管涵预制构件自动化装配系统的制作方法



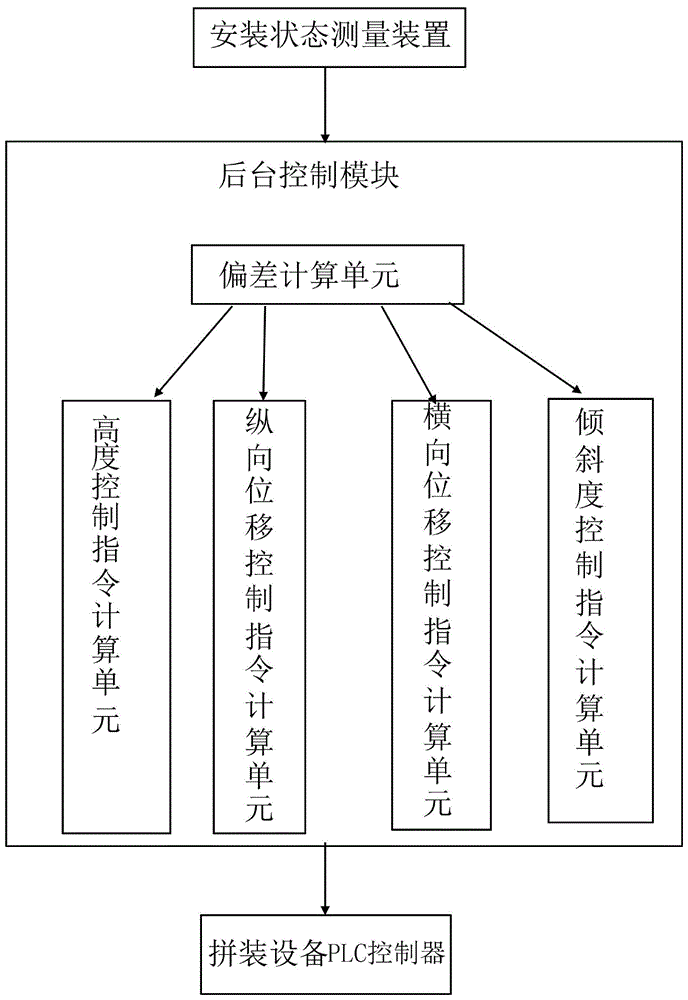
本实用新型涉及装配式管涵类工程建设技术领域,具体涉及一种实现管涵类预制构件装配过程的自动化无人化作业的装配系统。
背景技术:
装配式管涵类工程适用于多种市政基础设施工程,包括城市综合管廊、城市地下隧道、城市地下人行通道、电力管沟、排水涵、地下调蓄设施、桥涵等市政类线性工程。
上述各类工程的施工方法主要包括明挖预制法和盾构(顶管)法。相比盾构(顶管)法,明挖预制法的机械自动化水平不高,普遍采用的方法是起重吊装法,即使用吊车吊装预制构件进行装配施工,需要人工配合进行装配施工的测量、对位、调整、校准等工作。用工数量较多、施工效率不高、对位精度不高。
常规采用的装配构件的方法是起重吊装法,其装配精度有限。原因如下:预制构件在被吊装的过程中,其处于底部悬空状态,易发生微小的晃动、偏转,因此,整个构件处于一种位置和姿态不断发生动态变化的状态。在这种不可定量分析的过程态下,无论是将预制构件吊运就位,还是对其进行位置或姿态的调整,在实施过程中都不能做到精确的量化控制,只能在吊装过程中通过目测标记物、凭借感觉和经验等进行非精确量化的对位装配。在吊装工序结束后,预制构件最终被放置于稳定的位置上,构件的位置和姿态才能处于稳定状态,才能对其进行测量并获取其准确的位置和姿态数据。将测量数据与要求的数据进行比对后,如果装配误差超过限值,则需要再次吊起构件,再次进行非精确量化的调整,如此反复,耗时耗力,降低了施工效率,各个构件的装配精度也存在较大的离散性。
此外,由于起重吊装法主要使用大型起重机进行预制构件的吊装,因此,起重机需要随着构件的装配过程不断的移动其自身的位置,这就意味着在基坑侧面需要预留大量的场地,供给起重机站位使用,有的时候还要对起重机站位的地基做加强处理,施工成本高。同时,起重机吊臂较高,意味着其上部空间不能受障碍物阻碍。而在诸如老旧城区、桥下、高压线下等情况下,起重机不一定有足够的场地和条件开展作业。此外,起重机频繁的转移,也加大了的安全风险。
现有的装配式综合管廊的机械化装配施工技术及装备,一方面设备系统体量较大,不能灵活适用于不同类型、尺寸的工程,功能扩展性低,另一方面,装备周转使用能力也比较差。此外,该设备系统虽然在一定程度上实现了机械化装配、提高了装配精度,但仍需要人工测量、校核,同时需要人工操作该设备进行对位装配,未能实现自动化装配。
技术实现要素:
本实用新型的目的在于提供一种降低了人工成本、提高了装配效率和精度、降低了装配风险的管涵类预制构件的自动化装配系统,以解决上述背景技术中存在的至少一项技术问题。
为了实现上述目的,本实用新型采取了如下技术方案:
本实用新型提供一种管涵预制构件自动化装配系统,包括:
待安装预制构件安装状态测量装置,用于测量待安装预制构件的实际安装状态;
所述待安装预制构件安装状态测量装置的控制器连接后台控制模块,所述后台控制模块内预设有待安装预制构件的符合安装要求的预设安装状态;
所述后台控制模块连接待安装预制构件拼装设备,所述后台控制模块控制拼装设备实现待安装预制构件的状态调整。
优选的,所述后台控制模块包括偏差计算单元、高度控制指令计算单元、纵向位移控制指令计算单元、横向位移控制指令计算单元和倾斜度控制指令计算单元;
所述偏差计算单元分别连接所述高度控制指令计算单元、纵向位移控制指令计算单元、横向位移控制指令计算单元和倾斜度控制指令计算单元。
优选的,所述高度控制指令计算单元、所述纵向位移控制指令计算单元、所述横向位移控制指令计算单元和所述倾斜角度控制指令计算单元均连接所述待安装预制构件拼装设备的plc控制器。
