高效燃烧冷却系统及烟气冷却器的制作方法



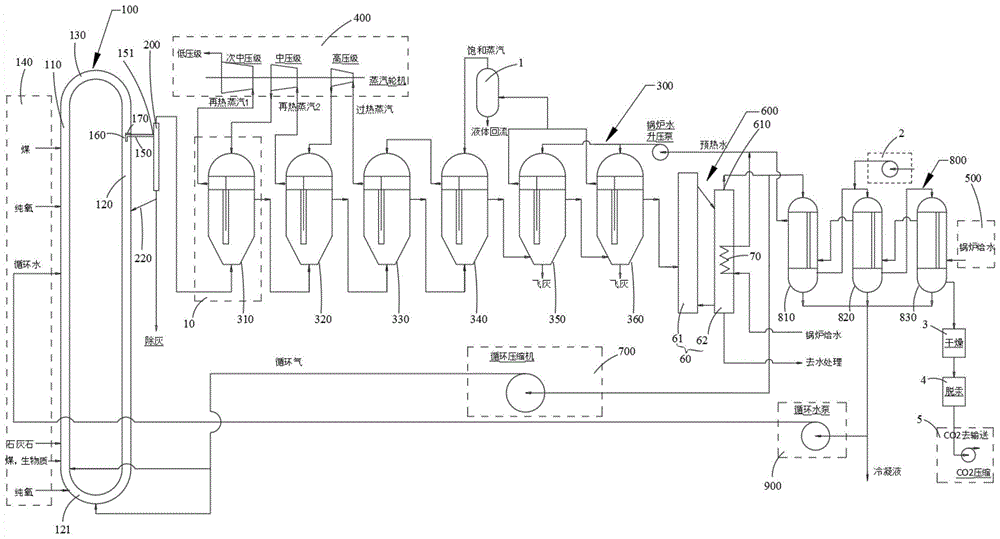
本实用新型涉及燃料燃烧技术领域,尤其是涉及一种利用纯氧的高效燃烧冷却系统及烟气冷却器。
背景技术:
随着我国国民经济日益增长,各行业用电量逐年增大,各电力行业如雨后春笋般迅猛发展。近年来,火电燃煤机组持续占据领导地位,在今后很长一段时间内不会发生明显变化。这些火电机组带给我们赖以生存的电能的同时,消耗了大量不可再生的煤炭资源。
作为储量丰富的煤炭在其被利用过程中会产生多种废弃物、污染物,同时释放大量的温室气体二氧化碳,高效、低碳、减排是实现煤炭洁净利用的重要课题。煤炭发电是其最重要的应用领域,现有的发电过程已可实现粉尘、硫化物、氮化物减排和控制,而对二氧化碳排放还只是一个设想和讨论的过程,还没有找到太好的办法。大量的研究和开发工作从各方面展开包括燃烧前脱碳如igcc(integratedgasificationcombinedcycle,整体煤气化联合循环发电系统)、燃烧后脱碳如烟气吸收二氧化碳、以及纯氧燃烧。igcc和烟气吸收二氧化碳脱碳均存在系统复杂成本增高等特点,而在纯氧燃烧方面,已经进行过的一些尝试如以纯氧代替空气在粉煤锅炉的试验效果不尽如意。
技术实现要素:
基于此,本实用新型的目的在于提供一种高效燃烧冷却系统及烟气冷却器,通过利用纯氧进行燃烧,实现低污染排放,并且能高效回收二氧化碳。
为解决上述技术问题,本实用新型所采用的技术方案是:一种高效燃烧冷却系统,其包括燃烧机构、旋风除尘器、冷却机构、蒸汽轮机、锅炉给水机构、除尘机构及冷凝机构,所述燃烧机构包括燃烧侧及料柱侧,所述燃烧侧上端部与料柱侧上端部通过第一连接管连通,所述料柱侧底端部连接有导料管,所述导料管一端与燃烧侧连通;所述料柱侧内侧上端部设置有短管,所述短管延伸出料柱侧设置,所述短管上设置有烟气出口,所述旋风除尘器与短管连接,所述旋风除尘器通过管道与冷却机构连接;所述冷却机构设置有多个烟气冷却器,所述烟气冷却器依次连接,所述烟气冷却器用于对从旋风除尘器出来的烟气进行降温处理,所述烟气冷却器与蒸汽轮机连接,所述除尘机构通过管道与冷却机构连接,所述除尘机构设置有出烟口,所述除尘机构的出烟口通过管道与冷凝机构连接,所述锅炉给水机构提供锅炉给水给冷凝机构,经由除尘机构的出烟口排出的含有水蒸汽的烟气进入到冷凝机构内,在冷凝机构内烟气与锅炉给水进行换热。
在其中一个实施例中,所述烟气冷却器包括容器外壳,所述容器外壳内设置有换热管,所述换热管设置有出口部及进口部,所述出口部一侧开设有水或蒸汽出口,所述容器外壳上端部设置有水或蒸汽进口,所述水或蒸汽进口与进口部连通,所述进口部内设置有进汽管及出汽管,所述出汽管与出口部连通设置;所述容器外壳下端部设置有气体入口,所述容器外壳上端部于出口部下方设置有气体出口机构,所述气体出口机构设置有多个气体出口导管,所述气体出口导管一端与容器外壳内连通,所述气体出口导管另一端连通有汇集管。
在其中一个实施例中,所述冷却机构包括第一烟气冷却器、第二烟气冷却器、第三烟气冷却器、第四烟气冷却器,所述第一烟气冷却器的气体入口通过管道与旋风除尘器连接,所述第一烟气冷却器的水或蒸汽进口与蒸汽轮机的中压级出口连接,所述第一烟气冷却器的水或蒸汽出口与蒸汽轮机的次中压级连接;所述第二烟气冷却器的水或蒸汽进口与蒸汽轮机的高压级出口连接,所述第二烟气冷却器的水或蒸汽出口与蒸汽轮机的中压级连接;所述第三烟气冷却器的水或蒸汽出口与蒸汽轮机的高压级连接,所述第三烟气冷却器的水或蒸汽进口连接有气液分离器;所述第四烟气冷却器的水或蒸汽出口与第三烟气冷却器的水或蒸汽进口连接,所述第四烟气冷却器的水或蒸汽进口与气液分离器连接。
