一种解耦燃烧机械炉排炉的制作方法



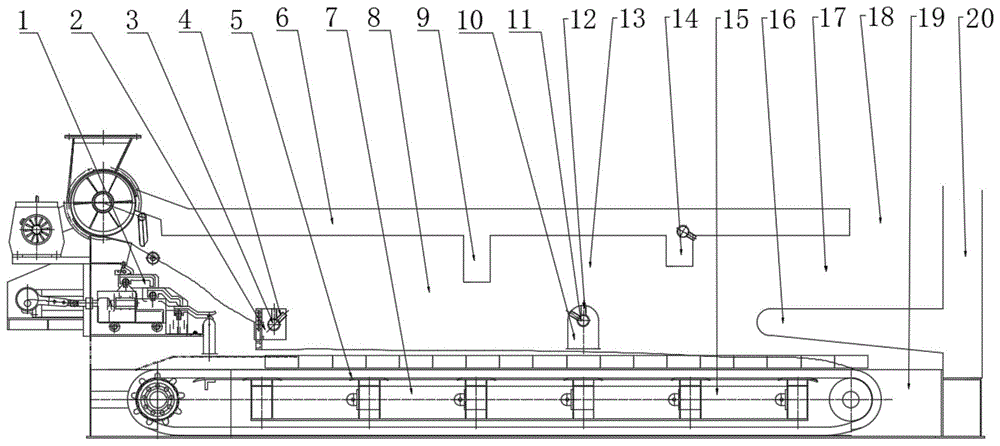
本实用新型属于燃烧设备技术领域,涉及一种解耦燃烧机械炉排炉。
背景技术:
传统的燃煤工业锅炉主要采用层燃方式且多为链条炉,普遍存在燃烧效率低、污染物排放量高等问题,因此需要研发相关减排技术,来降低nox的排放量,如低氧燃烧技术、烟气再循环燃烧技术、空气分及燃烧技术等,但上述技术的实现会受到燃煤锅炉自身结构及运行方式的限制,因此在改进燃烧技术的同时还需要对燃烧设备进行改进,以充分发挥新型燃烧技术的优势。
传统的机械炉排炉是一种常用的燃煤锅炉,其采用炉膛辐射加热燃料层上部的点火方式,高温高氧的炉膛出口区域必须靠近燃料点火区域,在炉膛的主要燃烧区,炉排上的燃料输送方向与炉膛中的烟气流向相反,因而无法有效实现燃烧初期为还原区,燃烧后期为氧化区的分区或分级燃烧,无法深度降低nox的排放;机械炉排炉再循环烟气与空气混合通入炉排下部,以通过降低空气中含氧量来降低nox的排放,但此种方式会显著降低了燃料的点火和燃尽速度,因而需大幅增加炉排长度和炉膛容积。
cn101650025a公开了一种解耦燃烧炉及解耦燃烧方法,包括热解气化室以及顺序设置在热解气化室下方的半焦燃烧区、焦炭燃烧区和燃尽区,该解耦燃烧炉还包括二次燃烧区、至少一个炉排、第一风口和第二风口,炉排推动燃料移动依次经过热解气化室、半焦燃烧区、焦炭燃烧区和燃尽区,所述二次燃烧区的下方与热解气化室的上方、焦炭区以及燃尽区流体连通,形成燃气通道,所述第一风口设置于燃气通道中,所述第二风口设置于二次燃烧区,均用于补充空气;该装置虽然能够较大程度解决热解速度较慢的问题,但共用一套炉排,且预燃速度较慢,当负荷提高时,容易造成预燃区燃烧中断,难以适用于大型燃烧设备。
cn102563614a公开了一种预燃式机械炉排解耦燃烧炉及其燃烧方法,包括炉体、主炉排和预燃炉排,炉体的内部设有燃烧室分隔墙,将炉体内部空间大致上分隔为上游的预燃室和下游的主燃烧室,主炉排位于炉体的下部,预燃室位于主炉排前段的上方,主燃烧室位于主炉排后段的上方,预燃室和主燃烧室通过分隔墙上方的烟气通道以及分隔墙下方的煤层通道相连通,预燃炉排位于预燃室内,且以一定倾角设置于主炉排上方,以使煤层沿该预热炉排运行至主炉排上;该装置主要是通过预燃室及预燃炉排的设置,来提高燃煤的燃烧效率,但并未对燃烧的还原区、氧化区进行明确的划分,仍然存在燃烧效果不佳的问题。
综上所述,对于机械炉排炉的解耦燃烧,需要对装置进行改进,以明确还原区、氧化区的划分及组分控制,以提高分级燃烧的效果,降低nox的排放。
技术实现要素:
针对现有技术存在的问题,本实用新型的目的在于提供一种解耦燃烧机械炉排炉,所述机械炉排炉通过与燃装置和主炉体的设置,尤其是主炉体中不同燃烧区以及分隔墙的设置,可以有效提高燃料燃烧时烟气、煤气以及调节风的扩散混合效果,控制炉膛内不同燃烧区域的稳定及燃烧气氛的过渡,实现机械炉排燃烧炉的深度分级燃烧。
为达此目的,本实用新型采用以下技术方案:
