一种旋转装卸货的驮背运输系统的制作方法



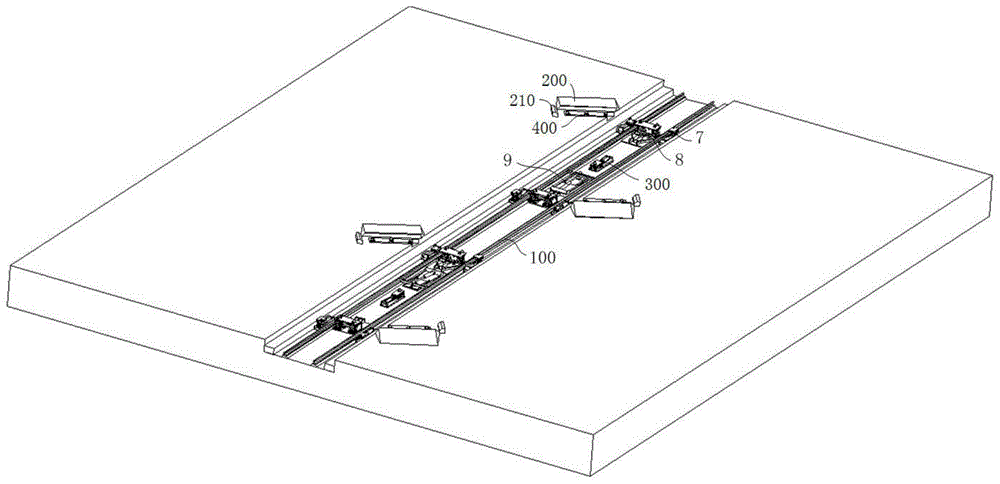
本实用新型涉及驮背车技术领域,具体涉及一种旋转装卸货的驮背运输系统。
背景技术:
驮背运输是指公路货车或半挂车等公路车辆装载货物后在始发地火车站自行开上驮背车,并通过铁路完成长距离运输,在到达目的地火车站后,公路车辆可自行开下驮背车并驶往最终目的地的一种便捷运输方式。
驮背车的车体一般可以包括本体部和可分离的托部,在装卸车时,可以先将托部自本体部旋转并分离出来,以方便公路车辆的开上、开下,在装卸车完成后,可以再将托部安装于本体部。
在这个过程中,如何实现托部和本体部的分离,仍是本领域技术人员亟待解决的技术问题。
技术实现要素:
本实用新型的目的是提供一种旋转装卸货的驮背运输系统,实现旋转装卸货,并可简化驮背车的车体结构,有利于实现车体轻量化,并降低成本。
为解决上述技术问题,本实用新型提供一种旋转装卸货的驮背运输系统,包括驮背车和地面设备,所述驮背车包括车体,所述车体包括本体部和托部;所述本体部包括至少一个本体单元,所述本体单元包括两个端部架,两所述端部架之间设有一个可分离的所述托部;所述地面设备包括转动装置、两组端部架举升部、托部举升部和设于轨道外的两组斜坡过渡装置;两组所述端部架举升部能够分别举升所述托部两端的所述端部架;所述托部举升部能够举升所述托部,使所述托部与两所述端部架脱离;所述托部与所述端部架处于脱离状态时,所述转动装置能够驱动所述托部绕其回转轴线转动,且当所述托部转动至预设角度时,所述托部的两端能够分别与两组所述斜坡过渡装置衔接。
当驮背车达到装卸车站场的预设位置后,托部前后两个端部架的下方分别设有一组端部架举升部,托部的下方设有托部举升部,先通过两组端部架举升部从托部的两端同时将端部架和托部一同举升,直至转向架心盘不再受力的位置后,端部架举升部保持其作用位置不变,再通过托部举升部向上举升托部、使其与端部架脱离,然后托部举升部保持其作用位置不变,最后通过转动装置作用于托部使其绕其回转轴线转动至预设角度,并且两端分别与斜坡过渡装置衔接后,斜坡过渡装置能够在地面和托部之间形成过渡连接,便于装卸车的进行。
采用这种方案,端部架举升部、托部举升部和转动装置等均为设于装卸车站场的地面设备,使得旋转式驮背车的车体无需设置相应的举升部和转动装置,如此一来,在实现旋转装卸货的同时,可简化驮背车的整体结构,进而减轻其自身的重量、提高经济性。并且,一套设于装卸车站场的各设备能配合经过该轨道的不同的旋转式驮背车装卸车,提高其适用性,进一步降低成本。
附图说明
图1为地面设备的结构示意图;
图2为图1的俯视图;
图3为本实用新型所提供旋转装卸货的驮背运输系统的正视图;
图4为图3的俯视图;
图5为托部转动一定角度后的结构示意图;
图6为托部转动至预设角度后的结构示意图;
图7为驮背车的车体的结构示意图;
图8为托部结构示意图;
图9为图8的分解视图;
图10为图9中上部勾处的局部放大图;
图11为图10的正视图;
图12为图9中a处的局部放大图;
图13为图9中b处的局部放大图;
图14为端部墙体的结构示意图;
图15为图14在另一视角下的结构示意图;
图16为中部墙体和斜墙体的连接结构图;
图17为图16在另一视角下的结构示意图;
图18为两个端部底架安装于转向架并相互连接的结构图;
图19为端部底架本体和端部连接机构的结构图;
图20为图19中结构安装于转向架并与托部相连的侧视图;图21为图19的分解视图;
图22为图19中端部纵向支撑件的放大图;
图23为图19中端部横向限位件的放大图;
图24为图19中第一组成的放大图;
图25为图19中第二组成的放大图;
图26为图19中第三组成的放大图。
图27为图19中第三纵梁和第四纵梁的放大图;
图28为图19中第一枕梁和第二枕梁的放大图;
图29为图19中一个端部旁承的放大图;
图30为图19中一个集装箱锁座的放大图;
图31为图19中一组补强板件的放大图;
图32为关节底架的结构图;
图33为图32安装于转向架并与托部相连的侧视图;
图34为图32中一个关节底架分部的结构图;
图35为图34的另一视角图;
图36为图32中另一个关节底架分部的结构图;
图37为图34的分解视图;
图38为图37中关节纵向支撑件的放大图;
图39为图37中关节横向限位件的放大图;
图40为图37中第一组成的放大图;
图41为图37中第二关节横梁和第三关节横梁的放大图;
图42为图37中一个关节旁承的放大图;
图43为图37中一组补强板件的放大图;
图44为第一种锁闭机构安装于端部连接钩的结构图;
图45为端部连接钩、托部以及第一种锁闭机构在锁定状态下的结构图;
图46为图45的侧视图;
图47为图45在解锁状态下的侧视图;
图48为第一锁体和第一锁闭驱动梁组件的连接结构图;
图49为图48的分解视图;
图50为第一限位部、第二限位部以及第一导向套固定于端部连接钩的结构图;
图51为第二种锁闭机构安装于端部连接钩的结构图;
图52为端部连接钩、托部以及第二种锁闭机构在锁定状态下的结构图;
图53为端部连接钩、托部以及第二种锁闭机构在解锁状态下的结构图;
图54为第二导向套、第四限位部、旋转支撑体固定于端部连接钩的结构图;
图55为第二推梁与连梁单元、第二锁体的连接结构图;
图56为第二连接套的结构示意图;
图57为转接块的结构示意图;
图58为锁头的结构示意图;
图59为第二锁体的结构示意图;
图60为旋转支撑体的结构示意图
图61为第一种横向止挡机构安装于端部连接钩的结构图;
图62为第一种横向止挡机构一种具体实施方式的结构图;
图63为图62的分解视图;
图64为支座的结构示意图;
图65为第一连梁的分体结构图;
图66为第一种横向止挡机构另一种具体实施方式的结构图;
图67为图66中第一止挡梁与连接端部的连接结构的分解视图;
图68为第二种横向止挡机构在止挡状态下与端部连接钩、托部的相对位置图;
图69为图68的局部放大图;
图70为第二种横向止挡机构在解挡状态下与端部连接钩、托部的相对位置图;
图71为图70的局部放大图;
图72为第二种横向止挡机构安装于端部连接钩的结构图;
图73为图72的分解视图;
图74为制动管防护装置的结构图;
图75为图74中c处的放大图;
图76为图74中d处的放大图;
图77为图74中e处的放大图;
图78为制动管防护装置在托部和本体部连接状态下的结构图;
图79为图78中圈内部分的放大图;
图80为制动管防护装置在托部和本体部分离状态下的结构图;
图81为图80中圈内部分的放大图;
图82为第一防护限位件和第二防护限位件设于支座的结构图
图83为第一枢接板的结构图;
图84为第二枢接板的结构图;
图85为防护隔板的结构图;
图86为管吊座板的结构图;
图87为管吊连接板结构图;
图88是端部架举升装置在最高位置的结构示意图;
图89是图88的透视图;
图90是端部架举升装置在最低位置的透视图;
图91是第一底座的结构示意图;
图92是第一支撑座的一种具体实施方式的结构示意图;图92a是第一支撑座的另一种具体实施方式的结构示意图;图93是第一推杆的结构示意图;
图94是第一摇杆的结构示意图;
图95是第一支撑杆的结构示意图;
图96是托部举升装置在最高位置的结构示意图;
图97是图96的透视图;
图98是托部举升装置在最低位置的透视图;
图99是第二底座的结构示意图;
图100是第二支撑座的结构示意图;
图101是推动件的结构示意图;
图102是第二推杆的结构示意图;
图103是第二摇杆的结构示意图;
图104是第三支撑杆的结构示意图;
图105是纵向定位装置在最高位置的结构示意图;
图106是图105的主视图;
图107是纵向定位装置在最低位置的结构示意图;
图108是图107的主视图;
图109是第三底座的结构示意图;
图110是第三滑动座的结构示意图;
图111是纵向定位装置的局部结构示意图。
附图标记说明如下:
1本体部;
2端部底架,21端部底架本体、2101第一横梁、2102第二横梁、2103第一纵梁、2104第二纵梁、2105第三纵梁、2106第四纵梁、2107第一枕梁、2108第二枕梁、2109端部牵引梁、2110冲击座、2111集装箱锁座、2112端部旁承、2113补强板件、2114鞍座安装座、2115缓冲器安装座,22端部连接机构、221端部连接钩、221a端部凹槽、221b端部钩主体、221b-1端部钩分体、221b-2端部容纳腔、221c端部钩壁板、221d端部第一连接孔、221e端部第二连接孔、222端部纵向支撑件、222a端部纵向支撑主体、222b端部磨耗板、223端部横向限位件、223a端部横向限位槽、223b左导引面、223c右导引面;
3关节底架、3a关节底架分部、31关节底架本体、3101第一关节横梁、3102第二关节横梁、3103第三关节横梁、3104第一关节纵梁、3105第二关节纵梁、3106关节牵引梁、3107第一关节地板、3108第二关节地板、3109关节旁承、3110补强板件、32关节连接机构、321端部连接钩、321a端部凹槽、321b关节钩主体、321b-1关节钩分体、321b-2关节容纳腔、321c关节钩壁板、321d关节第一连接孔、321e关节第二连接孔、322端部纵向支撑件、322a端部纵向支撑主体、322b关节磨耗板、323端部横向限位件、323a关节横向限位槽、323b左导引面、323c右导引面、33关节、34关节轴承;
4托部、41底墙、411中部墙体、411a纵向梁、411a-1平梁段、411a-1a平板、411a-1b加强梁、411a-2格栅梁段、411a-2a小横梁、411a-2b连接板、411b横向梁、411b-1旋转中心插接部、411b-2纵向定位块、412端部墙体、412a主体部分、412b连接部分、412b-1立板部、412b-2侧板部、412b-3倾斜板部、412c下部圆轴、412d压板、413斜墙体、42侧墙、421上部勾、421a顶面段、421b侧面段、421c磨耗板、422导向限位件、423加强结构、423a中立板、423b端立板、423c外侧板、423d内侧板、423e缺口槽;
5锁闭机构、51第一锁体、511锁定端部、512第一限位端部、513安装槽、514第二限位端部、52第三铰轴、521锁闭安装板、522螺栓、53第一限位部、54第一锁闭驱动梁组件、541第一推梁、541a第一连接套、541b第一弹性件、541c第一支撑件、542第一导向套、543传动梁、55第二限位部;
51′锁头、511′锁定部、512′支撑部、513′弧形缺口、514′支撑槽、52′第二锁体、521′插入段、522′滑槽、523′大尺寸支撑段、524′小尺寸支撑段、53′第二锁闭驱动梁组件、531′第二推梁、531a′第二连接套、531b′第二弹性件、531c′第二支撑件、532′第二导向套、533′连梁单元、533a′第一锁闭连梁、533b′第二锁闭连梁、533c′转接块、533c-1′固定铰接点、533c-2′第一铰接点、533c-3′第二铰接点、54′旋转支撑体、541′旋转轴部、542′第三限位部、543′滑轨、55′第四限位部;
6横向止挡机构、61支座、611过孔、612安装孔、613止挡连接板、614护板、615止挡上盖板、62第一止挡梁、621粗颈部、622细颈部、623台阶面、624第一防松件、63止挡驱动梁组件、631第一连梁、6311第一驱动端部、6312连接端部、631a长板件、631a-1条形导向孔、631b短板件、631b-1穿过孔、631c滚轮、631d滚轴、631d-1杆部、631d-2头部、631d-3锁紧螺母、631e条形导向槽、631f锁紧件、631g第一垫片、632第二连梁、633第一铰轴、633a安装板、634第二铰轴、64第三弹性件、65止挡限位件;
61′第二止挡梁、611′驱动端部、612′止挡端部、613′铰接轴、613a′大径段、613b′小径段、613c′第三限位件、613d′第二垫片、62′限位梁、63′第一限位件、64′第二限位件、65′第四弹性件;
7端部架举升装置、71第一底座、711第一滑道、712第一销座、713第一滚板、72第一支撑座、721第二滑道、731第一驱动件、732第一锁定组件、733第一推杆、7331第一段、7332第二段、7333第一折弯、7334第一v字型连接件、7335第一滚轮、734第一摇杆、7341第一凹缺口、7342第一轴孔、74第一支撑组件、741第一支撑杆、7411第一加强套、742第二支撑杆、75第一上滑动轴、751第一滚套、76第一下滑动轴、77第一解锁部、78第二解锁部;
8托部举升装置、81第二底座、811第三滑道、812第二销座、813第二滚板、82第二支撑座、821第四滑道、822安装架、831第二液压缸、8311第二活塞杆、832第二锁定组件、833第二推杆、8331第三段、8332第四段、8333第二折弯、8334第二v字型连接件、8335第二滚轮、834第二摇杆、8341第二凹缺口、8342第二轴孔、835推动件、8351驱动端、8352动作端、8353推动杆、84第二支撑组件、841第三支撑杆、8411第二加强套、842第四支撑杆、85第二上滑动轴、851第二滚套、86第二下滑动轴、87驱动轮;
9纵向定位装置、91第三底座、911第五滑道、92第三滑动座、921第一铰接座、922滑块、93第三液压缸、931第三活塞杆、94升降部、95定位部、951横梁、9511第二铰接座、952定位块、953第三滚轮、954抵接板、96摆杆、97限位部、971第一连杆、972第二连杆;
10制动管防护装置、11防护壳体、111c形防护梁、112防护封板、113管吊组件、1131防护隔板、1132管吊座板、1133管吊连接板、12防护连接件、12a防护内端部、12b防护外端部、12c防护转接部、12d防护过孔、121第一枢接板、122第二枢接板、123枢接转轴、1231限位销、124固定轴、125防护滚轮、13第一防护限位件、14磁性件、15第二防护限位件;
20制动管、201法兰接头;
100轨道、200斜坡过渡装置、210限位挡、300旋转定位装置、400转动装置、410主动轮、420从动轮。
具体实施方式
为了使本领域的技术人员更好地理解本实用新型的技术方案,下面结合附图和具体实施例对本实用新型作进一步的详细说明。
本文中所述“若干”是指数量不确定的多个,通常为两个以上;且当采用“若干”表示某几个不见的数量时,并不表示这些部件在数量上的相互关系。
本文中所述“第一”、“第二”等词,仅是为了便于描述结构相同或相类似的两个以上的结构或部件,并不表示对顺序的某种特殊限定。
本文中,以铁路轨道的延伸方向为纵向,纵向也即前后方向;在铁路轨道的安装平面内,与该纵向相垂直的方位横向,横向也即左右方向;与该安装平面相垂直的方向可以称之为竖向、垂向,竖向、垂向也即上下方向。
请参考图1-6,图1为地面设备的结构示意图,图2为图1的俯视图,图3为本实用新型所提供旋转装卸货的驮背运输系统的正视图,图4为图3的俯视图,图5为托部转动一定角度后的结构示意图,图6为托部转动至预设角度后的结构示意图。
如图1-6所示,本实用新型实施例提供了一种旋转装卸货的驮背运输系统,包括驮背车和地面设备,驮背车包括车头、车体以及与车体相连接的转向架等,其中,车体包括本体部1和托部4,本体部1包括至少一个本体单元,每一个本体单元均可以包括两个端部架,两端部架之间可以设有一个可分离的托部4。
