一种能够适应不同尺寸的包装盒组装的塑形压贴方法与流程



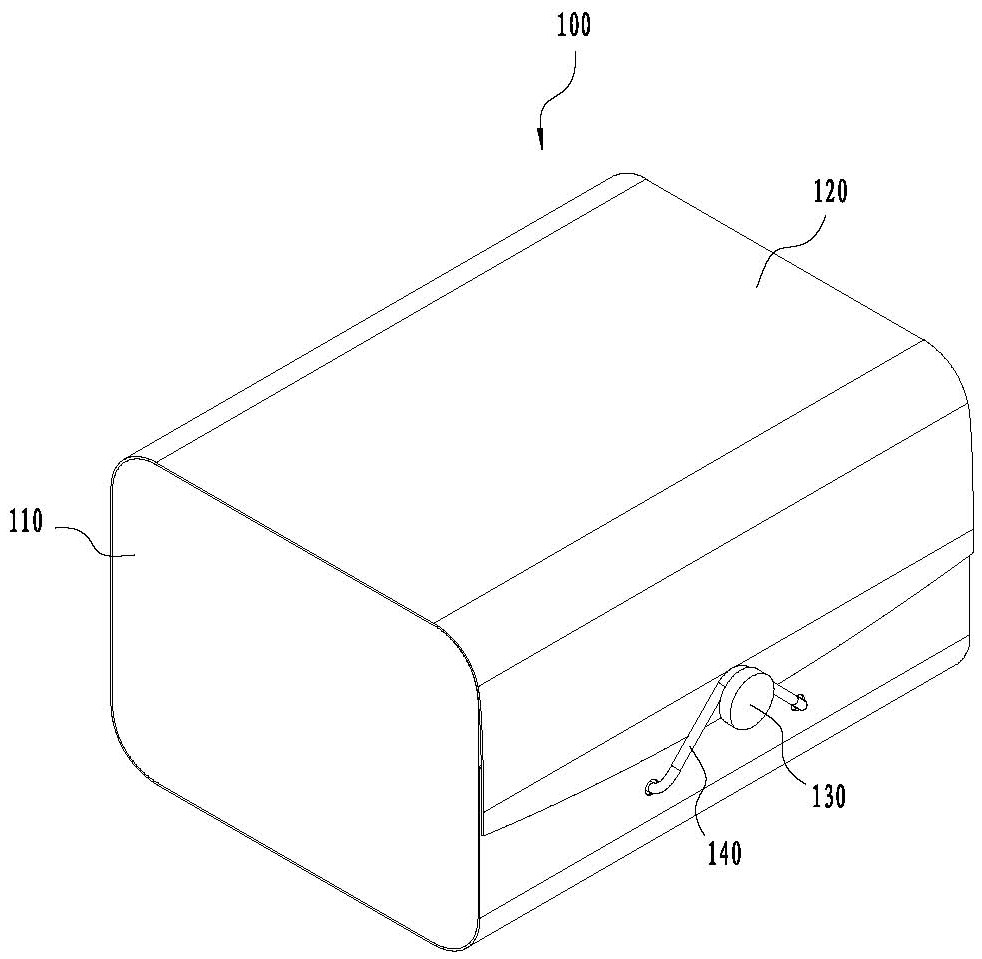
本发明涉及包装盒生产领域,具体涉及一种能够适应不同尺寸的包装盒组装的塑形压贴方法。
背景技术:
传统皮盒生产设备中,只能实现对固定尺寸的包装盒的组装。但是,实际生产过程中,需要针对不同客户的包装产品生产不同型号尺寸的包装盒。因此,有必要提供一种新的包装盒塑形组装方法,实现不同包装盒的组装需求。
技术实现要素:
本发明的目的是提供一种能够适应不同尺寸的包装盒组装的塑形压贴方法,其能够适应不同尺寸的包装盒的组装需求。
本发明采取的技术方案具体如下。
一种能够适应不同尺寸的包装盒组装的塑形压贴方法,所述包装盒由两间隔布置的硬质的盒板和包裹在盒板边部的柔性的盒皮组成,采用塑形模芯上相对布置的容置部容纳和定位盒板,采用塑形模芯上的塑型面对盒皮进行塑形,采用辊压机构对盒皮的边部涂胶处与盒板的涂胶处进行辊压粘合,包括如下步骤:步骤一,获取待组装的盒板的尺寸、盒皮的尺寸,其中,所述盒板的尺寸包括盒板的宽度、高度、厚度中的一者或者几者,所述盒皮的尺寸包括盒皮的宽度、长度中的一者或两者;步骤二,根据所获得的盒板的尺寸、盒皮的尺寸,调节塑形模芯上的容置部的尺寸和/或两容置部的间距;步骤三,将待组装的盒板、盒皮分别向组装工位输送;步骤四,启动塑形模芯将处于组装工位的盒皮压紧,将两个盒板分别移送至处于组装工位的盒皮的两侧边部涂胶处,并由塑形模芯对盒板进行定位;步骤五,将盒皮的两侧边部分别与两个盒板的板侧边进行挤压粘合,组装成包装盒。
优选地,塑型模芯包括沿盒板厚度方向相对布置的两个塑型子模芯,两个塑型子模芯沿盒板厚度方向活动安装,两个容置部分别位于两个塑型子模芯上;在步骤二中,通过调节两个塑型子模芯中的一者或两者移动,实现调节两容置部的间距。
优选地,通过调节两个塑型子模芯同步靠近/远离,实现调节两容置部的间距。
优选地,塑型子模芯包括两个相对布置的模芯子部,两个模芯子部沿盒板的宽度方向活动安装,容置部分为两个容置子部,两个容置子部分别位于同一塑型子模芯中的两个模芯子部上;通过调节各塑型子模芯中的两个模芯子部中的一者或两者移动,实现调节容置部沿盒板宽度方向的尺寸。
优选地,通过调节各塑型子模芯中的两个模芯子部同步靠近/远离移动,实现调节容置部沿盒板宽度方向的尺寸。
优选地,盒板在容置部内立状布置,容置部的上侧形成有限位结构,限位结构由两个相对布置的子限位结构组成,两个子限位结构分别位于同一容置部的两个容置子部的上侧;采用同一容置部处的两个子限位结构,对容置部处的盒板沿板宽方向的移动进行限位;通过调节同一塑型子模芯中的两个模芯子部的间距,使得容置部适配不同宽度尺寸的盒板。
优选地,同一容置部处的两个子限位结构,还能对容置部处的盒板沿板高方向的移动进行限位;将同一容置部处的两个子限位结构分别沿盒板的高度方向活动安装;通过同步调节同一容置部处的两个子限位结构沿板高方向移动,实现调节容置部沿盒板高度方向的尺寸。
优选地,在塑形模芯的下侧设有水平布置、能够相互靠近和远离的两定位板,定位板上设有对盒皮进行定位的定位浅槽,两定位板相靠近的一端分别安装沿盒板高度方向浮动的压辊,两压辊构成辊压机构,压辊的辊长方向与盒皮的宽度方向相一致;将盒皮的两侧边部分别与两个盒板的板侧边进行挤压粘合的方法为:在盒皮进入定位浅槽之前,调节两压辊的辊面下移至定位浅槽的槽底面以下,对盒皮的移入进行避让;在塑型模芯下移将处于组装工位的盒皮压紧、并对盒板进行定位之后,调节两定位板相互远离,同时调节两压辊的辊面凸出于定位浅槽的槽底面,以对盒皮与盒板的下侧板边进行挤压粘合;当定位板移动至两压辊恰好分别能够与盒板的两侧板边紧密贴压时,停止移动定位板、并保持两定位板之间的间距不变,然后,调节模芯继续下移,通过两压辊将盒皮分别压贴在盒板的两侧板边上。
优选地,还包括步骤六,将组装好的包装盒从塑型模芯上卸载下来。
优选地,容置部的下边部具有供盒板向下移出容置部的移出口;步骤四还包括:在盒板输送路径的末端,通过将盒板从容置部的外侧沿板厚方向水平移至容置部内,实现将盒板移送至组装工位的盒皮的两侧边部涂胶处;步骤六具体包括:通过将组装好的包装盒相对于塑形模芯下移,实现对包装盒的卸载。
优选地,塑型模芯上的塑型面位于两容置部之间,塑型面上具有沿盒板宽度方向间隔布置的两外模面,外模面立状布置且具有沿盒板宽度方向移动的自由度;步骤六还包括:
在组装成包装盒以后,调节模芯的外模面沿盒板宽度方向朝模芯的内部收拢,以允许包装盒从模芯上卸下。
本发明取得的技术效果为:
本发明提供的能够适应不同尺寸的包装盒组装的塑形压贴方法,其首先是获取待组装的盒板的尺寸、盒皮的尺寸;然后根据所获得的盒板的尺寸、盒皮的尺寸,调节塑形模芯上的容置部的尺寸和/或两容置部的间距;再将待组装的盒板、盒皮分别向组装工位输送;接着,启动塑形模芯将处于组装工位的盒皮压紧,将两个盒板分别移送至处于组装工位的盒皮的两侧边部涂胶处,并由塑形模芯对盒板进行定位;最后将盒皮的两侧边部分别与两个盒板的板侧边进行挤压粘合,组装成包装盒。通过采用上述方法能够满足不同尺寸的包装盒的组装需求。
除了上面所描述的目的、特征和优点之外,本发明还有其它的目的、特征和优点。下面将参照附图,对本发明作进一步详细的说明。
附图说明
构成本申请的一部分的附图用来提供对本发明的进一步理解,本发明的示意性实施例及其说明用于解释本发明,并不构成对本发明的不当限定。在附图中:
图1为本申请实施例提供的一种木皮包装盒的结构示意图;
图2为盒皮与盒板的装配示意图;
图3为本申请实施例提供的塑型模芯的主视图;
图4为图3的右视图;
图5为图3的轴测图;
图6为本申请实施例提供的定位机构的结构示意图;
图7为本申请实施例提供的塑形模芯与定位机构的应用参考图。
各附图标号对应关系如下:
100-包装盒,110-盒板,120-盒皮,200-塑形模芯,210-a塑型模芯,211-a1模芯部,211a-a1外模块,211b-a1中模块,211c-楔面驱动组件,212-a2模芯部,220-b塑型模芯,230-容置部,231-移出口,240-限位部件,241-a1限位部件,242-a2限位部件,250-升降支架,260-模芯安装架,270-活动杆,280-模芯调节弹簧,310-a辊,311-a1辊,312-a2辊,320-b辊,321-b1辊,322-b2辊,410-间距调节丝杆,510-宽度调节丝杆,610-a1高度调节丝杆,620-a1螺母组件,630-a2高度调节丝杆,640-a2螺母组件,710-a1板,720-a2板,730-b1板,740-b2板,750-c楔面驱动组件。
具体实施方式
