一种轴向贯通的椭圆形翅片管的制作方法



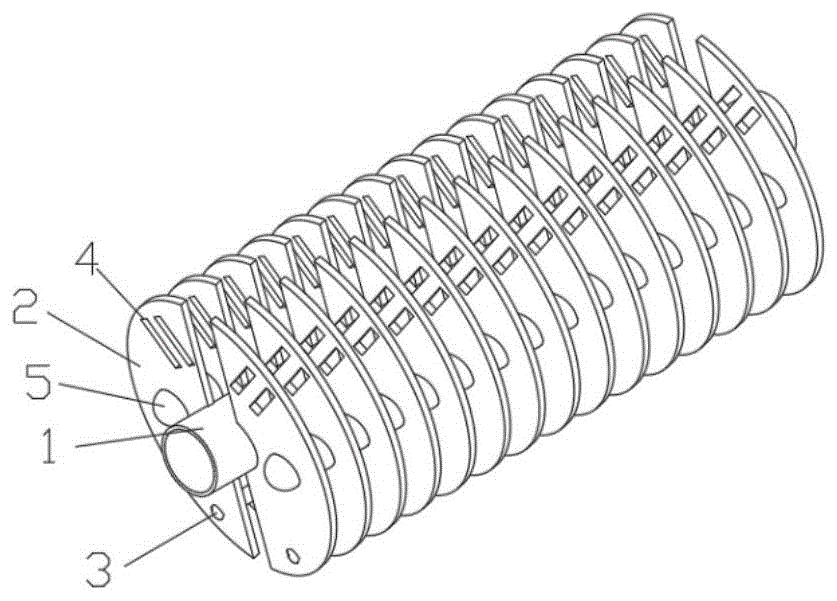
本发明涉及换热技术领域,特别是涉及一种轴向贯通的椭圆形翅片管。
背景技术:
随着社会的高速发展,我国对于能源的需求不断扩大。为了实现更加绿色、更可持续的发展,能源的高效可持续利用必须引起重视。我国能源资源结构基本呈现出富煤、贫油、少气的特点,这决定了我国现阶段的能源消耗状况以煤炭消耗为主,火电在电力工业中所占比重较大。由于火电在我国能源结构中的基础性作用,火电的能源转换效率将在很大程度上影响能源综合利用效率及能源消费总量。要提升火电机组的能源利用效率,减少火电厂锅炉排烟热损失是重要的技术方向。由于锅炉排烟温度较高,烟气流量大,以及烟气余热的巨大利用潜力,回收利用锅炉排烟余热可显著提高火电机组的能源利用率,对火电行业的节能减排有重要的意义。
低温省煤器是回收锅炉排烟余热的重要设备之一,低温省煤器利用烟气余热来加热凝结水,通过回收排烟热量进入回热系统,可取代部分抽汽,使单位新蒸汽在汽轮机中的做功增加,且与锅炉本身的省煤器相比,由于工况不同,制造成本较低,还可通过合理选择凝结水的取、回水位置及流量来控制烟气对换热器的腐蚀、提高热经济性。
目前国内的烟气换热设备多采用螺旋翅片管,但是由于在火力发电厂排放的烟气含尘量高,螺旋翅片管容易积灰,严重的甚至会堵塞烟道,从而影响整个电厂的正常运行。同时由于螺旋翅片管的烟气侧阻力损失大,在一些电厂改造工程中原有的引风机压头裕量小,若换热设备的阻力过大,需对引风机改造,这会极大的增加改造成本和工程量,因而极大的制约了这种换热管的使用。
技术实现要素:
鉴于上述问题,提出了本发明实施例以便提供一种克服上述问题或者至少部分地解决上述问题的一种轴向贯通的椭圆形翅片管。
为了解决上述问题,本发明实施例公开了一种轴向贯通的椭圆形翅片管,包括:
基管(1)、设置在基管(1)两侧的多个翅片组(2)以及绕流杆(3);
每个所述翅片组(2)包括两片对称的翅片;其中,所述翅片内侧中心设有凹槽;
所述翅片组(2)通过所述凹槽与基管(1)外壁对称连接;
所述翅片组(2)的迎风侧对称布置了扰流杆(3);其中,取包含所述基管(1)的轴线且垂直于烟气流动方向的平面为分界面,将所述翅片组(2)分为两部分,上游为背风侧,下游为所述迎风侧。
优选的,所述椭圆形翅片管,还包括:
涡发生器(5);
所述涡发生器(5)被对称的布置在所述翅片组(2)上;其中,所述涡发生器(5)形状为球凸、矩形、三角形以及异形中的一种。
优选的,所述涡发生器(5)的形状为球凸。
优选的,所述扰流杆(3)的截面形状为圆形、矩形、三角形以及异形中的至少一种。
优选的,所述扰流杆(3)的截面形状为圆形;
所述扰流杆(3)不超过3对;
所述扰流杆(3)的直径范围为4~10mm。
优选的,所述翅片组(2)内的翅片之间有间隙,并且所述迎风侧的间隙小于该翅片组所述背风侧的间隙;
所述翅片的所述迎风侧的面积大于该翅片所述背风侧的面积。
优选的,所述翅片组(2)在所述背风侧对称设置了两对呈倒“八”的开缝(4);其中,
所述开缝(4)长宽比为4∶1;
所述开缝(4)长度范围为10~16mm;
所述开缝(4)与来流方向夹角为30°~45°。
优选的,所述翅片的外侧轮廓呈半椭圆形;
所述翅片组(2)中的两片翅片的外侧轮廓整体呈椭圆型;
所述翅片组(2)构成的椭圆长轴与短轴的比值范围为2~8;
所述翅片的厚度为1~3mm;
所述翅片的高度h的范围为38~80mm;其中,h为所述基管(1)中心到所述长轴端点的距离。
