一种装配式钢管混凝土支撑系统的制作方法



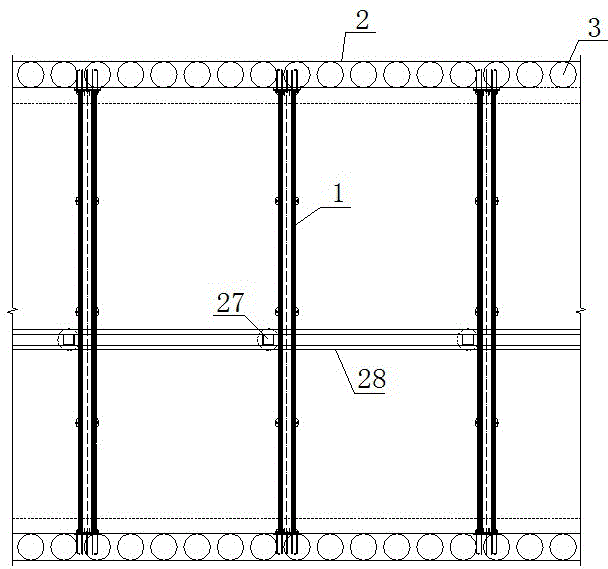
本实用新型属于地下基坑工程技术领域,具体涉及一种装配式钢管混凝土支撑系统。
背景技术:
传统现浇混凝土支撑,因其刚度大、整体性好、安全可靠等优势,普遍应用于地下工程,但也存在突出的问题和缺点:(1)费钱,投资高:混凝土支撑属于临时工程,车站结构主体完工,即破除外运,临时性废弃工程投资高,一般地下车站达数百万,复杂站点达数千万;(2)费时,工期长:混凝土支撑支模、绑扎钢筋、浇筑振捣、养护,后期的破除,整个工序长达好几个月,严重制约现场施工进度;(3)费力,难度大:混凝土支撑施工难度大,使用完成后破除施工,需耗费大量人力物力;(4)不环保,混凝土破除废渣污染环境,不符合绿色建造、环保节能的发展方向。
传统钢管撑虽然可以回收,施工较为便利,但是其与基坑支挡结构间只能承受压力,整体性较差,抗变形能力差,成为基坑安全的薄弱环节;且工厂预制的支撑节段为标准长度,在施工过程中总存在误差。
技术实现要素:
为了克服上述现有技术存在的不足,本实用新型的目的是提供一种装配式钢管混凝土支撑系统,能够提高支撑系统的稳定性,确保基坑工程安全,且装、拆卸方便,且便于构件的循环使用。
为实现上述目的,本实用新型的技术方案为一种装配式钢管混凝土支撑系统,包括围护结构和装配式钢管混凝土支撑;所述围护结构的顶部设有冠梁,所述冠梁相对的两侧之间支撑有所述装配式钢管混凝土支撑,所述装配式钢管混凝土支撑由多个钢管混凝土支撑预制件拼接而成;所述冠梁内设有支撑组件,所述装配式钢管混凝土支撑的两端与两侧所述支撑组件分别通过可伸缩连接件连接。
进一步地,所述支撑组件包括支撑钢板和支撑腿,所述支撑钢板的一侧与所述支撑腿连接,并通过加劲板加固,另一侧与所述可伸缩连接件连接。
进一步地,所述可伸缩连接件包括第一端头钢板、第一u形钢板、第二端头钢板和第二u形钢板;所述第一u形钢板焊接于所述第一端头钢板上,所述第一端头钢板与所述支撑组件固定;所述第二u形钢板焊接于所述第二端头钢板上,所述第二端头钢板与所述装配式钢管混凝土支撑的端部固定;所述第一u形钢板和所述第二u形钢板上均设有多列长圆螺栓孔,所述第一u形钢板和所述第二u形钢板上的长圆螺栓孔通过螺栓连接。
更进一步地,所述第一u形钢板和所述第二u形钢板连接形成u形槽,所述u形槽内设有与控制系统连接的千斤顶,所述千斤顶的前端和后端分别顶在所述第二端头钢板和所述第一端头钢板上。
进一步地,所述钢管混凝土支撑预制件的两端均设有环形的接头钢板,所述接头钢板上沿环向设有多个螺栓孔,相邻的所述钢管混凝土支撑预制件的相邻接头钢板上相对应的螺栓孔分别通过螺栓连接;所述可伸缩连接件与所述装配式钢管混凝土支撑端部的接头钢板连接。
更进一步地,所述钢管混凝土支撑预制件包括钢管,所述钢管内填充有混凝土,所述混凝土内具有沿轴向贯穿的中空部;所述接头钢板与所述钢管焊接,且所述接头钢板的内侧位于所述钢管内,所述接头钢板的外侧位于所述钢管外且设有所述螺栓孔。
进一步地,所述围护结构内还设有格构柱和钢围檩,所述格构柱上设有钢围檩,所述钢围檩与所述装配式钢管混凝土支撑连接。
与现有技术相比,本实用新型具有以下有益效果:
(1)本实用新型的支撑系统中采用的装配式钢管混凝土支撑是由多个钢管混凝土支撑预制件拼接而成,装配式钢管混凝土支撑与冠梁内的支撑组件通过可伸缩连接件可拆卸连接,不仅组装、拆卸方便,且便于构件的循环使用;且可伸缩连接件还可以调节端部接头长短;
