单线切片机布线装置的制作方法



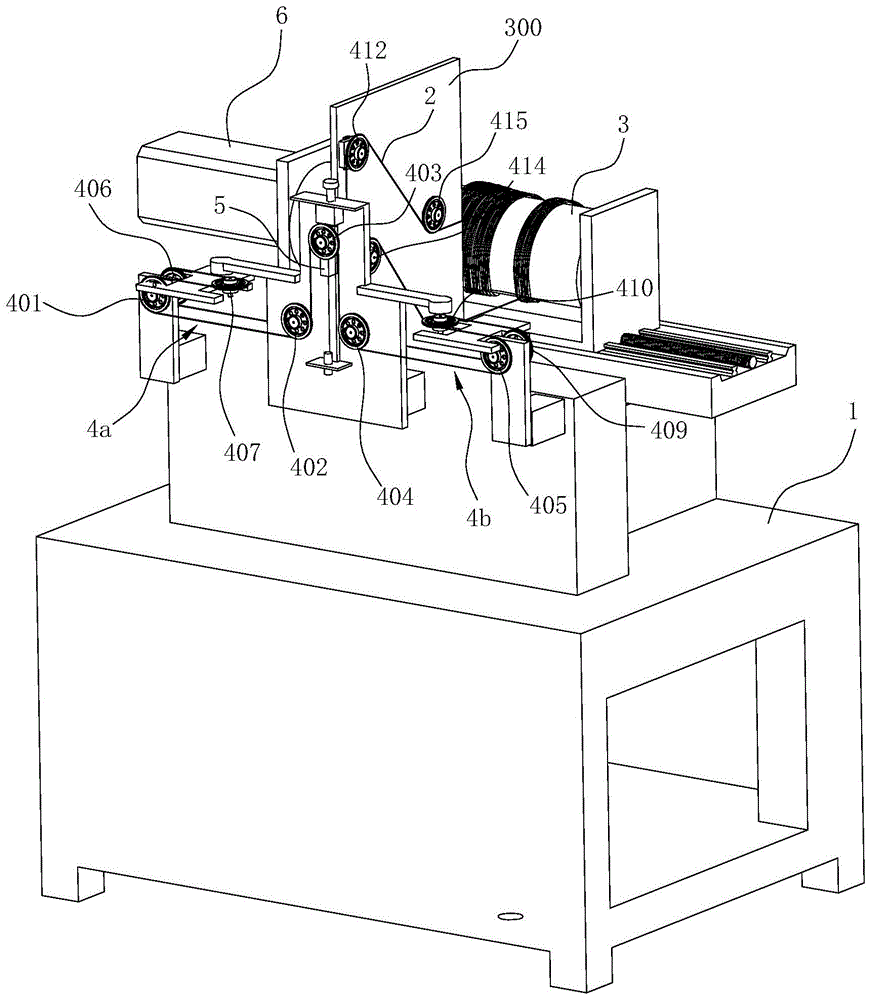
本实用新型涉及单线切割技术领域,具体指一种单线切片机布线装置。
背景技术:
机床对零件机械加工的材料涉及二大领域,即塑性材料和硬脆材料。塑性材料加工的机床即金属切割加工通用机床,机床性能范围广;硬脆材料零件加工的机床即为金刚钻工具加工的专用机床(电加工机床除外),该类机床中又有具备切片功能的金刚线工具机械加工硬脆材料零件的专用机床。
上述具有切片功能的机床切割范围包括钕铁硼磁性材料、铁氧体磁性材料、陶瓷、晶体、半导体、宝石、石英、玻璃、水晶、珍贵石材、硬质合金等硬脆材料,其发展情况如下:
1、最初的切片机为十九世纪五十年代出现的外园切片机(包括多刀切片机),由于刀片较厚,加工效果较差,切割后的材料需要进行二次加工,导致加工材料成本高、材料浪费率高;
2、锯形多带钢条切片机,由于其使用了颗粒钻磨砂,导致切割效率低下,而且带状钢条装夹紧度高,难度大,费工;
3、七十年代引进了日本的切片机,加工效果及效率都大大提高,但一位操作工只能操作2-3台机床,由于集成加工属于劳动密集行业,机床采用粗犷型开放加工,对环境污染大;
4、二十世纪以来,全自动切片机开始投入国内市场,进行全封闭加工,解决了三废的环境问题;并且,一位操作工可操作20-30台机床,促进了硬脆材料的集成加工发展,全国拥有十万余台这样的全自动切片机沿用至今;
5、钢线多线切片机出现,此种机床基本上为太阳能单晶硅加工服务,由于使用砂浆作为切割载体导致环境污染、效率低、投资成本高等问题,现已退出市场;
6、金刚线多线切片机出现。由于微颗粒金刚石涂覆高科技技术的突破,近几年金刚线多线切片机快速进入硬脆材料零件加工领域,它的最大优势为进行大批量加工,但是,由于其每加工一种产品,都要进行购置专用切割辊(俗称罗拉)加工,加工辅助费用成本极高,而且机床复杂,设备投资成本高昂,中小企业难以承担,严重限制了其在硬脆材料零件加工领域的应用。
同时,金刚线多线切片机由于金刚线的张力控制程度低,金刚线的切割张力小,所以零件粗糙度需二次加工,有換向时间长、单线计算切割效率低的缺陷。目前,市场上也有单线切割技术,但是,只是在金刚线多线切割机基础上进行改制,把多线切割辊改成单线或少线切割辊。因此切割效率低下、设备体积大、结构复杂,致使设备价格高,加工精度也无法保证,无法满足小微企业的需求。
因此,对于目前单线切割的设备,有待于做进一步的改进。
技术实现要素:
本实用新型所要解决的技术问题是针对现有技术的现状,提供一种通过改变绕线方式从而提高切割效率的单线切片机布线装置。
本实用新型解决上述技术问题所采用的技术方案为:一种单线切片机布线装置,包括用于切割物料的切割线,其特征在于:还包括用于引导切割线走向的导轮组件,所述切割线绕过导轮组件形成至少两组间隔布置的切割区域;
