一种具有高抗菌消臭效果的复合功能纤维材料制备方法与流程



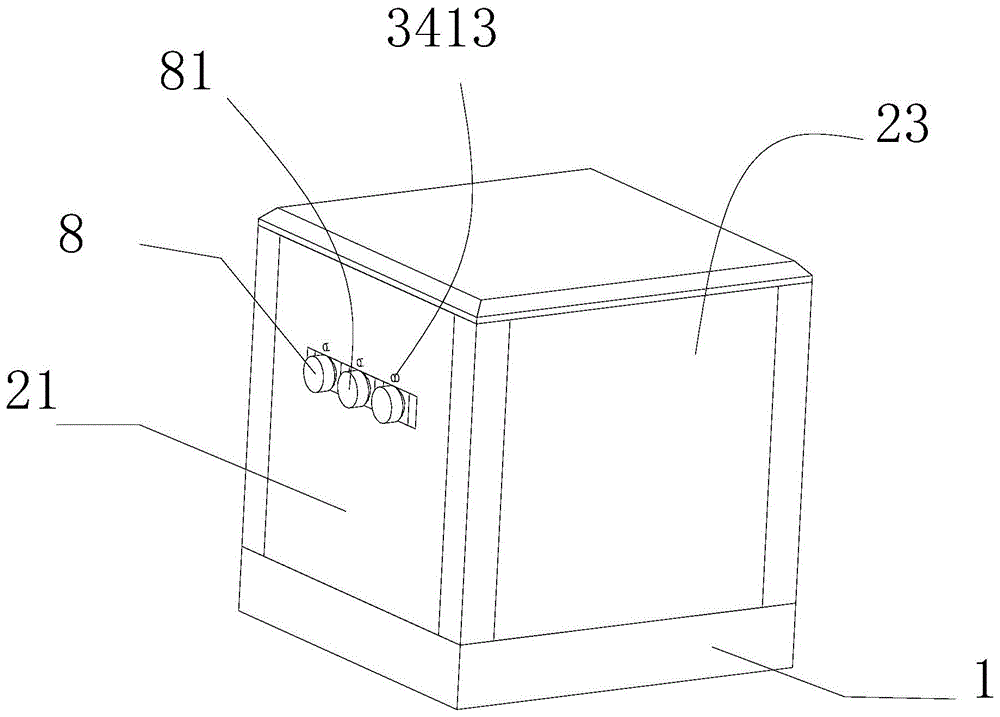
本发明属于纤维制造技术领域,尤其是涉及一种具有高抗菌消臭效果的复合功能纤维材料制备方法。
背景技术:
随着科学技术的不断发展,人们生活质量的不断提高,人们对于纺织品的需求已不仅仅停留在好看和舒适方面,原有的单一的纺织材料已不能满足人们的需求。
抗菌材料能抑制纤维上微生物的生长、繁殖,从而起到保护纤维不受微生物的侵袭,防止其变色和发霉,更能在与皮肤接触时,对人完全无毒、无刺激,并且对人体不产生致敏现象。抗菌化纤及织物的加工主要采用以下两种方法:后整理和纤维改性法。后整理法以有机抗菌剂为主,如季胺盐型抗菌剂。由于该法是将抗菌有效成分附着在纤维和织物表面,制得的抗菌产品耐洗涤、持久性差。因此这种方法逐渐被纤维改性法取代。纤维改性法主要是将抗菌剂添加到成纤高聚物中,得到永久性的抗菌纤维。
目前纳米纤维的制取一般采用静电纺丝法,市面现有的静电纺丝仪多采用一个注射器搭配针头作为原料供应装置,金属滚筒作为接受装置,这种装置存在的弊端如下:(1)、注射器的容量较小,完成大幅面的纤维材料需频繁更换注射器(2)注射器的安装固定比较繁琐,造成机器停机等待、(3)单针式注射器效率低下,制成的纤维材料纹路不均匀,质量差。
技术实现要素:
本发明为了克服现有技术的不足,提供一种具有高抗菌消臭效果的复合功能纤维材料及其多针头式无缝换料制备方法。
为了实现上述目的,本发明采用以下技术方案:一种具有高抗菌消臭效果的复合功能纤维材料制备方法,包括以下步骤:
(1)配置三种负载不同功能性物质的纺丝溶液a、纺丝溶液b和纺丝溶液c,其中:配置纺丝溶液a:将生物相容的合成高分子溶解在溶剂a中,其中高分子质量浓度为5wt%~35wt%,后加入相对于高分子质量的0.5wt%~5wt%的抗生素类药物,搅拌至溶液透明均一,即得到纺丝溶液a;配置纺丝溶液b:将水溶性合成高分子或天然高分子溶解在水中,其中高分子质量浓度为6wt%~20wt%,后加入相对于高分子质量的0.1wt%~2wt%的交联剂,后再加入相对于高分子质量的1wt%~20wt%的酶类物质,搅拌至溶液透明均一,即得到纺丝溶液b;配置纺丝溶液c:将生物相容的合成高分子溶解在溶剂a中,其中高分子质量浓度为配置5wt%~35wt%,后加入相对于高分子质量的0.5wt%~30wt%的激素类药物,搅拌至溶液透明均一即得到纺丝溶液c;
(2)将上述纺丝溶液a、纺丝溶液b、纺丝溶液c分别装载到三针头静电纺丝装置的针头a、针头b、针头c中进行多针头静电纺丝,纤维直径分布为200~1500nm;得到功能纳米纤维创面修复生物敷料。
其中,步骤(2)中静电纺丝装置包括底座、设于所述底座的保护箱体、设于所述箱体的前面板、后面板、左面板及右面板、固定连接于所述前面板的夹持机构、与所述夹持机构固定连接的进料机构、固定连接于所述保护箱体的稳压直流电源、与所述进料机构连接的出料机构、固定连接于所述底座的接收机构和用于驱动所述出料机构与所述接收机构的运转驱动机构;所述夹持机构包括固定连接于所述前面板的封装盒、固定连接于所述封装盒的矫正块、由所属矫正块组成的导孔、滑动连接于所述导孔的若干交换管、设于所述交换管上的封盖、设于所述交换管上的出口阀、设于所述出口阀上的第一出液孔、与所述出口阀滑动连接的回弹阀、连接所述回弹阀与出口阀的回弹弹簧、设于所述回弹阀上的第二出液孔、滑动连接于所述封装盒的若干夹持块、固定连接所述夹持块的上滑块、设于所述封装盒的第一滑槽、与所述第一滑槽连通的第二滑槽、滑动连接于所述第二滑槽的十字滑杆、与所述滑杆固定连接的压盖、固定连接于所述压盖的第一滑块、可转动连接于所述第一滑块与所述上滑块的连接杆、设于所述夹持块下方的第三滑槽