一种中温分离循环流化床锅炉掺烧污泥的系统及方法与流程



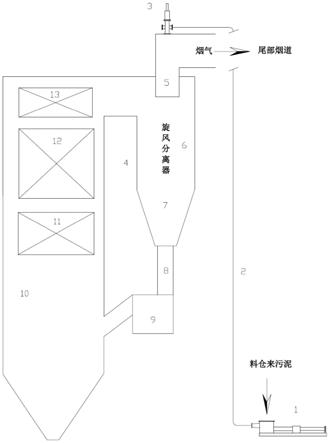
[0001]
本发明属于燃煤耦合污泥发电技术领域,具体涉及一种中温分离循环流化床锅炉掺烧污泥的系统及方法。
背景技术:
[0002]
随着我国城镇化率和城镇化水平的快速提高,我国城市污水处理能力不断提升。截止2016年底,全国废水排放总量711.10亿t,生活污水排放量占比71.4%,仅31座主要城市城镇生活污水排放量就已达176.81亿。城镇生活污水处理率93.44%,全国主要城市污泥产量按80%水分计约4 000万t。市政污泥虽然富含有机质和各类营养元素,但同时也含有大量病原菌、寄生虫卵、重金属、多环芳烃等有毒有害物质。污泥的处理技术主要包括污泥干化、浓缩脱水、厌氧消化、好氧发酵等,污泥的处置方式主要包括填埋、土地利用、建材利用、焚烧以及其他。
[0003]
目前,发达国家污泥处置技术相对成熟,法律体系亦较完善。欧洲地区污泥处置从土地利用和填埋逐步发展到焚烧,北美地区污泥处置一直以农用和焚烧为主,而日本污泥处置受土地限制主要以焚烧后建材利用为主。
[0004]
我国城镇污泥处理以土地填埋为主,各主要城市填埋场均已接近饱和,逐渐形成了“污泥围城”现象。随着城市环保政策的日益严格,会逐步降低城镇污泥直接填埋处理的比例。同时由于大多市政的工业和生活污水共用同一管网,导致污泥中各种重金属含量较高,土地利用受到限制。相比之下,污泥焚烧不仅能消灭有害物质,而且将大幅减小污泥体积,能够实现污泥的无害化处理,是最具前景的污泥处置方式之一。
[0005]
市政污泥,也称城市污泥,主要是指来自污水处理厂的污泥,这是数量最大的一类污泥,主要有以下几个特点:
[0006]
1)含水率高,通常可达80%左右;
[0007]
2)微生物、病原体含量高;
[0008]
3)恶臭污染环境;
[0009]
4)含有重金属;
[0010]
5)含有细粉末。
[0011]
污泥的上述特点,为污泥的无害化处置带了极大的困难,但同时污泥中含有不少有机质,有一定的利用价值。一般来说,污泥的处置应该按照无害化、减量化、资源化的原则来进行,而燃煤机组耦合焚烧污泥,完全符合这几项原则。
[0012]
燃煤机组耦合污泥发电作为一种污泥焚烧利用形式,具有处理能力大、适应性强、系统效率高等独特优势,近年来得到了广泛的关注。国家能源局在2017年提出“重点在直辖市、省会城市、计划单列市等36个重点城市和垃圾、污泥产生量大,土地利用较困难或空间有限,以填埋处置为主的地区,优先选取热电联产煤电机组,布局燃煤耦合垃圾及污泥发电技改项目”,并首批批准了42个污泥耦合发电示范项目。
[0013]
循环流化床cfb锅炉本身具有燃料适应性广、污染物排放低、运行灵活等诸多优
势,在国内外应用广泛。利用cfb锅炉焚烧污泥,能够发挥其燃料适应性广的特点,充分利用污泥热值,结合机组配套的已有设施提供清洁、稳定的绿色电力或热源,同时解决“污泥围城”的环境问题,是绿色循环经济的典范,近年来受到众多配有循环流化床锅炉的电厂或其它工业企业的青睐,也成为了工程应用研究领域的一个重要方向。
[0014]
对于常规的高温分离循环流化床锅炉,采用炉顶给料的方式,通过泵送系统将到厂的污泥输送至锅炉炉顶再进入cfb锅炉进行焚烧。污泥自炉顶以自由落体的形式进入炉膛,按照结团燃烧的理论机理完成整个焚烧过程。该方式的污泥掺烧比例通常可达5%~10%;
[0015]