(2)本实用新型通过在装配式钢管混凝土支撑两端的可伸缩连接件的另一端设置支撑组件,并在施工时,通过支撑组件支撑于围护结构上,再浇筑冠梁并将支撑组件浇筑于其中,提高装配式钢管混凝土支撑与冠梁的整体性;
(3)本实用新型的钢管混凝土支撑预制件与钢管混凝土支撑预制件之间通过螺栓连接,不仅能够满足中部节点的刚性连接、等强连接的需要,保证基坑工程的安全稳定,而且方便施工,安装和拆卸便利,便于工厂化制作和大面积的推广应用;
(4)本实用新型通过在可伸缩连接件的第一u形钢板和第二u形钢板上分别设置多列长圆螺栓孔,再通过螺栓穿过长圆螺栓孔将第二u形钢板和第一u形钢板连接,既能满足端部节点的刚性连接、等强连接的需要,保证工程安全,同时又能根据需要调节变位,调整施工误差;
(5)本实用新型通过在冠梁内侧的第一端头钢板和装配式钢管混凝土支撑端部的第二端头钢板之间设置千斤顶,在装配式钢管混凝土支撑使用过程中,出现应力松弛现象就及时进行应力补偿,出现应力过大则及时预警,防止基坑局部失稳,引起整个基坑的破坏。
附图说明
为了更清楚地说明本实用新型实施例或现有技术中的技术方案,下面将对实施例或现有技术描述中所需要使用的附图作简单地介绍,显而易见地,下面描述中的附图仅仅是本实用新型的一些实施例,对于本领域普通技术人员来讲,在不付出创造性劳动的前提下,还可以根据这些附图获得其它的附图。
图1为本实用新型实施例提供的装配式钢管混凝土支撑系统的平面布置图;
图2为本实用新型实施例提供的装配式钢管混凝土支撑系统的剖面图;
图3为本实用新型实施例提供的钢管混凝土支撑预制件的横断面图;
图4为本实用新型实施例提供的钢管混凝土支撑预制件连接处的横断面图;
图5为本实用新型实施例提供的钢管混凝土支撑预制件连接处的纵断面图;
图6为本实用新型实施例提供的装配式钢管混凝土支撑与冠梁连接处的俯视图;
图7为本实用新型实施例提供的装配式钢管混凝土支撑与冠梁连接处的剖面图;
图8为本实用新型实施例提供的第一u形钢板的左视图;
图9为本实用新型实施例提供的第二u形钢板的右视图;
图10为本实用新型实施例提供的第一端头钢板和第一u形钢板的连接示意图;
图11为本实用新型实施例提供的支撑组件的结构示意图;
图中:1、钢管混凝土支撑预制件;2、冠梁;3、围护结构;4、钢管;5、栓钉;6、混凝土;7、纵筋;8、螺旋箍筋;9、中空部;10、接头钢板;11、螺栓;12、加劲板;13、接头外衬管;14、接头内衬管;15、内包管;16、咬合齿;17、锚栓;18、第一端头钢板;19、螺母;20、第一u形钢板;21、第二u形钢板;22、千斤顶;23、穿孔塞焊;24、控制系统;25、导线;26、长圆螺栓孔;27、格构柱;28、钢围檩;29、支撑钢板;30、支撑腿;31、防腐涂层;32、第二端头钢板。
具体实施方式
下面将结合本实用新型实施例中的附图,对本实用新型实施例中的技术方案进行清楚、完整地描述,显然,所描述的实施例仅仅是本实用新型一部分实施例,而不是全部的实施例。基于本实用新型中的实施例,本领域普通技术人员在没有做出创造性劳动前提下所获得的所有其它实施例,都属于本实用新型保护的范围。
在本实用新型的描述中,需要理解的是,术语“中心”、“上”、“下”、“前”、“后”、“左”、“右”、“竖直”、“水平”、“顶”、“底”、“内”、“外”等指示的方位或位置关系为基于附图所示的方位或位置关系,仅是为了便于描述本实用新型和简化描述,而不是指示或暗示所指的装置或元件必须具有特定的方位、以特定的方位构造和操作,因此不能理解为对本实用新型的限制。