在其中一个实施例中,所述冷却机构还包括第五烟气冷却器及第六烟气冷却器,所述锅炉给水机构提供锅炉给水,经预热的锅炉给水通过水或蒸汽进口进入到第五烟气冷却器中,锅炉给水被第五烟气冷却器内的烟气加热蒸发成饱和水蒸汽,所述第五烟气冷却器的水或蒸汽出口通过管道与气液分离器连接,饱和水蒸汽从第五烟气冷却器的水或蒸汽出口进入到气液分离器内,再通过气液分离器将饱和水蒸汽提供给第三烟气冷却器及第四烟气冷却器;所述第六烟气冷却器的气体出口机构通过管道与除尘机构连接,所述除尘机构用于对从冷却机构出来的烟气进行除尘及降温处理。
在其中一个实施例中,所述除尘机构为洗涤器构造,所述洗涤器包括提升管及下降管,所述提升管与下降管通过管道连接在一起,所述出烟口设置在下降管的顶部,所述出烟口用于排出气体,所述下降管内还设置有第一换热器,所述锅炉给水机构用于提供第一换热器一部分锅炉给水,经由洗涤器的出烟口排出的含有饱和水蒸汽烟气进入到冷凝机构内,在冷凝机构内烟气与锅炉给水进行换热。
在其中一个实施例中,还包括循环压缩机,所述循环压缩机的进气端通过管道与除尘机构连接,所述循环压缩机的出气端通过管道与燃烧侧连接,所述循环压缩机用于提供循环气给燃烧侧。
在其中一个实施例中,所述燃烧机构还设置有供料侧,所述供料侧用于提供燃料物质;所述供料侧设置有备料单元、干式加煤单元及湿式加煤单元,所述备料单元用于将原料煤进行破碎、磨碎加工处理并将破碎、磨碎后的原料煤通过颗粒度大小分为粗颗粒煤和细粉煤,所述干式加煤单元用于将粗颗粒煤加压后送至燃烧侧,所述湿式加煤单元用于将细粉煤与水配置成水煤浆后送至燃烧侧;其中,所述供料侧提供的燃料物质中的石灰石可先磨细成石灰石粉后与水一起混合制成石灰石浆料,再将石灰石浆料通过加压泵或气压方式升压送至燃烧侧。
在其中一个实施例中,还包括循环水泵,所述循环水泵一端与冷凝机构连接,所述循环水泵另一端与燃烧侧连接;所述冷凝机构由多个冷凝器组成,所述循环水泵一端与冷凝器通过管道连接,从冷凝器排出的冷凝液经由循环水泵加压后可提供循环水给燃烧侧。
在其中一个实施例中,所述冷凝器包括冷凝壳体,所述冷凝壳体内设置有第二换热器,所述第二换热器立式设置在冷凝壳体内,所述冷凝壳体侧壁分别设置有进水口及出水口,所述冷凝壳体上端部设置有进气口,所述冷凝壳体下端部设置有出气口;烟气经由冷凝器的进气口进入到冷凝器内,并与冷凝器内流经的锅炉给水进行换热,烟气被冷凝器进行降温处理后形成冷凝液及气体,所述冷凝壳体下端部设置有冷凝液分离空间,所述出气口与冷凝液分离空间连通设置;所述冷凝机构通过管道连接有双氧水溶液泵,所述双氧水溶液泵将外部双氧水溶液泵入到冷凝器内,所述双氧水溶液泵与冷凝器的进气口连接,在冷凝器内双氧水溶液将烟气中残留的二氧化硫氧化为三氧化硫后并溶解于冷凝液中。
在其中一个实施例中,所述导料管为弧形构造。
一种烟气冷却器,其包括容器外壳,所述容器外壳内设置有换热管,所述换热管设置有出口部及进口部,所述出口部一侧开设有水或蒸汽出口,所述容器外壳上端部设置有水或蒸汽进口,所述水或蒸汽进口与进口部连通,所述进口部内设置有进汽管及出汽管,所述出汽管与出口部连通设置;所述容器外壳下端部设置有气体入口,所述容器外壳上端部于出口部下方设置有气体出口机构,所述气体出口机构设置有多个气体出口导管,所述气体出口导管一端与容器外壳内连通,所述气体出口导管另一端连通有汇集管。
综上所述,本实用新型高效燃烧冷却系统及烟气冷却器采用高速循环流化床技术进行高压纯氧燃烧,烟气热量用于生产高品质水蒸汽推动蒸汽轮机发电,燃烧过程控制和降低二氧化硫和氮化物的生成量,在烟气显热和水蒸汽潜热得到充分回收后得到高浓度的二氧化碳,对二氧化碳进行干燥和简易处理后进一步加压即可送至co2输送管,用于油田增油回收、碳回用或进行地下埋存。
附图说明
图1为本实用新型高效燃烧冷却系统的结构原理图;
图2为本实用新型冷凝器的结构原理图;
图3为本实用新型烟气冷却器的结构原理图;
图4为本实用新型烟气冷却器中换热管的结构原理图;
