直升机舱外机载设备安装架的制作方法



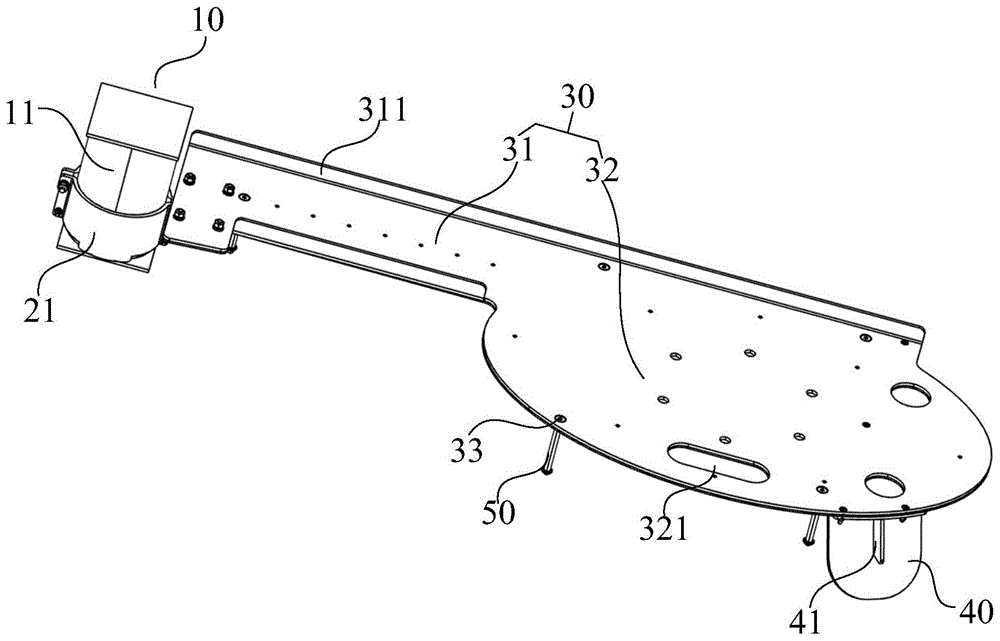
本发明涉及配合飞行器的设备技术领域,特别涉及直升机舱外机载设备安装架。
背景技术:
直升机相对于固定翼飞机,不需要修建机场,无需很长的机场跑道,不必花费大量的土地资源、财力和物力,其可在小面积场地垂直起降,因而在运输、巡逻、旅游、救护等多个领域得到了广泛运用。
在一些特殊使用情况下,需要在直升机的舱外加装外置设备,比如机载卫星通信系统,其主要用于解决高空通信受限的问题。目前在我国承担青藏高原地区飞行任务的直升机以及执行海上飞行任务的直升机,要求安装基于ku波段的机载卫星通信系统,其中,机载段的通信设备(位于直升机上的通信设备)主要包括机外天线、天线控制单元、功放、调制解调器以及无线接入设备,部分设备需安装于舱外,因此需要一个特殊设计的安装架用于承载这些卫星通信设备。
传统的直升机舱外机载设备安装架,其固定方式需要在直升机机壳可承力处进行打孔,然后通过螺栓固定安装,该方式对于直升机机壳改动大,破坏了飞机出厂时的原有结构,具有施工难度大、改装成本高的缺点。
技术实现要素:
为解决现有技术中,直升机舱外机载设备安装架存在的施工难度大、改装成本高的技术问题,本发明的技术方案如下:
本发明提供了一种直升机舱外机载设备安装架,所述直升机包括:用于降低螺旋桨振动的隔振器、开设于直升机外壳的机壳孔以及位于所述机壳孔内的机壳螺钉。需要特别说明的是:隔振器通常是具有一定阻尼的弹性装置,通过在振源的传递途径中安装隔振器来达到减小振源的传递称为“隔振”,在直升机的制造领域中,隔振器是一个关键设备,是设置于直升机螺旋桨与机舱的弹性元件,用以减少和消除由螺旋桨传递到机舱的振动力;直升机的机壳并非一体成型的结构,通常为组装件,机壳孔是开设于直升机机壳的原有安装孔,机壳孔内安装机壳螺钉,进而将散装的直升机机壳进行固定和装配。在本发明中,利用直升机的原有部件,在不对直升机进行改造的情况下,对安装架进行固定和装配,具体改进点为:紧固组件,与直升机原有的所述隔振器进行连接,为安装架提供主要的支撑点;水平支撑板,一侧与所述紧固组件固定连接,所述水平支撑板的形状与所述直升机的外壳形状相匹配,所述水平支撑板开设有多组通孔,所述通孔的开设位置与所述机壳孔的位置相匹配,多个通孔与机壳孔配合连接后,为安装架提供多个主要的支撑点。具体安装步骤为:拆卸所述机壳螺钉以露出所述机壳孔,将所述水平支撑板架设于所述直升机的外部,调节所述通孔与原有机壳孔使位置相应并通过孔连接件固定,所述水平支撑板通过所述紧固组件固定连接于所述隔振器,进而使所述安装架安装于所述直升机上。
以ec135p2直升机安装舱外设备为例,原有的安装固定方式需要在直升机机壳可承力处进行打孔,破坏了直升机出厂时的原有结构,导致机壳的强度下降,并且打孔过程施工难度大、改装成本高。本发明主要利用了原有直升机自身的可承力点和原有部件,将安装架的一侧与隔振器连接,同时,拆卸掉相应位置的机壳螺钉,利用原有的安装位置、机壳孔以及更换适当长度的孔连接件,进而完成安装架其他位置与机壳的固定和装配。本发明避免了传统安装方式的孔位配打操作,保证了直升机的机壳强度,并且改装施工简单、费用低。
在一种可能的设计中,所述紧固组件包括抱箍;所述抱箍为弧形板结构,所述隔振器包括设置于外部的支撑外壳,其中支撑外壳的作用是防止里面减振元件失效时,起到一个支撑作用。两个所述抱箍配合连接于所述支撑外壳外周,并通过螺栓螺母组件紧固。
