节能耐腐高效换热装置的制作方法



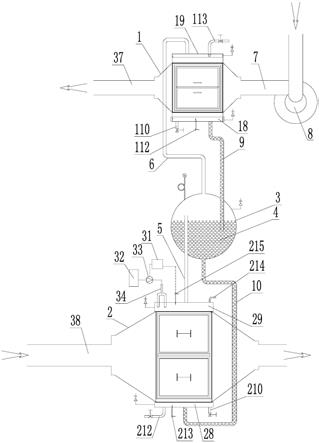
[0001]
本实用新型涉及电力、化工冶金等行业的节能设备技术领域,具体涉及节能耐腐高效换热装置。
背景技术:
[0002]
锅炉排烟热损失是电站锅炉中主要的热损失之一,排烟热损失是燃煤名炉各项热损失中占比最大的一项,占燃煤锅炉总热损失的75%以上。导致产生排烟热损失的主要因素是排烟温度,一般情况下,排烟温度每增加10℃,则:排烟热损失增加0.6%-1%,热耗增加1.2%-2.4%。此外,排烟温度过高不仅会严重降低能源的利用率,还会大大影响后续对烟气进行处理的脱硫烟气处理系统,降低除尘器的除尘效率,以及增加脱硫塔的耗水量。
[0003]
目前,国内很多电厂采用低温省煤器技术来降低排烟温度,提高电厂经济性。汽轮机热力系统中的凝结水在低温省煤器内吸收排烟热量,降低排烟温度,自身被加热、升高温度后再返回汽轮机低压加热系统,然而煤、石油、天然气等均为含硫燃料,燃烧是都会产生二氧化硫、三氧化硫,其中三氧化硫与水蒸汽在一定温度条件下产生化学反应生成硫酸蒸气,能够发生该反应的临界温度称之为酸露点,锅炉尾部设备中的金属壁面温度若低于硫酸蒸气的凝结点(酸露点)就会在其表面形成液态硫酸(酸露),会对金属换热设备产生腐蚀,可能导致泄漏,影响设备的运行安全和设备的使用寿命,同时也会使烟气中灰分附着换热器外壁,降低换热器的热效率。
[0004]
为了更为有效的利用烟气余热,进一步提高发电机组的经济性,需要研发一种耐腐换热系统装置,对烟气余热进行深度的利用,提高烟气余热的利用效率,又可防止酸露腐蚀金属设备,延长设备有效使用寿命,降低生产成本。
[0005]
一般电站排烟温度平均160℃左右,扣除20℃的安全裕度后,距烟气露点(97℃)仍有40℃以上温差的余热可以利用;作为热电企业,象这样较低品质的余热量大、点多、面广、回收利用有一定难度。如果能有效利用,显然可以提高全厂热效率,降低生产成本。
[0006]
通过对热力系统的排查,与上述低温烟气有直接传热温差的大容量介质只有锅炉的一、二次风。一、二次风设计温度为20℃,通过锅炉原有空气预热器加热到160℃后送入炉膛,如果利用较低温度的空气吸收较高温度烟气中的余热,然后进入空气预热器再进一步加热,从而提高了助燃空气温度,应该可以提高锅炉效率,达到节能、降低成本的目的。
技术实现要素:
[0007]
本实用新型的目的是提供一种节能、防腐、并能降低生产成本的节能耐腐高效换热装置。
[0008]
为实现上述目的,本实用新型采用了如下技术方案:节能耐腐高效换热装置,包括:两个呈上下布置的相变换热模块、以及布置在两个相变换热模块之间的气液分离塔,所述气液分离塔内的上部为气态工质、下部为液态工质;
[0009]
所述相变换热模块的结构包括:前后两端分别设置有进气口与出气口的相变换热
壳体,在相变换热壳体的内部顺着气体流动方向由前至后依次间隔设置有若干相变换热片,所述相变换热片的结构包括:呈上下分布的上联通管及下联通管,在上联通管与下联通管之间连接有若干根独立并联且呈左右间隔布置成排的换热翅片管,每根换热翅片管的上下两端分别连通上联通管与下联通管;所述所有相变换热片的下联通管同时与下集液管相连通,所有相变换热片的上联通管同时与上集气管相连通;
[0010]
定义位于下侧的相变换热模块为相变吸热模块,液态工质经相变吸热模块后因吸热而转变成气态工质;定义位于上侧的相变换热模块为相变放热模块,气态工质经相变放热模块后因散热而转变成液态工质;所述相变吸热模块中的上集气管与第一上升管路的下端相连通,第一上升管路的上端向上伸入气液分离塔且位于气液分离塔的上部空间,气液分离塔的顶部通过第二上升管路与相变放热模块中的上集气管相连通,相变放热模块的进气口设置有引风机,相变放热模块中的下集液管的底部与第一下降管路的上端相连通,第一下降管路的下端伸入气液分离塔且浸没在气液分离塔内下部空间的液态工质中,所述气液分离塔的底部通过第二下降管路与相变吸热模块中的下集液管相连通,从而使相变吸热模块、气液分离塔及相变放热模块三者形成闭环的工质循环回路。