为了使本申请的目的及优点更加清楚明白,以下结合实施例对本申请进行具体说明。应当理解,以下文字仅仅用以描述本申请的一种或几种具体的实施方式,并不对本申请具体请求的保护范围进行严格限定,在不冲突的情况下,本申请中的实施例及实施例中的特征可以相互组合。
参阅图1至图7,本申请实施例提供了一种用于包装盒组装的设备,其旨在解决的技术问题是:传统组装包装盒100的操作依赖人工,生产效率低,产品的质量标准无法统一把控。本实施例提供的实施方案包括塑型模芯200、定位机构和辊压机构,塑型模芯200上具有实现对盒皮120进行塑型的塑型部,塑型部上具有塑型面,塑型模芯200的两侧设置用于容置盒板110的容置部230,容置部230位于塑型面的两侧,塑型面和容置部230处于工作状态时,容置部230处的盒板110上涂胶处的板侧边和塑型面顺延布置,定位机构对涂胶后的盒皮120进行定位,辊压机构对盒皮120的边部涂胶处与盒板110的涂胶处进行辊压粘合。
本申请实施例在实施时的基本原理为:利用定位机构对盒皮120进行定位,并对盒皮120进行涂胶处理;然后将塑型模芯200的塑型面贴靠在盒皮120上,并调节塑型模芯200的容置部230和塑型面处于工作状态;再然后将涂胶后的盒板110装配到容置部230内进行定位,使得容置部230处的盒板110上涂胶处的板侧边和塑型面顺延布置;最后,通过辊压机构沿塑型面将盒皮120的边部涂胶处与盒板110的涂胶处进行辊压粘合起来,从而组装得到木质包装盒100。
参阅图1至图7,以形状为矩形的盒板110为例,塑型面的轮廓与盒板110周侧涂胶部位的外轮廓基本一致,盒板110上涂胶处的板侧边包括盒板110高度方向的底边、盒板110宽度方向的两侧边,盒皮120的边部涂胶处是指盒皮120沿宽度方向的两侧边部,这两侧边部均涂胶处理,涂胶范围能够满足将盒皮120沿塑型面辊压后,盒皮120与盒板110可靠粘结在一起。
本实施例提供的用于包装盒100组装的设备,通过塑型模芯200上的塑型部对盒皮120进行塑型,通过塑型模芯200两侧设置的容置部230,在工作状态下容置盒板110,并使盒板110上涂胶处的板侧边和塑型面顺延布置,通过定位机构对涂胶后的盒皮120进行定位,通过辊压机构对盒皮120的边部涂胶处与盒板110的涂胶处进行辊压粘合,由此完成包装盒100的组装。通过该设备实现包装盒100的组装,能够大大减少人工参与的工作量,提高了包装盒100组装操作的自动化水平,进而提高包装盒100组装的效率;另,由于包装盒100的组装操作大部分由该设备来完成,因此便于对产品的质量标准进行统一把控。
在容置部230处于工作状态下时,将盒板110在容置部230内立状布置,容置部230的上侧布置对盒板110沿板宽方向移动、盒板110向上移动的限位部件240,容置部230的下边部布置供盒板110向下移出容置部230的移出口231,盒板110从容置部230的外侧沿板厚方向水平移至容置部230内。其中,由于限位部件240的限制作用,使得容置部230处的盒板110不能沿板宽方向移动,这样就能够实现对盒板110沿板宽方向的准确定位,使得容置部230处的盒板110上涂胶处的板侧边和塑型面顺延布置;另,由于限制部件的作用,也不能向上移动,是能够在辊压机构将盒皮120辊压粘合在盒板110边部的时候,防止盒板110受力上移,不利于装配,而且影响产品质量;而且,由于在容置部230的下边部设置移出口231,可以用于盒板110向下移出容置部230,便于将组装完成的包装盒100从模芯上卸载的时候,将盒板110与模芯分离;再者,盒板110是从容置部230的外侧沿板厚方向水平移至容置部230内,能够通过模芯两侧的容置部230分别对两个盒板110的位置进行定位,之所以是沿板厚方向将盒板110移入容置部230内,是因为在限制部件的作用下,容置部230只剩下了供容置部230处的盒板110沿板厚方向移出、向下移出的自由度,而且木皮在与盒板110组装时,盒板110处于包装盒100中盒皮120的内侧,因此,不适宜从下往上从移出口231处将盒板110送入容置部230,而是沿板厚方向将盒板110送入容置部230内,并利用塑型模芯200的本体对盒板110的移入到位进行限制,方便且可靠。
辊压机构的目的在于实现将盒皮120的边部涂胶处与盒板110的涂胶处进行辊压粘合,具体实施时,辊压机构包括压辊,压辊沿盒板110的板厚方向布置,压辊和塑型模芯200之间沿板高和板宽方向具有相对运动的自由度。塑型模芯200至少升降式安装在机架上,压辊设置有两个,两压辊至少沿板宽方向活动安装在机架上。换言之,至少有如下的实施形式:其一是,塑型模芯200升降式安装,可以相对于压辊上下移动,而压辊是沿板宽方向移动,从而通过两者的相对运动进行配合,实现沿着塑型面定形的轮廓将盒皮120辊压粘合在盒板110的边部;其二是,塑型模芯200升降式安装,压辊除了能够沿板宽方向移动,还能够升降运动;其三是,塑型模芯200具有升降运动和沿盒板110板宽方向运动的自由度,而压辊只是具有沿板宽方向运动的自由度。以上三种实现形式只是众多实施形式中的几种,其他可以用于实现相应目的实施形式均可以应用于本实施方案中。综合而言,第一种实施形式,对于塑型模芯200和压辊的运动路径、运动行程的控制,相对于其他两种更为简单,这使得程控设计也相应地简单化,可以有效降低成本,而且简单的运动和简单的程控更为可靠,便于日常使用中的调整、维修甚至重新校正参数。
上述的定位机构由两能相互靠近和分离的水平布置的定位板构成,两定位板的上板面设置对盒皮120进行定位的定位浅槽,盒皮120平铺在定位浅槽内进行定位,两定位板相靠近的端部安装压辊。通过调节两定位板相互靠近,可以形成完整的定位浅槽,定位浅槽用于容置待定位的盒皮120;当盒皮120移入定位浅槽并被完全定位之后,塑型模芯200可以下降压紧处于定位浅槽中的盒皮120,然后,通过调节两定位板相互远离,可以带动两压辊沿着塑型面的下侧面作相互远离运动,利用压辊将盒皮120与盒板110的下侧边部辊压粘合在一起;当两个定位板之间的距离达到一定值之后,定位板停止运动并保持两个定位板之间的间距不变,此时的状态为,两个压辊的辊面在调节塑型模芯200继续下降的过程中,可以分别对塑型面上沿盒板110板宽方向的两侧面实施辊压,从而将盒皮120与盒板110上沿板宽方向的两侧边部辊压粘合到一起。