本实用新型提供了一种解耦燃烧机械炉排炉,所述机械炉排炉包括预燃装置和主炉体,所述预燃装置的出口和主炉体的入口相连;所述主炉体包括主炉排、顶拱、后墙以及由所述主炉排、顶拱和后墙围成的炉膛,所述预燃装置位于主炉排的前部上方,所述顶拱位于主炉排的上方,所述后墙位于主炉排的后部上方,所述后墙的下部与主炉排的后部之间设有排渣口,所述后墙的上部与顶拱的后部之间设有烟气出口;
所述后墙上设有向炉膛内延伸的后拱,所述后拱将炉膛的后部分为上下两部分,将排渣口和烟气出口隔开;所述主炉排的上方沿主炉排运动方向依次设有第一下隔墙和第二下隔墙,所述下隔墙与主炉排之间的区域为燃料通道,所述下隔墙与顶拱之间的区域为气体通道;所述第一下隔墙和第二下隔墙上独立地设有调节风管;
所述顶拱上沿气体流动方向依次设有向炉膛延伸的第一上隔墙和第二上隔墙,将下隔墙上方区域对应划分为气化燃烧区、过渡燃烧区和燃尽区,所述第一上隔墙的横向位置位于第一下隔墙和第二下隔墙之间,所述第二上隔墙的横向位置位于第二下隔墙后方。
本实用新型中,所述机械炉排炉的结构设计,先以预燃装置进行燃料的初步热解气化,使得燃料在炉排前端即可开始燃烧,再将主炉体中的气体区域划分为气化燃烧区、过渡燃烧区和燃尽区多个燃烧区域,再通过不同隔墙和调节风管的设计,控制不同燃烧区域的气氛组成,提高煤气、烟气及与调节风的扩散混合效果,在燃料氮主要转化阶段使炉膛形成的大范围还原性燃烧区更为稳定,并精确控制还原性气氛向氧化性气氛的过渡,减小燃尽区nox浓度的反弹,使得分区燃烧效果更为突出。
以下作为本实用新型优选的技术方案,但不作为本实用新型提供的技术方案的限制,通过以下技术方案,可以更好地达到和实现本实用新型的技术目的和有益效果。
作为本实用新型优选的技术方案,所述顶拱的前段与预燃装置的上部连接。
优选地,所述第一下隔墙设置于主炉排前端的上方,所述第一下隔墙上设有调节闸板。
优选地,所述第一下隔墙底部到主炉排的距离大于第二下隔墙到主炉排的距离。
本实用新型中,所述第一下隔墙上调节闸板的设置,可以有效调节主炉排上的半焦燃料层厚度,保障燃料层与下部通入的空气反应时,在适宜条件下进行气化燃烧,使之可以在燃料层下部燃烧产生co2,燃料层上部气化产生co。
而第二下隔墙与主炉排之间的距离控制,可调节进入后部炉排的半焦料层的厚度,保障半焦的能够燃尽,且有过量空气从半焦层穿过。
优选地,所述第一下隔墙和第二下隔墙之间的距离为主炉排长度的50~75%,比如50%、55%、60%、62%、65%、68%、70%、72%或75%等,但并不仅限于所列举的数值,该数值范围内其他未列举的数值同样适用。
作为本实用新型优选的技术方案,所述第一下隔墙的上部设有第一调节风管,所述第一调节风管连接有至少一支第一调节风喷管,例如一支、两支、三支或四支等。
优选地,所述第二下隔墙的上部设有第二调节风管,所述第二调节风管连接有至少一支第二调节风喷管,例如一支、两支、三支或四支等。
本实用新型中,第一下隔墙上设置第一调节风管,调节风能够经第一调节风喷管喷射进入气化燃烧区,通过调节还原区煤气组分和燃烧来调节组分的还原性;所述第一调节风喷管的角度可改变,从而改变调节风与气化燃烧区煤气的混合位置和组分分布。