而中温分离循环流化床锅炉为了实现中温分离,在炉膛上部布置了大量的蒸发管、过热器、高温省煤器等受热面管束,炉膛内剩余空间局限。在掺烧污泥时,为了避免污泥黏附在受热面管束上,同时考虑污泥中水分蒸发吸热对炉膛上部空间温度分布的影响,进而影响到对流受热面的传热换热,因此无法像高温分离循环流化床锅炉一样实现污泥炉顶给料,使得循环流化床锅炉燃料适应性广的优势在掺烧污泥时难以发挥。
[0016]
鉴于中温分离循环流化床锅炉的结构特点,有工程技术人员提出了借鉴循环流化床锅炉掺烧煤泥的实践经验,采用炉膛中部给料的方式,将泵送系统来的污泥通过喷枪注入炉膛中部。中部给料方案的系统布置受到现场条件影响比较多,布置困难;给料点一般设在侧墙中部,而循环流化床锅炉炉膛宽深比例悬殊,如果在侧墙给料势必较造成污泥分布的严重不均匀,影响锅炉运行的稳定性;另外,中部给料方式的喷枪机械故障较高,后期维护工作量大。同时,污泥含水率在
±
80%,远高于煤泥含水率30%,炉膛中部给料贴近床层,将大幅影响床温的稳定性。综上所述,对于掺烧污泥而言,炉膛中部给料在中温分离循环流化床锅炉上仍不够成熟。
技术实现要素:
[0017]
本发明的目的在于针对现有的循环流化床锅炉掺烧污泥技术,克服其难以在中温分离循环流化床锅炉上实现一定比例污泥掺烧的缺点,提供了一种中温分离循环流化床锅炉掺烧污泥的系统及方法,通过将污泥引入中温分离旋风分离器,利用500~650℃的中温烟气实现污泥干化,使污泥含水率在送入炉膛床层前降至40%左右(与褐煤相当),从而实现在中温分离流化床锅炉上掺烧污泥的目的。
[0018]
本发明采用如下技术方案来实现的:
[0019]
一种中温分离循环流化床锅炉掺烧污泥的系统,所述系统包括柱塞泵、泵送管道、立式给料机、中温分离旋风分离器、返料装置以及循环流化床锅炉炉膛;其中,柱塞泵用于将污泥经泵送管道输送至设置在中温分离旋风分离器中心筒转角烟道上方的立式给料机,立式给料机用于将团聚的污泥切割、打散后进入中心筒,污泥自上而下依次经过中心筒、分离器筒体、分离器锥体,污泥含水率降至40%左右后落入分离器排灰口,与循环灰混合后再经过返料装置输送至循环流化床锅炉炉膛进行燃烧。
[0020]
本发明进一步的改进在于,污泥的含水率为
±
80%。
[0021]
本发明进一步的改进在于,循环流化床锅炉炉膛上部自下而上依次布置有蒸发器、过热器和高温省煤器。
[0022]
本发明进一步的改进在于,循环流化床锅炉采用中温分离方式,中温烟气的温度
在500℃~650℃。
[0023]
一种中温分离循环流化床锅炉掺烧污泥的方法,该方法基于所述的一种中温分离循环流化床锅炉掺烧污泥的系统,包括以下步骤:在中温分离循环流化床锅炉掺烧污泥时,通过柱塞泵将污泥经泵送管道输送至设置在中温分离旋风分离器中心筒转角烟道上方的立式给料机,立式给料机将团聚的污泥切割、打散后进入中心筒,污泥自上而下依次经过中心筒、分离器筒体、分离器锥体,运动过程中与上升的中温烟气直接接触换热,在强烈的湍流作用下,污泥中的水分迅速蒸发,颗粒收缩、坍塌、再分散,污泥含水率降至40%左右后落入分离器排灰口,与循环灰混合后再经过返料装置输送至循环流化床锅炉炉膛进行燃烧。
[0024]
本发明进一步的改进在于,立式给料机以螺旋进料的方式将团聚的污泥切割、打散后进入中心筒。
[0025]
本发明至少具有如下有益的技术效果:
[0026]
