一种适用于大流量的微型荷电喷雾燃烧器的制作方法



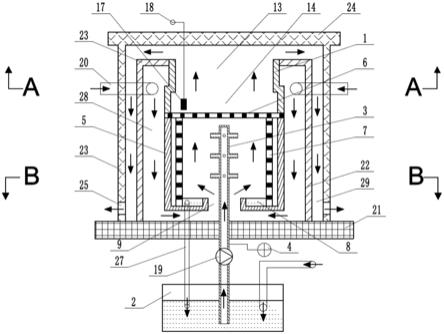
[0001]
本实用新型涉及微型液体燃烧装置技术领域,具体涉及一种适用于大流量的微型荷电喷雾燃烧器。
背景技术:
[0002]
近几十年来,随着mems微加工技术的快速发展,由于社会发展的需要,出现了大量的微小型医疗设备、微小型机械人、微小型飞行器以及便携式电子设备等微小型的装置。目前,绝大数的微小型设备和系统均由传统的化学电池供能,但传统化学电池存在能量密度低、使用时间短、充电时间长等缺点,不足以满足微型动力设备对续航能力的要求。而液体碳氢燃料能量密度是传统化学电池能量密度的几十倍,若将液体碳氢燃料作为微型燃烧器的燃料,可满足高能量密度、尺寸小、续航时间长等特点,有望代替化学电池。
[0003]
液体燃料燃烧速度主要取决于液体燃料的蒸发速度,如何快速地让液体燃料蒸发,并稳定地燃烧,成为微型燃烧器研发成功的关键。液体燃料荷电雾化产生的液滴具有良好单分散性特点,极大地增加与空气接触面积,大大地增加了蒸发速度。同轴单喷嘴荷电雾化的流量小,产热量低,同轴多喷嘴(喷嘴方向与喷管方向一致)荷电雾化流量较大,产热量高,但喷嘴之间相互影响,造成雾化射流射程长,喷管直径大,雾化区域宽,使得微型燃烧器的尺寸较大。因此对于需要大功率供能的设备,需要的流量大,若采用同轴多喷嘴荷电雾化,将造成燃烧器的尺寸大幅增加。
技术实现要素:
[0004]
本实用新型的目的是为了克服以上现有技术存在的不足,提供了一种尺寸合理、燃料效率较高的适用于大流量的微型荷电喷雾燃烧器。
[0005]
本实用新型的目的通过以下的技术方案实现:一种适用于大流量的微型荷电喷雾燃烧器,包括燃烧室、雾化单元、多嘴喷管、燃烧网板、燃料供给箱和高压直流电源;所述雾化单元包括雾化室和金属网格;所述燃烧室和雾化室均呈两端开口的筒状,所述燃烧室和雾化室上下设置且连通,所述燃烧室和雾化室之间通过燃烧网板分隔,所述金属网格环绕设置于雾化室中,所述金属网格的顶端与燃烧网板连接;所述多嘴喷管包括输料管和若干个设置在输料管上的喷料层,所述输料管的顶端密封,若干个喷料层沿输料管的轴向间隔排布,并靠近输料管的顶端,若干个喷料层均位于金属网格围成的腔体中,所述输料管的底端穿过雾化室的底端开口后与燃料供给箱连通,所述多嘴喷管与高压直流电源的正极连接,所述金属网格与高压直流电源的负极连接。
[0006]
进一步地,所述喷料层均包括若干个沿输料管的径向均匀分布的喷嘴,相邻两喷料层之间的喷嘴上下对齐。
[0007]
进一步地,所述雾化单元还包括燃料回收槽,所述燃料回收槽设置于雾化室的底端,并形成雾化室的进气口,所述金属网格的底端位于燃料回收槽中,所述燃料回收槽与燃料供给箱连通,所述输料管的底端穿过进气口后与燃料供给箱连通。
[0008]
进一步地,所述燃料回收槽为环形槽,其中部镂空为进气口,所述燃料回收槽的外缘与雾化室的底端连接,所述多嘴喷管的底端穿后进气口后与燃料供给箱连通。
[0009]
进一步地,所述进气口的直径大于输料管的外径。
[0010]
进一步地,所述金属网格与燃烧室内壁之间填充有多孔介质层,所述多孔介质层的顶端与燃烧网板连接,所述多孔介质层的底端位于燃料回收槽中。
[0011]