同理,调节风经第二调节风喷管喷射进入过渡燃烧区,通过调节供氧量和燃烧来调节还原性气氛向氧化性气氛的过渡,减小燃尽区nox浓度的反弹;所述第二调节风喷管的角度可改变,从而改变调节风与气化燃烧区流入过渡燃烧区的气化煤气的气流混合位置和组分分布。
作为本实用新型优选的技术方案,所述第一上隔墙的底部到主炉排的距离是顶拱到主炉排的距离的1/3~2/3,例如1/3、2/5、1/2、3/5或2/3等,但并不仅限于所列举的数值,该数值范围内其他未列举的数值同样适用。
优选地,所述第二上隔墙的底部到主炉排的距离是顶拱到主炉排的距离的1/2~4/5,例如1/2、3/5、2/3、7/10、3/4或4/5等,但并不仅限于所列举的数值,该数值范围内其他未列举的数值同样适用。
本实用新型中,第一上隔墙和第二上隔墙的设置有利于气体燃烧区域的划分以及气体的混合,而第一上隔墙与炉排的距离小于第二上隔墙与炉排的距离,可以适应炉膛后出烟的烟气量前小后大的特点,以维持炉膛内烟气最佳的流速和压降。
作为本实用新型优选的技术方案,所述主炉排下方对应第一下隔墙和第二下隔墙之间的区域设有气化燃烧区风室。
优选地,所述主炉排下方对应第二下隔墙后方的区域设有燃尽区风室。
本实用新型中,主炉排的下方设置风室,可以向主炉排上的半焦提供气化燃烧或燃尽所需的空气,根据不同阶段的燃烧情况,来调节通入的空气量;所述风室的数量均可以设有多个,以便于根据半焦的燃烧情况调节主炉排上不同区域空气的通入量。
优选地,所述燃尽区设有燃尽风喷口,所述燃尽风喷口设置于顶拱的下部、后拱的前端或炉膛的侧墙上。
本实用新型中,为了燃尽区内燃料及烟气的充分燃烧,可另外设置燃尽风喷口,以维持燃尽区内的过量空气。
本实用新型还提供了一种采用上述机械炉排炉进行解耦燃烧的方法,所述方法包括以下步骤:
(1)固体燃料进行预燃,热解气化生成半焦和热解气化煤气;
(2)步骤(1)生成的半焦进入主炉排后随主炉排运动,发生气化燃烧反应;步骤(1)生成的热解气化煤气进入气化燃烧区,与半焦气化燃烧产生的煤气混合后进行还原性燃烧;
(3)步骤(2)所述还原性燃烧产生的烟气进入过渡燃烧区,在通风条件下与气化燃烧区后部产生的煤气混合燃烧;步骤(2)所述半焦经过第二下隔墙后,在气体作用下充分燃尽,得到固体炉渣;
(4)步骤(3)所述混合燃烧后产生的烟气在过量空气作用下充分燃尽,然后经烟气出口离开。
作为本实用新型优选的技术方案,步骤(1)所述固体燃料包括煤和/或生物质。
优选地,步骤(1)所述预燃在预燃装置内进行。
优选地,所述预燃装置采用下点火方式燃烧。
本实用新型中,燃料进行预燃,可实现初步热解气化,使得燃料在炉排前端即可开始燃烧,消除了炉排上的预热点火段,提高了炉排的利用率;所述燃料进行预燃的温度为500~1000℃,例如500℃、600℃、700℃、800℃、900℃或1000℃等,但并不仅限于所列举的数值,该数值范围内其他未列举的数值同样适用。
作为本实用新型优选的技术方案,步骤(2)所述半焦气化燃烧过程中从气化燃烧区风室通入空气。
