智能移动商砼站的制作方法



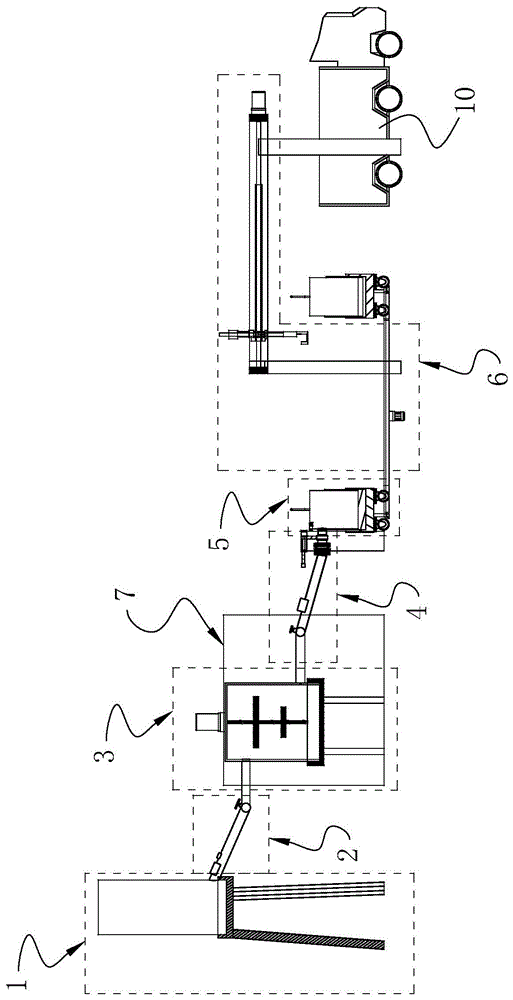
本申请涉及商砼站的技术领域,尤其是涉及智能移动商砼站。
背景技术:
混凝土主要是由水泥、黄砂、石子、粉煤灰、矿粉、外加剂、水等材料组成的一种人造建筑材料,被普遍应用于建筑施工当中,是我国一般建筑主体构成的主要组成部分。
目前我国主要生产商砼的方式是建立固定式搅拌站,一般固定式搅拌站至少包括一套及以上固定式搅拌设备,原材料筒仓及堆场,以及配套运送的运输车辆。传统搅拌站对商砼质量的控制,包括人为选定与供应客户要求相匹配的商砼生产配比,还包括商砼自搅拌站出厂至搅拌车运输到工地过程中对时间、温度、湿度的人工监测和控制,专业领域称之为对坍落度损失的控制。
现有技术中,固定式搅拌站生产的商品混凝土一般是通过车辆运输至施工现场,由于混凝土加水搅拌后在一段时间内会凝固,所以运输的距离会受到限制,一般不超过35km,否则运输时间过长将会导致混凝土在运输罐车内发生凝固,这也就限制了固定式搅拌站的选址。
同时,由于固定式搅拌站多为敞开式设置,生产过程中会产生扬尘和噪音污染,同样也限制了其选址,其选址不能离居民区过近。
技术实现要素:
为了便于选定搅拌站的地址,本申请提供智能移动商砼站。
本申请提供的智能移动商砼站,采用如下的技术方案:
智能移动商砼站,包括:
控制单元,配置为用于根据设定程序和/或临时输入的指令数据,输出控制信号;
存料单元,包括多个存料罐,分别用于存放多种生产原料;
混料单元,包括与所述控制单元控制连接的搅拌装置,用于混合自所述存料单元输送至所述混料单元内的生产原料;
第一出料单元,连通设置于所述存料单元和混料单元之间,且与控制单元控制连接,受控于控制单元的控制信号,控制多个存料罐与所述搅拌装置进料口之间的连通状态以及生产原料的输送状态;
存储单元,包括多个运输罐,分别用于存储所述混料单元混合并输出的不同种类的混合料;
第二出料单元,连通设置于所述混料单元和存储单元之间,且与控制单元控制连接,受控于控制单元的控制信号,控制多个运输罐与所述搅拌装置出料口之间的连通状态以及混合料的输送状态;
出料单元,与所述控制单元控制连接,受控于所述控制单元的控制信号将装有设定种类混合料的运输罐移送至装载工具上。
通过采用上述技术方案,控制单元控制第一出料单元将存料罐内的生产原料运送至混料单元内,并控制搅拌装置对多种生产原料进行充分的搅拌。控制单元将生产原料搅拌形成的混合料通过第二出料单元运送至运输罐内,而后出料单元在控制单元的控制下将运输罐移送至装载工具上。
在此过程中,完成自动搅拌多种生产原料,并将搅拌好的混合料装于运输罐内,便于运输,且搅拌过程中未添加水,运输距离不受限制,同时密闭设置降低粉尘的污染,实现便于搅拌站选择更加合适的场地进行作业的目的。
优选的,所述搅拌装置包括搅拌罐以及设置于所述搅拌罐内的搅拌器,所述搅拌器与所述控制单元控制连接,受控于控制单元输出的控制信号对生产原料进行搅拌。
通过采用上述技术方案,多种生产原料在搅拌罐内,由控制单元控制的搅拌器对搅拌罐内的多种生产原料进行充分地搅拌,实现将生产原料混合成混合料的目的。
优选的,所述第一出料单元包括:
第一输料管,配置为多根且各第一输料管的一端分别与所述存料罐的出料口相连通;
第一选通阀,与所述控制单元控制连接,其物料输入端分别与多根第一输料管远离各存料罐的一端相连通,物料输出端与所述搅拌装置的入料口相连通,受控于所述控制单元输出的控制信号,选通不同的存料罐与搅拌装置;
