高效耗能抗拉自复位支座的制作方法



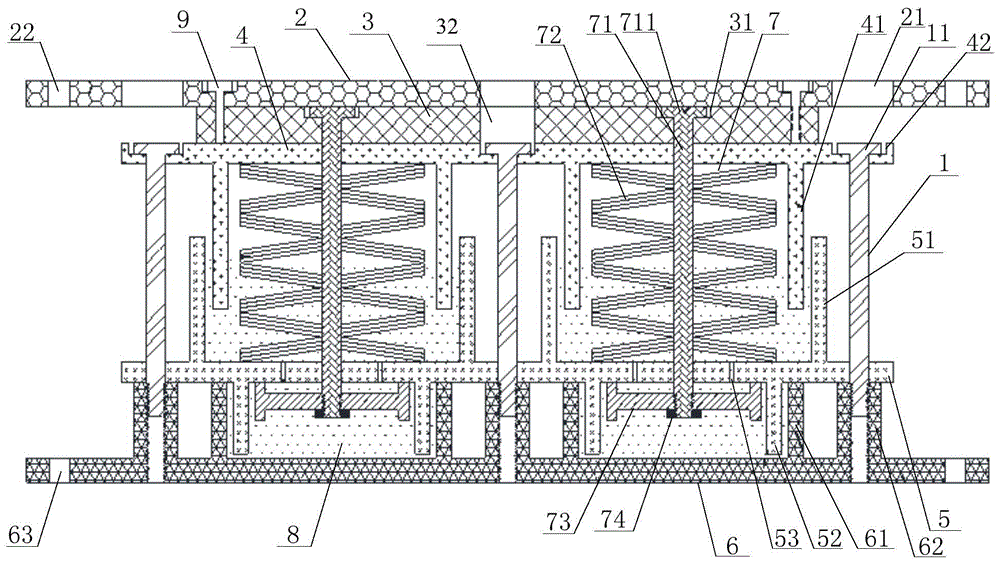
本实用新型涉及隔震/振装置领域,尤其涉及一种高效耗能抗拉自复位支座。
背景技术:
我国处于两大地震带交汇点,使得我国地震频发,并且具有地震烈度高、破坏性大的特性。结构被动隔震减震控制技术始于20世纪70年代,由于其对结构地震响应的出色控制,得到了广大学者的关注,展开了广泛研究并在实际工程当中得到广泛应用。
传统观点认为对结构破坏起决定性作用的是水平地震力,因此之前研究大多集中于水平隔震技术方面,技术成熟,应用广泛。但是,在高烈度区尤其是在发震断层或震中附近,竖向地震分量较大,对建筑物的破坏作用不容忽视。同时随着城市轨道交通的发展,尤其是轨道距离建筑较近时,列车运行会引起建筑结构振动,对建筑物的安全和人们居住舒适度造成影响。建筑附近的机器运行或建筑物内部机器设备的运行,同样会引起建筑物的振动超标,影响结构安全与人的舒适度。因此,竖向隔震/振技术的研究越来越急迫。
竖向隔震/振技术的研发多数是伴随着隔震/振支座的研发进行的。目前提出的竖向隔震支座大多数为厚肉型叠层橡胶支座或者是钢弹簧支座,抗拉能力差。当支座上部结构/装置遭受较大竖向地震作用或在较大水平地震作用下发生摇摆甚至倾覆的时候,支座会进入受拉状态,厚肉型橡胶支座可能出现拉断破坏,钢弹簧支座可能发生提离失效,对支座上部结构或装置的摇摆倾覆效应控制较差。
技术实现要素:
针对上述现有技术中的不足,本实用新型提供一种高效耗能抗拉自复位支座,支座不仅具有竖向隔震/振能力,而且当支座受拉时,具有弹性自复位的抗拉能力,避免支座竖向受拉破坏或提离失效,防止上部结构/装置倾覆。同时,支座还具有高效的、稳定可靠的耗能能力,可进一步保护隔震/振支座上部结构或装置的安全性。
为了实现上述目的,本实用新型提供一种高效耗能抗拉自复位支座,包括:复数个固定限位导杆以及依次排布的上连接板、上固定板、上活动限位耗能导板、下活动限位耗能导板和下限位耗能连接板;所述上固定板、所述上活动限位耗能导板和所述下活动限位耗能导板配合形成至少一支座耗能抗拉自复位核心结构,每一所述支座耗能抗拉自复位核心结构内设置有一耗能抗拉自复位组件;所述上连接板螺接所述上固定板;所述固定限位导杆的第一端形成一第一限位端并对所述上活动限位耗能导板限位,所述固定限位导杆穿设于所述上活动限位耗能导板和所述下活动限位耗能导板,所述固定限位导杆的第二端连接所述下限位耗能连接板;所述耗能抗拉自复位组件连接所述上固定板、所述上活动限位耗能导板和所述下活动限位耗能导板。
优选地,所述支座耗能抗拉自复位核心结构包括同轴设置的至少一第一限位耗能下伸筒、至少一第一限位耗能上伸筒、至少一第二限位耗能下伸筒和至少一第二限位耗能上伸筒;所述第一限位耗能下伸筒形成于所述上活动限位耗能导板邻近所述下活动限位耗能导板的一面,所述第一限位耗能上伸筒形成于所述下活动限位耗能导板邻近所述上活动限位耗能导板的一面,所述第二限位耗能下伸筒形成于所述下活动限位耗能导板邻近所述下限位耗能连接板的一面,所述第二限位耗能上伸筒形成于所述下限位耗能连接板邻近所述下活动限位耗能导板的一面;所述第一限位耗能下伸筒和所述第一限位耗能上伸筒的半径不同,且所述第一限位耗能下伸筒和相邻所述第一限位耗能上伸筒部分层叠;所述第二限位耗能下伸筒和所述第二限位耗能上伸筒的半径不同,且所述第二限位耗能下伸筒和相邻所述第二限位耗能上伸筒层叠或部分层叠。
