一种用于注塑成型插座本体的模具的制作方法



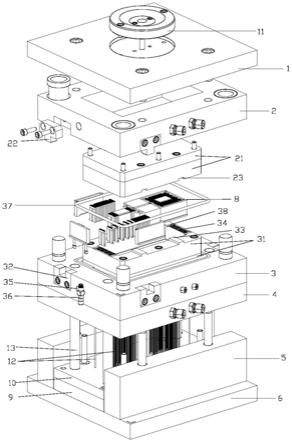
[0001]
本实用新型涉及模具领域,特别涉及一种用于注塑成型插座本体的模具。
背景技术:
[0002]
lga(land grid arry,栅格阵列)封装是一种将集成电路用绝缘的塑料或者陶瓷材料进行打包的技术。随着电子科技技术的进步与发展,lga封装技术在各行业中得到快速发展,主要在于它用金属触点式封装技术取代了过去的针状插脚式封装技术,lga插座是实现lga封装技术的关键性部件,被用于提供处理器和pc或服务器中的印刷电路板(pcb)之间可拆卸地的电连接与机械连接。
[0003]
lga插座包括插座本体、容纳在插座本体中的多个触点、附接到插座本体的加强件以及其他的一些配件。插座本体一般为框形体,在框形体的中间是多个排列成栅格阵列式的端子孔,在端子孔四周有凸出的侧壁,侧壁可用于处理器cpu的快速定位,在端子孔内插入端子触点。在lga插座使用时,当处理器被安装在lga插座上时,处理器的底面上的栅格阵列压在lga插座中细小的端子的栅格阵列上,从而形成可靠的电连接。因触点比较精密,与之相配的端子孔对尺寸要求很高,若因无法插入触点而使整组零件无法使用。
[0004]
通常情况下,lga插座上的端子触点多达几百甚至上千个,端子触点之间的间距为0.6-2mm,位置精度要求为0.04-0.1mm,安装端子触点的插座本体上的端子孔为异形孔,形状复杂;同时,由于芯片安装需求,lga插座平面的要求也极高,平面精度要求为0.2-0.4mm。在制作lga插座中需要先制备插座本体,然后在端子孔中安装触电以及后续的封装,目前制备lga插座上的端子触点多达几百甚至上千个,则需在插座本体上制备相应数量的异形端子孔,这些端子孔数量要求多,排列成栅格阵列,尺寸精度要求高,在成型过程中塑料熔体难以填充满型腔,且型腔内部气体无法排出,导致成型插座本体尺寸不稳定,成品率低。因此,成型插座本体具有极高的工艺需求,这对国内普通模具设计加工企业仍然具有一定的难度。
技术实现要素:
[0005]
本实用新型的目的在于针对因制备插座本体时端子孔数量多,端子孔尺寸精度和位置精度要求高,且成型过程塑料熔体难以填充满型腔且型腔内部气体无法排出导致成品率低的问题,提供一种用于注塑成型插座本体的模具,该模具能高效、精准的得到加工尺寸稳定的插座本体,保证产品尺寸的精度,且成品率高。
[0006]
为了实现上述实用新型目的,本实用新型提供了以下技术方案:
[0007]
一种用于注塑成型插座本体的模具,包括依次连接的顶板、定模板和动模板、托板、方铁和底板;
[0008]
所述定模板内设置有至少一个定模仁,每个所述定模仁内设置有至少一个定模镶件组件,所述动模板内设置有与所述定模仁数量匹配的动模仁,所述动模仁内设置有与所述定模镶件组件数量匹配的动模镶件组件,所述定模镶件组件与所述动模镶件组件相互配
合形成插座本体型腔;所述定模镶件组件包括定模内镶件组件和定模外镶件组件,所述定模内镶件组件包括定模内镶件二和多个定模内镶件一,所述定模内镶件一的下表面设置有若干个第一凸部,所述定模内镶件一的侧面设置有凹陷的定模排气槽;所述动模镶件组件包括动模内镶件组件和动模外镶件组件,所述动模内镶件组件包括动模内镶件二和多个动模内镶件一,所述动模内镶件一的上表面设置有若干个排列的第二凸部,所述动模内镶件一的侧面设置有凹陷的动模排气槽。
[0009]
本实用新型所述的用于注塑成型插座本体的模具采用在动模板和定模板中分别设置了动模仁和定模仁,动模仁和定模仁内分别设置了动模镶件组件和定模镶件组件,定模镶件组件和动模镶件组件相互配合即可形成插座本体型腔,在插座本体型腔内可成型插座本体,成型的插座本体具有多个端子孔且端子孔排列成栅格阵列,本实用新型将复杂的插座本体结构采用定模镶件组件和动模镶件组件配合来形成,定模镶件组件设置有定模排气槽,动模镶件组件设置有动模排气槽,排气槽的设置可以利于注射成型时型腔内多余其他的排出,成型过程时塑料熔体能填充满型腔,保证成型的插座本体尺寸的精度。本实用新型的模具能高效、精准的得到加工尺寸稳定的插座本体,保证产品尺寸的精度,且成品率高,可连续化、自动化大规模生产。