、固定连接于所述夹持块的齿条、可转动连接于所述第三滑槽的辅助齿轮、滑动连接于所述封装盒的套管、可转动连接于所述套管的调节齿轮、套设于所述调节齿轮与所述辅助齿轮的第一皮带、固定连接于所述封装盒且滑动连接于所述压盖的平衡管、设于所述平衡管内部的平衡弹簧、设于所述平衡管底部的若干平衡孔、设于所述第一滑块的卡槽、设于所述封装盒的第三滑槽、滑动连接于所述卡槽及第三滑槽的三角卡片、固定连接于所述三角卡片与所述第三滑槽的复位弹簧、滑动连接于所述封装盒的复位杆、固定连接于所述复位杆的推块、固定连接于所述复位杆的压块和固定连接于所述压块的复位按钮;所述套管外侧有螺纹;所述复位杆套设有弹簧;所述平衡孔中有一半是单向阀;装有液体的交换管沿着由矫正块形成的导孔滑动进入封装盒,沿着导孔向后移动,交换管底部触碰到推动压盖并推动压盖后移,带动十字滑杆与第一滑块沿着第二滑槽逐渐后移,连接杆带动上滑块沿着第一滑槽从两侧相中间滑动,夹持块逐渐与交换管贴合并夹紧,同时带动齿条沿着第三滑槽朝对侧移动,辅助齿轮被带动旋转,通过皮带带动调节齿轮旋转,在螺纹的作用下套管上升,带动回弹阀上升,回弹弹簧被压缩,第一出液孔与第二出液孔对齐,交换管中的液体从出液孔流出;同时第一滑块顶开三角卡片,复位弹簧先压缩后释放,三角卡片沿着第三滑槽进入卡槽并发出“啪嗒”声,至此,交换管被固定不再移动;此时,压盖后移挤压平衡弹簧,平衡管中气压变大,平衡孔全部打开直至平衡管内外气压达到平衡;当需要更换交换管时,按压复位按钮,推动压块后移,带动复位杆后移,推块后移,沿着斜面推动三角卡片,复位弹簧压缩,三角卡片从第三滑槽中滑出,平衡弹簧压力释放,推动压盖往前移动,平衡管中气压变小,平衡孔中的非单向阀从外界缓慢吸入气流补充压力,第一滑块往前移动,夹持块向两侧移动,交换管被缓慢推出;导孔为交换管的移动提供了精确的导向作用,使交换管能够顺利的抵达压盖;设计了专用交换管替代了注射器,容量更大,安装固定简单可靠,并且可以实现自动打开送料,更换方便快捷,减少了人员接触,使药品不易被污染,减少了更换次数,满足长时间的稳定供料需求;夹持块通过压盖联动,实现自动夹紧并通过三角卡片锁定,并且提供一定的声音反馈;更换交换管时,可一键解锁,使交换管缓慢弹出;平衡管和平衡孔中单向阀的存在,使交换管在进入时,平衡孔全部打开,气压迅速达到平衡,完成交换管的固定,而在弹出时,只有部分平衡孔打开,放缓了气压平衡的速度,为交换管的弹出提供明显的阻尼感,避免交换管快速弹出破碎。
所述进料机构包括设于所述封装盒底部的漏液孔、与所述漏液孔连接的竖管、固定连接于所述竖管底部的分流管、设于所述分流管的分流孔、与所述分流管固定连接与前面板的压力管、固定连接于所述压力管内的驱动电机、与所述驱动电机连接的凸轮、设于所述凸轮的工作弧面、固定连接于所述压力管内的法兰、设于所述法兰上的若干通孔、设于所述通孔内的单向阀、设于所述单向阀的阀盖、设于所述单向阀的阀口、连接所述单向阀的阀簧、设于所述法兰前方的缓冲仓、固定连接于所述法兰的隔板、设于隔板两侧的压力舱a与压力舱b、滑动连接于所述压力舱的活塞a与活塞b、固定连接于所述活塞后侧的压力杆、固定连接于所述隔板且套设于所述压力杆的支撑架、套设于所述压力杆的压力弹簧和设于所述缓冲仓底部的出液孔;驱动电机转动,带动凸轮转动,凸轮的弧面通过推动压力杆使活塞进行前后交替式运动,活塞a在压力弹簧的作用下向后运动时,压力舱a中产生负压,位于压力舱a上方的分流孔打开,压力舱a前方的单向阀关闭,液体通过漏液孔-竖管-分流管-分流孔进入压力舱a,同时,活塞b在凸轮的推动下向前运动,压力舱b压力变大,上方的分流孔关闭,前方的单向阀打开,将储存在压力舱b中的液体活塞将液体推进缓冲仓,最后从出液孔推出;当活塞b运动到尽头时,压力舱a开始进行出液动作,压力舱b开始进行进液动作,以此循环交替;压力舱a与压力舱b循环交替工作,可以将交换管中的液体抽出,并为缓冲仓提供源源不断的液体压力,系统高效的满足长时间液体供应的要求,并且两仓交替使用,可以有足够的时间替换交换管而不会使液体断供,实现无缝衔接工作;缓冲仓可以允许部分气泡的存在,少量不可避免的气泡可以寄存在缓冲仓上部,而不会从底部的出液孔流出,造成断流。
