一种大型桥梁支座垫板的制作方法



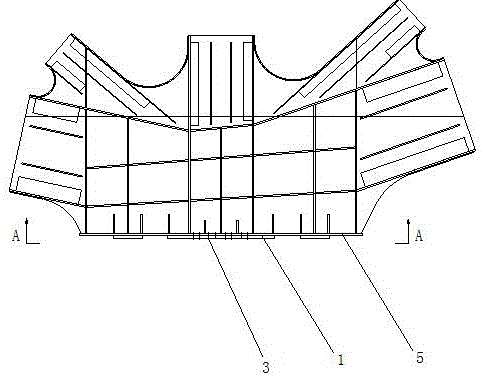
本实用新型涉及桥梁制造技术领域,具体涉及一种大型桥梁支座垫板。
背景技术:
钢桥梁支座部位的构造是桥梁受力最关键、结构最复杂的部位,也是桥梁易产生病害的关键部位之一。钢桥梁支座垫板与钢桥梁之间的连接大多采用垫板周圈角焊缝连接,对于中小桥梁,支座承受竖向荷载相对较小,支座垫板尺寸亦较小,该连接方式不会引起质量缺陷,但对于用钢量数万吨的大型桥梁,支座承受竖向荷载万吨以上,若采用悬臂架设,考虑配重及施工荷载,支座承受施工荷载可达数万吨,同时,在桥梁运营阶段,受热胀冷缩及横风影响,支座垫板承受水平力也较大,要保证支座垫板受力及使用安全,在制造和连接过程就要做到以下几点:
1)要保证支座垫板与钢梁底板5密贴连接;
2)保证周边焊接时支座垫板无变形;
3)尽量消除焊接产生的焊后残余应力;
4)设计合理的焊接坡口、焊缝尺寸及焊接顺序。
现有的支座垫板连接方式及优缺点:
1)支座垫板周圈采用角焊缝或坡口角焊缝焊接连接;该方法适用于小型桥梁支座垫板连接,其优点是操作简单,连接方便,缺点是连接精度较低,焊后支座垫板存在局部变形及焊接应力;
2)支座垫板周圈采用角焊缝或坡口角焊缝焊接连接,垫板中间开孔,焊接孔周边约束连接;该方法适用于各种支座垫板连接,其优点是适用范围广,缺点是全部采用焊接连接,焊接应力消除困难,存在一定隐患;
国内在建的宁波三官堂大桥,受航空限高及通航高度影响,桥梁结构形式采用了连续梁结构体系,其跨度同类桥梁世界第一,桥位安装施工无法采用扣塔,只能采用悬臂架设,假设过程中为保证梁体平衡,岸侧梁段需增加配重,支座竖向荷载大3万吨以上,支座垫板尺寸采用80mmx3300mmx3300mm。采用现有技术无法保证支座垫板安装精度及受力安全要求。
技术实现要素:
针对现有技术存在的支座垫板变形(中间鼓出)以及焊后应力较大,在桥梁竖向荷载及水平荷载作用下可能产生连接焊缝开裂病害,影响桥梁使用安全的问题,本实用新型提供了一种大型桥梁支座垫板,能有效解决现有技术存在的问题,保证超大支座垫板安装精度及受力安全,提高桥梁使用寿命和运营安全。
本实用新型的技术方案如下:
上述的大型桥梁支座垫板,安装在桥梁的钢梁底板底部且包括垫板本体;所述垫板本体的中部区域均匀开设有沉头螺栓孔,周向四边设有与钢梁底板焊接固定的连接焊缝;所述垫板本体通过所述沉头螺栓孔配以沉头螺栓匹配安装于钢梁底板的底部,并通过所述连接焊缝与钢梁底板的底部焊接固定。
一种大型桥梁支座垫板的连接方法,是先将支座垫板的垫板本体中部通过沉头螺栓孔配以沉头螺栓与桥梁的钢梁底板底部装配连接,再将垫板本体的周向四边通过连接焊缝与桥梁的钢梁底板底部焊接固定。
所述大型桥梁支座垫板的连接方法,其中,所述连接方法具体包括以下步骤:
(1)控制支座垫板连接精度
(1.1)对桥梁的钢梁底板预留工艺量整体机加工;
(1.2)对支座垫板的垫板本体单面进行加工;
(1.3)组装支座垫板;
(1.4)按施工图在支座垫板的垫板本体上钻制沉头螺栓孔;
(1.5)对支座垫板的垫板本体表面工艺余量整体机加工;
(2)消除支座垫板焊接应力
(2.1)在支座垫板的垫板本体上开设一定数量沉头螺栓孔;
(2.2)焊接支座垫板的垫板本体周向四边的连接焊缝;
(3)控制支座垫板变形
(3.1)对支座垫板的垫板本体单面进行加工;
(3.2)在支座垫板的垫板本体的沉头螺栓孔处安装沉头螺栓,并按要求施拧沉头螺栓到设计预紧力,以约束支座垫板的垫板本体焊后产生中间鼓起变形。
所述大型桥梁支座垫板的连接方法,其中:所述步骤(1.4)是按施工图在支座垫板的垫板本体上划出孔群位置线,按孔群位置线钻制沉头螺栓孔。
所述大型桥梁支座垫板的连接方法,其中:所述步骤(1.3)中是采用支架及顶紧装置控制支座垫板的组装精度,即使支座垫板的垫板本体组装时与钢梁底板之间密贴。
所述大型桥梁支座垫板的连接方法,其中,所述步骤(1.3)采用支架及顶紧装置控制支座垫板的组装精度的具体过程为:先在钢梁底板上焊接临时反力支架,再按线组装支座垫板,接着通过反力支架采用千斤顶将支座垫板的垫板本体顶紧,保证支座垫板的垫板本体与钢梁底板密贴。
所述大型桥梁支座垫板的连接方法,其中:所述步骤(1.2)中对支座垫板的垫板本体单面进行加工的工艺参数为进刀量0.5mm,铣刀盘走行速度0.5-0.6m/min。