所述导轮组件包括第一导轮、第二导轮、第三导轮、第四导轮及第五导轮,该第一导轮、第二导轮、第三导轮、第四导轮及第五导轮的轴心线前后延伸且均位于第一竖直平面内,所述第一导轮、第二导轮间隔布置在第三导轮的第一侧下方,所述第四导轮、第五导轮间隔布置在第三导轮的第二侧下方并与第一导轮、第二导轮位于同一直线上,所述切割线依次绕过第一导轮、第二导轮、第三导轮、第四导轮、第五导轮构成“几”字形结构,该“几”字形结构的第一侧横边位于第一切割区域内且形成第一切割工位,该“几”字形结构的第二侧横边位于第二切割区域内且形成第二切割工位。采用上述结构,分别在两个切割区域内形成切割工位,且并排布置的两切割区域相邻布置,便于一个操作人员兼顾两个切割区域的工作,提高加工效率。
在上述方案中,所述导轮组件包括能将切割线分为左右两边独立切割区域的转角导轮及进一步将两加工区域分为四个切割工位的转向导轮,所述“几”字形结构位于两切割区域之间。
作为改进,所述第三导轮能上下浮动地设于机架上并位于“几”字形结构的顶部,所述切割线绕过第三导轮的上边缘布置,所述机架上设置有能使第三导轮始终保持向上移动趋势的弹性件。本实用新型利用第三导轮将同一输送方向上的一股切割线分为两个切割工位,在切割线启用或换向时,容易存在切割线各处张紧力不均、切割线局部张紧力过松或过紧的问题,如果切割线局部过松就无法满足切割需求,影响切割质量;如果切割线局部过紧就极易导致切割线断线。采用上述结构,当切割线较松时,弹性件驱使第三导轮带动切割线向上移动一定位移,从而使切割线张紧;当切割线过紧时,允许第三导轮在切割线的拉动下向下移动一定位移;即第三导轮可随切割线的松紧上下浮动,实时有效的调节切割线松紧度,从而维持切割线各处松紧度均匀,保持稳定的切割力,且避免断线。
优选地,所述导轮组件还包括第六导轮、第七导轮、第八导轮、第九导轮、第十导轮及第十一导轮,所述第六导轮、第八导轮、第九导轮及第十一导轮的轴心线前后延伸且均位于第二竖直平面内,该第二竖直平面位于第一竖直平面的后侧,所述第六导轮对应第一导轮布置,所述第七导轮设于第一切割区域的上方或下方且用于使第一导轮、第六导轮之间的切割线换向,所述第八导轮对应第二导轮布置,所述第六导轮、第八导轮之间的切割线位于第一切割区域内且形成第三切割工位,所述第九导轮对应第五导轮布置,所述第十导轮设于第二切割区域的上方或下方且用于使第五导轮、第九导轮之间的切割线换向,所述第十一导轮对应第四导轮布置,所述第九导轮、第十一导轮之间的切割线位于第二切割区域内且形成第四切割工位。采用上述结构,巧妙的将切割线的走向逆转180°,并使第三切割工位与第一切割工位对齐,使第四切割工位与第二切割工位对齐,便于多个工位同时操作,进一步提高加工效率;且四个切割工位由一根切割线形成,便于控制各切割工位的切割力稳定、统一,提高切割效果。
优选地,所述第七导轮、第十导轮均位于相应切割区域的上方且轴心线竖直布置,所述切割线的第一端自前向后依次绕过第一导轮外缘、第七导轮内缘、第六导轮外缘、第八导轮下缘布置,所述切割线的第二端自前向后依次绕过第五导轮外缘、第十导轮内缘、第九导轮外缘、第十一导轮下缘布置。采用这样的结构,不仅方便完成切割线的换向,而且能尽可能缩短换向区域的切割线长度,有利于控制切割线的整体张力稳定。