[0010]
进一步,所述方铁有两个,相对设置在所述底板上。
[0011]
进一步,所述顶板上设有浇口套,所述浇口套中设置有浇口通道;所述浇口套中的所述浇口通道穿过所述顶板和所述定模板延伸至所述动模板的顶面,所述动模板上设置有分流道,所述分流道与所述插座本体型腔连通。
[0012]
进一步,所述模具设置有侧定位组件,所述侧定位组件包括凸件和凹件,所述凸件安装在所述定模板上,所述凹件安装在所述动模板上,所述侧定位组件有四组,用于在合模时所述动模板和所述定模板的定位,防止错位。
[0013]
进一步,所述模具还设置有镶件定位组件,所述镶件定位组件包括凸块和凹块,所述凹块设置在所述定模仁上,所述凸块设置在所述动模仁上,所述镶件定位组件有两组,用于所述定模镶件组件与所述动模镶件组件的精确定位,防止错位,避免造成成型后插座本体的尺寸差异或毛刺。
[0014]
进一步,所述模具还包括顶出机构,所述顶出机构包括上顶板、下顶板和若干根顶针,若干根所述顶针安装在所述上顶板上,所述顶针的截面为圆形,每根所述顶针的顶面与所述插座本体型腔接触,所述顶出机构在插座本体成型后将其顶出型腔,防止因插座本体腔型过小或异性的窄槽使得插座本体局部断裂并残留在型腔中,导致成型后型腔内残留的塑料不易清理的问题。
[0015]
进一步,所述动模仁上设置有第一型腔和反向排气槽,所述第一型腔与所述插座本体型腔连通,作为所述插座本体型腔的延伸部分,所述反向排气槽与所述第一型腔连通,所述反向排气槽设置为s形,所述反向排气槽的深度为0.2~0.3mm。所述第一型腔的设置增加了注射成型时型腔的空间,可以让热熔塑料充满所述插座本体型腔并将多余部分流入到所述第一型腔中,可以保证插座本体尺寸的稳定。所述反向排气槽的设置可以用于所述第一型腔和所述插座本体型腔内排气。
[0016]
进一步,所述动模板内设置有真空通道,所述真空通道与所述插座本体型腔连通,所述真空通道的真空孔设置在所述动模板的侧面,所述真空孔与真空发生器相连接,连接
上真空发生器后可进行抽真空操作从而保证插座本体型腔内的真空状态。
[0017]
进一步,所述定模板和所述动模板之间设置有密封件,所述密封件为环形,所述密封件位于所述动模仁的外周。所述密封件能形成与所述插座本体型腔连通的密封腔,可以确保所述插座本体型腔的真空度。
[0018]
进一步,所述模具还包括复位针,所述复位针的一端安装在所述顶出机构的上顶板的底面、另一端贯穿所述托板和所述动模板。
[0019]
进一步,所述定模板和所述动模板之间设置有导柱一。
[0020]
进一步,所述模具设置导柱二,所述导柱二设置于底板、下顶板、上顶板和托板导向孔内。
[0021]
进一步,所述插座本体型腔的内壁设置有铁氟龙涂层,所述铁氟龙涂层的厚度为0.0005~0.01mm,用于提高型腔的脱模能力。
[0022]
在本实用新型中,所述定模外镶件组件包括多个定模外镶件,所述动模外镶件组件包括多个动模外镶件,每个定模外镶件和每个定模外镶件均可进行单独拆分。进一步,所述定模内镶件组件包括定模内镶件二和多个定模内镶件一,所述动模内镶件组件包括动模内镶件二和多个动模内镶件一,每个定模内镶件和每个动模内镶件均可进行单独拆分。
[0023]
进一步,多个所述第一凸部在所述定模内镶件一的下表面排列成两排。
[0024]
进一步,多个所述第二凸部在所述动模内镶件一的上表面排列成两排。
[0025]
进一步,所述动模排气槽包括相互连通的动模第一排气槽和动模第二排气槽,所述动模第一排气槽与所述插座本体型腔连接,所述动模第二排气槽连接动模第一排气槽和所述动模内镶件一的下表面,所述动模第一排气槽的截面积小于动模第二排气槽的截面积。
[0026]
进一步,所述定模排气槽包括相互连通的定模第一排气槽和定模第二排气槽,所述定模第一排气槽与所述插座本体型腔连接,所述定模第二排气槽连接定模第一排气槽和所述定模内镶件一的上表面,所述定模第一排气槽的截面积小于定模第二排气槽的截面积。
[0027]
