一种喷注单元结构及双组元喷注器的制作方法



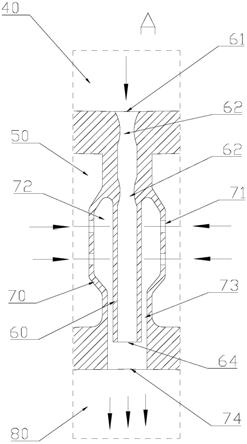
[0001]
本实用新型涉及喷注燃烧器技术领域,具体涉及一种喷注单元结构及双组元喷注器。
背景技术:
[0002]
喷注器是液体火箭发动机的核心部件,其位于推力室的头部,其功能是在规定的推进剂流量、混合比和喷注压降下,将推进剂均匀的喷入燃烧室,保证混合比和质量分布满足设计状态要求,并迅速的完成推进剂的雾化、混合过程,使得推进剂在燃烧室内高效充分的燃烧。喷注器的设计水平和加工精度对燃烧室的稳定性、效率和寿命都影响极大。经过喷注器组织燃烧的效率每损失一个百分点,都意味着发动机比冲性能损失同样的百分数。一般大推力液体火箭发动机推力室的燃烧效率都在96%以上,性能优异喷注器的燃烧室效率可以达到99%。喷注单元结构作为喷注器的重要组成部分,其结构形式也对喷注器的燃烧稳定性有较大影响,现有技术中,喷注单元结构的结构形式往往较为单一,抗干扰能力较差,稳定性较低,仍有较大改进空间。
技术实现要素:
[0003]
因此,本实用新型要解决的技术问题在于克服现有技术中喷注单元结构的稳定性较低的缺陷,从而提供一种稳定性较高的喷注单元结构。
[0004]
本实用新型要解决的另一个技术问题在于克服现有技术中双组元喷注器的喷注器燃烧效率较低的缺陷,从而提供一种喷注器燃烧效率较高的双组元喷注器。
[0005]
为解决上述技术问题,本实用新型提供的一种喷注单元结构,包括:
[0006]
燃料剂喷嘴,其侧壁上设置有至少一个径向孔;
[0007]
氧化剂喷嘴,其至少部分的套设于所述燃料剂喷嘴内部;
[0008]
所述氧化剂喷嘴内部贯穿,并与所述径向孔共同与喷注口导通。
[0009]
进一步地,所述氧化剂喷嘴远离所述喷注口一端的内侧壁设置有至少一个节流孔。
[0010]
进一步地,所述氧化剂喷嘴远离所述喷注口一端的内侧壁连续设置有两个节流孔。
[0011]
进一步地,所述径向孔为雨滴形结构。
[0012]
进一步地,所述燃料剂喷嘴内侧壁与所述氧化剂喷嘴外侧壁之间形成有环形容腔。
[0013]
进一步地,所述径向孔正对所述环形容腔设置。
[0014]
进一步地,所述燃料剂喷嘴内侧壁与所述氧化剂喷嘴外侧壁之间还形成有环形间隙,所述环形间隙一端与所述环形容腔相导通,另一端与所述喷注口相导通。
[0015]
本实用新型提供的双组元喷注器,包括:
[0016]
燃料剂腔;
[0017]
第一底面,设置于所述燃料剂腔底部;
[0018]
第二底面,设置于所述燃料剂腔顶部并与所述第一底面相对设置;以及
[0019]
至少一个如上述所述的喷注单元结构,所述喷注单元结构连通设置于所述第一底面与所述第二底面之间。
[0020]
进一步地,所述第一底面与所述第二底面均为曲面结构,且弯曲中部相靠近,使所述燃料剂腔构造为双曲面凹透镜式结构。
[0021]
进一步地,所述第一底面与所述第二底面之间设置有若干长度不同的所述喷注单元结构。
[0022]
本实用新型技术方案,具有如下优点:
[0023]
1.本实用新型提供的喷注单元结构,燃料剂喷嘴与氧化剂喷嘴采用嵌套式的结构设置,使得氧化剂喷嘴的第一端与设置在燃料剂喷嘴侧壁上的径向孔共同与所述燃料剂喷嘴的第二端构造成的喷注口导通。
[0024]
2.本实用新型提供的喷注单元结构,所述节流孔由所述氧化剂喷嘴内壁向中心位置凸出而成,使得所述节流孔处的流通面积减少,所述氧化剂喷嘴采用双节流孔设计,能够增强氧化剂流动时的抗干扰能力,从而增强喷注器的燃烧稳定性。
[0025]
3.本实用新型提供的喷注单元结构,采用雨滴形结构的径向孔,能够提高燃料剂喷嘴的流量系数,在相同的喷注速度下有利于减小燃料剂喷嘴的流阻。