地面设备包括转动装置400、两组端部架举升部、托部举升部和两组斜坡过渡装置200,其中,两组斜坡过渡装置200设于轨道100外的侧站台。两组端部架举升部分别设于托部4两端的端部架的下方,用于对托部4两端的端部架同时举升,使端部架带动托部4向上移动直至转向架的心盘不再受力;托部举升部设于托部4的下方,用于举升托部4、使托部4与端部架脱离;转动装置400用于当托部4与端部架脱离后,驱动托部4绕其回转中心转动至预设角度使托部4的两端能够分别两组斜坡过渡装置200衔接。
详细的讲,结合图3-6,当驮背车达到装卸车站场的预设位置后,托部4前后两个端部架的下方分别设有一组端部架举升部,托部4的下方设有托部举升部,先通过两组端部架举升部从托部4的两端同时将端部架和托部4一同举升,直至转向架心盘不再受力的位置后,端部架举升部保持其作用位置不变,再通过托部举升部向上举升托部4、使其与端部架脱离,然后托部举升部保持其作用位置不变,最后通过转动装置400作用于托部4使其绕其回转轴线转动至预设角度,并且两端分别与斜坡过渡装置200衔接后,斜坡过渡装置200能够在地面和托部4之间形成过渡连接,便于装卸车的进行。
本实施例中,端部架举升部、托部举升部和转动装置400等均为设于装卸车站场的地面设备,使得驮背车的车体无需设置相应的举升部和转动装置400,如此一来,在实现驮背车旋转装卸货的同时,可简化驮背车的整体结构,进而减轻其自身的重量、提高经济性。并且,一套设于装卸车站场的各设备能配合经过该轨道100的不同的旋转式驮背车装卸车,提高其适用性,进一步降低成本。
在上述实施例中,该地面设备还包括旋转定位装置300,该旋转定位装置300设于轨道100内,其包括升降机构和设于升降机构顶端的定位轴,托部4的下端面沿其回转轴线设有与定位轴相适配的旋转中心插接部411b-1(具体结构参见后文描述)。
当驮背车行驶至预设位置后,托部4的旋转中心插接部411b-1刚好与设于轨道100内的旋转定位装置300的定位轴相对应,定位轴位于旋转中心插接部411b-1的正下方,通过端部架举升部举升,再通过托部举升部举升托部4使其与端部架脱离后,启动旋转定位装置300的升降机构升降定位轴,使得定位轴上升至与旋转中心插接部411b-1配合,定位轴即为托部4的回转轴,然后通过转动装置400作用于托部4使其绕定位轴转动至预设角度并与斜坡过渡装置200衔接。
在装卸车结束后,转动装置400作用于托部4使其绕定位轴反向转动,直至托部4回转预设角度至端部架的上方,然后驱动升降机构使得定位轴下降至原位以不再与托部4作用,再通过托部举升部作用使得托部4下降并与端部架配合,最后通过端部架举升部作用使得端部架带动托部4下降至与转向架配合即可。
或者,本实施例中,还可以直接在驮背车的本体部设置回转轴,例如,可以在托部4的下方设置与两个端部架相固定的纵连支架,回转轴可以设于该纵连支架,这样,也能够实现托部4的旋转。比较而言,前述通过在装卸车站场设置旋转定位装置300的方案,托部4仅需设置相应的旋转中心插接部411b-1即可,车体无需设置回转轴,且不需要上述的纵连支架,驮背车的车体结构可以进一步地简化,更有利于实现轻量化,为本实用新型实施例的优选方案。
上述旋转定位装置300可以设置在靠近托部4纵向中心的区域,也可以设置在靠近托部4纵向两端部的区域,或者还可以设置在其他位置,只要能够实现托部4绕定位轴的转动即可。
在上述实施例中,该地面设备还包括设于地面的限位挡210,托部4转动至与限位挡210抵接时,说明该托部4已经转动了上述预设角度,此时,该托部4的两端能够分别与设于地面的斜坡过渡装置200衔接,可进行装卸车操作。或者,本实施例中,还可以通过控制转动装置400的驱动作用使得托部4能够在转动预设角度后即可停止,而通过限位挡210对其转动角度进行限位的方案,可在简化整体结构的同时确保稳定性好。
以下本实用新型实施例将针对上述驮背运输系统的各装置的结构进行分别阐述。
托部举升部
请参考图96-104,图96是托部举升装置在最高位置的结构示意图,图97是图96的透视图,图98是托部举升装置在最低位置的透视图,图99是第二底座的结构示意图,图100是第二支撑座的结构示意图,图101是推动件的结构示意图,图102是第二推杆的结构示意图,图103是第二摇杆的结构示意图,图104是第三支撑杆的结构示意图。
在上述实施例中,托部举升部的数量可以为两组,两组托部举升部可以分别作用于托部4的纵向两端部,这样,对于托部4的举升可以更为可靠,当然,托部举升部的数量并不局限于两组,也可以为一组或者三组以上。
每组托部举升部均可以包括设于轨道100内的托部举升装置8,如图96-98所示,该托部举升装置8包括第二底座81、第二支撑座82、支撑机构和驱动机构,其中,支撑机构连接于第二底座81和第二支撑座82之间,驱动机构能够作用于支撑机构以升降第二支撑座82。
本实施例中,第二支撑座82的上端面还设有旋转驱动部,该旋转驱动部为转动装置的一部分,包括驱动轮87,驱动轮87的数量可以为两个以上,以提高驱动的稳定性,驱动轮87的上端面与托部4的下端面抵接、并可推动托部4绕其回转轴线转动。每个举升装置包括至少两个驱动轮87,各驱动轮87的轴线延长线均经过该托部4的回转中心,并沿托部4的下端面均匀设置,第二支撑座82的上端面设有用于安装驱动轮87的安装架822,同一举升装置的各驱动轮87用于从一端对托部4进行旋转驱动,每个驱动轮87的上端面与托部4的下端面抵接,当驱动轮87转动时能够带动托部4的一端偏转,而两个举升装置的驱动轮87在两端同时向不同的方向(一端向左、另一端向右)转动时,能够从两端作用于托部4使其绕其回转轴线转动,具体的,回转轴线可以通过设于地面的回转轴形成,将回转轴与托部4的下端面配合,二者沿竖直方向不受力,托部4能够绕回转轴转动。
其中,驱动机构用于通过支撑机构驱动第二支撑座82升降,进而带动旋转驱动部升降并与托部4的下端面作用或脱离。详细的讲,当通过端部底架2的升降装置将端部底架2和托部4整体顶升至转向架的心盘不再受力后,通过本实施例所提供的托部举升装置8举升托部4,具体的,两个举升装置置于轨道100上,并分别从前后两端对托部4进行作用,第二支撑座82通过驱动机构的作用带动旋转驱动部上升至其能够与托部4配合作用,然后启动旋转驱动部,驱动托部4绕其回转轴线转动至适当角度即可与地面的斜面过渡装置配合,然后进行装卸操作。
也就是说,本实施例所提供的托部举升装置8,可在平稳地举升托部4至预设高度后,驱动托部4绕其回转轴线转动,易于实现托部4在被举升后相对于第二支撑座82之间转动,从而降低对后期用于转动托部4的转动装置400的要求,并且托部4在绕其旋转轴线转动时,该托部4和第二支撑座82之间通过驱动轮87形成滚动摩擦,进而可减小二者之间的磨损作用。
具体的,如图1所示,本实施例中的驱动轮87的数量为两个,还可以是三个或多个等间隔设置,保证两个举升装置能够从两端对托部4进行稳定的支撑和旋转驱动。
在上述实施例中,支撑机构包括设于第二支撑座82的下方并分别与各驱动轮87对应的支撑部。也就是说,每个驱动轮87的下方均对应设有一个支撑部,支撑部的数量不小于驱动轮87的数量,由于该举升装置通过驱动轮87与托部4的端部抵接从而对托部4进行举升,因此,驱动轮87所受压力较大,每个驱动轮87对应设有一个支撑部对其进行支撑,可在保证该举升装置整体结构的稳定性的同时,降低对第二支撑座82的强度要求。
在上述实施例中,第二底座81设有第三滑道811,第二支撑座82设有第四滑道821,支撑部包括两组对称设置的第二支撑组件84,该第二支撑组件84包括交叉设置的第三支撑杆841和第四支撑杆842两个支撑杆,其中,第三支撑杆841的顶端与第二支撑座82铰接,第三支撑杆841的底端可沿第三滑道811滑动,第四支撑杆842的底端与第二底座81铰接,第四支撑杆842的顶端可沿第四滑道821滑动,驱动机构能够作用于第二支撑组件84以改变第三支撑杆841和第四支撑杆842之间的夹角,从而改变第二支撑座82距离第二底座81的高度。
当驱动组件作用于第二支撑组件84使得第三支撑杆841和第四支撑杆842之间的夹角减小时,该第二支撑组件84的高度增大,从而带动第二支撑座82相对于第二底座81上升,进而将驮背车的托部4向上举升至预设高度(原位),即可通过旋转驱动部对托部4进行旋转驱动操作,而托部4装卸完成后,旋转驱动装置反向驱动托部4转动至原位,驱动组件作用于第二支撑组件84使得第三支撑杆841和第四支撑杆842之间的夹角增大,使第二支撑组件84的高度减小,从而带动第二支撑座82相对于第二底座81下降至托部4与端部底架2配合,然后再通过升降装置驱动端部底架2和托部4一同下降并与本体配合。或者,本实施例中,还可以将第二支撑组件84设置为剪刀叉或可伸缩的套管的结构,而将第二支撑组件84设置为两个交叉并可相对转动的支撑杆可简化整体结构。
在上述实施例中,驱动机构包括第二驱动件和第二锁定组件832,该第二驱动件设于第二底座81并提供动举升的力源,具体的,该第二驱动件能够作用于第二支撑组件84以改变两个支撑杆之间的夹角,当两个支撑杆之间的夹角达到最小即第二支撑座82上升至最高位置后,第二锁定组件832能够锁定两个支撑杆的相对位置,即保持第二支撑组件84的状态不变,使得第二支撑座82的高度位置稳定,避免由于第二驱动件发生突然失效等情况导致第二支撑座82跌落,从而保证该举升装置使用状态下能够对端部底架2提供稳定的支撑。
进一步的,上述第二锁定组件832包括第二推杆833和第二摇杆834,同时第二底座81还设有第二销座812,具体的,如图102所示,第二推杆833包括依次设置的第三段8331、第二折弯8333和第四段8332,其中,第二折弯8333与第二驱动件铰接,第三段8331的端部与第三支撑杆841的底端铰接并可沿第三滑道811滑动,第二摇杆834的一端与第四段8332的端部铰接,第二摇杆834的另一端与第二销座812铰接;第二驱动件能够作用于第二折弯8333并带动第二摇杆834绕第二销座812转动,进而带动第三支撑杆841的底端沿第三滑道811滑动,当两个之间的夹角达到最小时,第二折弯8333位于第二销座812的上方。
详细的讲,第二折弯8333的开口向下,第二摇杆834铰接于第四段8332和第二销座812之间,第二驱动件能够作用于第二折弯8333,并带动第二摇杆834绕其和第二销座812之间的铰接点转动,进而带动第二推杆833绕第二折弯8333和第二驱动件之间的铰接点转动,而第三段8331绕铰接点转动时能够带动第四支撑杆842移动,由于第三滑道811的限制,该第三支撑杆841的底端仅能够沿第三滑道811滑动,以实现两个支撑杆之间的夹角的改变。
当第三支撑杆741沿第三滑道711滑动至两个支撑杆之间的夹角最小使第二支撑座82上升至最高位置时,第二折弯8333刚好位于第二销座812的上方,第二驱动件不再作用,此时,若第二驱动件发生故障导致其推力不足时,该第二驱动件对第二支撑组件84的驱动作用撤除,而托部4仍继续下压第二支撑座82,并使两个支撑杆之间的角度有增大的趋势,由于第二折弯8333的开口向下并位于第二销座812的正上方,此时,竖直向下的压力无法将第二推杆833横向移动,进而限制了第二摇杆834的转动以及第三支撑杆841沿第三滑道811的滑动,从而可保持各第二支撑组件84的状态不变,即两个支撑杆之间的夹角不变、第二支撑座72的高度不变,稳定性更好。
通过上述锁定装置的设置,可使得当第二驱动件通过第二支撑组件84使得第二支撑座82升至最高位置时能够实现各第二支撑组件84之间的自动锁定,此种状态下,竖直方向的力无法改变各第二支撑组件84的状态,仅有在需要将第二支撑座82下降时,通过第二驱动件提供反向作用力使得第二推杆833横向移动至第二折弯8333与第二销座812脱离时,可实现解锁并带动第三支撑杆841的底端沿第三滑道811反向移动直至第二支撑座82下降至最低状态(如图98所示)即可。该第二锁定组件832可在实现第二支撑座82的升降的同时实现锁定和解锁,无需额外提供锁定部件,可简化整体结构并简化操作,保证整体结构的稳定性和操作便捷性。
在上述实施例中,第二推杆833的第三段8331的端部设有连接轴,该连接轴套设有第二滚轮8335,如图99所示,第二底座81还设有第二滚板813,第二滚轮8335能够沿第二滚板813滚动。具体的,该第三段8331的端部可以是设有凹槽,连接轴设于凹槽的两侧壁之间,或者,还可以将该第二推杆833设置为包括两个并列设置的第二v字型连接件8334的结构,两个第二v字型连接件8334朝向第三段8331的端部之间设有上述连接轴,该连接轴外套设有第二滚轮8335(如图102所示)。
第二驱动件作用于第二折弯8333使第二推杆833绕第二折弯8333和第二驱动件之间的铰接点转动时,第二推杆833的第三段8331的端部能够通过第二滚轮8335与第二底座81的第二滚板抵接并滚动,从而使得第三支撑杆841的下端沿第三滑道811滑动时,第二滚轮8335沿第二底座81滚动,减小阻力的同时还能够减小第三段8331和第二底座81之间的摩擦磨损,保证使用寿命。并且,当第二滚板813发生磨损后对其进行更换,从而保证第二底座81的使用寿命。
在上述实施例中,如图103所示,第二摇杆834朝向第二销座812的一端设有第二凹缺口8341,且第二凹缺口8341的两侧壁以及第二销座812分别设有第二轴孔8342,第二销座812设于第二凹缺口8341内并通过穿过第二轴孔8342的销轴可旋转连接。或者,本实施例中,还可以将第二摇杆834的一端设于第二销座812的一侧并通过销轴连接,而第二摇杆834设有第二凹缺口8341且第二销座812位于第二凹缺口8341内,可使得二者连接的更稳定,避免发生偏斜卡滞的情况。
在上述实施例中,驱动机构还包括推动件835,第二驱动件为第二液压缸831,其中,推动件835包括驱动端8351和动作端8352,驱动端8351与第二液压缸831的第二活塞杆8311连接,动作端8352设有至少两个推动杆8353,各推动杆8353分别与各第二推杆733的第二折弯(7333)底端铰接。也就是说,推动杆8353的数量与支撑部和驱动轮87的数量相同,当驱动轮87的数量为两个时,该第二推杆833的动作端8352的两个推动杆8353呈u型结构(如图101所示),通过同一个第二驱动件同时驱动各支撑部作用并带动第二支撑座82升降,具体的,第二液压缸831的数量可以是一个也可以是两个或多个,在此不做具体限制,各第二液压缸831可通过推动件835同时对各第二支撑组件84进行作用,保证各第二支撑组件84能够同步举升,稳定性好。
当然,本实施例中,还可以将第二驱动件设置为电机、齿轮和齿条或者电机、丝杆和螺母,在此不做具体限制。而通过第二液压缸831驱动可使得整体结构更稳定。
在上述实施例中,该举升装置还包括第二上滑动轴85和套设于第二上滑动轴85外的第二滚套851,第二支撑座82的两侧通过对称设置的第二支撑组件84与第二底座81连接,第二上滑动轴85穿过对称设置的第二支撑组件84的第四支撑杆842的顶端,并可沿第三滑道811滑动,第二滚套851位于两个第四支撑杆842之间并与第二支撑座82抵接滚动。也就是说,第二支撑组件84与第二支撑座82之间通过第二滚套851作用以保证第二支撑组件84对第二支撑座82之间的支撑力,稳定性好,同时,该第二滚套851设于两个第四支撑杆842之间,还能够对二者进行限位避免二者之间的距离发生变化影响托部4的升降。
进一步的,该举升装置还包括第二下滑动轴86,第二下滑动轴86穿过对称设置的第二支撑组件84的第三支撑杆841的底端以及第二推杆833的第三段8331,并可沿第三滑道811滑动。通过第二下滑动轴86的设置可实现第三支撑杆841的底端可沿第三滑道811滑动,并且第三支撑杆841的底端与第二推杆833的第三段8331的端部铰接,可简化整体结构。