优选的,所述翅片组(2)所在平面与所述基管(1)的轴线垂直线的夹角的取值范围为10°~20°;
相邻所述翅片组(2)的间距范围为4~10mm。
优选的,所述基管(1)为圆形或椭圆形;
所述基管(1)、所述翅片组(2)、所述绕流杆(3)以及所述涡发生器(5)之间的连接方式为焊接。
本发明实施例包括以下优点:
本发明实施例提供了一种轴向贯通的椭圆形翅片管,包括:基管1、设置在基管1两侧的多个翅片组2以及绕流杆3;每个所述翅片组2包括两片对称的翅片;其中,所述翅片内侧中心设有凹槽;所述翅片组2通过所述凹槽与基管1外壁对称连接;所述翅片组2的迎风侧对称布置了扰流杆3;其中,取包含所述基管1的轴线且垂直于烟气流动方向的平面为分界面,将所述翅片组2分为两部分,上游为背风侧,下游为所述迎风侧。相较现有技术,本发明在保证烟气阻力减少或者增加不大的情况下,增加了椭圆形翅片管的传热能力,改善了烟气的速度和翅片表面的温度梯度的协同性从而增强了椭圆形翅片管的综合换热性能,而且能够减轻椭圆形翅片管的积灰、腐蚀以及磨损,提高了低温省煤器运行的安全性和使用寿命。
附图说明
图1是本发明提供的一种轴向贯通的椭圆形翅片管的结构示意图;
图2(a)是本发明提供的翅片正面的示意图;
图2(b)是本发明提供的沿图2(a)中a-a线的截面图;
图3为本发明提供的将翅片以基管水平垂直线作为对称线镜像翻转所得另一种布置方式结构示意图;
图4(a)为本发明提供的图3翅片表面的结构示意图;
图4(b)是本发明提供的沿图4(a)中a-a线的截面图。
附图标记:1-基管、2-翅片组、3-扰流杆、4-开缝、5-涡发生器。
具体实施方式
下面将参照附图更详细地描述本发明的示例性实施例。虽然附图中显示了本发明的示例性实施例,然而应当理解,可以以各种形式实现本发明而不应被这里阐述的实施例所限制。相反,提供这些实施例是为了能够更透彻地理解本发明,并且能够将本发明的范围完整的传达给本领域的技术人员。
目前,目前国内的烟气换热设备多采用螺旋翅片管,但是由于在火力发电厂排放的烟气含尘量高,螺旋翅片管容易积灰,严重的甚至会堵塞烟道,从而影响整个电厂的正常运行。同时由于螺旋翅片管的烟气侧阻力损失大,在一些电厂改造工程中原有的引风机压头裕量小,若换热设备的阻力过大,需对引风机改造,这会极大的增加改造成本和工程量,因而极大的制约了这种换热管的使用。
同时,目前烟气换热设备还包括:全椭圆h型翅片管、组合式仿生防磨h型翅片椭圆式烟气换热管、轴向贯通的h型翅片管及其换热管束以及常规h型翅片管。下面对于这几种换热设备进行介绍。
一、全椭圆h型翅片管
该设备包括两根相互平行的基管,以及设在两根基管两侧若干组相互对称的翅片;基管为椭圆基管,翅片为半椭圆型翅片,相互对称的每组半椭圆型翅片组成的平面均垂直于椭圆基管的轴心线方向,翅片管整体呈双h型。其缺点在于:
由于h型翅片的4个角面离基管中心较远,其换热效果差,因此影响了整个翅片管的换热效率,且金属耗量大,存在着一定的浪费。
二、组合式仿生防磨h型翅片椭圆式烟气换热管
该设备采用椭圆管作为基管,在椭圆管中两侧设置翅片,通过在翅片上设置若干对半球形丁胞和涡产生器。其缺点在于:
尽管丁胞的存在可以有效地降低流动阻力,避免流场中大涡湍流的形成。但丁胞的位置对与传热效果的影响更加重要。将丁胞设置在迎风侧对于传热梯度的连续性造成破坏,且更容易磨损因而降低使用寿命。
三、轴向贯通的h型翅片管及其换热管束
该设备在烟气流出的一侧设置导流片穿过所有贯通槽,并将基管轴向各翅片组贯穿连接,使h型翅片管轴向横剖面由平面变成三维结构。
其缺点在于:
这种设计由于在背风侧也设置了贯通槽,这是不利于气流流动的,会产生严重的积灰磨损问题,降低翅片管使用寿命。
四、常规h型翅片管
这种设备均是通过对常规h型翅片管的翅片外侧边缘进行各种变形。其缺点在于:
虽然该设备在含灰高速气流下,翅片外侧磨损情况会更为严重,降低翅片管寿命。
参照图1,示出了本发明提供的一种轴向贯通的椭圆形翅片管的结构示意图,椭圆形翅片管包括:基管1、设置在基管1两侧的多个翅片组2以及绕流杆3;每个翅片组2包括两片对称的翅片;其中,翅片内侧中心设有凹槽;翅片组2通过该凹槽与基管1外壁对称连接;取包含基管1的轴线且垂直于烟气流动方向的平面为分界面,将翅片组2分为两部分,上游为背风侧,下游为所述迎风侧;翅片组2的迎风侧对称布置了扰流杆3。
需要说明的是,参照图2(a),示出了本发明提供的翅片正面的示意图,图中表示流动方向的箭头所在翅片组2的下半部分为迎风侧,与之相对的上半部分为背风侧。基管1的管径范围为20~40mm。
在本发明实施例中,椭圆形翅片管用于通过基管1中的液体回收被排放烟气中的热量,达到节能减排的目的。在实际生产中,该椭圆形翅片管可被应用于火力发电站,特别是应用到火力发电站锅炉侧的低温省煤器中进行排烟热量的回收。
在实际应用中,上述椭圆形翅片管还包括涡发生器5,该涡发生器5形状为球凸、矩形、三角形以及异形中的一种,该涡发生器5被对称的布置在所述翅片组2上。
参照图2(a),在本发明实施例中,优选球凸为涡发生器5的形状。
经试验发现球凸型涡发生器5相比较于矩形、三角形以及异形涡发生器最主要在于可以避过最大磨损角。基管1在迎风面最大磨损均发生在与来流方向15°~45°的范围,而无论矩形、异形还是三角形为了增强扰动提高换热效果的最佳角度均为30°~40°。选择球凸作为涡发生器时烟气的粒子正向冲击时,冲击角为90°,该角度并不在最大磨损角度范围内,因此基管1的磨损率相对较低。
进一步的,图2(a),翅片的外侧轮廓呈半椭圆形;翅片组2中的两片翅片的外侧轮廓整体呈椭圆型,上述球凸型涡发生器5被设置在翅片组2构成的椭圆短轴线上。
结合目前的纵向涡强化技术应用场合特点,将球凸型涡发生器5设置在翅片组2构成的椭圆短轴线上相对于将球凸型涡发生器5设置在迎风面的好处是:使翅片的迎风侧与背风侧的气流均可造成扰动与混流,也可强化传热,减少了积灰。当气流流经涡产生器时,由于球凸型涡产生器5结构的影响,翅片表面边界层遭到破坏。因为翅片传热不是连续的,基管1在翅片组2的中间,所以背风面会有一个区域传热效果不好,该区域称为传热管尾部滞止区。球凸型涡产生器5使传热管尾部滞止区明显减少,背风侧气流扰动明显增强,卷吸滞止区的气体进入主流区,从而强化了传热管尾部滞止区的对流传热性能。
同时,将球凸型涡发生器5设置在翅片组2构成的椭圆短轴线上,球凸型涡发生器5内部可产生类似龙卷风的气流,并且该气流可以造成一种类似气垫的效应,即使是在湍流流动的情况下,也能防止阻力的增加,实现了对气体流动阻力的控制,提高了低温省煤器运行的安全性和使用寿命。
在实际应用中,扰流杆3的截面形状可以为圆形、矩形、三角形以及异形中的至少一种。
参照图2(a)和图2(b),本发明实施例优选圆形作为扰流杆3的截面形状。
经试验发现,扰流杆3可以实现对椭圆形翅片管背风侧的涡流滞止区的改善,是一种新型简易的烟气均流方式。虽然可以选择矩形、三角形以及异形中的至少一种作为扰流杆3的截面形状,但是由于扰流杆3不仅可以增强扰动以提高换热效果,还可以增加扰流杆3与基管1之间的的有效传热,而其它形状没有增加扰流杆3与基管1之间的的有效传热的效果,所以圆形作为扰流杆3截面形状的最优选择。