[0011]
进一步地,前述的节能耐腐高效换热装置,其中:在每个相变换热模块中的下集液管上均设置有带阀门的排空管、带阀门的进出液管、带阀门的补液管、以及用以检测下集液管内液温的热电偶,在每个相变换热模块中的上集气管上均设置有带阀门的放气管。
[0012]
进一步地,前述的节能耐腐高效换热装置,其中:在相变吸热模块中的上集气管中设置有用以检测上集气管内工质蒸气温度的热电偶、以及能根据热电偶所反馈的工质蒸气温度来调节上集气管内工质蒸气温度的温度调节器。
[0013]
进一步地,前述的节能耐腐高效换热装置,其中:温度调节器的结构包括:控制器、调温水源、调节泵、以及穿设在上联通管及上集气管中的调温管,所述调温管通过调节泵连接调温水源,所述控制器同时与调节泵、以及相变吸热模块中用以检测上集气管内工质蒸气温度的热电偶电连接。
[0014]
进一步地,前述的节能耐腐高效换热装置,其中:相变换热模块中的相变换热壳体由底架、侧板、顶板、以及加强角钢组装而成。
[0015]
进一步地,前述的节能耐腐高效换热装置,其中:在相变换热壳体的侧板上设置有检查门。
[0016]
进一步地,前述的节能耐腐高效换热装置,其中:相变吸热模块中顺着气体流动方向的第一排相变换热片中的每根换热翅片管的迎烟面上均设置有防磨瓦。
[0017]
进一步地,前述的节能耐腐高效换热装置,其中:防磨瓦的具体安装结构包括:防磨瓦的内侧设置有具有u形卡口的卡子,防磨瓦通过将卡子的u形卡口卡扣在换热翅片管上而可拆卸地安装在换热翅片管上。
[0018]
进一步地,前述的节能耐腐高效换热装置,其中:在各相变换热模块的迎气侧均设置有用以引导气体流向相变换热片的导流板。
[0019]
进一步地,前述的节能耐腐高效换热装置,其中:在各相变换热模块中的上联通管及下联通管的外部均围设有用以保护对应联通管的集管护板。
[0020]
通过上述技术方案的实施,本实用新型的有益效果是:
[0021]
(1)可靠:节能系统可独立控制,不影响锅炉正常操作;适用于各种燃煤燃油燃气
锅炉、工业炉窑以及钢铁石化等行业换热设备;
[0022]
(2)节能:能降低能耗、提高吨煤产汽率、增加锅炉出力,能使锅炉热效率稳定提高1.5%以上;
[0023]
(3)节水:在回收热能的同时,降低后级脱硫系统的排烟温度,可节约大量脱硫工艺用水;
[0024]
(4)防腐:通过回收锅炉排烟的余热来提高空气预热器的进口风温,使其尾部最低壁面温度高于酸露点温度,防止空气预热器受酸露腐蚀;即使负荷和燃料种类发生变化也不会产生酸露腐蚀,从机理上根本解决了设备酸露腐蚀问题,消除结露性新灰垢产生;
[0025]
(5)与一般换热器相比,它能在较大幅度降低废气排放温度的同时,将整个换热设备的壁面温度维持在合适的温度水平,使整个换热设备的壁面温度始终在酸露点之上10℃左右,防止酸露腐蚀从而消除泄漏隐患;既最大可能地提高了换热设备的热效率,又避免了因结露引起低温腐蚀和灰堵现象;
[0026]
(6)减排:节约能源的消耗量是最大的减排,减少co2、nox排放同时,有效降低粉尘的排放;
[0027]
(7)克服了空气预热器负荷不能主动调节、每年有10%-30%热管传热功能失效和空气泄漏率较高等缺点;
[0028]
(8)传热效率高,体积小,重量轻,不具备热载体循环泵、管内操作压力低、系统复杂和应用范围小等缺点。
附图说明
[0029]
图1是本实用新型所述的节能耐腐高效换热装置的结构原理示意图。
[0030]
图2为图1中所示的相变吸热模块的结构示意图。
[0031]
图3为图2中所示的a部位的放大示意图。
[0032]
图4为图2左视方向中隐去喇叭口后的结构示意图。
[0033]
图5为图4俯视方向的结构示意图。
[0034]
图6为图5中所示的相变吸热片的结构示意图。
[0035]
图7为图6左视方向的结构示意图。
[0036]
