自动打钉系统及其打钉方法与流程



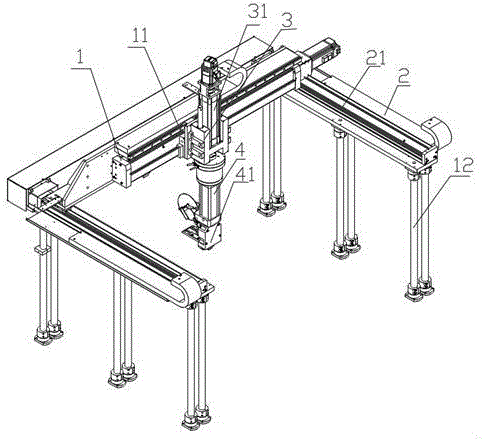
本发明涉及一种自动打钉系统及其打钉方法。
背景技术:
随着生活水平的提高,汽车在人们生活中已经成为了不可或缺的交通工具。汽车的底护板在组装时,需要将金属板和底护板用钉子组装到一起,现有的打钉方式一般都是采用人工手持式操作打钉,采用排钉形式,一排数量约为100pcs;人工打钉劳动强度大,且打钉位置由于不同的操作人员的经验程度会导致精确度和打钉质量不稳定,同时,也会存在一定的安全隐患,整个打钉操作可以说费时费力,效率低下。
技术实现要素:
为了解决现有技术的不足,本发明提供了一种自动打钉系统及其打钉方法。
本发明的目的通过以下技术方案来实现:
自动打钉系统,包括一组平行机架及架设于所述平行机架上的第二移动机架,所述机架上设置有滑轨,所述第二移动机架的两端设置于所述滑轨上,所述第二移动机架上设置有第二滑轨,所述第二滑轨上垂直向下设置有自动打钉枪组件。
优选地,所述自动打钉枪组件通过连接滑块设置于所述第二滑轨上,所述连接滑块带动所述自动打钉枪组件在所述第二滑轨上移动。
优选地,所述自动打钉枪组件包括自动打钉枪、设置于自动打钉枪上方的驱动机构,所述驱动机构包括直线气缸及设置于直线气缸上方的电机,所述电机驱动所述自动打钉枪进行周向运动。
优选地,所述自动打钉枪包括设置于直线气缸正下方的打钉盒,所述打钉盒的一侧设置有进料机构,所述进料机构包括用于放置排钉的卷料轴,所述卷料轴的一端通过连杆与所述直线气缸连接,所述打钉盒的下部与其垂直设置有一底板,所述底板的一端延伸置于所述打钉盒内,所述底板上设置有压料板,所述排钉的一端置于所述压料板与底板之间进入打钉盒。
优选地,所述打钉盒的进料端还设置有拉料凸轮,所述拉料凸轮的外侧通过弹性连杆与打钉盒连接,所述拉料凸轮上设置有压料胶带。
优选地,所述拉料凸轮的一侧设置有压轮,所述压轮的一侧通过连接杆与拉料凸轮上端连接,所述压轮压紧所述压料胶带的一端,并将所述压料胶带贴紧进料的所述排钉。
优选地,所示直线气缸为二级伸缩气缸,所述打钉盒与所述二级伸缩气缸的外气缸轴连接,所述打钉盒内设置有排钉折弯块,所述排钉折弯块的上端与二级伸缩气缸的内气缸轴连接,所述排钉折弯块呈门形,所述排钉折弯块设置于所述底板的上方。
优选地,所述自动打钉枪下方设置有排钉检测组件,所述排钉检测组件包括用于排钉数量检测的传感器及与所述传感器电性连接的报警机构。
优选地,以上所述的自动打钉系统的打钉方法,包括如下步骤:
s1、将待打钉产品置于打钉操作台面,所述操作台面上设置有与所述自动打钉枪配合的钉槽;第二移动支架带动自动打钉枪组件移动至待打钉产品上方;
s2、电机工作,驱动自动打钉枪旋转至待打钉位置方向;
s3、二级伸缩气缸工作,外气缸轴带动打钉盒下压与待打钉产品接触;此时,拉料凸轮的一侧受到压轮拉动带动其运转,从而使得卷料轴上排钉向打钉盒内前进;
s4、二级伸缩气缸继续工作,内气缸轴带动打钉枪上的排钉折弯块向下,驱动排钉完成折弯,并与操作台面上钉槽配合完成一次打钉。
本发明的有益效果体现在:实现了自动化打钉,卷装排钉一次上料可以完成5000颗打钉,大大提高了打钉效率,降低了人工操作的作业强度。同时,打钉位置精准,保证了打钉质量的稳定性。
附图说明
图1:本发明的结构示意图。
图2:本发明自动打钉枪组件的结构示意图。
图3:本发明下压打钉时的内部原理结构图。
其中,1第二移动机架,11第二滑轨,2机架,21滑轨,3连接滑块,31电机,4直线气缸,41打钉盒,42外气缸轴,43内气缸轴,44排钉折弯块,5卷料挡板,51卷料轴,53连杆,71压料板,72底板,6拉料凸轮,61弹性连杆。