术语“第一”、“第二”仅用于描述目的,而不能理解为指示或暗示相对重要性或者隐含指明所指示的技术特征的数量。由此,限定有“第一”、“第二”的特征可以明示或者隐含地包括一个或者更多个该特征;在本实用新型的描述中,除非另有说明,“多个”的含义是两个或两个以上。
实施例一
本实施例提供一种装配式钢管混凝土支撑系统,包括围护结构3和装配式钢管混凝土支撑;所述围护结构3的顶部设有冠梁2,所述冠梁2相对的两侧之间支撑有所述装配式钢管混凝土支撑,所述装配式钢管混凝土支撑由多个钢管混凝土支撑预制件1拼接而成;所述冠梁2内设有支撑组件,所述装配式钢管混凝土支撑的两端与两侧所述支撑组件分别通过可伸缩连接件连接。本实施例的支撑系统中采用的装配式钢管混凝土支撑是由多个钢管混凝土支撑预制件1拼接而成,装配式钢管混凝土支撑与冠梁2内的支撑组件通过可伸缩连接件可拆卸连接,不仅组装、拆卸方便,且便于构件的循环使用;且可伸缩连接件还可以调节端部接头长短。
进一步地,所述支撑组件包括支撑钢板29和支撑腿30,所述支撑钢板29的一侧与所述支撑腿30连接,并通过加劲板12加固,另一侧与所述可伸缩连接件连接。如图6、图7和图11所示,支撑钢板29竖直布置,大小同第一端头钢板18一致,厚度宜大于30mm;支撑钢板29的底部连接有两个支撑腿30,且支撑钢板29与两个支撑腿30之间分别通过加劲板12焊接加固,提高支撑组件的整体性以及其与冠梁2连接的稳固性。
更进一步地,冠梁2内设有多个锚栓17,第一端头钢板18和支撑钢板29上均设有多个锚栓孔,锚栓17的一端依次穿过支撑钢板29和第一端头钢板18上对应的锚栓孔,并通过螺母19固定。如图6-图8所示,本实施例中锚栓17在冠梁2中需具有足够的锚固长度,且锚栓17和支撑腿30可与冠梁2内的钢筋形成可靠连接;螺母19下宜设垫板,可为两个,避免一个失效破坏或松弛。
进一步地,所述可伸缩连接件包括第一端头钢板18、第一u形钢板20、第二端头钢板32和第二u形钢板21;所述第一u形钢板20焊接于所述第一端头钢板18上,所述第一端头钢板18与所述支撑组件固定;所述第二u形钢板21焊接于所述第二端头钢板32上,所述第二端头钢板32与所述装配式钢管混凝土支撑的端部固定;所述第一u形钢板20和所述第二u形钢板21上均设有多列长圆螺栓孔26,所述第一u形钢板20和所述第二u形钢板21上的长圆螺栓孔26通过螺栓11连接。如图6-图10所示,本实施例中第一u形钢板20的两侧板上以及第二u形钢板21的两侧板上均设置多列可调节位置的长圆螺栓孔26,且长圆螺栓孔26均沿支撑方向布置,通过螺栓11穿过相对应的长圆螺栓孔26将第二u形钢板21和第一u形钢板20连接,既能满足端部节点的刚性连接、等强连接的需要,保证工程安全和端部节点可拆卸性,便于预制构件循环利用,同时又能根据需要调整长圆螺栓孔26的相对位置来改变接头的长度,调整施工中的误差。
更进一步地,所述第一u形钢板20和所述第二u形钢板21连接形成u形槽,所述u形槽内设有与控制系统24连接的千斤顶22,所述千斤顶22的前端和后端分别顶在所述第二端头钢板32和所述第一端头钢板18上。如图6所示,本实施例通过在冠梁和装配式钢管混凝土支撑之间设置千斤顶22,并将千斤顶22与控制系统24连接形成智能应力补偿装置,能根据需要施工预应力,满足预应力损失以及支撑松弛需要重复加载的需求;在装配式钢管混凝土支撑使用过程中,出现应力松弛现象就及时进行应力补偿,出现应力过大则及时预警,防止基坑局部失稳,引起整个基坑的破坏。本实施例采用的千斤顶22为智能千斤顶,具有足够的顶进力,同时能够感知自身应力并通过导线25传输至控制系统24,控制系统24根据应力做出相应反应,若应力松弛,则自动应力补偿;若应力过大,超过设计预警值,则自动报警。