在完成将盒皮120与盒板110通过辊压方式粘合到一起之后,就组装成了包装盒100的基本结构形式,但是在组装过程中,塑型模芯200的塑型面是紧贴盒皮120布置的,直至包装盒100组装完成亦是如此。这样给包装盒100的卸载/脱模带来困难,因此,为了便于实现对包装盒100的卸载,塑型模芯200包括沿着板宽方向依次布置的前模块、中模块和后模块,前模块、后模块活动安装在中模块上,活动安装的目的是,至少能够满足允许前模块、后模块沿盒板110板宽方向移动的需求;前模块、中模块和后模块的外模面组成所述的塑型面,塑型面可以紧贴容置在组装好的包装盒100的内部空腔中,也可以对待组装的盒皮120和盒板110分别进行形状、位置的限制,前模块和后模块上沿板高方向布置的外模面可以向靠近中模块的一侧移动收拢,从而可以使整个塑型面在组装好的包装盒100内的占位空间减小,相当于对组装好的包装盒100进行松夹,以便将包装盒100与塑型模芯200分离。
具体地,前模块包括前模块本体和前模块本体上活动设置的前模活动部,后模块包括后模块本体和后模块本体上活动设置的后模活动部,前模活动部、后模活动部处于a1和a2两种状态,a1状态为:前模活动部、后模活动部的外表面和中模块的下表面组成所述的塑型面;a2状态为:前模活动部、后模活动部的外表面向靠近中模块的一侧移动,方便塑型模芯200从粘贴好的包装盒100移出。通过将前模块分为前模块本体和前模块本体上活动设置的前模活动部、以及将后模块分为后模块本体和后模块本体上活动设置的后模活动部,有利于后续对塑型面的外轮廓尺寸进行调整,调整的方式可以是通过调节前模活动部相对于前模块本体移动和/或调节后模活动部相对于后模块本体移动,也可以是通过更换相应尺寸的前模活动部和/或后模活动部,从而能够适应不同尺寸包装盒100的组装需求。当前模活动部、后模活动部处于a1状态时,可以通过塑型面对盒皮120进行定位,也就是通过塑型面对盒皮120进行塑型,以便将盒皮120辊压粘合在盒板110上;当前模活动部、后模活动部处于a1状态时,前模活动部、后模活动部的外表面向靠近中模块的一侧移动,使得塑型面沿盒板110宽度方向的尺寸减小,从而方便将粘贴好的包装盒100从塑型模芯200上卸载下来。
在实现将前模活动部、后模活动部的外表面向靠近中模块的一侧移动的目的时,前模活动部和中模块之间、以及后模活动部和中模块之间分别设置有a楔面驱动组件,前模块本体、后模块本体沿着板高方向相对中模块移动,且前模块本体和后模块本体相对于中模块下移时触发a楔面驱动组件调整前模活动部、后模活动部处于a1状态。其实施原理为:通过调节前模块本体、后模块本体沿着板高方向相对中模块上移/下移,可以触发a楔面驱动组件调整前模活动部、后模活动部处于a2状态/a1状态,其中,调节前模块本体、后模块本体沿着板高方向相对中模块上移,可以实现调节前模活动部、后模活动部的外表面向靠近中模块的一侧移动,方便塑型模芯200从粘贴好的包装盒100移出;调节前模块本体、后模块本体沿着板高方向相对中模块上下移,可以实现调节前模活动部、后模活动部的外表面向远离中模块的一侧移动的目的,直至前模活动部、后模活动部的外表面和中模块的下表面组成塑型面,利用塑型面可以对待组装的盒皮120进行塑型。
前模活动部和中模块之间、以及后模活动部和中模块之间分别设置有a楔面驱动组件,具体的理解可以是,前模活动部和中模块之间a楔面驱动组件可以设置在前模活动部与前模块本体之间/前模块本体与中模块之间;后模活动部和中模块之间a楔面驱动组件可以设置在后模活动部与后模块本体之间/后模块本体与中模块之间。
以前模活动部和中模块之间的a楔面驱动组件的装配形式为例进行说明,当a楔面驱动组件设置在前模活动部与前模块本体之间时,前模活动部沿盒板110高度方向相对于中模块移动的自由度受到限制,且前模活动部具有沿盒板110宽度方向相对于中模块移动的自由度,通过调节前模块本体通过上下移动,可以实现调节前模活动部沿盒板110宽度方向靠近/远离中模块的目的;当a楔面驱动组件设置在前模块本体与中模块之间时,前模活动部和前模块本体均具有沿盒板110高度方向和宽度方向移动的自由度,在前模块本体相对于中模块运动的同时,前模活动部随之升降,同时沿板宽方向作靠近/远离中模块的运动。后模活动部和中模块之间的a楔面驱动组件的装配形式,与前模活动部和中模块之间的a楔面驱动组件的装配形式同理。
在将已粘贴好的包装盒100从塑型模芯200上卸载之后,需要将组装好的包装盒100转送至其他工位,以便对包装盒100进行胶液固化等工序的处理。因此,在定位机构的下侧可以设置转送机构,对辊压后的盒体完成卸载以后实施转送。具体地,转送机构为转送输送带构成,转送输送带上设置有对辊压后的包装盒100进行夹持的夹持机构,可以在完成包装盒100的卸载以后,将卸载后的包装盒100进行夹持,然后利用转送输送带对夹持的各包装盒100,依序输送。更具体地,可以在塑型模芯200下降的过程中,将粘结好的包装盒100装配到转送输送带的夹持机构上,并在夹持机构对包装盒100实施夹紧以后,通过将塑型模芯200上移、同时调节塑型面进行收拢,可以达到脱模的目的,而且一举两得,不仅减少包装盒100二次装夹的操作,而且可以有效利用夹持机构夹持的作用,对塑型模芯200上的已粘贴好的包装盒100进行脱模。从而有利于进一步提高包装盒100生产的效率和降低劳动强度。
上述夹持机构包括沿转送输送带的输送方向间隔布置的夹持单元,夹持单元包括沿输送方向相对布置的两夹持件,两夹持件、与转送输送带的带面之间构成用于夹持装配包装盒100的夹持区域,夹持件通过扭簧转动装配在转送输送带的带面上,同一夹持单元中两个夹持件上装配的扭簧的扭转复位方向相反,在初始状态下,两夹持件呈倒八字形,夹持区域的入口沿着背离转送输送带的带面的方向先逐渐减小后逐渐增大,也即初始状态下,两夹持件背离转送输送带的带面的一端靠近布置、且具有一端外翻的弯折部;在工作状态下,塑型模芯200下移,驱使包装盒100下移与弯折部构成楔面驱动配合,将两夹持件撑开,以便允许包装盒100移入夹持区域内,在包装盒100完全移入夹持区域后,转送输送带的带面对包装盒100的盒底进行支撑、夹持件对包装盒100上对应盒板110的部位进行夹持,然后塑型模芯200的塑型面在塑型模芯200上移的同时进行收拢,使得包装盒100与塑型面分离,完成卸载以及将包装盒100装夹到转送输送带上的目的。
在盒皮120与盒板110粘接组装成包装盒100以后,胶液还需固化处理才能使得包装盒100可靠使用,对包装盒100进行胶液固化处理的方式有很多,可以将包装盒100归置到一个区域进行自然晾干,也可以采用加速空气流动的方式吹干,也可以用加热方式烘干处理。本申请实施例在转送输送带的输送路径上设置有烘箱。在利用转送输送带对组装好的包装盒100进行输送的途中,通过布置烘箱,也即采用烘干的方式对包装盒100进行胶液固化的处理,从而能够在转送过程中完成对包装盒100进行胶液固化处理的目的,在转送输送带的出料端,即可获得胶液已经固化完成的包装盒100。不仅节约了设备的空间占用,而且大大缩减了整个包装盒100生产的周期,进而提高了包装盒100生产的效率。
