所示,其在具有传统锥套液压拆卸工具功能的基础上,还增加了快速定位的功能,能实现卡爪1.1与锥套10的耳环9的快速重合。本实用新型包括主要由缸体1(卡爪1.1位于缸体1底部)、复位压簧2、端盖3、定位螺钉4、活塞5、手柄6、密封组件7、进油口8组成。缸体1的外侧固定有用于转动缸体1的手柄6。缸体1的顶部设有进油口8,缸体1内设有可以上下滑动的活塞5,活塞5上部的侧面与缸体1的内壁之间通过密封组件7密封连接,活塞5上部的侧面设有卡槽,密封组件7套在卡槽上,活塞5顶部与缸体1顶部之间形成与进油口8接通的密封腔体,缸体1下部的内壁上设有端盖3,端盖3的中间设有可供活塞5下部穿过的通孔,活塞5的下部套有复位压簧2,复位压簧2设于端盖3与活塞5上部之间。缸体1上位于端盖3的下方设有用于放置锥套10上耳环9的凹槽13,缸体1的底部位于凹槽13的边缘上均布有多个用于卡住耳环9且与耳环9位置相对应的卡爪1.1,卡爪1.1的长度不小于耳环9的长度。相邻两个卡爪1.1之间的间隙可供耳环9穿过(即大于耳环9的长度)。至少一个卡爪1.1一端的位置所对应的凹槽13侧壁上设有用于挡住耳环9的凸起,凸起固定在缸体1的内壁上。当耳环9与卡爪1.1重合时,至少一个耳环9一端与凹槽13侧壁上的凸起接触连接。通过凸起挡住耳环9,即可实现快速定位的功能。
本实施例中,凸起的数量为一个,凸起为定位螺钉4,缸体1上开有螺纹通孔,定位螺钉4设于螺纹通孔内。
如图4、图5所示,本实用新型的使用过程如下:
在拆卸辊环11的操作时,先将本实用新型的拆卸工具套在辊箱轴12的端面,通过手柄6转动缸体1及卡爪1.1,缸体1上的定位螺钉4用于判断卡爪1.1是否与锥套10的耳环9的完全重合,当本实用新型的拆卸工具因为定位螺钉4接触到耳环9无法再次转动时,则可立即判断卡爪1.1已经与耳环9完全重合。此时可以进行下一步加压拉拔锥套10的步骤。
操作液压站由本实用新型的拆卸工具的进油口8输入压强,活塞5伸出后顶推辊箱轴12的端面,卡爪1.1随缸体1向上移动并扣住耳环9将锥套10拔出。电动泵卸荷后,活塞5在复位压簧2的作用力下回复到初始位置。锥套10的拆卸步骤结束。
本实用新型在传统锥套液压拆卸工具功能的基础上,对拆辊工具的活塞5结构进行了变化,通过在活塞5的端部增设不同规格的垫圈。其中,第一垫圈5.1可适用于一种品牌辊环锥套更换,第二垫圈5.4可适用于另一种品牌辊环锥套更换,如图6、图7所示,在活塞5下端的内侧开设一个平台型凹槽,用于与各种不同规格的垫圈固定连接,第一垫圈5.1的高度突出于活塞5下端的端部,第一垫圈5.1的高度小于活塞5下端的端部,位于活塞5内。第一垫圈5.1和第二垫圈5.4通过相应的第一垫圈固定螺钉5.2和第二垫圈固定螺钉5.3固定在活塞5的平台型凹槽的平台上。通过更换垫垫圈的手段,来实现一种型号拆卸工具对应多种品牌机组锥套的功能。继而实现用户只需购买一种规格的拆辊工具,配套安装针对不同品牌机组的垫圈,即可实现节省备件费用的目的。解决了现有技术中一个规格的拆卸工具无法拆卸多个品牌机组辊环锥套的问题。
本实用新型对现有拆辊工具各主要部件的材质进行了优化。针对缸体1,由高强度合金钢(例如,42crmo)替代了原先采用45#钢材质制作的缸体1,在保证缸体1机械性能的前提下,减薄了缸体1的壁厚(全系列产品壁厚减薄了2.5mm;本实用新型中规格为5寸的拆辊工具缸体外径由125mm减到120mm;规格为6寸的拆辊工具缸体外径由125mm减到120mm;规格为8寸的拆辊工具缸体外径由155mm减到150mm;规格为9寸的拆辊工具缸体外径由179mm减到175mm。),起到减重的作用。与此同时针对活塞5,采用了铝合金材质,相较于原先的45#钢起到了轻量化的目的。解决了现有拆卸工具重量较重的问题。
起点商标作为专业知识产权交易平台,可以帮助大家解决很多问题,如果大家想要了解更多知产交易信息请点击 【在线咨询】或添加微信 【19522093243】与客服一对一沟通,为大家解决相关问题。
此文章来源于网络,如有侵权,请联系删除


