一种无支撑隧道检测机器人的制作方法



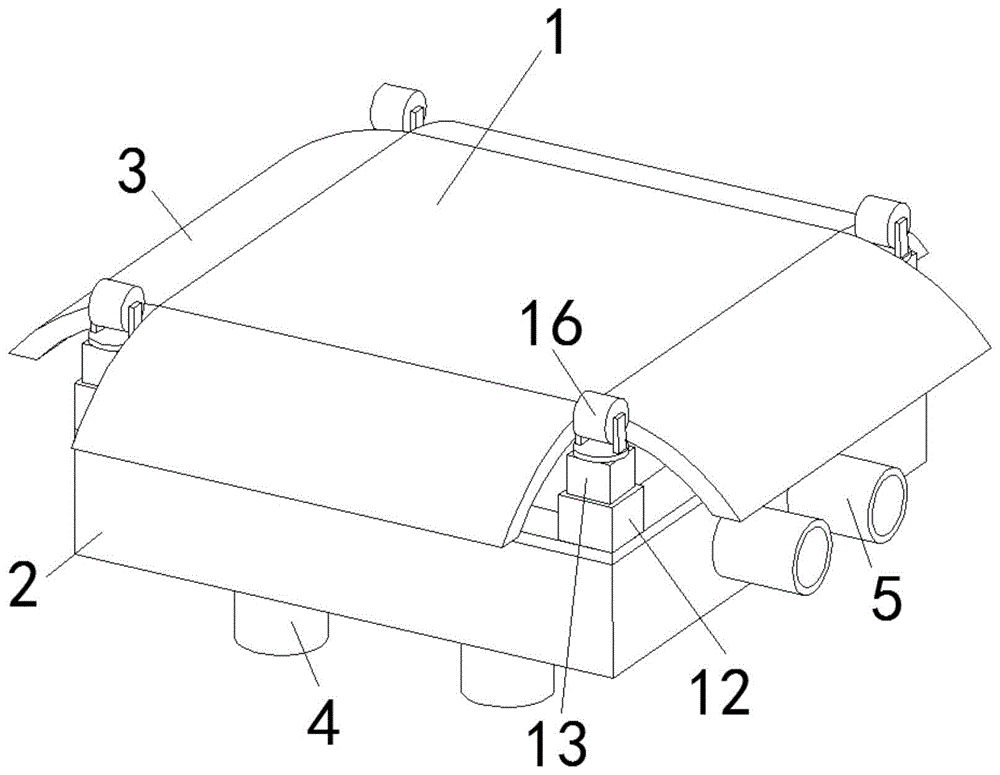
本实用新型属于隧道衬砌质量检测设备领域,具体涉及一种无支撑隧道检测机器人。
背景技术:
随着国家交通的不断发展,铁路、公路隧道里程数逐年增加。为保障隧道运营安全,常需要对在建隧道以及运营隧道进行衬砌质量检测作业,如检测隧道衬砌厚度、隧道衬砌背后未回填的空洞等,从而使隧道施工缺陷及运营病害能够得到及时治理。
目前,在隧道衬砌质量检测方面,一般是采用人工的方式,预先在隧道拱顶、左右拱腰、左右边墙共布置5条轴向检测线,由人工托举雷达天线,或由检测人员将地质雷达固定在长杆上,举着长杆让雷达紧贴检测线,并借助装载机等移动载体顺着检测线移动完成检测。在进行检测时,为维持长杆推举的稳定性,往往需要多人扶持长杆,耗费较多人力;同时,在对隧道进行检测时,检测距离长,多个操作人员需要挤在车载平台上实施检测,其随车移动过程中存在较大的安全隐患,且长时间托举雷达或长杆劳动强度大,随着人员体力下降,会造成地质雷达天线无法始终紧贴隧道衬砌壁,使得雷达天线与检测衬砌壁脱空,严重影响着隧道衬砌质量检测效率、质量和作业安全性,另外近年来也有开发一种浮动机械检测臂设备以使得雷达天线始终与隧道衬砌壁保持浮动贴合,该类设备效果较好,能有效降低作业人员劳动强度,提高检测效率,但设备本身浮动结构复杂,作业时需要将机械臂伸长至隧道衬砌检测雷达处,设备整体体积庞大,移动检测作业不便,且在既有线铁路隧道有大量接触网的情况下,很难高效检测作业,综上,现有技术其存在着:人工扶持检测装置劳动强度大且无法始终紧贴隧道衬砌内壁,浮动机械臂设备整体结构复杂、设备体积庞大,隧道内移动检测作业不便的技术问题。
技术实现要素:
本实用新型目的在于提供一种无支撑隧道检测机器人,用于解决现有技术中存在的技术问题,如:人工扶持检测装置劳动强度大且无法始终紧贴隧道衬砌内壁,浮动机械臂设备整体结构复杂、设备体积庞大,隧道内移动检测作业不便等。
为实现上述目的,本实用新型所采用的技术方案是:
一种无支撑隧道检测机器人,包括检测装置盒、底座、第一推力装置、第二推力装置、万向轮、连接机构和驱动机构,所述检测装置盒的一侧连接所述底座的一侧,所述底座的另一侧设有若干所述第一推力装置,所述若干第一推力装置呈矩形阵列分布,所述若干第一推力装置的推力方向均朝向所述检测装置盒,所述底座的两侧分别固定连接若干所述第二推力装置,所述第一推力装置的推力方向与所述第二推力装置的推力方向互相垂直,不同侧的所述若干第二推力装置的推力方向相反,所述底座与所述若干第一推力装置之间通过所述连接机构连接,所述连接机构用于使所述底座可转动地连接所述若干第一推力装置,所述驱动机构连接所述连接机构,所述驱动机构用于控制所述若干第一推力装置的转动量,适量调整第一推力装置的推力角度,所述底座设有空腔,所述连接机构和所述驱动机构均设置于所述空腔内,所述底座远离所述第一推力装置的一侧连接若干所述万向轮,所述若干万向轮用于使检测机器人在隧道内壁上滚动。