本实用新型中,在第一下隔墙和第二下隔墙之间炉排上半焦进行气化燃烧,该阶段燃料含氮量较高,控制空气的通入量使之发生贫氧燃烧,生成的co含量较多,保持较高的还原性气氛,以减小燃料氮向nox的转化;而在后部分炉排上,燃料氮含量较少,此时需要通入过量空气,加速半焦的完全燃烧。
采用气化燃烧的方式,能够增加可处理的燃料层的厚度,增加空间室燃比例,提高后期燃料的燃尽速度,从而可减小炉排的长度和炉膛的体积;在还原区采用较厚的燃料层和产生更多的煤气,还可提高机械炉排炉分区燃烧的还原区气氛的稳定;而且,采用燃料气化燃烧有利于提高燃料的适应性,对燃料组分和不规则燃料的尺寸规格要求降低,可提高燃烧生物质和垃圾的性能;生物质挥发分含量高,垃圾主要污染物也在挥发分中,采用炉膛后部出烟,可显著增加挥发分在高温炉膛的停留时间,有利于挥发物质的燃尽。
优选地,步骤(2)所述气化燃烧区内通入由空气和循环烟气组成的混合气。
优选地,所述混合气由第一调节风管通入。
本实用新型中,从调节风管通入的一般是助燃空气与循环烟气的混合气,其中空气和循环烟气的比例可以调节,通过改变调节风的空气和烟气配比可在需氧量较小或不需补氧时保持调节风的刚度,实现调节风对气流的扰混作用;同时通过改变调节风的入射角度,可更精确调节不同区域的还原性气氛;调节风混入适量循环烟气也可增加还原性气氛均匀性,避免出现局部过氧;本实用新型改变了传统烟气再循环使用方式,不仅可保障燃料的燃尽速度和燃尽率,也减小了烟气再循环量和由此增加的能耗。
本实用新型中,第一调节风管通入的混合气中,助燃空气占进入炉膛总空气量的0~10%,循环烟气量占进入炉膛总空气量的0~10%。
优选地,步骤(2)所述还原性燃烧过程中nox被还原为n2。
优选地,步骤(2)所述气化燃烧区的过量空气系数为0.6~0.95,例如0.6、0.65、0.7、0.75、0.8、0.9或0.95等,但并不仅限于所列举的数值,该数值范围内其他未列举的数值同样适用。
本实用新型中,所述气化燃烧区的燃烧温度为700~1100℃,例如700℃、800℃、900℃、1000℃或1100℃等,但并不仅限于所列举的数值,该数值范围内其他未列举的数值同样适用。
作为本实用新型优选的技术方案,步骤(3)所述过渡燃烧区内通入由空气和循环烟气组成的混合气。
优选地,所述混合气由第二调节风管通入。
本实用新型中,第二调节风管的设置,通过助燃空气与循环烟气的混合气的喷入,除了上述两者比例、喷射角度等因素的作用,此处还可精确控制控制还原性气氛向氧化性气氛的过渡,避免气化燃烧区和燃尽区分不明显,影响各自燃烧效果的问题。
本实用新型中,第二调节风管通入的混合气中,助燃空气占进入炉膛总空气量的0~15%,循环烟气量占进入炉膛总空气量的0~15%。
优选地,步骤(3)所述过渡燃烧区的过量空气系数为0.85~1.1,例如0.85、0.9、0.95、1.0、1.05或1.1等,但并不仅限于所列举的数值,该数值范围内其他未列举的数值同样适用。
本实用新型中,所述过渡燃烧区的燃烧温度为800~1200℃,例如800℃、900℃、950℃、1000℃、1050℃、1100℃、1150℃或1200℃,但并不仅限于所列举的数值,该数值范围内其他未列举的数值同样适用。
优选地,步骤(3)经过第二下隔墙后的半焦厚度小于第二下隔墙前的半焦厚度。
