一种大巴车身总拼设备及方法与流程



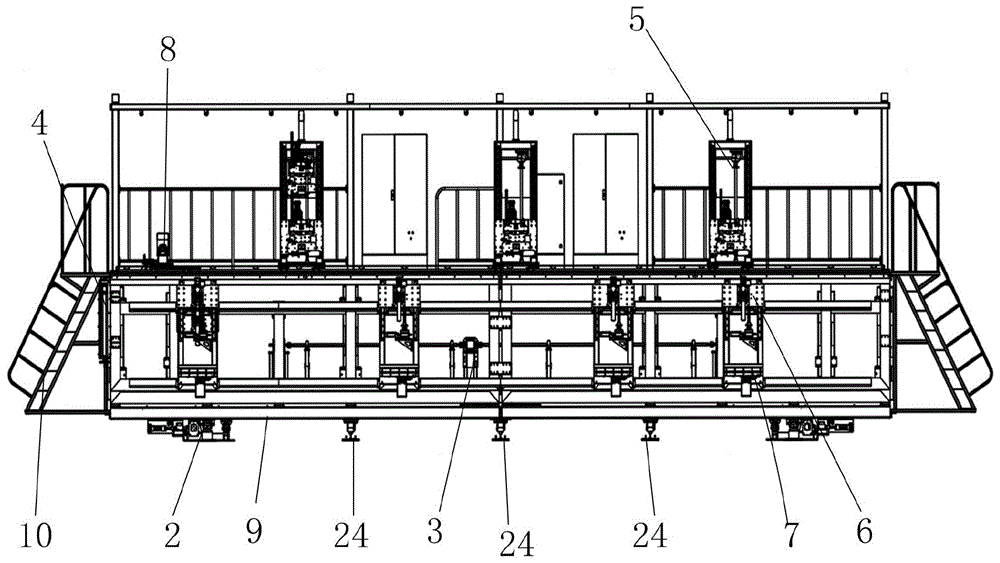
本发明涉及汽车智能制造技术领域,更具体的说是涉及一种大巴车身总拼设备及方法。
背景技术:
目前,目前客车行业具有定制化、小批量化的发展趋势,客车厂商都是根据订单来生产相应的车型,每个订单量从几台到几百台不等,一家大型车企的客车型号多达百来种,客车车身焊接生产时要求能够生产设备快速切换型号,对产线的柔性化、可调节、通用性生产需求很高。而目前行业内绝大多数大巴车身焊接设备都是在一个车型基础上设计,通过夹钳夹紧定位等方式实现相似车型的焊接生产。设备投入成本高,车型定位定位精度差,员工工作强度大。
因此,提供一种大巴车身总拼设备及方法,是本领域技术人员亟需解决的问题。
技术实现要素:
有鉴于此,本发明提供了一种大巴车身总拼设备及方法,采用此设备可实现不同规格大巴车身快速、精确、稳定、安全的柔性化切换生产,系统定位精度高,确保车身合拢拼装的质量的同时大幅度提高生产效率。
为了实现上述目的,本发明采用如下技术方案:
一种大巴车身总拼设备,包括底座和两侧对称布置的:
桁架,所述桁架设置在所述底座上,并与所述底座滑动连接;
桁架推进定位机构,所述桁架推进定位机构安装在所述底座上,用于实现两个所述桁架的靠近及远离;
侧围升降机构,所述侧围升降机构安装在所述桁架上用于对车身侧围的z轴方向定位;
侧围定位机构,所述侧围定位机构安装在所述桁架内测,用于对车身侧围的x轴方向定位;
窗立柱定位夹紧机构,所述窗立柱定位夹紧机构与所述桁架滑动连接,用于对车身侧围窗立柱的y轴方向定位;
腰梁定位夹紧机构,所述腰梁定位夹紧机构安装在所述侧围升降机构上,用于对车身侧围腰梁的y轴方向定位;
裙部立柱定位机构,所述裙部立柱定位机构安装在所述侧围升降机构上,用于对车身侧围立柱的y轴方向定位;
前围定位机构,所述前围定位机构设置在所述桁架的首端,用于车身前围z轴方向定位及y轴方向定位;
电气控制系统,所述电气控制系统均与上述机构电连接,并用于控制上述机构。
进一步的,还包括楼梯,所述楼梯倾斜的设置在所述桁架两端。
进一步的,所述桁架推进定位机构包括:架体锁紧装置、架体推进装置以及沿x轴方向铺设的直线导轨和辅助导轨,所述直线导轨和辅助导轨均设置在所述底座上,所述桁架与所述直线导轨和辅助导轨滑动连接;所述架体推进装置安装在所述底座上,包括液压油缸和驱动杆,所述驱动杆的端与所述桁架固定连接,所述架体锁紧装置安装在所述桁架的底部,包括气缸和定位轴,所述定位轴与所述气缸的驱动端固定连接,两个所述桁架靠近后所述定位轴与所述驱动杆抵接。
进一步的,还包括架体定宽装置、所述架体定宽装置包括伺服电机、螺旋升降机和定位板,所述伺服电机与所述螺旋升降机传动连接,所述螺旋升降机的伸缩轴端部连接有所述定位扳,所述定位板上设置有用于探测桁架与车身侧围距离的接近传感器。
进一步的,所述侧围升降机构包括:伺服电机、换向器、传动轴、螺旋升降机和架体,所述架体与所述桁架通过竖直导轨滑动连接,所述伺服电机与所述螺旋升降机均安装在所述底座上,所述换向器有两个动力输出端和一个动力输入端,所述动力输入端与所述伺服电机的转轴固定连接;两个所述螺旋升降机对称分布在所述换向器两侧,其动力输入端分别与所述换向器的动力输出端固定连接,其动力输出端与所述架体固定连接
