一种单箱三室大截面悬浇箱梁腹板钢筋的预制和吊装工艺的制作方法



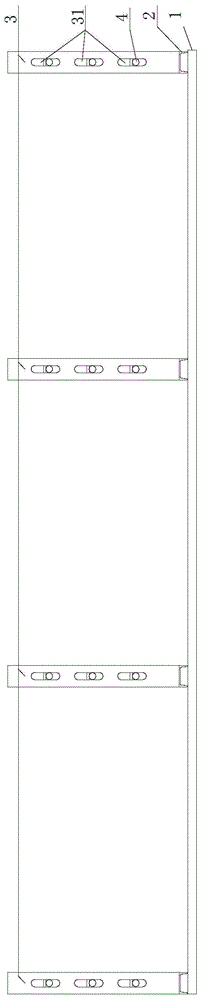
本发明涉及一种造桥工艺,具体涉及一种单箱三室大截面悬浇箱梁腹板钢筋的预制和吊装工艺。
背景技术:
新建的剑潭东江特大桥为全国最宽的高速铁路四线桥,主桥跨径为260m预应力混凝土矮塔斜拉桥。它的主梁为预应力混凝土箱梁,采用变高度单箱三室斜腹板截面,边腹板为斜腹板;跨中及边跨最低点梁高为6.0m,0号块处的梁高为13.0m,整个梁底按抛物线变化,箱梁顶宽为31.2m,底宽由边支点及跨中的22.61m变化至中支点的19.11m。主跨连续箱梁分成六十多个节段施工,采用挂篮悬臂浇筑法进行施工,每个施工节段整体截面高,重量大,对整个挂篮性能要求高。单箱多室大尺寸截面悬浇箱梁斜腹板钢筋安装工艺相对比小截面悬浇箱梁腹板钢筋安装工艺更为复杂,由于本箱梁斜腹板的最高高度达到13m,更增加了腹板钢筋的安装难度和安全风险。由于悬臂浇筑一个节段共有8块腹板,在每个腹板钢筋施工中由箍筋、纵向分布筋、纵向预应力管道、竖向预应力、端头模板安装等多道工序组成,工序数量多且繁杂,作业人员在挂篮模板内进行钢筋绑扎和预应力安装作业时,施工速度慢、工效低,难以提高工效,同时也存在作业不安全隐患。每个腹板钢筋的施工时间达48小时,同时需要6名作业人员。腹板钢筋的绑扎和安装一直是连续梁施工过程中工期的卡控点。
技术实现要素:
本发明的目的在于克服现有技术的缺陷而提供一种单箱三室大截面悬浇箱梁腹板钢筋的预制和吊装工艺,它实现了在地面上进行腹板钢筋的模块化预制,避开腹板钢筋直接在挂篮模板内绑扎存在作业空间狭小、工序互相干扰的短板,且操作方便、快捷、安全性高,有效缩短了主梁施工的作业时间。
本发明的目的是这样实现的:一种单箱三室大截面悬浇箱梁腹板钢筋的预制和吊装工艺,包括腹板钢筋整体预制流程和腹板钢筋整体吊装流程;
所述腹板钢筋整体预制流程,是在地面上采用钢筋绑扎胎具进行,用以卧式绑扎腹板钢筋;腹板钢筋整体预制时包括以下步骤:钢筋绑扎胎具制作、箍筋绑扎、吊装劲性骨架安装、端头模板安装、纵向钢筋安装和预应力筋安装:
进行钢筋绑扎胎具制作步骤时,钢筋绑扎胎具包括所述底座由三根平行设置的横向槽钢和四根间隔一致地跨接在三根横向槽钢左端之间、左部之间、右部之间和右端之间的纵向槽钢构成;
每列竖向骨架的数量为三根,每根竖向槽钢的腰部上间隔地开设三个第一竖向腰形孔;四列竖向骨架一一对应地固定在四根纵向槽钢上,且每列竖向骨架的三根竖向槽钢各自位于三根横向槽钢上;
每组纵向骨架由三根圆钢管构成,每组纵向骨架的三根圆钢管一一对应地插在每列竖向骨架的三根竖向槽钢的三个第一竖向腰形孔中;
所述卡具间隔地焊接在每根圆钢管的顶面上和每根纵向槽钢的顶面上;