第一出料驱动组件,包括多个第一驱动件,分别设置于多根所述第一输料管上且与所述控制单元控制连接,受控于所述控制单元输出的控制信号,驱动各所述第一输料管中的生产原料自存料罐运动至搅拌装置。
通过采用上述技术方案,控制单元控制第一选通阀的输入端与第一输料管的连通状态,同时控制连通的第一输料管上的第一出料驱动件工作,从而控制多种生产原料依次输送至搅拌装置内,通过第一选通阀连通第一输料管的时间不同,实现搅拌装置混合不同配比的混凝土。
优选的,所述第二出料单元包括:
第二输料管,配置为多根且各第二输料管的一端分别与所述运输罐的进料口相连通;
第二选通阀,与所述控制单元控制连接,其物料输出端分别与多根第二输料管远离各运输罐的一端相连通,物料输入端与所述搅拌装置的出料口相连通,受控于所述控制单元输出的控制信号,选通不同的运输罐与搅拌装置;
第二出料驱动组件,包括多个第二驱动件,分别设置于多根所述第二输料管上且与所述控制单元控制连接,受控于所述控制单元输出的控制信号,驱动各所述第二输料管中的混合料自搅拌装置运动至运输罐。
通过采用上述技术方案,控制单元控制第二选通阀的输入端与第二输料管的连通状态,同时控制连通的第二输料管上的第二出料驱动件工作,从而控制多种不同配比的混合料输送至不同的运输罐内,便于出料单元将不同配比的混合料运送至多个相对应的装载工具上。
优选的,所述出料单元包括:
移送组件,包括与所述控制单元控制连接的自移动搭载平台和用于承载所述自移动搭载平台的运输轨道,用于将运输罐转移至设定位置;
起吊组件,包括起吊件以及与所述控制单元控制连接的起吊驱动件,用于将放置于设定位置处的运输罐转移至装载工具上。
通过采用上述技术方案,自移动搭载平台将装有混合料的运输罐沿运输轨道运送至设定位置,便于起吊组件将运输罐移送至相对应的装载工具上。
优选的,所述自移动搭载平台的数量为多个且分别对应设置于各运输罐的下方,其上设置有用于承接运输罐的安装架,受控于控制器的控制信号,将选定的运输罐沿所述运输轨道转移至设定位置。
通过采用上述技术方案,不同配比的混合料对应于不同的运输罐,不同的运输罐通过不同的自移动搭载平台进行运送,并通过安装架稳定运输罐的位置,提高运输罐的安全性。
优选的,所述运输轨道于运输罐与第二输料管相接处,和所述设定位置之间形成循环运输回路。
通过采用上述技术方案,当装载工具到达设定位置时,将空运输罐通过起吊组件移送至运输轨道的回程上,从而形成循环。
优选的,各所述第一输料管上设置有用于测定所述第一输料管内生产原料流量的计量装置;
所述计量装置与所述控制单元信号连接,输出采集到的生产原料流量信号;
所述控制单元接收并响应于所述生产原料流量信号控制第一选通阀和/或第一驱动件的动作。
通过采用上述技术方案,计量装置对第一输料管内流过的生产原料进行计量,并根据计量装置输出至控制单元的生产原料流量信号控制第一选通阀导通的第一输料管,从而便于搅拌装置搅拌不同配比的混合料。
优选的,所述自移动搭载平台上设置有称重装置,所述称重装置与所述控制单元信号连接,采集并输出反映所述运输罐重量的称重信号;
所述控制单元接收并响应于所述称重信号控制第二选通阀和/或第二驱动件的动作。
通过采用上述技术方案,称重装置对运输罐内装有的混合料进行称重,并根据称重装置输出至控制单元的称重信号控制第二选通阀导通的第二输料管,从而便于在运输罐装满混合料时关断第二选通阀,降低混合料的浪费。