进一步地,所述燃烧室包括上下设置的上腔室和下腔室,所述上腔室的内径小于下腔室的内径,所述上腔室与下腔室之间的衔接过渡为直角过渡。
[0012]
进一步地,所述燃烧网板表面涂有催化剂。
[0013]
进一步地,还包括供给泵,所述输料管的底端通过供给泵与燃料供给箱连通。
[0014]
进一步地,所述燃烧网板包括呈圆形的网孔部和设置在网孔部外周的密封板,所述燃烧室和雾化室分别与密封板的上下两侧连接。
[0015]
进一步地,还包括点火器,所述点火器靠近燃烧网板,所述点火器的引线连接外部电源。
[0016]
进一步地,还包括进气管、下盖板和换热套筒,所述换热套筒的底端由下盖板密封,所述燃烧室和雾化室均位于换热套筒中,所述燃烧室的顶端与换热套筒的顶端连接,所述燃烧室的内腔与外界连通,所述燃烧室的外壁和雾化室的外壁与换热套筒的内壁之间均具有间隙,所述雾化室的底端与下盖板之间具有间隙,以使雾化室与换热套筒之间形成空气流道,所述进气管穿过换热套筒与空气流道连通,所述多嘴喷管的底端穿过下盖板后与燃料供给箱连通。
[0017]
进一步地,还包括外套筒和上盖板;所述外套筒套设于换热套筒的外周,所述外套筒的顶端由上盖板密封,所述外套筒的底端由下盖板密封,所述换热套筒的顶端与上盖板之间留有间隙,所述换热套筒的外壁与外套筒的内壁之间留有间隙,以使燃烧室的内腔、换热套筒与外套筒之间形成尾气排放通道,所述外套筒的筒壁开有尾气排出口。
[0018]
一种适用于大流量的微型荷电喷雾燃烧器的燃烧方法,包括如下步骤:
[0019]
开启供给泵和高压直流电源,其中,多嘴喷管与高压直流电源的正极连接,金属网格与高压直流电源的负极连接;
[0020]
在供给泵的作用下,液体燃料以20~100ml/h的流量,由多嘴喷管喷出,在雾化室内雾化为细小的液滴,并在电场力的牵引作用下,被金属网格捕获;
[0021]
空气通过多根对称分布的进气管流入空气流道,沿着燃料回收槽的外壁面流进雾化室与燃料混合;燃料蒸汽和空气组成的混合气体在燃烧网板处被点火器点燃,在燃烧室内充分燃烧,燃烧后的尾气,经过尾气排放通道和尾气排出口后排出。
[0022]
本实用新型相对于现有技术具有如下优点:
[0023]
1、本燃烧器中的多孔喷嘴,其喷料层的出料方向与输料管的轴向垂直,可在有限的空间内排布较多的喷料层,从而提高液体燃料的流量,控制燃烧器的尺寸;本燃烧器中的多孔喷嘴和金属网格分别连接高压直流电源的正极和负极,轴向分布的喷料层结合荷电雾化的技术手段,使得多嘴喷管喷出的燃料液滴雾化流向金属网格,雾化区域宽,雾化射流短。本燃烧器结构简单紧凑,能够实现液体充分稳定的燃烧,燃烧效率高,应用前景广阔。
[0024]
2、本燃烧器中的多嘴喷管的喷料层包括多个沿输料管的径向均匀分布的喷嘴,有效提高了燃料的流量,径向分布的喷嘴之间相互影响小,喷雾射流较短,更为发散,加速液
滴的蒸发流量,有利于组织燃烧。当燃料流量和喷嘴数量相同时,本多嘴喷管与同轴多喷嘴(喷嘴方向与喷管方向一致)相比,同轴多喷嘴的喷嘴之间相互影响大,雾化射流射程长且雾化区域宽,与之对应的雾化室的体积较大,可见本多喷嘴设计可有效减小燃烧器的尺寸。
[0025]
3、本燃烧器中在雾化室的底端设置燃料回收槽对未蒸发完全的液滴进行回收利用,提高了燃料利用率。本实用新型在金属网格和雾化室的内壁之间填充多孔介质层,扩展了燃料液滴与空气接触表面积,加速液滴的蒸发速度。燃烧网板表面涂有催化剂,增加燃料的燃烧效率,同时燃烧网板起到稳定火焰面的作用。