进一步的,所述连接机构包括两个转动轴和安装套,所述两个转动轴的两端均可转动地连接所述底座,所述两个转动轴互相平行地设置,所述两个转动轴与所述第二推力装置的推力方向互相平行,所述两个转动轴均固定连接有若干个所述安装套,所述两个转动轴上的所述安装套的数量一致,所述若干安装套均设有与所述第一推力装置适配的通孔,所述安装套的通孔内均固定连接有所述第一推力装置,所述底座空腔底部设有若干个直径大于所述第一推力装置径向的通孔,所述若干第一推力装置均设置于所述底座的底部通孔内,所述若干第一推力装置远离所述安装套的一端均延伸出所述底座的底部。
进一步的,所述驱动机构包括蜗杆、步进电机和两个蜗轮,所述蜗杆的两端可转动地连接所述底座,所述蜗杆垂直于所述两个转动轴,所述两个转动轴均固定连接有一个所述蜗轮,所述两个蜗轮均与所述蜗杆啮合,所述步进电机的输出端连接所述蜗杆,所述步进电机固定连接所述底座。
进一步的,还包括缓冲机构和四个弧形板,所述底座空腔设有开口,所述开口方向远离所述第一推力装置,所述开口端面可拆卸地连接有盖板,所述盖板用于盖住所述开口端面,所述检测装置盒的一侧固定连接所述盖板,所述检测装置盒为长方体结构,所述长方体结构的四侧分别固定连接所述四个弧形板的一侧,所述四个弧形板的弧心均朝向所述盖板,所述万向轮设有四个,任意一个所述弧形板的两侧均设有两个所述万向轮,所述缓冲机构设有四个,所述四个缓冲机构分别连接所述四个万向轮;
进一步的,所述缓冲机构包括连接块、固定块和弹簧,所述固定块设有具有开口的空腔,所述固定块远离开口端面的一侧固定连接所述盖板,所述连接块的一端可滑动地设置于所述固定块的空腔内,所述连接块的另一端连接所述万向轮,所述弹簧设置于所述固定块的空腔内,所述弹簧的一端固定连接所述空腔远离开口端面的一端,所述弹簧的另一端固定连接所述连接块远离所述万向轮的一端。
进一步的,所述第一推力装置和所述第二推力装置均为微型涡喷。
本实用新型的有益效果是:
(1)该一种无支撑隧道检测机器人设置有第一推力装置、万向轮、驱动机构和连接机构,通过第一推力装置可以提供使整个装置贴附于衬砌内壁上的推动力,以及通过驱动机构和连接机构改变角度以使整个装置通过万向轮沿隧道轴向行进,节约了人力,同时提高了检测效率和检测精度,达到了检测装置始终贴附衬砌内壁且节省人力的有益效果。
(2)该一种无支撑隧道检测机器人设置有第二推力装置和万向轮,通过第二推力装置可以使整个装置通过万向轮沿隧道周向滑动,可以使整个装置在隧道的拱顶、拱腰和边墙部分自由切换且沿隧道轴向行进以完成检测作业,达到了便于自由切换检测轴线的有益效果。
(3)该一种无支撑隧道检测机器人设置有第二推力装置和万向轮,通过在整个装置滑动过程中,可以通过调整底座两侧的第二推力装置的不同推力输出大小,可以使整个装置发生偏移,相关人员可以由此控制整个装置的行进路线,达到了防止跑偏的有益效果。
(4)该一种无支撑隧道检测机器人设置有蜗杆和蜗轮,通过蜗杆螺旋线升角可以设置在蜗轮的自锁范围内,进而蜗轮不能带动蜗杆转动,达到了防止第一推力装置4回转的有益效果。