图5为本实用新型气体出口机构与汇集管的结构组合图;
图6为本实用新型供料侧中备料单元、干式加煤单元及湿式加煤单元的结构组合原理图;
图7为本实用新型料柱侧与短管的结构组合图;
图8为本实用新型高效燃烧冷却系统另一实施例的结构原理图。
具体实施方式
下面将结合附图对本实用新型的技术方案进行清楚、完整地描述,显然,所描述的实施例是本实用新型一部分实施例,而不是全部的实施例。基于本实用新型中的实施例,本领域普通技术人员在没有做出创造性劳动前提下所获得的所有其他实施例,都属于本实用新型保护的范围。
在本实用新型的描述中,需要说明的是,术语“上”、“下”、“内”、“外”等指示的方位或位置关系为基于附图所示的方位或位置关系,仅是为了便于描述本实用新型和简化描述,而不是指示或暗示所指的装置或元件必须具有特定的方位、以特定的方位构造和操作,因此不能理解为对本实用新型的限制。此外,术语“第一”、“第二”、“第三”仅用于描述目的,而不能理解为指示或暗示相对重要性。
在本实用新型的描述中,需要说明的是,除非另有明确的规定和限定,术语“安装”、“相连”、“连接”应做广义理解,例如,可以是固定连接,也可以是可拆卸连接,或一体地连接;可以是机械连接,也可以是电连接;可以是直接相连,也可以通过中间媒介间接相连,可以是两个元件内部的连通。对于本领域的普通技术人员而言,可以具体情况理解上述术语在本实用新型中的具体含义。
如图1至图7所示,本实用新型高效燃烧冷却系统包括燃烧机构100、旋风除尘器200、冷却机构300、蒸汽轮机400、锅炉给水机构500、除尘机构600、循环压缩机700、冷凝机构800及循环水泵900,所述燃烧机构100为高速循环流化床燃烧器构造,所述燃烧机构100包括燃烧侧110及料柱侧120,所述燃烧侧110上端部与料柱侧120上端部通过第一连接管130连通,使得固体颗粒在燃烧侧110与料柱侧120之间连续高速循环,所述第一连接管130为弧形构造,有利于降低流体流动阻力,所述第一连接管130一端与燃烧侧110上端部连接,所述料柱侧120底端部连接有导料管121,所述导料管121一端与燃烧侧110连通,所述导料管121为弧形构造,以将料柱侧120内的流体引导入燃烧侧110内后重新利用,将导料管121设置为弧形构造有利于分散大尺寸结构特别是含有长尺寸的燃烧侧110和料柱侧120组成的回路在各种工作条件下形成的结构应力,从而较易于进行设备设计、制作和操作的优化。
所述燃烧机构100还设置有供料侧140,所述供料侧140用于提供燃料物质,具体地,所述燃料物质包括燃料煤炭或生物质、纯氧、石灰石、循环水、循环气等,所述供料侧140设置有多个管道,每个管道对应提供不同的燃料物质,所述管道分别设置在燃烧侧110不同的高度上,具体地,纯氧可通过燃烧侧110中部或底端部进入,以提供煤粉及其他固体向上流动的动力,石灰石用于吸收煤炭燃烧过程产生的硫化物,由于高浓度氧的存在和高压条件下,首先易于so3的生成,而so3更易于与石灰石反应从而实现高脱硫效果;将煤炭与氧气采用交叉方式从多个高度位置进入燃烧侧110将使可能生成的氮化物浓度降低;对于高含硫煤炭,可根据需要在燃烧侧110内顶部加入一定量的低硫燃料,用于消耗剩余的氧气,在供料侧140的煤炭中按一定比例加入大颗粒燃料物质,也可使燃烧机构100出来的烟气中氧气含量降至最低。
在其中一个实施例中,所述供料侧140提供的燃料物质中的燃料煤炭需要预先制备,具体地,所述供料侧140设置有备料单元141、干式加煤单元142及湿式加煤单元143,所述备料单元141用于将原料煤进行加工处理,包括破碎、磨碎等操作,如果原料煤中水份含量高时,所述备料单元141需要对进厂原料煤进行干燥处理;另外,为尽量减少备料单元141在干燥过程中能耗,所述备料单元141将破碎和磨细的原料煤进行颗粒度分级,分为粗颗粒煤和细粉煤两部分,当颗粒度分级点为75微米时,大于75微米的颗粒为粗颗粒,小于75微米的颗粒为细粉煤,颗粒度分级点可在一个范围内变化,如45至100微米;粗颗粒煤不需继续磨细,将其送干式加煤单元142加压后再送至燃烧侧,一般细粉煤用于干式加压时,操作会困难,不可靠,需要进行深度干燥,所述湿式加煤单元143用于将细粉煤与水按比例配置成水煤浆,通过水煤浆泵将细粉煤加压后送至燃烧侧,通过干式加煤单元142和湿式加煤单元143的结合,既避免了细粉煤加压操作的难度,也不需要将煤深度干燥,节省能源。