优选的,所述运输罐上设置有用于标志其身份编码的标识件;
所述运输罐与第二输料管相接处设置有用于识别运输罐身份编码的第一识别装置;
所述设定位置处设置有用于识别装载工具身份编码的第二识别装置;
所述第一识别装置、第二识别装置均与控制单元信号连接,所述控制单元接收第一识别装置、第二识别装置输出的识别信号,输出控制信号控制与所述装载工具相对应的运输罐移送至设置位置。
通过采用上述技术方案,当装载工具到达后,通过第二识别装置对装载工具的身份进行识别,便于控制单元控制相对应于装载工具的运输罐动作。控制单元通过第一识别装置识别运输罐的身份,即运输罐内装有的混合料的配比信息。
综上所述,本申请包括以下至少一种有益技术效果:
1.通过控制单元、存料单元、混料单元、第一出料单元、存储单元、第二出料单元和出料单元的设置,控制单元控制第一出料单元将存料罐内的生产原料运送至混料单元内,并控制搅拌装置对多种生产原料进行充分的搅拌。控制单元将生产原料搅拌形成的混合料通过第二出料单元运送至运输罐内,而后出料单元在控制单元的控制下将运输罐移送至装载工具上;
2.进一步地,通过运输轨道形成循环运输回路,当装载工具到达设定位置时,将空运输罐通过起吊组件移送至运输轨道的回程上,从而形成循环;
3.进一步地,通过计量装置的设置,控制单元根据计量装置输出的生产原料流量信号控制第一选通阀导通的第一输料管,从而便于搅拌装置搅拌不同配比的混合料;
通过称重装置的设置,控制单元根据称重装置输出的称重信号控制第二选通阀导通的第二输料管,从而便于在运输罐装满混合料时关断第二选通阀,降低混合料的浪费。
附图说明
图1是本申请实施例的主视图。
图2是本申请实施例的整体结构示意图。
图3是本申请为显示混料单元、第二出料单元和存储单元的整体结构示意图。
图4是为显示混料单元内部结构的剖视图。
图5是图3中a部分的放大示意图。
图6是为显示出料单元和装载工具的整体结构示意图。
图7是为显示运输罐和自移动搭载平台的结构示意图。
附图标记说明:1、存料单元;11、存料罐;12、支撑架;2、第一出料单元;21、第一输料管;22、第一选通阀;23、第一出料驱动组件;231、第一驱动件;24、计量装置;3、混料单元;31、搅拌装置;311、搅拌罐;312、搅拌器;3121、搅拌驱动件;3122、搅拌轴;3123、搅拌叶片;4、第二出料单元;41、第二输料管;42、第二选通阀;43、第二出料驱动组件;431、第二驱动件;44、移管组件;441、夹持件;442、移管驱动件;5、存储单元;51、运输罐;511、吊耳;512、标识件;6、出料单元;61、移送组件;611、自移动搭载平台;6111、安装架;6112、运输驱动件;6113、移动轮;612、运输轨道;62、称重装置;63、起吊组件;631、起吊件;632、起吊驱动件;633、伸缩驱动件;7、控制单元;8、第一识别装置;9、第二识别装置;10、装载工具。
具体实施方式
以下结合附图1-7对本申请作进一步详细说明。
本申请实施例公开智能移动商砼站。参照图1和图2,包括存料单元1、第一出料单元2、混料单元3、第二出料单元4、存储单元5、出料单元6和控制单元7。
参照图2,存料单元1包括多个存料罐11,分别用于存放多种不同或者相同的生产原料,本申请实施例中设置有三个存料罐11,存料罐11靠近地面的一端还设置有用于支撑存料罐11的支撑架12,便于输出存料罐11内底部的生产原料。
使用频率较多的生产原料可以存放于多个存料罐11内,便于及时送料。
