一种适用于连续作业的多层门板热压胶合机的输送装置的制作方法



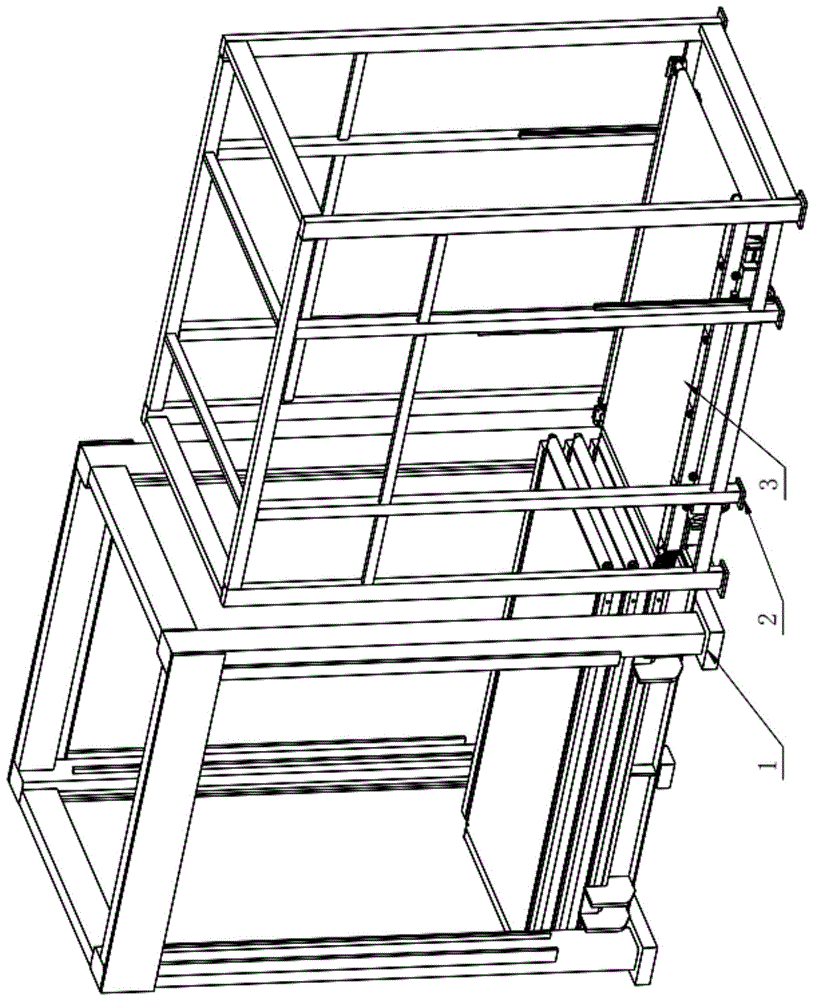
本发明属于输送装置技术领域,涉及一种用于胶合机的输送装置,特指一种适用于连续作业的多层门板热压胶合机的输送装置。
背景技术:
目前,用于门板坯胶合的设备-多层热压机带摩擦情况下为硬输送,且输送装置存在转换繁琐,且对有漆面及多种规格厚度的门板输送不能进行精度控制也不准。
技术实现要素:
为克服现有输送在多层门板热压胶合设备实际使用过程中存在的上述缺陷,本发明创造的目的是提供一种可以满足多层压机无摩擦自动流水式输送之目的。
本发明创造解决上述输送缺陷的问题所采用的技术方案,它包括对应安装在主机进口和出口的进出输送线架、输送装置及辅助线架,所述的输送装置包括安装在主机上的层叠放置的热压板总成,所述的热压板总成包括固定安装在热压板上的主出调节辊、主出固定辊、主进料固定辊、主进料辊及绕主进料辊、主出调节辊圆周旋转且绕主进料固定辊与主出固定辊圆周外切线涨紧旋转的主机输送带,所述主机输送带与输送装置之间安装有进线摩擦辊。
本发明创造进一步方案,所述的输送装置上还包括可沿齿条上下方向运动的进线升降架,固定安装在进线升降架上的轴承座、直线导轨副、升降减速电机、主动链轮、升降架滚轮,安装在轴承座上的传动轴b、传动轴a及其上的传动齿轮和传动链轮,所述传动齿轮与固定安装在进出输送线架上的齿条上下方向相啮合,同时升降架滚轮沿齿条的侧面上下运动;传动链轮与升降减速电机上的主动链轮通过链条的联接传动;进线升降架上的直线导轨副上联接有进线输送架,进线输送架的另一端固定安装有气缸,进线输送架上固定安装有输送架滚轮,进线输送架通过气缸气压与输送架滚轮的双重作用使其沿直线导轨副的左右方向运动;所述的进线输送架上固定安装有进线固定座、进线传动辊、进线摩擦辊、进线微调轴承、进线传动轮、进线输送减速电机、主动轮、进线过渡辊、调节轴承、进线调节辊、进线输送带、调节螺栓,进线输送减速电机上的主动轮与进线传动轮通过同步带的联接传动将进线输送带及其上的门板c输送进主机中的热压板总成上。
本发明创造进一步方案,所述的输送装置上的主动轮的运动将带动进线输送带旋转运动,进线输送带将其上的未热压的门板c输送进主机热压板总成中,同时进线输送架上的气缸将转动中的进线输送带、进线摩擦辊摩擦旋转并带动主进料辊圆周方向上的主机输送带同步旋转将热压后的门板c带出热压板总成的热压区域。
本发明创造进一步方案,所述的输送装置、辅助线架与工厂的流水线对接后形成完整的连续作业模式。
采用上述结构后,与现有技术相比有如下优点:
1.主机热压板总成的输送结构采用此结构后,将输送带上下两层都布置在加热板同一个平面上,通过安装在热压板两侧的主进料辊、主进料固定辊、主出固定辊、主出调节辊对输送带进行涨紧,从而可达到热压板中的某一层打开热压窗口时,通过输送带可顺利的将热压后的门板送出、且运动中又不影响相邻上下层的保持热压中的状态。由于采用耐高温带做为本机的输送带,它的特点是耐高温达350℃、不易粘附任何物质、摩擦系数低、高绝缘性能又防火阻燃,可有效地解决免漆门的门坯在运动中被刮伤而导致对产品质量的影响。
