一种熔体流化冷激器及其应用系统和系统应用方法与流程



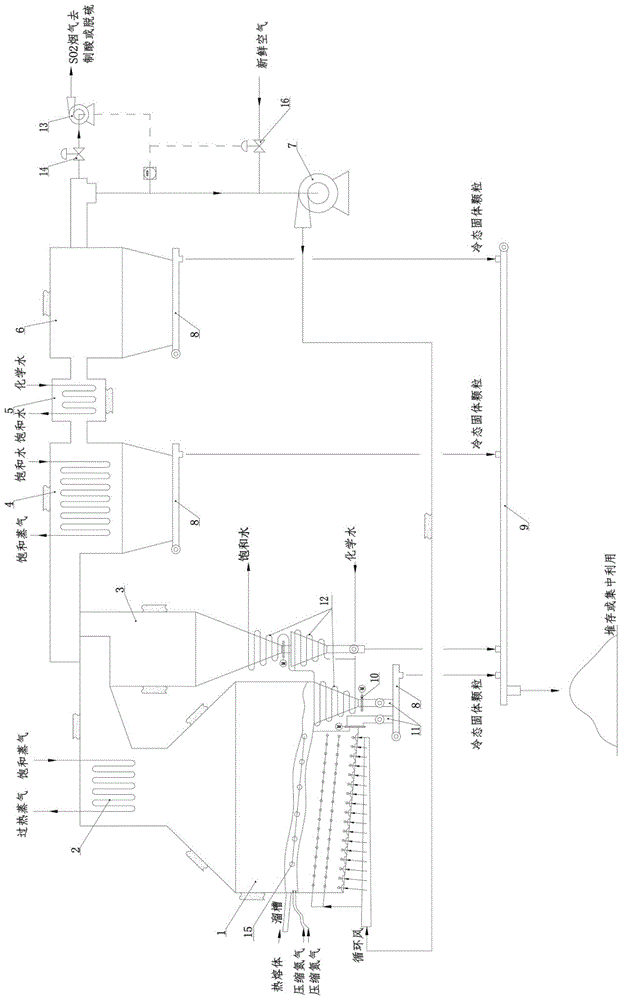
本发明属于火法冶金能源利用领域,具体为一种熔体流化冷激器及其应用系统和系统应用方法。
背景技术:
目前铜冶炼厂对于冰铜和吹炼渣的粒化都是水淬+风淬的形式。具体是以氮气和高压水对熔池溜槽流出的高温热熔体(温度达1200-1500℃)共同冲击,达到粒化降温的目的。氮气的主要作用是打散熔体,高压水主要起蒸发降温兼打散熔体的作用。熔体粒化降温至60℃左右(含水8-10%)被收集,送堆存或下道工序利用。这样带来了以下两个问题:
1、因为高温熔体的显热全部转化为60℃水蒸气的潜热,这种低品位潜热难以利用,随着烟气(含水率60%)被带走。
2、要获得好的降温效果一般需加入过量水,过量水会夹带粒化固体流走,造成地面环境较差,生产期间难以进人,而且大量泥浆淤积在设备底部地坑和地沟中,大型机械难以进入该区域,人工清理困难、工作量大。
技术实现要素:
本发明的目的在于提供一种能快速高效带走热溶体中热量的流化冷激器及具有该流化冷激器的高效能源回收系统和该系统的应用方法。
本发明提供的这种熔体流化冷激器,其箱体的前端板中部连接有溜槽和氮气喷嘴;箱体底部分为独立的托流区和集料区,托流区的底面和两侧分别设置有循环风喷嘴,两侧的循环风喷嘴倾斜朝上对称设置,底面的循环风喷嘴朝上设置,托流区的底面为下倾斜面,其后端最低位置处有出料口;集料区的后端底面连接有集料锥斗;箱体的顶部有上升烟道;热熔体从溜槽进入箱体中时,氮气喷嘴往熔体流中喷入氮气,托流区的循环风喷嘴同时往箱体中喷入循环风。
上述技术方案的一种实施方式中,所述箱体侧壁对应熔体流高度区域设置水冷壁;箱体底部托流区的横截面形状为锥形,托流区两侧的循环风喷嘴呈上下多排布置,每排的排布与底面平行。
上述技术方案的一种实施方式中,所述箱体在托流区侧壁及其上方熔体颗粒悬浮层对应的侧壁设置声波清灰装置或爆破清灰装置。
上述技术方案的一种实施方式中,所述上升烟道中设置有蒸汽过热器。
上述技术方案的一种实施方式中,所述集料锥斗设置有水冷盘管。
上述技术方案的一种实施方式中,所述托流区的出料口和集料锥斗的出口分别连接电动阀,两电动阀的出口分别连接星形卸灰阀,两星形卸灰阀的出口连接至同一台刮板机。
本发明提供的这种熔体能源干法回收系统,其包括上述熔体流化冷激器,还包括旋风分离器、余热锅炉、省煤器、收尘器、循环风机和刮板机;熔体流化冷激器、旋风分离器、余热锅炉、省煤器、收尘器和循环风机之间依次通过循环风管连通,循环风机的出口通过循环风管将循环风送至熔体流化冷激器托流区的循环风喷嘴;旋风分离器底部的出料斗设置有水冷盘管,出料斗出口处连接有电动阀和星型卸灰阀,该水冷盘管与流化冷激器集料锥斗设置的水冷盘管串联,且该水冷盘管的出口与余热锅炉连通;熔体流化冷激器、旋风分离器、余热锅炉和收尘器的出料口均连接至刮板机。