以ec135p2直升机为例,螺旋桨下侧的通风孔内部就是隔振器,紧固组件伸入通风孔内,两个抱箍套设在支撑外壳的外部,通过螺栓螺母组件紧固。需要说明的是,紧固组件在伸入通风孔内前,需要将机壳等部件拆除,以为工人和设备提供操作空间。
可选地,抱箍与水平支撑板可以通过螺栓螺母组件进行连接,也可以设计为一个抱箍与水平支撑板焊接,另一个抱箍再与两者通过螺栓螺母组件进行连接。
在一种可能的设计中,所述紧固组件还包括衔接块;所述衔接块用于连接所述抱箍和所述水平支撑板,连接处通过螺栓螺母组件紧固。以进一步提高紧固组件的装配灵活性,同时,使安装架的整体为可拆卸的结构,方便安装架在工厂预制,并且便于储存和运输,零部件通用性也较强。
在一种可能的设计中,所述水平支撑板包括一体成型的直线部和机载设备安装部,所述直线部与所述衔接块连接。直线部主要为了匹配ec135p2直升机的通风孔孔道,用于衔接机载设备安装部与隔振器。机载设备安装部为主要的安装平台,卫星通信设备安装于此。
可选地,为了保证直线部的强度,直线部的宽度与通风孔孔道尽可能适配,直线部的宽度略小于通风孔的孔径即可。
在一种可能的设计中,所述直线部的两侧具有加强筋一。
其中,加强筋一主要有两个作用:一是为了提高直线部的自身强度,由于机载设备安装部与隔振器具有一定距离,衔接这两个部件的力均由直线部提供,因此需要保证直线部的强度;二是加强筋一为翻边结构,使直线部的侧面具有一定宽度,设置在通风孔孔道内时,可以提高直线部与通风孔孔道的接触面积,降低对孔道漆面的破坏。
在一种可能的设计中,所述机载设备安装部开设多个用于安装机载设备的通槽。
可选地,所述通槽为腰型槽、圆形槽等,其作用:一是为了装配机载设备;二为了降低自重和生产成本。
在一种可能的设计中,还包括:底部支撑板,设置于所述水平支撑板与所述直升机外壳之间。由于直升机外壳并不是一个平面,由此需要设计底部支撑板以对水平支撑板进行支撑。
可选地,底部支撑板可以与水平支撑板通过螺栓螺母组件固定连接,与直升机外壳抵接;或者,底部支撑板与水平支撑板和直升机外壳均通过孔连接件固定连接,此时,底部支撑板与机壳孔进行配位设计,并对机壳孔内的机壳螺钉进行拆卸。
在一种可能的设计中,所述底部支撑板具有加强筋二,进一步提高底部支撑板的强度。
在一种可能的设计中,所述孔连接件为螺栓螺母组件、销子或线绳。优选地采用螺栓螺母组件,使用时,通孔与原有机壳孔对齐并从直升机机壳外侧穿入螺栓至直升机内部,然后在直升机内部旋拧安装上螺母。
在一种可能的设计中,所述螺母为自锁螺母。
其中,由于普通螺纹紧固件主要受力点仅仅是螺母的第一、第二牙螺纹接触处,其余各牙基本不受力,因此当拧紧力矩较大时,应力集中在第一牙螺纹处,第一牙螺纹很容易产生弯曲和剪切变形,只有这样才使第二牙螺纹面承受应力并产生锁紧力。由此类推,承载负荷面将受力逐个传递,相应造成螺纹依次的剪切和磨损,各牙的剪切和磨损破坏严重,导致螺母和螺纹强度大幅度下降,最终导致滑丝。而自锁螺母的螺纹由于结构独特全部螺栓牙尖紧紧地顶在30°楔形斜面上,而且螺旋线上每牙承受的负载都比较均匀,同样负荷能分散到每个面、每个点上,使螺纹上各处产生防松摩擦力相近,能够有效抗阻横向振动。据研究,自锁螺纹第一个承受负载面承受i7%的负荷,而最后一个承载面也承受12.5%的负荷。因此它的每牙螺纹能均匀承受负载,不存在应力集中,也就不易产生松脱或滑牙问题,疲劳强度也得到成倍的改善。
附图说明
图1是本发明中,一种实施例提供的直升机舱外机载设备安装架的示意图;
图2是图1的另一视角的示意图;
图3是本发明中,一种实施例提供的紧固组件的示意图;
图4是本发明中,一种实施例提供的底部支撑板的示意图;
图5是本发明中,另一种实施例提供的紧固组件的示意图。