本实用新型有益效果:实现预制构件在基坑内的运输,并实现运输过程的自动化;同时,实现了待安装预制构件状态的实时测量,自动控制系统装置行走至适当的位置,并自动停车;同时,自动获取预制构件的位置及姿态的数据,并通过软件算法,计算该实测数据与标准要求数据之间的偏差,并进一步转化为系统装置的各动作机构的运动参数,自动控制系统装置进行对位调整,实现了对构件进行六自由度的高精度位置及姿态的调整功能,消除了人力作业的不稳定影响因素,使预制构件的对位安装更加准确可靠。
本实用新型附加的方面和优点将在下面的描述中部分给出,这些将从下面的描述中变得明显,或通过本实用新型的实践了解到。
附图说明
为了更清楚地说明本实用新型实施例的技术方案,下面将对实施例描述中所需要使用的附图作简单地介绍,显而易见地,下面描述中的附图仅仅是本实用新型的一些实施例,对于本领域普通技术人员来讲,在不付出创造性劳动的前提下,还可以根据这些附图获得其他的附图。
图1为本实用新型实施例所述的管涵预制构件自动化装配系统原理框图。
图2为本实用新型实施例所述的管涵预制构件自动化装配系统工作状态示意图。
图3为本实用新型实施例所述的管涵预制构件拼装设备运载待安装预制构件时的状态结构图。
图4为本实用新型实施例所述的管涵预制构件自动化装配系统调整预制构件高度位置示意图。
图5为本实用新型实施例所述的管涵预制构件自动化装配系统调整预制构件横向位置示意图。
图6为本实用新型实施例所述的管涵预制构件自动化装配系统调整预制构件方位角示意图。
图7为本实用新型实施例所述的管涵预制构件自动化装配系统调整预制构件滚动角示意图。
图8为本实用新型实施例所述的管涵预制构件自动化装配系统调整预制构件俯仰角示意图。
其中:1-待安装预制构件;2-全站仪;3-后视棱镜;4-前视棱镜;5-倾角仪;6-全站仪安装架;7-已安装预制构件;8-棱镜安装架;12-控制器;13轨道;14-拼装设备;15-后台控制模块;16-plc控制器。
具体实施方式
下面详细叙述本实用新型的实施方式,所述实施方式的示例在附图中示出,其中自始至终相同或类似的标号表示相同或类似的元件或具有相同或类似功能的元件。下面通过附图描述的实施方式是示例性的,仅用于解释本实用新型,而不能解释为对本实用新型的限制。
本技术领域技术人员可以理解,除非另外定义,这里使用的所有术语(包括技术术语和科学术语)具有与本实用新型所属领域中的普通技术人员的一般理解相同的意义。还应该理解的是,诸如通用字典中定义的那些术语应该被理解为具有与现有技术的上下文中的意义一致的意义,并且除非像这里一样定义,不会用理想化或过于正式的含义来解释。
本技术领域技术人员可以理解,除非特意声明,这里使用的单数形式“一”、“一个”、“所述”和“该”也可包括复数形式。应该进一步理解的是,本实用新型的说明书中使用的措辞“包括”是指存在所述特征、整数、步骤、操作、元件和/或组件,但是并不排除存在或添加一个或多个其他特征、整数、步骤、操作、元件和/或它们的组。
在本专利的描述中,需要理解的是,术语“中心”、“上”、“下”、“前”、“后”、“左”、“右”、“竖直”、“水平”、“顶”、“底”、“内”、“外”等指示的方位或位置关系为基于附图所示的方位或位置关系,仅是为了便于描述本专利和简化描述,而不是指示或暗示所指的装置或元件必须具有特定的方位、以特定的方位构造和操作,因此不能理解为对本专利的限制。
在本说明书的描述中,参考术语“一个实施例”、“一些实施例”、“示例”、“具体示例”、或“一些示例”等的描述意指结合该实施例或示例描述的具体特征、结构、材料或者特点包含于本实用新型的至少一个实施例或示例中。而且,描述的具体特征、结构、材料或者特点可以在任一个或多个实施例或示例中以合适的方式结合。此外,在不相互矛盾的情况下,本领域的技术人员可以将本说明书中描述的不同实施例或示例以及不同实施例或示例的特征进行结合和组合。