具体的,虽然矩形、三角形以及异形都可以通过增加面积来达到增强换热的效果,但是在扰流杆3与翅片贯通的边界处会形成一个不均匀的温度梯度,而截面为圆形的扰流杆3在翅片贯穿处可以形成一个均匀的温度梯度,利于提高热量传递效率。
同时,气流飞回粒子在扰流杆3处受两侧壁面影响更大,扰流杆3能更大程度减少了粒子对基管1外壁的冲击速度,而在包括撞击角度在内的其他条件不变的情况下,撞击速度越大基管1的磨损就越大,因此截面为圆形的扰流杆结构明显优于截面为其他形状的扰流杆。此外,扰流杆3的布置位置可以选择迎风侧及背风侧。当扰流杆3布置在迎风侧时对于背风侧涡流滞止区的影响更大。所以综合考虑,扰流杆3截面选择圆形并且布置在迎风侧为最优方案。
更进一步的,扰流杆3不超过3对,被对称布置在迎风侧的两侧。同时,扰流杆3的直径范围为4~10mm。
在本发明实施例中,参照图2(a),翅片组2内的翅片之间有间隙,并且迎风侧的间隙小于该翅片组背风侧的间隙,并且翅片的迎风侧的面积大于该翅片背风侧的面积。
经试验发现,烟气流经现有背风侧和迎风侧面积相等的翅片管时,背风侧会产生明显的气流分离和回流,换热性能降低且积灰更加严重。本发明椭圆形翅片管通过改变迎风侧和背风侧翅片之间的间隙大小,让迎风侧面积与背风侧的间隙更大,使本发明椭圆形翅片管可以有效避免传热恶化。
同时,翅片组2内翅片中部间隙去除了部分在翅片进口和出口分离区的换热面积,降低了进出口分离区传热恶化对整个翅片传热的影响,提高了翅片的平均对流换热系数和翅片的传热效率。
在本发明实施例中,参照图2(a),翅片组2在背风侧对称设置了两对呈倒“八”的开缝4;其中,开缝4长宽比为4∶1;开缝4长度范围为10~16mm;开缝4与来流方向夹角为30°~45°。
具体的开缝原因为:一、因为倒“八”型开缝4的缝隙沿基管1的中心线延伸,所以开缝后基管1向翅片外侧的导热受影响不大,避免了开缝阻断部分导热路径从而产生的消极影响;二、倒“八”型开缝4有效地针对气流流动路径进行了缝隙的布置,具有倒“八”型开缝的翅片可使气流在流动路径中多次受到缝隙的影响,从而使气流所受到的扰动更强,并对于更大范围的翅片表面边界层进行了破坏,改善了开缝附近流场与温度场的协同性,提高了换热性能。
在本发明实施例中,参照图2(a),翅片的外侧轮廓呈半椭圆形;翅片组2中的两片翅片的外侧轮廓整体呈椭圆型;翅片组2构成的椭圆长轴与短轴的比值范围为2~8;翅片的厚度为1~3mm;翅片的高度h的范围为38~80mm;其中,h为基管1中心到上述长轴端点的距离。
设计椭圆形翅片组2的原因:根据圆锥曲线的定义,椭圆是平面内到两定点的距离之和等于常数的动点轨迹。两定点即为椭圆焦点,如果翅片组2构成的椭圆以两椭圆基管作为焦点,则翅片边缘任意点到两基管距离和为定值,保证了整个翅片组2的换热均匀性,避免了边缘传热不均,以及性能劣化,进而造成材料的浪费的缺点。本发明翅片组2构成的椭圆能够有效改善流场,减小烟气阻力。
由于椭圆型翅片组2表面的流程更长,换热效果更好,意味着对于换热量一定的换热设备,采取本发明提出的结构可以节省钢材消耗,降低成本。
在本发明实施例中,参照图2(b),图中翅片左倾。翅片组2所在平面与基管1的轴线垂直线的夹角的取值范围为10°~20°,即翅片组2所在平面与基管1的轴线的夹角范围为70°~80°;相邻翅片组2的间距范围为4~10mm;球凸涡发生器5半径范围为2~5mm;球凸涡发生器5的中心与基管1壁面的最短距离的范围为10~20mm;基管1为圆形或椭圆形;基管1、翅片组2、绕流杆3以及涡发生器5之间的连接方式为焊接。