进行箍筋绑扎步骤时,采用连环套双肢箍筋并采用对插的方式,即从钢筋绑扎胎具的左端和右端各自将弯好的开口矩形箍筋顺着卡具的方向并靠在卡具的一侧穿入钢筋绑扎胎具,插到位后进行对应绑扎连接,并在绑扎连接位置进行点焊加强;
进行吊装劲性骨架安装步骤时,吊装劲性骨架为在每根圆钢管的一旁和每根纵向槽钢的一旁均放置一根粗钢筋,每根粗钢筋均与箍筋焊接连接,形成吊装劲性骨架;
进行端头模板安装步骤时,端头模板采用钢板制作,并按照设计图在端头模板上预留相应的波纹管孔和钢筋孔;端头模板的尺寸以0号块的端头模板为基础,根据箱梁截面的变化,本节段的端头模板在上一个节段的端头模板的基础上进行调整改造;将端头模板临时固定在已绑扎好的箍筋的前端面上;若预制的腹板钢筋中含有纵向预应力筋的张拉端,应将锚垫板插在端头模板上设定的波纹管孔中,并对应锚垫板的安装位置将锚盒通过螺栓连接在端头模板上;
进行纵向钢筋安装步骤时,根据端头模板上预留的钢筋孔定位纵向钢筋的间距,纵向钢筋的一端从端头模板的钢筋孔中穿入并与箍筋绑扎成型,纵向钢筋的两端交错预留足够的搭接长度;
进行预应力筋安装步骤时,包括竖向预应力筋安装工序和纵向预应力管道安装工序;
进行竖向预应力筋安装工序时,竖向预应力筋采用缓粘结预应力钢绞线,按计算长度下料,有序穿入,每隔50cm采用一道u型卡扣与腹板钢筋加固在一起,并对每根竖向预应力筋的底部进行加固;
进行纵向预应力管道安装工序时,采用波纹管作为纵向预应力管道;先将波纹管从端头模板上的波纹管孔插入,临时固定于腹板钢筋上,待腹板钢筋整体吊装完成后,将波纹管与上一节段的波纹管连接好,再按设计钢筋的坐标进行精确定位,波纹管的直线段每隔50cm采用卡环与腹板钢筋加固在一起,波纹管的曲线段每隔30cm采用卡环与腹板钢筋加固在一起;最后拆除四组纵向骨架;
所述腹板钢筋整体吊装流程,包括以下步骤:吊点设置、整体起吊和整体入模安装;
进行吊点设置步骤时,在预制完成的腹板钢筋的顶面的中部均布地设置四个第一吊点,并在腹板钢筋的左侧面或右侧面的四个角部各自设置一个第二吊点;
进行整体起吊步骤时,采用塔吊和汽车吊组合的方式进行腹板钢筋整体起吊;将汽车吊的大钩勾在四个第二吊点上,汽车吊的小钩勾在四个第一吊点上,同时将塔吊的吊钩也勾在四个第一吊点上,汽车吊的大钩和小钩以及塔吊的吊钩同步上升,待腹板钢筋整体从已拆除了四组纵向骨架的钢筋绑扎胎具上吊离,并在离地面大于6.5米时,汽车吊的小钩继续上升,汽车吊的大钩慢慢下降,使腹板钢筋整体完成空中转体,直到腹板钢筋整体完全立起,此时塔吊的吊钩起钩摆正并开始受力,汽车吊的大钩和小钩不受力并放松,拆除汽车吊的挂钩卡环,塔吊的吊钩继续起钩,将腹板钢筋整体吊到本节段挂篮前端的底板作业平台位置;
进行整体入模安装步骤时,先在已完成浇筑的上一个节段的桥面上安装两个手拉葫芦,各自挂在腹板钢筋整体的顶部左边和顶部右边,同时在已浇筑完成上一个节段的底板面上也安装两个手拉葫芦,各自挂在腹板钢筋整体的底部左边和底部右边;每个手拉葫芦挂点位置均安装两根粗钢筋并与箍筋和纵向钢筋焊接;再通过塔吊和四个手拉葫芦共同作用将腹板钢筋整体向腹板的模板内侧牵引安装;腹板钢筋整体安装到位后进行与上一个节段的纵向钢筋连接和纵向预应力管道连接安装;待本节段混凝土浇筑完成后将端头模板拆除重新周转使用。