所述出料机构包括与所述出液孔连接的出液管、与所述出液管连接的移动台、固定连接于所述底座的立柱、固定连接于所述立柱的三角梁、固定连接于三角梁且滑动连接于所述移动台的滑动轴、可转动连接于所述三角梁且可转动连接于所述移动台的螺纹杆、设于所述移动台的若干储液槽、固定连接于所述移动台的若干纺丝针和连接所述稳压电源于移动台的正极电源线;所述接收机构包括固定连接于所述底座的三脚架、可转动连接于所述三脚架的接收筒、固定连接于所述接收筒一端的第一伞齿轮、可转动连接于所述右侧板的齿轮轴、固定连接于所述齿轮轴的第二伞齿轮、与所述齿轮轴可转动连接的定轴套、由所述第一伞齿轮与第二伞齿轮形成的v形槽、可转动连接于所述右侧板的若干定位螺钉、套设于所述定位螺钉的转动齿、可转动连接于所述转动齿的调节旋钮、固定连接于所述底座的工作电机、与所述工作电机连接的长轴、套设于所述螺纹杆的驱动套环、套设于所述驱动套环与所述长轴的第二皮带、套设于所述v形槽与所述长轴的第三皮带、固定连接于所述右侧板的调节轴、可转动连接于所述调节轴的调节辊和与所述稳压电源与所述三脚架固定连接的负极线;所述稳压电源的电场力提供的纺丝射流速度与移动台的移动速度比的变化范围为(1,+∞);所述v形槽与所述驱动套环之间的传动比变化范围为(1,+∞);所述接收筒的线速度与所述纺丝射流速度保持同步;从出液孔流出的液体经由出液管到达移动台中的储液槽中,并从纺丝针尖端处流出,纺丝针连接稳压电源的正极,处于高电位,接收筒处于低点位,在纺丝针与接收筒形成的强电场作用下,液滴在纺丝针尖端处形成泰勒锥,最终形成射流,喷射向接收筒。工作电机带动长轴转动,第二皮带带动驱动套环转动,第三皮带带动第一伞齿轮和第二伞齿轮转动,接收筒转动,并将由射流冷却形成的纤维缠绕在接收筒上;当需要改变纤维的致密度时,调节旋钮转动,调节稳压电源的输出电压,同时带动转动齿转动,定位螺钉推动第二伞齿轮靠近第一伞齿轮,v形槽与第三皮带的传动直径变化,从而使传动比发生变化,接收筒的转速发生变化;阵列式纺丝针最多允许三种液体九支纺丝针同时工作,相比于传统的单针式,极大地提高了纺丝的效率和速度,并且配合射流速度和移动台的速度变化,可以实现多样化的更加复杂的多种材料的纤维编织,稳压电源的电势差越大,纺丝针与接收筒之间的电场力越大,纺丝射流速度越大,与移动台的移动速度比越大,相邻纺丝的缠绕间距越小,克服了传统纺丝设备针头间距造成的纤维间距无法进一步缩小的难题,使纤维间距更加致密,从而生产出多种规格的纤维材料,使静电纺丝仪的适应性更加广泛;同时,v形槽可同步调节接收筒的转速,保证纺丝射流速度变化的同时,改变接收速度,不会导致纤维的断裂;调节辊可以保证第三皮带时刻处于张紧状态。
所述步骤(1)中的溶剂a为n,n-二甲基甲酰胺、丙酮、氯仿、乙醇中的一种或者两种。
所述步骤(1)中配置纺丝溶液a中的生物相容的合成高分子为聚乳酸pla、聚己内酯pcl、聚氨酯pu或聚乳酸-乙醇酸共聚物plga。
所述步骤(1)中配置纺丝溶液b中的水溶性合成高分子为聚乙烯醇pva,天然高分子为羧甲基壳聚糖、丝胶、海藻酸钠中的一种或两种,交联剂为50%戊二醛或京尼平。
所述步骤(1)中配置纺丝溶液c中的生物相容的合成高分子为聚乳酸pla、聚己内酯pcl、聚氨酯pu或聚乳酸-乙醇酸共聚物plga。
所述步骤(2)中的静电纺丝具体为:三针头成等边三角形分布,针头之间的距离为5~20厘米,静电纺丝装置的工作电压为15~30千伏,以铝箔为阴极接收产物,接收距离为10~30厘米。