参照图3,示出了本发明提供的将翅片以基管水平垂直线作为对称线镜像翻转所得另一种布置方式结构示意图,该图中翅片为右倾,翅片组2所在平面与基管1的轴线垂直线的夹角的取值范围为10°~20°。图1、图2(a)、图2(b)和图3、图4(a)、图4(b)分别是一种轴向贯通的椭圆形翅片管中翅片左倾和右倾的结构示意图,它们除了翅片的倾斜方向与基管1的轴线垂直线对称外,其它结构参数和上述实施例相同,所以在此不再累述。
举例说明,具体参照图2(a)和图2(b)。在实际应用中会采用多组椭圆形翅片管去进行烟气等流体的热量回收,椭圆形翅片管采用顺排或者错排的形式排列。其中,每根椭圆形翅片管中的基管1两侧都对称焊接了多组翅片组2,两个半椭圆形的翅片中间为基管1,所有翅片的排列方向均相同,翅片采用磨具加工制得,基管1的横截面为圆环形。基管1的管径为20mm;翅片厚度为2mm;翅片组2构成的椭圆长轴为76mm,短轴为38mm;球凸型涡发生器5的半径为4mm;翅片与基管1轴线的垂直线夹角为15°;相邻翅片组2之间的间距为6mm;迎风侧对称的设置了一对扰流杆3,且扰流杆3的中心到基管1中心的垂直距离为10mm,扰流杆3的直径为4mm;开缝4的长为12mm,宽为3mm,开缝4与来流方向夹角为45°;球凸型涡发生器5的中心与基管1壁面的最小距离为20mm。
在回收烟气的热量过程中,基管1中用循环流动的水通过各翅片组2吸收烟气中的热量。具体的,烟气从图2(a)中标注的流动方向进入椭圆形翅片管的迎风侧经过扰流杆3的扰动,让扰流杆3与翅片贯穿处的边界温度呈均匀的温度梯度,同时该扰流杆3也减少了粒子对基管1外壁的冲击速度,减少了基管1的磨损度;然后,烟气经过球凸型涡发生器5,使球凸型涡发生器5产生类似龙卷风的气流造成一种类似气垫的效应,实现了对烟气阻力的控制,同时球凸型涡发生器5也使翅片表面边界层遭到破坏,基管1尾部滞止区明显减少,背风侧流体扰动明显增强,卷吸滞止区的气体进入主流区,从而强化了基管1的对流传热性能;接着烟气流经背风侧的开缝4,让烟气受到的扰动更强,对更大范围的翅片表面边界层进行了破坏。上述整个过程都是为了减少烟气对基管1的磨损,增加烟气的扰动,以及增加基管1的传热效率。
上述实施例的有益效果:
本发明实施例提供了一种轴向贯通的椭圆形翅片管,包括:基管1、设置在基管1两侧的多个翅片组2以及绕流杆3;每个所述翅片组2包括两片对称的翅片;其中,所述翅片内侧中心设有凹槽;所述翅片组2通过所述凹槽与基管1外壁对称连接;所述翅片组2的迎风侧对称布置了扰流杆3;其中,取包含所述基管1的轴线且垂直于烟气流动方向的平面为分界面,将所述翅片组2分为两部分,上游为背风侧,下游为所述迎风侧。相较现有技术,本发明在保证烟气阻力减少或者增加不大的情况下,增加了椭圆形翅片管的传热能力,改善了烟气的速度和翅片表面的温度梯度的协同性从而增强了椭圆形翅片管的综合换热性能,而且能够减轻椭圆形翅片管的积灰、腐蚀以及磨损,提高了低温省煤器运行的安全性和使用寿命。
上面结合附图对本发明的实施例进行了描述,但是本发明并不局限于上述的具体实施方式,上述的具体实施方式仅仅是示意性的,而不是限制性的,本领域的普通技术人员在本发明的启示下,在不脱离本发明宗旨和权利要求所保护的范围情况下,还可做出很多形式,均属于本发明的保护之内。
起点商标作为专业知识产权交易平台,可以帮助大家解决很多问题,如果大家想要了解更多知产交易信息请点击 【在线咨询】或添加微信 【19522093243】与客服一对一沟通,为大家解决相关问题。
此文章来源于网络,如有侵权,请联系删除


