一种低TG结晶共聚酯高效造粒系统的制作方法



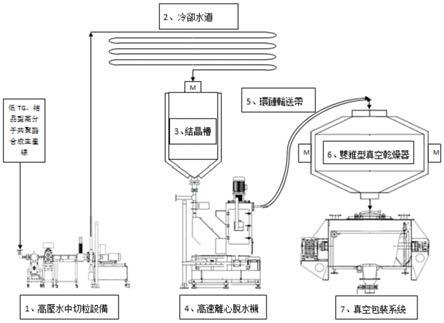
一种低tg结晶共聚酯高效造粒系统
技术领域
[0001]
本发明涉及高分子设备技术领域,尤其涉及一种低tg结晶共聚酯高效造粒系统。
背景技术:
[0002]
随着国家及市场对环保的要求日趋严格,高分子聚酯产品从溶剂型逐渐向无溶剂型转变,无溶剂型高分子聚酯则以固体微小颗粒的形式生产,以利于后段应用。现有的技术成熟造粒设备主要适用于普通的高tg或者非结晶型材料的生产工艺。在材料熔融状态下通过加压使得材料通过孔板模头后,对材料进行切粒或者切断,同时利用水(或者冷媒)迅速将材料从熔融状态冷却成为固体(无粘连性),然后通过冷却的水通道进一步冷却及输送到下一设备。颗粒经过离心或者热风等方式干燥后即可经过震动筛网筛选后进行包装。
[0003]
然而,现有的成熟造粒系统对于低tg、结晶型的共聚酯的造粒等无法适用,主要有以下问题:
[0004]
1、低tg、结晶型共聚酯产品从熔融状态经挤出后,虽然可以用切粒机在水中切分成小颗粒,但由于其结晶时间比较长(约30min~50min),结晶之前很容易因为回粘出现结块的现象,结块后,无法快速干燥及重新成粒。而切粒水道往往只有几十米,几百米,以水流速,其经过时间最长也只有几分钟;
[0005]
2、低tg、结晶型共聚酯材料有水解性,水分会导致产品出现分解从而性能劣化直至客户无法使用。所以在切粒及结晶完成后,需尽快对颗粒进行干燥及密封包装。而现有干燥做法均为利用离心机或者热风的方式进行干燥,前者无法到达干燥(需求水份低于900ppm),后则因风温(超过60℃颗粒会回粘结块)受限十分低效,尤其是南方比较潮湿;
[0006]
3、产品的结晶和干燥工序在现有的成套设备下效率非常低下,也无法连续量产。
技术实现要素:
[0007]
针对上述问题,本发明提出一种低tg结晶共聚酯高效造粒系统,主要解决背景技术中的问题。
[0008]
本发明提出一种低tg结晶共聚酯高效造粒系统,包括高压水中切粒设备,所述高压水中切粒设备与结晶槽通过冷却水道连接,所述结晶槽的底端连接有高速离心脱水机,所述高速离心脱水机与双锥型真空干燥器通过环链输送带连接,所述双锥型真空干燥器的底端连接有真空包装系统。
[0009]
进一步改进在于,所述冷却水道的水道水温为11~18℃,以防止树脂结晶前回粘。
[0010]
进一步改进在于,所述高压水中切粒设备包括齿轮泵,所述齿轮泵将熔融状态的高分子共聚酯挤压到孔板的模头处,通过高速切刀对共聚酯进行切粒,且所述齿轮泵为变频电机。
[0011]
进一步改进在于,所述高压水中切粒设备中设置有若干个压力传感器和若干个温度传感器。
[0012]
进一步改进在于,所述高压水中切粒设备的切粒压力为100~120bar。
[0013]
进一步改进在于,所述结晶槽配备有高速分散功能,以防止结晶过程中颗粒堆积结块,且所述结晶槽通过外层夹套控制槽内温度,以利于结晶。
[0014]
进一步改进在于,所述双锥型真空干燥机通过抽真空的模式将水的沸点降低至回粘温度以下,并利用夹层内的热水循环可精准控制温度,以确保水分能够快速蒸发。
[0015]
进一步改进在于,所述真空包装系统采用铝塑膜作为包装袋,并利用充氮后负压进行包装封口。
[0016]
与现有技术相比,本发明的有益效果为:
[0017]
1、本发明通过水循环系统、帮助切粒在切完之后快速进入结晶槽;在结晶完毕,经过高转速离心机做初步的脱水,将含水率降低至2000ppm以下,由环链输送入双锥干燥机。干燥至含水率低于900ppm后,卸料入包装槽包装,以此实现产品高效、连续生产的目的;
[0018]
2、本发明对于结晶槽的设置,可以将单批次切粒量从500kg,提高至2000kg,解决了现有技术中单批次间的颗粒结晶间隔此前为连续生产的瓶颈,导致产能偏低,无法有效满足客户需求的难题。本发明的结晶槽可有效移除结晶间隔,实现大量连续生产,可有效提高月产能。
附图说明
[0019]
附图仅用于示例性说明,不能理解为对本专利的限制;为了更好说明本实施例,附图某些部件会有省略、放大或缩小,并不代表实际产品的尺寸;对于本领域技术人员来说,附图中某些公知结构及其说明可能省略是可以理解的。
[0020]
图1为本发明一实施方式的整体流程示意图;
[0021]
其中:1、高压水中切粒设备;2、冷却水道;3、结晶槽;4、高速离心脱水机;5、环链输送带;6、双锥型真空干燥机;7、真空包装系统。
具体实施方式
[0022]
在本发明的描述中,需要说明的是,除非另有明确的规定和限定,术语“安装”、“连接”应做广义理解,例如,可以是固定连接,也可以是可拆卸连接,或一体地连接;可以是机械连接,也可以是电连接;可以是直接相连,也可以是通过中间媒介间接连接,可以说两个元件内部的连通。对于本领域的普通技术人员而言,可以具体情况理解上述术语在本发明的具体含义。下面结合附图和实施例对本发明的技术方案做进一步的说明。