[0026]
4、本实用新型中的燃烧室分为上腔室和下腔室,上腔室的内径小于下腔室的内径,上腔室与下腔室的衔接过渡为直角过渡,该结构使得燃料在燃烧室内部的停留时间延长,提高燃烧效率。
[0027]
5、本实用新型燃烧室燃烧后的尾气并未直接排放,而是通过迂回至尾气排放通道,由上至下方流动,并由下部的尾气排气口排出。在尾气排放通道中,高温尾气与新进空气通过换热套筒持续换热,不仅可以对空气进行预热,还可以对燃烧器进行保温,形成了有效的保温层,减少热量损失,大幅提高了燃烧效率,同时被预热的空气通过雾化室的壁面对多孔介质层进行加热,以及经金属网格对多孔介质层的热传导,使得液滴温度升高,加速蒸发。
附图说明
[0028]
构成本申请的一部分的说明书附图用来提供对本实用新型的进一步理解,本实用新型的示意性实施例及其说明用于解释本实用新型,并不构成对本实用新型的不当限定。在附图中:
[0029]
图1示出了根据本实用新型的适用于大流量的微型荷电喷雾燃烧器的结构示意图;
[0030]
图2示出了图1中a-a方向的结构示意图;
[0031]
图3示出了图1中b-b方向的结构示意图;
[0032]
图4示出了根据本实用新型中多嘴喷管的结构示意图;
[0033]
图5示出了图4中c-c方向的结构示意图;
[0034]
图6示出了根据本实用新型中金属网格与燃烧室之间填充多孔介质层的结构示意图;
[0035]
图7示出了根据本实用新型中燃烧网板的结构示意图;
[0036]
图中,1为燃烧室;2为燃料供给箱;3为多嘴喷管;4为高压直流电源;5为雾化室;6为燃烧网板;7为金属网格;8为燃料回收槽;9为进气口;10为输料管;11为喷嘴;12为多孔介质层;13为上腔室;14为下腔室;15为网孔部;16为密封板;17为点火器;18为引线;19为供给泵;20为进气管;21为下盖板;22为换热套筒;23为外套筒;24为上盖板;25为尾气排出口;26为回料口;27为燃料回收管;28为空气流道;29为尾气排放通道。
具体实施方式
[0037]
下面结合附图和实施例对本实用新型作进一步说明。
[0038]
如图1-图3所示,一种适用于大流量的微型荷电喷雾燃烧器,包括燃烧室1、雾化单
元、多嘴喷管3、燃烧网板6、燃料供给箱2和高压直流电源4;所述雾化单元包括雾化室5和金属网格7;所述燃烧室1和雾化室5均呈两端开口的筒状,所述燃烧室1和雾化室5上下设置且连通,所述燃烧室1和雾化室5之间通过燃烧网板6分隔,所述金属网格7环绕设置于雾化室5中,所述金属网格7的顶端与燃烧网板6连接;所述多嘴喷管3包括输料管10和若干个设置在输料管10上的喷料层,所述输料管10的顶端密封,若干个喷料层沿输料管10的轴向间隔排布,并靠近输料管10的顶端,若干个喷料层均位于金属网格7围成的腔体中,所述输料管10的底端穿过雾化室5的底端开口后与燃料供给箱2连通,所述多嘴喷管3与高压直流电源4的正极连接,所述金属网格7与高压直流电源4的负极连接。燃烧室1的底端和雾化室5的顶端的均与燃烧网板6的边缘密封,且二者内腔连通,雾化室5的底端开口用于流入空气,燃烧室1的顶端开口用于排出燃烧尾气。开启高压直流电源4使得多嘴喷管3与金属网格7之间形成静电场,有助于雾化、收集燃料液滴,提高燃料的利用率。
[0039]