第一出料单元2连通设置于存料单元1和混料单元3之间,且与控制单元7控制连接,受控于控制单元7的控制信号,控制多个存料罐11与混料单元3之间的连通状态以及生产原料的输送状态。
其中,第一出料单元2包括第一输料管21、第一选通阀22和第一出料驱动组件23。
详述的,第一输料管21配置为三根且各第一输料管21的一端分别与存料罐11的出料口相连通。
本申请实施例中第一选通阀22设置为四通阀,与控制单元7控制连接。其物料输入端设置为三通选择端,分别与三根第一输料管21远离各存料罐11的一端相连通,物料输出端与混料单元3的入料口相连通,受控于控制单元7输出的控制信号,选通不同的存料罐11与混料单元3。
控制单元7控制第一选通阀22选通所需生产原料相对应的阀门,使得所需生产原料能够在相对应的第一出料驱动组件23的驱动下将生产原料运送至混料单元3内。
第一出料驱动组件23包括三个第一驱动件231,分别设置于三根第一输料管21上且与控制单元7控制连接,受控于控制单元7输出的控制信号,驱动各第一输料管21中的生产原料自存料罐11运动至混料单元3。
第一驱动件231可以设置为混凝土搅拌站常用的螺旋叶片式送料装置。
各第一输料管21上设置有用于测定第一输料管21内生产原料流量的计量装置24;本申请实施例中,计量装置24设置为多普勒流量计。计量装置24与控制单元7信号连接,输出采集到的生产原料流量信号;控制单元7接收并响应于生产原料流量信号控制第一选通阀22和/或第一驱动件231的动作。
第一驱动件231受控于控制单元7以进行运输生产原料时,同时触发计量装置24对第一输料管21的生产原料进行计量,同时输出生产原料流量信号至控制单元7,当生产原料流量信号达到预设的阈值时,控制单元7控制第一驱动件231停止运送生产原料,并将第一选通阀22对应的阀门关断。
参照图3和图4,混料单元3包括与控制单元7控制连接的搅拌装置31,用于混合自存料单元1输送至混料单元3内的生产原料。
搅拌装置31包括搅拌罐311以及设置于搅拌罐311内的搅拌器312,搅拌器312与控制单元7控制连接,受控于控制单元7输出的控制信号对生产原料进行搅拌。
搅拌器312包括搅拌驱动件3121、搅拌轴3122和搅拌叶片3123,搅拌驱动件3121设置在搅拌罐311的顶端,本申请实施例中搅拌驱动件3121可以设置为转动电机。搅拌驱动件3121的输出轴贯穿搅拌罐311并固定连接于搅拌轴3122的一端,搅拌轴3122悬置于搅拌罐311内,搅拌叶片3123固定于搅拌轴3122的侧壁,搅拌叶片3123可以设置有多片,多片搅拌叶片3123沿搅拌轴3122呈圆周阵列分布,且根据搅拌需求可以将叶片设置成不同的形状。
搅拌驱动件3121可以在生产原料开始输送进入搅拌罐311时同步驱动,便于在生产原料进入搅拌罐311时被搅拌,实现更加充分搅拌生产原料的目的。
第二出料单元4连通设置于混料单元3和存储单元5之间,且与控制单元7控制连接,受控于控制单元7的控制信号,控制存储单元5与搅拌装置31出料口之间的连通状态以及混合料的输送状态。
其中,第二出料单元4包括第二输料管41、第二选通阀42和第二出料驱动组件43。
详述的,第二输料管41配置为三根且各第二输料管41的一端分别与存储单元5相连通。
本申请实施例中第二选通阀42设置为四通阀,与控制单元7控制连接。其物料输出端设置为三通选择端,分别与三根第二输料管41远离存储单元5的一端相连通,物料输入端与搅拌装置31的出料口相连通,受控于控制单元7输出的控制信号,选通存储单元5与搅拌装置31。