由于将盒板110装配到工作状态下的容置部230以后,盒板110的下侧边部通常是与盒皮120的上表面紧贴布置了,如果在这个时候要对盒板110进行涂胶操作,实在不便。因此,本申请实施例优选的是,在容置部230的两外侧设置有用于对盒板110边部上待涂胶处进行涂胶的涂胶装置。也就是在盒板110移至容置部230内以前,通过涂胶装置对盒板110边部上待涂胶处进行涂胶处理。
塑型模芯200在具体装配实施时,安装在模芯安装架260上,模芯安装架260的下端设置有活动杆270,中模块装配在活动杆270的下端,活动杆270和模芯安装架260之间设置有模芯调节弹簧280,模芯调节弹簧280驱使中模块向远离模芯安装架260一侧移动。在初始状态下,塑型模芯200远离定位浅槽布置,对盒皮120进入定位浅槽的动作等进行避让,此时塑型模芯200在模芯调节弹簧280的驱使下远离模芯安装架260布置,前模活动部、后模活动部的外表面靠近中模块的一侧布置;待盒皮120在定位浅槽内平铺定位完毕之后,塑型模芯200下行,先是将处于定位浅槽内的盒皮120压紧,压紧到位后,使得中模块相对于模芯安装架260回缩,前模活动部、后模活动部的外表面远离中模块一侧布置,塑型面处于工作状态,此时可以将盒板110送入塑型模芯200上沿盒皮120厚度方向的两侧容置部230中进行定位;待盒板110在容置部230内定位完毕以后,可以调节两定位板相互远离运动,利用两压辊沿塑型面的下表面将盒皮120辊压贴合在盒板110的下边部上;当两压辊移动到位后,两压辊的辊面恰好能够满足与盒板110两侧边部进行辊压的需求,再将塑型模芯200继续下移,可以利用压辊沿塑型面上沿板宽方向的两侧面将盒皮120辊压贴合在盒板110的两侧边部上,当塑型模芯200移动至低位后,盒皮120与盒板110即完成组装,获得具有初步形态的包装盒100,后续可以将组装好的包装盒100从塑型模芯200上卸载下来、对卸载的包装盒100进行转送、以及对包装盒100进行胶液固化处理。
具体地,上述的定位浅槽的槽口朝上布置,定位浅槽的槽宽与盒皮120的宽度相一致,定位浅槽的槽长方向与盒皮120的输送方向保持一致,定位浅槽沿盒皮120输送方向的首端槽壁设置进料口,定位浅槽沿盒皮120输送方向的末端槽壁用于限制盒皮120沿输送方向移出;定位浅槽的槽深大于等于盒皮120的厚度。其实施原理为:利用定位浅槽对移入的盒皮120沿宽度方向和输送方向的位置进行限定,定位浅槽沿盒皮120输送方向的首端槽壁设置进料口,以供盒皮120进入。
定位浅槽的槽深大于盒皮120的厚度,定位浅槽上沿其槽宽方向的两侧槽壁分别开设有供盒板110移入的b空缺部,b空缺部的下边部与处于定位浅槽内的盒皮120的上表面齐平。首先,定位浅槽的槽深大于盒皮120的厚度,是有利于对盒皮120进行定位和防止盒皮120沿输送方向移出的,其次,通过开设下边部与盒皮120上表面齐平的b空缺部,能够在盒板110移至盒皮120上的过程中,对盒板110进行导送和定位。
压辊的辊长方向与定位浅槽的槽宽方向一致,压辊具有沿盒皮120长度方向和盒皮120厚度方向相对于机架分别进行移动的自由度,当塑型模芯200位于定位浅槽的上方且与盒皮120间隔布置时,两压辊处于低位,对进入定位浅槽的盒皮120进行避让;当塑型模芯200下行且自接触盒皮120上表面开始,两压辊上移至高位,使得辊面凸出于定位浅槽槽底面布置,同时两压辊沿水平方向相互远离运动,对塑型模芯200的继续下行进行避让,并使得两压辊最终分别能将盒皮120压贴在盒板110宽度方向的两侧面上。
本实施例还包括沿盒皮120的输送方向滑动装配的定位支架,两个压辊沿盒皮120的厚度方向分别浮动安装在两个定位支架上,移动定位支架向塑型模芯200的外侧移动,使得压辊对塑型模芯200进行避让。
两个槽形件分别安装在两个定位支架上,压辊的两端分别沿辊长方向延伸至定位浅槽的外部,使得压辊的辊长大于定位浅槽的槽宽,有利于将定位浅槽内的盒皮120可靠辊压在盒板110上。移动定位支架使得两个槽形件分别与对应的压辊相对于机架同步移动,换言之,每个定位支架上都有一个槽形件和一个压辊,移动定位支架可以使得该定位支架上的槽形件和压辊同步移动,从而便于快速调节槽形件和压辊对塑型模芯200进行避让。
为了实现调节压辊上下浮动,将槽形件的中部铰接安装在定位支架上,两个压辊分别安装在两个槽形件上相互靠近的一端,采用翻转槽形件的方式调节压辊上下移动;还包括有与槽形件相连的c楔面驱动组件750,c楔面驱动组件750分别设置在两槽形件上相互远离的一端与b平移驱动组件之间,c楔面驱动组件750用于调节槽形件正向转动,使得压辊向高位移动,高位是指压辊向上移动至距离定位浅槽的槽底面最远时的位置;其中,正向转动的方向为使得压辊靠近盒皮120移动时槽形件的转动方向;槽形件与定位支架之间设置有b复位部,b复位部用于分别驱使槽形件反向转动,使得压辊向低位移动,低位是指压辊向下移动至不超出定位浅槽的槽底面的位置;其中,反向转动的方向为使得压辊远离盒皮120移动时槽形件的转动方向;还包括与定位支架相连的b平移驱动组件,b平移驱动组件用于驱使定位支架滑动,b平移驱动组件沿盒皮120的身长方向相对于定位支架靠近运动时,触发c楔面驱动组件750调整槽形件转动、压辊上移;在两个压辊分别随两个定位支架相互远离运动的过程中,压辊上移与盒皮120接触,并使盒皮120上与压辊接触的部位压贴在盒板110上的边部涂胶面。
具体实施时,c楔面驱动组件750包括c1楔面驱动部和c2楔面驱动部,c1楔面驱动部设置在c导送件的另一端,c2楔面驱动部与c1楔面驱动部对应布置,c2楔面驱动部还与b平移驱动组件相连,b平移驱动组件驱使c2楔面驱动部与c1楔面驱动部相互靠近构成楔面驱动配合、以及驱使定位支架沿盒皮120的身长方向移动,使得压辊将盒皮120压贴在盒板110上的边部涂胶面。c2楔面驱动部与c1楔面驱动部相互靠近构成楔面驱动配合,是用于实现调节槽形件进行正向和反向转动,槽形件的转动动作发生在b平移驱动组件驱使定位支架进行平移运动的过程中,即b平移驱动组件驱使定位支架进行平移运动是主运动,槽形件的转动是在定位支架滑移运动基础上的子运动,子运动的动作实现要与主运动的动作实现相适应。
c1楔面驱动部的楔形面上设置有b滑槽,b滑槽的槽口沿远离槽底的方向呈收口状设置,c2楔面驱动部的楔形面上设置有与b滑槽适配的b滑台,b滑台与b滑槽之间在c1楔面驱动部与c2楔面驱动部相对滑动时构成滑动导向配合;b复位部为设置在c2楔面驱动部与定位支架之间的压缩弹簧,压缩弹簧用于驱使c1楔面驱动部与c2楔面驱动部沿盒皮120身长方向相互远离运动、槽形件反向转动。由于b滑台与b滑槽之间在c1楔面驱动部与c2楔面驱动部相对滑动时构成滑动导向配合,且b滑槽的槽口沿远离槽底的方向呈收口状设置,因此能限制c2楔面驱动部沿垂直于楔面的方向远离c1楔面驱动部移动,因此可以利用压缩弹簧的恢复力,驱使c2楔面驱动部和槽形件同步复位。