进一步的,所述窗立柱定位夹紧机构包括支座以及安装在所述支座上的夹紧座、伺服电机、螺旋升降机、气缸和压臂,所述支座两侧设有导向滑轨,所述夹紧座通过导向滑轨与所述支座竖直滑动连接,所述伺服电机与所述螺旋升降机传动连接,所述压臂与所述气缸均固定安装在所述夹紧座上,所述压臂自由端与所述气缸的驱动杆固定连接。
进一步的,腰梁定位夹紧机构包括安装在所述架体上的伺服电机、螺旋升降机、油缸和压臂,所述架体通过滑轨与所述桁架竖直滑动连接,所述伺服电机与所述螺旋升降机传动连接,所述压臂自由端与所述油缸的驱动杆固定连接。
一种大巴车身总拼方法,采用上述的一种大巴车身总拼设备,包括:
(1)准备:根据生产车型调出控制系统已存储车型数据(新车型可手动输入车型数据并存储),腰梁定位夹紧机构自动调整z轴方向位置,裙部立柱定位机构自动调整y轴方向位置,窗立柱夹紧机构自动调整y轴、z轴方向位置;
(2)吊装车身侧围:用桁车同时吊装车身左右两侧骨架,放置在总拼设备的定位点上,同时进行侧围骨架x方向的定位,启动腰梁定位夹紧机构、窗立柱定位夹紧机构分别对车身两侧的骨架夹紧;
(3)车身底座就位:通过地拖链将车身底座抬升输送至总拼工位;
(4)侧围合装:两侧桁架架体带动侧围骨架沿y轴方向合拢至控制系统设定的位置,人工调节车身底座位置,至架体合拢到位,锁紧焊接;
(5)前围拼装:用桁车吊装前围骨架到总拼设备的前围定位机构位置上,微调前围z向高度,调整到位后,人工夹紧前围与侧围立柱,进行焊接;
(6)顶盖总成安装:通过桁车将顶盖骨架总成运送到车身骨架上方,使顶盖落位至车身骨架上,进行焊接;
(7)后围拼装:用桁车吊装后围骨架到总拼设备的后围z向定位装置上,微调后围z向高度,调整到位后,人工夹紧后围与侧围立柱,进行焊接;
(8)合拼设备侧围夹紧装置打开,架体锁紧装置打开,桁架退回原位,合拼后的车身骨架通过地拖链移至下一工位。
进一步的,在所述侧围合装过程中:当侧围骨架高度方向不满足要求,使用侧围升降机构对左右侧围进行整体微调,侧围位置调节完成后,架体合拢到位并锁紧架体,进行焊接。
经由上述的技术方案可知,与现有技术相比,本发明公开提供了一种大巴车身总拼设备,通过采用上述的技术方案,实现了大巴车身合装工位自动化生产方式,设备根据程序自动调用车型数据,自动调节各个定位机构的初始定位状态、自动保持夹紧工作状态、自动检测定位精度,可实现6m-13.6m各种不同规格大巴车身快速、精确、稳定、安全的柔性化切换生产,并可兼容后续新开发车型。系统定位精度高,确保车身合拢拼装的质量的同时大幅度提高生产效率。
附图说明
为了更清楚地说明本发明实施例或现有技术中的技术方案,下面将对实施例或现有技术描述中所需要使用的附图作简单地介绍,显而易见地,下面描述中的附图仅仅是本发明的实施例,对于本领域普通技术人员来讲,在不付出创造性劳动的前提下,还可以根据提供的附图获得其他的附图。
图1为本发明提供的整体结构示意图。
图2为本发明的桁架推进定位机构的结构示意图。
图3为本发明的桁架整体的结构示意图。
图4为本发明的侧围升降机构的结构示意图。
图5为本发明的侧围定位机构的结构示意图。
图6为本发明的窗立柱定位夹紧机构的结构示意图。
图7为本发明的腰梁定位夹紧机构的结构示意图。
图8为本发明的腰梁定位夹紧机构的局部结构示意图。
图9为本发明的裙部立柱定位机构的结构示意图。
图10为本发明的前围定位机构的结构示意图。
其中:
1-桁架;2-桁架推进定位机构;3-侧围升降机构;4-侧围定位机构;5-窗立柱定位夹紧机构;6-腰梁定位夹紧机构;7-裙部立柱定位机构;8-前围定位机构;9-底座;21-架体锁紧装置;22-架体推进装置;23-直线导轨;24-辅助导轨;25-架体定宽装置;211-气缸;31-伺服电机;33-螺旋升降机;32-传动轴;34-架体;41-手轮;42-安装板;43-摆臂;44-固定座;45-螺纹滑座;51-支座;52-夹紧座;53-锁紧气缸;54-压臂;55-导向滑轨;71-防护罩;72-位置检测器;81-滑座;82-刻度尺;83-滑杆;84-定位轴。
具体实施方式
下面将结合本发明实施例中的附图,对本发明实施例中的技术方案进行清楚、完整地描述,显然,所描述的实施例仅仅是本发明一部分实施例,而不是全部的实施例。基于本发明中的实施例,本领域普通技术人员在没有做出创造性劳动前提下所获得的所有其他实施例,都属于本发明保护的范围。
本发明实施例公开了一种大巴车身总拼设备,图1所示,包括底座9和两侧对称布置的:桁架1,桁架推进定位机构2,侧围升降机构3,侧围定位机构4,窗立柱定位夹紧机构5,腰梁定位夹紧机构6,裙部立柱定位机构7,前围定位机构8和电气控制系统;
其中桁架1设置在底座9上,并与底座9滑动连接;桁架1是各个机械组件安装固定的台架,桁架1单侧设计可放置4台二氧化碳焊机位置,并配有co2气体管线、电插座供焊机、角磨机和照明灯,架体上台面预留风扇(落地式)固定位置,上层设置有行走通道,宽度800mm,前后设有特制的双向楼梯10方便人员上下,桁架1顶部竖直设有立柱,立柱顶部沿y向的线缆滑轨,使桁车沿滑轨平行移动。
桁架推进定位机构2安装在底座1上,用于实现两个桁架1的靠近及远离,包括架体锁紧装置21、架体推进装置22以及沿x轴方向铺设的直线导轨23和辅助导轨24,直线导轨23和辅助导轨24均设置在底座9上,桁架1通过直线导轨23和辅助导轨24与底座9滑动连接,每侧桁架1底部布置3条辅助轨道,保证桁架1的运行精度,也确保桁架1的支撑刚度要求;架体推进装置22安装在底座9上,包括油缸221和驱动杆,驱动杆的自由端与桁架1固定连接,通过油缸221推动桁架1沿y轴方向整体移动;架体锁紧装置21安装在桁架1的底部,包括气缸211和定位轴,定位轴与气缸211的驱动端固定连接,定位轴与驱动杆垂直设置,当两个桁架1靠近并停止移动后,桁架1带动气缸211和定位轴移动,通过气缸211推动定位轴使其与驱动杆抵接,对桁架1锁紧防止退回。
有利的,桁架推进定位机构2还包括架体定宽装置25,架体定宽装置25包括伺服电机31、螺旋升降机33和定位板,伺服电机31与螺旋升降机33传动连接,螺旋升降机33的伸缩轴端部连接有定位扳,定位板上设置有用于探测桁架1与车身侧围距离的接近传感器,为实现桁架1在车身宽度的准确定位,通过伺服电机和螺旋升降机控制,保证架体宽度定位的无级调整精度,宽度方向(y方向)定位精度0-1mm。
侧围升降机构3安装在桁架1上用于对车身侧围的z轴方向定位,包括:伺服电机31、换向器、传动轴32、螺旋升降机33和架体34,架体34与桁架1通过竖直布置的4条导轨滑动连接,伺服电机31与螺旋升降机33均安装在底座9上,换向器有两个动力输出端和一个动力输入端,动力输入端与伺服电机31的转轴固定连接;两个螺旋升降机33对称分布在换向器两侧,其动力输入端分别与换向器的动力输出端固定连接,其动力输出端与架体34固定连接,推动架体34沿竖直方向升降;采用4套精密直线滑轨,来保证架体34运行精度和重复精度,进一步保证设备行走时的安全,通过一台三菱hg-sn302bj-s1003kw伺服电机,驱动左右2台螺旋升降机实现竖直方向±100mm范围内任意移动调节;