2.由于采用新式的输送装置后,可有效地减少主机的整体高度又能顺畅的将待热压的门板输入或将热压中的门板输出,采用进出料辅助线可更好的转换门板在主机与外接流水线的连续作业。
附图说明
图1为本发明创造的整机立体配合位置示意图。
图2为本发明创造的输送装置立体示意图。
图3为本发明创造的输送装置主视图。
图4为本发明创造的输送装置俯视图。
图5为本发明创造的输送装置结构图。
图6为可输送门坯的种类图。
其中1主机,2进料输送线架,3输送装置,301主机输送带,302主出调节辊,303主出固定辊,304热压板,305主进料固定辊,306主进料辊,307进线传动辊,308调节螺栓,309进线输送架,310输送架滚轮,311传动轴b,312轴承座,313升降架滚轮,314直线导轨副,315进线升降架,316进线过渡辊,317齿条,318传动齿轮,319气缸,320调节轴承,321进线调节辊,322进线输送带,323传动轴a,324链条,325升降减速电机,326主动链轮,327传动链轮,328进线输送减速电机,329主动轮,330进线传动轮,331进线微调轴承,332进线固定座,333进线摩擦辊,c1带防撬边的子门,c2带防撬边的母门,c3普通门。
具体实施方式
图1至图5所示,为本发明创造的具体实施方案,它包括对应安装在主机1进口和出口的进出输送线架2、输送装置3及辅助线架,所述的输送装置3包括安装在主机1上的层叠放置的热压板总成,所述的热压板总成包括固定安装在热压板304上的主出调节辊302、主出固定辊303、主进料固定辊305、主进料辊306及绕主进料辊306、主出调节辊302圆周旋转且绕主进料固定辊305与主出固定辊303圆周外切线涨紧旋转的主机输送带301,所述主机输送带301与输送装置3之间安装有进线摩擦辊333。
为了更好、更稳定的结构和平稳性且连续作业,所述的输送装置3还包括沿固定安装在进出输送线架2上的齿条317上下方向相啮合运动的进线升降架315,固定安装在进线升降架315上的轴承座312、直线导轨副314、升降减速电机325、主动链轮326、升降架滚轮313,安装在轴承座312上的传动轴b311、传动轴a323及其上的传动齿轮318、传动链轮327,所述的传动齿轮318与固定安装在进出输送线架2上的齿条317上下方向相啮合的同时升降架滚轮313沿齿条317的侧面上下运动;传动链轮327与升降减速电机325上的主动链轮326通过链条324的联接传动;进线升降架315上的直线导轨副314上联接有进线输送架309,进线输送架309的另一端固定安装有气缸319,进线输送架309上左右前后方向固定安装有输送架滚轮310,进线输送架309通过气缸319气压与输送架滚轮310的双重作用下沿直线导轨副314的左右方向运动;所述的进线输送架309上固定安装有进线固定座332、进线传动辊307、进线摩擦辊333、进线微调轴承331、进线传动轮330、进线输送减速电机328、主动轮329、进线过渡辊316、调节轴承320、进线调节辊321、进线输送带322、调节螺栓308,进线输送减速电机328上的主动轮329与进线传动轮330通过同步带的联接传动将进线输送带322及其上的门板c输送进主机1中的热压板总成上。