b复位部在实施时可以包括扭簧和压缩弹簧,扭簧设置在槽形件与定位支架铰接处,用于驱使槽形件反向翻转、以及使得c1楔面驱动部与c2楔面驱动部紧贴布置;压缩弹簧用于驱使c1楔面驱动部与c2楔面驱动部沿盒皮120身长方向相互远离运动。即c2楔面驱动部通过压缩弹簧的弹性恢复力进行复位,而槽形件通过扭簧的弹性扭转复位作用力进行复位。
b平移驱动组件为气缸的活塞杆构成,活塞杆与c2楔面驱动部相连,气缸的缸身与机架相连。
本实施例提供的用于固定尺寸的包装盒100组装的设备,只能适应一种尺寸型号的包装盒100的组装需求,产品较为单一;可以通过结合上述的实施例进行改进,使得设备能够适应不同尺寸的包装盒100的生产,从而提高设备的利用率。
传统皮盒生产设备中,只能实现对固定尺寸的包装盒100的组装。但是,实际生产过程中,需要针对不同客户的包装产品生产不同型号尺寸的包装盒100,因此,就需要针对不同尺寸的盒皮120的塑形需求、不同尺寸盒板110的容置需求、定位需求,对现有设备做出改进。
参阅图1至图7,针对上述问题,本申请实施例提供了一种能够适应不同尺寸包装盒100组装的塑形压贴装置,所述包装盒100由两间隔布置的硬质的盒板110和包裹在盒板110边部的柔性的盒皮120组成,包括塑型模芯200和辊压机构,塑型模芯200上具有实现对盒皮120进行塑型的塑型部,塑型部上具有塑型面,塑型面用于在对盒皮120进行塑型时与盒皮120的一表面贴合布置,塑型模芯200的两侧设置用于容置盒板110的容置部230,容置部230位于塑型面的两侧,塑型面和容置部230处于工作状态时,容置部230处的盒板110上涂胶处的板侧边和塑型面顺延布置,辊压机构对盒皮120的边部涂胶处与盒板110的涂胶处进行辊压粘合,两容置部230的间距方向与容置部230处的盒板110的厚度方向相一致,容置部230沿容置部230处的盒板110的宽度方向和/或盒板110高度方向的尺寸和/或两容置部230的间距设置成可调式结构。
通过将容置部230的尺寸和/或两容置部230的间距设置成可调式结构,可以满足不同尺寸的包装盒100的组装需求。
本实施例提供的能够适应不同尺寸包装盒100组装的塑形压贴装置,通过塑型模芯200上的塑型面实现对盒皮120进行塑型,通过塑型模芯200的两侧设置的容置部230容置盒板110,塑型面和容置部230处于工作状态时,容置部230处的盒板110上涂胶处的板侧边和塑型面顺延布置,再由辊压机构对盒皮120的边部涂胶处与盒板110的涂胶处进行辊压粘合,实现包装盒100的组装,并通过将容置部230沿容置部230处的盒板110宽度方向和/或盒板110高度方向的尺寸和/或两容置部230的间距设置成可调式结构,可以适应不同尺寸包装盒100在组装过程中的盒皮120塑形和盒板110定位需求,从而提高塑形压贴装置的兼容性。
本实施例提供的能够适应不同尺寸包装盒100组装的塑形压贴装置,可以结合上述实施例1中的方案进行实施。
参阅图3至图5,上述的塑型模芯200包括沿盒板110厚度方向相对布置的a塑型模芯210和b塑型模芯220,a塑型模芯210上具有a塑型子面,a塑型子面用于对盒皮120上沿盒板110厚度方向的一侧边部进行塑形,b塑型模芯220上具有b塑型子面,b塑型子面用于对盒皮120上沿盒板110厚度方向的一侧边部进行塑形,a塑型子面与b塑型子面构成所述塑型面;a塑型模芯210、b塑型模芯220沿盒板110厚度方向活动安装在升降支架250上,通过调节升降支架250升降实现塑型模芯200靠近和远离组装工位,组装工位用于定位盒板110、盒皮120以及实现盒皮120与盒板110的组装,通过调节a塑型模芯210、b塑型模芯220中的一者或两者沿盒板110厚度方向移动,可以实现改变a塑型模芯210、b塑型模芯220的间距的目的;a塑型模芯210和/或b塑型模芯220与间距调节机构相连,间距调节机构调节a塑型模芯210、b塑型模芯220沿盒板110的盒板110厚度方向相互靠近/远离。
参阅图3至图5、以及图7,a塑型模芯210、b塑型模芯220沿盒板110厚度方向滑动装配在升降支架250上,间距调节机构包括转动安装在升降支架250上的间距调节丝杆410,间距调节丝杆410的杆长方向与盒板110厚度方向保持一致,间距调节丝杆410上沿其杆长方向的两端分别设有a间距调节丝杆410段、b间距调节丝杆410段,a间距调节丝杆410段、b间距调节丝杆410段的螺纹旋向相反,a间距调节丝杆410段与a塑型模芯210构成丝杆螺母配合连接,b间距调节丝杆410段与b塑型模芯220构成丝杆螺母配合连接,转动间距调节丝杆410调节a塑型模芯210、b塑型模芯220沿盒板110的盒板110厚度方向相互靠近/远离。
间距调节丝杆410的杆端可以设置调节手轮或者调节旋钮抑或是调节手柄,从而便于实施手动调节间距调节丝杆410转动。当然,也可以将间距调节丝杆410与步进电机等驱动源相连,自动控制间距调节丝杆410的转动。
参阅图3至图5,a塑型模芯210、b塑型模芯220的结构相同,a塑型模芯210包括沿着盒板110宽度方向相对布置的a1模芯部211和a2模芯部212,a1模芯部211上具有a1塑型子面,a2模芯部212上具有a2塑型子面,a1塑型子面和a2塑型子面构成所述的a塑型子面,a1模芯部211、a2模芯部212沿盒板110宽度方向活动安装在a模芯安装架上,a1模芯部211和/或a2模芯部212与宽度调节机构相连,宽度调节机构调节a1模芯部211、a2模芯部212沿盒板110宽度方向相互靠近/远离。
参阅图3至图5,上述的模芯安装架260包括a模芯安装架和b模芯安装架,a模芯安装架、b模芯安装架分别与a塑型模芯210、b塑型模芯220对应布置
b塑型模芯220包括沿着盒板110宽度方向相对布置的b1模芯部和b2模芯部,b1模芯部上具有b1塑型子面,b2模芯部上具有b2塑型子面,b1塑型子面和b2塑型子面构成所述的b塑型子面,b1模芯部、b2模芯部沿盒板110宽度方向活动安装在b模芯安装架上,b1模芯部和/或b2模芯部与宽度调节机构相连,宽度调节机构调节b1模芯部、b2模芯部沿盒板110宽度方向相互靠近/远离。