在本专利的描述中,需要说明的是,术语“第一”、“第二”仅用于描述目的,而不能理解为指示或暗示相对重要性或者隐含指明所指示的技术特征的数量。由此,限定有“第一”、“第二”的特征可以明示或隐含地包括至少一个该特征。在本实用新型的描述中,“多个”的含义是两个或两个以上,除非另有明确具体的限定。
除非另有明确的规定和限定,术语“安装”、“相连”、“连接”、“设置”应做广义理解,例如,可以是固定相连、设置,也可以是可拆卸连接、设置,或一体地连接、设置。对于本领域的普通技术人员而言,可以根据具体情况理解上述术语在本专利中的具体含义。
为便于理解本实用新型,下面结合附图以具体实施例对本实用新型作进一步解释说明,且具体实施例并不构成对本实用新型实施例的限定。
本领域技术人员应该理解,附图只是实施例的示意图,附图中的部件并不一定是实施本实用新型所必须的。
实施例
以下实施例所示意的预制管涵构件均为矩形管涵构件。需要说明的是,本项技术可适用于矩形、圆形以及其他异形管涵类构件的自动装配。矩形管涵构件相比圆形管涵构件,实施难度更高。难点在于矩形管涵构件不能忽略滚动角的影响,而圆形管涵构件可以忽略滚动角的影响。
如图1所示,本实用新型实施例提供的一种管涵预制构件自动化装配系统,包括:
待安装预制构件安装状态测量装置,用于测量待安装预制构件的实际安装状态;待安装预制构件安装状态测量装置通过控制器连接后台控制模块,所述后台控制模块内预设有待安装预制构件的符合安装要求的预设安装状态;
所述后台控制模块,用于根据待安装预制构件的实际安装状态,结合预设安装状态,输出控制待安装预制构件拼装设备运行状态的控制指令。
待安装预制构件拼装设备,用于根据所述控制指令调整运行状态,实现待安装预制构件的状态调整。
后台控制模块读取由待安装预制构件安装状态测量装置输入的数据,然后控制拼装设备做出相应的动作。例如,安装状态测量装置,测量待安装预制构件的安装状态,得到待安装预制构件的实际高度位置、实际纵向位置、实际横向位置以及实际俯仰角信息、实际滚动角信息、实际方位角信息,安装状态测量装置通过控制器,将上述数据输出给后台控制模块。后台控制模块的偏差计算单元读取上述数据,并与待拼构件的预设状态参数进行对比,计算出待安装预制构件实际值与预设值的偏差,计算结果假设为高度位置偏差20mm、纵向位置偏差100mm、横向位置偏差25mm、俯仰角偏差1.2°、方位角偏差0.5°以及滚动角偏差0.3°。上述计算结果需要由高度、纵向位移、横向位移、倾斜度控制指令计算单元进一步按照一定的换算规则,最终换算得到拼装系统控制参数,需要拼装设备的左侧车身前进78mm,右侧车身前进122mm,1号油缸顶升-22.5mm,2号油缸顶升-7mm,3号油缸下降-48.5mm,4号油缸下降-33mm,横移装置向左平移25mm。后台控制模块将上述指令输出给拼装系统plc控制器,plc控制器根据预定程序规则,控制拼装系统执行上述指令。
需要进一步说明的是,安装状态测量装置的控制器、后台控制模块以及拼装系统的plc控制器,需要使用统一的通讯协议,并且通过有线或者无线的方式传输数据。
拼装设备执行所有指令后,安装状态测量装置复核测量安装状态,检验动作结果是否符合要求。如果不符合,再进一步给出调整数据,然后由plc控制设备做出调整。