图8为图7中所示的b部位的放大示意图。
[0037]
图9为图7俯视方向所示的换热翅片管与防磨瓦的位置关系示意图。
[0038]
图10为图1中所示的相变放热模块的结构示意图。
[0039]
图11为图10中所示的c部位的放大示意图。
[0040]
图12为图10中所示的d部位的放大示意图。
[0041]
图13为图10左视方向中隐去喇叭口后的结构示意图。
[0042]
图14为图13俯视方向的结构示意图。
[0043]
图15为图14中所示的相变放热片的结构示意图。
[0044]
图16为图15左视方向的结构示意图。
具体实施方式
[0045]
为了使本实用新型的目的、技术方案及优点更加清楚明白,以下结合附图及实施
例,对本实用新型进行进一步详细说明。应当理解,此处所描述的具体实施例仅仅用以解释本实用新型,并不用于限定本实用新型。
[0046]
如图1所示,所述的节能耐腐高效换热装置,包括:两个呈上下布置的相变换热模块,定义位于上侧的相变换热模块为相变放热模块1,气态工质经相变放热模块后因散热而转变成液态工质;定义位于下侧的相变换热模块为相变吸热模块2,液态工质经相变吸热模块后因吸热而转变成气态工质;以及布置在相变放热模块1与相变吸热模块2之间的气液分离塔3,所述气液分离塔3内的上部为气态工质、下部为液态工质4;本实施例中,液态工质为水、气态工质为水蒸气;其工作原理是:相变换热模块是在多根并联的密闭换热管束内利用相变工质汽化潜热传递热量,相变吸热模块2内的水吸收热量汽化为饱和蒸气,蒸气在一定的压差下上升到相变放热模块1放出热量,然后凝结成液体,饱和水经汽水分离塔3回到相变吸热模块2,并再次气化,往复循环,完成了把热量由高端向低端单向导热;
[0047]
其中,如图10、图11、图12、图13、图14、图15、图16所示,所述的相变放热模块1的结构包括:前后两端分别设置有第一进气口11与第一出气口12的相变换热壳体,本实施例中,定义相变放热模块1中的相变换热壳体为相变放热壳体13,相变放热壳体13由底架、侧板、顶板、以及加强角钢组装而成,在相变放热壳体13的侧板上设置有第一检查门131,在相变换热壳体的第一进气口11与第一出气口12处分别设置有喇叭口116;在相变放热壳体13的内部顺着气体流动方向由前至后依次间隔设置有若干相变换热片,本实施例中,定义相变放热模块1中的相变换热片为相变放热片14,所述相变放热片14的结构包括:呈上下分布的第一上联通管15及第一下联通管16,在第一上联通管15与第一下联通管16之间连接有若干根呈左右间隔布置成排的第一换热翅片管17,每根第一换热翅片管17的上下两端分别连通第一上联通管15与第一下联通管16;所有相变放热片14的第一下联通管16同时与第一下集液管18相连通,所有相变放热片14的第一上联通管15同时与第一上集气管19相连通;在本实施例中,定义所有第一换热翅片管均为左旋翅片管的相变放热片为左旋相变放热片,定义所有第二换热翅片管均为右旋翅片管的相变放热片为右旋相变放热片,顺着气体流动方向,左旋相变放热片与右旋相变放热片呈前后交替布置在相变放热壳体内;
[0048]
在相变放热模块1中的第一下集液管18上设置有带阀门的第一排空管110、带阀门的第一进出液管111、以及用以检测第一下集液管18内液温的第一热电偶112,在相变放热模块1中的第一上集气管上19上设置有带阀门的第一放气管113;在本实施例中,在相变放热模块1的迎气侧设置有用以引导气体流向相变放热片14的第一导流板114,在相变放热模块1中的第一上联通管15及第一下联通管16的外部均围设有用以保护对应联通管的第一集管护板115;
[0049]