其中,干式加煤单元142的加煤方式采用包含煤锁加压和给煤控制装置的系统,给煤控制可采用机械式控制如螺旋给料器或气流控制等方法,将高压下计量后的煤料通过输送管线送入燃烧侧110;湿式加煤单元143的加煤方式则是将细粉煤与一定比例的水混合制备水煤浆,然后通过泵将水煤浆加压并送反应器,也可以将水煤浆通过气压的方式控制流量加入燃烧侧110。干式加煤需要干燥,且煤粉操作不稳定,而湿式加煤需要煤磨细的能耗高,各有特点,将两者结合利用各自优点,可使操作可靠性高,能耗降低。
在其中一个实施例中,所述供料侧提供的燃料物质中的石灰石可先磨细成石灰石粉后与水一起混合制成石灰石浆料,再将石灰石浆料通过加压泵或气压方式升压送至燃烧侧110,进而与燃烧侧110内的其他燃料物质进行反应;其中,石灰石粉粒度一般小于100微米。
所述料柱侧120内侧上端部设置有一截面为“l”型的短管150,所述短管150下端部开口朝下设置,所述短管150上端部呈水平方向延伸出料柱侧120设置,所述短管150上端部设置有烟气出口151,所述烟气出口151用于供料柱侧120内的烟气流出;所述短管150与料柱侧120之间形成有环隙160,来自燃烧侧110和第一连接管130的流体在料柱侧120内经过环隙160向下流动,由于流体流通面积变小,流体向下流动速度加快,流体中的固体颗粒得到比气体更大的运动惯性,固体颗粒继续向下流动,而气体则在料柱侧内减速、再回头向上流向短管150下端部开口处,最后经过短管150上端部从烟气出口151流出燃烧机构100;由于环隙160的尺寸较小,使得分离出气体再次夹带固体颗粒的机会变小,有利于提高固体颗粒分离效率,短管150上端部设置有保护层170,以防止短管150被料柱侧120内的流动流体所磨损。
所述旋风除尘器200与短管150连接,所述旋风除尘器200下方通过第二连接管220与料柱侧120连接,所述旋风除尘器200通过管道与冷却机构300连接;在料柱侧120顶部与部分固体分离后的烟气通过短管150的烟气出口151离开燃烧机构100进入到旋风除尘器200内,通过旋风除尘器200将烟气中夹带的大部分剩余固体再次分离出来,分离出来的大部分剩余固体的一部分经由第二连接管220进入到料柱侧120,用以保证料柱侧120内料位的稳定性,同时也可在燃烧机构100内协助其他燃料物质进行高速循环燃烧,分离出来的固体的另一部分则通过旋风除尘器200排出至高效燃烧冷却系统外,经旋风除尘器200处理后的烟气则通过管道进入到冷却机构300内。
所述冷却机构300设置有多个烟气冷却器10,所述烟气冷却器10用于对从旋风除尘器200出来的烟气进行降温处理,所述烟气冷却器10为刀鞘式构造,所述烟气冷却器10包括容器外壳11,所述容器外壳11内设置有保温层12,以避免容器外壳11内的热量流散到外部影响热量的回收工作;所述容器外壳11内设置有换热管30,所述换热管30截面为t形构造,所述换热管30设置有出口部31及进口部32,所述出口部31一侧开设有水或蒸汽出口33,所述容器外壳11上端部设置有水或蒸汽进口13,所述水或蒸汽进口13与进口部32连通,所述进口部32内设置有进汽管34及出汽管35,所述出汽管35与出口部31连通设置,从而使得外部水或蒸汽进入到进口部32内后,经由进汽管34、出汽管35及水或蒸汽出口33排出。