侧围定位机构4安装在桁架1首端外测,用于对车身侧围的x轴方向定位,包括手轮41、安装板42、摆臂43、螺杆和固定座44,固定座44沿竖直方向通过安装板42与桁架1固定连接,螺杆设置在固定座44的内部并与手轮41连接,摆臂43通过套设在螺杆上的螺纹滑座45与螺杆螺纹连接,摆臂43通过转轴与螺纹滑座45转动连接,通过手轮41转动带动摆臂43沿竖直方向升降移动,固定座44外侧沿长度方向刻有标尺,保证位移精度。
窗立柱定位夹紧机构5设置在桁架1的顶部并设置多个,窗立柱定位夹紧机构5与桁架1沿x轴方向滑动连接,用于对车身侧围窗立柱的y轴方向定位,每个窗立柱定位夹紧机构5间距为2-3米,x方向采用手动单独调节,适应不同窗立柱位置需求,x方向调整到位后,锁紧气缸53伸出锁紧桁架1定位;窗立柱定位夹紧机构5包括支座51以及安装在支座51上的夹紧座52、伺服电机31、螺旋升降机33、气缸211和压臂54,支座51的顶部设有容纳线缆的支管,支座51两侧设有沿z向的导向滑轨55,夹紧座52通过导向滑轨55与支座51竖直滑动连接,气缸211和压臂54均固定安装在夹紧座52上;伺服电机31与螺旋升降机33传动连接,带动夹紧座52沿z向上下移动(调整行程0-1100mm)能够保证各种车型窗立柱宽度的定位夹紧,压臂54的自由端与气缸211的驱动杆固定连接,通过气缸211的伸缩带动压臂54的收紧与放开。
腰梁定位夹紧机构6安装在侧围升降机构上,用于对车身侧围腰梁的y轴方向定位,包括安装在架体34上防护壳61,所述防护壳61内安装有伺服电机31、螺旋升降机33、油缸221和压臂54,架体底部顶部设有容纳线缆的支管62,架体34通过滑轨与桁架1竖直滑动连接,伺服电机31与螺旋升降机33传动连接,压臂54自由端与油缸221的驱动杆固定连接;z方向可分别或同时调整,调整行程450mm,定位精度0-0.5mm,z向调整由伺服电机31驱动螺旋升降机33带动整体上下移动,满足不同高度窗下梁的定位夹紧,采用液压夹紧方式,可根据需要夹紧或打开进行动作控制,使压臂54对侧围腰梁位置锁紧或松开。
裙部立柱定位机构7安装在架体34的底部,用于对车身侧围立柱的y轴方向定位;设置为多个,相互之间间距2-3米,包括防护罩71以及安装在防护罩71内的伺服电机31、螺旋升降机33和型号为e2b-m12kn05-wz-c2-2m的位置检测器72,伺服电机31与螺旋升降机33传动连接,无级数控调宽,带动整体z向上下移动,调整行程150mm,定位精度0-0.5mm,每个裙立柱定位机构调整可分别动作,保证车型长度变化定位,x方向采用手动单独调节与侧围定位机构4类似,适应不同侧舱门立柱y方向调整需要。
前围定位机构8设置在桁架1的靠近首端的顶部,用于车身前围z轴方向定位及y轴方向定位;包括手轮41、螺旋升降机33、滑座81、气缸211和沿x向设置的刻度尺82及滑杆83,气缸211沿y向安装在滑座81上,通过转动手轮41使滑座81沿滑杆83进行x向平行移动,观察刻度尺82准确定位,通过气缸211驱动定位轴84对车身前围y轴方向定位,z轴方向上下由螺旋升降机33调整,行程为800mm,y向伸缩调整行程为200mm,前围焊接前,可点动控制对前围高度进行微调。