(5)该一种无支撑隧道检测机器人设置有弧形板、万向轮和弹簧,通过弧形板的弧形结构总能够使整个装置顺利通过障碍物和凹凸不平的区域,并且在通过时,万向轮挤压弹簧,弹簧收缩,整个装置受到缓冲,达到了便于通过障碍物和凹凸不平的区域的有益效果。
附图说明
图1为本实用新型一种无支撑隧道检测机器人的整体结构示意图。
图2为本实用新型一种无支撑隧道检测机器人的侧剖视示意图。
图3为本实用新型一种无支撑隧道检测机器人的底座空腔内示意图。
图4为本实用新型一种无支撑隧道检测机器人的图3仰视示意图。
图5为本实用新型一种无支撑隧道检测机器人的连接机构和驱动机构示意图。
图6为本实用新型一种无支撑隧道检测机器人的万向轮和缓冲机构示意图。
图7为本实用新型一种无支撑隧道检测机器人的图3中沿转动轴的轴心竖直剖开的剖视示意图。
图8为本实用新型一种无支撑隧道检测机器人的整个装置在拱腰部分状态示意图。
图9为本实用新型一种无支撑隧道检测机器人的整个装置在拱顶部分状态示意图。
图10为本实用新型一种无支撑隧道检测机器人的整个装置在拱顶部分时第一推力装置转动状态示意图。
图11为本实用新型一种无支撑隧道检测机器人的整个装置在边墙部分状态示意图
图12为本实用新型一种无支撑隧道检测机器人的整个装置在边墙或拱腰部分时第一推力装置转动状态示意图。
图中,1-检测装置盒,2-底座,3-弧形板,4-第一推力装置,5-第二推力装置,6-转动轴,7-蜗杆,8-步进电机,9-能源装置,10-蜗轮,11-加强块,12-固定块,13-连接块,14-盖板,15-安装套,16-万向轮。
具体实施方式
下面结合本实用新型的附图1-12,对本实用新型实施例中的技术方案进行清楚、完整地描述,显然,所描述的实施例仅仅是本实用新型一部分实施例,而不是全部的实施例。基于本实用新型中的实施例,本领域普通技术人员在没有做出创造性劳动前提下所获得的所有其他实施例,都属于本实用新型保护的范围。
一种无支撑隧道检测机器人,包括检测装置盒1、底座2、第一推力装置4、第二推力装置5、万向轮16、连接机构和驱动机构,所述检测装置盒1的一侧连接所述底座2的一侧,所述底座2的另一侧设有若干所述第一推力装置4,所述若干第一推力装置4呈矩形阵列分布,所述若干第一推力装置4的推力方向均朝向所述检测装置盒1,所述底座2的两侧分别固定连接若干所述第二推力装置5,所述第一推力装置4的推力方向与所述第二推力装置5的推力方向互相垂直,不同侧的所述若干第二推力装置5的推力方向相反,所述底座2与所述若干第一推力装置4之间通过所述连接机构连接,所述连接机构用于使所述底座2可转动地连接所述若干第一推力装置4,所述驱动机构连接所述连接机构,所述驱动机构用于控制所述若干第一推力装置4的转动量,适量调整第一推力装置4的推力角度,所述底座2设有空腔,所述连接机构和所述驱动机构均设置于所述空腔内,所述底座2远离所述第一推力装置4的一侧连接若干所述万向轮16,所述若干万向轮16用于使检测机器人在隧道内壁上滚动。
第一推力装置4和第二推力装置5均可以给底座2施加一个反向作用力,而检测装置盒1中则设有检测雷达,其主要用于检测隧道衬砌内壁的质量,底座2处于检测装置盒1和第一推力装置4之间,第二推力装置5处于底座2的两侧,第一推力装置4的推力方向与第二推力装置5的推力方向互相垂直。