所述容器外壳11下端部设置有气体入口14,所述容器外壳11上端部于出口部31下方设置有气体出口机构40,所述气体出口机构40设置有多个气体出口导管41,所述气体出口导管41一端与容器外壳11内连通,所述气体出口导管41另一端连通有汇集管50,所述汇集管50为环形构造,以将气体出口导管41内的气体进行汇流再排出;所述气体出口机构40为双层构造,上下两层汇集管50可整合为一整体构造,通过设置多个气体出口导管41,使得烟气进入到气体出口导管41内的速度大大降低,有效减缓烟气对单一气体出口导管41的冲刷和磨蚀。
在其中一个实施例中,所述换热管30外侧部设置有传热鳍片36,以提高换热管30内部水或蒸汽与换热管30外部烟气的换热效率。
所述烟气冷却器10依次连接,即前一烟气冷却器10的汇集管50通过管道与下一烟气冷却器10的气体入口14连接,烟气冷却器10的水或蒸汽进口13则用于供外部蒸汽进入,通过换热管30的作用,将烟气冷却器10内烟气的热量与外部蒸汽进行换热,进而使得烟气冷却器10内的烟气得到降温处理,同时提高外部蒸汽品质。
具体地,所述烟气冷却器10的水或蒸汽进口13及水或蒸汽出口33分别与蒸汽轮机400连接,使得从蒸汽轮机400出来的蒸汽进入到烟气冷却器10内进行换热处理后变成高品质蒸汽重新进入到蒸汽轮机400内,进而推动蒸汽轮机400发电。
所述冷却机构300包括第一烟气冷却器310、第二烟气冷却器320、第三烟气冷却器330、第四烟气冷却器340、第五烟气冷却器350及第六烟气冷却器360,所述第一烟气冷却器310的气体入口14通过管道与旋风除尘器200连接,所述第一烟气冷却器310的水或蒸汽进口13与蒸汽轮机400的中压级出口连接,所述第一烟气冷却器310的水或蒸汽出口33与蒸汽轮机400的次中压级连接,从旋风除尘器200送出的烟气与蒸汽轮机400的中压级出口得到的次中压主蒸汽进行换热,使次中压主蒸汽被加热,被加热的次中压主蒸汽返回蒸汽轮机400的次中压级,同时烟气被第一烟气冷却器310进行降温处理,烟气热量用于生产高品质水蒸汽推动蒸汽轮机400发电。
同理,所述第二烟气冷却器320的水或蒸汽进口13与蒸汽轮机400的高压级出口连接,所述第二烟气冷却器320的水或蒸汽出口33与蒸汽轮机400的中压级连接,经第一烟气冷却器310降温后的烟气进入到第二烟气冷却器320中,在第二烟气冷却器320中,烟气与蒸汽轮机400的高压级出口得到的中压主蒸汽进行换热,使中压主蒸汽被加热,被加热的中压主蒸汽返回蒸汽轮机400的中压级,同时烟气被第二烟气冷却器320进行降温处理,烟气热量用于生产高品质水蒸汽推动蒸汽轮机400发电。
所述第三烟气冷却器330的水或蒸汽出口33与蒸汽轮机400的高压级连接,经第二烟气冷却器320降温后的烟气进入到第三烟气冷却器330中,在第三烟气冷却器330中,烟气与外部饱和水蒸汽进行换热,使得饱和水蒸汽被进一步加热得到最终的过热水蒸汽,过热水蒸汽送蒸汽轮机400的高压级,同时烟气被第三烟气冷却器330进行降温处理,烟气热量用于生产高品质水蒸汽推动蒸汽轮机400发电;其中,外部饱和水蒸汽由气液分离器1提供,所述第三烟气冷却器330的水或蒸汽进口13与气液分离器1连接。
所述第四烟气冷却器340的水或蒸汽出口33与第三烟气冷却器330的水或蒸汽进口13连接,经第三烟气冷却器330降温后的烟气进入到第四烟气冷却器340中,在第四烟气冷却器340中,烟气与外部饱和水蒸汽进行换热,使得饱和水蒸汽被初步过热,初步过热的饱和水蒸汽从第四烟气冷却器340进入第三烟气冷却器330,同时烟气被第四烟气冷却器340进行降温处理,烟气热量用于生产高品质水蒸汽推动蒸汽轮机400发电;其中,外部饱和水蒸汽由气液分离器1提供,所述第四烟气冷却器340的水或蒸汽进口13与气液分离器1连接。