在一个具体的实施例中,桁架两侧两侧独立布置有气动液压系统液压站系统,为该设备中的液压组件提供动力,系统压力可在3~7mpa范围内连续调整,工作压力为7mpa,设备在连续运行4小时后油温不高于55℃,合拼夹具在合拢后液压系统设置有保压装置,油缸221能持续的保证有压力,桁架不会退回,保证了合装时的精度,同时可以减少一定的消耗,气动系统配置气动三联件,系统压力可在0~1mpa范围内连续调整,工作压力为0.5mpa。
电气控制系统均与上述机构电连接,并用于控制上述机构;电气控制系统能存储至少500种各车型的成组数据,理论值和修正值都可以在显示屏上进行更改设置,能够输入调整值,调整值系统不存储,调整后不影响下次正常定位。还能够按车型长度、造型分类搜索车型数据,可实现离线编程。控制系统有状态检测及自检功能,能及时的发现设备存在的问题,配备相关的所有的plc、hmi、数控系统、网络通信、现场总线及其他专用设备的应用、编程、设计软件、操作系统及协议,可以跟公司内的其他系统实时进行数据交互。
本发明实施例公开了一种大巴车身总拼方法,包括:
(1)准备:根据生产车型调出控制系统已存储车型数据(新车型可手动输入车型数据并存储),腰梁定位夹紧机构自动调整z轴方向位置,裙部立柱定位机构自动调整y轴方向位置,窗立柱夹紧机构自动调整y轴、z轴方向位置;
(2)吊装车身侧围:用桁车同时吊装车身左右两侧骨架,放置在总拼设备的定位点上,同时进行侧围骨架x方向的定位,启动腰梁定位夹紧机构、窗立柱定位夹紧机构分别对车身两侧的骨架夹紧;
(3)车身底座就位:通过地拖链将车身底座抬升输送至总拼工位;
(4)侧围合装:两侧桁架架体带动侧围骨架沿y轴方向合拢至控制系统设定的位置,人工调节车身底座位置,至架体合拢到位,锁紧焊接;
(5)前围拼装:用桁车吊装前围骨架到总拼设备的前围定位机构位置上,微调前围z向高度,调整到位后,人工夹紧前围与侧围立柱,进行焊接。
(6)顶盖总成安装:通过桁车将顶盖骨架总成运送到车身骨架上方,采用顶盖脱钩装置将顶盖落位至车身骨架上,进行焊接。
(7)后围拼装:用桁车吊装后围骨架到总拼设备的后围z向定位装置上,微调后围z向高度,调整到位后,人工夹紧后围与侧围立柱,进行焊接。
(8)合拼设备侧围夹紧装置打开,架体锁紧装置打开,桁架退回原位,合拼后的车身骨架通过地拖链移至下一工位。
具体的,顶盖脱钩装置原理与腰梁定位夹紧机构类似,采用气缸211带动压臂,实现压臂54张开与卡紧,顶盖脱钩装置安装在支座51上。
通过采用上述的技术方案,此设备可实现6m-13.6m各种不同规格大巴车身快速、精确、稳定、安全的柔性化切换生产,并可兼容后续新开发车型。系统定位精度高,确保车身合拢拼装的质量的同时大幅度提高生产效率。
本说明书中各个实施例采用递进的方式描述,每个实施例重点说明的都是与其他实施例的不同之处,各个实施例之间相同相似部分互相参见即可。对于实施例公开的装置而言,由于其与实施例公开的方法相对应,所以描述的比较简单,相关之处参见方法部分说明即可。
对所公开的实施例的上述说明,使本领域专业技术人员能够实现或使用本发明。对这些实施例的多种修改对本领域的专业技术人员来说将是显而易见的,本文中所定义的一般原理可以在不脱离本发明的精神或范围的情况下,在其它实施例中实现。因此,本发明将不会被限制于本文所示的这些实施例,而是要符合与本文所公开的原理和新颖特点相一致的最宽的范围。
起点商标作为专业知识产权交易平台,可以帮助大家解决很多问题,如果大家想要了解更多知产交易信息请点击 【在线咨询】或添加微信 【19522093243】与客服一对一沟通,为大家解决相关问题。
此文章来源于网络,如有侵权,请联系删除