优选地,所述第一导轮与第六导轮前后对齐,所述第二导轮与第八导轮前后对齐。所述第四导轮与第十一导轮前后对齐,所述第五导轮与第九导轮前后对齐。采用上述结构,使对应第一切割工位、第二切割工位、第三切割工位、第四切割工位的切割线长度一致,切割力一致且稳定;且第一切割工位的切割线与第三切割工位的切割线前后对齐,第二切割工位的切割线与第四切割工位的切割线前后对齐,在切割物料时,物料对应于前后相同位置时,切割线的张紧力一致,切割效果一致,从而在保持高切割效果的基础上,提高物料切割效果的一致性。
为了便于将切割线缠绕在滚筒上,所述导轮组件还包括第十二导轮、第十三导轮、第十四导轮,所述第十二导轮设于竖直装配板上且该竖直装配板垂直布置在第二竖直平面的后侧,所述第十三导轮设于第二竖直平面上并位于第八导轮的上方,且所述第十三导轮的内边缘与第十二导轮的前边缘对齐,所述第十四导轮设于竖直装配板上且位于第十二导轮的后下方,所述滚筒横向布置的第十四导轮后方,所述切割线的第一端自前向后依次绕过第八导轮下缘、第十三导轮内缘、第十二导轮前缘及上缘、第十四导轮下缘缠绕于滚筒上侧。采用上述结构,使切割线无偏差的缠绕在滚筒上,滚筒正转时,滚筒下侧为切割线释放侧,滚筒上侧为切割线回线侧;滚筒反转时,滚筒上侧为切割线释放侧,滚筒下侧为切割线释放侧,以实现切割线的稳定往复传动。
优选地,所述导轮组件还包括第十五导轮、第十六导轮,所述第十五导轮设于竖直装配板上且位于第十二导轮下方,所述第十五导轮的前边缘与第十一导轮的内边缘对齐,所述第十六导轮设于竖直装配板上且位于第十五导轮的后下方,所述切割线的第二端自前向后依次绕过第十一导轮的下缘及内缘、第十五导轮的前缘及上缘、第十六导轮的下缘缠绕于滚筒下侧。上述结构有利于提高切割线的传送稳定性。
在上述各方案中,所述机架上设置有能控制滚筒转动方向及转动速度的驱动机构。
作为替代方案,所述第七导轮设于第一导轮、第六导轮上方,所述第七导轮的轴心线横向布置且其后边缘与第六导轮的外边缘相对应、其前边缘与第一导轮的外边缘相对应;所述第十导轮设于第五导轮、第九导轮上方,所述第十导轮的轴心线横向布置且其后边缘与第九导轮的外边缘相对应、其前边缘与第五导轮的外边缘相对应;所述切割线的第一端自前向后依次绕过第一导轮外缘、第七导轮上缘、第六导轮外缘、第八导轮下缘布置,所述切割线的第二端自前向后依次绕过第五导轮外缘、第十导轮上缘、第九导轮外缘、第十一导轮下缘布置。为了便于在整机上对第七导轮、第十导轮进行安装及合理排布,还可以采用上述结构。
与现有技术相比,本实用新型的优点在于:本实用新型提供了一种单线切割的绕线结构,切割线可以是自一绕线筒的一侧输出、自该绕线的另一侧收回,并通过绕线筒的正反转实现切割线的往复传送,本实用新型通过“几”字形结构的转角导轮,使切割线的走向转90°方向,形成左右对称的两边切割区域布局,左右两边布局中转向导轮进一步使切割线的走向转向180°,形成由配对两个切割轮组成的四个切割工位,可实现多个物料的同时切割,提高了切割效率;
本实用新型采用配对的切割轮代替现有技术中配对的多线切割线切片机的专用切割辊(罗拉),具有布线简单、引线方便的优势,而且能使机床整体结构简化,控制操作更加方便。
附图说明
图1为本实用新型实施例1的结构示意图;
图2为本实用新型实施例1的侧视图;
图3为本实用新型实施例1中导轮组件与切割线的配合结构示意图;
图4为本实用新型实施例1中导轮组件与切割线另一角度的配合结构示意图;