本实用新型中,根据主炉排上前后燃烧反应的不同,其料层厚度也会发生不同,根据需要第一下隔墙和第二下隔墙之间的料层厚度是需要大于第二下隔墙之后的料层厚度的;整体来说,随着半焦的燃烧,沿主炉排的运动方向半焦厚基本是逐渐减小的。
优选地,步骤(3)所述半焦燃尽过程中从燃尽区风室通入空气。
作为本实用新型优选的技术方案,步骤(4)所述空气由燃尽区喷口通入。
优选地,步骤(4)所述燃尽区的过量空气系数为1.05~2,例如1.05、1.1、1.2、1.3、1.4、1.5、1.6、1.8或2等,但并不仅限于所列举的数值,该数值范围内其他未列举的数值同样适用。
本实用新型中,所述燃尽区的燃烧温度为1000~1400℃,例如1000℃、1100℃、1150℃、1200℃、1250℃、1300℃、1350℃或1400℃,但并不仅限于所列举的数值,该数值范围内其他未列举的数值同样适用。
与现有技术相比,本实用新型具有以下有益效果:
(1)本实用新型以预燃装置进行燃料的初步热解气化,使得燃料在炉排前端即可开始燃烧,实现机械炉排炉主燃烧区的燃料流向与烟气流向一致;
(2)本实用新型所述机械炉排炉的主炉体内通过划分不同燃烧区,设置不同隔墙与调节风,提高了炉膛内煤气、烟气及与调节风的扩散混合效果,在燃料氮主要转化阶段使炉膛形成的大范围还原性燃烧区更为稳定,组分更易控制,精确控制还原性气氛向氧化性气氛的过渡,减小燃尽区nox浓度的反弹,实现燃料的分级分区燃烧,燃烧效率可达到90%以上;
(3)本实用新型所述机械炉排炉的设计提高了炉排利用率和燃烧效率,增强了燃料适应性,减小了烟气再循环量和能耗。
附图说明
图1是本实用新型实施例1提供的解耦燃烧机械炉排炉的结构示意图;
其中,1-预燃装置,2-第一下隔墙,3-第一调节风管,4-第一调节风喷管,5-主炉排,6-顶拱,7-气化燃烧区风室,8-气化燃烧区,9-第一上隔墙,10-第二下隔墙,11-第二调节风管,12-第二调节风喷管,13-过渡燃烧区,14-第二上隔墙,15-燃尽区风室,16-后拱,17-燃尽区,18-烟气出口,19-排渣口,20-后墙。
具体实施方式
为更好地说明本实用新型,便于理解本实用新型的技术方案,下面对本实用新型进一步详细说明。但下述的实施例仅是本实用新型的简易例子,并不代表或限制本实用新型的权利保护范围,本实用新型保护范围以权利要求书为准。
以下为本实用新型典型但非限制性实施例:
实施例1:
本实施例提供了一种解耦燃烧机械炉排炉,所述机械炉排炉的结构示意图如图1所示,包括预燃装置1和主炉体,所述预燃装置1的出口和主炉体的入口相连;所述主炉体包括主炉排5、顶拱6、后墙20以及由所述主炉排5、顶拱6和后墙20围成的炉膛,所述预燃装置1位于主炉排5的前部上方,所述顶拱6位于主炉排5的上方,所述顶拱6的前段与预燃装置1的上部连接,所述后墙20位于主炉排5的后部上方,所述后墙20的下部与主炉排5的后部之间设有排渣口19,所述后墙20的上部与顶拱6的后部之间设有烟气出口18;