优化地,如图10所示,第一u形钢板20和第一端头钢板18壁厚宜适当加厚,二者之间采用等强焊接,在不影响其他构件安装前提下,可以焊接加劲板12,增强二者之间的连接刚度。
优化地,第一u形钢板20的底板与第二u形钢板21的底板上相对应的位置处预留泄水孔,以防止千斤顶22所在的u形槽内积水;同时泄水孔尺寸不宜过大,防止对接头处钢板造成削弱。
进一步地,所述钢管混凝土支撑预制件1的两端均设有环形的接头钢板10,所述接头钢板10上沿环向设有多个螺栓孔,相邻的所述钢管混凝土支撑预制件1的相邻接头钢板10上相对应的螺栓孔分别通过螺栓11连接;所述可伸缩连接件与所述装配式钢管混凝土支撑端部的接头钢板10连接。如图4和图5所示,本实施例中钢管混凝土支撑预制件1之间通过多个螺栓11连接,不仅能够满足中部节点的刚性连接、等强连接的需要,保证基坑工程的安全稳定,而且方便施工,安装和拆卸便利,便于工厂化制作和大面积的推广应用。本实施例中的接头钢板10可以为圆形或方形法兰盘,接头钢板10与钢管4可以预制为整体,也可以分体预制后焊接为一体;螺栓11可以为高强螺栓,也可以为机械螺栓,满足受力需求即可;本实施例可以在接头钢板10上沿环向设置一排或多排螺栓孔,每排螺栓孔均有多个,相邻接头钢板10上的相对应的螺栓孔均通过螺栓11实现钢性连接,且每两列螺栓11之间均焊接加劲板12,确保中间节点的刚性连接,实现节点与构件的等强连接,保证基坑工程的安全稳定。
本实施例中的钢管混凝土支撑预制件1可以采用实心结构,也可以采用空心结构。
作为一种实施方式,如图3-5所示,所述钢管混凝土支撑预制件1包括钢管4,所述钢管4内填充有混凝土6,所述混凝土6内具有沿轴向贯穿的中空部9;所述接头钢板10与所述钢管4焊接,且所述接头钢板10的内侧位于所述钢管4内,所述接头钢板10的外侧位于所述钢管4外且设有所述螺栓孔。本实施例的钢管混凝土支撑预制件1为钢管4内填混凝土6的空心构件,不仅能够充分发挥钢材和混凝土两种材料的优势,性价比高,相对于纯钢支撑,具有显著的经济效益,而且钢管4为预制支撑的外表皮,可保护内部填充的混凝土6不受破坏,在工程完毕后可拆卸,实现预制构件多次循环使用,同时钢管4的套箍作用可显著提升内填混凝土6的承载能力,可以达到常规混凝土支撑相同甚至更高的强度和刚度,确保基坑工程安全。此外,本实施例中,组成钢管混凝土支撑预制件1的多个钢管混凝土支撑预制件1的中空部连通,使得装配式钢管混凝土支撑的承载能力更高、抗变形能力更强,确保基坑工程安全。
具体地,钢管4的截面可以为圆形、方形、五边形、多边形等,钢管4的厚度可在8-20mm之间,钢管4的材料可以为高强钢材,也可以为合金钢钢材料,满足受力,易于焊接即可;钢管4内填充的混凝土6可以为超高强混凝土、轻质高强混凝土、泡沫混凝土等,但需满足强度要求,且重量不宜过大,其厚度在满足支撑刚度条件下宜取小值,减轻预制构件自重;中空部可以不加任何内壁,也可以采用有内壁形式的,内壁材料可以为钢管、pvc等,其截面也不限于圆形,也可为方形、多边形等多种形状。