上述系统的一种实施方式中,所述收尘器的烟气出口连接有便于调节烟气中so2浓度的引风机,引风机的入口前连接有抽气阀,所述循环风机的入口前连接有用于补足引风机抽走烟气量的漏风阀。
上述系统的一种实施方式中,所述熔体流化冷激器、旋风分离器、余热锅炉、省煤器、收尘器和循环风机及循环风管外均设置保温层。
本发明提供的这种利用上述系统干法回收熔体能源的工艺:
首先通过压缩氮气将从溜槽流入熔体流化冷激器箱体内的熔体打散成熔体颗粒,根据设定的颗粒力度和分散程度选择压缩氮气的压力,根据熔体颗粒的重力确定托流区循环烟气的托力,使被打散的熔体颗粒被箱体托流区的多层循环流化风托起,形成一个下倾斜的悬浮层与循环流化风进行均匀换热;
循环流化风与悬浮层换热升温至900℃左右的烟气进入熔体流化冷激器箱体顶部的上升烟道,与上升烟道内蒸汽过热器中的饱和蒸汽换热降温至600℃后进入旋风分离器;
从旋风分离器出来的烟气进入余热锅炉与饱和水换热降温至300℃后进入省煤器中与化学水换热降温至150℃进入收尘器,烟气在收尘器中降温至100℃排出;
从收尘器出来的烟气通过循环风机送回至流化冷激器继续升温回用;
当烟气中的so2浓度需要调节时,打开引风机抽走相应的烟气量,同时给循环风机补足抽走烟气量相应的新鲜空气;
流化冷激器上升烟道中蒸汽过热器中的饱和蒸汽被加热成过热蒸汽,流化冷激器集料锥斗和旋风分离器设置的水冷盘管将常温化学水加热成饱和水后进入余热锅炉被加热成饱和蒸汽,省煤器将常温化学水加热成饱和水后进入余热锅炉被加热成饱和蒸汽,过热蒸汽和饱和蒸汽送可去发电机组进行余热发电;
流化冷激器上升烟道出来的烟气中的细尘粉末在旋风分离中旋风的离心力作用下大量落入底部灰斗,灰斗中的固定颗粒被冷却至100℃以下后通过刮板机排出;
收尘器可采用金属、陶瓷或ptfe耐温收尘器,将烟气中的颗粒物除至30mg/nm3以下;
流化冷激器底部收集的冷态固体颗粒最后经刮板机排出堆存或者集中利用。
本发明通过熔体流化冷激器通过干燥的循环风快速吸收高温熔体的热量形成高温流化烟气,然后依次加热蒸汽过热器中的饱和蒸汽至过热蒸汽,经旋风分离器除尘后加热余热锅炉中的饱和水至饱和蒸汽,加热省煤器中的常温化学水至饱和水,并送至余热锅炉中继续加热成饱和蒸汽,通过收尘器除尘后经循环风机送回至熔体冷激器中回用,高温流化烟气在不断加热其它物质的同时自身温度降低至高于其自身露点温度、烟气中的灰尘颗粒被收尘后回到熔体流化冷激器中继续吸收高温熔体中的热量,一直循环。高温熔体的热量回收没有水份进入,为干法回收系统,最大化回收了高温熔体的热量,环境干燥,密封性好,生产条件干净,同时还有副产物过热蒸汽和饱和蒸汽可作为发电能源。
附图说明
图1为本发明一个实施例的系统原理图。
图2为图1中熔体流化冷激器的左视示意图。
具体实施方式
本实施例公开的这种熔体能源干法回收系统,可用于处理铜冶炼冰铜熔体和熔炼渣熔体。
如图1所示,本系统包括熔体流化冷激器1、蒸汽过热器2、旋风分离器3、余热锅炉4、省煤器5、收尘器6、循环风机7、小型刮板机8、大型刮板机9、电动闸板阀10、星形卸灰阀11、水冷盘管12、引风机13、抽气阀14、清灰装置15、漏风阀16。