优选地,所述支座耗能抗拉自复位核心结构还包括若干阻尼孔,下活动限位耗能导板形成所述阻尼孔,所述阻尼孔距离所述第二限位耗能下伸筒中轴线的距离小于所述第二限位耗能下伸筒的内径和所述第二限位耗能上伸筒的内径。
优选地,所述耗能抗拉自复位组件包括弹簧挤压导杆、弹簧、固定耗能闭锁端板和固定螺母;所述上活动限位耗能导板在对应所述第一限位耗能下伸筒的中轴线位置形成第一连接孔;所述下活动限位耗能导板在对应所述第一限位耗能上伸筒的中轴线位置形成第二连接孔;所述上固定板在对应所述第一连接孔的位置形成第一凹槽,所述第一凹槽的底部形成第三连接孔;所述弹簧挤压导杆穿设于所述第三连接孔、所述第一连接孔和所述第二连接孔内,且所述弹簧挤压导杆的第一端形成第二限位端,所述第一凹槽的深度与所述第二限位端配合,所述第二限位端设置于所述第一凹槽内并对所述上固定板限位,所述弹簧挤压导杆的第二端形成第一外螺纹;所述弹簧套设于所述弹簧挤压导杆外并设置于所述上活动限位耗能导板和所述下活动限位耗能导板之间;所述固定耗能闭锁端板中部形成一第四连接孔,所述第四连接孔内壁形成与所述第一外螺纹配合的第一内螺纹,所述固定耗能闭锁端板通过所述第一内螺纹与所述弹簧挤压导杆螺接并设置于所述下活动限位耗能导板邻近所述下限位耗能连接板的一侧;所述固定螺母螺接于所述弹簧挤压导杆的第二端并位于所述固定耗能闭锁端板邻近所述下限位耗能连接板的一侧。
优选地,所述第一限位耗能上伸筒和所述第二限位耗能上伸筒内填充有阻尼液。
优选地,当所述第一限位耗能下伸筒的个数为一时,所述第一限位耗能下伸筒的外径小于或等于所述第一限位耗能上伸筒的内径,所述第一限位耗能下伸筒与所述第一限位耗能上伸筒部分紧密贴合或间隙层叠;当所述第一限位耗能下伸筒的个数为复数时,所述第一限位耗能下伸筒与所述第一限位耗能上伸筒部分交错层叠并紧密贴合或间隙配合。
优选地,所述第二限位耗能下伸筒的长度小于等于所述第二限位耗能上伸筒的长度;当所述第二限位耗能下伸筒的个数为一时,所述第二限位耗能下伸筒的外径小于或等于所述第二限位耗能上伸筒的内径,所述第二限位耗能下伸筒与所述第二限位耗能上伸筒全部或部分紧密贴合或间隙层叠;当所述第二限位耗能下伸筒的个数为复数个时,所述第二限位耗能下伸筒与所述第二限位耗能上伸筒全部或部分交错层叠并紧密贴合或间隙配合。
优选地,所述上活动限位耗能导板在所述支座耗能抗拉自复位核心结构的周围形成第二凹槽,每一所述第二凹槽的底部形成第一限位孔,所述第二凹槽的深度与所述第一限位端的厚度配合;所述下活动限位耗能导板形成与所述第一限位孔位置对应的复数个第二限位孔;所述下限位耗能连接板形成与所述第二限位孔位置对应的复数个螺纹突出部,每一所述螺纹突出部形成位置与所述第二限位孔对应的一螺孔;所述固定限位导杆穿设于所述第一限位孔和所述第二限位孔内,所述第一限位端设置于所述第二凹槽内,所述固定限位导杆的第二端形成与所述螺孔配合的外螺纹并与所述螺孔螺接;所述上连接板形成与所述固定限位导杆位置对应的复数个第一变形安装孔;当存在位置与所述上固定板对应的所述固定限位导杆时,所述上固定板形成与所述固定限位导杆位置对应的若干第二变形安装孔;所述上连接板形成复数个第五连接孔;所述下限位耗能连接板形成复数个第六连接孔。