进一步,所述动模第一排气槽的深度为10~50μm,所述动模第二排气槽的深度为50~300μm,因动模第一排气槽直接和所述插座本体型腔接触,为防止出现溢料,所以排气槽不易开太大。
[0028]
进一步,所述定模第一排气槽的深度为10~50μm,所述定模第二排气槽的深度为50~300μm。
[0029]
进一步,所述模具还设置有加热系统和冷却系统,所述加热系统包括了电加热系统和/或液体加热系统,所述电加热系统通过加热棒对模具进行温度控制,所述液体加热系统通过将模具内道管与模温机相接,然后利用介质水或者导热油对模具进行温度控制。
[0030]
与现有技术相比,本实用新型的有益效果:
[0031]
1、本实用新型的模具用于lga插座的插座本体的注塑成型,该模具能高效、精准的得到加工尺寸稳定的插座本体,保证产品尺寸的精度,且成品率高,可连续化、自动化大规模生产。
[0032]
2、本实用新型的模具在定模镶件组件与动模镶件组件上分别设置有定模排气槽和动模排气槽,在成型过程中插座本体型腔内多余气体可从定模排气槽和动模排气槽排
出,同时,模具还设置有第一型腔和反向排气槽,第一型腔的设置增加了注射成型时型腔的空间,可以让热熔塑料充满插座本体型腔后并将多余部分流入到第一型腔中,插座本体型腔和第一型腔内的多余气体也可从反向排气槽排出,保证插座本体尺寸的稳定。
[0033]
3、本实用新型的模具设置有顶出机构,顶出机构有若干顶针,若干顶针在插座本体成型后将其顶出型腔,防止因插座本体腔型过小或异性的窄槽使得插座本体局部断裂并残留在型腔中,导致成型后型腔内残留的塑料不易清理的问题。
附图说明
[0034]
图1是本实用新型lga插座本体的模具的三维示意图;
[0035]
图2是本实用新型lga插座本体的模具的爆炸图;
[0036]
图3是本实用新型中模具上半部分三维示意图;
[0037]
图4是本实用新型中模具下半部分三维示意图;
[0038]
图5是本实用新型定模镶件组件的结构示意图;
[0039]
图6是本实用新型定模镶件组件的局部放大图;
[0040]
图7是本实用新型定模内镶件一的结构示意图;
[0041]
图8是本实用新型动模镶件组件的结构示意图;
[0042]
图9是本实用新型动模镶件组件的局部放大图;
[0043]
图10是本实用新型动模内镶件一的结构示意图;
[0044]
图11是本实用新型动模内镶件二的结构示意图;
[0045]
图标:1-顶板,2-定模板,3-动模板,4-托板,5-方铁,6-底板,7-定模镶件组件,8-动模镶件组件,9-下顶板,10-上顶板,11-浇口套,12-顶针,13-复位针,14-加热棒,15-液体管道,21-定模仁;22-凸块;23-凹部;24-复位针;20-螺栓孔;31-动模仁,32-凹块,33-凸部,34第一型腔,35-真空孔,36-真空发生器,37-密封件,38-反向排气槽,71定模外镶件组件,72-定模内镶件一,73-定模内镶件二,721-第一凸部,722-定模第一排气槽,723-定模第二排气槽,81-动模外镶件组件,82-动模内镶件一,83-动模内镶件二,821-第二凸部,822-动模第一排气槽,823-动模第二排气槽。
具体实施方式
[0046]
下面结合试验例及具体实施方式对本实用新型作进一步的详细描述。但不应将此理解为本实用新型上述主题的范围仅限于以下的实施例,凡基于本实用新型内容所实现的技术均属于本实用新型的范围。
[0047]
实施例1
[0048]
如图1-9所示,一种用于lga插座本体的模具,包括依次连接的顶板1、定模板2和动模板3、托板4、方铁5和底板6;定模板2内设置有一个定模仁21,定模仁21内设置有至少一个定模镶件组件7,本实施例设置有两个定模镶件组件7,动模板3内设置有一个动模仁31,动模仁31内设置有与定模镶件组件7数量匹配的2个动模镶件组件8,定模镶件组件7与动模镶件组件8相互配合形成插座本体型腔;定模镶件组件7包括定模内镶件组件和定模外镶件组件71,所述定模内镶件组件包括定模内镶件二73和多个定模内镶件一72,定模内镶件一72的下表面设置有若干个第一凸部721,定模内镶件一72的侧面设置有凹陷的动模排气槽;动