所述后墙20上设有向炉膛内延伸的后拱16,所述后拱16将炉膛的后部分为上下两部分,将排渣口19和烟气出口18隔开;所述主炉排5的上方沿主炉排5运动方向依次设有第一下隔墙2和第二下隔墙10,所述下隔墙与主炉排5之间的区域为燃料通道,所述下隔墙与顶拱6之间的区域为气体通道;所述第一下隔墙2和第二下隔墙10上独立地设有调节风管;
所述顶拱6上沿气体流动方向依次设有向炉膛延伸的第一上隔墙9和第二上隔墙14,将下隔墙上方区域对应划分为气化燃烧区8、过渡燃烧区13和燃尽区17,所述第一上隔墙9的横向位置位于第一下隔墙2和第二下隔墙10之间,所述第二上隔墙14的横向位置位于第二下隔墙10后方。
所述第一下隔墙2设置于主炉排5前端的上方,所述第一下隔墙2上设有调节闸板;所述第一下隔墙2底部到主炉排5的距离大于第二下隔墙10到主炉排5的距离;所述第一下隔墙2和第二下隔墙10之间的距离为主炉排5长度的70%。
所述第一下隔墙2的上部设有第一调节风管3,所述第一调节风管3连接有三支第一调节风喷管4;所述第二下隔墙10的上部设有第二调节风管11,所述第二调节风管11连接有三支第二调节风喷管12。
所述第一上隔墙9的底部到主炉排5的距离是顶拱6到主炉排5的距离的1/3,所述第二上隔墙14的底部到主炉排5的距离是顶拱6到主炉排5的距离的1/2。
所述主炉排5下方对应第一下隔墙2和第二下隔墙10之间的区域设有气化燃烧区风室7;所述主炉排5下方对应第二下隔墙10后方的区域设有燃尽区风室15。
所述燃尽区17设有燃尽风喷口,所述燃尽风喷口设置于后拱16的前端。
实施例2:
本实施例提供了一种解耦燃烧机械炉排炉,所述机械炉排炉包括预燃装置1和主炉体,所述预燃装置1的出口和主炉体的入口相连;所述主炉体包括主炉排5、顶拱6、后墙20以及由所述主炉排5、顶拱6和后墙20围成的炉膛,所述预燃装置1位于主炉排5的前部上方,所述顶拱6位于主炉排5的上方,所述顶拱6的前段与预燃装置1的上部连接,所述后墙20位于主炉排5的后部上方,所述后墙20的下部与主炉排5的后部之间设有排渣口19,所述后墙20的上部与顶拱6的后部之间设有烟气出口18;
所述后墙20上设有向炉膛内延伸的后拱16,所述后拱16将炉膛的后部分为上下两部分,将排渣口19和烟气出口18隔开;所述主炉排5的上方沿主炉排5运动方向依次设有第一下隔墙2和第二下隔墙10,所述下隔墙与主炉排5之间的区域为燃料通道,所述下隔墙与顶拱6之间的区域为气体通道;所述第一下隔墙2和第二下隔墙10上独立地设有调节风管;
所述顶拱6上沿气体流动方向依次设有向炉膛延伸的第一上隔墙9和第二上隔墙14,将下隔墙上方区域对应划分为气化燃烧区8、过渡燃烧区13和燃尽区17,所述第一上隔墙9的横向位置位于第一下隔墙2和第二下隔墙10之间,所述第二上隔墙14的横向位置位于第二下隔墙10后方。
所述第一下隔墙2设置于主炉排5前端的上方,所述第一下隔墙2上设有调节闸板;所述第一下隔墙2底部到主炉排5的距离大于第二下隔墙10到主炉排5的距离;所述第一下隔墙2和第二下隔墙10之间的距离为主炉排5长度的50%。
所述第一下隔墙2的上部设有第一调节风管3,所述第一调节风管3连接有一支第一调节风喷管4;所述第二下隔墙10的上部设有第二调节风管11,所述第二调节风管11连接有两支第二调节风喷管12。