图5为本实用新型实施例2中导轮组件与切割线的配合结构示意图。
具体实施方式
以下结合附图实施例对本实用新型作进一步详细描述。
在本实用新型的说明书、权利要求书中及下述实施例中使用了“上”、“下”、“左”、“右”“侧”等方位词,但这些方位词仅仅表示相对位置关系,并不限定为绝对方向,比如“上”、“下”并不限定为与重力方向相反或一致的方向。
实施例1:
如图1~4所示,本实施例的单线切片机布线装置包括切割线2及导轮组件4。其中,切割线2用于切割物料,切割线2缠绕在一滚筒3上,本实施例的切割线2采用金刚线,当然切割线并不限于金刚线。滚筒3能转动地设于机架1后侧,且滚筒3左右横向布置。滚筒3的上侧为第一绕线侧,滚筒3的下侧为第二绕线侧,第一绕线侧与第二绕线侧随滚筒3转动方向的转换而在排线状态与回线状态之间往复切换。例如,滚筒3绕一个方向旋转时,滚筒3的上侧为切割线2排线侧,滚筒3的下侧为切割线2回线侧;滚筒3反向旋转时,滚筒3的下侧为切割线2排线侧,滚筒3的上侧为切割线2回线侧。导轮组件4包括多个导轮,各导轮均能转动地设于机架1上,导轮组件4用于引导切割线2的走向,切割线2绕过导轮组件4形成至少两组间隔布置的切割区域。
具体的,本实施例的导轮组件4包括第一导轮401、第二导轮402、第三导轮403、第四导轮404、第五导轮405、第六导轮406、第七导轮407、第八导轮408、第九导轮409、第十导轮410、第十一导轮411、第十二导轮412、第十三导轮413、第十四导轮414、第十五导轮415、第十六导轮416。
上述第一导轮401、第二导轮402、第三导轮403、第四导轮404及第五导轮405的轴心线前后延伸且均位于第一竖直平面100内,第一竖直平面100平行滚筒3的轴向布置且位于滚筒3的前侧,第三导轮403位于第一竖直平面100中上部,第一导轮401、第二导轮402间隔布置在第三导轮403的左侧下方,第四导轮404、第五导轮405间隔布置在第三导轮403的右侧下方并与第一导轮401、第二导轮402位于同一直线上,切割线2依次绕过第一导轮401、第二导轮402、第三导轮403、第四导轮404、第五导轮405构成“几”字形结构,更加确切的说,该“几”字形结构为
上述第六导轮406、第八导轮408、第九导轮409及第十一导轮411的轴心线前后延伸且均位于第二竖直平面200内,该第二竖直平面200平行布置在第一竖直平面100的后侧、滚筒3的前侧,第六导轮406对应第一导轮401布置,第七导轮407设于第一切割区域4a的上方且用于使第一导轮401、第六导轮406之间的切割线2换向,第八导轮408对应第二导轮402布置,第六导轮406、第八导轮408之间的切割线2位于第一切割区域4a内且形成第三切割工位43。第九导轮409对应第五导轮405布置,第十导轮410设于第二切割区域4b的上方且用于使第五导轮405、第九导轮409之间的切割线2换向,第十一导轮411对应第四导轮404布置,第九导轮409、第十一导轮411之间的切割线2位于第二切割区域4b内且形成第四切割工位44。本实施例的第七导轮407、第十导轮410均位于相应切割区域的上方且轴心线竖直布置,当然,第七导轮407、第十导轮410也可以位于相应切割区域的下方,只要能实现前后对应的切割线2换向即可。