所述前后左右面板均为透明具有保温效果的塑料面板;保温面板可以防止射流骤冷引起的硬化和气流引起的射流扰动,透明面板可以实时观察机器工作情况。
综上所述,本发明具有以下优点:,本发明通过多针头纺丝工艺,每个针头中含有的高分子溶液纺丝液中都负载一种具有不同作用的功能性物质,多针头同时纺丝得到单层的多种高分子负载抗菌消臭性物质的复合纤维膜,三针头纺丝的引入可以有效的解决不同溶解性的功能物质不能同时溶解到一种纺丝溶液中的难题;具有高抗菌消臭效果的复合功能纤维材料的制备可以满足人们对抗菌面料的日益需求;本法,本发明通过夹持机构,实现了交换管的快速安装固定,并且可以自动导流提高了效率,配合进料机构可以自动将交换管中的液体抽出,并为纺丝针提供源源不断的液体压力,满足长时间液体供应的要求,并且两仓交替使用,可以有足够的时间替换交换管而不会使液体断供,实现无缝衔接长续航工作;阵列式纺丝针最多允许三种液体九支纺丝针同时工作,相比于传统的单针式,极大地提高了纺丝的效率和速度,并且配合射流速度和移动台的速度变化,可以实现多样化的更加复杂的多种材料的纤维编织,稳压电源的电势差越大,纺丝针与接收筒之间的电场力越大,纺丝射流速度越大,与移动台的移动速度比越大,相邻纺丝的缠绕间距越小,纤维更加致密,从而高质量生产出多种规格的纤维材料,使静电纺丝仪的适应性更加广泛。
附图说明
图1为本发明的结构示意图。
图2为本发明的左视图。
图3为本发明隐藏掉左面板和右面板的结构示意图。
图4为本发明隐藏掉右面板的结构示意图。
图5为本发明的正视图。
图6为图5沿a-a的剖视图。
图7为图6中a处的放大图。
图8为图5沿b-b的剖视图。
图9为图8中b处的放大图。
图10为图5沿c-c的剖视图。
图11为图10中c处的放大图。
图12为本发明夹持机构的爆炸示意图。
图13为图12中d处的放大图。
图14为本发明交换管的结构示意图。
图15为本发明中进料机构的爆炸示意图。
图16为本发明中第一伞齿轮部分的结构示意图。
图17为本发明中移动台的上视图。
图18为图17沿d-d的剖视图。
图19为本发明中沿e-e的剖视图。
图20为本发明中纺丝射流速度与移动台移动速度关系曲线图。
具体实施方式
实施例1
一种具有高抗菌消臭效果的复合功能纤维材料制备方法,包括以下步骤:
(1)配置三种负载不同功能性物质的纺丝溶液a、纺丝溶液b和纺丝溶液c,其中:配置纺丝溶液a:将生物相容的合成高分子溶解在溶剂a中,其中高分子质量浓度为5wt%~35wt%,后加入相对于高分子质量的0.5wt%~5wt%的抗生素类药物,搅拌至溶液透明均一,即得到纺丝溶液a;配置纺丝溶液b:将水溶性合成高分子或天然高分子溶解在水中,其中高分子质量浓度为6wt%~20wt%,后加入相对于高分子质量的0.1wt%~2wt%的交联剂,后再加入相对于高分子质量的1wt%~20wt%的酶类物质,搅拌至溶液透明均一,即得到纺丝溶液b;配置纺丝溶液c:将生物相容的合成高分子溶解在溶剂a中,其中高分子质量浓度为配置5wt%~35wt%,后加入相对于高分子质量的0.5wt%~30wt%的激素类药物,搅拌至溶液透明均一即得到纺丝溶液c;
(2)将上述纺丝溶液a、纺丝溶液b、纺丝溶液c分别装载到三针头静电纺丝装置的针头a、针头b、针头c中进行多针头静电纺丝,纤维直径分布为200~1500nm;得到功能纳米纤维创面修复生物敷料。