进一步地,所述钢管4两端的内侧和外侧分别设有接头内衬管14和接头外衬管13,所述接头内衬管14和所述接头外衬管13均与所述接头钢板10焊接。如图4和图5所示,本实施例的钢管4两端的内外两侧分别布置接头内衬管14和接头外衬管13,且接头内衬管14和接头外衬管13均可靠焊接于钢管4和接头钢板10,消除接头钢板10与钢管4连接处的受力薄弱环节;接头内衬管14和接头外衬管13材料为钢材或合金材料,壁厚取10-20mm为宜,长度以0.5-1.0m为宜,满足接头受力过渡即可。
更进一步地,所述接头钢板10伸至所述钢管4外的部分与所述接头外衬管13通过加劲板12连接。如图4和图5所示,本实施例通过加劲板12增加接头钢板10与钢管4的连接刚度,加劲板12大小及厚度根据计算及尺寸要求控制;作为一种实施方式,如图4所示,加劲板12可以有多个且沿钢管4环向间隔布置,厚度可取10-20mm,大小根据受力确定,预留富余度。
更进一步地,所述混凝土6两端的内侧均设有内包管15,所述内包管15与所述接头钢板10焊接;更进一步地,所述内包管15上设有一圈咬合齿16,所述咬合齿16嵌入所述混凝土6内。如图4和图5所示,本实施例在混凝土6的内侧焊接内包管15于接头钢板10上,保护端部混凝土;同时在内包管15内侧设置一圈咬合齿咬入混凝土6内,进一步增加钢管混凝土支撑预制件1的整体性。本实施例的内包管15壁厚以8-15mm为宜,内伸长度0.3-0.5m,材料为钢材或合金材料,但需要与接头钢板10实现可靠焊接;咬合齿16沿环向均匀设置8-12个,咬合齿16以方形为宜,边长为30-50mm即可,厚度同内包管15相同,内凹入填充混凝土6,实现二者的紧密咬合。
更进一步地,所述混凝土6内配置有螺旋箍筋8和多根纵筋7,多根纵筋7沿所述螺旋箍筋8的内侧间隔布置且均与所述螺旋箍筋8连接,所述纵筋7通过穿孔塞焊23与接头钢板10连接。如图3-图5所示,本实施例的混凝土6内沿支撑方向配置螺旋箍筋8和多根纵筋7,螺旋箍筋8取径8-14mm的一级钢为宜,在两端的接头区间距加密;纵筋7靠内侧布置,其直径和布置根数可根据实际情况确定,内部混凝土保护层厚度以50mm-80mm为宜;纵筋7的端部通过穿孔塞焊23与接头钢板10连接,将接头钢板10内凹并锚入混凝土6内,有效将接头钢板10与混凝土6融为一体,加强接头钢板10与钢管混凝土的连接强度及刚度。
更进一步地,所述钢管4的内壁上焊接有多个栓钉5,所述栓钉5嵌入所述混凝土6内。如图3所示,本实施例可以在钢管4制作前在钢带表面焊接栓钉5,并在钢管4制作时使栓钉5位于钢管4内壁上,且栓钉5嵌入混凝土6内,增加钢管4与内部混凝土6的可靠连接;栓钉5的数量以每圈8-10个为宜,长度以20mm-50mm为宜;优化地,可以在栓钉5背离钢管4内壁的一端设置锚头,增强混凝土6与钢管4之间的紧密连接效果。
本实施例中,钢管4、栓钉5、螺旋箍筋8、纵筋7紧紧与填充混凝土6连接为整体,强度高、刚度大,在使用过程中不易损坏,钢管混凝土支撑预制件1可多次循环使用;并通过在钢管4的内外两侧分别设置接头内衬管14和接头外衬管13,并将接头内衬管14和接头外衬管13均焊接于钢管4及接头钢板10,同时将接头钢板10通过穿孔塞焊23与纵筋7相连,并在混凝土6的内侧焊接内包管15于接头钢板10,确保接头钢板10与钢管4、混凝土6形成可靠连接,提高钢管混凝土支撑预制件1的整体性。
进一步地,如图3所示,所述钢管4的外表面涂刷有防腐涂层31,防止钢管混凝土支撑预制件1表面生锈破坏或者强度降低。