如图9和图10所示,在检测隧道拱顶部分时,第一推力装置4将整个装置升于空中,第一推力装置4源源不断的提供反向作用力使得万向轮16和检测装置盒1与衬砌内壁抵接,并且由于连接机构使底座2可以转动连接第一推力装置4,驱动机构可以控制第一推力装置4的转动量,所以可以控制第一推力装置4转动以达到如图10的状态,此时第一推力装置4的推力可以正交分解为一个竖直分力和一个水平分力,竖直分力继续保持检测装置盒1和隧道衬砌内壁的抵接状态,而水平分力则为整个装置提供了一个沿着隧道轴向前进的驱动力,在此驱动力的作用下,整个装置可以沿隧道一直前进,进而完成整个隧道拱顶的检测,并且根据驱动机构控制第一推力装置4的转动量的大小进而可以调节整个装置的行进速度,此外,在整个装置行进的过程中,底座2两侧的第二推力装置5可以控制推力的输出大小,又因为万向轮16可以转动的特性,所以可以控制两侧的第二推力装置5的推力大小,使整个装置向两侧偏移,在整个装置跑偏的情况下,第二推力装置5可以有效的将整个装置偏移回正常检测路线。
此外更进一步的,拱顶部分检测完成之后,在需要检测拱腰和边墙时,相关人员可以控制第一推力装置4恢复至初始状态,整个装置在惯性力的作用下继续滑行一小段距离,然后停下,此时控制一侧的第二推力装置5的推力输出大小,由于第一推力装置4始终有分力垂直于隧道衬砌内壁,所以整个装置可以沿隧道周向滑动,如图8所示,在滑动至拱腰部分时,相关人员可以控制处于下方的第二推力装置5的推力输出大小,并关闭处于上方的第二推力装置5,整个装置受到第二推力装置5向上推动的力、重力以及和衬砌内壁的摩擦力,三者受力平衡,整个装置紧贴在衬砌内壁上,同样的,在需要检测边墙部分时,整个装置可以从拱腰部分滑动至边墙部分,如图11所示,第二推力装置5推力方向竖直朝上,又如图12所示,在整个装置在检测边墙和拱腰部分时,可以通过驱动机构调整第一推力装置4的角度,以产生一个沿隧道轴向的驱动力,在此驱动力的作用下,整个装置可以沿隧道一直前进。
综上,本装置通过设置于底座2底部以及两侧的第一推力装置4以及第二推力装置5,第一推力装置4可以提供使整个装置贴附于衬砌内壁上的推动力,以及通过驱动机构和连接机构改变角度以使整个装置通过万向轮16沿隧道轴向行进,相比现有技术中人工托举的检测方式,节约了人力,同时提高了检测效率和检测精度,达到了检测装置始终贴附衬砌内壁且节省人力的有益效果,与此同时,第二推力装置5则可以使整个装置通过万向轮16沿隧道周向滑动,可以使整个装置在隧道的拱顶、拱腰和边墙部分自由切换且沿隧道轴向行进以完成检测作业,达到了便于自由切换检测轴线的有益效果,而且在整个装置滑动过程中,可以通过调整底座2两侧的第二推力装置5的不同推力输出大小,可以使整个装置发生偏移,相关人员可以由此控制整个装置的行进路线,达到了防止跑偏的有益效果。