[0026]
4.本实用新型提供的喷注单元结构,所述环形容腔能够增强环形间隙处燃料剂流动的稳定性和均匀性。
[0027]
5.本实用新型提供的喷注单元结构,所述径向孔正对所述环形容腔设置,使得燃料剂由所述径向孔进入所述喷注单元结构后,优先进入所述环形容腔,相当于一个集合器,起到均流作用。
[0028]
6.本实用新型提供的双组元喷注器,所述第一底面与所述第二底面均为曲面结构,从而提高燃料剂腔的承压能力,由于相同厚度曲面比平面承压能力高,曲面能够把承受的压力均匀的沿着整个表面分散开来,并把压力均匀的扩散到底面各处,使得曲面能够承受较大压力,从而提高双组元喷注器的结构强度。
[0029]
7.本实用新型提供的双组元喷注器,燃料剂腔构造为双曲面凹透镜式结构,且第一底面与所述第二底面的弯曲中部相靠近,使得燃料剂腔边缘区域的燃料剂流速较低,燃料剂腔中心区域的燃料剂流速较高,进而使得燃料剂腔具有等静压均流特性,每个喷注单元结构流量分布更均匀,有利于提高喷注燃烧效率。
附图说明
[0030]
为了更清楚地说明本实用新型具体实施方式或现有技术中的技术方案,下面将对具体实施方式或现有技术描述中所需要使用的附图作简单地介绍,显而易见地,下面描述中的附图是本实用新型的一些实施方式,对于本领域普通技术人员来讲,在不付出创造性劳动的前提下,还可以根据这些附图获得其他的附图。
[0031]
图1为本实用新型双组元喷注器的截面示意图一;
[0032]
图2为图1中a处放大图;
[0033]
图3为本实用新型喷注单元结构的示意图;
[0034]
图4为本实用新型双组元喷注器的截面示意图二;
[0035]
图5为本实用新型第一底面截面示意图。
[0036]
附图标记说明:
[0037]
10-第一底面,11-发汗冷却通道,20-第二底面,30-第三底面;
[0038]
40-氧化剂腔,41-氧化剂入口,50-燃料剂腔,51-燃料剂入口;
[0039]
60-氧化剂喷嘴,61-氧化剂喷嘴入口端,62-节流孔,63-氧化剂喷嘴出口端;
[0040]
70-燃料剂喷嘴,71-径向孔,72-环形容腔,73-环形间隙,74-喷注口;
[0041]
80-燃烧室。
具体实施方式
[0042]
下面将结合附图对本实用新型的技术方案进行清楚、完整地描述,显然,所描述的实施例是本实用新型一部分实施例,而不是全部的实施例。基于本实用新型中的实施例,本领域普通技术人员在没有做出创造性劳动前提下所获得的所有其他实施例,都属于本实用新型保护的范围。
[0043]
在本实用新型的描述中,需要说明的是,术语“中心”、“上”、“下”、“左”、“右”、“垂直”、“水平”、“内”、“外”等指示的方位或位置关系为基于附图所示的方位或位置关系,仅是为了便于描述本实用新型和简化描述,而不是指示或暗示所指的装置或元件必须具有特定的方位、以特定的方位构造和操作,因此不能理解为对本实用新型的限制。此外,术语“第一”、“第二”、“第三”仅用于描述目的,而不能理解为指示或暗示相对重要性。
[0044]
在本实用新型的描述中,需要说明的是,除非另有明确的规定和限定,术语“安装”、“相连”、“连接”应做广义理解,例如,可以是固定连接,也可以是可拆卸连接,或一体地连接;可以是机械连接,也可以是电连接;可以是直接相连,也可以通过中间媒介间接相连,可以是两个元件内部的连通。对于本领域的普通技术人员而言,可以具体情况理解上述术语在本实用新型中的具体含义。
[0045]
此外,下面所描述的本实用新型不同实施方式中所涉及的技术特征只要彼此之间未构成冲突就可以相互结合。
[0046]
实施例一
[0047]
结合图1-3所示,本实施例提供一种喷注单元结构,包括:
[0048]