附图标记:10、隔振器;11、支撑外壳;20、紧固组件;21、抱箍;22、衔接块;30、水平支撑板;31、直线部;311、加强筋一;32、机载设备安装部;321、通槽;33、通孔;40、底部支撑板;41、加强筋二;50、孔连接件。
具体实施方式
下面将结合附图,对本发明中的技术方案进行描述。显然,所描述的实施例仅仅是本发明一部分实施例,而不是全部的实施例。
在本发明的描述中,需要说明的是,除非另有明确的规定和限定,术语“安装”、“相连”、“连接”应做广义理解,例如,可以是固定连接,也可以是可拆卸连接,或一体地连接;可以是机械连接,也可以是电连接或可以相互通讯;可以是直接相连,也可以通过中间媒介间接相连,可以是两个元件内部的连通或两个元件的相互作用关系。对于本领域的普通技术人员而言,可以根据具体情况理解上述术语在本发明中的具体含义。
在本发明的描述中,需要理解的是,术语“上”、“下”、“侧”、“内”、“外”、“顶”、“底”等指示的方位或位置关系为基于安装的方位或位置关系,仅是为了便于描述本发明和简化描述,而不是指示或暗示所指的装置或元件必须具有特定的方位、以特定的方位构造和操作,因此不能理解为对本发明的限制。
还需说明的是,本发明实施例中以同一附图标记表示同一组成部分或同一零部件,对于本发明实施例中相同的零部件,图中可能仅以其中一个零件或部件为例标注了附图标记,应理解的是,对于其他相同的零件或部件,附图标记同样适用。
以下,术语“第一”、“第二”等仅用于描述目的,而不能理解为指示或暗示相对重要性或者隐含指明所指示的技术特征的数量。由此,限定有“第一”、“第二”等的特征可以明示或者隐含地包括一个或者更多个该特征。
如图1-5所示,本发明提供了一种直升机舱外机载设备安装架,直升机包括:用于降低螺旋桨振动的隔振器10、开设于直升机外壳的机壳孔以及位于机壳孔内的机壳螺钉。需要特别说明的是:隔振器10通常是具有一定阻尼的弹性装置,通过在振源的传递途径中安装隔振器10来达到减小振源的传递称为“隔振”,在直升机的制造领域中,隔振器10是一个关键设备,是设置于直升机螺旋桨与机舱的弹性元件,用以减少和消除由螺旋桨传递到机舱的振动力;直升机的机壳并非一体成型的结构,通常为组装件,机壳孔是开设于直升机机壳的原有安装孔,机壳孔内安装机壳螺钉,进而将散装的直升机机壳进行固定和装配。在本发明中,利用直升机的原有部件,在不对直升机进行改造的情况下,对安装架进行固定和装配,具体改进点为:紧固组件20,与直升机原有的隔振器10进行连接,为安装架提供主要的支撑点;水平支撑板30,一侧与紧固组件20固定连接,水平支撑板30的形状与直升机的外壳形状相匹配,水平支撑板30开设有多组通孔33,通孔33的开设位置与机壳孔的位置相匹配,多个通孔33与机壳孔配合连接后,为安装架提供多个主要的支撑点。具体安装步骤为:拆卸机壳螺钉以露出机壳孔,将水平支撑板30架设于直升机的外部,调节通孔33与原有机壳孔使位置相应并通过孔连接件50固定,水平支撑板30通过紧固组件20固定连接于隔振器10,进而使安装架安装于直升机上。
以ec135p2直升机安装舱外设备为例,原有的安装固定方式需要在直升机机壳可承力处进行打孔,破坏了直升机出厂时的原有结构,导致机壳的强度下降,并且打孔过程施工难度大、改装成本高。本发明主要利用了原有直升机自身的可承力点和原有部件,将安装架的一侧与隔振器10连接,同时,拆卸掉相应位置的机壳螺钉,利用原有的安装位置、机壳孔以及更换适当长度的孔连接件50,进而完成安装架其他位置与机壳的固定和装配。本发明避免了传统安装方式的孔位配打操作,保证了直升机的机壳强度,并且改装施工简单、费用低。