更进一步的,如图104所示,第三支撑杆841的底端两侧分别设有套设于第二下滑动轴86外的第二加强套8411。该第二加强套8411的设置能够增加第三支撑杆841的底端的结构强度的同时,还可对该第三支撑杆841的底端进行限位,减小其两侧分别与第二底座81及第二推杆833的第一端之间的间距,避免发生偏斜的情况,稳定性好。
在上述实施例中,第二底座81和第二支撑座82分别设有侧板,第三滑道811和第四滑道821均为设于侧板的长条孔。或者,本实施例中,还可以将第三滑道811和第四滑道821设置为滑轨或滑槽的结构,而长条孔的结构设置较为简单,可简化制作工艺。
在上述实施例中,转动装置400还可以包括两组动力轮组,这两组动力轮组能够从两端驱动托部4转动至预设角度,各动力轮组包括间隔设于底面的主动轮410和从动轮420,其中,如图4所示,主动轮410朝向靠近轨道100的一侧设置,也就是说,托部4在经过设于第二支撑座82上端面的驱动轮87作用使其相对于端部底架2绕其旋转轴线转动至一定角度(该一定角度小于上述预设角度)后,其外侧(朝向旋转方向的前侧)能够在驱动轮87的作用下转动至与主动轮410配合(如图5所示的状态),然后主动轮410可继续驱动该托部4绕其旋转轴线转动至从动轮420的上方,接着,托部4将在主动轮410的作用下继续转动至与驱动轮87脱离,直至转动上述预设角度与限位挡210抵接并与斜坡过渡装置200衔接(如图6所示的状态),当托部4转动至与驱动轮87脱离时,其下方至少有一个主动轮410和一个从动轮420,以保证托部4在旋转过程中,始终有至少两个滚轮(驱动轮包括主动轮410和从动轮420)从一端对其进行支撑,稳定性好。
或者,本实施例中,对于转动装置400的具体结构不做限制,如还可将其设置为推动装置,以从两端通过推拉托部4使其绕其旋回转轴线转动即可,而主动轮410和从动轮420的设置可在驱动托部4转动的同时从托部4的下方对其提供支撑,旋转定位装置300无需受力或仅承受较小的力,保证整体结构的稳定性。
请参照图7,图7为驮背车的车体的结构示意图。
如图7所示,驮背车的车体中,托部4的纵向两端均设有连接结构,其中,连接结构包括上部勾421和沿横向延伸的下部圆轴412c,端部架设有端部连接机构22,端部连接机构22包括端部连接钩221和端部纵向支撑件222,端部连接钩221形成朝上设置的钩口,组装状态下,下部圆轴412c能够挂靠于端部连接钩221的钩口,上部勾421能够卡装于端部纵向支撑件222。
采用这种结构,托部4的纵向两端与本体部1之间均可以存在上部勾421与端部纵向支撑件222、下部圆轴412c与端部连接钩221所形成的两个连接点,托部4与本体部1的连接可以更为可靠;且在分离时,通过对于本体部1的举升,本体部1、托部4还能够以下部圆轴412c的中轴线为旋转中心线进行相对转动,迫使上部勾421与端部纵向连接件222的连接处产生松动,进而可以方便托部4与本体部1的分离。
托部
请参考图8-17,图8为托部的结构示意图,图9为图8的分解视图,图10为图9中上部勾处的局部放大图,图11为图10的正视图,图12为图9中a处的局部放大图,图13为图9中b处的局部放大图,图14为端部墙体的结构示意图,图15为图14在另一视角下的结构示意图,图16为中部墙体和斜墙体的连接结构图,图17为图16在另一视角下的结构示意图。
如图8所示,并结合图10、图11,上部勾421与端部纵向支撑件222的卡装面可以包括顶面段421a和两个侧面段421b,以形成开口朝下的u型卡装面;两侧面段421b中,第一者可以为竖直面,第二者可以为自上而下沿远离第一者方向倾斜的倾斜面,或者,两侧面段421b均可以为自上而下沿远离对方的方向倾斜的倾斜面。
如此,卡装面可以形成自下而上逐渐缩小的锥形卡装口,这种形式的锥形卡装口可以方便上部勾421与端部纵向支撑件222的卡装,且卡紧效果会随着托部4与本体部1的靠近程度而增加,可形成越落越紧的连接特点;而且,由于锥形卡装口的下部开口较大,一旦上部勾421与端部纵向支撑件222的连接处产生松动,二者的分离可以较为容易。
需要说明,上述锥形卡装口的方案仅为本实用新型实施例的一种优选方案,并不能够作为对本实用新型所提供旋转装卸货的驮背运输系统的实施范围的限定,在具体实施时,两个侧面段421b也可以均设置为竖直面,这同样能够满足与端部架卡接安装的技术效果。
在托部4与端部架的安装、分离等过程中,上部勾421的卡装面与端部架之间会存在滑动摩擦、静摩擦等形式的摩擦力,有可能会对上部勾421造成磨损,为此,可以在两侧面段421b设置托部磨耗板421c,以通过托部磨耗板421c的磨损来代替对于上部勾421的直接磨损,这对于提高托部4的使用寿命具有积极效果。
请继续参考图11,各托部磨耗板421c可以通过螺钉等形式的连接件与侧面段421b相连,而托部4在安装、分离以及使用过程中,各托部磨耗板421c所受到的摩擦力的方向与上述连接件的轴向是相垂直的,这就会导致各连接件承受不必要的剪切力,长期使用条件下,这种剪切力会严重影响托部磨耗板421c的连接可靠性。实际上,即便托部磨耗板421c是通过焊接固定,焊缝处也会受到上述的剪切力。
针对此,本实用新型实施例在托部磨耗板421c和侧面段421b之间可以设有抗剪止挡结构,以通过该抗剪止挡结构来抵消托部磨耗板421c所承受的摩擦力,这样,各连接件(或者焊缝)在垂向上基本可以处于不受力的状态,连接的可靠性可以更高。
详细而言,该抗剪止挡结构可以设置在托部磨耗板421c上,如附图11中位于左侧的托部磨耗板421c,该托部磨耗板421c可以大致为l形,l形的横部可以与侧面段421b相抵,这样,作用于托部磨耗板421c的摩擦力可以通过横部作用在上部勾421上,从而可以消除上述的剪切力;或者,该抗剪止挡结构也可以设置在侧面段421b上,如附图11中位于右侧的侧面段421b,该侧面段421b可以设有缺口,托部磨耗板421c可以安装在该缺口内,并与缺口的顶壁相抵,进而可通过与顶壁的作用力来抵消托部磨耗板421c所承受的摩擦力,以最终消除剪切力。
结合图9,托部4可以包括底墙41和与底墙41相连的两个侧墙42,两侧墙42的纵向两端均可以设有上部勾421。
而且,侧墙42还可以设有导向限位件422,该导向限位件422具体可以设置在上部勾421上,其形状可以为板状,也可以为块状、柱状等,其主要用于和端部架的限位导向件(具体结构可以参见后文中有关本体部1的描述)相配合,以对托部4的安装进行导向,并能够形成托部4的横向限位。
举例说明,本体部1的限位导向件可以设有限位导向槽,自下而上,该限位导向槽可以包括等宽槽段和变宽槽段,这里的宽度是指横向尺寸,等宽槽段的宽度可以大体与导向限位件422相同,而变宽槽段的宽度则可以自下而上逐渐增加,这样,通过导向限位件422与变宽槽段的配合,可以对托部4的安装进行导向,以保证托部4安装位置的准确性,而当导向限位件422插入等宽槽段时,导向限位件422与等宽槽段的配合又能够对托部4进行横向限位。
侧墙42的外侧面还可以设有加强结构423,以提高侧墙42的强度,该加强结构423具体可以为加强筋、加强板等形式的加强部件,或者,在用于运输集装箱时,该加强结构423可以为集装箱锁的安装位,如此,可以省却单独设置的加强结构423,有利于简化侧墙42的结构。
结合图12、图13,在一种示例性的方案中,设置集装箱锁的安装位可以首先对侧墙42的上盖板进行改造,上盖板的外侧可以设置缺口槽423e,对应缺口槽423e的位置,可以分别在内外两侧设置内侧板423d和外侧板423c,以及连接内侧板423d、外侧板423c的中立板423a和端立板423b,这种形式的安装位对于侧墙42的加强效果明显,可以替代传统加强筋、加强板等形式的加强部件。
可以理解,上述关于集装箱锁安装位的具体结构的说明仅是针对一种特定集装箱锁的安装位的示例性描述,这并不能够代表所有形式的集装箱锁的安装位,在具体实施时,如果所需集装箱锁的结构发生变化,上述安装位的结构可以进行适应性的调整,这点可以参照现有技术,在此不做详细描述。
底墙41可以包括中部墙体411和位于中部墙体411纵向两侧的端部墙体412。如图14、图15所示,端部墙体412可以包括主体部分412a和连接部分412b,其中,连接部分412b可用于连接主体部分412a和侧墙42;在装卸货的过程中,由于公路车辆要不断地开上开下,公路车辆的车轮要频繁地碾压主体部分412a,为提高主体部分412a的强度和使用寿命,主体部分412a可以采用箱式结构,这一方面可以保证强度,另一方面又可以降低重量;下部圆轴412c可以安装在主体部分412a远离中部墙体411的一端。
连接部分412b可以为包括立板部412b-1和侧板部412b-2的c型板,这样,连接部分412b自身的强度可以较高,能够较大程度地保证主体部分412a和侧墙42的连接可靠性。而且,侧板部412b-2还可以包括由内向外逐渐向上倾斜的倾斜板段412b-3,结合图14,这种形式的倾斜板段412b-3可以对公路车辆的轮胎进行导向,以尽可能地保证公路车辆的轮胎在主体部分412a上滚动。
主体部分412a的横向两侧还可以设有压板412d,在托部4下落并安装在主体部时,该压板412d可以作为驱动件存在,以驱使制动管防护装置(图中未示出)旋转回位。
再如图16、图17所示,中部墙体411可以包括沿横向间隔设置的两个纵向梁411a,两纵向梁411a可以通过若干沿纵向间隔设置的横向梁411b相连。由于公路车辆的重量主要通过横向两侧的车轮来传递,采用上述结构的中部墙体411,即可以通过横向上间隔的两个纵向梁411a来分别承担横向两侧的车轮所传递的重力,而横向中间区域无需直接与车轮相接触的部分则可以采用若干相间隔的横向梁411b所组成的镂空结构,这对于减轻中部墙体411的重量具有积极效果。
当然,中部墙体411也可以采用一体式的墙体,这并不影响其对于公路车辆的承载功能。
每一个纵向梁411a均可以包括平梁段411a-1和格栅梁段411a-2,平梁段411a-1可以包括平板411a-1a和安装于平板411a-1a底部的若干加强梁411a-1b,加强梁411a-1b的结构形式可以多种多样,如附图所示的方案为横纵交错的梁体的组合,当然,也可以采用其他的结构,只要能够实现对平板411a-1a进行加强的技术效果即可;格栅梁段411a-2则可以包括若干沿纵向间隔设置的小横梁411a-2a,沿纵向相邻的两小横梁411a-2a之间可以通过连接板411a-2b进行连接。
采用这种设计,格栅梁段411a-2的相邻两小横梁411a-2a之间具有间隙,可以方便安装掩挡,以对公路车辆的车轮进行限位;而平梁段411a-1又可以作为半挂车支腿的停放位置,以便于和支腿底板相配合,进而可对半挂车的支腿进行可靠支撑。
需要指出,本实用新型实施例并不限定纵向梁411a、横向梁411b在中部墙体411横向上的占比,同时,也不限定平梁段411a-1和格栅梁段411a-2在纵向梁411a纵向上的占比,在具体实施时,本领域技术人员可以根据实际需要进行设置。
中部墙体411还可以设有纵向定位结构,具体来说,该纵向定位结构可以包括纵向定位块411b-2,并可以安装在横向梁411b上,纵向定位块411b-2可以设有v形或者其他形状的定位口,在驮背车开到指定站、并停靠时,地面上的定位设备(具体结构可以参照后文中的纵向定位装置9)可以与该定位口相作用,以对驮背车的纵向位置进行精准定位,更方便托部4的安装和分离。
托部4还可以设置有旋转中心插接部411b-1,该旋转中心插接部411b-1具体可以为孔型或者槽型,其安装位置可以在横向梁411b上,在驮背车开到指定站后,前述旋转定位装置300的定位轴可以插入旋转中心插接部411b-1内,进而可以作为托部4的旋转中心。
底墙41还可以包括由内向外逐渐向上倾斜的斜墙体413,斜墙体413位于中部墙体411的横向两侧,用于连接中部墙体411和侧墙42。该斜墙体413的作用与前述倾斜板部412b-3相类似,均可以用于对公路车辆的轮胎进行导向,以尽可能地保证公路车辆的轮胎停留在两个纵向梁411a上;在附图的方案中,斜墙体413的纵向两端可以与前述的倾斜板部412b-3相连。
本体部
基于上述形式的托部4,本实用新型实施例实际上并不限定驮背车的车体的本体部1的结构,只要能够具有前述的端部连接机构22,以与托部4纵向两端的连接结构相配合即可。
本实用新型实施例根据每一节车体所包括本体单元的数量,可以将车体分成两种形式:
其一,如图7所示,本体单元的数量可以为一个,本体单元可以包括两个端部架,这两个端部架的结构可以大致相同,以下称之为端部底架2,两端部底架2的下方分别可以设有一个转向架,两端部底架2均可以设有前述端部连接机构22,托部4可以安装在两端部底架2之间。
其二,本体单元的数量可以为多个,受轴重限制,同一节车体的本体单元的数量通常不会超过两个。以两个为例,本体单元的两个端部架分别为一个端部底架2和第一个关节底架分部3a,其中,两个本体单元的两个关节底架分部3a可以通过关节相连,以组合形成一个关节底架3,两关节底架分部3a可以位于两端部底架2之间,两端部底架2的下方分别设有一个转向架,两关节底架分部3a的下方可以共用一个转向架,两个托部4可以分别安装在相邻的端部底架2、关节底架分部3a之间;这样,可以更为充分地利用每一节车体的纵向长度,以使用较少数量的转向架来满足车体的载货需求,进而可以有效降低运输成本。
对于端部底架2,其可以包括上述的端部连接机构22,具体的结构形式以参照图18-25,图18为两个端部底架安装于转向架并相互连接的结构图,图19为端部底架本体和端部连接机构的结构图,图20为图19中结构安装于转向架并与托部相连的侧视图,图21为图19的分解视图,图22为图19中端部纵向支撑件的放大图,图23为图19中端部横向限位件的放大图,图24为图19中第一组成的放大图,图25为图19中第二组成的放大图,图26为图19中第三组成的放大图,图27为图19中第三纵梁和第四纵梁的放大图,图28为图19中第一枕梁和第二枕梁的放大图,图29为图19中一个端部旁承的放大图,图30为图19中一个集装箱锁座的放大图,图31为图19中一组补强板件的放大图。
如图18所示,当存在多节车体时,相邻的两车体可以通过两个端部底架2相连,图中,两个端部底架2通过车钩连接。并且,每个端部底架2下方都设有一个转向架,也就是说,一个端部底架2对应安装在一个转向架上。
结合图19,端部连接机构22连在端部底架本体21的后端,这里有关前后的定义主要是结合附图中的视角进行确定,实际上,由于每一节车体均包括两个对称设置的端部底架2,两个端部底架2的前后、左右的位置关系实际上是相反的,对此可以结合图18中有关前后左右的标注进行理解。
端部连接机构22包括端部连接钩221。端部连接钩221的钩口朝上,端部连接钩221的内钩面上设有沿横向延伸的端部凹槽221a。
如图20所示,连接状态下,托部4的下部圆轴412c安放于端部凹槽221a,受到来自端部凹槽221a的内表面的向上的支撑力,因而垂向得到了有效支撑,同时,端部凹槽221a的内表面还能够对下部圆轴412c起到一定的纵向限位作用。因此,该端部底架2与托部4具有较好的连接可靠性。而且,通过向托部4施加向上的举升力,即可使下部圆轴412c从端部凹槽221a中脱出,方便端部底架2与托部4的分离。
进一步的,如图19所示,端部连接机构22还包括端部纵向支撑件222,端部纵向支撑件222位于端部连接钩221的上方,具体可以是正上方,也可以是斜上方。
如图22所示,端部纵向支撑件222包括端部纵向支撑主体222a以及固定在端部纵向支撑主体222a的前端和后端的端部磨耗板222b。
如图8所示,托部4的端部设有上部勾421,上部勾421的钩口朝下。