切割线2的第一端自前向后依次绕过第一导轮401外缘、第七导轮407内缘、第六导轮406外缘、第八导轮408下缘布置,切割线2的第二端自前向后依次绕过第五导轮405外缘、第十导轮410内缘、第九导轮409外缘、第十一导轮411下缘布置。上述结构巧妙的将切割线2的走向逆转180°,并使第三切割工位43与第一切割工位41对齐,使第四切割工位44与第二切割工位42对齐,便于多个工位同时操作,进一步提高加工效率;且四个切割工位由一根切割线2形成,便于控制各切割工位的切割力稳定、统一,提高切割效果。
本实施例的第一导轮401与第六导轮406前后对齐,第二导轮402与第八导轮408前后对齐。第四导轮404与第十一导轮411前后对齐,第五导轮405与第九导轮409前后对齐。采用上述结构,使对应第一切割工位41、第二切割工位42、第三切割工位43、第四切割工位44的切割线2长度一致,切割力一致且稳定;且第一切割工位41的切割线2与第三切割工位43的切割线2前后对齐,第二切割工位42的切割线2与第四切割工位44的切割线2前后对齐,在切割物料时,物料对应于前后相同位置时,切割线2的张紧力一致,切割效果一致,从而在保持高切割效果的基础上,提高物料切割效果的一致性。
上述第十二导轮412设于竖直装配板300上,竖直装配板300垂直布置在第二竖直平面200的后侧、滚筒3的前侧,第十三导轮413设于第二竖直平面200上并位于第八导轮408的上方,第十二导轮412位于第十三导轮413上方,且第十三导轮413的内边缘与第十二导轮412的前边缘对齐,第十四导轮414设于竖直装配板300上且位于第十二导轮412的后下方,滚筒3横向布置的第十四导轮414后方,切割线2的第一端自前向后依次绕过第八导轮408下缘、第十三导轮413内缘、第十二导轮412前缘及上缘、第十四导轮414下缘缠绕于滚筒3上侧。第十五导轮415设于竖直装配板300上且位于第十二导轮412下方,第十五导轮415的前边缘与第十一导轮411的内边缘对齐,第十六导轮416设于竖直装配板300上且位于第十五导轮415的后下方,切割线2的第二端自前向后依次绕过第十一导轮411的下缘及内缘、第十五导轮415的前缘及上缘、第十六导轮416的下缘缠绕于滚筒3下侧。上述结构使切割线2无偏差的缠绕在滚筒3上,从右侧看,滚筒3正转时,滚筒3下侧为切割线释放侧,滚筒3上侧为切割线回线侧;滚筒3反转时,滚筒3上侧为切割线释放侧,滚筒3下侧为切割线释放侧,以实现切割线2的稳定往复传动。
本实施例的切割线2自滚筒3上侧向前依次绕过第十五导轮415下缘、第十二导轮412上缘及前缘、第十三导轮413右缘、第八导轮408右下缘、第六导轮406下缘及左缘及上缘、第七导轮407后缘及右缘及前缘、第一导轮401上缘及左缘及下缘、第二导轮402下缘及右缘、第三导轮403左缘及上缘及右缘、第四导轮404左缘及下缘、第五导轮405下缘及右缘及上缘、第十导轮410前缘及左缘及后缘、第九导轮409上缘及右缘及下缘、第十一导轮411下缘及左缘、第十四导轮414前缘及上缘、第十六导轮416下缘向后缠绕在滚筒3的下侧上。