经第四烟气冷却器340降温后的烟气进入到第五烟气冷却器350中,在第五烟气冷却器350中,锅炉给水机构500提供锅炉给水,经预热的锅炉给水通过水或蒸汽进口13进入到第五烟气冷却器350中,锅炉给水被第五烟气冷却器350内的烟气加热蒸发成饱和水蒸汽,同时烟气被第五烟气冷却器350进行降温处理;第五烟气冷却器350的水或蒸汽出口33通过管道与气液分离器1连接,饱和水蒸汽从第五烟气冷却器350的水或蒸汽出口33进入到气液分离器1内,再通过气液分离器1将饱和水蒸汽提供给第三烟气冷却器330及第四烟气冷却器340。
同理,经第五烟气冷却器350降温后的烟气进入到第六烟气冷却器360中,在第六烟气冷却器360中,所述锅炉给水机构500提供锅炉给水,经预热的锅炉给水通过水或蒸汽进口13进入到第五烟气冷却器350中,锅炉给水被第五烟气冷却器350内的烟气加热蒸发成饱和水蒸汽,所述第五烟气冷却器350的水或蒸汽出口33通过管道与气液分离器1连接,饱和水蒸汽从第五烟气冷却器350的水或蒸汽出口33进入到气液分离器1内,再通过气液分离器1将饱和水蒸汽提供给第三烟气冷却器330及第四烟气冷却器340。
所述除尘机构600通过管道与冷却机构300连接,所述第六烟气冷却器360的气体出口机构40通过管道与除尘机构600连接,所述除尘机构600用于对从冷却机构300出来的烟气进行除尘及降温处理;所述除尘机构600设置有出烟口610,所述除尘机构600的出烟口610通过管道与冷凝机构800连接。
所述循环压缩机700的进气端通过管道与除尘机构600连接,所述循环压缩机700的出气端通过管道与燃烧侧110连接,所述循环压缩机700用于提供循环气给燃烧侧110,以对燃烧侧110的燃烧温度进行调节,循环气的用量与加煤量成正比;所述循环压缩机700提供循环气的管道可设置在燃烧侧110不同的高度,以满足燃烧侧110对循环气不同的需求,提高循环气的利用率;具体地,所述循环压缩机700提供循环气的管道分别连接至导料管的最低点及燃烧侧110的底端部。
在其中一个实施例中,所述除尘机构600为洗涤器60构造,所述洗涤器60包括提升管61及下降管62,所述提升管61与下降管62通过管道连接在一起,所述第六烟气冷却器360中的烟气通过管道进入到提升管61内,所述出烟口610设置在下降管62的顶部,所述出烟口610用于排出气体,所述下降管62内还设置有第一换热器70,所述锅炉给水机构500用于提供第一换热器70一部分锅炉给水,在提升管61内从第六烟气冷却器360出来的烟气与洗涤器60中的循环洗涤水高速接触,使得烟气得到一定的降温处理,此时,烟气中的粉尘被洗涤器60中的水洗涤,烟气在出烟口610处与洗涤器60中的循环洗涤水分离后进入到冷凝机构800内;洗涤器60中的循环洗涤水与烟气进行接触后水温升高,在循环洗涤水与烟气分离后,下降管62中布置的第一换热器70将洗涤器60中的循环洗涤水进行换热降温处理,经冷却的洗涤水从下降管62中进入到提升管61底部继续与来自第六烟气冷却机构300内的烟气进行接触;其中,调节锅炉给水的流量可控制洗涤器60出烟口610排出的烟气温度;另外,烟气在洗涤器60中进行洗涤冷却过程时会使烟气中一部分所含水份冷凝出来形成冷凝水,这部分冷凝水含尘、含有溶解的残留硫氧化物、氮氧化物及二氧化碳等,将它们减压排出洗涤器60后作去水处理,处理后的水送至水冷却塔做补水之用。
所述锅炉给水机构500提供锅炉给水给冷凝机构800,经由洗涤器60的出烟口610排出的含有饱和水蒸汽的烟气进入到冷凝机构800内,在冷凝机构800内烟气与锅炉给水进行换热,伴随着换热过程,烟气中水蒸汽得到冷凝,锅炉给水则会进行加热处理,在冷凝机构800内烟气流动方向与锅炉给水流动方向相反,如此可充分利用水蒸汽的冷凝热,大大提高锅炉给水的加热效果。