其中,如图2、图3、图4、图5、图6、图7、图8、图9所示,所述的相变吸热模块2的结构包括:前后两端分别设置有第二进气口21与第二出气口22的相变换热壳体,本实施例中,定义相变吸热模块2中的相变换热壳体为相变吸热壳体23,相变吸热壳体23由底架、侧板、顶板、以及加强角钢组装而成,在相变吸热壳体23的侧板上设置有第二检查门231,在相变吸热壳体23的第二进气口21与第二出气口22处分别设置有喇叭口218;在相变吸热壳体23的内部顺着气体流动方向由前至后依次间隔设置有若干相变换热片,本实施例中,定义相变吸热模块2中的相变换热片为相变吸热片24,所述相变吸热片24的结构包括:呈上下分布的第二上联通管25及第二下联通管26,在第二上联通管25与第二下联通管26之间连接有若干
根呈左右间隔布置成排的第二换热翅片管27,每根第二换热翅片管27的上下两端分别连通第二上联通管25与第二下联通管26;所有相变吸热片24的第二下联通管26同时与第二下集液管28相连通,所有相变吸热片24的第二上联通管25同时与第二上集气管29相连通;在本实施例中,定义所有第二换热翅片管均为左旋翅片管的相变吸热片为左旋相变吸热片,定义所有第二换热翅片管均为右旋翅片管的相变吸热片为右旋相变吸热片,顺着气体流动方向,左旋相变吸热片与右旋相变吸热片呈前后交替布置在相变吸热壳体内;
[0050]
在相变吸热模块2中的第二下集液管28上设置有带阀门的第二排空管210、带阀门的第二进出液管211、带阀门的补液管212、以及用以检测第二下集液管28内液温的第二热电偶213,在相变吸热模块2中的第二上集气管29上设置有带阀门的第二放气管214;在本实施例中,在相变吸热模块2的迎气侧设置有用以引导气体流向相变吸热片24的第二导流板216,在相变吸热模块2中的第二上联通管25及第二下联通管26的外部均围设有用以保护对应联通管的第二集管护板217;
[0051]
在本实施例中,相变吸热模块2中顺着气体流动方向的第一排相变吸热片24中的每根第二换热翅片管27的迎烟面上均设置有防磨瓦35,防磨瓦35可以保护第二换热翅片管,避免第二换热翅片管受烟气直接冲刷损坏,延长了设备的使用寿命;本实施例中,防磨瓦35的具体安装结构包括:防磨瓦35的内侧设置有具有u形卡口的卡子36,防磨瓦35通过将卡子36的u形卡口卡扣在第二换热翅片管27上而可拆卸地安装在第二换热翅片管27上,这样便于拆装更换防磨瓦,提高了安装与维修效率;
[0052]
在本实施例中,在相变吸热模块2中的第二上集气管29中设置有用以检测第二上集气管29内工质蒸气温度的第三热电偶215、以及能根据第三热电偶215所反馈的工质蒸气温度来调节第二上集气管29内工质蒸气温度的温度调节器,根据pv=nrt的原理,在密闭容器中,气体温度越高则容器内压力会越大,所以温度调节器通过对第二上集气管29内即将进入气液分离塔3的工质蒸汽的温度进行调节,来间接地对气液分离塔3的内部压力进行调节,确保气液分离塔内压力能保持在安全水平,保证了设备安全顺行;在本实施例中,温度调节器的结构包括:控制器31、调温水源32、调节泵33、以及穿设在第二上联通管25及第二上集气管29中的调温管34,所述调温管34通过调节泵33连接调温水源32,所述控制器31同时与调节泵33、以及相变吸热模块2中用以检测第二上集气管29内工质蒸气温度的第三热电偶215电连接,控制器31会根据第三热电偶215所反馈的第二上集气管29中工质蒸气温度,通过调节泵33自动控制调节流经调温管34内的水的流速,使第二上集气管29中工质蒸气与调温管24进行换热,从而调节第二上集气管29中工质蒸气温度,确保气液分离塔内压力能保持在安全水平,保证了设备安全顺行;在本实施例中,相变吸热模块2中各第二上联通管25的管径顺着气体流动方向逐渐减小,并且调温管34穿设在最前端的两根上联通管中,这样可以确保相变速度更加均衡;
[0053]
所述相变吸热模块2中的第二上集气管与29第一上升管路5的下端相连通,第一上升管路5的上端向上伸入气液分离塔3且位于气液分离塔3的上部空间,气液分离塔3的顶部通过第二上升管路6与相变放热模块1中的第一上集气管19相连通,相变放热模块1的第一进气口11通过冷风进风管道7连通引风机8的出风口,相变放热模块1中的第一下集液管18的底部与第一下降管路9的上端相连通,第一下降管路9的下端伸入气液分离塔3且浸没在气液分离塔3内下部空间的液态工质4中,所述气液分离塔3的底部通过第二下降管路10与