本实施例中的钢管混凝土支撑预制件1可以根据需要设计几种长度适宜的固定模数节段,长度过长不宜吊装施工,长度过短导致接头过多和连接困难;作为一种实施方式,中间节段预制构件可以设计4m、5m、6m等规格的标准模数,端部节段预制构件可以设计2m规格的标准模数,根据实际基坑需要,选择长度规格完全相同、不完全相同或者完全不同的钢管混凝土支撑预制件1进行组合,满足不同宽度、不同长度基坑支撑的需要,具有普遍适用性。
进一步地,所述围护结构3内还设有格构柱27和钢围檩28,所述格构柱27上设有钢围檩28,所述钢围檩28与所述装配式钢管混凝土支撑连接。如图1和图2所示,本实施例在围护结构3内的沿宽度方向的中间区域竖直设置多根格构柱27,且多根格构柱27与冠梁2相对应的位置处通过沿长度方向布置的钢围檩28连接;优化地,钢围檩28与装配式钢管混凝土支撑垂直布置并连接,防止装配式钢管混凝土支撑中部发生较大变形,进一步提高整个支撑系统的稳定性。本实施例中的格构柱27是由四根角钢及缀板焊接而成的型钢立柱,格构柱27为方形,边长根据计算确定,通常可取500mm或者600mm;钢围檩28为两根槽钢组合而成,两根槽钢可分别布置在格构柱27的两侧,槽钢断面由计算确定,钢围檩28与格构柱27连接,并与相交的钢管混凝土支撑预制件1连接,保证支撑系统的稳固。
实施例二
本实施例提供一种装配式钢管混凝土支撑系统的施工方法,包括如下步骤:
s1、根据设计图纸,在工厂制作钢管混凝土支撑预制件1,施工围护结构3及格构柱27;
s2、将钢管混凝土支撑预制件1运至施工现场,并通过螺栓11拼接形成装配式钢管混凝土支撑;
s3、将第一u形钢板20与第一端头钢板18焊接,将锚栓17依次穿过底部带有支撑腿30的支撑钢板29和第一端头钢板18,并通过螺母19固定;
s4、将第二u形钢板21与第二端头钢板32焊接,再将第二端头钢板32与装配式钢管混凝土支撑的端部通过螺栓11固定;
s5、将第一u形钢板20上的长圆螺栓孔26与第二u形钢板21上的长圆螺栓孔26通过螺栓11预连接,不拧紧;
s6、在格构柱27上安装钢围檩28;凿除围护结构3上的浮渣部分,使围护结构3的顶面平整;
s7、吊装整根装配式钢管混凝土支撑,下放至设计位置,使装配式钢管混凝土支撑的中部支撑于钢围檩28上,两端的支撑腿30分别支撑于两侧的围护结构3上,调整至设计标高;此时整根支撑形成三点支撑稳定体系;
s8、浇筑冠梁2,同时将锚栓17、支撑钢板29和支撑腿30浇筑于冠梁2内,并养护至设计强度;
s9、在第一u形钢板20和第二u形钢板21形成的u形槽内放置千斤顶22,通过控制系施加压力,使千斤顶22压力达到设计值;
s10、拧紧长圆螺栓孔26中的螺栓11,使第一u形钢板20与第二u形钢板21固定,并将装配式钢管混凝土支撑与钢围檩28相连。
本实施例中先将装配式钢管混凝土支撑以及与其端部连接的可伸缩连接件(第一端头钢板18、第一u形钢板20、第二端头钢板32和第二u形钢板21)和支撑组件(支撑腿30、支撑钢板29和锚栓17)组装后下放至指定位置,再施工冠梁2时,可以将支撑腿30和锚栓17直接浇筑到冠梁2内,提高装配式钢管混凝土支撑和冠梁2的节点强度以及支持系统的整体性。
本实施例中钢管混凝土支撑预制件1之间、钢管混凝土支撑预制件1与第二端头钢板32之间、第一u形钢板20与第二u形钢板21之间以及第一端头钢板18与支撑钢板29之间均采用螺栓连接,容易实现安装和拆卸,因此,在基坑工程施工完毕后,可以拆除螺栓,实现钢管混凝土支撑预制件1的回收,同时可多次循环利用,降低成本。
进一步地,步骤s1中制作钢管混凝土支撑预制件1的具体方法为:
s101、根据设计图纸,准备钢管4、接头钢板10、螺旋箍筋8、纵筋7、加劲板12、接头内衬管14、接头外衬管13及内包管15;