结合图1、图2可以看出:
熔体流化冷激器1的箱体包括中部的方形段、方形段下端前部的托流区及后部的集料区、方形段上端的上升烟道。
箱体的前端板中部连接有溜槽,前端板对应溜槽连接位置的近下侧连接有压缩氮气喷嘴。
方形段下端的托流区和集料区相互独立,托流区的长度大于集料区的长度,托流区垂直于溜槽方向的截面形状为内收的锥斗形,集料区沿溜槽方向的截面形状为内收的锥斗形,且托流区锥斗有倾斜设置的底板,出料口设置在底板和托流区后端板之间,集料区为集料锥斗,其下端口为出料口。
托流区出料口连接电动闸板阀10,电动闸板阀的出口连接星形卸灰阀11,星形卸灰阀11的出口连接至小型刮板机8,集料锥斗的出口连接电动闸板阀10,电动闸板阀10的出口连接至同一台小型刮板机8。
托流区的底板和两侧壁上分别设置有循环风喷嘴,两侧壁上的循环风嘴对称设置,且两侧臂分别设置有多排,每排循环风喷嘴与底板平行设置,相邻排循环风喷嘴之间的间距及每排相邻循环风喷嘴之间的间距均根据设计要求确定。
熔体流化冷激器1的箱体顶部有上升烟道,且上升烟道中设置有蒸汽过热器2。
当热溶体从溜槽流入熔体流化冷激器1箱体中时,同时使压缩氮气喷嘴往熔体流中喷入压缩氮气,循环风喷嘴往托流区喷入循环风,通过压缩氮气将熔体进行快速打散,压缩氮气的压力根据设定的打散后的颗粒力度和分散程度确定。
熔体在其重力作用下会以朝下微倾斜的方向流动,所以压缩氮气喷嘴的安装角度为与水平方向有向上的夹角,以利于更好更快的熔体流打散成熔体颗粒。分散的熔体颗粒被托流区底面和两侧吹入的多层循环流化风托起,形成一个悬浮层进行均匀换热,所以托流区的循环风流量及压力需控制好,使熔体悬浮层的重力与循环风的托力基本处于平衡状态,使被压缩氮气打散的高温熔体颗粒顺着悬浮层逐步移动至悬浮层颗粒出口,颗粒温度降至250℃。从悬浮层排出的大量颗粒落入集料锥斗,少量颗粒落入托流区的出料口。
由于集料锥斗中颗粒具有较高的温度,为了利用颗粒的能源,在集料锥斗的侧壁设置水冷盘管12。
流化冷激器1两个出料口收集的颗粒达到设定量后打开电动闸板阀10,使颗粒经星形卸灰阀11排出至小型刮板机8。
熔体流化冷激器1托流区的循环流化风与悬浮层换热被加热至900℃左右的流化烟气进入上升烟道,在上升烟道中加热蒸汽过热器2中的饱和蒸汽后降温至600℃排出进入旋风分离器3中,蒸汽过热器2中的饱和蒸汽被加热成过热蒸汽。
在旋风分离器3中,烟气中的细尘粉末在旋风离心力作用下大量落入底部锥斗中形成固体颗粒。在旋风分离器底部灰斗壁设置水冷盘管12加热常温化学水,且该水冷盘管与熔体冷激器集料锥斗侧壁连接的水冷盘管串联,固体颗粒被冷却至100℃以下后排出,水冷盘管中的常温化学水被加热至饱和水温度后进入余热锅炉4被烟气继续加热。旋风分离器3底部灰斗收集的颗粒被降温至低于100℃后排出至其底部连接的小型刮板机8。
旋风分离器3出来的600℃烟气进入余热锅炉4中换热降温至300℃,余热锅炉中的饱和水被加热成饱和蒸气,烟气中的烟尘被余热锅炉底部的灰斗收集后通过其底部连接的小型刮板机8排出。