如图20所示,连接状态下,端部纵向支撑主体222a伸入上部勾421的钩口,两者钩挂在一起,同时,前端的端部磨耗板222b与上部勾421的内钩面前侧抵接,后端的端部磨耗板222b与上部勾421的内钩面后侧抵接,从而对托部4起到纵向支撑作用。这样,可以进一步提升端部底架2与托部4的连接可靠性,且不会影响端部底架2与托部4的分离便捷性。
如图22所示,前端的端部磨耗板222b的上部相对下部向后倾斜,后端的端部磨耗板222b的上部相对下部向前倾斜。同时,端部凹槽221a的内表面形成端部导引面,该端部导引面与下部圆轴412c配合时能够导引安装时托部4的落入,而且,该端部导引面还能够与下部圆轴412c相配合,以导引托部4与本体部1的转动分离。
具体来说,在连接托部4与端部底架2时,上述端部导引面可以导引下部圆轴412c逐渐滑入端部连接钩221内,以导引托部4的安装,且在托部4不断下落时,端部纵向支撑主体222a与上部勾421的卡紧程度可以逐渐加大,这样,便于上部勾421牢固地钩住端部纵向支撑主体222a;分离托部4与端部底架2时,可以向端部底架2靠近后端的位置施加向上的举升力(图20中力f),举升到一定高度时,端部底架2在端部凹槽221a的内表面的导引作用下、以下部圆轴412c的中轴线为旋转中心进行逆时针转动,可使得端部纵向支撑主体222a与上部勾421解卡,从而可方便端部底架2与托部4的分离。简言之,如此设置,能够提升端部底架2与托部4的连接可靠性和分离便捷性。
图示方案中,端部纵向支撑主体222a的顶部为上小下大的梯形结构(参见图22),后端的端部磨耗板222b的高度位置低于前端的端部磨耗板222b的高度位置,这样,可以保证端部底架2能够顺利地产生如上的逆时针转动,而不会出现干涉。当然,避免干涉的结构不局限于此,可以在实际实施时合理调整。图22中,端部磨耗板222b与端部纵向支撑主体222a通过螺栓螺母连接,端部纵向支撑主体222a为中空结构,且底部设有长圆孔,这样,便于端部磨耗板222b的更换。
图示方案中,端部凹槽221a为圆柱形槽(参见图19),这样,其内表面与圆柱形的下部圆轴412c配合时能够起到上述导引作用,当然,实际实施时,端部凹槽221a不局限于圆柱形槽。
进一步的,如图19所示,端部连接机构22还包括端部横向限位件223,该端部横向限位件223即为设置在端部底架2上的与托部4的导向限位件422相配合的限位导向件,端部横向限位件223位于端部连接钩221的上方,具体可以是正上方,也可以是斜上方,并且,端部横向限位件223位于端部纵向支撑件222的前方,具体可以是正前方,也可以是斜前方。
如图23所示,端部横向限位件223包括端部横向限位槽223a。
结合图20,连接状态下,导向限位件422插于端部横向限位槽223a,端部横向限位槽223a的左侧槽壁和右侧槽壁分别位于导向限位件422的左右两侧,以限定导向限位件422的横向位置。这样,能够进一步提升端部底架2与托部4的连接可靠性。
图示方案中,端部横向限位槽223a的左侧槽壁上部和/或右侧槽壁上部可以分别形成左导引面223b和右导引面223c(参见图23),左导引面223b的上侧相对下侧向左倾斜,右导引面223c的上侧相对下侧向右倾斜,这样可以将导向限位件422导引到端部横向限位槽223a内。
图23中,端部横向限位件223由一块u形板和两块筋板组成,实际实施时,端部横向限位件223的结构不局限于此。
如图19和图21所示,端部底架本体21包括第一横梁2101、第二横梁2102、第一纵梁2103、第二纵梁2104、第三纵梁2105、第四纵梁2106、第一枕梁2107、第二枕梁2108、端部牵引梁2109、冲击座2110、端部旁承2112、鞍座安装座2114以及缓冲器安装座2115(见图26)。
如图19所示,第一横梁2101布置在第二横梁2102的前方、第一纵梁2103和第二纵梁2104分别固定在第一横梁2101的两端后侧,第三纵梁2105和第四纵梁2106分别固定在第二横梁2102的两端前侧,第一纵梁2103的后端以及第三纵梁2105的前端分别与第一枕梁2107的右端固定,第二纵梁2104的后端以及第四纵梁2106的前端分别与第二枕梁2108的左端固定,从而形成框架。端部牵引梁2109位于框架内部,端部牵引梁2109的前端与第一横梁2101固定、后端与第二横梁2102固定,第一枕梁2107的左端以及第二枕梁2108的左端分别与端部牵引梁2109的左右两侧固定。梁与梁之间的固定方式可以是焊接。冲击座2110固定在第一横梁2101的前侧,具体可以拉铆或者螺栓固定,冲击座2110处连接车钩,以承受车钩冲击。端部连接机构22固定于第二横梁2102,具体可以焊接固定。一个端部旁承2112固定于第一枕梁2107,另一端部旁承2112固定于第二枕梁2108,具体可以焊接固定。
如图24所示,第二横梁2102和端部连接钩221组成第一组成。图中,设有两个端部连接钩221,一个固定在第二横梁2102的左端下侧,另一个固定在第二横梁2102的右端下侧。结合图19,还设有两个端部纵向支撑件222,一个固定在第二横梁2102的左端后侧,另一个固定在第二横梁2102的右端后侧,还设有两个端部横向限位件223,一个固定在第二横梁2102的左端上侧,另一个固定在第二横梁2102的右端上侧。
如图25所示,第一横梁2101、第一纵梁2103和第二纵梁2104以及冲击座2110组成第二组成。
如图26所示,鞍座安装座2114以及缓冲器安装座2115固定在端部牵引梁2109的内部,组成第三组成。端部牵引梁2109包括平行布置的牵引上板和牵引下板,以及布置在两者之间的牵引腹板,牵引上板上设有供鞍座安装座2114露出的板口。
如图27所示,第三纵梁和第四纵梁的结构相同,均包括槽口朝上的槽形梁、盖设在槽形梁槽口上的盖板和横向穿设于槽形梁的圆管。
如图28所示,第一枕梁和第二枕梁的结构相同,均包括枕梁上板、枕梁下板、两个枕梁腹板以及两个枕梁隔板。
如图21所示,两个端部旁承的结构相同。如图29所示,端部旁承包括旁承底板、三个旁承立板,旁承调整垫板和旁承磨耗板。三个旁承立板连在旁承底板上方且三者呈工字形连接。旁承调整垫板连在旁承底板下方,旁承磨耗板连在旁承调整垫板下方,三者通过螺栓螺母垫圈连在一起。
进一步的,如图19所示,端部底架本体21还包括两个集装箱锁座2111。一集装箱锁座2111固定在第三纵梁2105、第一枕梁2107以及第二横梁2102上侧,另一集装箱锁座2111固定在第四纵梁2106、第二枕梁2108以及第二横梁2102上侧,具体可以焊接固定。图中,两个集装箱锁座2111的结构相同。
如图30所示,集装箱锁座2111包括水平布置的集装底板、连在集装底板左右两侧的纵向集装立板、连在两块纵向集装立板之间的三块横向集装立板,一块横向集装立板位于集装底板的端部,另两块横向集装立板位于集装底板的中部。中部的两块横向集装立板与集装底板之间设有筋板,筋板位于中部的两块横向集装立板之间。
进一步的,如图21所示,端部底架本体21还包括补强板件2113。图21中设有两组补强板件2113,一组连在第二横梁2102与第三纵梁2105之间,另一组连在第二横梁2102与第四纵梁2106之间。两组补强组件2113的结构相同。如图31所示,每组补强组件2113包括一块横向筋板和两块三角筋板。
关节底架3的结构与端部底架2存在一定的相似性,尤其是在端部连接机构22处,具体可以参照图32-43,图32为关节底架的结构图,图33为图32安装于转向架并与托部相连的侧视图,图34为图32中一个关节底架分部的结构图,图35为图34的另一视角图,图36为图32中另一个关节底架分部的结构图,图37为图34的分解视图,图38为图37中关节纵向支撑件的放大图,图39为图37中关节横向限位件的放大图,图40为图37中第一组成的放大图,图41为图37中第二关节横梁和第三关节横梁的放大图,图42为图37中一个关节旁承的放大图,图43为图37中一组补强板件的放大图。
如图32所示,关节底架分部3a包括关节底架本体31、关节连接机构32和关节33,关节连接机构32即为安装在关节底架3的端部连接机构3,其固定在关节底架本体31的后端、关节33固定在关节底架本体31的前端。需要说明的是,两个关节底架分部3a的相互靠近的一端为两者的前端,相互远离的一端为两者的后端。应用时,两个关节底架分部3a的关节33通过关节轴承连接,连接状态下,两个关节底架分部3a能够绕横向和垂向转动,以适应车辆转弯和走坡道时的柔性需求。
如图33所示,应用时,每个关节底架分部3a各连接一托部4,使相邻的两托部4通过关节底架3连接,两个关节底架分部3a下方设有一个转向架,也就是说,两个关节底架分部3a(一个关节底架3)对应安装在一个转向架上。
如图34和图36所示,两个关节底架分部3a的关节33的结构不同,一个关节底架分部3a的关节33设置为凹关节,另一个关节底架分部3a的关节设置为凸关节,连接状态下,凸关节伸入凹关节内,实现可转动地连接。
两个关节底架分部3a的关节连接机构32的结构相同、关节底架本体31的结构也相同,连接状态下,两者的关节连接结构32相对横向对称,两者的关节底架本体31也相对横向对称。下面先说明关节连接机构32的具体结构,再说明关节底架本体31的具体结构。
如图34所示,关节连接机构32包括关节连接钩321。关节连接钩321的钩口朝上,关节连接钩321的内钩面上设有沿横向延伸的关节凹槽321a。
如图33所示,连接状态下,托部4的下部圆轴412c安放于关节凹槽321a,受到来自关节凹槽321a的内表面的向上的支撑力,因而垂向得到了有效支撑,同时,关节凹槽321a的内表面还能够对下部圆轴412c起到一定的纵向限位作用。因此,该关节底架3与托部4具有较好的连接可靠性。而且,通过向托部4施加向上的举升力,即可使下部圆轴412c从关节凹槽321a中脱出,方便关节底架3与托部4的分离。
进一步的,如图34所示,关节连接机构32还包括关节纵向支撑件322,关节纵向支撑件322位于关节连接钩321的上方,具体可以是正上方,也可以是斜上方。
如图38所示,关节纵向支撑件322包括关节纵向支撑主体322a以及固定在关节纵向支撑主体322a的前端和后端的关节磨耗板322b。
如图8所示,托部4的端部上侧设有上部勾421,上部勾421的钩口朝下。
如图33所示,连接状态下,端部纵向支撑主体322a伸入上部勾421的钩口,两者钩挂在一起,同时,前端的关节磨耗板322b与上部勾421的内钩面前侧抵接,后端的关节磨耗板322b与上部勾421的内钩面后侧抵接,从而对托部4起到纵向支撑作用。这样,可以进一步提升关节底架3与托部4的连接可靠性,且不会影响关节底架3与托部4的分离便捷性。
如图38所示,前端的关节磨耗板322b的上部相对下部向后倾斜,后端的关节磨耗板322b的上部相对下部向前倾斜。同时,关节凹槽321a的内表面形成关节导引面,该关节导引面与下部圆轴412c配合时能够导引安装时托部4的落入,而且,该关节导引面还能够与下部圆轴412c相配合,以导引托部4与关节底架3的转动分离。
具体来说,在连接托部4与关节底架3时,上述关节导引面可以导引下部圆轴412c逐渐滑入关节连接钩321内,以导引托部4的安装,且在托部4不断下落时,关节纵向支撑主体322a与上部勾421的卡紧程度可以逐渐加大,这样,便于上部勾421牢固地钩住关节纵向支撑主体322a;分离托部4与关节底架3时,可以向关节底架3靠近后端的位置施加向上的举升力(图33中力f),举升到一定高度时,关节底架3在关节凹槽321a的内表面的导引作用下、以下部圆轴412c的中轴线为旋转中心进行转动,可使得关节纵向支撑主体322a与上部勾421解卡,从而方便关节底架3与托部4的分离。简言之,如此设置,能够提升关节底架3与托部4的连接可靠性和分离便捷性。
图示方案中,关节纵向支撑主体322a的顶部为上小下大的梯形结构(参见图38),后端的关节磨耗板322b的高度位置低于前端的关节磨耗板322b的高度位置,这样,可以保证关节底架分部3a能够顺利地产生如上绕横向的转动,而不会出现干涉。当然,避免干涉的结构不局限于此,可以在实际实施时合理调整。图38中,关节磨耗板322b与关节纵向支撑主体322a通过螺栓螺母连接,关节纵向支撑主体322a为中空结构,且底部设有长圆孔,这样,便于关节磨耗板322b的更换。
图示方案中,关节凹槽321a为圆柱形槽(参见图34),这样,其内表面与圆柱形的下部圆轴412c配合时能够起到上述导引作用,当然,实际实施时,关节凹槽321a不局限于圆柱形槽。
进一步的,如图34所示,关节连接机构32还包括关节横向限位件323,该关节横向限位件323即为设置在关节底架3上的与托部4的导向限位件422相配合的限位导向件,关节横向限位件323位于关节连接钩321的上方,具体可以是正上方,也可以是斜上方,并且,关节横向限位件323位于关节纵向支撑件322的前方,具体可以是正前方,也可以是斜前方。
如图39所示,关节横向限位件323包括关节横向限位槽323a。
如图33所示,连接状态下,导向限位件422插于关节横向限位槽323a,关节横向限位槽323a的左侧槽壁和右侧槽壁分别位于导向限位件422的左右两侧,以限定导向限位件422的横向位置。这样,能够进一步提升关节底架3与托部4的连接可靠性。
图示方案中,关节横向限位槽323a的左侧槽壁上部和/或右侧槽壁上部分别形成左导引面323b和右导引面323c(参见图39),左导引面323b的上侧相对下侧向左倾斜,右导引面323c的上侧相对下侧向右倾斜,这样可以将导向限位件422导引到关节横向限位槽323a内。
图39中,关节横向限位件323由一块u形板和两块筋板组成,实际实施时,关节横向限位件323的结构不局限于此。
如图34和图35所示,关节底架本体31包括第一关节横梁3101、第二关节横梁3102、第三关节横梁3103、第一关节纵梁3104、第二关节纵梁3105、关节牵引梁3106、第一关节地板3107、第二关节地板3108。
第一关节横梁3101布置在第二关节横梁3102和第三关节横梁3103后方、第一关节横梁3101的左端通过第一关节纵梁3104与第二关节横梁3102的左端固定,第一关节横梁3101的右端通过第二关节纵梁3105与第三关节横梁3103的右端固定,第二关节横梁3102的右端和第三关节横梁3103的左端分别与关节牵引梁3106的前端固定,从而形成关节框架;关节牵引梁3106的后端固定于第一关节横梁3101;梁与梁之间的固定方式可以是焊接。关节33固定在关节牵引梁3106的前端,具体可以是焊接固定。
第一关节地板3107和第二关节地板3108覆盖在关节框架的顶部框口并分别位于关节牵引梁3106的左右两侧,第一关节地板3107固定于第二关节横梁3102、第一关节纵梁3104和关节牵引梁3106,第二关节地板3108固定于第三关节横梁3103、第二关节纵梁3105和关节牵引梁3106,具体可以是焊接固定。
如图40所示,第一关节横梁3101和关节连接钩321组成第一组成。图中,设有两个关节连接钩321,一个固定在第一关节横梁3101的左端下侧,另一个固定在第一关节横梁3101的右端下侧。结合图34,还设有两个关节纵向支撑件322,一个固定在第一关节横梁3101的左端后侧,另一个固定在第一关节横梁3101的右端后侧;还设有两个关节横向限位件323,一个固定在第一关节横梁3101的左端上侧,另一个固定在第一关节横梁3101的右端上侧。
具体的方案中,第二关节横梁3102、第三关节横梁3103的结构相同,均包括底板、双腹板和设置在双腹板之间的隔板(参见图41)。第一关节纵梁3104和第二关节纵梁3105的结构相同,均为槽口朝上的槽形梁(参见图37)。第一关节地板3107和第二关节地板3108的结构相同,均为中心设有孔的板结构。关节牵引梁3106包括牵引上盖板和牵引下盖板以及设置在两者之间的牵引立板。