上述的单箱三室大截面悬浇箱梁腹板钢筋的预制和吊装工艺,其中,所述第一竖向腰形孔的宽度为55mm、两头孔距为150mm。
上述的单箱三室大截面悬浇箱梁腹板钢筋的预制和吊装工艺,其中,每根所述竖向槽钢的两侧腿部上各自对应地间隔开设三个第二竖向腰形孔,每根圆钢管通过插置在第二竖向腰形孔下部的定位钢筋调节高低位置。
上述的单箱三室大截面悬浇箱梁腹板钢筋的预制和吊装工艺,其中,所述第二竖向腰形孔的宽度为20mm、两头孔距为180mm,所述定位钢筋的直径为16mm,长度为15cm。
上述的单箱三室大截面悬浇箱梁腹板钢筋的预制和吊装工艺,其中,所述圆钢管的直径为48mm。
上述的单箱三室大截面悬浇箱梁腹板钢筋的预制和吊装工艺,其中,所述卡具采用直径为16mm,长度为5cm的钢筋头。
上述的单箱三室大截面悬浇箱梁腹板钢筋的预制和吊装工艺,其中,进行整体起吊步骤时,先在每个第一吊点处和第二吊点处各自在所述腹板钢筋内穿入一根粗钢筋。
本发明的单箱三室大截面悬浇箱梁腹板钢筋的预制和吊装工艺具有以下特点:将腹板钢筋在施工现场的地面上进行预制,实现了腹板钢筋模块化预制,再采用汽车吊和塔吊将腹板钢筋整体吊装入位,分别与箱梁的顶板钢筋与底板钢筋拼接的方式,并在上一个节段的混凝土浇筑完毕挂篮行走之前完成腹板钢筋的预制,使腹板钢筋绑扎与顶板钢筋与底板钢筋同时绑扎,用极短的时间进行腹板钢筋安装,避开腹板钢筋直接在挂篮模板内绑扎存在作业空间狭小、工序互相干扰的短板,同时避免高空作业等不安全因素影响,有效降低了安全风险。腹板钢筋在地面预制完成后采用汽车吊和塔吊整体吊装,安装效率快,占用塔吊时间少,进而有效缩短了主梁施工的作业时间。本发明所应用的范围广,在所有连续梁施工中均可应用,可大幅缩短工期,节省造价。
附图说明
图1是本发明的工艺在进行腹板钢筋整体预制流程中采用的单箱多室大截面悬浇箱梁斜腹板钢筋的预制绑扎胎具的正视图;
图2是图1的侧视图;
图3是图1的俯视图;
图4是本发明的工艺在进行腹板钢筋整体预制流程的箍筋绑扎步骤时的状态图;
图5是本发明的工艺在进行腹板钢筋整体吊装流程时的状态图。
具体实施方式
下面将结合附图对本发明作进一步说明。
本发明的一种单箱三室大截面悬浇箱梁腹板钢筋的预制和吊装工艺,包括腹板钢筋整体预制流程和腹板钢筋整体吊装流程;
腹板钢筋整体预制流程是在地面上采用钢筋绑扎胎具进行,用以卧式绑扎腹板钢筋;腹板钢筋整体预制时包括以下步骤:钢筋绑扎胎具制作、箍筋绑扎、吊装劲性骨架安装、端头模板安装、纵向钢筋安装和预应力筋安装:
进行钢筋绑扎胎具制作步骤时,钢筋绑扎胎具包括底座、四列竖向骨架、四组纵向骨架和卡具(图1至图3);其中,