s102、钢管4在制作时已经在其内壁上预留栓钉5,在钢管4内配置螺旋箍筋8和纵筋7;
s103、在钢管4的两端分别焊接接头钢板10;
s104、在钢管4两端的内侧和外侧分别焊接接头内衬管14和接头外衬管13,使接头内衬管14和接头外衬管13均与钢管4和接头钢板10相连;
s105、将接头钢板10通过穿孔塞焊23与纵筋7连接;
s106、将外壁上设有咬合齿16的内包管15置于螺旋箍筋8内,并与接头钢板10焊接;焊接加劲板12,使其一端焊接于接头外衬管13上,一端焊接于接头钢板10上;
s107、在钢管4内填充混凝土6并预留中空部9,完成钢管混凝土支撑预制件1的制作。
上述钢管混凝土支撑预制件1的制作方法中,接头钢板10与钢管4是直接预制成整体,作为另一种实施方式,接头钢板10与钢管4也可以分体预制后连为整体,具体可以在钢管4制作后,先在在钢管4内配置螺旋箍筋8和纵筋7,接着在钢管4两端的内侧和外侧分别焊接接头内衬管14和接头外衬管13,然后将接头内衬管14端部的内侧与一环形钢板的外侧焊接,并将该环形钢板通过穿孔塞焊23与纵筋7连接,再在该环形钢板的内侧焊接内包管15,之后在钢管4内填充混凝土6并预留中空部9,完成钢管混凝土部分的预制;最后将接头内衬管14、接头外衬管13、钢管4、环形钢板、内包管15均与接头钢板10焊接,并焊接加劲板12,使其一端焊接于接头外衬管13上,一端焊接于接头钢板10上,将预制的钢管混凝土部分与接头钢板10连接成整体,完成钢管混凝土支撑预制件1的制作。
由于钢管4中心的混凝土6对构件的承载能力、整体性和刚度贡献有限,去除并不显著降低构件的承载能力,却可以显著降低构件的重量,便于安装、运输和拆卸,因此,本实施例的钢管混凝土支撑预制件1采用钢管4内填充混凝土6的空心结构形式。本实施例中可以采用离心工艺在钢管4内填充混凝土6,能够自动形成内部空心,且可以将钢管4作为离心工艺的外模板,无需拆除,同时,相比于常规的现浇振捣工艺,离心工艺方便实现高强混凝土,空心钢管混凝土的承载能力和抗变形能力更高、耐久性更好;也可采用其他工艺完成。
更进一步地,步骤s2中将钢管混凝土支撑预制件1拼接形成装配式钢管混凝土支撑的具体方法为:将两个钢管混凝土支撑预制件1对中,使两个钢管混凝土支撑预制件1相邻的接头钢板10完全对齐,并在相邻接头钢板10上相对应的螺栓孔中插入螺栓11并拧紧,依次连接各钢管混凝土支撑预制件1形成装配式钢管混凝土支撑。
本实施例的钢管混凝土支撑预制件1之间通过接头钢板10上的多个高强螺栓连接,接头钢板10与钢管4可以整体制作或者焊接,并通过加劲板12增加接头钢板10与钢管4的稳固性,同时采用接头内衬管14和接头外衬管13增加传力,还将纵筋7与接头钢板10通过穿孔塞焊23连接,中间节点结构的刚度完全可以保证。
本实施例的支撑系统中所采用的钢管4、接头钢板10、第一端头钢板18、第二端头钢板32、第一u形钢板20、第二u形钢板21、加劲板12等钢结构的外侧均可预先涂刷防腐涂层,防止钢结构生锈破坏,导致强度降低。
以上所述仅为本实用新型的较佳实施例而已,并不用以限制本实用新型,凡在本实用新型的精神和原则之内,所作的任何修改、等同替换、改进等,均应包含在本实用新型的保护范围之内。
起点商标作为专业知识产权交易平台,可以帮助大家解决很多问题,如果大家想要了解更多知产交易信息请点击 【在线咨询】或添加微信 【19522093243】与客服一对一沟通,为大家解决相关问题。
此文章来源于网络,如有侵权,请联系删除