优选地,所述上连接板邻近所述下限位耗能连接板的一面向下延伸形成一限位防尘筒;所述限位防尘筒罩设于所述上固定板、所述上活动限位耗能导板和所述下活动限位耗能导板的外侧。
优选地,所述第一限位耗能下伸筒形成若干填充孔;所述填充孔与所述下活动限位耗能导板的距离大于所述第一限位耗能上伸筒的长度。
本实用新型由于采用了以上技术方案,使其具有以下有益效果:
1)当高效耗能抗拉自复位支座受压时,支座上部压力推动上连接板、上固定板、上活动限位耗能导板、弹簧挤压导杆、固定耗能闭锁端板和固定螺母同步向下运动。固定耗能闭锁端板与下活动限位耗能导板脱离,上活动限位耗能导板第二凹槽底面与固定限位导杆螺帽底面脱离,弹簧受上活动限位耗能导板和下活动限位耗能导板的挤压变形,为支座提供承载力与恢复力。第一限位耗能下伸筒与第一限位耗能上伸筒之间对阻尼液的剪切挤压作用和固定耗能闭锁端板宽翼缘与第二限位耗能下伸筒之间对阻尼液的剪切挤压作用提供耗能能力,并且阻尼液通过下活动限位耗能导板的阻尼孔进行流通时也会产生阻尼力,提供耗能能力。
当高效耗能抗拉自复位支座受拉时,支座上部拉力拉动上连接板、上固定板、弹簧挤压导杆、下活动限位耗能导板、固定耗能闭锁端板和固定螺母同步向上运动。上固定板与上活动限位耗能导板脱离,下活动限位耗能导板与下限位耗能连接板的螺纹突出部和第二限位耗能上伸筒顶面脱离,弹簧受上活动限位耗能导板和下活动限位耗能导板的挤压变形,为支座提供恢复力和自复位能力,防止支座受拉破坏和提离失效。第一限位耗能下伸筒与第一限位耗能上伸筒之间对阻尼液的剪切挤压作用和第二限位耗能下伸筒与第二限位耗能上伸筒之间对阻尼液的剪切挤压作用提供耗能能力。
可保证高效耗能抗拉自复位支座受压时提供支撑力和隔震/振能力,支座受拉时具有自复位抗拉能力,防止支座受拉破坏和提离失效,无论支座处于受压状态还是受拉状态均具有稳定高效的耗能能力。
2)高效耗能抗拉自复位支座第一限位耗能下伸筒、第一限位耗能上伸筒、第二限位耗能下伸筒和第二限位耗能上伸筒不仅可以对阻尼液的剪切挤压具有耗能能力,而且可以限制支座水平变形。
3)弹簧挤压导杆穿设上固定板、上活动限位耗能导板、弹簧、下活动限位耗能导板、固定耗能闭锁端板和固定螺母,共同组成支座耗能抗拉自复位核心,通过对固定耗能闭锁端板和固定螺母的拧动调节上活动限位耗能导板和下活动限位耗能导板之间的距离对支座施加不同预压力,以满足支座上部不同结构/装置所需预压力。
4)支座耗能抗拉自复位核心通过固定限位导杆与下限位耗能连接板的螺纹突出部固定连接,通过对固定限位导杆的拧动调节使支座耗能抗拉自复位核心与下限位耗能连接板紧密抵接,并且固定限位导杆具有水平限位的作用。
5)上连接板和上固定板分别预留第一变形安装孔和第二变形安装孔,支座受压时,固定限位导杆可通过变形安装孔使支座自由变形,防止构件之间发生碰撞影响支座变形;而且可以通过第一变形安装孔和第二变形安装孔对固定限位导杆进行调节。
6)第一限位耗能下伸筒、第一限位耗能上伸筒、第二限位耗能下伸筒和第二限位耗能上伸筒的数量可以为一层或多层,根据支座实际所需阻尼力、耗能需求和支座水平限位抗侧力确定。