本微型荷电喷雾燃烧器中设置多嘴喷管3,其喷料层的出料方向与输料管的轴向垂直,经喷料层喷出后的燃料在雾化室5内雾化呈小液滴,小液滴在静电场的作用下流向金属网格7,随后与空气混合后蒸发,在燃烧网板6上燃烧。本装置中喷料层垂直于输料管,从而能够在有限的空间内布置尽量多的喷料层,以提高燃料流量。喷出的燃料液滴在静电场的作用下流向金属网格,能够降低各喷料层之间的相互影响,解决现有技术中同轴单喷嘴产热小,多喷嘴产热大但尺寸较大,燃料雾化效果不好,燃料利用率低等问题。
[0040]
如图4和图5所示,所述喷料层均包括若干个沿输料管10的径向均匀分布的喷嘴11,相邻两喷料层之间的喷嘴11上下对齐。喷嘴11的喷射方向与输料管10垂直,相邻两层喷嘴喷出的射流互不干扰。采用此种轮辐式结构,各喷嘴之间影响小,提高了燃料的流量,喷雾射流较短,更为发散,加速液滴的蒸发流量,增加放热量,减小燃烧器的尺寸。
[0041]
如图6所示,所述金属网格7与燃烧室1的内壁之间填充有多孔介质层12,所述多孔介质层12的顶端与燃烧网板6连接。雾化室5中的燃料小液滴,在静电场的作用下发散且流向金属网格7,然后流进金属网格7后的多孔介质层12,从而增加燃料液滴与空气的接触面积,提高燃料的蒸发率。多孔介质层12和金属网格7与燃烧网板6的连接处密封,防止燃料泄露。
[0042]
如图1和图6所示,所述雾化单元还包括燃料回收槽8,所述燃料回收槽8设置于雾化室5的底端,并形成雾化室5的进气口9,所述金属网格7和多孔介质层12的底端均位于燃料回收槽8中,燃料回收槽8的底端开有回料口26,燃料回收管27的一端伸入回料口26,进入燃料回收槽8中,其另一端伸入燃料供给箱2中,所述输料管10的底端穿过进气口9后与燃料供给箱2连通。金属网格7和多孔介质层12中未完全蒸发的液滴在重力作用下流到燃料回收槽8中,最后经燃料回收管27回到燃料供给箱2,将液体燃料循环利用。
[0043]
所述燃料回收槽8为环形槽,其中部镂空形成雾化室5的进气口9,所述燃料回收槽8的外缘与雾化室5的底端一体连接,所述多嘴喷管3的输料管10的底端穿后进气口9后与燃料供给箱2连通。所述进气口9的直径大于输料管10的外径。此设置便于空气的流入,提高燃烧器的燃烧效率。
[0044]
如图1所示,所述燃烧室1包括上下设置的上腔室13和下腔室14,所述上腔室13的内径小于下腔室14的内径,所述上腔室13与下腔室14之间的衔接过渡为直角过渡。此设置能够增加燃烧气体在燃烧室的停留时间,促进其充分燃烧,从而提高燃烧效率。
[0045]
还包括供给泵19,所述输料管10的底端通过供给泵19与燃料供给箱2连通。液体燃料经供给泵19泵入输料管10中。
[0046]
所述燃烧网板6包括呈圆形的网孔部15和设置在网孔部15外周的密封板16,所述燃烧室1和雾化室5分别与密封板16的上下两侧连接。其中,燃烧室1和雾化室5上下设置,燃烧室1的底端与密封板16的上侧密封连接,雾化室5的顶端与密封板16的下侧密封连接,通过此设置能够有效防止燃料外泄,提高燃料的燃烧效率。所述燃烧网板6表面涂有催化剂,催化燃烧和稳定火焰面。
[0047]
还包括点火器17,所述点火器17靠近燃烧网板6,所述点火器17的引线18连接外部电源。点火器17与燃烧网板6之间具有微小的间隙。通过设置点火器,有助于点火,方便本燃烧器的使用。
[0048]