所述大型桥梁支座垫板的连接方法,其中:所述步骤(2.2)是先焊支座垫板的垫板本体的上下两条连接焊缝,24h后,待应力释放基本完成,再焊支座垫板的垫板本体的左右两条连接焊缝,以避免焊接应力产生。
所述大型桥梁支座垫板的连接方法,其中:所述步骤(3.1)对支座垫板的垫板本体单面进行加工的工艺参数为进刀量0.5mm,铣刀盘走行速度0.5-0.6m/min。
有益效果:
本实用新型大型桥梁支座垫板结构设计简单、合理,安装方便,采用设计栓焊组合连接方式与桥梁支座连接,即沉头螺栓孔和沉头螺栓的设计能避免支座垫板与桥梁支座连接产生碰撞问题,支座垫板通过沉头螺栓孔配以沉头螺栓匹配安装于桥梁支座上,再通过连接焊缝与桥梁支座焊接固定,有效解决了大型桥梁超大支座垫板焊后变形及焊接应力问题,可保证桥梁使用和运营安全,提高桥梁使用寿命。
本实用新型大型桥梁支座垫板的连接方法构思合理,操作流程简单,采用栓焊组合的支座垫板连接工艺,解决了支座垫板连接焊接变形问题,避免了焊接应力产生,可有效保证大型桥梁超大支座垫板连接精度;同时,通过设计和控制铣削加工参数,能有效避免支座垫板加工热变形;通过连接结构、焊接顺序设计和焊接间隔时间设计,有利于控制支座垫板连接焊接变形,消除焊接应力;且钢梁底板5及支座垫板均进行整体或单件机加工,保证了支座垫板连接精度;采用支架及顶紧装置辅助支座垫板组装,保证了支座垫板组装精度。
附图说明
图1为本实用新型大型桥梁支座垫板与钢梁底板的装配俯视图。
图2为本实用新型大型桥梁支座垫板与钢梁底板的装配主视图。
图3为本实用新型大型桥梁支座垫板的连接方法中支座垫板上下两条连接焊缝焊接顺序示意图。
图4为本实用新型大型桥梁支座垫板的连接方法中支座垫板的左右两条连接焊缝焊接顺序示意图。
具体实施方式
如图1、2所示,本实用新型大型桥梁支座垫板,安装在桥梁的钢梁底板5底部且包括垫板本体1;该垫板本体1为矩形板状结构且中部区域均匀开设有多个沉头螺栓孔2,在多个沉头螺栓孔2处匹配安装有多个高强度的螺栓3,周向四边设有与桥梁支座焊接固定的连接焊缝4。
如图3、4所示,本实用新型大型桥梁支座垫板的连接方法,适用于大型桥梁支座垫板的连接及连接精度的控制,先将支座垫板1的中部通过沉头螺栓孔2配以沉头螺栓3与钢梁底板5装配连接,再将支座垫板1的周向四边通过连接焊缝4与钢梁底板5焊接固定。
本实用新型大型桥梁支座垫板的连接方法,具体包括以下步骤:
(1)控制支座垫板连接精度
(1.1)对桥梁的钢梁底板5预留工艺量整体机加工,保证钢梁底板5平面度在公差范围内;
(1.2)对支座垫板的垫板本体1单面进行加工,加工过程严格执行工艺参数,避免产生加工热变形;垫板本体1加工工艺参数:进刀量0.5mm,铣刀盘走行速度0.5-0.6m/min;
(1.3)组装支座垫板,采用支架及顶紧装置控制支座垫板组装精度,以保证支座垫板组装时能够与钢梁底板5之间密贴;具体操作过程为:先在钢梁底板5上焊接临时反力支架,再按线组装支座垫板,接着通过反力支架采用千斤顶将支座垫板的垫板本体1顶紧,保证支座垫板的垫板本体1与钢梁底板5密贴;
(1.4)按施工图在垫板本体1上划出孔群位置线,按孔群位置线钻制沉头螺栓孔2;
(1.5)对垫板本体1表面工艺余量整体机加工,保证垫板本体1平面度满足要求。
(2)消除支座垫板焊接应力
(2.1)在垫板本体1的中部区域开设一定数量沉头螺栓孔2,以起到螺栓连接作用和释放周边焊接产生的焊接应力;
(2.2)焊接垫板本体1周向四边的连接焊缝4,应如图3所示先焊垫板本体1的上下两条连接焊缝4,24h后,待应力释放基本完成,如图4所示再焊垫板本体1的左右两条连接焊缝4,以避免焊接应力产生。
(3)控制支座垫板变形
(3.1)对垫板本体1单面进行加工,加工过程严格执行工艺参数,避免产生加工热变形;垫板本体1加工工艺参数:进刀量0.5mm,铣刀盘走行速度0.5-0.6m/min;
(3.2)在垫板本体1中部的沉头螺栓孔2处安装沉头螺栓3,并按要求施拧沉头螺栓3到设计预紧力,以约束支座垫板焊后产生中间鼓起变形。
本实用新型能有效解决现有技术存在的问题,保证超大支座垫板安装精度及受力安全,提高桥梁使用寿命和运营安全。
起点商标作为专业知识产权交易平台,可以帮助大家解决很多问题,如果大家想要了解更多知产交易信息请点击 【在线咨询】或添加微信 【19522093243】与客服一对一沟通,为大家解决相关问题。
此文章来源于网络,如有侵权,请联系删除