7)支座内部部件之间的摩擦作用可以为支座提供一定耗能能力。
8)支座耗能抗拉自复位核心结构和耗能抗拉自复位组件的数量可以为一套或多套,根据支座用途、支座上部结构/装置特性确定支座所需承载力,通过对支座耗能抗拉自复位核心结构和耗能抗拉自复位组件的单独使用/并联使用/串联使用进行拼装。
9)支座耗能抗拉自复位核心结构和耗能抗拉自复位组件的各部件、上连接板、固定限位导杆和下限位耗能连接板均可拆卸,所有部件均可在工程中进行规格化生产加工,构件主要采用螺纹或高强螺栓进行拼装连接。
10)本实用新型利用高效耗能抗拉自复位支座,不仅使隔震/振支座抗拉能力差的问题得以解决,充分发挥新型高效耗能抗拉自复位支座的抗拉能力和自复位能力,防止支座受拉破坏和提离失效,而且新型支座具有高效的、稳定可靠的耗能能力,进一步提高结构在地震等外部激励作用下的安全性。
附图说明
图1为本实用新型实施例一的高效耗能抗拉自复位支座的结构示意图;
图2为本实用新型实施例一的高效耗能抗拉自复位支座的受压状态图;
图3为本实用新型实施例一的高效耗能抗拉自复位支座的受拉状态图;
图4为本实用新型实施例二的高效耗能抗拉自复位支座的结构示意图;
图5为本实用新型实施例三的高效耗能抗拉自复位支座的受压状态图;
图6为本实用新型实施例四的高效耗能抗拉自复位支座的受拉状态图;
图7为本实用新型实施例五的高效耗能抗拉自复位支座的结构示意图;
图8为本实用新型实施例五的高效耗能抗拉自复位支座的受压状态图;
图9为本实用新型实施例五的高效耗能抗拉自复位支座的受拉状态图。
具体实施方式
下面根据附图1~图9,给出本实用新型的较佳实施例,并予以详细描述,使能更好地理解本实用新型的功能、特点。
请参阅图1,本实用新型实施例一的一种高效耗能抗拉自复位支座,包括:复数个固定限位导杆1以及依次排布的上连接板2、上固定板3、上活动限位耗能导板4、下活动限位耗能导板5和下限位耗能连接板6;上固定板3、上活动限位耗能导板4和下活动限位耗能导板5配合形成两支座耗能抗拉自复位核心结构,每一支座耗能抗拉自复位核心结构内设置有一耗能抗拉自复位组件7;上连接板2螺接上固定板3;固定限位导杆1的第一端形成一第一限位端11并对上活动限位耗能导板4限位,固定限位导杆1穿设于上活动限位耗能导板4和下活动限位耗能导板5,固定限位导杆1的第二端连接下限位耗能连接板6;耗能抗拉自复位组件7连接上固定板3、上活动限位耗能导板4和下活动限位耗能导板5。
每一支座耗能抗拉自复位核心结构包括同轴设置的一第一限位耗能下伸筒41、一第一限位耗能上伸筒51、一第二限位耗能下伸筒52和一第二限位耗能上伸筒61;第一限位耗能下伸筒41形成于上活动限位耗能导板4邻近下活动限位耗能导板5的一面,第一限位耗能上伸筒51形成于下活动限位耗能导板5邻近上活动限位耗能导板4的一面,第二限位耗能下伸筒52形成于下活动限位耗能导板5邻近下限位耗能连接板6的一面,第二限位耗能上伸筒61形成于下限位耗能连接板6邻近下活动限位耗能导板5的一面;第一限位耗能下伸筒41和第一限位耗能上伸筒51的半径不同,且第一限位耗能下伸筒41和相邻第一限位耗能上伸筒51部分层叠;第二限位耗能下伸筒52和第二限位耗能上伸筒61的半径不同,且第二限位耗能下伸筒52和相邻第二限位耗能上伸筒61层叠或部分层叠。