[0023]
参照图1,一种低tg结晶共聚酯高效造粒系统,包括高压水中切粒设备1,所述高压水中切粒设备1与结晶槽3通过冷却水道2连接,所述结晶槽3的底端连接有高速离心脱水机4,所述高速离心脱水机4与双锥型真空干燥器通过环链输送带5连接,所述双锥型真空干燥器的底端连接有真空包装系统7。
[0024]
作为本发明一优选实施方案,所述冷却水道2的水道水温为11~18℃,以防止树脂结晶前回粘。
[0025]
作为本发明一优选实施方案,所述高压水中切粒设备1包括齿轮泵,所述齿轮泵将熔融状态的高分子共聚酯挤压到孔板的模头处,通过高速切刀对共聚酯进行切粒,且所述齿轮泵为变频电机。
[0026]
作为本发明一优选实施方案,所述高压水中切粒设备1中设置有若干个压力传感
器和若干个温度传感器。
[0027]
作为本发明一优选实施方案,所述高压水中切粒设备1的切粒压力为100~120bar。
[0028]
作为本发明一优选实施方案,所述结晶槽3配备有高速分散功能,以防止结晶过程中颗粒堆积结块,且所述结晶槽3通过外层夹套控制槽内温度,以利于结晶。
[0029]
作为本发明一优选实施方案,所述双锥型真空干燥机6通过抽真空的模式将水的沸点降低至回粘温度以下,并利用夹层内的热水循环可精准控制温度,以确保水分能够快速蒸发。
[0030]
作为本发明一优选实施方案,所述真空包装系统7采用铝塑膜作为包装袋,并利用充氮后负压进行包装封口。
[0031]
本发明的工作过程为:
[0032]
树脂在合成后,先通过真空脱泡后,控制温度在切粒适宜温度,包出熔融状态。利用高压水中切粒设备1将颗粒加压在水中切成颗粒,通过循环水进入冷却水道2后进入结晶槽3。待颗粒结晶完毕后,利用水将颗粒带入高速离心脱水机4,经过初步脱水后,走环链输送带5进入双锥型真空干燥机6。待干燥至含水率低于900ppm,进入真空包装系统7。
[0033]
其中:
[0034]
1、高压水中切粒设备1:是利用齿轮泵将熔融状态的高分子共聚酯挤压到孔板的模头处,在水中使用高速切到对共聚酯进行切粒。其中整体的切利设备含有多个压力、温度监控以确保切粒过程参数可及时反馈,齿轮泵为变频电机、切粒设备各处可加热/冷却以控制模头温度尽量缩短结晶时间;其中切粒压力控制在100~120bar为高效出料状态。
[0035]
2、冷却水道2是利用冷冻水,将水道水温稳定控制在11~18℃之间,以防止树脂结晶前回粘;
[0036]
3、结晶槽3配备有高速分散功能以防止结晶过程中颗粒堆积结块,且可通过外层夹套控制槽内温度,以利于结晶;
[0037]
4、高速离心机,将在水中结晶的颗粒进行高速离心做初步脱水;
[0038]
5、环链输送带5则是将初步脱水后的颗粒输送至双锥型真空干燥机6;
[0039]
6、双锥型真空干燥机6:腔体可通过抽真空的模式将水的沸点降低至回粘温度以下(50℃),以确保水分能快速蒸发且颗粒不会回粘;外壳为夹套控温,利用热水/冷却水控制温度;双锥腔体可旋转,帮助提高水分移除效率;
[0040]
7、真空包装系统7:将颗粒装入铝塑膜的包装袋后,利用充氮后负压将包装袋袋中多余的气体/水分进一步移除,然后封口。
[0041]
与现有技术相比,本发明的有益效果为:
[0042]
1、本发明通过水循环系统、帮助切粒在切完之后快速进入结晶槽3;在结晶完毕,经过高转速离心机做初步的脱水,将含水率降低至2000ppm以下,由环链输送入双锥干燥机。干燥至含水率低于900ppm后,卸料入包装槽包装,以此实现产品高效、连续生产的目的;
[0043]
2、本发明对于结晶槽3的设置,可以将单批次切粒量从500kg,提高至2000kg,解决了现有技术中单批次间的颗粒结晶间隔此前为连续生产的瓶颈,导致产能偏低,无法有效满足客户需求的难题。本发明的结晶槽3可有效移除结晶间隔,实现大量连续生产,可有效提高月产能。
[0044]
图中,描述位置关系仅用于示例性说明,不能理解为对本专利的限制;显然,本发明的上述实施例仅仅是为清楚地说明本发明所作的举例,而并非是对本发明的实施方式的限定。对于所属领域的普通技术人员来说,在上述说明的基础上还可以做出其它不同形式的变化或变动。这里无需也无法对所有的实施方式予以穷举。凡在本发明的精神和原则之内所作的任何修改、等同替换和改进等,均应包含在本发明权利要求的保护范围之内。
起点商标作为专业知识产权交易平台,可以帮助大家解决很多问题,如果大家想要了解更多知产交易信息请点击 【在线咨询】或添加微信 【19522093243】与客服一对一沟通,为大家解决相关问题。
此文章来源于网络,如有侵权,请联系删除



tips