底座由三根横向槽钢1和四根纵向槽钢2构成;三根横向槽钢1以一前、一中、一后的方式平行设置,三根横向槽钢1的间距为2075mm;四根纵向槽钢2跨接在三根横向槽钢1的左端之间、中左部之间、中右部之间和右端之间,四根纵向槽钢2的间距为2000mm;
每列竖向骨架由三根1250mm高的竖向槽钢3构成,每根竖向槽钢3的腰部上间隔地开设三个第一竖向腰形孔31,每个第一竖向腰形孔31的宽度为55mm、两头孔距为150mm;每根竖向槽钢3的两侧腿部上各自对应地间隔开设三个第二竖向腰形孔32,每个第二竖向腰形孔32的宽度为20mm、两头孔距为180mm;四列竖向骨架一一对应地固定在四根纵向槽钢2上,且每列竖向骨架3的三根竖向槽钢各自位于三根横向槽钢1上;
横向槽钢1、纵向槽钢2和竖向槽钢3均采用14号槽钢;
每组纵向骨架由三根直径为48mm的圆钢管4构成,每组纵向骨架的三根圆钢管4一一对应地插在每列竖向骨架的三根竖向槽钢3的三个第一竖向腰形孔31中;根据腹板尺寸,每根圆钢管4通过插置在第二竖向腰形孔31中的定位钢筋40调节高低位置,定位钢筋40的直径为16mm,长度为15cm;
卡具5按照设计图中箍筋的间隔尺寸(125mm)焊接在每根圆钢管4的顶面上和每根纵向槽钢2的顶面上;卡具5采用直径为16mm,长度为5cm的钢筋头。
进行箍筋绑扎步骤时,采用连环套双肢箍筋并采用对插的方式,即从钢筋绑扎胎具的左端和右端各自将弯好的开口矩形箍筋顺着卡具5的方向并靠在卡具5的一侧穿入钢筋绑扎胎具(见图4),插到位后进行对应绑扎连接,并在绑扎连接位置进行点焊加强,以保证腹板钢筋预制好后整体起吊过程中结构稳定不散架;
进行吊装劲性骨架安装步骤时,吊装劲性骨架为在每根圆钢管4的一旁和每根纵向槽钢2的一旁均放置一根粗钢筋,每根粗钢筋均与箍筋焊接连接,形成吊装劲性骨架,确保整体吊装稳定性;
进行端头模板安装步骤时,端头模板采用5mm厚的钢板制作,并按照设计图在端头模板上预留相应的波纹管孔和钢筋孔;端头模板的尺寸以0号块的端头模板为基础,根据箱梁截面的变化,本节段的端头模板在上一个节段的端头模板的基础上进行调整改造;将端头模板临时固定在已绑扎好的箍筋的前端面上,保证后续钢筋预制及整体起吊过程中不会脱落即可;若预制的腹板钢筋含有纵向预应力筋的固定端或张拉端,应将锚垫板插在端头模板上设定的波纹管孔中,并对应锚垫板的安装位置将锚盒通过螺栓连接在端头模板上;
进行纵向钢筋安装步骤时,根据端头模板上预留的钢筋孔定位纵向钢筋的间距,纵向钢筋的一端从端头模板的钢筋孔中穿入并与箍筋绑扎成型,纵向钢筋的两端交错预留足够的搭接长度;
进行预应力筋安装步骤时,包括竖向预应力筋安装工序和纵向预应力管道安装工序;
进行竖向预应力筋安装工序时,竖向预应力筋采用缓粘结预应力钢绞线,按计算长度下料,有序穿插入腹板钢筋,每隔50cm采用一道u型卡扣与腹板钢筋加固在一起,并对每根竖向预应力筋的底部进行加固,防止起吊过程中钢绞线滑落;