所述第一上隔墙9的底部到主炉排5的距离是顶拱6到主炉排5的距离的2/3,所述第二上隔墙14的底部到主炉排5的距离是顶拱6到主炉排5的距离的4/5。
所述主炉排5下方对应第一下隔墙2和第二下隔墙10之间的区域设有气化燃烧区风室7;所述主炉排5下方对应第二下隔墙10后方的区域设有燃尽区风室15。
所述燃尽区17设有燃尽风喷口,所述燃尽风喷口设置于顶拱6的下部。
实施例3:
本实施例提供了一种解耦燃烧机械炉排炉的燃烧方法,所述方法在实施例1的机械炉排炉内进行,包括以下步骤:
(1)生物质燃料进入预燃装置1进行预燃,预燃温度为600℃,热解气化生成半焦和热解气化煤气;
(2)步骤(1)生成的半焦进入主炉排5后随主炉排5运动,发生气化燃烧反应,所述半焦气化燃烧过程中从气化燃烧区风室7通入空气;步骤(1)生成的热解气化煤气进入气化燃烧区8,与半焦气化燃烧产生的煤气混合后进行还原性燃烧,燃烧温度为900℃,气化燃烧区8通入由空气和循环烟气组成的混合气,过量空气系数为0.8,所述还原性燃烧过程中nox被还原为n2;
(3)步骤(2)所述还原性燃烧产生的烟气进入过渡燃烧区13,在通风条件下与气化燃烧区8后部产生的煤气混合燃烧,燃烧温度为1000℃,过渡燃烧区13通入由空气和循环烟气组成的混合气,过量空气系数为1.0;步骤(2)所述半焦经过第二下隔墙10后,在燃尽区风室15通入空气作用下充分燃尽,得到固体炉渣,从排渣口19排出;
(4)步骤(3)所述混合燃烧后产生的烟气在燃尽区喷口通入的过量空气作用下充分燃尽,燃尽温度为1200℃,过量空气系数为1.5,然后经烟气出口18离开。
本实施例中,采用所述机械炉排炉进行生物质燃料的解耦燃烧,燃烧效率可达到92%,烟气中nox含量满足排放要求,无需再额外处理。
实施例4:
本实施例提供了一种解耦燃烧机械炉排炉的燃烧方法,所述方法在实施例1的机械炉排炉内进行,包括以下步骤:
(1)粉煤燃料进入预燃装置1进行预燃,预燃温度为800℃,热解气化生成半焦和热解气化煤气;
(2)步骤(1)生成的半焦进入主炉排5后随主炉排5运动,发生气化燃烧反应,所述半焦气化燃烧过程中从气化燃烧区风室7通入空气;步骤(1)生成的热解气化煤气进入气化燃烧区8,与半焦气化燃烧产生的煤气混合后进行还原性燃烧,燃烧温度为1100℃,气化燃烧区8通入由空气和循环烟气组成的混合气,过量空气系数为0.6,所述还原性燃烧过程中nox被还原为n2;
(3)步骤(2)所述还原性燃烧产生的烟气进入过渡燃烧区13,在通风条件下与气化燃烧区8后部产生的煤气混合燃烧,燃烧温度为1200℃,过渡燃烧区13通入由空气和循环烟气组成的混合气,过量空气系数为0.85;步骤(2)所述半焦经过第二下隔墙10后,在燃尽区风室15通入空气作用下充分燃尽,得到固体炉渣,从排渣口19排出;
(4)步骤(3)所述混合燃烧后产生的烟气在燃尽区喷口通入的过量空气作用下充分燃尽,燃尽温度为1400℃,过量空气系数为1.5,然后经烟气出口18离开。
本实施例中,采用所述机械炉排炉进行粉煤燃料的解耦燃烧,燃烧效率可达到94%,烟气中nox含量满足排放要求,无需再额外处理。