如图2所示,本实用新型实施例中,所述待安装预制构件安装状态测量装置包括在待安装预制构件后方安装的全站仪,所述全站仪的后方安装有后视棱镜;在所述待安装预制构件上安装的多个不在同一条直线上的前视棱镜,在所述待安装预制构件的底部安装的倾角仪;所述全站仪,用于测量所述前视棱镜的位置信息,并发送给控制器;所述倾角仪,用于测量所述待安装预制构件的倾斜角度信息,并发送给所述控制器;所述控制器,用于根据所述前视棱镜的位置信息,并结合所述后视棱镜的标定位置信息计算出所述待安装预制构件的实际位置信息。
结合图2、图3,管涵预制构件安装状态测量装置,包括:
在待安装预制构件1后方安装的全站仪2,所述全站仪2的后方安装有后视棱镜3;在所述待安装预制构件1上安装的多个不在同一条直线上的前视棱镜4。在本实施例中,在所述待安装预制构件1的上表面、左侧面以及右侧面上均安装一所述前视棱镜4,共有三个前视棱镜。
所述全站仪2、所述倾角仪5均与一控制器12通信连接;所述全站仪2,用于测量所述前视棱镜4的位置信息,并发送给控制器。所述控制器,用于根据三个所述前视棱镜4的位置信息,并结合所述后视棱镜3的标定位置信息计算出所述待安装预制构件1的实际位置信息。所述全站仪2通过全站仪安装架6安装在所述待安装预制构件1后方的已安装预制构件7的顶部。所述后视棱镜3通过棱镜安装架8安装在所述全站仪2后方的已安装预制构件7的顶部。
在实际应用中,也可通过两个前视棱镜加装倾角仪的方式测量待安装预制构件的实际位置。所述倾角仪5,用于测量所述待安装预制构件1的倾斜角度信息,并发送给所述控制器,控制器根据两个前视棱镜的坐标信息、结合后视棱镜标定信息和倾角仪的信息计算待安装预制构件的实际位置;所述倾角仪5设于所述待安装预制构件1的下表面。
在本实用新型实施例中,所述待安装预制构件拼装设备,使用如申请号为2019108929729的中国实用新型专利申请公开的地铁隧道二衬结构拼装设备,该设备的具体结构及工作原理在此不再赘述。
在本实用新型实施例中,所述后台控制模块包括偏差计算单元、高度控制指令计算单元、纵向位移控制指令计算单元、横向位移控制指令计算单元和倾斜度控制指令计算单元;
所述偏差计算单元,用于根据所述实际安装状态结合所述预设安装状态,获取所述待安装预制构件的安装状态偏差;
所述高度控制指令计算单元,用于根据所述高度位置偏差计算所述待安装预制构件的高度控制指令;
所述纵向位移控制指令计算单元,用于根据所述纵向位置偏差计算所述待安装预制构件的纵向位移控制指令;
所述横向位移控制指令计算单元,用于根据所述横向位置偏差计算所述待安装预制构件的横向位移控制指令;
所述倾斜度控制指令计算单元,用于根据所述俯仰角偏差、方位角偏差以及滚动角偏差计算所述倾斜度控制指令。
在本实用新型实施例中,使用待安装预制构件安装状态测量装置实时测量待安装预制构件的实际安装状态;
后台控制模块根据待安装预制构件的实际安装状态,结合预设安装状态,输出控制待安装预制构件拼装设备运行状态的控制指令;
根据所述控制指令控制待安装预制构件拼装设备调整运行状态,实现待安装预制构件的状态调整。
所述待安装预制构件的实际安装状态包括实际位置信息和实际倾斜角度信息;所述预设安装状态包括符合安装要求的预设位置信息和预设倾斜角度信息;
所述控制指令包括高度控制指令、纵向位移控制指令、横向位移控制指令以及倾斜度控制指令;
所述实际位置信息包括待安装预制构件的实际高度位置、实际纵向位置和实际横向位置;所述预设位置信息包括符合安装要求的预设高度位置、预设纵向位置和预设横向位置;所述实际倾斜角度信息包括实际俯仰角信息、实际滚动角信息和实际方位角信息;所述预设倾斜角度信息包括预设俯仰角信息、预设滚动角信息和预设方位角信息。
根据所述实际安装状态结合所述预设安装状态,获取所述待安装预制构件的安装状态偏差;其中,所述安装状态偏差包括高度位置偏差、纵向位置偏差、横向位置偏差、俯仰角偏差、方位角偏差以及滚动角偏差;