进一步的,如图34所示,关节底架本体还包括两个关节旁承3109,两个关节旁承3109分别位于关节33的左右两侧,一关节旁承3109固定在第二关节横梁3102的前侧,另一关节旁承3109固定在第三关节横梁3103的前侧。具体的方案中,两个关节旁承3109的结构相同。如图42所示,关节旁承包括旁承下盖板、旁承上盖板和设置在两者之间的旁承立板。
进一步的,如图34所示,关节底架本体31还包括补强板件3110。具体的方案中设有两组补强板件3110(参见图37),一组补强板件3110固定在第一关节地板3107与第一关节横梁3101之间,另一组所述补强板件固定在第二关节地板3108与第一关节横梁3101之间。如图43所示,每组补强组件3110包括一块横向筋板和两块三角筋板。
上述端部底架2、关节底架3均可以安装有锁闭机构5,该锁闭机构5可以实现垂向上托部4与本体部1的锁定或者解锁,锁闭机构5在端部底架2和关节底架3的安装位置相类似。
在端部底架2中,结合图24,端部连接钩221包括端部钩主体221b,端部钩主体221b包括两个沿横向间隔布置的端部钩分体221b-1以及形成在两个端部钩分体221b-1之间的端部容纳腔221b-2,锁闭机构4可以安装在该端部容纳腔221b-2内。图24中,端部连接钩221还包括包覆在端部钩主体221b外钩面的端部钩壁板221c,端部钩壁板221c设有端部第一连接孔221d,端部第一连接孔221d与端部容纳腔221b-2相通,以便解锁部件能够通过端部第一连接孔221d伸入所述端部容纳腔221b-2对锁闭机构进行解锁,解锁后,托部4方能与端部底架2分离。另外,图20中,端部连接钩221还设有端部第二连接孔221e。
在关节底架3中,关节连接钩321包括关节钩主体321b,关节钩主体321b包括两个沿横向间隔布置的关节钩分体321b-1以及形成在两个关节钩分体321b-1之间的关节容纳腔321b-2,锁闭机构5可以安装在该关节容纳腔321b-2内。图40中,关节连接钩321还包括包覆在关节钩主体321b外钩面的关节钩壁板321c,关节钩壁板321c设有关节第一连接孔321d,关节第一连接孔321d与关节容纳腔321b-2相通,以便解锁部件能够通过关节第一连接孔321d伸入所述关节容纳腔321b-2对锁闭机构进行解锁,解锁后,托部4方能与关节底架3分离。
由于锁闭机构在端部底架2和关节底架3的安装结构相类似,以下在有关锁闭机构具体结构的描述中,均是以安装在端部底架2为例进行阐述,且针对该锁闭机构5,本实用新型实施例提供了两种结构的锁闭机构5。
第一种锁闭机构5可以参照图44-50,图44为第一种锁闭机构安装于端部连接钩的结构图,图45为端部连接钩、托部以及第一种锁闭机构在锁定状态下的结构图,图46为图45的侧视图,图47为图45在解锁状态下的侧视图,图48为第一锁体和第一锁闭驱动梁组件的连接结构图,图49为图48的分解视图,图50为第一限位部、第二限位部以及第一导向套固定于端部连接钩的结构图。
如图44-46所示,该锁闭机构5包括:第一锁体51,第一锁体51通过第三铰轴52与端部连接钩221铰接,第一锁体51的一端部为锁定端部511,另一端部为第一限位端部512,第三铰轴52位于锁定端部511和第一限位端部512之间;第一限位部53,第一限位部53固定在端部容纳腔221b-2内(参见图50);
第一锁闭驱动梁组件54,与第一锁体51相连;
锁定状态下,如图46所示,第一限位端部512自上而下与第一限位部53相抵,锁定端部511与托部4相抵,以锁定托部4;解锁状态下,如图47所示,第一锁闭驱动梁组件54能够驱使第一限位端部512自下而上脱离第一限位部53、锁定端部511旋转脱离托部4。
采用这种结构,如图46、图47所示,在锁定时,如果托部4与端部连接钩221之间存在分离趋势,托部4会对锁定端部511产生向上的力,以驱使锁定端部511进行逆时针转动,而由于第一限位部53对第一限位端部512所产生的自下而上的支撑力,可阻挡第一锁体51沿逆时针方向的转动,从而可保证锁定端部511的位置不变,也就可以对托部4进行可靠锁定;在解锁时,第一锁闭驱动梁组件54能够驱使第一限位端部512自下而上脱离第一限位部53,第一锁体51可以进行顺时针转动,其转动方向与第一限位部53的止挡方向相反,锁定端部511与托部4可以顺利分离,能够实现托部4的顺利解锁,而不影响托部4与端部连接钩221的分离。
这里,本实用新型实施例并不限定第一限位部53的结构,其可以为板状,也可以为块状;同样地,本实用新型实施例也不限定第一限位部53的数量,其可以为一个,也可以包括多个相互独立的限位件,只要其能够实现上述的技术效果即可。
在一种详细的方案中,如图48所示,第一锁闭驱动梁组件54可以包括第一推梁541、第一导向套542和传动梁543,第一导向套542固定在端部容纳腔221b-2内(可以参照附图50),第一推梁541与第一导向套542可以滑动连接,传动梁543的一端可以与第一锁体51铰接,另一端与可以第一推梁541铰接。
如此,当第一推梁541受到驱动力向上移动时,铰接设置的传动梁543可以将第一推梁541的直线运动转换为第一锁体51的旋转运动,以向第一锁体51传递解锁的驱动力,可实现第一锁体51的解锁;而当驱动力消失时,依靠自身的重力等,第一推梁541又可以沿第一导向套542自动下滑,并带动第一锁体51的反向旋转,以实现第一锁体51的自动上锁,当然,也可以是由外部设备提供反向的驱动力来带动第一推梁541复位、锁定。
具体第一推梁541可以正对上述端部第一连接孔221d(参照图46和图47),以便解锁部件能够穿过端部第一连接孔221d与第一推梁541接触,从而向第一推梁541施加向上的解锁驱动力。
需要指出,本实用新型实施例并不限定第一推梁541在解锁时所受到的驱动力的来源,其可以采用手动驱动的方案,例如,可以设置解锁杆等解锁部件,当需要解锁时,可以由工作人员手动操作解锁部件,以对第一推梁541产生驱动力;或者,也可以采用自动驱动的方案,此时,动力源可以为电机、气缸、油缸等,这些动力源可以安装在车体上,也可以安装在地面设备上,具体可以根据实际情况进行选择,动力源与第一推梁541之间还可以设有传动机构,以传递动力源的驱动力。
第一推梁541位于第一导向套542上方的梁段还可以设有第一连接套541a,如图49所示,该第一连接套541a具体可以为u型板,u型板的底板部可以和第一推梁541相连,并能够与第一导向套542形成支撑,以作为第一推梁541向下移动的限位部件,传动梁543可以铰接在u型板的两个侧板部之间。
实际上,第一推梁541的下移限位也可以通过第一限位端部512和第一限位部53的配合来实现,如此,上述的第一连接套541a也可以不存在;或者,也可以采用传动梁543进行限位,传动梁543与第一推梁541采用的是铰连的方案,二者在实际工作过程中通常是呈夹角设置的,传动梁543同样能够作为第一推梁541向下移动的限位部件。
在上述的方案中,是通过传动梁543来将第一推梁541的直线运动转换为第一锁体51的旋转运动,事实上,除了这种方案之外,也可以采用其他的方案,例如,可以在第一锁体51上设置导向孔,第一推梁541可以铰接在该导向孔内,当第一推梁541产生轴向位移时,第一推梁541的铰接轴可以在导向孔内进行滑动,以自然地带动第一锁体51进行旋转,这样也能够实现直线运动向旋转运动的转换。
进一步地,该锁闭机构5还可以包括第一弹性件541b,该第一弹性件541b的一端可以与第一推梁541相作用,解锁过程为第一弹性件541b的变形量增加的过程,以集聚弹性力。如此设置,当作用于第一推梁541的驱动力消失后,第一弹性件541b的弹性力可以释放,以与第一推梁541自身的重力相配合,来共同驱动第一锁体51的复位、锁定。
具体而言,该第一弹性件541b可以为弹簧,其可以外套安装于第一推梁541,且第一推梁541的下端部可以设有第一支撑件541c,弹簧的两端可以分别与第一导向套542、第一支撑件541c相作用。其中,第一推梁541可以充当弹簧柱的作用,有利于防止弹簧在伸缩过程中的径向窜动,对于提高结构的稳定性、动力传动的可靠性均具有积极效果;且采用这种结构,在解锁状态下,第一推梁541可以向上位移,第一弹性件541b可以被压缩,而在恢复锁定时,第一推梁541可以向下位移,第一弹性件541b可以释放。
实际上,在锁定状态下,第一弹性件541b也可以有一定的预压缩量,也就是说,在锁定时第一弹性件541b仍可以提供一定的弹性力,这对于保证第一锁体51锁定状态的稳定具有积极效果,可避免轨道车辆通过曲线时第一锁体51的自动解锁。
为方便地调整该预压缩量,第一支撑件541c可以为螺母,这样,通过改变螺母拧接的位置,即可以调整第一支撑件541c和第一导向套542的间距,进而可以调整锁定状态下第一弹性件541b的预压缩量。
在解锁状态下,第一弹性件541b实际上也可以处于拉伸状态,此时,第一弹性件541b的安装位置可以发生变化,具体来说,其可以设置在第一连接套541a和第一导向套542之间,且其两端与第一连接套541a、第一导向套542均可以为固定连接,以便传递拉力。
第一锁体51可以设有安装槽513,传动梁543可以铰接在该安装槽513内,这样,该锁闭机构在传动梁543与第一锁体51的铰接轴的轴向上的厚度可以较小,整体结构可以更为紧凑。除此之外,上述的安装槽513也可以设置在传动梁543内,然后可以将第一锁体51铰接在传动梁543的安装槽513内;或者,也可以不设置安装槽513,此时,传动梁543与第一锁体51所形成的组合件在传动梁543与第一锁体51的铰接轴的轴向上的厚度会相对较大。
进一步地,该锁闭机构5还可以包括固定设置的第二限位部55,第二限位部55可以固定在端部容纳腔221b-2内,其结构等与第一限位部53可以相类似,在此不做重复性的描述;第一锁体51还可以包括第二限位端部514,锁定状态下,第二限位端部514可以自下而上与第二限位部55相抵。
如此,在锁定状态下,第一锁体51可以形成三点支撑的方案,第一锁体51的受力更为均衡,第一锁体51对于托部4的锁定更为可靠。
详细而言,第一锁体51可以包括呈夹角设置的两个锁臂,这两个锁臂可以大致形成l形,第三铰轴52可以设置在两锁臂的连接处,即l形的拐角处,其中,一个锁臂远离第三铰轴52的端部可以为锁定端部511,另一锁臂远离第三铰轴52的端部可以为第一限位端部512;两锁臂之间形成了一个小夹角(<180度)和一个大夹角(>180度),其中,小夹角所在侧为该连接处的内端部,大夹角所在侧为该连接处的外端部,该外端部即可以作为上述的第二限位端部514。
结合图46,在锁定状态下,第一限位部53可以对第一限位端部512产生自下而上的支撑力,第二限位部55可以对第二限位端部514产生自上而下的支撑力,再配合托部4对于锁定端部511产生的向上的推力,第一锁体51的受力可以更为平衡;而且,通过三个受力点的相互作用,第三铰轴52基本处于不受力的状态,这对于保证锁定机构的可靠性具有积极效果。
上述形式的锁闭机构5,除了第一导向套542、第一限位部53、第二限位部55所形成的安装支撑点外,第三铰轴52也可以作为一个安装支撑点,具体而言,可以结合图49,第三铰轴52的外壁可以设有插槽,插槽内可以设有锁闭安装板521(锁闭安装板521与第三铰轴52的连接方式也可以直接采用焊接),锁闭安装板521可以通过螺栓522等形式的连接件与端部连接钩221相连,当然,除了螺栓连接外,锁闭安装板521与端部连接钩221之间也可以通过焊接等方式进行固连。
第二种锁闭机构5的结构可以参照图51-54,图51为第二种锁闭机构安装于端部连接钩的结构图,图52为端部连接钩、托部以及第二种锁闭机构在锁定状态下的结构图,图53为端部连接钩、托部以及第二种锁闭机构在解锁状态下的结构图,图54为第二导向套、第四限位部、旋转支撑体固定于端部连接钩的结构图,图55为第二推梁与连梁单元、第二锁体的连接结构图,图56为第二连接套的结构示意图,图57为转接块的结构示意图,图58为锁头的结构示意图,图59为第二锁体的结构示意图,图60为旋转支撑体的结构示意图。
该锁闭机构5在锁定时,可以实现托部4与端部连接钩221在垂向上的锁定,以保证二者的可靠连接及行车安全,在解锁时,又不影响托部4与端部连接钩221分离的便捷性。
如图51-54所示,该锁闭机构5包括:锁头51′,锁头51′可转动地连于端部连接钩221,锁头51′在其旋转中心线的两侧分别设有锁定部511′和支撑部512′;第二锁体52′,第二锁体52′可滑动地连于端部连接钩221;第二锁闭驱动梁组件53′,与第二锁体52′传动连接;锁定状态下,第二锁体52′自下而上与支撑部512′相支撑,以使锁定部511′压紧托部;解锁状态下,第二锁闭驱动梁组件53′能够驱动第二锁体52′沿远离锁头51′的方向位移,支撑部512′能够绕旋转中心线向下转动,以使锁定部511′向上转动脱离托部。
采用这种结构,结合图52,在锁定状态下,如果托部与端部连接钩221产生分离趋势,托部会对锁定部511′产生向上的力,以驱使锁头51′进行逆时针转动,而由于第二锁体52′对于支撑部512′所产生的自下而上的支撑力,可阻挡锁头51′沿逆时针方向的转动,也就可以保证锁定部511′的位置不变,继而可对托部4进行可靠锁定;结合图53,在解锁时,第二锁闭驱动梁组件53′可以驱动第二锁体52′沿远离锁头51′的方向进行滑动,支撑部512′能够绕旋转中心线向下转动,锁定部511′可以向上转动,以解除对于托部的锁定,而不影响托部4与端部连接钩221的分离。
上述锁头51′的转动设置具体可以为铰接设置,此时,可以为锁头51′设置铰接轴,铰接轴可以固定于端部连接钩221,并位于锁定部511′和支撑部512′之间。或者,还可以设置旋转支撑体54′,该旋转支撑体54′可以固定于端部连接钩221,其上可以设有旋转轴部541′,旋转轴部541′具有弧形柱面,锁头51可以设有与旋转轴部541′相匹配的弧形缺口513′,这里的相匹配是指旋转轴部541′的外径与弧形缺口513′的内径大体一致。在装配时,锁头51′可以通过弧形缺口513′插装在旋转轴部541′,并能够以旋转轴部541′的中轴线作为旋转中心线进行转动,这样也可以实现锁头51′的转动设置。
在解锁时,锁头51′的转动可以依靠重心的偏置来实现,锁头51′的重心可以在纵向上偏离旋转中心线,并位于支撑部512′所在侧,具体而言,可以参照图52,弧形缺口513′可以设置在锁头51′重心的右侧,这样,当第二锁体52′向左位移时,锁头51′可以自然进行逆时针的转动,以解除对于托部的锁定。
和/或,也可以为锁头51′设置弹簧等形式的第三弹性件,在锁定状态下,该第三弹性件可以集聚拉伸力/压缩力等形式的弹性力,当第二锁体52′逐渐远离时,第三弹性件的弹性力可以释放,以驱使锁头51′自动进行转动解锁。比较而言,上述的两种方式均可以实现锁头51′在解锁时的自动转动,具体实施时,本领域技术人员可以根据实际需要进行选择。
结合图54,在具体装配时,旋转支撑体54′的数量可以为两个,这样,锁头51′可以架设在两个旋转支撑体54′上,锁头51′安装的稳定性更高,且两旋转支撑体54′之间的空间可用来插接第二锁体52′,锁头51′、第二锁体52′以及旋转支撑体54′的连接结构也可以更为紧凑。
再如图60所示,旋转支撑体54′还可以包括第三限位部542′,该第三限位部542′可以为角形等,在解锁状态下,第三限位部542′可以与支撑部512′相抵,以对支撑部512′的向下转动进行限位,同时,也可以支撑出第二锁体52′自支撑部512′下方插入的间隙,以便于第二锁体52′的再次插入,进而对支撑部512′进行支撑。
