一种医疗废物等离子熔融处置系统的制作方法



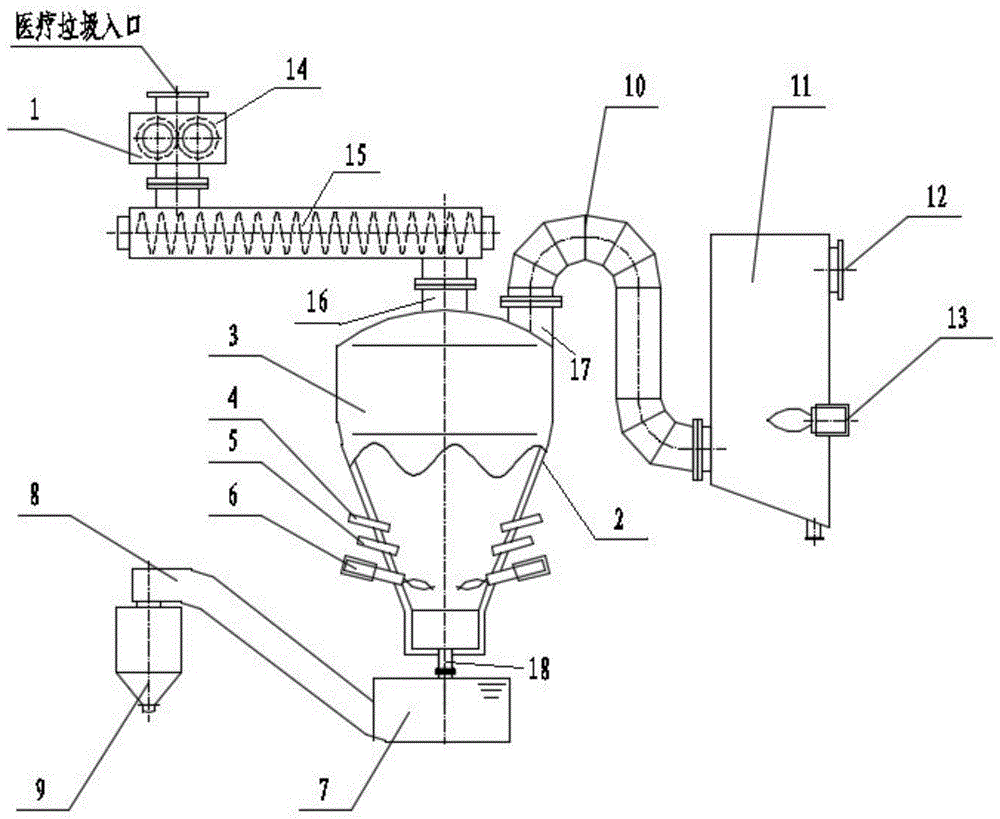
本实用新型属于危险废物处理技术领域,尤其是一种医疗废物等离子熔融处置系统。
背景技术:
医疗保健行业正在飞速发展,伴随而来的是医疗废物的显著增加。据世界卫生组织统计,发达国家每张病床每天产生的医疗废物约有0.5kg,而发展中国家每张病床每天可以产生0.5-2.5kg医疗废物。美国每年产生的医疗废物总量约为260万吨,而印度每天产生的医疗废物就达到了500吨。
医疗废物来源广泛,很难准确、严格地统计产生量。相关研究根据医疗机构的病床数、病床使用率以及单位病床平均每天产生的医疗废物量估算,我国2018年的医疗废物总产量已经突破206.01万吨,医疗废物市场规模达到76.9亿元。预计到2023年,医疗废物处理市场规模将达到107.37亿元,同时产量达到249.56万吨。
医疗废弃物的产生量在大幅提升,进一步加剧处理医疗废弃物的压力。对于大量产生的医疗废物,目前普遍采用的方式是小规模焚烧或卫生填埋。
然而,世界卫生组织2004年的政策文件和“斯德哥尔摩公约”强调,需要考虑医疗废物焚烧带来的颗粒物、重金属、酸性气体、一氧化碳、病原体、二噁英等风险,以及垃圾填埋可能引起的水源污染问题。事实上,许多工业化国家正在逐步淘汰医疗焚烧炉并探索不产生任何二恶英的技术。美国、爱尔兰、葡萄牙、加拿大和德国等国已完全关闭或暂停医疗废物焚烧炉。
目前,我国沿用的仍然是2003年推行的以集中焚烧为主的单一处置模式。可以预见,医疗废物产量每年在迅速增长,如若继续按照传统单一的集中焚烧处置,而不是探索新的更加多元灵活的模式来解决,未来的医废处置行业负荷率只会越来越高,由医疗废物导致的一系列问题也将越来越严重。
等离子熔融处置作为一种近年来得到广泛应用的技术,因其具有更高的温度和能量密度,在处理医疗垃圾废物时能够彻底摧毁有害物质,通过温度控制,也能避免二噁英、呋喃等烟气中有害物质的生成,最终产物可以实现玻璃化并进行资源化利用,因此备受关注。
目前,虽然也存在一些医疗废物处理设备,但是主要存在如下问题:
①大颗粒卡料,上料管容易堵塞,设备上料系统密封不好,容易有气体逸出。
②原来两段式结构,上小下大的等离子炉体结构,等离子炬离物料远,热利用率不高。核心熔融温度不能调节,容易造成能源浪费。
③出渣系统不易控制,不能实现自动化操作,环境不友好。
因此,亟需一种或几种新的相关设备。
技术实现要素:
本实用新型的目的在于克服现有技术的不足之处,提供一种医疗废物等离子熔融处置系统。
本实用新型解决其技术问题是采取以下技术方案实现的:
一种医疗废物等离子熔融处置系统,所述系统包括医疗垃圾预处理系统、等离子炬熔融炉、烟气管道、二燃室和熔融渣出渣系统,所述医疗垃圾预处理系统、熔融渣出渣系统均与等离子炬熔融炉相连接设置,所述二燃室通过烟气管道与等离子炬熔融炉相连接设置;