具体实施方式
本发明揭示了一种自动打钉系统,结合图1-图3所示,包括一组平行设置的机架2及架设于所述机架2上的第二移动机架1,所述机架2上设置有滑轨21,所述第二移动机架1的两端设置于所述滑轨21上,所述第二移动机架1上设置有第二滑轨11,所述第二滑轨11上垂直向下设置有自动打钉枪组件。所述自动打钉枪组件通过连接滑块3设置于所述第二滑轨11上,所述连接滑块3带动所述自动打钉枪组件在所述第二滑轨上移动。
所述自动打钉枪组件包括自动打钉枪、设置于自动打钉枪上方的驱动机构,所述驱动机构包括直线气缸4及设置于直线气缸4上方的电机31,所述电机31驱动所述直线气缸带动所述自动打钉枪进行周向运动。具体的,本实施例中,所述直线气缸为二级伸缩气缸。
所述自动打钉枪包括与所述二级伸缩气缸的外气缸轴42连接的打钉盒41,所述打钉盒41的一侧设置有进料机构,所述进料机构包括用于放置排钉的卷料轴51,所述卷料轴51的一端设置有卷料挡板5,所述卷料挡板5通过连杆53与所述直线气缸4连接。排钉则套置于所述卷料轴51上。
所述打钉盒51的下部与其垂直设置有一底板72,所述底板72的一端延伸置于所述打钉盒41内。由于排钉为直线形,为了便于送入打钉盒51内,所述底板72上设置有压料板71,所述排钉在进料时置于所述压料板71与底板72之间。所述打钉盒内设置有排钉折弯块44,所述排钉折弯块44的上端与二级伸缩气缸的内气缸轴43连接,所述排钉折弯块44呈门形,所述排钉折弯块44设置于所述底板72的上方,排钉进入打钉盒41后,排钉折弯块44下压,将排钉折弯。
为辅助进料,所述打钉盒41的进料端还设置有拉料凸轮6,所述拉料凸轮6的外侧通过弹性连杆61与打钉盒41连接,所述拉料凸轮6上设置有压料胶带(图中未示意)。所述拉料凸轮6的一侧设置有压轮7,所述压轮7的一侧通过连接机构与拉料凸轮6上端连接,所述连接机构包括与所述压轮一端连接的连接轴及设置于连接轴上方的弹性杆3构成,所述弹性杆3的一侧与拉料凸轮上端连接。所述压轮7用于压紧所述压料胶带从而更好配合排钉的进料。
为更好的实现自动化,所述自动打钉枪下方设置有排钉检测组件,所述排钉检测组件包括用于排钉数量检测的传感器及与所述传感器电性连接的报警机构。当传感器检测到排钉数量不足时,则将信号发送至报警机构进行提醒更换报警。
本发明还揭示了以上所述的自动打钉系统的打钉方法,包括如下步骤:
s1、将待打钉产品置于打钉操作台面,所述操作台面上设置有与所述自动打钉枪配合的钉槽;第二移动支架带动自动打钉枪组件移动至待打钉产品上方;
s2、电机31工作,驱动自动打钉枪旋转至待打钉位置方向;
s3、二级伸缩气缸工作,外气缸轴先带动打钉盒41下压与待打钉产品接触;此时,拉料凸轮6的一侧受到压轮7拉动带动其运转,从而使得卷料轴51上排钉向打钉盒内前进;
s4、二级伸缩气缸继续工作,内气缸轴43带动打钉枪上的排钉折弯块44向下,驱动排钉完成折弯,并与操作台面上钉槽配合完成一次打钉。所述钉槽与折弯后排钉实现的打钉原理与现有技术打钉连接原理一致故在此不再赘述。
同时,以上实施例仅用以说明本发明的技术方案,而非对其限制;尽管参照前述实施例对本发明进行了详细的说明,本领域的普通技术人员应当理解:其依然可以对前述各实施例所记载的技术方案进行修改,或者对其中部分技术特征进行等同替换;而这些修改或者替换,并不使相应技术方案的本质脱离本发明各实施例技术方案的精神和范围。
起点商标作为专业知识产权交易平台,可以帮助大家解决很多问题,如果大家想要了解更多知产交易信息请点击 【在线咨询】或添加微信 【19522093243】与客服一对一沟通,为大家解决相关问题。
此文章来源于网络,如有侵权,请联系删除