其中,步骤(2)中静电纺丝装置包括底座1、保护箱体2、前面板21、后面板22、左面板23、右面板24、夹持机构3、进料机构4、稳压直流电源5、出料机构6、接收机构7;所述保护箱体2设于所述底座1上、所述前面板21、后面板22、左面板23及右面板24固定连接于所述箱体的;所述夹持机构3固定连接于所述前面板21;所述进料机构4与所述夹持机构3固定连接;所述稳压直流电源5固定连接于所述保护箱体2;所述接收机构7与所述进料机构4连接的出料机构6且固定连接于所述底座1;所述夹持机构3包括封装盒31、矫正块32、导孔321、交换管8、封盖81、出口阀82、第一出液孔83、回弹阀84、回弹弹簧85、第二出液孔86、夹持块33、上滑块331、第一滑槽311、第二滑槽312、十字滑杆341、压盖34、第一滑块342、连接杆343、第三滑槽313、齿条332、辅助齿轮35、套管351、调节齿轮352、第一皮带353、平衡管344、平衡弹簧345、平衡孔346、卡槽347、第三滑槽313、三角卡片348、复位弹簧349、复位杆3410、推块3411、复位按钮3413;所述封装盒31固定连接于所述前面板21;所述矫正块32固定连接于所述封装盒31;所述导孔321由所属矫正块32组成;所述交换管8共三只且滑动连接于所述导孔321;所述封盖81设于所述交换管8上;所述出口阀82设于所述交换管8上;所述第一出液孔431383设于所述出口阀82上;所述回弹阀84与所述出口阀82滑动连接;所述回弹弹簧85连接所述回弹阀84与出口阀82;所述第二出液孔431386设于所述回弹阀84上;所述夹持块33共六枚滑动连接于所述封装盒31;所述上滑块331固定连接所述夹持块33;所述第一滑槽311设于所述封装盒31;所述第二滑槽312与所述第一滑槽311连通;所述十字滑杆341滑动连接于所述第二滑槽312;所述压盖34与所述滑杆固定连接;所述第一滑块342固定连接于所述压盖34;所述连接杆343可转动连接于所述第一滑块342与所述上滑块331;所述第三滑槽313设于所述夹持块33下方;所述齿条332固定连接于所述夹持块33;所述辅助齿轮35可转动连接于所述第三滑槽313;所述套管351滑动连接于所述封装盒31;所述调节齿轮352可转动连接于所述套管351;所述第一皮带353套设于所述调节齿轮352与所述辅助齿轮35;所述平衡管344固定连接于所述封装盒31且滑动连接于所述压盖34;所述平衡弹簧345设于所述平衡管344内部;所述平衡孔346共4个设于所述平衡管344底部;所述卡槽347设于所述第一滑块342上;所述第三滑槽313设于所述封装盒31上;所述三角卡片348滑动连接于所述卡槽347及第三滑槽313;所述复位弹簧349固定连接于所述三角卡片348与所述第三滑槽313;所述复位杆3410滑动连接于所述封装盒31;所述推块3411固定连接于所述复位杆3410;所述压块3412固定连接于所述复位杆3410;所述复位按钮3413固定连接于所述压块3412;所述套管351外侧有螺纹;所述复位杆3410套设有弹簧;所述平衡孔346中有一半是单向阀436;装有液体的交换管8沿着由矫正块32形成的导孔321滑动进入封装盒31,沿着导孔321向后移动,交换管8底部触碰到推动压盖34并推动压盖34后移,带动十字滑杆341与第一滑块342沿着第二滑槽312逐渐后移,连接杆343带动上滑块331沿着第一滑槽311从两侧相中间滑动,夹持块33逐渐与交换管8贴合并夹紧,同时带动齿条332沿着第三滑槽313朝对侧移动,辅助齿轮35被带动旋转,通过皮带带动调节齿轮352旋转,在螺纹的作用下套管351上升,带动回弹阀84上升,回弹弹簧85被压缩,第一出液孔83与第二出液孔86对齐,交换管8中的液体从出液孔4313流出;同时第一滑块342顶开三角卡片348,复位弹簧349先压缩后释放,三角卡片348沿着第三滑槽313进入卡槽347并发出“啪嗒”声,至此,交换管8被固定不再移动;此时,压盖34后移挤压平衡弹簧345,平衡管344中气压变大,平衡孔346全部打开直至平衡管344内外气压达到平