为了更好的减少人工及提高机床自动化程度及便于更好的上下料及外接流水线,所述的输送装置3上的主动轮329的旋转运动将进线输送带322及其上的未热压的门板c输送进主机1热压板总成中的同时进线输送架309上的气缸319将转动中的进线输送带322、进线摩擦辊333摩擦旋转并带动主进料辊306圆周方向上的主机输送带301同步旋转将热压后的门板c带出热压板总成的热压区域。所述的输送装置3、辅助线架与工厂的流水线对接后形成完整的连续作业模式。
本发明创造工作过程如下,以图1、2、4、5、6为例:
以连续作业c3普通门并结合整机其他机构为例,整机都处于原始状态时:主机1上的插抬机构上的插销退回平衡架内且平衡架处于主机上距地面最近的第一组热压板总成与第二组热压板总成中间时;输送装置3均处于进出料输送线架2的最下方;进出料辅助线处于待机状态。
第一步:外接流水线将待热压的门板c3输送到右侧的进出料辅助线上;经光电感应检测后,启动输送装置3上的升降减速电机325上升到与右侧的进出料辅助线的上平面平齐;启动进出料辅助线上的输送减速电机带动输送带将待热压的门板c3输送到输送装置3上,同步输送装置3上的进线输送减速电机328启动将待热压的门板c3接入输送装置3内;同步插抬机构上的伺服电机驱动带动平衡架及其上的插销接近地面往上第二组热压板总成的下平面一定距离、插销通过气缸的作用下伸出至第二组热压板总成的下平面,伺服电机驱动平衡架及其上的插销、热压板总成、承压板向上抬高到一定距离;同步输送装置3上的升降减速电机325下降到与左侧主机的第一组热压板总成的上平面平齐;同步输送装置3上的进线输送减速电机328启动将进线输送带322及其上的待热压的门板c3输送进主机1热压板总成中的同时进线输送架309上的气缸319将转动中的进线输送带322、进线摩擦辊333摩擦旋转并带动主进料辊306圆周方向上的主机输送带301同步旋转将待热压的门板c3输送到热压板总成的指定位置(并可同步将热压后的门板c3输出主机1至主机左侧的输送装置3上);经光电感应检测后,插抬机构上的伺服电机驱动带动平衡架及其上的插销、热压板总成、承压板向下下降到一定距离成待机状态,热压板总成上的待热压的门板c3在上部的热压板总成及上面的承压板的重力作用下成热压固化成型中状态,同步插销通过气缸的作用下退回初始状态;同时进线输送架309上的进线输送带322、进线摩擦辊333通过气缸319的作用下使进线摩擦辊333脱离主机输送带301;经光电感应检测后,同步输送装置3上的升降减速电机325上升到与右侧的进出料辅助线的上平面平齐成待机状态;
重复第一步骤直至将热压板总成上方的空间全部装满。
一种适用于连续作业的多层门板热压胶合机的输送装置上的相关机构都回归原始状态:即主机1上的插抬机构上的插销退回平衡架内且平衡架处于主机上距地面最近的第一组热压板总成与第二组热压板总成中间时;输送装置3均处于进出料输送线架2的最下方;进出料辅助线处于待机状态。
以上所述,只是本发明创造的具体实施例,并非对本发明创造作出任何形式上的限制,在不脱离本发明创造的技术方案基础上,所作出的简单修改、等同变化或修饰,均落入本发明创造的保护范围。
起点商标作为专业知识产权交易平台,可以帮助大家解决很多问题,如果大家想要了解更多知产交易信息请点击 【在线咨询】或添加微信 【19522093243】与客服一对一沟通,为大家解决相关问题。
此文章来源于网络,如有侵权,请联系删除