燃料剂喷嘴70,其侧壁上设置有至少一个径向孔71;
[0049]
氧化剂喷嘴60,其至少部分的套设于所述燃料剂喷嘴70内部;
[0050]
所述氧化剂喷嘴60内部贯穿,并与所述径向孔71共同与喷注口74导通。
[0051]
优选的,所述氧化剂喷嘴60至少部分的套设于所述燃料剂喷嘴70内部,所述燃料剂喷嘴70的第一端与所述氧化剂喷嘴60的外壁相连接,所述燃料剂喷嘴70的第二端构造为喷注口74;所述氧化剂喷嘴60内部贯穿,所述氧化剂喷嘴60远离所述喷注口74的一端构造为氧化剂喷嘴入口端61,所述氧化剂喷嘴60靠近所述喷注口74的一端构造氧化剂喷嘴出口端63,使得所述氧化剂喷嘴入口端61经由所述氧化剂喷嘴出口端63与所述喷注口74导通设置;同时,燃料剂喷嘴70的侧壁上设置的至少一个径向孔71 也与所述喷注口74导通。
[0052]
所述氧化剂喷嘴入口端61适于通入氧化剂,所述燃料剂喷嘴70的侧壁上设置的至少一个径向孔71适于通入燃料剂,经由所述喷注单元结构后,所述氧化剂与所述燃料剂混
合,并一同从所述喷注口74排出。
[0053]
本实施例提供的喷注单元结构,燃料剂喷嘴70与氧化剂喷嘴60采用嵌套式的结构设置,使得氧化剂喷嘴60的第一端与设置在燃料剂喷嘴70 侧壁上的径向孔71共同与所述燃料剂喷嘴70的第二端构造成的喷注口74 导通。
[0054]
优选的,每个所述燃料剂喷嘴70共设置2排径向孔71,每排4个,所述径向孔71在所述燃料剂喷嘴70侧壁周向均布。
[0055]
具体地,所述氧化剂喷嘴60远离所述喷注口74一端的内侧壁设置有至少一个节流孔62,即所述氧化剂喷嘴入口端61处设置有至少一个节流孔 62,作为进一步地优选形式,所述氧化剂喷嘴60远离所述喷注口74一端的内侧壁连续设置有两个节流孔62。所述节流孔62由所述氧化剂喷嘴60 内壁向中心位置凸出而成,使得所述节流孔62处的流通面积减少,所述氧化剂喷嘴60采用双节流孔设计,能够增强氧化剂流动时的抗干扰能力,从而增强喷注器的燃烧稳定性。
[0056]
具体地,所述径向孔71为雨滴形结构。采用雨滴形结构的径向孔,能够提高燃料剂喷嘴70的流量系数,在相同的喷注速度下有利于减小燃料剂喷嘴70的流阻。
[0057]
具体地,所述燃料剂喷嘴70内侧壁与所述氧化剂喷嘴60外侧壁之间形成有环形容腔72。
[0058]
具体地,所述燃料剂喷嘴70内侧壁与所述氧化剂喷嘴60外侧壁之间还形成有环形间隙73,所述环形间隙73一端与所述环形容腔72相导通,另一端与所述喷注口74相导通。
[0059]
所述环形容腔72能够增强环形间隙73处燃料剂流动的稳定性和均匀性。
[0060]
具体地,所述径向孔71正对所述环形容腔72设置,使得燃料剂由所述径向孔71进入所述喷注单元结构后,优先进入所述环形容腔72,相当于一个集合器,起到均流作用。
[0061]
实施例二
[0062]
结合图1所示,本实施例提供一种双组元喷注器,包括:
[0063]
燃料剂腔50;
[0064]
第一底面10,设置于所述燃料剂腔50底部;
[0065]
第二底面20,设置于所述燃料剂腔50顶部并与所述第一底面10相对设置;以及
[0066]
至少一个如上述所述的喷注单元结构,所述喷注单元结构连通设置于所述第一底面10与所述第二底面20之间。
[0067]
具体地,所述第一底面10与所述第二底面20均为曲面结构,且弯曲中部相靠近,使所述燃料剂腔50构造为双曲面凹透镜式结构。
[0068]
优选的,所述燃料剂腔50构造为封闭式或局部开口式的腔体结构,其底部与顶部分别由第一底面10和第二底面20围合而成,在所述第一底面 10与所述第二底面20之间设置至少一个喷注单元结构,即所述喷注单元结构设置在所述燃料剂腔50内,且喷注单元结构上下开口,将所述第一底面 10与所述第二底面20贯穿,从而将第二底面20上部空间与第一底面10下部空间导通。