衡;当需要更换交换管8时,按压复位按钮3413,推动压块3412后移,带动复位杆3410后移,推块3411后移,沿着斜面推动三角卡片348,复位弹簧349压缩,三角卡片348从第三滑槽313中滑出,平衡弹簧345压力释放,推动压盖34往前移动,平衡管344中气压变小,平衡孔346中的非单向阀436从外界缓慢吸入气流补充压力,第一滑块342往前移动,夹持块33向两侧移动,交换管8被缓慢推出;导孔321为交换管8的移动提供了精确的导向作用,使交换管8能够顺利的抵达压盖34;设计了专用交换管8替代了注射器,容量更大,安装固定简单可靠,并且可以实现自动打开送料,更换方便快捷,减少了人员接触,使药品不易被污染,减少了更换次数,满足长时间的稳定供料需求;夹持块33通过压盖34联动,实现自动夹紧并通过三角卡片348锁定,并且提供一定的声音反馈;更换交换管8时,可一键解锁,使交换管8缓慢弹出;平衡管344和平衡孔346中单向阀436的存在,使交换管8在进入时,平衡孔346全部打开,气压迅速达到平衡,完成交换管8的固定,而在弹出时,只有部分平衡孔346打开,放缓了气压平衡的速度,为交换管8的弹出提供明显的阻尼感,避免交换管8快速弹出破碎。
所述进料机构4包括漏液孔41、竖管42、分流管421、分流孔422、压力管43、驱动电机431、凸轮432、工作弧面433、法兰434、通孔435、单向阀436、缓冲仓437、隔板438、压力舱a4381、压力舱b4382、活塞439a、活塞439b、压力杆4310、支撑架4311、压力弹簧4312、出液孔4313、阀盖4361、阀口4362、阀簧4363;所述漏液孔41设于所述封装盒31底部;所述竖管42与所述漏液孔41连接;所述分流管421固定连接于所述竖管42底部;所述分流孔422设于所述分流管421上;所述压力管43与所述分流管421固定连接与前面板21;所述驱动电机431固定连接于所述压力管43内;所述凸轮432与所述驱动电机431连接;所述工作弧面433设于所述凸轮432;所述法兰434固定连接于所述压力管43内;所述通孔435共两枚设于所述法兰434上;所述单向阀436设于所述通孔435内;所述阀盖4361设于所述单向阀上;所述阀口4362设于所述单向阀侧壁;所述阀簧4363连接所述单向阀底部;所述缓冲仓437设于所述法兰434前方;所述隔板438固定连接于所述法兰434;所述压力舱a4381与压力舱b4382设于隔板438两侧;所述活塞439a与活塞439b滑动连接于所述压力舱;所述压力杆4310固定连接于所述活塞439后侧;所述支撑架4311固定连接于所述隔板438且套设于所述压力杆4310;所述压力弹簧4312套设于所述压力杆4310;出液孔4313设于所述缓冲仓437底部;驱动电机431转动,带动凸轮432转动,凸轮432的弧面通过推动压力杆4310使活塞439进行前后交替式运动,活塞439a在压力弹簧4312的作用下向后运动时,压力舱a4381中产生负压,位于压力舱a4381上方的分流孔422打开,压力舱a4381前方的单向阀436关闭,液体通过漏液孔41-竖管42-分流管421-分流孔422进入压力舱a4381,同时,活塞439b在凸轮432的推动下向前运动,压力舱b4382压力变大,上方的分流孔422关闭,前方的单向阀436打开,将储存在压力舱b4382中的液体活塞439将液体推进缓冲仓437,最后从出液孔4313推出;当活塞439b运动到尽头时,压力舱a4381开始进行出液动作,压力舱b4382开始进行进液动作,以此循环交替;压力舱a4381与压力舱b4382循环交替工作,可以将交换管8中的液体抽出,并为缓冲仓437提供源源不断的液体压力,系统高效的满足长时间液体供应的要求,并且两仓交替使用,可以有足够的时间替换交换管8而不会使液体断供,实现无缝衔接工作;缓冲仓437可以允许部分气泡的存在,少量不可避免的气泡可以寄存在缓冲仓437上部,而不会从底部的出液孔4313流出,造成断流。