本发明提供的一种中温分离循环流化床锅炉掺烧污泥的系统及方法,采用柱塞泵将污泥经泵送管道输送至设置在中温分离旋风分离器中心筒转角烟道上方的立式给料机,输送方式简单可靠,可实现连续输送,且泵体与管道均处于密封状态,无臭气泄漏,对环境无不良影响。立式给料机以螺旋进料的方式给入中温分离旋风分离器,给料机的螺旋翅片可将团聚的污泥进行切割、打散,能够有效防止污泥过度结团,同时也更加有利于污泥在进入中心筒后的前段干燥过程。污泥进入旋风分离器后,自上而下依次经过中心筒、分离器筒体、分离器锥体,运动过程中与上升的中温烟气(温度在500℃~650℃)直接接触换热,污泥与烟气逆向运动,受上升烟气的托举作用,污泥在旋风分离器内与烟气的接触时间更长,同时由于旋风分离器中气流运动轨迹为螺旋式,气流的湍动度更强,在强烈的湍流作用下,污泥中的水分迅速蒸发,颗粒收缩、坍塌、再分散,污泥含水率降至40%左右,物理性状由团聚态变为分散态,最后落入旋风分离器排灰口,再经过返料装置输送至循环流化床锅炉炉膛进行燃烧,由于送入炉膛床层的污泥含水率在40%左右,与褐煤相当,其对炉内燃烧的影响很小,尤其对于燃用褐煤的循环流化床锅炉,几乎不会对床层燃烧产生任何不利影响。携湿烟气经中心筒进入尾部烟道,利用锅炉已配备的脱硝、除尘、脱硫等环保设施,最终实现达标排放,最大限度地利用了既有设施,在降低环保成本的基础上实现了较好的环保效益。
[0027]
与现有污泥掺烧技术相比,本发明采用旋风分离器中心筒给料的方式,很好地解决了传统中温分离循环流化床锅炉难以进行污泥掺烧的问题,巧妙地避开了布置在炉膛上部的大量蒸发、过热受热面管束,避免污泥黏附在受热面管束上,也防止了污泥中水分蒸发吸热对炉膛上部空间温度分布的影响,进而影响到对流受热面的传热换热,同时利用分离器内螺旋上升的高湍动度烟气与污泥进行逆流换热,实现了污泥入炉前的干燥,降低了掺烧污泥对炉内燃烧影响;干燥污泥(含水率40%)经返料装置送入炉膛,最大限度地降低了对床层参数的影响。利用旋风分离器内具有高湍动度的中温烟气(温度在500℃~650℃)完成污泥入炉前的改造过程,污泥含水率降至40%左右,物理性状由团聚态变为分散态,再经过返料装置回送至炉内燃烧,由于送入炉膛床层的污泥含水率在40%左右,与褐煤相当,尤其对于燃用褐煤的循环流化床锅炉,几乎不会对床层燃烧产生任何不利影响。
附图说明
[0028]
图1为本发明一种中温分离循环流化床锅炉掺烧污泥的系统及方法示意图。
[0029]
图中标记说明:
[0030]
1为柱塞泵,2为泵送管道,3为立式给料机,4为中温分离旋风分离器,5为中心筒,6为分离器筒体,7为分离器锥体,8为分离器排灰口,9为返料装置,10为循环流化床锅炉炉膛,11为蒸发器,12为过热器,13为高温省煤器。
具体实施方式
[0031]
下面结合附图对本发明做进一步地详细说明。
[0032]
参见图1,本发明提供的一种中温分离循环流化床锅炉掺烧污泥的系统,所述系统包括柱塞泵1、泵送管道2、立式给料机3、中温分离旋风分离器4、返料装置9、循环流化床锅炉炉膛10。其中中温分离旋风分离器4由中心筒5、分离器筒体6、分离器锥体7以及分离器排灰口8,循环流化床锅炉为中温分离循环床锅炉,循环流化床锅炉炉膛10上部自下而上依次布置有蒸发器11、过热器12和高温省煤器13。从料仓来的污泥自柱塞泵2入口吸入,通过往复运动的活塞加压后经泵送管道2进入设置在中温分离旋风分离器4顶部的立式给料机3,再由立式给料机3给入分离器中心筒5。污泥在下落过程中与上升的中温烟气(温度在500℃~650℃)直接接触换热,自上而下依次经过中心筒5、分离器筒体6、分离器锥体7,同时在烟气的作用下进行干燥,污泥含水率降至40%左右后落入分离器排灰口8,再经过返料装置9输送至循环流化床锅炉炉膛10进行燃烧。
[0033]