所述二燃室上相连接设置二燃室烟气出口和二燃室烧嘴,该二燃室烟气出口设置于二燃室的顶部或顶部一侧,该二燃室烧嘴设置于二燃室的中下部,且其输出端设置于二燃室内;所述医疗垃圾预处理系统包括相连接设置的剪切式破碎机和混料机,该剪切式破碎机能够输入医疗废物且能够对其进行剪切处理,所述混料机能够对剪切式破碎机处理后的医疗废物进行混合处理;所述等离子炬熔融炉包括熔融炉本体、废物输入口、烟气出口和废渣出口,该熔融炉本体沿竖直方向设置,所述废物输入口、烟气出口间隔紧密相连通设置于熔融炉本体的顶部,所述废渣出口相连通紧密设置于熔融炉本体的底部;所述熔融渣出渣系统包括捞渣机、捞渣机水箱和熔融渣仓,所述捞渣机的输入端与捞渣机水箱相连接设置,该捞渣机的输出端与熔融渣仓相连接设置,所述捞渣机水箱设置在废渣出口的正下方。
而且,所述剪切式破碎机的出料粒度为10-30mm。
而且,所述混料机为桨叶式混料机。
而且,所述剪切式破碎机、混料机均为壳体式微负压操作设备。
而且,所述等离子炬熔融炉还包括二次风系统、一次风系统和等离子炬,所述二次风系统、一次风系统和等离子炬均设置在熔融炉本体上,且与熔融炉本体相连通设置。
而且,所述二次风系统、一次风系统和等离子炬均对称设置2个。
而且,所述熔融炉本体采用上段圆柱形、下段锥形的组合体结构。
而且,所述熔融炉本体采用竖式壳体结构,内部紧密设置有耐火材料层。
而且,所述耐火材料层为通过浇注料连接设置在一起的铝铬材料。
而且,所述熔融炉本体内部由上至下依次设置烘干段、预热段和熔融段。
本实用新型取得的优点和积极效果是:
1、本系统对原料进行定尺破碎、出料粒度均匀,混料机对原料进行精准混合,预处理后的原料更加适合等离子炬熔融炉处置,熔融渣品质能够得到保证,烟气组分更加合理可控。
2、本系统的等离子炬熔融炉采用竖式壳体结构,可以配合2套对称布置的一次风系统、二次风系统及等离子炬作为热源,熔融炉内部医疗垃圾物料分3段,核心温度可调可控,熔融处置更加彻底,设备更加节能。
3、本系统的等离子炬熔融炉的烟气通过二次燃烧处置,充分焚毁有机物、有害物质,二噁英、呋喃的排放高于欧盟标准(0.1ngteq/nm3)。
4、本系统的熔融渣通过水箱急冷成颗粒,用捞渣机捞出至熔融渣仓,机械化程度高、环境友好、可实现自动化控制。
附图说明
图1为本实用新型的一种结构连接示意图;
图2为本实用新型使用时的一种工艺流程图。
具体实施方式
下面结合通过具体实施例对本实用新型作进一步详述,以下实施例只是描述性的,不是限定性的,不能以此限定本实用新型的保护范围。
本实用新型未具体详细描述的结构,均可以理解为本领域的常规结构。
一种医疗废物等离子熔融处置系统,如图1和图2所示,所述系统包括医疗垃圾预处理系统1、等离子炬熔融炉2、烟气管道10、二燃室11和熔融渣出渣系统,所述医疗垃圾预处理系统、熔融渣出渣系统均与等离子炬熔融炉相连接设置,所述二燃室通过烟气管道与等离子炬熔融炉相连接设置;
所述二燃室上相连接设置二燃室烟气出口12和二燃室烧嘴13,该二燃室烟气出口设置于二燃室的顶部或顶部一侧,该二燃室烧嘴设置于二燃室的中下部,且其输出端设置于二燃室内;所述医疗垃圾预处理系统包括相连接设置的剪切式破碎机14和混料机15,该剪切式破碎机能够输入医疗废物且能够对其进行剪切处理,所述混料机能够对剪切式破碎机处理后的医疗废物进行混合处理;所述等离子炬熔融炉包括熔融炉本体3、废物输入口16、烟气出口17和废渣出口18,该熔融炉本体沿竖直方向设置,所述废物输入口、烟气出口间隔紧密相连通设置于熔融炉本体的顶部,所述废渣出口相连通紧密设置于熔融炉本体的底部;所述熔融渣出渣系统包括捞渣机8、捞渣机水箱7和熔融渣仓9,所述捞渣机的输入端与捞渣机水箱相连接设置,该捞渣机的输出端与熔融渣仓相连接设置,所述捞渣机水箱设置在废渣出口的正下方。