支座耗能抗拉自复位核心结构还包括若干阻尼孔53,下活动限位耗能导板5形成阻尼孔53,阻尼孔53距离第二限位耗能下伸筒52中轴线的距离小于第二限位耗能下伸筒52的内径和第二限位耗能上伸筒61的内径。
本实施例中,耗能抗拉自复位组件7包括弹簧挤压导杆71、弹簧72、固定耗能闭锁端板73和固定螺母74;上活动限位耗能导板4在对应第一限位耗能下伸筒41的中轴线位置形成第一连接孔;下活动限位耗能导板5在对应第一限位耗能上伸筒51的中轴线位置形成第二连接孔;上固定板3在对应第一连接孔的位置形成第一凹槽31,第一凹槽31的底部形成第三连接孔;弹簧挤压导杆71穿设于第三连接孔、第一连接孔和第二连接孔内,且弹簧挤压导杆71的第一端形成一第二限位端711,第一凹槽31的深度与第二限位端711配合,第二限位端711设置于第一凹槽31内并对上固定板3限位,弹簧挤压导杆71的第二端形成第一外螺纹;弹簧72套设于弹簧挤压导杆71外并设置于上活动限位耗能导板4和下活动限位耗能导板5之间;固定耗能闭锁端板73中部形成第四连接孔,第四连接孔内壁形成与第一外螺纹配合的第一内螺纹,固定耗能闭锁端板73通过第一内螺纹与弹簧挤压导杆71螺接并设置于下活动限位耗能导板5邻近下限位耗能连接板6的一侧;固定螺母74螺接于弹簧挤压导杆71的第二端并位于固定耗能闭锁端板73邻近下限位耗能连接板6的一侧。
本实施例中,固定耗能闭锁端板73在支座安装完毕后的初始稳定状态下可以紧密贴合下活动限位耗能导板5底面,也可与下活动限位耗能导板5底面脱离开一定距离,根据实际需要确定。
通过调节上活动限位耗能导板4和下活动限位耗能导板5之间的距离可以对支座施加预压力,以满足支座上部不同结构、装置的需求。
第一限位耗能上伸筒51和第二限位耗能上伸筒61内填充有阻尼液8。阻尼液8可以为粘滞阻尼液、阻尼油等各种类型阻尼材料。
本实施例中,第一限位耗能下伸筒41的外径小于或等于第一限位耗能上伸筒51的内径,第一限位耗能下伸筒41与第一限位耗能上伸筒51部分紧密贴合或间隙层叠,具有限制支座水平变形能力和对阻尼液8的剪切挤压耗能能力。
第二限位耗能下伸筒52的长度小于等于第二限位耗能上伸筒61的长度;第二限位耗能下伸筒52的外径小于或等于第二限位耗能上伸筒61的内径,第二限位耗能下伸筒52与第二限位耗能上伸筒61全部或部分紧密贴合或间隙层叠。
上活动限位耗能导板4在支座耗能抗拉自复位核心结构的周围形成第二凹槽42,每一第二凹槽42的底部形成一第一限位孔,第二凹槽42的深度与第一限位端11的厚度配合;下活动限位耗能导板5形成与第一限位孔位置对应的复数个第二限位孔;下限位耗能连接板6形成与第二限位孔位置对应的复数个螺纹突出部62,每一螺纹突出部62形成位置与第二限位孔对应的一螺孔;固定限位导杆1穿设于第一限位孔和第二限位孔内,第一限位端11设置于第二凹槽42内,固定限位导杆1的第二端形成与螺孔配合的外螺纹并与螺孔螺接;上连接板2形成与固定限位导杆1位置对应的复数个第一变形安装孔21;上固定板3形成与固定限位导杆1位置对应的第二变形安装孔32;上连接板2形成复数个第五连接孔22;下限位耗能连接板6形成复数个第六连接孔63。