本发明提供的一种中温分离循环流化床锅炉掺烧污泥的方法,包括以下步骤:在中温分离循环流化床锅炉掺烧污泥时,通过柱塞泵1将污泥经泵送管道2输送至设置在中温分离旋风分离器4中心筒5转角烟道上方的立式给料机3,立式给料机3以螺旋进料的方式将团聚的污泥切割、打散后进入中心筒,污泥自上而下依次经过中心筒5、分离器筒体6、分离器锥体7,运动过程中与上升的中温烟气(温度在500℃~650℃)直接接触换热,在强烈的湍流作用下,污泥中的水分迅速蒸发,颗粒收缩、坍塌、再分散,污泥含水率降至40%左右后落入分离器排灰口8,与循环灰混合后再经过返料装置9输送至循环流化床锅炉炉膛10进行燃烧。
[0034]
污泥通过柱塞泵1经泵送管道2输送至设置在中温分离旋风分离器4中心筒5转角烟道上方的立式给料机3,输送方式简单可靠,可实现连续输送,且泵体与管道均处于密封状态,无臭气泄漏,对环境无不良影响。立式给料机3以螺旋进料的方式给入中温分离旋风分离器4,给料机的螺旋翅片可将团聚的污泥进行切割、打散,能够有效防止污泥过度结团,同时也更加有利于污泥在进入中心筒后的前段干燥过程。污泥进入旋风分离器4后,自上而下依次经过中心筒5、分离器筒体6、分离器锥体7,运动过程中与上升的中温烟气(温度在500℃~650℃)直接接触换热,污泥与烟气逆向运动,受上升烟气的托举作用,污泥在旋风分离器4内与烟气的接触时间更长,同时由于旋风分离器4中气流运动轨迹为螺旋式,气流的湍动度更强,在强烈的湍流作用下,污泥中的水分迅速蒸发,颗粒收缩、坍塌、再分散,污泥含水率降至40%左右,物理性状由团聚态变为分散态,最后落入分离器排灰口8,再经过返料装置9输送至循环流化床锅炉炉膛10进行燃烧,由于送入炉膛床层的污泥含水率在40%左右,与褐煤相当,其对炉内燃烧的影响很小,尤其对于燃用褐煤的循环流化床锅炉,几乎不会对床层燃烧产生任何不利影响。携湿烟气经中心筒5进入尾部烟道,利用锅炉已配备的脱硝、除尘、脱硫等环保设施,最终实现达标排放,最大限度地利用了既有设施,在降低
环保成本的基础上实现了较好的环保效益。
[0035]
本发明中,污泥自料仓被吸入柱塞泵,水分通常在80%左右,加压后进入分离器顶部的立式给料机,由给料机给入中心筒。污泥在中心筒下落运动的过程中与高湍动度的烟气(温度在500℃~650℃)相遇并逆向运动,实现了极为强烈的对流换热,大幅度提高了换热系数,使得污泥能够在较短的时间和行程内完成部分水分的蒸发过程。
[0036]
本发明充分考虑中温分离循环流化床的结构特点,炉膛上部布置有较多的受热面管束。采用分离器中心筒给料方式,避免了污泥黏附受热面管束以及对受热面传热换热的影响,解决了中温分离循环流化床锅炉掺烧污泥的问题。
[0037]
综上所述,本发明通过分离器中心筒给料的方式,巧妙地避开了布置在炉膛上部的大量蒸发、过热受热面管束,避免污泥黏附在受热面管束上,也防止了污泥中水分蒸发吸热对炉膛上部空间温度分布的影响,进而影响到对流受热面的传热换热,同时利用分离器内螺旋上升的高湍动度烟气与污泥进行逆流换热,实现了污泥入炉前的干燥,降低了掺烧污泥对炉内燃烧影响;干燥污泥(含水率40%)经返料装置送入炉膛,最大限度地降低了对床层参数的影响,同时携湿烟气经中心筒进入尾部烟道,利用锅炉已配备的脱硝、除尘、脱硫等环保设施,最终实现达标排放,最大限度地利用了既有设施,在降低环保成本的基础上实现了较好的环保效益。对中温分离循环流化床锅炉的改造工程量少,系统布置简单,能够实现相当比例污泥掺烧,生产运行成本低,能够实现可观的经济效益。
起点商标作为专业知识产权交易平台,可以帮助大家解决很多问题,如果大家想要了解更多知产交易信息请点击 【在线咨询】或添加微信 【19522093243】与客服一对一沟通,为大家解决相关问题。
此文章来源于网络,如有侵权,请联系删除



tips