[0069]
本实施例提供双组元喷注器,所述第一底面10与所述第二底面20均为曲面结构,从而提高燃料剂腔的承压能力,由于相同厚度曲面比平面承压能力高,曲面能够把承受的压力均匀的沿着整个表面分散开来,并把压力均匀的扩散到底面各处,使得曲面能够承受较大压力,从而提高双组元喷注器的结构强度。
[0070]
具体地,所述燃料剂腔50的至少其中一侧设置有燃料剂入口51,所述燃料剂入口51用于向所述燃料剂腔50中通入燃料剂。优选的,所述燃料剂入口51设置于连接所述第一底面10与所述第二底面20的竖向壁面上,从而使得所述燃料剂入口51对燃料剂的喷注方向与所述喷注单元结构的延伸方向相垂直或呈一定夹角。所述燃料剂腔50构造为双曲面凹透镜式结构,且所述第一底面10与所述第二底面20的弯曲中部相靠近,使得燃料剂入口51处的燃料剂腔50流通面积较大,此处燃料剂的流速较低,而燃料剂腔50中心处流通面积小,此处燃料剂的流速较高,这样就会使得燃料剂腔 50内部压力分布更均匀,较佳的,上述压力分布情况,已通过三维的流体仿真分析进行验证。
[0071]
本实施例提供的双组元喷注器,燃料剂腔50构造为双曲面凹透镜式结构,且第一底面10与所述第二底面20的弯曲中部相靠近,使得燃料剂腔 50边缘区域的燃料剂流速较低,燃料剂腔50中心区域的燃料剂流速较高,进而使得燃料剂腔50具有等静压均流特性,每个喷注单元结构流量分布更均匀,有利于提高喷注燃烧效率。
[0072]
具体地,如图5所示,所述第一底面10上还贯通设置有至少一个发汗冷却通道11。
[0073]
具体地,所述发汗冷却通道11构造为曲回形结构。
[0074]
所述发汗冷却通道11通过曲回形的通道布置形式,将所述第一底面10 贯穿,使得燃料剂腔50与外界能够连通,在双组元喷注器的应用环境中,所述外界通常为燃烧室,即所述燃料剂腔50与所述燃烧室通过所述第一底面10进行分隔,所述第一底面10上设置的所述发汗冷却通道11将燃料剂腔50与燃烧室80进行导通。由于所述第一底面10贴近燃烧室80侧,燃烧室80温度较高,所述第一底面10需要采用冷却措施对其进行冷却,因此所述第一底面10通常采用特制的多孔金属材料加工,所述第一底面10 通常也称为多孔面板。
[0075]
本实施例提供的双组元喷注器,将曲回形结构的发汗冷却通道结构群阵式布于所述第一底面10,使得燃料剂腔50内的燃料剂能够从曲回形通道缓慢流出,从而对所述第一底面10的燃气面起到发汗冷却的作用。
[0076]
具体地,所述双组元喷注器还包括:
[0077]
氧化剂腔40,所述氧化剂腔40以所述第二底面20为底部,并以远离所述第一底面10设置的第三底面30为顶部。
[0078]
所述双组元喷注器构造为三底两腔结构,三底分别为第一底面10、第二底面20、第三底面30,在第一底面10与第二底面20之间形成有燃料剂腔50,在第二底面20与第三底面30之间形成有氧化剂腔40。所述氧化剂腔40的至少其中一侧设置有氧化剂入口41,所述氧化剂入口41用于向所述氧化剂腔40中通入氧化剂。优选的,所述氧化剂入口41设置于连接所述第二底面20与第三底面30的竖向壁面上。所述第二底面20为曲面结构,能够提高双组元喷注器的结构强度。
[0079]
具体地,所述第一底面10与所述第二底面20之间设置有若干长度不同的所述喷注单元结构。
[0080]
由于所述燃料剂腔50内设置有多个喷注单元结构,多个所述喷注单元结构在所述燃料剂腔50内的分布形式可以为蜂窝式分布、棋盘式分布、同心圆式分布等,此外,喷注单元结构的结构形式包括自击式、互击式、同轴直流式、同轴离心式等。优选的,本实施例中,所述喷注单元结构采用同轴直流式喷注单元结构。