通过预留的第一变形安装孔21和第二变形安装孔32,可以对固定限位导杆1进行安装与调节。
固定耗能闭锁端板73与弹簧挤压导杆71通过螺纹固定连接,通过固定耗能闭锁端板73的上下拧动调节可以为支座提供预压力,并且可以使耗能抗拉自复位组件7和支座耗能抗拉自复位核心结构成为一个整体便于支座的组合安装。
下活动限位耗能导板5的下底面与第二限位耗能上伸筒61和螺纹突出部62顶面抵接,固定限位导杆1穿过上活动限位耗能导板4和下活动限位耗能导板5与螺纹突出部62固定连接,通过对固定限位导杆1拧动调节以保证耗能抗拉自复位组件7和支座耗能抗拉自复位核心结构与下限位耗能连接板6的牢靠连接;弹簧挤压导杆71的第二限位端711底面与第一凹槽31底面抵接,第二限位端711顶面与上连接板2底面抵接,上连接板2和上固定板3通过固定螺栓9固定连接,支座运动变形过程中保证上连接板2、上固定板3和上活动限位耗能导板4这三个部件共同运动。
请参阅图2,当高效耗能抗拉自复位支座受压时,支座上部压力推动上连接板2、上固定板3、上活动限位耗能导板4、弹簧挤压导杆71、固定耗能闭锁端板73和固定螺母74同步向下运动。固定耗能闭锁端板73与下活动限位耗能导板5脱离,第二凹槽42底面与第一限位端11底面脱离,弹簧72受上活动限位耗能导板4和下活动限位耗能导板5的挤压变形,为支座提供承载力与恢复力。第一限位耗能下伸筒41与第一限位耗能上伸筒51之间对阻尼液8的剪切挤压作用和固定耗能闭锁端板73宽翼缘与第二限位耗能下伸筒52之间对阻尼液8的剪切挤压作用提供耗能能力,并且阻尼液8通过下活动限位耗能导板5的阻尼孔53进行流通时也会产生阻尼力,提供耗能能力。
请参阅图3,当高效耗能抗拉自复位支座受拉时,支座上部拉力拉动上连接板2、上固定板3、弹簧挤压导杆71、下活动限位耗能导板5、固定耗能闭锁端板73和固定螺母74同步向上运动。上固定板3与上活动限位耗能导板4脱离,下活动限位耗能导板5与螺纹突出部62和第二限位耗能上伸筒61顶面脱离,弹簧72受上活动限位耗能导板4和下活动限位耗能导板5的挤压变形,为支座提供恢复力和自复位能力,防止支座受拉破坏和提离失效。第一限位耗能下伸筒41与第一限位耗能上伸筒51之间对阻尼液8的剪切挤压作用和第二限位耗能上伸筒61与第二限位耗能下伸筒52之间对阻尼液8的剪切挤压作用提供耗能能力。
请参阅图1~图3,高效耗能抗拉自复位支座的第一限位耗能下伸筒41、第一限位耗能上伸筒51、第二限位耗能下伸筒52和第二限位耗能上伸筒61不仅可以对阻尼液8的剪切挤压具有耗能能力,而且可以限制支座水平变形。上述外伸筒体重叠部分,可紧密贴合或留有一定缝隙。
支座在变形过程中,内部各部件之间的摩擦作用可以起到耗能能力。
耗能抗拉自复位组件7中弹簧72可为碟形弹簧和/或波形弹簧和/或螺旋弹簧,通过对不同形式的弹簧72进行叠合/组合获得抗拉弹性自复位核心系统所需力学性能。
通过对耗能抗拉自复位组件7中固定耗能闭锁端板73和固定螺母74的拧动调节,可以改变上活动限位耗能导板4和下活动限位耗能导板5之间的距离以对支座施加不同预压力,以满足支座上部不同结构/装置所需预压力。