参阅图3至图5,a1模芯部211和a2模芯部212沿盒板110宽度方向滑动安装在a模芯安装架上;宽度调节机构包括转动安装在模芯安装架260上的宽度调节丝杆510,宽度调节丝杆510的杆长方向与盒板110宽度方向保持一致,宽度调节丝杆510上沿其杆长方向的两端分别设有a宽度调节丝杆510段、b宽度调节丝杆510段,a宽度调节丝杆510段、b宽度调节丝杆510段的螺纹旋向相反,a宽度调节丝杆510段与a1模芯部211构成丝杆螺母配合连接,b宽度调节丝杆510段与a2模芯部212构成丝杆螺母配合连接,转动宽度调节丝杆510调节a1模芯部211、a2模芯部212沿盒板110宽度方向相互靠近/远离。
上述的宽度调节丝杆510设有两组,两组宽度调节丝杆510分别与a模芯安装架、b模芯安装架对应布置。
参阅图3至图5,b1模芯部和b2模芯部沿盒板110宽度方向滑动安装在b模芯安装架上;宽度调节机构包括转动安装在模芯安装架260上的宽度调节丝杆510,宽度调节丝杆510的杆长方向与盒板110宽度方向保持一致,宽度调节丝杆510上沿其杆长方向的两端分别设有a宽度调节丝杆510段、b宽度调节丝杆510段,a宽度调节丝杆510段、b宽度调节丝杆510段的螺纹旋向相反,a宽度调节丝杆510段与b1模芯部构成丝杆螺母配合连接,b宽度调节丝杆510段与b2模芯部构成丝杆螺母配合连接,转动宽度调节丝杆510调节b1模芯部、b2模芯部沿盒板110宽度方向相互靠近/远离。
上述的两组宽度调节丝杆510可以通过建立传动连接关系,以便仅操纵一组宽度调节丝杆510,就能够实现同步调节两组宽度调节丝杆510转动,提高调节效率和调节精度。
具体实施时,参阅图3至图5,可以采用涡轮蜗杆组件将两组宽度调节丝杆510传动连接起来。具体地,在两组宽度调节丝杆510的杆端分别设置涡轮,在升降支架250上安装同步调节轴,同步调节轴的两端分别沿调节轴的轴向滑动安装滑套,滑套的外表面设置蜗杆段,两个滑套上的蜗杆段的旋向相反布置,两个蜗杆段分别与两个涡轮啮合传动连接。还包括两组滑动座,两组滑动座分别转动安装在同步调节轴上,两组滑动座分别与两个滑套对应布置,两组滑动座可沿同步调节轴的轴向移动,且移动时能够带动两个滑套同步移动,两组滑动座分别与a模芯安装架、b模芯安装架相连,从而在a模芯安装架、b模芯安装架相对于升降支架250移动时,能够分别带动两个滑套随动,从而保持两个滑套上的蜗杆段分别与两个涡轮保持传动连接关系。通过转动同步调节轴,可以驱使两个宽度调节丝杆510同步转动。
参阅图7,为了在包装盒100组装完成后,方便包装盒100的卸载,本申请实施例进一步优选的实施方案为:a1模芯部211包括沿盒板110宽度方向依次布置的a1外模块211a、a1中模块211b,a1外模块211a活动安装在a1中模块211b上,a2模芯部212包括沿盒板110宽度方向依次布置的a2中模块、a2外模块,a2外模块活动安装在a2中模块上,a1中模块211b、a2中模块分别位于a1模芯部211、a2模芯部212相靠近的一侧;a1外模块211a、a1中模块211b的外模面组成所述的a1塑型子面,a2中模块、a2外模块的外模面组成所述的a2塑型子面;a1外模块211a上沿盒板110高度方向布置的外模面可以向靠近a1中模块211b的一侧移动收拢,a2外模块上沿盒板110高度方向布置的外模面可以向靠近a2中模块的一侧移动收拢。
具体地,参阅图3至图5,a1模芯部211与a2模芯部212相同,a1外模块211a包括a1外模块211a本体和a1外模块211a本体上活动设置的a1外模活动部,a1外模活动部、a1中模块211b处于a1和a2两种状态,a1状态为:a1外模活动部的外表面和a1中模块211b的下表面组成所述的a1塑型子面;a2状态为:a1外模活动部的外表面向靠近a1中模块211b的一侧移动,方便a1模芯部211从粘贴好的包装盒100内移出,如图7所示。当a1模芯部211处于a1状态时,a2模芯部212、b1模芯部、b2模芯部均处于a1状态;当a1模芯部211处于a2状态时,a2模芯部212、b1模芯部、b2模芯部均处于a2状态。
参阅图3至图5,下面以a1模芯部211在a1状态、a2状态的切换为例进行说明:
a1外模活动部和a1中模块211b之间设置有楔面驱动组件211c,a1外模块211a本体沿着盒板110高度方向相对a1中模块211b移动,且a1外模块211a本体相对a1中模块211b下移时触发楔面驱动组件211c调整a1外模活动部处于a1状态。
具体地,a模芯安装架的下端设置有活动杆270,a1中模块211b装配在活动杆270的下端,a1活动杆270和a模芯安装架之间设置有模芯调节弹簧280,模芯调节弹簧280驱使a1中模块211b向远离a模芯安装架一侧移动。
盒板110在容置部230内立状布置,容置部230的上侧形成具有对盒板110沿盒板110宽度方向移动、沿盒板110高度方向移动进行限制的限位部件240,a塑型模芯210上的限位部件240与b塑型模芯220上的限位部件240相同。为了能够适应不同高度尺寸的盒板110的容置和定位需求,本实施例进一步的实施方案包括:a塑型模芯210上的限位部件240包括a1限位部件241和a2限位部件242,a1限位部件241沿盒板110的高度方向活动安装在a1外模块211a上,a2限位部件242沿盒板110的高度方向活动安装在a2外模块上,a1限位部件241、a2限位部件242与高度调节机构相连,高度调节机构调节a1限位部件241、a2限位部件242沿盒板110的高度方向移动。
a1限位部件241沿盒板110高度方向滑动安装在a1外模块211a上,a2限位部件242沿盒板110高度方向滑动安装在a2外模块上;高度调节机构包括a1高度调节丝杆610、a2高度调节丝杆630,a1高度调节丝杆610、a2高度调节丝杆630的杆长方向均与盒板110高度方向保持一致;a1高度调节丝杆610的下端与a1限位部件241相连,a1高度调节丝杆610的上端通过a1螺母组件620与a1外模块211a构成锁紧连接,a1螺母组件620与a1高度调节丝杆610构成丝杆螺母配合连接,转动a1螺母组件620/a1高度调节丝杆610调节a1限位部件241沿盒板110高度方向移动;a2高度调节丝杆630的上端通过a2螺母组件640与a2外模块构成锁紧连接,a2螺母组件640与a2高度调节丝杆630构成丝杆螺母配合连接,转动a2螺母组件640/a2高度调节丝杆630调节a2限位部件242沿盒板110高度方向移动。
参阅图1至图7,上述的塑型模芯200升降式安装在机架上;上述的辊压机构包括沿盒板110的输送方向布置的两个压辊,压辊的辊长方向与盒板110的厚度方向一致,两压辊至少沿盒板110宽度方向活动安装在机架上。