这里,本实用新型实施例并不限定第三限位部542′的支撑高度,在具体实施时,本领域技术人员可以根据实际需要进行设置,只要保证第三限位部542′与支撑部512′支撑时,锁定部511′可以对托部进行解锁、同时又预留了第二锁体52′的插入间隙即可。
进一步地,如图58所示,在锁头51′上还可以设有支撑槽514′,在解锁时,前述的第三限位部542′可以插接在支撑槽514′内。可以理解,第三限位部542′插入支撑槽514′的深度实际上也决定着解锁时支撑部512′的支撑高度,因此,在具体实践中,也可以通过调整支撑槽514′的深度来调整支撑部512′的支撑高度。
结合图59,第二锁体52′可以包括具有倾斜引导面的插入段521′,在进行锁定时,该插入段521′可以自支撑部512′的下方插入,并能够以倾斜引导面与支撑部512′相支撑,以逐步地带动支撑部512′向上转动、锁定部511′向下转动,并对托部进行锁定。
第二锁体52′可以仅包括该插入段521′,这种条件下,处于锁定状态时,第二锁体52′仍可以倾斜引导面与支撑部512′相支撑,而处于解锁状态时,第二锁体52′可以与支撑部512′完全脱离,也可以倾斜引导面与支撑部512′相支撑,也就是说,在解锁时,第二锁体52′与锁头51′也可以不完全脱离,此时,第二锁体52′自身也可以对锁头51′的转动形成限位,且由于锁头51′仍在第二锁体52′上,不存在第二锁体52′无法插入的问题,前述的第三限位部542′也可以不存在。
而在附图的方案中,仍以图59为参照,第二锁体52′可以包括三部分结构,分别为垂向尺寸较大的大尺寸支撑段523′、垂向变尺寸的插入段521′以及垂向尺寸较小的小尺寸支撑段524′,大尺寸支撑段523′具有第一支撑平面,小尺寸支撑段524′具有第二支撑平面,在锁定状态下,第二锁体52′可以通过第一支撑平面与支撑部512′相支撑,而在解锁状态下,第二锁体52′又可以通过第二支撑平面与支撑部512′相支撑。
由于与支撑部512′相支撑的面为平面,锁头51′在解锁以及锁定时的稳定性均可以较高;且基于上述设计,支撑部512′与第二锁体52′在解锁时并未完全脱离,小尺寸支撑段524′将自然形成支撑部512′的转动限位,前述的第三限位部542′也可以不存在。
作为附图59方案的变形,第二锁体52′也可以仅包括大尺寸支撑段523′(或者小尺寸支撑段524′)和插入段521′,这同样能够实现第二锁体52′的功能。
在第二锁体52′与旋转支撑体54′之间可以设有导向结构,用于导引第二锁体52′的滑动方向。
具体而言,在第二锁体52′、旋转支撑体54′中,一者可以设有滑槽522′,另一者可以设有与滑槽522′相匹配的滑动部,滑动部可以插接于滑槽522′,并能够沿滑槽522′进行滑动。该滑动部可以为一体式结构,如附图所示出的长条形的滑轨543′,或者,也可以为分体式结构,例如,可以包括若干间隔设置的滑块。
进一步地,还可以包括固定设置的第四限位部55′,第四限位部55′可以固定在端部容纳腔221b-2内,在锁定状态下,第四限位部55′能够自上而下与支撑部512′相抵紧。
如此,在锁定状态下,锁头51′可以形成三点支撑的方案,锁头51′的受力更为均衡,锁头51′对于托部的锁定可以更为可靠;而且,由于三个受力点的相互作用,弧形缺口513′和旋转轴部541′之间基本不存在力的作用,这对于保证锁闭机构的可靠性具有积极效果。
这里,本实用新型实施例并不限定第四限位部55′的结构,其可以为板状,也可以为块状;同样地,本实用新型实施例也不限定第四限位部55′的数量,其可以为一个,也可以包括多个相互独立的限位件,只要其能够实现上述的技术效果即可。
请参考图55,并结合图52、图53,在一种示例性的方案中,第二锁闭驱动梁组件53′可以包括第二推梁531′、第二导向套532′和连梁单元533′,第二导向套532′可以固定设置,具体可以是安装在端部容纳腔221b-2内(可以参照附图54),第二推梁531′与第二导向套532′可以滑动连接,连梁单元533′的一个端部与第二推梁531′铰接,另一端部与第二锁体52′铰接。
采用这种结构,当第二推梁531′受到驱动力向上移动时,铰接设置的连梁单元533′可以带动第二锁体52′向远离锁头51′的方向进行滑动,然后,锁头51′可自行转动解锁;而当驱动力消失时,依靠自身的重力等,第二推梁531′又可以沿第二导向套532′自动下滑,并通过连梁单元533′驱使第二锁体52′向靠近锁头51′的方向滑动,以再次对支撑部512′进行支撑,锁头51′可以反向旋转,以实现自动上锁,当然,也可以是由外部设备提供反向的驱动力来带动第二推梁531′复位、锁定。
具体第二推梁531′可以正对上述端部第一连接孔221d(参照图52和图53),以便解锁部件能够穿过端部第一连接孔221d与第二推梁531′接触,从而向第二推梁531′施加向上的解锁驱动力。
需要指出,本实用新型实施例并不限定第二推梁531′在解锁时所受到的驱动力的来源,其可以采用手动驱动的方案,例如,可以设置解锁杆等解锁部件,当需要解锁时,可以由工作人员手动操作解锁部件,以对第二推梁531′产生驱动力;或者,也可以采用自动驱动的方案,此时,动力源可以为电机、气缸、油缸等,这些动力源可以安装在车体上,也可以安装在地面设备上,具体可以根据实际情况进行选择,动力源与第二推梁531′之间还可以设有传动机构,以传递动力源的驱动力。
第二推梁531′位于第二导向套532′上方的梁段还可以设有第二连接套531a′,如图56所示,该第二连接套531a′具体可以包括管部和铰接部,管部能够通过螺纹连接、焊接、过盈配合等方式安装于第二推梁531′的上部,铰接部可以包括相对设置的两个铰接板,前述的连梁单元533′可以铰接在这两个铰接板之间。
上述的第二连接套531a′与第二导向套532′相配合还可以作为第二推梁531′向下移动的限位件,以限定第二推梁531′的最大下移距离,同时,也限定了第二锁体52′的位移距离。
实际上,第二推梁531′的下移限位也可以通过锁头51′与第四限位部55′的配合来实现,如此,上述的第二连接套531a′也可以不存在;或者,也可以采用连梁单元533′与第二推梁531′的连接端部进行限位,该连接端部与第二推梁531′采用的是铰连的方案,二者在实际工作过程中通常是呈夹角设置的,因此,即便不存在第二连接套531a′,该连接端部同样能够作为第二推梁531′向下移动的限位部件。
进一步地,还可以包括第二弹性件531b′,该第二弹性件531b′的一端可以与第二推梁531′相作用,在解锁状态下,第二弹性件531b′的变形量可以增加,以集聚弹性力。如此设置,当作用于第二推梁531′的驱动力消失后,第二弹性件531b′的弹性力可以释放,以与第二推梁531′自身的重力相配合,来共同驱动锁头51′的复位、锁定。
具体而言,该第二弹性件531b′可以为弹簧,其可以外套安装于第二推梁531′,且第二推梁531′的下端部可以设有第二支撑件531c′,弹簧的两端可以分别与第二导向套532′、第二支撑件531c′相抵。其中,第二推梁531′可以充当弹簧柱的作用,有利于防止弹簧在伸缩过程中的径向窜动,对于提高结构的稳定性、动力传动的可靠性均具有积极效果;且采用这种结构,在解锁状态下,第二推梁531′可以向上位移,第二弹性件531b′可以被压缩,而在恢复锁定时,第二推梁531′可以向下位移,第二弹性件531b′又可以释放。
实际上,在锁定状态下,第二弹性件531b′也可以有一定的预压缩量,也就是说,第二弹性件531b′在锁定时仍可以提供一定的弹性力,这对于保证锁头51′锁定状态的稳定具有积极效果,可避免轨道车辆通过曲线时锁头51′的自动解锁。
为方便地调整该预压缩量,第二支撑件531c′可以为螺母,这样,通过改变螺母拧接的位置,即可以调整第二支撑件531c′和第二导向套532′的间距,进而可以调整锁定状态下第二弹性件531b′的预压缩量。
在解锁状态下,第二弹性件531b′实际上也可以处于拉伸状态,此时,第二弹性件531b′的安装位置可以发生变化,具体来说,其可以设置在第二连接套531a′和第二导向套532′之间,且其两端与第二连接套531a′、第二导向套532′均可以为固定连接,以便传递拉力。
连梁单元533′可以是由多个连梁组合形成的结构,在一种示例性的方案中,该连梁单元533′可以包括第一锁闭连梁533a′、第二锁闭连梁533b′和转接块533c′,转接块533c′可以设有不共线的固定铰接点533c-1′、第一铰接点533c-2′和第二铰接点533c-3′,固定铰接点533c-1′可以固定设置,具体可以固定在端部连钩221,第一锁闭连梁533a′的一端可以与第二推梁531′铰接、另一端可以铰接于第一铰接点533c-2′,第二锁闭连梁533b′的一端可以与第二锁体52′铰接、另一端可以铰接于第二铰接点533c-3′。
采用这种结构,如图52、图53所示,当第二推梁531′向上移动时,可以带动第一锁闭连梁533a′向上移动,然后可以驱使转接块533c′绕固定铰接点533c-1′进行顺时针转动,并由转接块533c′带动第二锁闭连梁533b′、第二锁体52′向左移动,锁头51′可以逆时针转动,以解锁托部;而当第二推梁531′向下移动时,可以带动第一锁闭连梁533a′向下移动,然后可以驱使转接块533c′进行逆时针转动,并由转接块533c′带动第二锁闭连梁533b′、第二锁体52′向右移动,锁头51′可以顺时针转动,以重新锁定托部。
需要指出,上述的有关第二锁闭驱动梁组件53′的具体结构的描述,仅为本实用新型实施例的一种优选方案,并不能够作为对本实用新型所提供旋转装卸货的驮背运输系统的实施范围的限定,在满足功能的条件下,也可以采用其他形式的第二锁闭驱动梁组件53′,例如,第二锁闭驱动梁组件53′可以采用直接设置为能够进行线性位移的梁件。
进一步的,如图7所示,本体部1还设有横向止挡机构6。当托部4从与端部底架2分离的位置向与端部底架2相连的位置复位时,横向止挡机构能够对托部4的复位位置进行确定,以保证托部4准确地安装于本体部1。
具体来讲,横向止挡机构6可以安装在端部底架2以及关节底架3上,由于安装结构相类似,以下仅以安装在端部底架2为例来描述横向止挡机构6的结构,同样地,本实用新型实施例也提供了两种结构形式的横向止挡机构6。
第一种横向止挡机构6的结构可以参照图61-61,图61为第一种横向止挡机构安装于端部连接钩的结构图,图62为第一种横向止挡机构一种具体实施方式的结构图,图63为图62的分解视图,图64为支座的结构示意图,图65为第一连梁的分体结构图,图66为第一种横向止挡机构另一种具体实施方式的结构图,图67为图66中第一止挡梁与连接端部的连接结构的分解视图。
如图61-图63所示,第一种横向止挡机构6包括:支座61,支座61固定于端部连接钩221,具体可以通过焊接等方式固定,支座61上设有过孔611;第一止挡梁62;止挡驱动梁组件63,与第一止挡梁62传动连接;在止挡状态下,第一止挡梁62能够伸出过孔611,以对托部4形成横向止挡,在解挡状态下,止挡驱动梁组件63能够驱动第一止挡梁62缩回,以解除对托部4的止挡。
采用这种结构,在止挡状态下,第一止挡梁62可以自过孔611伸出,以对托部4形成横向止挡,进而可以保证托部4的准确复位;而在解挡状态下,止挡驱动梁组件63又能够作用于第一止挡梁62,以使其缩回,进而可以解除对托部4的止挡,以不影响托部4和端部底架2的正常分离。
进一步地,还可以包括第三弹性件64,第三弹性件64可以作用于第一止挡梁62,在解挡的过程中,第三弹性件64的变形量会增加,以集聚弹性力。这样,当作用于止挡驱动梁组件63的驱动力消失时,第三弹性件64可以释放,以驱使第一止挡梁62自动回复至止挡位置,可提高设备的自动化程度。
结合图63,第一止挡梁62可以包括粗颈部621和细颈部622,二者之间可以形成台阶面623,第三弹性件64可以为弹簧,其可以外套安装于细颈部622,并能够与台阶面623相作用。此时,细颈部622还可以起到弹簧柱的作用,以对弹簧的伸缩进行导向,可较大程度地避免弹簧在伸缩过程中的径向窜动,对于提高传动的稳定性和可靠性具有积极效果。
需要指出,除了采用弹簧的方案外,第三弹性件64也可以采用弹性球、弹性块、拉力绳等其他形式的弹性元件,只要能够满足使用效果即可。
支座61还可以设有止挡限位件65,第三弹性件64的两端可以分别与止挡限位件65、台阶面623相作用,在附图的方案中,第一止挡梁62可以粗颈部621作为止挡部位,以提高止挡部位的强度,在解挡时,台阶面623可以对第三弹性件64产生压缩力,以增加第三弹性件64的压缩量,这种方案中,第三弹性件64与止挡限位件65、台阶面623之间均为接触关系。
而且,粗颈部621的截面可以为非圆形,过孔611可以与粗颈部621相匹配,这里的相匹配是指二者的形状、尺寸大体一致,如此,当粗颈部621插接在过孔611内时,二者不会产生相对转动,可以提高止挡定位的可靠性。进一步地,粗颈部621与托部4相接触的止挡面可以为平面,这样,托部4与止挡面之间的接触面积可以较大,止挡的可靠性可以获得更大程度地提高。
实际上,在解挡的过程中,第三弹性件64也可以产生拉力,此时,可以第一止挡梁62的细颈部622作为与托部4相接触的止挡部位,且这种方案中,第三弹性件64的两端需要和止挡限位件65、台阶面623相连接,以便在解挡时能够产生拉力。
止挡限位件65的结构在此不做限定,具体实施时,本领域技术人员可以根据实际需要进行设定,只要能够实现上述的效果即可。举例说明,在图63的方案中,止挡限位件65可以为套筒状,该套筒可以为圆筒,也可以为方筒或者其他形状的异形筒,该套筒可以对弹簧进行防护,以较大程度地避免雨水、灰尘等介入而影响弹簧的正常工作;在图66的方案中,止挡限位件65可以为板状或者块状,其可以通过止挡上盖板615与支座61相连,此时,弹簧处在相对开放的空间内,操作人员可以进行直接观察,以方便对弹簧的安装状态进行调整。
结合图64,实际上,本实用新型实施例并不对支座61的结构做限定,其结构主要是为了适应与端部连接钩221的连接,在具体实施时,本领域技术人员可以根据端部连接钩221来调整支座61的形状,支座61需要提供相应的安装点,其中一个安装点为前述的过孔611,图中还示出了另外一个安装点——安装孔612,该安装孔612可用于安装驮背车的制动管组件(图中未示出)。
止挡驱动梁组件63可以包括铰接设置的第一连梁631,第一连梁631的一端部可以为第一驱动端部6311,用于接受外部的驱动力,另一端部可以为连接端部6312,第一连梁631的第一铰轴633可以固定设置,具体来说,可以固定安装在支座61,并位于第一驱动端部6311和连接端部6312之间,连接端部6312则可以与第一止挡梁62传动连接。
这里,本实用新型实施例并不限定止挡驱动梁组件63在解挡时所受到的驱动力的来源,其可以采用手动驱动的方案,例如,可以设置解挡杆等解挡部件,当需要解挡时,可以由工作人员手动操作解挡部件,以对第一驱动端部6311产生驱动力;或者,也可以采用自动驱动的方案,此时,动力源可以为电机、气缸、油缸等,这些动力源可以安装在车体上,也可以安装在地面设备上,具体可以根据实际情况进行选择,动力源与第一驱动端部6311之间还可以设有传动机构,以传递动力源的驱动力。
在一种方案中,如图61-图63所示,止挡驱动梁组件63还可以包括第二连梁632,第二连梁632的一端部可以通过螺纹连接或者焊接等方式与第一止挡梁62相连,另一端部与连接端部6312中,一者可以设有第二铰轴634,另一者可以设有条形导向孔631a-1,第二铰轴634可以插接于条形导向孔631a-1内。