如图5所示,在一种实施例中,紧固组件20包括抱箍21;抱箍21为弧形板结构,隔振器10包括设置于外部的支撑外壳11,其中支撑外壳11的作用是防止里面减振元件失效时,起到一个支撑作用。两个抱箍21配合连接于支撑外壳11外周,并通过螺栓螺母组件紧固。
以ec135p2直升机为例,螺旋桨下侧的通风孔内部就是隔振器10,紧固组件20伸入通风孔内,两个抱箍21套设在支撑外壳11的外部,通过螺栓螺母组件紧固。需要说明的是,紧固组件20在伸入通风孔内前,需要将机壳等部件拆除,以为工人和设备提供操作空间。
在一种实施例中,抱箍21与水平支撑板30可以通过螺栓螺母组件进行连接,也可以设计为一个抱箍21与水平支撑板30焊接,另一个抱箍21再与两者通过螺栓螺母组件进行连接。
如图3所示,在一种实施例中,紧固组件20还包括衔接块22;衔接块22用于连接抱箍21和水平支撑板30,连接处通过螺栓螺母组件紧固。以进一步提高紧固组件20的装配灵活性,同时,使安装架的整体为可拆卸的结构,方便安装架在工厂预制,并且便于储存和运输,零部件通用性也较强。
如图1-2所示,在一种实施例中,水平支撑板30包括一体成型的直线部31和机载设备安装部32,直线部31与衔接块22连接。直线部31主要为了匹配ec135p2直升机的通风孔孔道,用于衔接机载设备安装部32与隔振器10。机载设备安装部32为主要的安装平台,卫星通信设备安装于此。
在一种实施例中,为了保证直线部31的强度,直线部31的宽度与通风孔孔道尽可能适配,直线部31的宽度略小于通风孔的孔径即可。
在一种实施例中,直线部31的两侧具有加强筋一311。其中,加强筋一311主要有两个作用:一是为了提高直线部31的自身强度,由于机载设备安装部32与隔振器10具有一定距离,衔接这两个部件的力均由直线部31提供,因此需要保证直线部31的强度;二是加强筋一311为翻边结构,使直线部31的侧面具有一定宽度,设置在通风孔孔道内时,可以提高直线部31与通风孔孔道的接触面积,降低对孔道漆面的破坏。
在一种实施例中,机载设备安装部32开设多个用于安装机载设备的通槽321。
优选地,通槽321为腰型槽、圆形槽等,其作用:一是为了装配机载设备;二为了降低自重和生产成本。
如图4所示,在一种实施例中,还包括:底部支撑板40,设置于水平支撑板30与直升机外壳之间。由于直升机外壳并不是一个平面,由此需要设计底部支撑板40以对水平支撑板30进行支撑。
在一种实施例中,底部支撑板40可以与水平支撑板30通过螺栓螺母组件固定连接,与直升机外壳抵接。
在一种实施例中,底部支撑板40与水平支撑板30和直升机外壳均通过孔连接件50固定连接,此时,底部支撑板40与机壳孔进行配位设计,并对机壳孔内的机壳螺钉进行拆卸。
在一种实施例中,底部支撑板40具有加强筋二41,进一步提高底部支撑板40的强度。
在一种实施例中,孔连接件50为螺栓螺母组件,使用时,通孔33与原有机壳孔对齐并从直升机机壳外侧穿入螺栓至直升机内部,然后在直升机内部旋拧安装上螺母。
优选地,螺母为自锁螺母。
以上所述,仅为本发明的具体实施方式,但本发明的保护范围并不局限于此,任何熟悉本技术领域的技术人员在本发明揭露的技术范围内,可轻易想到变化或替换,都应涵盖在本发明的保护范围之内。因此,本发明的保护范围应以所述权利要求的保护范围为准。
起点商标作为专业知识产权交易平台,可以帮助大家解决很多问题,如果大家想要了解更多知产交易信息请点击 【在线咨询】或添加微信 【19522093243】与客服一对一沟通,为大家解决相关问题。
此文章来源于网络,如有侵权,请联系删除