根据高度位置偏差计算所述待安装预制构件的高度控制指令,根据高度控制指令控制所述待安装预制构件拼装设备的四个液压千斤顶同时运行,实现待安装预制构件高度位置的调整;
根据所述纵向位置偏差计算所述待安装预制构件的纵向位移控制指令,根据纵向位移控制指令控制所述待安装预制构件拼装设备的两个纵向行走驱动电机同时运行,实现待安装预制构件纵向位置的调整;
根据所述横向位置偏差计算所述待安装预制构件的横向位移控制指令,根据所述横向位移控制指令控制所述待安装预制构件拼装设备的横向驱动电机运行,实现待安装预制构件横向位置的调整;
根据所述俯仰角偏差、所述方位角偏差以及所述滚动角偏差计算所述倾斜度控制指令,根据所述倾斜角度控制指令控制所述待安装预制构件拼装设备的相应位置的千斤顶运行,实现俯仰角、方位角以及滚动角的调整。而方位角的调整,实际上是靠两个纵向行走驱动电机的不同步行走实现的。
如图3所示,待安装的预制构件在拼装通过拼装设备运送和对位,预制构件的顶部下表面及侧面均安装有安装状态测量装置的前视棱镜,通过安装状态测量装置实时测量待安装预制构件在拼装设备上运送过程中的状态。图3(a)为使用拼装设备运送待安装预制件的侧视结构图。图3(b)为使用拼装设备运送待安装预制构件的运送方式一的横截面图,该运送方式中,待安装预制构件的两侧均固定有三角托架,三角托架置于拼装设备的左右两个车体上。图3(c)为使用拼装设备运送待安装预制构件的运送方式二的横截面图,该运送方式中,待安装预制构件直接放置在拼装设备的左右两个车体上。
本实用新型实施例中,利用确定刚体内不共线的三点即可确定待安装预制构件的空间位置的原理,在预制构件上设置三个不共线的测点分别安装上前视棱镜,或者,在预制构件上设置两个测点分别安装上前视棱镜,并且在预制构件的底部安装一个测角装置(倾角仪),通过测量三个点的坐标或两个点的坐标和一个角度,确定预制构件的实际位置及姿态,并与设计要求的位置及姿态进行对比,得出偏差值,指导对位施工。
本实用新型实施例所述的装配系统工作原理如下:首先待安装预制构件安装状态测量装置测得坐标数据,计算出待安装预制构件的实际安装状态,安装状态测量装置的控制器将实际安装状态数据发送给后台控制模块,并与预设安装状态进行比对,得到位置及姿态偏差数据,再然后进一步将偏差数据换算为液压伺服千斤顶的升降高度、行走驱动伺服电机的行走距离及对位装置驱动伺服电机的平移距离等动作数据。最后,将上述动作数据转为动作指令传输给拼装设备的plc控制器,控制各机构执行动作指令。
本实用新型实施例中,使用装配系统进行预制构件的装配时,具体如下:当对待安装预制构件的水平纵向位置进行调整时,安装状态测量装置测得待安装预制构件的纵向位置(即在管涵中的纵向位置),通过后台控制器中预先输入的标准纵向位置进行比对,获取纵向位移差,通过纵向位移控制指令计算单元获取纵向位移控制指令,发送给拼装设备的plc控制器,plc控制器控制左右两个车体的纵向移动驱动电机(即第一驱动电机)驱动两个车体同时移动,从而调整带安装预制构件的纵向位置,待运送至符合安装要求的纵向位置时,plc控制器控制第一驱动电机停止工作。
如图4所示,当对待安装预制构件的高度进行调整时,安装状态测量装置测得待安装预制构件的运送高度位置,通过与后台控制器中预先输入的标准高度位置比对,获取高度差,通过高度控制指令计算单元计算高度控制指令发送给拼装设备的plc控制器,plc控制器控制液压千斤顶同时升高或降低,实现待安装预制构件的高度的调整,从而调整到符合安装要求的高度。待高度符合要求,控制器控制四个液压千斤顶同时停止升高或降低。