上述第十五导轮415、第十六导轮416为定位导轮,用于对进出线的位置进行限定;第十二导轮412、第十四导轮414为上下浮动导轮,用于和张力调节机构7配合实现张力调节;第八导轮408、第十一导轮411为转角导轮,用于引导切割线的走向进行90度转角;第七导轮407、第十导轮410为转向导轮,用于引导切割线换向;第三导轮403为张力轮,用于与张力控制机构配合实现张力控制;切割轮第一导轮401、第二导轮402之间形成一切割工位,第四导轮404、第五导轮405之间形成一切割工位,第六导轮406、第八导轮408之间形成一切割工位,第九导轮409、第十一导轮411之间形成一切割工位;八个切割轮第一导轮401、第二导轮402、第四导轮404、第五导轮405、第六导轮406、第八导轮408、第九导轮409、第十一导轮411的中心线位于同一平面内,且八个切割轮分别安装在竖向布置的板件上,以节约安装空间;第三导轮403为张力轮,位于前排切割轮第一导轮401、第二导轮402、第四导轮404、第五导轮405的上方且与该4个切割轮处于同一平面内。
在本实施例中,机架1上设置有能控制滚筒3转动方向及转动速度的驱动机构6。该驱动机构6可以为电机等常规驱动结构,在此不做赘述。
本实施例利用第三导轮403将同一输送方向上的一股切割线2分为两个切割工位,在切割线2启用或换向时,容易存在切割线2各处张紧力不均、切割线2局部张紧力过松或过紧的问题,如果切割线2局部过松就无法满足切割需求,影响切割质量;如果切割线2局部过紧就极易导致切割线2断线。采用本实施例的结构,当切割线2较松时,弹性件5驱使第三导轮403带动切割线2向上移动一定位移,从而使切割线2张紧;当切割线2过紧时,允许第三导轮403在切割线2的拉动下向下移动一定位移;即第三导轮403可随切割线2的松紧上下浮动,实时有效的调节切割线2松紧度,从而维持切割线2各处松紧度均匀,保持稳定的切割力,且避免断线。
本实施例通过导轮组件4引导切割线2走向而将切割线2的不同段间分隔为不同的切割区域,可实现多个物料的同时切割,提高了切割效率。
实施例2:
本实施例与实施例1的区别在于:第七导轮、第十导轮的设置位置不同。
如图5所示,第七导轮407’设于第一导轮401、第六导轮406上方,第七导轮407’的轴心线横向布置且其后边缘与第六导轮406的外边缘相对应、其前边缘与第一导轮401的外边缘相对应;第十导轮410’设于第五导轮405、第九导轮409上方,第十导轮410’的轴心线横向布置且其后边缘与第九导轮409的外边缘相对应、其前边缘与第五导轮405的外边缘相对应。切割线2的第一端自前向后依次绕过第一导轮401外缘、第七导轮407’上缘、第六导轮406外缘、第八导轮408下缘布置,切割线2的第二端自前向后依次绕过第五导轮405外缘、第十导轮410’上缘、第九导轮409外缘、第十一导轮411下缘布置。
当切片机整机的机架构造需要作出相应改变时,可采用上述结构以使整机结构更加紧凑、便于装配。
起点商标作为专业知识产权交易平台,可以帮助大家解决很多问题,如果大家想要了解更多知产交易信息请点击 【在线咨询】或添加微信 【19522093243】与客服一对一沟通,为大家解决相关问题。
此文章来源于网络,如有侵权,请联系删除