余热锅炉4出来的300℃烟气进入省煤器5中加热化学水至饱和水,饱和水再进余热锅炉4中继续加热成饱和蒸汽,烟气降温至150℃后排出进入收尘器6。收尘器采用除尘和耐腐蚀性能优秀的金属、陶瓷或ptfe等耐温收尘器,可将烟气中颗粒物除至30mg/nm3以下。
余热锅炉4和收尘器6灰斗收集的烟尘颗粒分别排出至其底部连接的小型刮板机冷却后排出。
过热蒸气和饱和蒸气送去发电机组进行余热发电,以达到充分利用回收能源的目的。
各小型刮板机8将收集的烟尘颗粒排出至一台大型刮板机9,大型刮板机9将烟尘颗粒排出堆存或者直接利用,注意确保大型刮板机排出的颗粒温度低于100℃。
从收尘器6出来的大部分烟气通过循环风机7返回至熔体流化冷激器1中升温回用。烟气在循环过程中绝大部分的o2被逐步消耗,最终循环风成分是含n2、so2和少量o2的混合气体,极端情况为n2占比79%,so2占比21%。
为了确保循环烟气的最低工作温度始终高于烟气露点,系统设有引出风机13将so2烟气抽出系统,以控制循环烟气的so2浓度,抽出系统的烟气量以循环流化风中so2浓度进行控制,同时在循环风机7入口设置漏风阀16连锁,补足系统抽走烟气量相应的新鲜空气。引风机13前设置抽气阀14,在引风机不工作时,抽气阀关闭。
为了充分有效地保存和利用熔体的热能,熔体流化冷激器、旋风分离器、余热锅炉、收尘器、循环风机、循环风管等凡有循环气体过流的设备和工艺管道外部均做保温,且在熔体流化冷激器箱体的中段高热部位设水冷壁。
在熔体流化冷激器的箱体对应悬浮层高度的中段侧壁及中段下方的锥斗斜壁等易积灰部位设置声波清灰或爆破清灰装置15,自动按时清灰,保证物料与设备的接触面少积灰、不结块。
下面分别针对利用本系统处理铜冶炼冰铜熔体和处理熔炼渣熔体的相应参数确定及副产物蒸汽的产量。
1、处理铜冶炼冰铜熔体
冰铜处理量:81.2t/h
冰铜组成及比热:
冰铜计算平均比热:0.6016kj/(kg·k)
循环风比热:1.1kj/(kg·k)
冰铜温降:1250-250=1000(k)
循环风温升/温降:900-150=750(k)
循环风流量:
81.2×1000×0.6016×1000/750/1.1/28.959×22.4=45800.75nm3/h
式中28.959为循环气体平均分子量。
根据计算,粒化冷却81.2t/h冰铜,循环风量为4.58×104nm3/h,考虑到系统保温热损,取40000nm3/h比较适宜。最大热态风量为(900+273)/273×40000=171868m3/h,流化冷激器上部烟道流速应按此风量设计。
循环风机入口风量:(150+273)/273×101325(标准大气压)/(101325-5000)×40000=65195.15m3/h,考虑到流化颗粒的密度较大(4.4~4.7t/m3),取流化密相区的空隙率为0.7,密相区平均密度为0.3×(4.4~4.7)=1.32~1.41t/m3,密相区高度按最大5m计算,颗粒重力为1.41×5×1×9.8×1000=69090pa,考虑系统其它设备阻力5000pa,循环风机的全压应不小于69090+5000=74090pa,可采用两台接力鼓风机来克服此系统阻力。101325为标准大气压值。