所述出料机构6包括出液管61、移动台62、立柱63、三角梁64、滑动轴65、螺纹杆66、储液槽67、纺丝针68、正极电源线69;所述出液管61与所述出液孔4313连接;所述移动台62与所述出液管61连接;所述立柱63固定连接于所述底座1;所述三角梁64固定连接于所述立柱63;所述滑动轴65固定连接于三角梁64且滑动连接于所述移动台62;所述螺纹杆66可转动连接于所述三角梁64且可转动连接于所述移动台62;所述储液槽67共三个且设于所述移动台62;所述纺丝针68共九枚固定连接于所述移动台62;所述正极电源线69连接所述稳压电源于移动台62;所述接收机构7包括三脚架71、接收筒72、第一伞齿轮721、齿轮轴722、第二伞齿轮723、定轴套724、v形槽725、定位螺钉726、转动齿727、调节旋钮728、工作电机73、长轴731、驱动套环732、第二皮带733、第三皮带734、调节轴735、调节辊736、负极线74;所述三脚架71固定连接于所述底座1;所述接收筒72可转动连接于所述三脚架71;所述第一伞齿轮721固定连接于所述接收筒72一端;所述齿轮轴722可转动连接于所述右侧板;所述第二伞齿轮723固定连接于所述齿轮轴722;所述定轴套724与所述齿轮轴722可转动连接;所述v形槽725由所述第一伞齿轮721与第二伞齿轮723形成;所述定位螺钉726共三枚且可转动连接于所述右侧板;所述转动齿727套设于所述定位螺钉726;所述调节旋钮728可转动连接于所述转动齿727;所述工作电机73固定连接于所述底座1;所述长轴731与所述工作电机73连接;所述驱动套环732套设于所述螺纹杆66;所述第二皮带733套设于所述驱动套环732与所述长轴731;所述第三皮带734套设于所述v形槽725与所述长轴731;所述调节轴735固定连接于所述右侧板;所述调节辊736可转动连接于所述调节轴735;所述负极线74与所述稳压电源与所述三脚架71固定连接;所述稳压电源的电场力提供的纺丝射流速度与移动台62的移动速度比的变化范围为(1,+∞);所述v形槽725与所述驱动套环732之间的传动比变化范围为(1,+∞);所述接收筒72的线速度与所述纺丝射流速度保持同步;从出液孔4313流出的液体经由出液管61到达移动台62中的储液槽67中,并从纺丝针68尖端处流出,纺丝针68连接稳压电源的正极,处于高电位,接收筒72处于低点位,在纺丝针68与接收筒72形成的强电场作用下,液滴在纺丝针68尖端处形成泰勒锥,最终形成射流,喷射向接收筒72。工作电机73带动长轴731转动,第二皮带733带动驱动套环732转动,第三皮带734带动第一伞齿轮721和第二伞齿轮723转动,接收筒72转动,并将由射流冷却形成的纤维缠绕在接收筒72上;当需要改变纤维的致密度时,调节旋钮728转动,调节稳压电源的输出电压,同时带动转动齿727转动,定位螺钉726推动第二伞齿轮723靠近第一伞齿轮721,v形槽725与第三皮带734的传动直径变化,从而使传动比发生变化,接收筒72的转速发生变化;阵列式纺丝针68最多允许三种液体九支纺丝针68同时工作,相比于传统的单针式,极大地提高了纺丝的效率和速度,并且配合射流速度和移动台62的速度变化,可以实现多样化的更加复杂的多种材料的纤维编织,稳压电源的电势差越大,纺丝针68与接收筒72之间的电场力越大,纺丝射流速度越大,与移动台62的移动速度比越大,相邻纺丝的缠绕间距越小,纤维更加致密,从而生产出多种规格的纤维材料,使静电纺丝仪的适应性更加广泛;同时,v形槽725可同步调节接收筒72的转速,保证纺丝射流速度变化的同时,改变接收速度,不会导致纤维的断裂;调节辊736可以保证第三皮带734时刻处于张紧状态。