[0081]
本实施例提供双组元喷注器,设置于所述第一底面10与所述第二底面 20之间喷
注单元结构采用不同长度设计,能够使得喷注单元结构声学频率错频,有利于提高燃烧的稳定性。
[0082]
具体地,所述喷注单元结构适于将所述燃料剂腔50和/或所述氧化剂腔40与外界导通;所述喷注单元结构包括:
[0083]
燃料剂喷嘴70,其至少部分的与所述燃料剂腔50连通,所述燃料剂喷嘴70一端与所述第一底面10连接并贯穿所述第一底面10;以及
[0084]
氧化剂喷嘴60,其第一端与所述第二底面20连接并贯穿所述第二底面 20与所述氧化剂腔40连通,其第二端至少部分的设置于所述燃料剂喷嘴 70内部。
[0085]
所述燃料剂喷嘴70其至少部分的与所述燃料剂腔50连通,在本实施例中,具体是通过设置在所述燃料剂喷嘴70侧壁上的至少一个径向孔71 与所述燃料剂腔50连通,所述径向孔71能够方便燃料剂进入所述喷注单元结构。
[0086]
所述燃料剂喷嘴70一端与所述第一底面10连接并贯穿所述第一底面10,使得所述喷注单元结构与所述第一底面10的接触位置形成有贯通所述第一底面10的喷注口74。
[0087]
所述氧化剂喷嘴60的第一端与所述第二底面20连接并贯穿,使得所述喷注单元结构与所述第二底面20的接触位置形成有贯通所述第二底面20 的氧化剂喷嘴入口端61,所述氧化剂喷嘴入口端61将所述氧化剂腔40与所述喷注单元结构连通,使得位于所述氧化剂腔40内的氧化剂能够从所述氧化剂喷嘴入口端61进入所述喷注单元结构。
[0088]
所述氧化剂喷嘴60的第二端至少部分的设置于所述燃料剂喷嘴70内部,且所述喷注单元结构的燃料剂喷嘴70与氧化剂喷嘴60采用嵌套式的结构设置,氧化剂喷嘴60设置于燃料剂喷嘴70内部并形成一定环形间隙 73;同时,由于所述喷注单元结构其上部与下部分别与所述第二底面20、所述第一底面10连接并贯穿设置,所述氧化剂喷嘴60内部贯穿,使得所述氧化剂喷嘴60在所述燃料剂喷嘴70内部形成有氧化剂喷嘴出口端63,所述氧化剂喷嘴60与所述燃料剂喷嘴70共用所述喷注口74,从而使得由所述径向孔71进入所述喷注单元结构的燃料剂,能够与由所述氧化剂喷嘴入口端61进入、并从氧化剂喷嘴出口端63流出的氧化剂混合,并使得混合后的燃料剂与氧化剂共同从所述喷注口74排出,喷注进入燃烧室80。
[0089]
实施例三
[0090]
结合图4所示,本实施例提供一种双组元喷注器区别于实施例二提供的所述双组元喷注器,本实施例中,第一底面10与第二底面20均为平面结构,连通设置于所述第一底面10与所述第二底面20之间的至少一个喷注单元结构均为等长度的喷注单元结构。
[0091]
实施例四
[0092]
如上述实施例一、实施例二、实施例三所述的双组元喷注器通过3d打印制成。
[0093]
通过3d打印制成所述双组元喷注器,能够降低双组元喷注器的研制成本,提高产品生产效率,依托3d打印工艺技术,将三底两腔喷注器结构和数百个喷注单元以一个整体零件形式一同打印出来,将零件数大幅减少,降低了双组元喷注器的产品成本;同时,双组元喷注器的零件数由数百件整合为一件,提高了产品的生产效率,生产周期大大缩短,且有助于提高产品固有的可靠性,提高产品的成品率。此外,一体化结构设计减少了很多钎焊、氩弧焊等人工环节,为双组元喷注器产品自动化批生产创造了条件。
[0094]
利用3d打印工艺将曲回形发汗冷却通道结构群阵式布于第一底面10,燃料从曲回形通道缓慢流出,对第一底面10燃气面起到发汗冷却的作用。与传统的多孔面板具有相同