进行纵向预应力管道安装工序时,采用波纹管作为纵向预应力管道;先将波纹管从端头模板上的波纹管孔插入,临时固定于腹板钢筋上,待腹板钢筋整体吊装完成后,将波纹管与上一节段的波纹管连接好,再按设计钢筋的坐标进行精确定位,波纹管的直线段每隔50cm采用卡环与腹板钢筋加固在一起,波纹管的曲线段每隔30cm采用卡环与腹板钢筋加固在一起;最后拆除四组纵向骨架;
腹板钢筋整体吊装流程,包括以下步骤:吊点设置、整体起吊和整体入模安装;
进行吊点设置步骤时,一个节段上所有的腹板钢筋预制完成后,将在每一节段挂篮的端部进行吊装安放到位;先在预制完成的腹板钢筋的顶面(腹板钢筋预制时为左端面或右端面)的中部均布地设置四个第一吊点,并在腹板钢筋的左侧面或右侧面(腹板钢筋预制时为顶面)的四个角部各自设置一个第二吊点;为保证整体稳定性,起吊前在每个第一吊点处和每个第二吊点处各自在腹板钢筋内穿入一根粗钢筋,作为局部加强钢筋,并与吊装劲性骨架形成整体;
进行整体起吊步骤时,采用塔吊和汽车吊组合的方式进行腹板钢筋整体起吊;将汽车吊的大钩勾在四个第二吊点上,汽车吊的小钩勾在四个第一吊点上,同时将塔吊的吊钩也勾在四个第一吊点上,汽车吊的大钩和小钩以及塔吊的吊钩同步上升,待腹板钢筋整体从已拆除了四组纵向骨架的钢筋绑扎胎具上吊离,并在离地面大于6.5米时,汽车吊的小钩继续上升,汽车吊的大钩慢慢下降,使腹板钢筋整体完成空中转体,直到腹板钢筋整体完全立起,此时塔吊的吊钩起钩摆正并开始受力,汽车吊的大钩和小钩不受力并放松,拆除汽车吊的挂钩卡环,塔吊400的吊钩继续起钩,将腹板钢筋整体100吊到挂篮200前端的底板作业平台位置;
进行整体入模安装步骤时,先在已完成浇筑的上一个节段的桥面上安装两个2t手拉葫芦300,各自挂在腹板钢筋整体100的顶部左边和顶部右边,同时在已浇筑完成上一个节段的底板面上也安装两个2t手拉葫芦300,各自挂在腹板钢筋整体100的底部左边和底部右边;每个手拉葫芦挂点位置均安装两根粗钢筋并与箍筋和纵向钢筋焊接;再通过塔吊400和四个手拉葫芦300共同作用将腹板钢筋整体100向腹板的模板内侧牵引安装(见图5);腹板钢筋整体100安装到位后进行与上一个节段500的纵向钢筋连接和纵向预应力管道连接安装;待本节段混凝土浇筑完成后将端头模板拆除重新周转使用。
以上实施例仅供说明本发明之用,而非对本发明的限制,有关技术领域的技术人员,在不脱离本发明的精神和范围的情况下,还可以作出各种变换或变型,因此所有等同的技术方案也应该属于本发明的范畴,应由各权利要求所限定。
起点商标作为专业知识产权交易平台,可以帮助大家解决很多问题,如果大家想要了解更多知产交易信息请点击 【在线咨询】或添加微信 【19522093243】与客服一对一沟通,为大家解决相关问题。
此文章来源于网络,如有侵权,请联系删除