模镶件组件8包括动模内镶件组件和动模外镶件组件81,动模内镶件组件包括动模内镶件二83和多个动模内镶件一82,动模内镶件一82的上表面设置有若干个第二凸部821,动模内镶件一的侧面设置有凹陷的动模排气槽。
[0049]
顶板上设有浇口套11,浇口套11中设置有浇口通道;浇口套11通过螺栓与顶板1连接,浇口套11中的浇口通道穿过顶板1和定模板2延伸至动模板3的顶面,动模板上设置有2个分流道,每个分流道与插座本体型腔连通。顶板1通过四个螺栓和定模板2连接,定模板2和动模板3之间设置有导柱一。
[0050]
本实用新型的模具有两个方铁5,分别设置在底板6的两侧,模具还设置有导柱二,导柱二设置于底板6、下顶板9、上顶板10和托板4的导向孔内。如图1、2所示,本实施例的模具还包括顶出机构,所述顶出机构包括上顶板10、下顶板9和若干根顶针12,若干根顶针12的底端安装在上顶板10上,顶针12的截面为圆形,顶针12穿过上顶板10、托板4、动模板3中的动模镶件组件8,每根顶针12的顶面与插座本体型腔接触,顶出机构在插座本体成型后将其顶出型腔。因动模内镶件一82的上表面设置有若干个第一凸部821,插座本体在顶出的过程中容易受到凸部821的影响,导致插座本体无法顶出或插座本体的端子孔被破坏,成品率低,因此本实用新型的顶针12设置有多个,每个顶针12的上部设置在动模内镶件一82内,如图8所示,在动模内镶件一82内有安装顶针的孔,在图9或图10中可以清晰的看出,每间隔一个动模内镶件一82设置有一排顶针,不同位置的动模内镶件一82内的顶针12数量不同,有2个、3个或者4个,这些顶针12可以完整的将插座本体顶出型腔中,不会受到凸部821的干扰。同时,插座本体型腔的内壁设置有铁氟龙涂层,用于提高型腔的脱模能力,本实施例中铁氟龙涂层的厚度为0.001-0.002mm。模具还设置复位针13,复位针13的一端安装在所述顶出机构的上顶板10的底面、另一端贯穿托板4和动模板3。
[0051]
本实用新型的模具设置有侧定位组件,侧定位组件包括凸块22和凹块32,凸块22安装在定模板2上,凹块32安装在动模板3上,侧定位组件有四组,分别设置在定模板2与动模板3的四个侧面,用于在合模时动模板3和定模板2的定位,防止错位。
[0052]
如图2所示,定模仁21包括定模仁上板和定模仁下板,定模仁下板内镶嵌有2个定模镶件组件7,定模仁上板和定模仁下板通过螺栓连接,在定模仁上板上设置有螺栓,可将定模仁21与顶板1连接。动模仁31包括动模仁上板和动模仁下板,动模仁上板内镶嵌有2个动模镶件组件8,动模仁上板和动模仁下板通过螺栓连接,在动模仁下板上设置有螺栓,可将动模仁31与托板4连接。如图3、4所示,模具设置有设置有镶件定位组件,镶件定位组件包括凸部23和凹部33,凹部23设置在所述定模仁21上,凸部设置在动模仁31上,镶件定位组件有两组,用于定模镶件组件7与动模镶件组件8的精确定位,防止错位,避免造成成型后插座本体的尺寸差异或毛刺,本实用新型的模具在合模过程中通过定模板2和动模板3的侧定位组件,同时配合定模仁21和动模仁31的镶件定位组件双重保证定模镶件组件7与动模镶件组件8能精确的定位,保证成型后的插座本体尺寸的高精度。
[0053]
如图4所示,动模仁31上设置有第一型腔34和反向排气槽38,第一型腔34与插座本体型腔连通,反向排气槽38与第一型腔38连通。本实用新型第一型腔34位于远离分流道进口的一侧,作为插座本体型腔的延伸部分,这样的设置增加了注射成型时型腔的空间,保证塑料熔体先充满插座本体型腔,多余的塑料熔体再流入第一型腔34,可以保证插座本体尺寸的稳定,第一型腔34内成型的塑料在插座本体成型后要被裁掉。反向排气槽38设置为s
形,反向排气槽38的深度为0.2-0.3mm,用于第一型腔34和插座本体型腔的排气,反向排气槽口38通过槽口与第一型腔34连通,槽口与第一型腔34内塑料熔体流动方向之间有夹角,夹角为90
°-
150
°
,这种夹角的设置可以防止塑料熔体流入到反向排气槽口38中。
[0054]