第二出料驱动组件43包括三个第二驱动件431,分别设置于三根第二输料管41上且与控制单元7控制连接,受控于控制单元7输出的控制信号,驱动各第二输料管41中的混合料自搅拌装置31运动至存储单元5。
第二驱动件431可以与第一驱动件231相同设置。
参照图3,存储单元5包括多个运输罐51,本申请中设置为三个,分别用于存储混料单元3混合并输出的不同种类,即不同配比的混合料。运输罐51的顶端还固定有呈倒u型设置的吊耳511。
控制单元7控制第二选通阀42选通存储相对应混合料的相对应的阀门,使得混合料能够在相对应的第二驱动件431的驱动下将混合料运送至相对应的运输罐51内。
参照图3和图5,运输罐51靠近第二输料管41的一侧还设置有移管组件44,移管组件44包括夹持件441和移管驱动件442,此时第二输料管41靠近运输罐51的一端设置为能够伸缩的伸缩端,夹持件441设置为能够夹持伸缩端的u型夹或者o型夹,始终保持夹持伸缩端的状态。
夹持件441位于伸缩端的上方,夹持件441远离伸缩端的一侧固定连接于移管驱动件442的输出端,移管驱动件442设置为伸缩电机,移管驱动件442受控于控制单元7的控制信号。
当第二输料管41开始移送混合料时,移管驱动件442驱动夹持件441朝向靠近运输罐51的方向移动,直至伸缩端伸入运输罐51的入料口;当运输罐51装满混合料时,移管驱动件442驱动夹持件441方向移动,使得伸缩端远离运输罐51。
参照图6和图7,出料单元6与控制单元7控制连接,受控于控制单元7的控制信号将装有设定种类混合料的运输罐51移送至装载工具10上,本申请实施例中将装载工具10设置为运输车。其中,出料单元6包括移送组件61和起吊组件2。
详述的,移送组件61包括与控制单元7控制连接的自移动搭载平台611和用于承载自移动搭载平台611的运输轨道612,用于将运输罐51转移至设定位置。
自移动搭载平台611的数量为多个且分别对应设置于各运输罐51的下方,本申请实施例中设置为三个,其上设置有用于承接运输罐51的安装架6111本申请实施例中安装架6111呈环状设置。
自移动搭载平台611靠近运输轨道612的一侧还设置有运输驱动件6112,本申请实例中设置为相互配合的皮带和转动轮,以及皮带设置的驱动件,皮带的驱动件受控于控制器的控制信号,将选定的运输罐51沿运输轨道612转移至设定位置,设定位置为运输轨道612靠近起吊装置的一端。
自移动搭载平台611靠近运输轨道612的一侧还设置有移动轮6113用于支撑导向运输罐51的移动,便于减轻运输轨道612的承载力,以延长运输轨道612的使用寿命。
运输轨道612于运输罐51与第二输料管41相接处,和设定位置之间形成循环运输回路。满载混合料的运输罐51通过去程到达设定位置;当装载工具10到达设定位置时,将装载的空运输罐51通过起吊组件63移送至运输轨道612的回程。
自移动搭载平台611上设置有称重装置62,称重装置62用于称量运输罐51的重量,由于满载混合料的运输罐51重量通常在10吨等较重的重量,本申请实施例中称重装置62可以设置为能够称量10吨以上重量的吨称重器。
称重装置62与控制单元7信号连接,采集并输出反映运输罐51重量的称重信号;控制单元7接收并响应于称重信号控制第二选通阀42和/或第二驱动件431的动作。