相变吸热模块2中的第二下集液管28相连通;工作时,相变吸热模块2、第一上升管路5、气液分离塔3、第二上升管路6、相变放热模块1、第一下降管路9、气液分离塔3、第二下降管路形成了闭合循环回路;
[0054]
安装时,将相变放热模块1的第一出气口12通过热风出风管道37连接空预器,将相变吸热模块2的第二进气口21通过进烟烟道38连接锅炉的排烟管道,将相变吸热模块2的第二出气口22连接除尘器;
[0055]
工作时,相变吸热模块2中各第二换热翅片管27内的液态工质(通常为水)会与锅炉排出的过热烟气(烟温为160℃)进行热交换,对锅炉排出的过热烟气进行冷却降温,过热烟气经热交换后烟温会降低至115℃排出,而相变吸热模块2中各第二换热翅片管27内的液态工质经热交换后会吸热升温并蒸发形成工质蒸气,工质蒸汽依次经对应的第二换热翅片管27进入对应的第二上联通管25,各第二上联通管25内的工质蒸气再汇集至第二上集气管29中,第二上集气管29内的工质蒸气再经第一上升管路5进入气液分离塔3的上部空间,气液分离塔3上部空间的工质蒸气经第二上升管路6进入相变放热模块1的第一上集气管19,经第一上集气管19自行分配至各第一上联通管15及各第一换热翅片管17中,当引风机8将外界冷空气经冷风进风管道7引入相变放热模块1后,冷空气会与各第一换热翅片管17内的工质蒸气进行热交换,冷空气经热交换后形成烟温为20℃的热风、并经热风出风管道37进入空预器中,而相变放热模块1中各第一换热翅片管17内的工质蒸气经热交换后会形成冷凝液凝结于管壁上、并在重力作用下汇集至对应第一下联通管16中,各第一下联通管16中的冷凝液再汇集至第一下集液管18中、并经第一下降管路9回流至气液分离塔3内部,气液分离塔3内的液态工质再经第二下降管路10回流至相变吸热模块2的第二下集液管28中,再经各第二下联通管26自行分配至各第二换热翅片管27中,重新对锅炉排出的过热烟气进行冷却降温。
[0056]
本实用新型的优点是:
[0057]
(1)可靠:节能系统可独立控制,不影响锅炉正常操作;适用于各种燃煤燃油燃气锅炉、工业炉窑以及钢铁石化等行业换热设备;
[0058]
(2)节能:能降低能耗、提高吨煤产汽率、增加锅炉出力,能使锅炉热效率稳定提高1.5%以上;
[0059]
(3)节水:在回收热能的同时,降低后级脱硫系统的排烟温度,可节约大量脱硫工艺用水;
[0060]
(4)防腐:通过回收锅炉排烟的余热来提高空气预热器的进口风温,使其尾部最低壁面温度高于酸露点温度,防止空气预热器受酸露腐蚀;即使负荷和燃料种类发生变化也不会产生酸露腐蚀,从机理上根本解决了设备酸露腐蚀问题,消除结露性新灰垢产生;
[0061]
(5)与一般换热器相比,它能在较大幅度降低废气排放温度的同时,将整个换热设备的壁面温度维持在合适的温度水平,使整个换热设备的壁面温度始终在酸露点之上10℃左右,防止酸露腐蚀从而消除泄漏隐患;既最大可能地提高了换热设备的热效率,又避免了因结露引起低温腐蚀和灰堵现象;
[0062]
(6)减排:节约能源的消耗量是最大的减排,减少co2、nox排放同时,有效降低粉尘的排放;
[0063]
(7)克服了空气预热器负荷不能主动调节、每年有10%-30%热管传热功能失效和空
气泄漏率较高等缺点;
[0064]
(8)传热效率高,体积小,重量轻,不具备热载体循环泵、管内操作压力低、系统复杂和应用范围小等缺点。
[0065]
以上所述仅是本实用新型的较佳实施例,并非是对本实用新型作任何其他形式的限制,而依据本实用新型的技术实质所作的任何修改或等同变化,仍属于本实用新型要求保护的范围。
起点商标作为专业知识产权交易平台,可以帮助大家解决很多问题,如果大家想要了解更多知产交易信息请点击 【在线咨询】或添加微信 【19522093243】与客服一对一沟通,为大家解决相关问题。
此文章来源于网络,如有侵权,请联系删除



tips