所述冷凝机构800由多个冷凝器80组成,具体地,所述冷凝器80的数量为3个,所述冷凝器80包括冷凝壳体81,所述冷凝壳体81内设置有第二换热器90,所述第二换热器90立式设置在冷凝壳体81内,所述冷凝壳体81侧壁分别设置有进水口82及出水口83,所述冷凝壳体81上端部设置有进气口84,所述冷凝壳体81下端部设置有出气口85,所述冷凝器80依次连接,即前一冷凝器80的出水口83通过管道与下一冷凝器80的进水口82连接,前一冷凝器80的出气口85通过管道与下一冷凝器80的进气口84连接;所述冷凝壳体81下端部设置有冷凝液分离空间86,所述出气口85与冷凝液分离空间86连通设置,烟气经由冷凝器80的进气口84进入到冷凝器80内,并与冷凝器80内流经的锅炉给水进行换热,烟气被冷凝器80进行降温处理后形成冷凝液及气体,所述冷凝液分离空间86用于促进冷凝液与气体的分离,冷凝液从冷凝器80底部排出,气体则从冷凝器80侧面的出气口85排出后进入下一冷凝器80内,如此无需单独设立气液分离器,简化工艺,减少设备。
所述冷凝机构800通过管道连接有双氧水溶液泵2,所述双氧水溶液泵2将外部双氧水溶液泵入到冷凝器80内,具体地,所述双氧水溶液泵2与冷凝器80的进气口连接,在冷凝器80内双氧水溶液将烟气中残留的二氧化硫氧化为三氧化硫后并溶解于冷凝液中,双氧水溶液的加入量由烟气中的残留二氧化硫量或从冷凝机构800排出的下游允许二氧化硫量决定。
所述冷凝机构800包括第一冷凝器810、第二冷凝器820及第三冷凝器830,所述第一冷凝器810的进气口通过管道与除尘机构600连接,所述第一冷凝器810的出水口与第五烟气冷却器350的水或蒸汽进口13进入连接,所述第一冷凝器810的进水口与第二冷凝器820的出水口连接,所述第一冷凝器810的出气口通过管道与第二冷凝器820的进气口连接,所述第二冷凝器820的进气口通过管道还连接有双氧水溶液泵2,所述双氧水溶液泵2将外部双氧水溶液泵2入到第二冷凝器820内,并在第二冷凝器820内将烟气中残留的二氧化硫氧化为三氧化硫后并溶解于冷凝液中,冷凝液从第二冷凝器820底部排出。
所述循环水泵900一端与冷凝机构800连接,所述循环水泵900另一端与燃烧侧110连接,具体地,所述循环水泵900一端与冷凝器80的出水口83通过管道连接,从冷凝器80排出的部分冷凝液经由循环水泵900加压后可提供循环水给燃烧侧110,用以对燃烧侧110的燃烧温度进行控制;循环水泵900将循环水送至燃烧侧110后将增加离开燃烧机构100的烟气水份含量,从而使得烟气的单位热含量增高,加水量越多,可有利于减少循环气的用量,同时水蒸汽的分压提高,水蒸汽冷凝温度上升,有利于冷凝热被回收利用。循环水量的控制要保证烟气冷凝器80中水份冷凝热回收的最大化,同时烟气中水分加入使二氧化碳分压降低,有利于硫组分与石灰石反应,提高脱硫效率。
在其中一个实施例中,所述循环水泵900一端与洗涤器60连接,烟气在洗涤器60中进行洗涤冷却过程时会使烟气中一部分所含水份冷凝出来形成冷凝水,这部分冷凝水含尘、含有溶解的残留硫氧化物、氮氧化物及二氧化碳等,将它们减压排出洗涤器60后作去水处理,根据水中组分如氯化物含量等情况,也可以将洗涤器60排出的部分水经由循环水泵900给燃烧侧110提供循环水,循环水中含有的硫组分可被燃烧侧110内的石灰石再一次吸收。
如图8所示,在其中一个实施例中,所述循环压缩机700的进气端也可通过管道与冷却机构300连接,所述循环压缩机700的出气端通过管道与燃烧侧110连接,所述循环压缩机700用于提供循环气给燃烧侧110,具体地,所述循环压缩机700的进气端通过管道与第六烟气冷却器360的气体出口机构40连接,所述除尘机构600为干式中温除尘器,此时,循环压缩机700的进气端由于与第六烟气冷却器360连接,循环压缩机700需要选择适应含尘气体的压缩机型号,将循环压缩机700与冷却机构300连接的方式有别于将循环压缩机700的进气端与除尘机构600连接,当循环压缩机700的循环气取自于干式中温除尘器时,所需的循环气通过干式中温除尘器的流量会大大增加,使得干式中温除尘器设备变得较大;所述导料管121可为斜向下方向设置,以将料柱侧120内的流体引导入燃烧侧110内后重新利用。