第二驱动件431受控于控制单元7以进行运输混合料时,同时触发称重装置62对运输罐51进行称重,同时输出称重信号至控制单元7,当称重信号达到预设的阈值时,控制单元7控制第二驱动件431停止运送混合料,并将第二选通阀42对应的阀门关断。
起吊组件63包括起吊件631以及与控制单元7控制连接的起吊驱动件632,用于将放置于设定位置处的运输罐51转移至装载工具10上。
起吊件631设置为吊钩,通过钩接运输罐51顶端的吊耳511,以移送运输罐51。起吊件631远离地面的一端设置有伸缩驱动件633,本申请实施例中可以设置为伸缩电机,用于驱动起吊件631在竖直方向的伸缩,以便吊起运输罐51,或者放下运输罐51。
起吊驱动件632设置为伸缩气缸,用于驱动起吊件631和伸缩驱动件633在水平方向的移动,以便将设定位置的满载运输罐51移送至装载工具10,或者将装载工具10上的空载运输罐51移送至设定位置。
控制单元7,配置为用于根据设定程序和/或临时输入的指令数据,输出控制信号。控制单元7可以设置为控制中心,使得本申请提出的商砼站可以通过自动控制完成搅拌,可以由人工控制控制中心的操作台面以进行搅拌。
控制单元7包括存储模块,用于存储不同客户所需的不同配比的混合料,同时存储不通存料罐11内存储的生产原料类型以及重量。
进一步地,运输罐51上设置有用于标志其身份编码的标识件512;运输罐51与第二输料管41相接处设置有用于识别运输罐51身份编码的第一识别装置8。标识件512和第一识别装置8,可以设置为相互匹配的图形码和识别件,图形码可以是二维码、条形码和数字编码等中的一种或者多种。
参照图5和图6,设定位置处设置有用于识别装载工具10身份编码的第二识别装置9,本申请中第二识别装置9设置为能够识别装载工具10车牌号码的识别器。
第一识别装置8、第二识别装置9均与控制单元7信号连接,控制单元7接收第一识别装置8、第二识别装置9输出的识别信号,输出控制信号控制与装载工具10相对应的运输罐51移送至设置位置。
存储模块内还存储不同客户对应的装载工具10的车牌号码。
控制单元7内还设有比对模块,分别接收第一识别装置8、第二识别装置9输出的识别信号,而后将两个识别信号进行比对,使得装载工具10达到设定位置时,控制单元7控制与装载工具10相对应的运输罐51移送至设定位置,并由起吊组件63,移送至装载工具10上。
本申请实施例智能移动商砼站的实施原理为:控制单元7控制第一选通阀22选通不同的存料罐11,第一出料单元2中相对应的第一驱动件231将存料罐11内的生产原料运送至搅拌罐311内,并控制搅拌器312对多种生产原料进行充分的搅拌。控制单元7选通相对应搅拌罐311内配比的运输罐51,并通过第二驱动件431将生产原料搅拌形成的混合料运送至运输罐51内。而后第二识别装置9识别装载工具10的车牌号码,比对模块比对装有与车牌号码相对应配比的混合料的运输罐51,先将空载的运输罐51通过起吊组件63移送至运输轨道612的回程,同时控制自移动搭载平台611将运输罐51沿运输轨道612的去程移送至设定位置,起吊组件63在控制单元7的控制下将运输罐51移送至装载工具10上。
以上均为本申请的较佳实施例,并非依此限制本申请的保护范围,故:凡依本申请的结构、形状、原理所做的等效变化,均应涵盖于本申请的保护范围之内。
起点商标作为专业知识产权交易平台,可以帮助大家解决很多问题,如果大家想要了解更多知产交易信息请点击 【在线咨询】或添加微信 【19522093243】与客服一对一沟通,为大家解决相关问题。
此文章来源于网络,如有侵权,请联系删除