实施例5:
本实施例提供了一种解耦燃烧机械炉排炉的燃烧方法,所述方法在实施例2的机械炉排炉内进行,包括以下步骤:
(1)生物质燃料进入预燃装置1进行预燃,预燃温度为500℃,热解气化生成半焦和热解气化煤气;
(2)步骤(1)生成的半焦进入主炉排5后随主炉排5运动,发生气化燃烧反应,所述半焦气化燃烧过程中从气化燃烧区风室7通入空气;步骤(1)生成的热解气化煤气进入气化燃烧区8,与半焦气化燃烧产生的煤气混合后进行还原性燃烧,燃烧温度为800℃,气化燃烧区8通入由空气和循环烟气组成的混合气,过量空气系数为0.9,所述还原性燃烧过程中nox被还原为n2;
(3)步骤(2)所述还原性燃烧产生的烟气进入过渡燃烧区13,在通风条件下与气化燃烧区8后部产生的煤气混合燃烧,燃烧温度为850℃,过渡燃烧区13通入由空气和循环烟气组成的混合气,过量空气系数为1.05;步骤(2)所述半焦经过第二下隔墙10后,在燃尽区风室15通入空气作用下充分燃尽,得到固体炉渣,从排渣口19排出;
(4)步骤(3)所述混合燃烧后产生的烟气在燃尽区喷口通入的过量空气作用下充分燃尽,燃尽温度为1100℃,过量空气系数为1.2,然后经烟气出口18离开。
本实施例中,采用所述机械炉排炉进行生物质燃料的解耦燃烧,燃烧效率可达到91%,烟气中nox含量满足排放要求,无需再额外处理。
对比例1:
本对比例提供了一种解耦燃烧机械炉排炉,所述机械炉排炉的结构参照实施例1中的结构,区别仅在于:所述主炉排的上方未设置第二下隔墙10及其调节风管,所述顶拱6上未设置第二上隔墙14,下隔墙上方区域的划分不包括过渡燃烧区13。
本对比例中,该机械炉排炉由于未设置过渡燃烧区,难以保障气相燃烧区域中还原性气氛向氧化性气氛的过渡,造成还原性燃烧区的还原性气氛稳定性较差,nox还原效率较低,在燃尽区富氧下nox浓度容易反弹,烟气中nox含量相对较高,无法达标排放。
综合上述实施例和对比例可以看出,本实用新型所述机械炉排炉以预燃装置进行燃料的初步热解气化,使得燃料在炉排前端即可开始燃烧;主炉体内通过划分不同燃烧区,设置不同隔墙与调节风,提高了炉膛内煤气、烟气及与调节风的扩散混合效果,在燃料氮主要转化阶段使炉膛形成的大范围还原性燃烧区更为稳定,组分更易控制,精确控制还原性气氛向氧化性气氛的过渡,减小燃尽区nox浓度的反弹,实现燃料的分级分区燃烧,燃烧效率可达到90%以上;所述机械炉排炉的设计提高了炉排利用率和燃烧效率,增强了燃料适应性,减小了烟气再循环量和能耗。
申请人声明,本实用新型通过上述实施例来说明本实用新型的详细装置,但本实用新型并不局限于上述详细装置,即不意味着本实用新型必须依赖上述详细装置才能实施。所属技术领域的技术人员应该明了,对本实用新型的任何改进,对本实用新型装置的等效替换及辅助装置的添加、具体方式的选择等,均落在本实用新型的保护范围和公开范围之内。
起点商标作为专业知识产权交易平台,可以帮助大家解决很多问题,如果大家想要了解更多知产交易信息请点击 【在线咨询】或添加微信 【19522093243】与客服一对一沟通,为大家解决相关问题。
此文章来源于网络,如有侵权,请联系删除