在本实施例中,所述剪切式破碎机的出料粒度为10-30mm。
在本实施例中,所述混料机为桨叶式混料机。
在本实施例中,所述剪切式破碎机、混料机均为壳体式微负压操作设备。
在本实施例中,所述等离子炬熔融炉还包括二次风系统4、一次风系统5和等离子炬6,所述二次风系统、一次风系统和等离子炬均设置在熔融炉本体上,且与熔融炉本体相连通设置。
较优地,所述二次风系统、一次风系统和等离子炬均对称设置2个。
在本实施例中,所述熔融炉本体采用上段圆柱形、下段锥形的组合体结构。
在本实施例中,所述熔融炉本体采用竖式壳体结构,内部紧密设置有耐火材料层(图中未示出),较优地,所述耐火材料层为通过浇注料连接设置在一起的铝铬材料。
在本实施例中,所述熔融炉本体内部由上至下依次设置烘干段、预热段和熔融段。
本医疗废物等离子熔融处置系统的工作原理及使用方法可以如下:
因医疗垃圾来料尺寸不规则,因此,本医疗废物等离子熔融处置系统先将来料经过剪切式破碎机处置,破碎后的物料进入混料机进行搅拌混合,物料经过混合后进入等离子炬熔融炉进行熔融处置。
医疗垃圾预处理系统设备可以均为壳体式微负压操作,避免有害气体外溢。此外,系统还设置氮气密封及置换口,保证运行及检修安全。
本等离子炬熔融炉可以采用上段圆柱、下段锥形的组合体结构,竖式布置,内部砌筑耐火材料,耐火材料优选铝铬砖及浇注料。等离子炬熔融炉热源包含对称的2套一次风系统、二次风系统及等离子炬,均通过熔融炉壳体插入医疗垃圾物料内部,直接对物料进行加热。医疗垃圾物料由上至下分别经历烘干段、预热段、熔融段。烘干段温度为120-220℃,去除医疗垃圾物料中的水分。预热段温度为220-1200℃,该阶段医疗垃圾物料由固态向熔融态开始转变,有害物质及有机物开始分解。为了彻底焚毁有害物质,并适度节能,熔融段根据物料需求可以在1200-3000℃区间内进行调整。
等离子炬熔融炉的烟气通过烟气管道抽出至二燃室,二燃室可以设1个烧嘴,将烟气再次燃烧。其燃烧温度大于1100℃,烟气停留时间不小于2s,确保进入二燃室烟气中的微量有机物及二噁英得以充分分解。二燃室出来的烟气再经过烟气处理设备进行余热利用、烟气治理后即可达标排放。
等离子炬熔融炉的熔融渣由设备底部排渣口排出。熔融渣进入捞渣机水池箱进行粒化及冷却,冷却后的粒状熔融渣再通过捞渣机捞起至熔融渣仓内储存。经过等离子炬熔融炉高温处置过的医疗垃圾,其熔融渣浸出毒性满足《危险废物鉴别标准浸出毒性鉴别》(gb5085.3-2007)的要求,可以作为市政路基和基层混合料、混凝土河砂替代品等资源化使用。
尽管为说明目的公开了本实用新型的实施例,但是本领域的技术人员可以理解:在不脱离本实用新型及所附权利要求的精神和范围内,各种替换、变化和修改都是可能的,因此,本实用新型的范围不局限于实施例所公开的内容。
起点商标作为专业知识产权交易平台,可以帮助大家解决很多问题,如果大家想要了解更多知产交易信息请点击 【在线咨询】或添加微信 【19522093243】与客服一对一沟通,为大家解决相关问题。
此文章来源于网络,如有侵权,请联系删除