还包括进气管20、下盖板21和换热套筒22,所述换热套筒22的底端由下盖板21密封,所述燃烧室1和雾化室5均位于换热套筒22中,所述燃烧室1的顶端与换热套筒22的顶端连接,所述燃烧室1的内腔与外界连通,所述燃烧室1的外壁和雾化室5的外壁与换热套筒22的内壁之间均具有间隙,所述雾化室5的底端与下盖板21之间具有间隙,以使燃烧室1、雾化室5和燃料回收槽8与换热套筒22之间形成空气流道,所述进气管20的一端穿过换热套筒22与空气流道连通,从而将外界空气输送至雾化室5的内腔中。所述多嘴喷管的底端和燃料回收管27均穿过下盖板21后与燃料供给箱2连通。燃烧产生的尾气经燃烧室1的内腔排出。
[0049]
还包括外套筒23和上盖板24;所述外套筒23套设于换热套筒22的外周,所述外套筒23的顶端由上盖板24密封,所述外套筒23的底端由下盖板21密封,所述换热套筒22的顶端与上盖板24之间留有间隙,所述换热套筒22的外壁与外套筒23的内壁之间留有间隙,以使燃烧室1的内腔、换热套筒22与外套筒23之间形成尾气排放通道29,所述外套筒23的筒壁开有均匀分布的尾气排出口25。燃烧产生的尾气依次经尾气排放通道29、尾气排出口25排出。其中,尾气排出口25靠近下盖板21设置。
[0050]
通过设置下盖板21、上盖板24、换热套筒22和外套筒23,将燃烧室1和雾化室5封装,防止外界干扰,有助于提高燃烧的稳定性。通过设置尾气排放通道29和空气流道28,利用高温尾气加热入空气,有利于液体燃料的蒸发,提高液体燃料的利用率。
[0051]
具体地:
[0052]
上盖板24和外套筒23均采用低导热系数、耐高温的陶瓷材料制成,上盖板24的直径为75mm,厚度为3mm,外套筒的直径为70mm,厚度为2mm,上盖板24和外套筒23的整体高度为83mm。上盖板24的顶部开有1mm小孔,用于引线18(点火器引线)穿出。尾气排气口25的直径约为2~3mm,其距下盖板21的距离为4~5mm,并沿燃烧器的中轴线对称。
[0053]
下盖板21呈圆形,采用低导热系数、绝缘的碳化硅制成,直径78mm,厚度为3mm。其圆中心处开有3mm的小孔,输料管10穿过此小孔从而与燃料供给箱2连通。其距离圆周中心距离10mm处开有一个2~3mm的小孔,燃料回收管27穿过小孔此并伸入燃料回收槽8内0.5mm。
[0054]
输料管10的外径为4mm,内径为3.5mm,各喷料层之间间隔15mm,每一层四个喷嘴对称分布,每个喷嘴内径为0.5~0.8mm,外径为0.8~1.2mm,高度3mm,材料选用不锈钢,多喷嘴喷管下端光管与小孔过盈配合。多嘴喷管3的顶端距离燃烧网板6为8mm,最底端的喷嘴11距离下盖板21距离为20mm。
[0055]
多嘴喷管3与高压直流电源4的正极连接,高压直流电源4的电压为2~15kv,金属网格7与高压直流电源4的负极连接。通过设置多嘴喷管3、金属网格7和高压直流电源,能将雾化室17中的燃料液滴雾化。输料管10和多嘴喷管3均采用导电性好,且具有一定强度的材料制成,例如不锈钢等。
[0056]
换热套筒22采用高导热系数、耐高温材料的不锈钢制成,高度为77mm,与上盖板1间隔2~3mm,与下盖板7相连接,从而形成尾气排放通道29。
[0057]
燃烧网板6的直径为50mm,材料选用不锈钢,厚度0.5mm~1mm,网孔部15的网格密度为100孔/cm
2