两压辊沿盒板110宽度方向活动安装在机架上,两压辊与辊压调节机构相连,辊压调节机构调节两压辊沿盒板110宽度方向相互靠近和远离,当盒皮120位于a1状态下的a塑型子面的下表面与两压辊之间时,辊压调节机构调节两压辊沿盒板110宽度方向相互远离,直至压辊的辊面与盒板110宽度方向的侧边部相切布置,使得盒皮120辊压粘接在盒板110的下侧边部;升降支架250与升降调节机构相连,升降调节机构在压辊的辊面与盒板110宽度方向的侧边部相切布置时调节塑型模芯200下降,使得盒皮120与盒板110宽度方向的侧边部粘接。其中,两压辊相互远离到极限位置,恰好两压辊相向布置的一侧辊面与盒板110宽度方向的侧边部相切,此时通过将塑型模芯200下移,可以将盒皮120与盒板110宽度方向的两侧边辊压粘合起来,从而完成盒皮120与盒板110的组装。
参阅图7,塑型模芯200的下方布置定位机构,定位机构对盒皮120进行定位,定位机构包括沿a方向能够相互远离和靠近的a板组件、b板组件,a方向与b方向垂直,b方向为盒皮120向定位机构输送的方向。a板组件、b板组件上相邻的边部上表面向a板组件、b板组件本体设置凹陷部,凹陷部的表面形成a定位支撑面、b定位支撑面,a定位支撑面对盒皮120沿b方向的一边部进行支撑,b定位支撑面对盒皮120沿b方向的另一边部进行支撑,凹陷部周边的高于凹陷部表面的a板组件的板身形成a1定位部、a2定位部,凹陷部周边的高于凹陷部表面的b板组件的板身形成b1定位部、b2定位部,a1定位部、b1定位部对盒皮120沿a方向的偏移进行限定,a2定位部、b2定位部对盒皮120沿b方向的移动停止位置进行限定。其工作原理为:盒皮120沿b方向输送,当盒皮120移至a板组件上和b板组件上是,a板组件上的a1定位部用于对处于a板组件上的盒皮120沿a方向远离b板组件的移动进行限制,a板组件上的a2定位部用于对处于a板组件上的盒皮120局部身段沿b方向的继续移动进行限制;同理,b板组件上的b1定位部用于对处于b板组件上的盒皮120沿a方向远离a板组件的移动进行限制,b板组件上的b2定位部用于对处于b板组件上的盒皮120局部身段沿b方向的继续移动进行限制。
参阅图3至图7,a板组件包括沿b方向依次顺延布置的a1板710和a2板720,b板组件包括沿b方向依次顺延布置的b1板730和b2板740,a1板710和b1板730相对布置组成盒皮120前端定位部,a2板720和b2板740相对布置组成盒皮120后端定位部,盒皮120前、后端定位部沿b方向可相互靠近和远离。在具体实施时,可以采用气缸作为动力分别驱动盒皮120前、后端定位部相互靠近和远离。
a板组件、b板组件分别通过a滑动支架、b滑动支架沿a方向滑动安装在定位支架上,定位支架上转动安装有定位调节丝杆,定位调节丝杆上沿杆身方向的两端分别具有a定位丝杆段、b定位丝杆段,a定位丝杆段、b定位丝杆段分别与a滑动支架、b滑动支架构成丝杆螺母装配连接,转动调节丝杆调节a板组件、b板组件沿a方向相互靠近/远离,a滑动支架、b滑动支架和定位调节丝杆构成所述的定位调节单元。
a滑动支架包括沿b方向依次顺延布置的a1滑动支架、a2滑动支架,b滑动支架包括沿b方向依次顺延布置的b1滑动支架、b2滑动支架,定位调节丝杆设有两个,两个定位调节丝杆沿b方向依次顺延布置,其中一个定位调节丝杆上的a定位丝杆段、b定位丝杆段分别与a1滑动支架、b1滑动支架构成丝杆螺母配合连接,另一个定位调节丝杆的a定位丝杆段、b定位丝杆段分别与a2滑动支架、b2滑动支架构成丝杆螺母配合连接,a1板710、a2板720分别安装在a1滑动支架、a2滑动支架上,b1板730、b2板740分别安装在b1滑动支架、b2滑动支架上,两个定位调节丝杆传动连接,转动其中一个定位调节丝杆调节a板组件、b板组件相互靠近/远离。
两个压辊分别安装在a板组件、b板组件相互靠近的一端,两个压辊分别记为a辊310、b辊320,a辊310包括沿a方向布置的a1辊311、a2辊312,a1辊311、a2辊312分别安装在a1板710、b1板730上,a1辊311与a2辊312的轴线重合布置,b辊320包括沿a方向布置的b1辊321、b2辊322,b1辊321、b2辊322分别安装在a2板720、b2板740上,b1辊321、b2辊322的轴线重合布置,a1辊311与b1辊321对应布置,a2辊312与b2辊322对应布置。
参阅图6和图7,以a1辊311为例,为了实现调节a1辊311上下浮动,将a1板710的中部铰接安装在a11滑动支架上,a11滑动支架沿b方向滑动安装在a1滑动支架上;还包括有与a1板710相连的c楔面驱动组件750,c楔面驱动组件750分别设置在a1板710上远离a2板720的一端与b平移驱动组件之间,c楔面驱动组件750用于调节a1板710正向转动,使得a1辊311向高位移动,高位是指a1辊311向上移动至距离定位浅槽的槽底面最远时的位置;其中,正向转动的方向为使得a1辊311靠近盒皮120移动时a1板710的转动方向;a1板710与定位支架之间设置有b复位部,b复位部用于分别驱使a1板710反向转动,使得a1辊311向低位移动,低位是指a1辊311向下移动至不超出定位浅槽的槽底面的位置;其中,反向转动的方向为使得a1辊311远离盒皮120移动时a1板710的转动方向;b平移驱动组件与定位支架相连,b平移驱动组件用于驱使定位支架滑动,b平移驱动组件沿盒皮120的身长方向相对于定位支架靠近运动时,触发c楔面驱动组件750调整a1板710转动、a1辊311上移;在两个a1辊311分别随两个定位支架相互远离运动的过程中,a1辊311上移与盒皮120接触,并使盒皮120上与a1辊311接触的部位压贴在盒板110上的边部涂胶面。
具体实施时,参阅图3至图7,c楔面驱动组件750包括c1楔面驱动部和c2楔面驱动部,c1楔面驱动部设置在a1滑动支架上,c2楔面驱动部与c1楔面驱动部对应布置,c2楔面驱动部还与b平移驱动组件相连,b平移驱动组件驱使c2楔面驱动部与c1楔面驱动部相互靠近构成楔面驱动配合、以及驱使定位支架沿盒皮120的身长方向移动,使得a1辊311将盒皮120压贴在盒板110上的边部涂胶面。c2楔面驱动部与c1楔面驱动部相互靠近构成楔面驱动配合,是用于实现调节a1板710进行正向和反向转动,a1板710的转动动作发生在b平移驱动组件驱使定位支架进行平移运动的过程中,即b平移驱动组件驱使定位支架进行平移运动是主运动,a1板710的转动是在定位支架滑移运动基础上的子运动,子运动的动作实现要与主运动的动作实现相适应。
c1楔面驱动部的楔形面上设置有b滑槽,b滑槽的槽口沿远离槽底的方向呈收口状设置,c2楔面驱动部的楔形面上设置有与b滑槽适配的b滑台,b滑台与b滑槽之间在c1楔面驱动部与c2楔面驱动部相对滑动时构成滑动导向配合;b复位部为设置在c2楔面驱动部与定位支架之间的压缩弹簧,压缩弹簧用于驱使c1楔面驱动部与c2楔面驱动部沿盒皮120身长方向相互远离运动、槽形件反向转动。由于b滑台与b滑槽之间在c1楔面驱动部与c2楔面驱动部相对滑动时构成滑动导向配合,且b滑槽的槽口沿远离槽底的方向呈收口状设置,因此能限制c2楔面驱动部沿垂直于楔面的方向远离c1楔面驱动部移动,因此可以利用压缩弹簧的恢复力,驱使c2楔面驱动部和槽形件同步复位。