如此设置,通过第二铰轴634与条形导向孔631a-1的配合,可以将连接端部6312的旋转运动转化为第二连梁632的直线运动,进而可驱使第一止挡梁62进行伸出或缩回。
在附图中,上述的条形导向孔631a-1可以设置在连接端部6312上,第二铰轴634可以固定在第二连梁632上,这样,第二连梁632的尺寸相对可以较小,结构可以更为紧凑。
具体实践中,弹簧可以具有一定的预压缩量,以保证第一止挡梁62处于止挡位置时的可靠性,而上述预压缩量的调整则可以通过第二连梁632与第一止挡梁62的连接位置进行确定。
基于第二连梁632与第一止挡梁62之间采用螺纹连接进行固定的方案,还可以设置第一防松件624,第一防松件624也可以与第一止挡梁62相连,并能够与第二连梁632相抵紧,以对第二连梁632进行防松固定。该第一防松件624具体可以为防松螺母,当然,也可以为插条、挡块等形式的防松止挡限位件。
进一步地,还可以包括止挡连接板613和护板614,止挡连接板613的一端可以与支座61相连,另一端可以与护板614相连,用于对止挡驱动梁组件63形成防护,前述的第一铰轴633可以安装在止挡连接板613上,具体的安装方式可以为焊接,或者,也可以借助安装板633a和螺栓进行安装,只要能够保证第一铰轴633的可靠固定即可。实际上,止挡连接板613、护板614也可以作为支座61的一部分。
在另一种方案中,如图66、图67所示,连接端部6312可以设有条形导向槽631e,第一止挡梁62可以插接于条形导向槽631e,且连接端部6312可以与设置在第一止挡梁62的锁紧件631f相抵,用于限定连接端部6321与第一止挡梁62的连接位置。
如此设置,通过第一止挡梁62与条形导向槽631e的配合,也可以将连接端部6312的旋转运动转化为第一止挡梁62的直线运动,以驱动第一止挡梁62进行解挡或者回复止挡。
详细而言,连接端部6312可以限定在锁紧件631f和止挡限位件65之间,第三弹性件64预压缩量的调节可以通过锁紧件631f在第一止挡梁62上的安装位置进行确定,锁紧件631f与连接端部6312之间还可以设有第一垫片631g,以减轻二者连接处的磨耗。
锁紧件631f与第一止挡梁62的连接方式可以为螺纹连接,也可以为焊接等,当为螺纹连接时,还可以包括第二防松件,该第二防松件可以为防松螺母,也可以为止挡插条(附图未标注)、止挡块等,用于对锁紧件631f的安装位置进行限定。
比较而言,上述的两种方案均可以实现第一连梁631旋转运动向第一止挡梁62直线运动的转化,能够实现第一止挡梁62在止挡状态和解挡状态之间的切换,在具体应用中,本领域技术人员可以根据实际需要进行选择。
以前述的第一种方案为例,第一连梁631可以包括间隔设置的长板件631a和短板件631b,第一铰轴633与长板件631a、短板件631b均可以相连,长板件631a的一端部形成上述的连接端部6312,前述的条形导向孔631a-1可以设置在该长板件631a上,长板件631a的另一端部与短板件631b之间可以连接有滚轮631c,此时,长板件631a、短板件631b以及滚轮631c共同组合形成第一驱动端部6311。
当外部的驱动力与滚轮631c相作用时,滚轮631c可以旋转,能够削减第一驱动端部6311与外部驱动设备之间的摩擦力,对于第一驱动端部6311的降低磨耗具有积极效果。
结合图65,还可以包括滚轴631d,滚轴631d可以包括杆部631d-1和头部631d-2,头部631d-2的径向尺寸可以大于杆部631d-1,长板件631a、短板件631b均可以设有穿过孔631b-1,且二者中位于内侧的一者的穿过孔631b-1可以为阶梯孔,装配状态下,至少部分头部631d-2可以隐藏在阶梯孔的大径孔段,杆部631d-1远离头部631d-2的一端则可以与锁紧螺母631d-3进行配合锁定。
这里的“内侧”是指靠近端部连接钩221的一侧,采用这种设计,滚轴631d在内侧突出的长度可以较短,能够较大程度地避免第一驱动端部6311转动时与端部连接钩221之间的接触摩擦。
在上述的各方案中,第一止挡梁62的恢复止挡主要是依靠与第一止挡梁62直接相作用的第三弹性件64,实际上,除了这种方案外,也可以通过止挡驱动梁组件63来带动第一止挡梁62回复止挡状态,也就是说,第一止挡梁62的解挡和回复止挡均可以由止挡驱动梁组件63来完成,这种方案可以通过对止挡驱动梁组件63设置弹性件来实现。
另外,上述横向止挡机构的一个核心在于止挡驱动梁组件63和第一止挡梁62的分离,在止挡状态下,实际只有第一止挡梁62和支座61受力,用于参与驱动的止挡驱动梁组件63不受力,这是上述横向止挡机构的可靠性较高的一个关键点。
第二种横向止挡机构6的结构可以参照图68-67,图68为第二种横向止挡机构在止挡状态下与端部连接钩、托部的相对位置图,图69为图68的局部放大图,图70为第二种横向止挡机构在解挡状态下与端部连接钩、托部的相对位置图,图71为图70的局部放大图,图72为第二种横向止挡机构安装于端部连接钩的结构图,图73为图72的分解视图。
如图69和图71-图73所示,该横向止挡机构6包括:铰接设置的第二止挡梁61′,第二止挡梁61′的两个端部分别为驱动端部611′和止挡端部612′,第二止挡梁61′的铰接轴613′位于驱动端部611′和止挡端部612′之间,且铰接轴613′固定于端部连接钩221;限位梁62′,其固定于端部连接钩221;在止挡状态下,限位梁62′沿横向与第二止挡梁61′的外侧相抵紧,第二止挡梁61′能够对托部4形成横向止挡;在解挡状态下,驱动端部611′受力能够旋转,以驱使止挡端部612′解除对于托部4的止挡。
采用上述结构,在止挡状态下,限位梁62′可以沿横向与第二止挡梁61′相抵紧,以为第二止挡梁61′提供横向的支撑力,然后由第二止挡梁61′对托部4形成横向止挡,可确保托部4的准确复位;而在解挡状态下,驱动端部611′可以受力,并带动整个第二止挡梁61′进行旋转,进而可驱使止挡端部612′转动解除止挡,以不影响托部4和端部底架2的正常分离。
更为重要的是,在止挡状态下,托部4在复位并撞击第二止挡梁61′时,只有止挡端部612′和限位梁62′受力,作为横向止挡机构运动部分的驱动端部611′并不受力,这对于保证横向止挡机构的可靠性具有关键作用。
需要指出,本实用新型实施例并不限定驱动端部611′在解挡时所受到的驱动力的来源,其可以采用手动驱动的方案,例如,可以设置解挡杆等解挡部件,当需要解挡时,可以由工作人员手动操作解挡部件,以对驱动端部611′产生驱动力;或者,也可以采用自动驱动的方案,此时,动力源可以为电机、气缸、油缸等,这些动力源可以安装在车体上,也可以安装在地面设备上,具体可以根据实际情况进行选择,动力源与驱动端部611′之间还可以设有传动机构,以传递动力源的驱动力。
进一步地,还可以包括第一限位件63′,第一限位件63′固定于端部连接钩221,在解挡状态下,第二止挡梁61′可以与第一限位件63′相抵,以避免第二止挡梁61′的转动过量。
这里,本实用新型实施例并不限定第一限位件63′的形状,其可以为板状,也可以为块状、柱状等,具体可以根据实际情况进行确定;同样地,本实用新型实施例也不限定该第一限位件63′的数量和安装位置,只要能够实现上述的效果即可。在本实用新型的一种示例性的方案中,该第一限位件63′可以由端部连接钩221的端部钩壁板221c延伸而形成,这样,就无需专门设置第一限位件63′,零部件的数量可以较少。
在解挡状态下,也即第二止挡梁61′与第一限位件63′相抵时,第二止挡梁61′的重心在纵向上可以偏离铰接轴613′,并位于止挡端部612′所在侧。如此,当作用于驱动端部611′的驱动力消失时,在第二止挡梁61′自身重力的作用下,第二止挡梁61′可以自动回转至止挡状态,而无需设置其他的驱动部件,设备的结构可以较为简单。
和/或,还可以包括止挡第四弹性件65′,该止挡第四弹性件65′可以作用于第二止挡梁61′,在解挡过程中,止挡第四弹性件65′的变形量可以增加,以集聚弹性力。这样,当作用于驱动端部611′的驱动力消失时,止挡第四弹性件65′所集聚的弹性力可以释放,以独自或者与前述的重力相配合,来共同驱使第二止挡梁61′回转至止挡状态。
上述止挡第四弹性件65′具体可以为扭簧,其可以外套安装于铰接轴613′,扭簧的两个伸出端中,一个伸出端可以固定(或者与固定的部件相抵接,如端部连接钩221),另一个伸出端则可以与第二止挡梁61′相抵,第二止挡梁61′在转动以解除止挡状态时,扭簧可以集聚扭转变形力,而当作用于驱动端部611′的驱动力消失时,上述的扭转变形力可以释放,以驱使第二止挡梁61′自动回转。
上述止挡第四弹性件65′也可以为直线弹簧,如拉簧、压簧等通过轴向上的位移来产生弹性力的弹簧元件,以图71中的方案为例,该直线弹簧可以为拉簧,拉簧的一端可以固定,另一端可以与第二止挡梁61′相连,这样也可以在第二止挡梁61′旋转解除止挡时集聚弹性力。
除上述的扭簧、直线弹簧外,止挡第四弹性件65′也可以采用弹性块、弹性球、拉力绳等形式的弹性元件,只要能够实现上述的技术效果即可。
更进一步地,还可以包括第二限位件64′,第二限位件64′固定于端部连接钩221,在止挡状态下,第二止挡梁61′可以与第二限位件64′相抵,以对第二止挡梁61′在止挡状态下的位置进行限定。第二限位件64′结构、数量以及安装位置的限定与第一限位件63′可以相类似,在此不做重复性的描述。
而且,通过上述第二限位件64′的支撑,第二止挡梁61′在垂向上与限位梁62′可以间隙设置,这样,限位梁62′无需承担第二止挡梁61′的重力,相应地,限位梁62′与端部连接钩221的连接处不会产生剪切应力,限位梁62′与端部连接钩221的连接可靠性可以较高。
针对上述各实施方式所涉及的托部4的横向止挡机构6,以下本实用新型实施例还将对第二止挡梁61′的结构进行描述。
结合图69,在止挡状态下,驱动端部611′可以为自上而下逐渐朝向止挡端部612′倾斜的端部,这样,当驱动端部611′受到向上的驱动力作用时,第二止挡梁61′将自然朝向解除止挡状态的方向进行转动,以保证第二止挡梁61′能够顺利进行解锁。
可以理解,调整驱动端部611′的形状,实际上就是调整驱动力和驱动端部611′的作用方向,如此,在具体实施时,也可以通过调整驱动力的方向来实现第二止挡梁61′的旋转解锁。
另外,在止挡状态下,第二止挡梁61′远离驱动端部611′的一端可以设有向下折弯的弯头,该弯头即可以作为上述止挡端部612′,该弯头的设置能够提高止挡端部612′的强度,同时,还能够避让车体和制动管防护装置(图中未示出)。
再结合图73,第二止挡梁61′的铰接轴613′可以为台阶轴,具体可以包括大径段613a′和小径段613b′,其中,大径段613a′可用于和端部连接钩221相连,第二止挡梁61′可以安装于大径段613a′;还可以包括第三限位件613c′,第三限位件613c′具体可以为螺母,其可以安装于小径段613b′,以与端部连接钩221相配合来限定第二止挡梁61′的安装位置。应当理解,第三限位件613c′的作用主要为限位,并非锁死,在安装完成后,要保证第二止挡梁61′能够顺畅的转动。
第三限位件613c′与第二止挡梁61′之间还可以设有第二垫片613d′,该第二垫片613d′可以为橡胶材质,也可以为金属材质等,可避免第二止挡梁61′与第三限位件613c′间的直接摩擦,对于减轻磨耗具有积极效果。
端部架举升部
请参考图88-95,图88是端部架举升装置在最高位置的结构示意图,图8是图88的透视图,图90是端部架举升装置在最低位置的透视图,图91是第一底座的结构示意图,图92是第一支撑座的结构示意图,图93是第一推杆的结构示意图,图94是第一摇杆的结构示意图,图95是第一支撑杆的结构示意图。
各组所述端部架举升部均包括两个分别位于轨道100两侧的端部架举升装置7,也就是说,端部架举升装置7一共有四个,一个端部架2的两侧分别对应设置有端部架举升装置7,以从两侧对端部架进行举升,如此一来,可保证举升的稳定性,并可减小单个端部架举升装置7的强度要求。需要指出,这里的端部架举升装置7既可以用来举升前述的端部底架2,也可以用来举升前述的关节底架分部3a。
具体的,本实施例中,如图88-90所示,端部架举升装置7包括第一底座71、第一支撑座72和驱动机构,其中,第一支撑座72的两侧分别通过第一支撑组件74和第一底座71连接。具体的,第一底座71设有第一滑道711,第一支撑座72设有第二滑道721,第一支撑组件74包括交叉设置的第一支撑杆741和第二支撑杆742,其中,第一支撑杆741的顶端与第一支撑座72铰接,第一支撑杆741的底端可沿第一滑道711滑动,第二支撑杆742的底端与第一底座71铰接,第二支撑杆742顶端可沿第二滑道721滑动,驱动机构能够作用于第一支撑组件74以改变第一支撑杆741和第二支撑杆742之间的夹角,从而改变第一支撑座72距离第一底座71的高度。
其中,第一支撑座72与端部架2朝向托部4的一端的下端面抵接,当驱动机构作用于第一支撑组件74使得第一支撑杆741和第二支撑杆742之间的夹角减小时,该第一支撑组件74的高度增大,从而带动第一支撑座72相对于第一底座71上升,进而将驮背车的端部架2朝向托部4的一端向上举升直至转向架的心盘不再受力,即可通过托部举升装置8进行托部4的举升操作,此时,端部架2由于该端部架举升装置7的支撑不会发生偏斜,而托部4装卸完成并再次与端部架2配合后,驱动机构作用于第一支撑组件74使得第一支撑杆741和第二支撑杆742之间的夹角增大,使第一支撑组件74的高度减小,从而带动第一支撑座72相对于第一底座71下降至原位即可。
在上述实施例中,驱动机构包括第一驱动件731和第一锁定组件732,该第一驱动件731设于第一底座71并提供动力源,作用于第一支撑组件74以改变两个支撑杆(第一支撑杆741和第二支撑杆742)之间的夹角,当第一支撑杆741和第二支撑杆742之间的夹角达到最小,也就是说第一支撑座72上升至最高位置时,第一锁定组件732能够锁定两个支撑杆的相对位置,即保持第一支撑组件74的状态不变,使得第一支撑座72的高度位置稳定,避免由于第一驱动件731发生突然失效等情况导致第一支撑座72跌落,从而保证该端部架举升装置7使用状态下能够对端部架2提供稳定的支撑。
进一步的,上述第一锁定组件732包括第一推杆733和第一摇杆734,同时第一底座71还设有第一销座712,具体的,第一推杆733包括依次设置的第一段7331、第一折弯7333和第二段7332,其中,第一段7331的端部与第一支撑杆741的底端铰接并可沿第一滑道711滑动,第一折弯7333与第一驱动件731铰接,第一摇杆734的一端与第二段7332的端部铰接,第一摇杆734的另一端与第一销座712铰接;第一驱动件731能够作用于第一折弯7333使第一摇杆734绕第一销座712转动,并带动第一支撑杆741的底端沿第一滑道711滑动,当两个之间的夹角达到最小时,第一折弯7333刚好位于第一销座712的上方。
详细的讲,第一折弯7333的开口向下,第一摇杆734铰接于第二段7332和第一销座712之间,第一驱动件731能够作用于第一折弯7333,并带动第一摇杆734绕其和第一销座712之间的铰接点转动,进而带动第一推杆733绕第一折弯7333和第一驱动件731之间的铰接点转动,而第一段7331绕铰接点转动时能够带动第一支撑杆741移动,由于第一滑道711的限制,该第一支撑杆741的底端仅能够沿第一滑道711滑动,以实现两个支撑杆之间的夹角的改变。