,表面涂有催化剂,其作用是催化燃料燃烧和稳定火焰面。密封板16与雾化室5和燃烧室1无缝连接并做密封处理。金属网格7的外径为42mm,厚度为1mm,高度为53mm,其下端与燃料回收槽8间隔1mm。
[0058]
多孔介质层12与金属网格7贴紧,其外径为46mm,厚度为2~3mm,材料选用透气性能优良的烧结材料,比如碳化硅等,透气率为35%,其作用是扩展燃料液滴的表面积,加速蒸发,同时具有蓄热和导热的功能,促进燃料蒸发。
[0059]
雾化室5和燃料回收槽8是一个整体,雾化室5的外径为50mm,厚度为2mm,燃料回收槽8为外径为46mm、内径为15mm的环形槽,槽高度为3mm。燃料回收槽8底部开有2~3mm的小孔,与燃料回收管27过盈配合。
[0060]
燃烧室1的下腔室14的外径为50mm,高度为10mm,上腔室13的外径为40mm,高度为7mm,燃烧室1的壁厚均为2mm。其材料选用低导热系数、耐高温的陶瓷,其作用为提高混合蒸气在燃烧室1中的停留时间,减少燃烧过程中的热量损失,提高燃料的燃烧效率,维持燃烧室的温度。
[0061]
换热套筒22、燃烧室1、雾化室5、燃料回收槽8和下盖板21形成空气流道28,燃烧室1、上盖板24换热套筒22之间形成尾气排放通道29。尾气排放通道29中的尾气与空气流道28内的空气持续换热,以利用尾气中的余热预热空气,同时保温燃烧器,减小热量损失。
[0062]
进气管20贯穿外套筒23和换热套筒4,接通空气流道16,且进气管20的出口端的中心正对燃烧室1上、下腔室的直角过渡台阶。进气管20的出口端正对燃烧室1的直角过渡台阶,使得新进入的空气分流,增加扰动,从而增加空气的停留时间,与尾气交换更多的热量,还能使空气温度分布更均匀。
[0063]
燃料供给箱2体积300ml,燃料回收管27伸入燃料供给箱2中,并被其中的燃料浸没。消耗的燃料由燃料进料管补给,材料选用塑料管。
[0064]
本燃烧器具有尺寸紧凑,燃料回收利用率高,尾气预热空气热效率高,采用多孔介质结构加快燃料蒸发,燃烧网板催化燃烧提高燃烧稳定性,燃烧腔可增加燃气停留时间提高燃烧效率等优点,应用前景广阔。
[0065]
一种适用于大流量的微型荷电喷雾燃烧器的燃烧方法,包括如下步骤:
[0066]
开启供给泵19和高压直流电源4,其中,多嘴喷管3与高压直流电源4的正极连接,金属网格7与高压直流电源4的负极连接;
[0067]
在供给泵19的作用下,液体燃料以20~100ml/h的流量,由多嘴喷管喷出,在雾化室5内雾化为细小的液滴,并在电场力的牵引作用下,被金属网格7捕获;
[0068]
空气通过多根对称分布的进气管20流入空气流道28,沿着燃料回收槽8的外壁面流进雾化室5与燃料混合;燃料蒸汽和空气组成的混合气体在燃烧网板6处被点火器17点
燃,在燃烧室20内充分燃烧,燃烧后的尾气,经过尾气排放通道29和尾气排出口25后排出。
[0069]
上述具体实施方式为本实用新型的优选实施例,并不能对本实用新型进行限定,其他的任何未背离本实用新型的技术方案而所做的改变或其它等效的置换方式,都包含在本实用新型的保护范围之内。
起点商标作为专业知识产权交易平台,可以帮助大家解决很多问题,如果大家想要了解更多知产交易信息请点击 【在线咨询】或添加微信 【19522093243】与客服一对一沟通,为大家解决相关问题。
此文章来源于网络,如有侵权,请联系删除



tips