进一步的优化本方案,所述连接机构包括两个转动轴6和安装套15,所述两个转动轴6的两端均可转动地连接所述底座2,所述两个转动轴6互相平行地设置,所述两个转动轴6与所述第二推力装置5的推力方向互相平行,所述两个转动轴6均固定连接有若干个所述安装套15,所述两个转动轴6上的所述安装套15的数量一致,所述若干安装套15均设有与所述第一推力装置4适配的通孔,所述安装套15的通孔内均固定连接有所述第一推力装置4,所述底座2空腔底部设有若干个直径大于所述第一推力装置4径向的通孔,所述若干第一推力装置4均设置于所述底座2的底部通孔内,所述若干第一推力装置4远离所述安装套15的一端均延伸出所述底座2的底部。
两个互相平行的转动轴6上设有若干安装套15,第一推力装置4插在安装套15内且固定连接安装套15,当转动轴6转动时,第一推力装置4随安装套15和转动轴6一起转动,并且因为第一推力装置4下方伸出底座2且处于底座2的底部通孔内,如图3和4所示,因为底座2的底部通孔大于第一推力装置4的径向,所以第一推力装置4可以在底部通孔内转动,并且其转动量受到限制,上述“所述连接机构用于使所述底座2可转动地连接所述若干第一推力装置4”的功能得以实现,此外,为了增强转动轴6的稳定性以及刚性,底座2的空腔内还设有若干加强块11,如图3所示,两个转动轴6均可转动地连接若干加强块11,加强块11固定连接底座2,在转动轴6受到第一推力装置4的推力时,加强块11可以稳定转动轴6的受力,使其两端受到的切力分散到各个加强块11上,起到了提高转动轴6的稳定性以及刚性的作用。
进一步的优化本方案,所述驱动机构包括蜗杆7、步进电机8和两个蜗轮10,所述蜗杆7的两端可转动地连接所述底座2,所述蜗杆7垂直于所述两个转动轴6,所述两个转动轴6均固定连接有一个所述蜗轮10,所述两个蜗轮10均与所述蜗杆7啮合,所述步进电机8的输出端连接所述蜗杆7,所述步进电机8固定连接所述底座2。
如图3和图5所示,与两个转动轴6垂直的蜗杆7连接步进电机8,当步进电机8驱动蜗杆7转动时,与蜗杆7啮合的两个蜗轮10进而带动两个转动轴6一并转动,进而使第一推力装置4的角度得以改变,并且由于步进电机8的特性,其可以通过逻辑电路轻松控制转动量,上述“所述驱动机构用于控制所述若干第一推力装置4的转动量”的功能得以实现,而且在蜗轮10和蜗杆7的传动关系中,当蜗杆7螺旋线升角小于3-6度时,蜗轮10不能带动蜗杆7转动,只能由蜗杆7带动蜗轮10转动,本装置中的蜗杆7螺旋线升角可以设置在上述角度值范围内,进而蜗轮10不能带动蜗杆7转动,由于第一推力装置4改变角度的同时,其推力会给蜗轮10以及转动轴6施加一个旋转分力,如果不对此旋转分力加以限制,第一推力装置4容易造成回转的情况,影响步进电机8控制其转动的精度,而上述将蜗杆7螺旋线升角设置于小于3-6度,此时蜗轮10不能带动蜗杆7转动,进而达到了防止第一推力装置4回转的有益效果,蜗杆7和步进电机8的连接方式可以齿轮连接、齿条连接或皮带连接等多种连接方式,在此不做限制。
此外,在整个装置在衬砌内壁实际行进过程中,其有可能遇到障碍物(例如:电线或光缆)或者凹凸不平的区域,整个装置还需解决此技术问题。