动模板3内设置有真空通道,真空通道与插座本体型腔连通,真空通道的真空孔35设置在所述动模板3的侧面,真空孔35与真空发生器36相连接,连接上真空发生器36后,向真空通道中通入喷射压缩空气,可进行抽真空操作,真空度范围为-120kpa~-90kpa,从而保证插座本体型腔内的真空状态。
[0055]
如图4所示,定模板2和动模板2之间设置有密封件37,密封件37为环形,密封件37位于动模仁31的外周,在定模板3上设置有相应位置的凹槽,如图3所示;合模后的定模板2和动模板3可以用密封件37能形成一个腔,这个腔与所述插座本体型腔连通成密封腔,可以确保所述插座本体型腔的真空度。
[0056]
如图5、6所示,定模镶件组件7包括定模内镶件组件和定模外镶件组件71,定模外镶件组件71包括多个定模外镶件,定模内镶件组件包括多个定模内镶件一72和定模内镶件二73,多个定模外镶件和多个定模内镶件一72均可以单独拆分,如图7所示,定模内镶件一72的下表面设置有若干个第一凸部721,若干个第一凸部721在定模内镶件一72的下表面均匀地排列成两排,第一凸部721为异形,形状如图6的局部放大图所示,定模内镶件一72的两个侧面均设置有定模排气槽。
[0057]
如图8、9所示,动模镶件组件8包括动模内镶件组件和动模外镶件组件81,动模外镶件组件81包括多个动模外镶件,动模内镶件组件包括多个动模内镶件一82和动模内镶件二83,动模内镶件二83的结构如图11所示,多个动模外镶件和多个动模内镶件一82均可以单独拆分,如图10所示,动模内镶件一82的上表面设置有若干个排列的第二凸部821,第二凸部821在动模内镶件一82的上表面排列成两排,且与每个第一凸部721位置相对应,用于成型插座本体的端子孔,第二凸部821为异形,形状如图9的局部放大图所示,第一凸部721和第二凸部821的特征尺寸为0.2~0.5mm,第一凸部721之间的间距为0.6~2mm,位置度要求为0.08mm,成型后插座本体的平面度为0.2~0.4mm。动模内镶件一82的两个侧面均设置有动模排气槽。
[0058]
定模排气槽包括相互连通的定模第一排气槽722和定模第二排气槽723,定模第一排气槽722与插座本体型腔连接,定模第二排气槽723连接定模第一排气槽722和定模内镶件一72的上表面,定模第一排气槽722的截面积小于定模第二排气槽723的截面积。进一步,定模第一排气槽722的深度为10~50μm,定模第二排气槽723的深度为50~300μm。
[0059]
动模排气槽包括相互连通的动模第一排气槽822和动模第二排气槽823,动模第一排气槽822与插座本体型腔连接,动模第二排气槽823连接动模第一排气槽822和动模内镶件一82的下表面,动模第一排气槽822的截面积小于动模第二排气槽823的截面积。进一步,动模第一排气槽822的深度为10~50μm,动模第二排气槽823的深度为50~300μm。
[0060]
本实施例模具设置有加热系统和冷却系统,所述加热系统包括了电加热系统和液体加热系统,所述电加热系统通过电加热棒对模具进行温度控制,定模板2和动模板3的板体上设有加热棒14,加热棒14用于板体的加热,定模板2和托板4的板体上设有液体管道15,液体管道15与外界连通;在注射成型前,液体管道15可以与模温机相接,通过热的介质水或者导热油对模具加热,形成液体加热系统,本实施例的模具通过电加热系统和液体加热系
统的双加热系统对模具进行温度控制,可以保证模具温度的稳定性。同时,定模板2和动模板3板体上分别设置有一个温度传感器,用于监控板体的温度。此外,当注射成型完成后,液体管道14可以接冷却水或者冷却液,形成冷却系统,用于浇注后模具和成型插座本体的冷却。
[0061]
以上所述仅为本实用新型的较佳实施例而已,并不用以限制本实用新型,凡在本实用新型的精神和原则之内所作的任何修改、等同替换和改进等,均应包含在本实用新型的保护范围之内。
起点商标作为专业知识产权交易平台,可以帮助大家解决很多问题,如果大家想要了解更多知产交易信息请点击 【在线咨询】或添加微信 【19522093243】与客服一对一沟通,为大家解决相关问题。
此文章来源于网络,如有侵权,请联系删除



tips