b复位部在实施时可以包括扭簧和压缩弹簧,扭簧设置在槽形件与定位支架铰接处,用于驱使槽形件反向翻转、以及使得c1楔面驱动部与c2楔面驱动部紧贴布置;压缩弹簧用于驱使c1楔面驱动部与c2楔面驱动部沿盒皮120身长方向相互远离运动。即c2楔面驱动部通过压缩弹簧的弹性恢复力进行复位,而槽形件通过扭簧的弹性扭转复位作用力进行复位。
b平移驱动组件为气缸的活塞杆构成,活塞杆与c2楔面驱动部相连,气缸的缸身与机架相连。
参阅图4和图5,为了便于容置部230处已组装完成的包装盒100移出,容置部230的下边部具有供盒板110向下移出容置部230的移出口231,盒板110从容置部230的外侧沿盒板110厚度方向水平移至容置部230内。其实施原理为:当塑型模芯200处于压紧待组装的盒皮120上时,可以沿盒板110厚度方向向容置部230内水平输送盒板110,容置部230对盒板110与盒皮120的相对位置进行限定;当盒皮120与盒板110组装完毕之后,通过将包装盒100相对于塑型模芯200下移,可以实现对已组装完成的包装盒100的卸载。
参阅图1至图7,本申请实施例提供了一种能够适应不同尺寸的包装盒组装的塑形压贴方法,所述包装盒100由两间隔布置的硬质的盒板110和包裹在盒板110边部的柔性的盒皮120组成,采用塑型模芯200上相对布置的容置部230容纳和定位盒板110,采用塑型模芯200上的塑型面对盒皮120进行塑形,采用辊压机构对盒皮120的边部涂胶处与盒板110的涂胶处进行辊压粘合,包括如下步骤:
步骤一,获取待组装的盒板110的尺寸、盒皮120的尺寸,其中,所述盒板110的尺寸包括盒板110的宽度、高度、厚度中的一者或者几者,所述盒皮120的尺寸包括盒皮120的宽度、长度中的一者或两者;
步骤二,根据所获得的盒板110的尺寸、盒皮120的尺寸,调节塑型模芯200上的容置部230的尺寸和/或两容置部230的间距;
步骤三,将待组装的盒板110、盒皮120分别向组装工位输送;
步骤四,启动塑型模芯200将处于组装工位的盒皮120压紧,将两个盒板110分别移送至处于组装工位的盒皮120的两侧边部涂胶处,并由塑型模芯200对盒板110进行定位;
步骤五,将盒皮120的两侧边部分别与两个盒板110的板侧边进行挤压粘合,组装成包装盒100。
通过采用上述方法能够满足不同尺寸的包装盒100的组装需求,而且有利于降低生产成本。
塑型模芯200包括沿盒板110厚度方向相对布置的两个塑型子模芯,两个塑型子模芯沿盒板110厚度方向活动安装,两个容置部230分别位于两个塑型子模芯上;在步骤二中,通过调节两个塑型子模芯中的一者或两者移动,实现调节两容置部230的间距。
具体地,通过调节两个塑型子模芯同步靠近/远离,实现调节两容置部230的间距。
塑型子模芯包括两个相对布置的模芯子部,两个模芯子部沿盒板110的宽度方向活动安装,容置部230分为两个容置子部,两个容置子部分别位于同一塑型子模芯中的两个模芯子部上;在这样的应用场景下,通过调节各塑型子模芯中的两个模芯子部中的一者或两者移动,实现调节容置部230沿盒板110宽度方向的尺寸。
具体地,通过调节各塑型子模芯中的两个模芯子部同步靠近/远离移动,实现调节容置部230沿盒板110宽度方向的尺寸。
盒板110在容置部230内立状布置,容置部230的上侧形成有限位结构,限位结构由两个相对布置的子限位结构组成,两个子限位结构分别位于同一容置部230的两个容置子部的上侧;在此应用场景下,采用同一容置部230处的两个子限位结构,对容置部230处的盒板110沿板宽方向的移动进行限位;通过调节同一塑型子模芯中的两个模芯子部的间距,使得容置部230适配不同宽度尺寸的盒板110。
同一容置部230处的两个子限位结构,还能对容置部230处的盒板110沿板高方向的移动进行限位;将同一容置部230处的两个子限位结构分别沿盒板110的高度方向活动安装;通过同步调节同一容置部230处的两个子限位结构沿板高方向移动,实现调节容置部230沿盒板110高度方向的尺寸。
在塑型模芯200的下侧设有水平布置、能够相互靠近和远离的两定位板,定位板上设有对盒皮120进行定位的定位浅槽,两定位板相靠近的一端分别安装沿盒板110高度方向浮动的压辊,两压辊构成辊压机构,压辊的辊长方向与盒皮120的宽度方向相一致;将盒皮120的两侧边部分别与两个盒板110的板侧边进行挤压粘合的方法为:在盒皮120进入定位浅槽之前,调节两压辊的辊面下移至定位浅槽的槽底面以下,对盒皮120的移入进行避让;在塑型模芯200下移将处于组装工位的盒皮120压紧、并对盒板110进行定位之后,调节两定位板相互远离,同时调节两压辊的辊面凸出于定位浅槽的槽底面,以对盒皮120与盒板110的下侧板边进行挤压粘合;当定位板移动至两压辊恰好分别能够与盒板110的两侧板边紧密贴压时,停止移动定位板、并保持两定位板之间的间距不变,然后,调节模芯继续下移,通过两压辊将盒皮120分别压贴在盒板110的两侧板边上。
进一步地,还包括步骤六,将组装好的包装盒100从塑型模芯200上卸载下来。
容置部230的下边部具有供盒板110向下移出容置部230的移出口231;步骤四还包括:在盒板110输送路径的末端,通过将盒板110从容置部230的外侧沿板厚方向水平移至容置部230内,实现将盒板110移送至组装工位的盒皮120的两侧边部涂胶处;步骤六具体包括:通过将组装好的包装盒100相对于塑型模芯200下移,实现对包装盒100的卸载。
塑型模芯200上的塑型面位于两容置部230之间,塑型面上具有沿盒板110宽度方向间隔布置的两外模面,外模面立状布置且具有沿盒板110宽度方向移动的自由度;步骤六还包括:在组装成包装盒100以后,调节模芯的外模面沿盒板110宽度方向朝模芯的内部收拢,以允许包装盒100从模芯上卸下。
以上所述仅是本发明的优选实施方式,应当指出,对于本技术领域的普通技术人员来说,在不脱离本发明原理的前提下,还可以作出若干改进和润饰,这些改进和润饰也应视为本发明的保护范围。本发明中未具体描述和解释说明的结构、装置以及操作方法,如无特别说明和限定,均按照本领域的常规手段进行实施。
起点商标作为专业知识产权交易平台,可以帮助大家解决很多问题,如果大家想要了解更多知产交易信息请点击 【在线咨询】或添加微信 【19522093243】与客服一对一沟通,为大家解决相关问题。
此文章来源于网络,如有侵权,请联系删除