进一步的优化本方案,还包括缓冲机构和四个弧形板3,所述底座2空腔设有开口,所述开口方向远离所述第一推力装置4,所述开口端面可拆卸地连接有盖板14,所述盖板14用于盖住所述开口端面,所述检测装置盒1的一侧固定连接所述盖板14,所述检测装置盒1为长方体结构,所述长方体结构的四侧分别固定连接所述四个弧形板3的一侧,所述四个弧形板3的弧心均朝向所述盖板14,所述万向轮16设有四个,任意一个所述弧形板3的两侧均设有两个所述万向轮16,所述缓冲机构设有四个,所述四个缓冲机构分别连接所述四个万向轮16;
进一步的,所述缓冲机构包括连接块13、固定块12和弹簧,所述固定块12设有具有开口的空腔,所述固定块12远离开口端面的一侧固定连接所述盖板14,所述连接块13的一端可滑动地设置于所述固定块12的空腔内,所述连接块13的另一端连接所述万向轮16,所述弹簧设置于所述固定块12的空腔内,所述弹簧的一端固定连接所述空腔远离开口端面的一端,所述弹簧的另一端固定连接所述连接块13远离所述万向轮16的一端。
四个弧形板3呈弧形且其两端均设有万向轮16和缓冲机构,当整个装置沿隧道轴向或者周向滑动时,如图1所示,弧形板3的弧形结构总能够使整个装置顺利通过障碍物和凹凸不平的区域,并且在通过时,万向轮16挤压弹簧,弹簧收缩,整个装置受到缓冲,达到了便于通过障碍物和凹凸不平的区域的有益效果。
此外,第一推力装置4以及第二推力装置5需要输出较大的推力才能满足本装置需求。
进一步的优化本方案,所述第一推力装置4和所述第二推力装置5均为微型涡喷。
微型涡喷常用于航模以及无人机领域,其输出力一般较大,在本装置的需求上完全足够,(例如北京通航电科科技有限公司生产的型号为:pbs-tj100的微型涡喷,其最大输出推力可以达到1300n),而且根据需求的不同,微型涡喷还可以分为电动型和燃油型,底座2的空腔中还设有能源装置9,并且能源装置9与微型涡喷连接,其用于给微型涡喷提供动力来源,根据不同型号的微型涡喷的动力源的不同,能源装置9可以为蓄电池或者燃油箱,微型涡喷以及其与能源装置9之间的连接方式为现有常规技术,其安装连接方式本技术领域人员完全可以实现,本实用新型不涉及对微型涡喷的改造所以不再赘述。
另外,整个装置还设有与步进电机8和微型涡喷连接的逻辑控制电路,其可以控制步进电机8的转动量和微型涡喷输出推力大小,其安装连接方式本技术领域人员完全可以实现,本实用新型不涉及对其的改造所以不再赘述。
在本实用新型的描述中,需要理解的是,术语“逆时针”、“顺时针”“纵向”、“横向”、“上”、“下”、“前”、“后”、“左”、“右”、“竖直”、“水平”、“顶”、“底”、“内”、“外”等指示的方位或位置关系为基于附图所示的方位或位置关系,仅是为了便于描述本实用新型,而不是指示或暗示所指的装置或元件必须具有特定的方位、以特定的方位构造和操作,因此不能理解为对本实用新型的限制。
起点商标作为专业知识产权交易平台,可以帮助大家解决很多问题,如果大家想要了解更多知产交易信息请点击 【在线咨询】或添加微信 【19522093243】与客服一对一沟通,为大家解决相关问题。
此文章来源于网络,如有侵权,请联系删除