如图5所示,当对待安装预制构件的横向位置进行调整时,安装状态测量装置测得待安装预制构件的横向位置,通过与后台控制模块中预先输入的标准横向位置比对,获取横向位移差,通过横向位移控制指令计算单元计算横向位移控制指令,发送给拼装设备的plc控制器,plc控制器控制横向驱动电机(即第二驱动电机)运行,使拼装设备上的滑台和滚轮带动待安装预制构件发生横向移动,实现预制构件横向位置的调节,从而调整到符合安装要求的位置。待横向位置符合要求时,控制器控制第二驱动电机停止工作。
如图6所示,其中,图6(a)为待安装预制构件方位角对正的状态示意图,图6(b)表示待安装预制构件的方位角倾斜的状态示意图,图6(b)中,拼装设备左侧车体单独向前行走或者右侧车体单独向后行走,都可以使待安装构件方位角发生转动,达到调整方位角的目的。当对待安装预制构件的方位角进行调整时,假设方位角以正北为0°,如果构件当前的方位角是1°,那么通过后台控制模块计算,就可以得出一侧车体前进或者另一侧车体后退的距离。具体是哪一侧车体移动,可以通过程序控制,比如无论前进还是后退,只允许左侧车体移动。
如图7所示,其中,图7(a)为待安装预制构件滚动角对正的状态示意图,图7(b)表示待安装预制构件的滚动角倾斜的状态示意图,此时,拼装设备左右两侧的车体的千斤顶高度位置不一致,但是,位于同一侧的千斤顶的高度是一致的,导致待安装预制构件整体倾斜,滚动角不对正。当对待安装预制构件的滚动角进行调整时,可以规定只调整一侧油缸,升高或降低,来实现滚动角的调整。
如图8所示,其中,图8(a)为待安装预制构件俯仰角对正的状态示意图,图8(b)表示待安装预制构件的俯仰角倾斜的状态示意图,此时,拼装设备车体的四个千斤顶高度位置不一致,但是,位于前侧的两个千斤顶的高度是一致的,后侧的两个千斤顶的高度是一致的,但是前侧和后侧千斤顶的高度不一致,导致待安装预制构件整体前后倾斜,俯仰角不对正。当对待安装预制构件的俯仰角进行调整时,俯仰角比如设计要求是上坡,坡度1%,就可以以最低位油缸为0,其他油缸升高或降低,调整至这个俯仰角。
总之,滚动角及俯仰角的角度控制实际最终也是靠高度来调整的,而方位角的控制,是通过控制两侧车体的驱动电机的不同步来实现的。
综上所述,本实用新型实施例所述的管涵预制构件自动化装配系统,实现预制构件在基坑内的运输,并实现运输过程的自动化:该系统装置具备驮运构件在基坑内行走的功能。同时,集成行走里程实时安装状态测量装置,自动控制拼装设备行走至适当的位置,并自动停车。实现了预制构件安装的对位、测量、校核、调整的自动化:系统具备对构件进行六自由度的大幅度位置及姿态的调整功能,意味着其完成构件的对位工作。同时,集成预制构件的位置及姿态自动测量系统,自动获取预制构件的位置及姿态的数据,并通过软件算法,计算该实测数据与标准要求数据之间的偏差,并进一步转化为系统的各动作机构的运动参数,自动控制系统装置进行对位调整。
本领域普通技术人员可以理解:本实用新型实施例中的装置中的部件可以按照实施例的描述分布于实施例的装置中,也可以进行相应变化位于不同于本实施例的一个或多个装置中。上述实施例的部件可以合并为一个部件,也可以进一步拆分成多个子部件。
以上所述,仅为本实用新型较佳的具体实施方式,但本实用新型的保护范围并不局限于此,任何熟悉本技术领域的技术人员在本实用新型揭露的技术范围内,可轻易想到的变化或替换,都应涵盖在本实用新型的保护范围之内。因此,本实用新型的保护范围应该以权利要求的保护范围为准。
起点商标作为专业知识产权交易平台,可以帮助大家解决很多问题,如果大家想要了解更多知产交易信息请点击 【在线咨询】或添加微信 【19522093243】与客服一对一沟通,为大家解决相关问题。
此文章来源于网络,如有侵权,请联系删除