耗能抗拉自复位组件7通过固定限位导杆1与下限位耗能连接板6的螺纹突出部62固定连接,通过上连接板2和上固定板3的预留第一变形安装孔21和第二变形安装孔32对固定限位导杆1进行调节,确保支座耗能抗拉自复位核心与下限位耗能连接板6的可靠连接,同时固定限位导杆1具有限制支座水平变形的功能。
本实施例中,支座可以布置二套支座耗能抗拉自复位核心结构和耗能抗拉自复位组件7,可以理解的是,可以根据支座用途和所需承载力计算所需支座耗能抗拉自复位核心结构数量,通过支座耗能抗拉自复位核心结构的并联/串联等不同组合方式获得支座所需承载力和变形量。
本实用新型实施例一的一种高效耗能抗拉自复位支座,通过对支座的耗能抗拉自复位核心构造设计,可以实现支座无论是在受压状态还是受拉状态,支座中弹簧构件均为受压变形从而防止支座受拉破坏和提离失效,支座受压状态下弹簧为支座提供承载力与恢复力,支座受拉状态下弹簧为支座提供抗拉自复位恢复力,并且在支座运动过程中,支座中的阻尼耗能构造可以为支座提供稳定高效的耗能能力,进一步提高上部结构或装置的安全性。
请参阅图4,本实用新型实施例二的一种高效耗能抗拉自复位支座,其结构与实施例一基本相同,其区别在于:第一限位耗能上伸筒51和第二限位耗能上伸筒61的个数为二。可以理解的是,第一限位耗能下伸筒41数量、第一限位耗能上伸筒51、第二限位耗能下伸筒52和第二限位耗能上伸筒61的数量均可以根据支座实际所需的阻尼力、耗能需求和水平限位抗侧力进行修改。
第一限位耗能下伸筒41与第一限位耗能上伸筒51部分交错层叠并紧密贴合或间隙配合。
第二限位耗能下伸筒52与第二限位耗能上伸筒61全部或部分交错层叠并紧密贴合或间隙配合。
请参阅图5,本实用新型实施例三的一种高效耗能抗拉自复位支座,其结构与实施例一基本相同,其区别在于:上连接板2邻近下限位耗能连接板6的一面向下延伸形成一限位防尘筒23;限位防尘筒23罩设于上固定板3、上活动限位耗能导板4和下活动限位耗能导板5的外侧。
限位防尘筒23不仅可以具有限制支座水平变形能力,而且可以防止外部灰尘杂物等进入到支座内部,影响阻尼液性能和支座内部各部件的运动变形。
请参阅图6,本实用新型实施例四的一种高效耗能抗拉自复位支座,其结构与实施例一基本相同,其区别在于:第一限位耗能下伸筒41形成若干填充孔411;填充孔411与下活动限位耗能导板5的距离大于第一限位耗能上伸筒51的长度。填充孔411,用于阻尼液8的注入等。
请参阅图7~图9,本实用新型实施例五的一种高效耗能抗拉自复位支座,其结构与实施例一基本相同,其区别在于:上活动限位耗能导板4、下活动限位耗能导板5和下限位耗能连接板6配合形成一支座耗能抗拉自复位核心结构。且仅设置一耗能抗拉自复位组件7。其他情况应用时,可通过对整体支座的数量和组合方式进行调整与设计,获得所需承载力。
以上结合附图实施例对本实用新型进行了详细说明,本领域中普通技术人员可根据上述说明对本实用新型做出种种变化例。因而,实施例中的某些细节不应构成对本实用新型的限定,本实用新型将以所附权利要求书界定的范围作为本实用新型的保护范围。
起点商标作为专业知识产权交易平台,可以帮助大家解决很多问题,如果大家想要了解更多知产交易信息请点击 【在线咨询】或添加微信 【19522093243】与客服一对一沟通,为大家解决相关问题。
此文章来源于网络,如有侵权,请联系删除