在其中一个实施例中,所述第一连接管130另一端延伸至料柱侧120内一段距离,以引导流体在料柱侧120内部持续向下流动而增加固体分离效果。
在其中一个实施例中,所述冷凝机构800通过管道连接有干燥器3,所述干燥器3通过管道连接有汞吸收器4,所述汞吸收器4则通过管道连接至co2输送管93,co2输送管5用于对co2进行输送,用于油田增油回收、碳回用或进行地下埋存。
从冷凝机构800排出的烟气已经被降温至较低温度,且含水份很低,再送至干燥器3利用干燥剂将烟气中残留的水分除掉;再送至汞吸收器4利用汞吸附剂将烟气中的大部分汞吸收掉,如此得到含二氧化碳浓度很高的气体,经由汞吸收器4排出的气体中残留的水份、氧气、硫化物、氮化物等含量均很低,其中经由汞吸收器4排出的气体组分取决于空分所得纯氧的浓度、氮气与氩气的含量,二氧化碳气体中含有部分氮气和氩气等不可凝气体,根据co2输送管5的指标要求,对空分、脱硫控制、干燥等工序进行相应的设计和操作。
本实用新型具体工作时,生物质可按与煤炭一定比例加入到燃烧侧110,为了降低燃烧机构100的烟气出口151的氧气浓度,可加入低含硫的燃料物质,包括低硫煤、经热解的煤焦、高温焦炭、天然气等,这些燃料物质加入到燃烧侧110的最上部,以便将烟气中残留的最后氧气消耗掉。
其中,燃烧侧110的操作条件包括10至70大气压的压力,800至1000℃的燃烧温度,煤炭加料颗粒大部分在0~2毫米,少部分可在0~5毫米;入炉煤水分基本没有限制,只要水分能满足加煤系统的要求即可,如此尽可能减少对煤炭干燥的需要;空分制氧所得氧气浓度的要求与最终co2输送管的要求相匹配,在co2中允许的可凝气体范围内,尽量降低对o2纯度的要求,有利于使空分电耗降至最低。
对于一个500mw的蒸汽轮机发电系统,以加压循环流化床燃烧纯氧燃烧机构100,并采用模块化的烟气冷却器10组合为基础,以某次烟煤为例,加煤量约为200吨/小时,氧气流量约为340吨/小时,循环气流量约为1650吨/小时,循环水流量约为100吨/小时,燃烧机构100在70大气压的压力下操作,燃烧机构100的烟气出口151温度为950℃左右,超过95%的燃烧生成水份的潜热得到回收利用,99%以上的二氧化碳被回收,所得co2的浓度在96~99%,主要取决于空分氧气的纯度,蒸汽轮机400可采用亚临界或超临界蒸汽条件。
本实用新型还提供一种烟气冷却器,包括上述一种高效燃烧冷却系统的容器外壳11、换热管30及气体出口机构40。
上述一种烟气冷却器的其他技术特征与上述一种高效燃烧冷却系统相同,此处不予赘述。
综上所述,本实用新型高效燃烧冷却系统及烟气冷却器采用高速循环流化床技术进行高压纯氧燃烧,烟气热量用于生产高品质水蒸汽推动蒸汽轮机400发电,燃烧过程控制和降低二氧化硫和氮化物的生成量,在烟气显热和水蒸汽潜热得到充分回收后得到高浓度的二氧化碳,对二氧化碳进行干燥和简易处理后进一步加压即可送至co2输送管5,用于油田增油回收、碳回用或进行地下埋存。
以上所述实施例仅表达了本实用新型的几种实施方式,其描述较为具体和详细,但并不能因此而理解为对本实用新型范围的限制。应当指出的是,对于本领域的普通技术人员来说,在不脱离本实用新型构思的前提下,还可以做出若干变形和改进,这些都属于本实用新型的保护范围。因此,本实用新型的保护范围应以所附权利要求为准。
起点商标作为专业知识产权交易平台,可以帮助大家解决很多问题,如果大家想要了解更多知产交易信息请点击 【在线咨询】或添加微信 【19522093243】与客服一对一沟通,为大家解决相关问题。
此文章来源于网络,如有侵权,请联系删除