的功能和效果,但成本相较于传统多孔面板大大降低,仅为传统多孔面板的1/5,同时,由于传统的多孔面板工艺复杂,工序多,采用3d打印工艺制成的第一底面10,工艺简单,工序少,生产周期能够大幅缩短。
[0095]
优选的,所述双组元喷注器整体结构与所述喷注单元一同采用slm激光打印成形工艺制造。
[0096]
优选的,3d打印用粉材料牌号为gh3625,粉末颗粒粒度为10~80μm,应能通过no.100#筛,且通过no.100#筛的粉末颗粒重量不少于95%。
[0097]
产品生产工艺流程主要为:采用slm激光3d打印设备打印
→
清理产品
→
热等静压
→
固溶热处理
→
机械加工
→
液流试验,具体工艺方法参数如下:
[0098]
热等静压:温度范围1050~1180℃,压力大于150mpa,保温保压时间 3~5h,氩气保护,空冷。
[0099]
固溶热处理:温度范围1090℃~1200℃保温2h、氩气速冷。
[0100]
根据使用要求进行氧化剂喷嘴和燃料喷嘴的水流阻试验,试验合格后完成产品生产。
[0101]
实施例五
[0102]
本实施例结合具体实例,对上述实施例提供的双组元喷注器进行更加详细记述,优选的,所述第一底面10、第二底面20均为曲面结构,使所述燃料剂腔50构造为双曲面凹透镜式结构,且所述第一底面10、第二底面20的球弧半径优选选用双组元喷注器直径的2~4倍。
[0103]
优选的,所述径向孔71为雨滴形,每个所述燃料剂喷嘴70共设置2 排径向孔,每排4个,所述径向孔71在所述燃料剂喷嘴70侧壁周向均布,雨滴形径向孔总面积优选采用环形间隙73面积的4~6倍。
[0104]
优选的,氧化剂喷嘴60与燃料剂喷嘴70同轴设置,其轴线平行于双组元喷注器的轴线,氧化剂喷嘴出口端63相对于喷注口74缩进4~10mm。
[0105]
氧化剂喷嘴60上游采用2处拉瓦尔型节流孔节,如图3所示,节流孔直径d1按下述公式1计算。
[0106]
公式1:
[0107]
式中,qo——每个喷注单元的氧化剂流量
[0108]
cdo——氧化剂喷嘴流量系数,一般为0.75~0.95
[0109]
d1——节流孔直径
[0110]
ρ——氧化剂密度
[0111]
pio——氧化剂腔压力
[0112]
pe——燃烧室压力
[0113]
燃料喷嘴与氧化剂喷嘴形成的环形间隙上游设有环形容腔,环形容腔横截面积一般是下游环形间隙横截面积的3~5倍,如图3所示,下游环形间隙尺寸d2、d3按下述公式2计算。
[0114]
公式2:
[0115]
式中,qf——每个喷注单元的燃料剂流量;
[0116]
cdf——燃料喷嘴流量系数,一般为0.7~0.9
[0117]
d2——环形间隙外径
[0118]
d3——环形间隙内径
[0119]
ρ——燃料密度
[0120]
k——燃料绝热指数
[0121]
pif——燃料剂腔压力
[0122]
pe——燃烧室压力
[0123]
所述第一底面10内的曲回形发汗冷却通道结构如图5所示,通道直径 d4优选选用0.1~1.0mm,发汗冷却剂用量占燃料剂总量的1%~10%,各通道均布于所述第一底面10上,各通道之间的间距不大于10mm。
[0124]
显然,上述实施例仅仅是为清楚地说明所作的举例,而并非对实施方式的限定。对于所属领域的普通技术人员来说,在上述说明的基础上还可以做出其它不同形式的变化或变动。这里无需也无法对所有的实施方式予以穷举。而由此所引伸出的显而易见的变化或变动仍处于本实用新型创造的保护范围之中。
起点商标作为专业知识产权交易平台,可以帮助大家解决很多问题,如果大家想要了解更多知产交易信息请点击 【在线咨询】或添加微信 【19522093243】与客服一对一沟通,为大家解决相关问题。
此文章来源于网络,如有侵权,请联系删除



tips