所述步骤(1)中的溶剂a为n,n-二甲基甲酰胺、丙酮、氯仿、乙醇中的一种或者两种。
所述步骤(1)中配置纺丝溶液a中的生物相容的合成高分子为聚乳酸pla、聚己内酯pcl、聚氨酯pu或聚乳酸-乙醇酸共聚物plga。
所述步骤(1)中配置纺丝溶液b中的水溶性合成高分子为聚乙烯醇pva,天然高分子为羧甲基壳聚糖、丝胶、海藻酸钠中的一种或两种,交联剂为50%戊二醛或京尼平。
所述步骤(1)中配置纺丝溶液c中的生物相容的合成高分子为聚乳酸pla、聚己内酯pcl、聚氨酯pu或聚乳酸-乙醇酸共聚物plga。
所述步骤(2)中的静电纺丝具体为:三针头成等边三角形分布,针头之间的距离为5~20厘米,静电纺丝装置的工作电压为15~30千伏,以铝箔为阴极接收产物,接收距离为10~30厘米。
所述前后左右面板24均为透明具有保温效果的塑料面板。
具体工作过程如下:
将配置好的溶液a、溶液b、溶液c分别装到交换管8中,并装入夹持机构3被自动固定,液体流入进料机构4,并由压力活塞439送出压力管43送达移动台62的储液槽67,在纺丝针68尖端形成射流喷出,并收集在收集筒上。
实施例2
一种具有高抗菌消臭效果的复合功能纤维材料制备方法,包括以下步骤:
(1)配置三种负载不同功能性物质的纺丝溶液a、纺丝溶液b和纺丝溶液c,其中:配置纺丝溶液a:将生物相容的合成高分子溶解在溶剂a中,其中高分子质量浓度为20wt%,后加入相对于高分子质量的2.5wt%的抗生素类药物,搅拌至溶液透明均一,即得到纺丝溶液a;配置纺丝溶液b:将水溶性合成高分子或天然高分子溶解在水中,其中高分子质量浓度为13wt%,后加入相对于高分子质量的1wt%的交联剂,后再加入相对于高分子质量的10wt%的酶类物质,搅拌至溶液透明均一,即得到纺丝溶液b;配置纺丝溶液c:将生物相容的合成高分子溶解在溶剂a中,其中高分子质量浓度为配置20wt%,后加入相对于高分子质量的1530wt%的激素类药物,搅拌至溶液透明均一即得到纺丝溶液c;
(2)将上述纺丝溶液a、纺丝溶液b、纺丝溶液c分别装载到三针头静电纺丝装置的针头a、针头b、针头c中进行多针头静电纺丝,纤维直径分布为800nm;得到功能纳米纤维创面修复生物敷料。
步骤(2)静电纺丝仪的结构与实施例1相同,不再赘述。
实施例3
一种具有高抗菌消臭效果的复合功能纤维材料制备方法,包括以下步骤:
(1)配置三种负载不同功能性物质的纺丝溶液a、纺丝溶液b和纺丝溶液c,其中:配置纺丝溶液a:将生物相容的合成高分子溶解在溶剂a中,其中高分子质量浓度为35wt%,后加入相对于高分子质量的5wt%的抗生素类药物,搅拌至溶液透明均一,即得到纺丝溶液a;配置纺丝溶液b:将水溶性合成高分子或天然高分子溶解在水中,其中高分子质量浓度为20wt%,后加入相对于高分子质量的2wt%的交联剂,后再加入相对于高分子质量的20wt%的酶类物质,搅拌至溶液透明均一,即得到纺丝溶液b;配置纺丝溶液c:将生物相容的合成高分子溶解在溶剂a中,其中高分子质量浓度为配置35wt%,后加入相对于高分子质量的30wt%的激素类药物,搅拌至溶液透明均一即得到纺丝溶液c;
(2)将上述纺丝溶液a、纺丝溶液b、纺丝溶液c分别装载到三针头静电纺丝装置的针头a、针头b、针头c中进行多针头静电纺丝,纤维直径分布为1500nm;得到功能纳米纤维创面修复生物敷料。
步骤(2)中静电纺丝仪的结构与实施例1相同,不再赘述。
起点商标作为专业知识产权交易平台,可以帮助大家解决很多问题,如果大家想要了解更多知产交易信息请点击 【在线咨询】或添加微信 【19522093243】与客服一对一沟通,为大家解决相关问题。
此文章来源于网络,如有侵权,请联系删除