锅炉产蒸汽量:
40000/22.4×28.959×1.1×750/2250(104℃锅炉给水的汽化热)/1000=18.96t/h。
2250为104℃锅炉给水的汽化热。
2、处理熔炼渣熔体
熔炼渣产出量:146.92t/h
熔炼渣组成及比热:
熔炼渣计算平均比热:0.852kj/(kg·k)
循环风比热:1.1kj/(kg·k)
熔炼渣温降:1250-250=1000k
循环风温升/温降:900-150=750k
循环风流量:
146.92×1000×0.852×1000/750/1.1/28.959(循环气体平均分子量)×22.4=117362.95nm3/h
考虑10%热损,循环风量按105626.7nm3/h取值。
最大热态风量达(900+273)/273×105626.7=453846.3m3/h,流化冷激器上部烟道流速应按此风量设计。
蒸汽产量:105626.7/22.4×28.959×1.1×750/2250/1000=50.07t/h。
熔炼渣密度约3.7t/m3,流化密相区的空隙率为0.7,密相区平均密度为0.3×3.7=1.11t/m3,密相区高度按最大5m计算,颗粒重力为1.11×5×1×9.8×1000=54390pa,考虑系统其它设备阻力5000pa,风机的全亚应不小于54390+5000=59390pa,可采用鼓风机接力来克服此系统阻力。
3、处理吹炼渣熔体
吹炼渣产出量:13.64t/h
吹炼渣组成及比热:
吹炼渣计算平均比热:0.764kj/(kg·k)
循环风比热:1.1kj/(kg·k)
熔炼渣温降:1250-250=1000k
循环风温升/温降:900-150=750k
循环风流量:
13.64×1000×0.764×1000/750/1.1/28.959×22.4=9770.53nm3/h
考虑10%热损,循环风量按8793.5nm3/h取值。
最大热态风量为(900+273)/273×8793.5=37783.0m3/h,流化冷激器上部烟道流速应按此风量设计
蒸汽产量:8793.5/22.4×28.959×1.1×750/2250/1000=4.17t/h。吹炼渣密度约3.89t/m3,流化密相区的空隙率为0.7,密相区平均密度为0.3×3.89=1.167t/m3,密相区高度按最大5m计算,颗粒重力为1.167×5×1×9.8×1000=57183pa,风机的全压应不小于57183+5000=62183pa,可采用鼓风机接力来克服此系统阻力。
起点商标作为专业知识产权交易平台,可以帮助大家解决很多问题,如果大家想要了解更多知产交易信息请点击 【在线咨询】或添加微信 【19522093243】与客服一对一沟通,为大家解决相关问题。
此文章来源于网络,如有侵权,请联系删除