如图89所示,当第一支撑杆741沿第一滑道711滑动至两个支撑杆之间的夹角最小使第一支撑座72上升至最高位置时,第一折弯7333刚好位于第一销座712的上方,第一驱动件731不再作用,此时,若第一驱动件731发生故障导致其推力不足时,该第一驱动件731对第一支撑组件74的驱动作用撤除,而端部架2仍继续下压第一支撑座72,并使两个支撑杆之间的角度有增大的趋势,由于第一折弯7333的开口向下并位于第一销座712的正上方,此时,竖直向下的压力无法将第一推杆733横向移动,进而限制了第一摇杆734的转动以及第一支撑杆741沿第一滑道711的滑动,从而可保持各第一支撑组件74的状态不变,即两个支撑杆之间的夹角不变、第一支撑座72的高度不变,稳定性更好。
通过上述锁定装置的设置,可使得当第一驱动件731通过第一支撑组件74使得第一支撑座72升至最高位置时能够实现各第一支撑组件74之间的自动锁定,此种状态下,竖直方向的力无法改变各第一支撑组件74的状态,仅有在需要将端部架2下降时,通过第一驱动件731提供反向作用力使得第一推杆733横向移动至第一折弯7333与第一销座712脱离时,可实现解锁并带动第一支撑杆741的底端沿第一滑道711反向移动直至第一支撑座72下降至最低状态(如图90所示)即可。该第一锁定组件732可在实现第一支撑座72的升降的同时实现锁定和解锁,无需额外提供锁定部件,可简化整体结构并简化操作,保证整体结构的稳定性和操作便捷性。
具体的,如图88-9所示,本实施例中,第一驱动件731为液压缸,该液压缸的活塞杆与第一推杆733的第一折弯7333铰接,第一支撑座72的两侧分别通过第一支撑组件74和第一底座71连接,液压缸与其中一个第一支撑组件74的第一支撑杆741的底端作用即可实现所有第一支撑组件74的整体升降,稳定性好。当然,本实施例中,还可以通过电机、齿轮和齿条或者电机、丝杆和螺母提供动力源,在此不做具体限制。
在上述实施例中,第一推杆733的第一段7331的端部还设有连接轴,该连接轴套设有第一滚轮7335,第一驱动件731作用于第一折弯7333使第一推杆733绕第一折弯7333和第一驱动件731之间的铰接点转动时,第一段7331的端部沿第一滑道711滑动,此时,第一滚轮7335能够沿底板71滚动。第一推杆733的第一段7331的端部能够通过第一滚轮7335与第一底座71接触,从而使得第一段7331的端部沿第一滑道711滑动时,第一滚轮7335沿第一底座71滚动,减小阻力的同时还能够减小第一段7331和第一底座71之间的摩擦磨损,保证使用寿命。具体的,该第一推杆733可以是如图93所示的,包括两个并列设置的第一v字型连接件7334,两个第一v字型连接件7334朝向第一段7331的端部之间还设有连接轴,或者,还可以将第一段7331的端部设置有凹槽,连接轴设于凹槽的两侧壁之间。
进一步的,如图91所示,第一底座71还设有第一滚板713,第一滚轮7335能够沿第一滚板713滚动,或者,本实施例中,还可以将第一滚轮7335设置为直接沿第一底座71的上表面滚动,而第一滚板713的设置可在其发生磨损后对其进行更换,从而保证第一底座71的使用寿命。
在上述实施例中,如图94所示,第一摇杆734朝向第一销座712的一端设有第一凹缺口7341,且第一凹缺口7341的两侧壁以及第一销座712分别设有第一轴孔7342,第一销座712设于第一凹缺口7341内并通过穿过第一轴孔7342的销轴可旋转连接。或者,本实施例中,还可以将第一摇杆734的一端设于第一销座712的一侧并通过销轴连接,而第一摇杆734设有第一凹缺口7341且第一销座712位于第一凹缺口7341内,可使得二者连接的更稳定,避免发生偏斜卡滞的情况。
在上述实施例中,该端部架举升装置7还包括第一上滑动轴75和套设于第一上滑动轴75外的第一滚套751,第一支撑座72的两侧通过对称设置的第一支撑组件74与第一底座71连接,第一上滑动轴75穿过对称设置的第一支撑组件74的第二支撑杆742的顶端,并可沿第二滑道721滑动,第一滚套751位于两个第二支撑杆742之间并与第一支撑座72抵接滚动。也就是说,第一支撑组件74与第一支撑座72之间通过第一滚套751作用以保证第一支撑组件74对第一支撑座72之间的支撑力,稳定性好,同时,该第一滚套751设于两个第二支撑杆742之间,还能够对二者进行限位避免二者之间的距离发生变化影响端部架2的升降。
进一步的,该端部架举升装置7还包括第一下滑动轴76,第一下滑动轴76穿过对称设置的第一支撑组件74的第一支撑杆741的底端以及第一推杆733的第一段7331,并可沿第一滑道711滑动。通过第一下滑动轴76的设置可实现第一支撑杆741的底端可沿第一滑道711滑动,并且第一支撑杆741的底端与第一推杆733的第一段7331的端部铰接,可简化整体结构。
更进一步的,如图95所示,第一支撑杆741的底端两侧分别设有套设于第一下滑动轴76外的第一加强套7411。该第一加强套7411的设置能够增加第一支撑杆741的底端的结构强度的同时,还可对该第一支撑杆741的底端进行限位,减小其两侧分别与第一底座71及第一推杆733的第一端之间的间距,避免发生偏斜的情况,稳定性好。
在上述实施例中,第一底座71和第一支撑座72分别设有侧板,第一滑道711和第二滑道721均为设于侧板的长条孔。或者,本实施例中,还可以将第一滑道711和第二滑道721设置为滑轨或滑槽的结构,而长条孔的结构设置较为简单,可简化制作工艺。
在上述实施例中,如图92所示,该端部架举升装置7还包括第一解锁部77,该第一解锁部77设于第一支撑座72的上端面,用于解锁前述锁闭机构5。以前述的第一中锁闭机构5为例,在解锁时,第一解锁部77可以随端部架举升装置7向上位移,并穿过第一连接孔221d、以与第一推梁541相作用,进而驱使第一锁体51进行转动,从而解除对于托部4的锁定。
如此设置,在端部架被举升时,可以实现锁闭机构5的自动解锁,自动化程度更高。
另外,本实施例中,对于上述旋转定位装置300的具体结构不做限制,如还可将该端部架举升装置7用于旋转定位装置300中的升降机构,将定位轴设于第一支撑座72的上端面即可。
结合图92a,该端部架举升装置7还可以设有第二解锁部78,在端部架举升装置7向上位移时,第二解锁部78可以解锁相应的横向止挡机构6。以第二种横向止挡机构6为例,第二解锁部78在向上位移时,可以与第二止挡梁61′的驱动端部611′相作用,以驱使第二止挡梁61′绕铰接轴613′进行转动,进而解除对于托部4的横向止挡。
如此设置,在端部架被举升时,可以实现横向止挡机构6的自动解锁,配合前述第一解锁部77对于锁闭机构5的解锁,在端部架举升装置7的作用下,不仅可以实现端部架的举升,还可以同步地实现锁闭机构5、横向止挡机构6的解锁,也就是说,端部架在被举升后,托部4即已经具备了可被举升分离的条件,托部4的旋转分离操作可以更为快速,这对于提高装卸货的效率具有积极效果。
此外,对于一个本体单元而言,横向止挡机构6实际上有四个,这四个横向止挡机构6可以分别设置在两个端部架的横向两侧,以对托部4纵向两端部的横向两侧进行限位。在实现托部4的旋转分离时,实际上只需要解锁对角的两个横向止挡机构6即可,因此,每一组端部架举升部的两个端部架举升装置7中可以仅有一个设置前述的第二解锁部78,且两组端部架举升部中设有第二解锁部78的端部架举升装置7可以分别位于轨道的横向不同侧,这才能够实现对角设置的两个横向止挡机构6的解锁,进而可以实现托部4的旋转分离。而另外两个对角设置、且未被解锁的横向止挡机构6则可以作为托部4回转的限位结构,以保证托部4能够准确地回转到位。
纵向定位装置
请参考图105-图111,图105是纵向定位装置在最高位置的结构示意图,图106是图105的主视图,图107是纵向定位装置在最低位置的结构示意图,图108是图107的主视图,图109是第三底座的结构示意图,图110是第三滑动座的结构示意图,图111是纵向定位装置的局部结构示意图。
上述地面设备还包括设于轨道100内的纵向定位装置9,该纵向定位装置9包括第三底座91、第三滑动座92、升降部94、驱动部和定位部95,其中,驱动部能够驱动第三滑动座92相对于第三底座91沿纵向滑动,升降部94和定位部95均设于第三滑动座92,升降部94能够升降定位部95,定位部95与设于驮背车托部4下端面的纵向定位结构相适配,当通过升降部94作用定位部95使其处于升起状态时,驱动部能够驱动第三滑动座92相对于第三底座91沿纵向滑动,并带动设于第三滑动座92的定位部95沿纵向滑动至与设于托部4下端面的定位结构配合,然后驱动部继续驱动,并可通过定位部95和纵向定位结构的配合作用推动托部4,使其沿纵向移动至预设位置。
其中,纵向是指该驮背车的长度方向,通过该纵向定位装置9能够驱动车辆移动至预设位置,使得此各本体部和托部4分别与站台设置的其它装卸车站场设备(包括端部底架举升装置7、托部举升装置8、斜坡过渡装置200和转动装置400等)的设置位置对应,保证装卸车顺利进行。
具体的,该纵向定位装置9设于装卸车站场的轨道100内,托部4的下端面设有定位结构,该定位结构与本实施例所提供的纵向定位装置9的限位机构相适配,当驮背车停止后托部4位于预设范围内时,启动该纵向定位装置9的升降部94使定位部95处于升起状态,此时,定位部95与定位结构处于同一高度,然后启动驱动部,使得第三滑动座92带动定位部95沿纵向移动,直至该定位部95与托部4下端面的定位结构配合,然后驱动部继续驱动并通过定位部95与限位结构的作用推动托部4沿纵向移动至预设位置,此时,该驮背车的各端部底架2和托部4分别与其它装卸车站场设备的设置位置对应,然后可通过端部底架举升装置7举升端部底架2和托部4,再通过托部举升装置8将托部4举升使其与端部底架2脱离,然后通过转动装置400驱动托部4旋转至与斜坡过渡装置200衔接后,即可进行装卸车操作。
也就是说,当驮背车到达装卸车站场停止后,端部底架2和托部4的位置并不一定是上述预设位置,而是位于预设位置的预设距离范围内,此时,通过本实施例所提供的纵向定位装置9可对该托部4进行推动作用,使其沿纵向移动至预设位置即可实现端部底架2和托部4的纵向位置的精准定位,便于后期通过端部底架举升装置7、托部举升装置8和转动装置400等的动作。该纵向定位装置9的结构简单,仅需通过升降部94和驱动部作用,使得定位部95与托部4的纵向定位结构配合并对托部4进行推动即可,结构简单、稳定性好。
预设范围是指距离预设位置一定距离的范围内,该纵向定位装置9与固设于轨面,当托部4所停的位置在预设范围内时,可通过该纵向定位装置9对其进行纵向定位,若超出预设范围,则超出该纵向定位装置9的作用行程,无法使托部4达到预设位置。具体的,托部4的停止位置在预设范围内时,可能是在预设位置的前侧也可以是在预设位置的后侧,因此,对于同一装卸车站场,可通过设置一组或多组包括沿纵向方向相向设置的两个纵向定位装置9对驮背车的各托部4的纵向位置进行调节使其到达预设位置,灵活性更好。
在上述实施例中,定位部95包括横梁951和固设于该横梁951的定位块952,横梁951的两端分别设有能够沿托部4的下端面滚动的第三滚轮953,当车辆停止在预设范围内后,定位部95与定位结构处于脱离状态,然后,升降部94作用于定位部95使其高度与定位结构的高度一致,然后驱动部驱动第三滑动座92带动定位部95滑动至与定位结构配合的过程中,该定位部95相对于托部4是滑动状态,第三滚轮953的设置可减小该定位部95在此过程中与托部4的下端面之间的滑动摩擦,进而减少摩擦磨损的情况,延长使用寿命。
对于定位块952和定位结构的设置,在此不做具体限制,如图111所示的,本实施例中,定位部95为三角形定位块952,相应的,纵向定位结构可设置为位于托部4的横向支架的v型缺口或凹坑,或者,将该定位块952设置为方形块或圆形块均可。
在上述实施例中,升降部94为设于第三滑动座92的空气弹簧,由于转向架弹簧的作用,当托部4处于空载状态时,其高度最高,而当托部4载有公路车辆时,其高度相较于空载时的高度低,因此,将升降部94设置为空气弹簧时,其充气后的高度具有弹性调节相较于刚性提升高度的装置来说,可适应于托部4不同状态下的不同高度要求,适用性更好。具体的,该定位部95(横梁951)的下端还可设有抵接板954,用于与空气弹簧抵接作用,增加二者之间的作用面积,提高稳定性。
进一步的,第三滑动座92还设有摆动件,该摆动件包括铰接端和动作端,其中,铰接端与第三滑动座92铰接,空气弹簧的顶端能够推动动作端使其绕铰接端摆动,上述横梁951固设于动作端。也就是说,空气弹簧充气后能够向上推动动作端使其绕铰接端转动,而当空气弹簧排气后,动作端将绕铰接端转动并下降至最低位置(如图107和图108所示),该摆动件的设置可保证该定位部95的稳定性的同时,简化整体结构。
更进一步的,摆动件包括两根平行且间隔设置的摆杆96,或者,本实施例中,还可以将该摆动件设置为一整块板状结构,该板状结构的一侧边与第三滑动座92铰接,另一侧边与横梁951固定,而两根摆杆96的方案可简化整体结构并减轻重量。
在上述实施例中,驱动部包括与第三底座91铰接的第三液压缸93,该第三液压缸93的第三活塞杆931的端部与定位部95铰接,第三液压缸93的第三活塞杆931推拉定位部95使得第三滑动座92和定位部95整体沿纵向滑动,或者,本实施例中,还可以将该液压杆的第三活塞杆931与第三滑动座92作用,即直接推拉第三滑动座92使其带动定位部95沿纵向滑动,而将第三液压缸93的第三活塞杆931与定位部95铰接时,当第三活塞杆931在缩回状态下时,第三液压缸93的部分位于滑动部的上方(两根摆杆96之间),可减小第三滑动座92的端部与第三底座91的端部之间的距离,进而减小该纵向定位装置9的整体体积。
或者,本实施例中,还可以将该驱动部设置为包括电机、齿轮和齿条的结构或者将其设置为包括电机、丝杆和螺母的结构均可,此时,驱动部可固设于第三底座91并直接作用于第三滑动座92使其相对于第三底座91沿纵向滑动,而将驱动部设置为第三液压缸93时,可简化整体结构,并且稳定性更好。
在上述实施例中,该纵向定位装置9还包括限位部97,该限位部97用于限制动作端的升降高度,使得动作端升至最高位置时(如图105和图106所示),该定位部95能够与处于空载状态下的托部4的定位结构配合,如此设置,可在对空气弹簧进行充气以向上推动定位部95时,避免由于充气压力过大导致充气弹簧破损的情况,为空气弹簧提供充气保护。
具体的,该限位部97包括相互铰接设置的第一连杆971和第二连杆972,其中,如图110和图111所示,第三滑动座92设有第一铰接座921,定位部95(横梁951)设有第二铰接座9511,第一连杆971的端部与第一铰接座921铰接,第二连杆972的端部与第二铰接座9511铰接,升降部94升降定位部95时能够通过动作端带动第二连杆972相对于第一连杆971展开或折叠。也就是说,当升降部94升降定位部95时,两根连杆(第一连杆971和第二连杆972)之间的夹角发生变化,当二者之间的夹角展开至最大时,即可对该空气弹簧进行限位。或者,本实施例中,还可以将该限位部97设置为链条或拉绳,当链条或拉绳处于拉直状态时即可对该空气弹簧进行限位。而将限位部97设置为相互铰接并可折叠的两根连杆的方案时,在空气弹簧排气后,两根连杆处于折叠状态,此时二者的高度较低,不会对定位部95的下降造成阻碍。
进一步的,该限位部97还包括设于第一连杆971和/或第二连杆972的限位结构,该限位结构能够限制第一连杆971和第二连杆972之间转动的最大夹角,使其小于180°,如此设置可避免两根连杆之间的夹角达到180°后形成死点,影响定位部95的下降。具体的,可以是第一连杆971和第二连杆972中的一者设有限位结构,二者转动至最大夹角时,该限位结构能够与另一连杆抵接以限制其继续转动,或者,还可以是包括分别设于两根连杆并相互适配的限位结构,当二者之间的夹角达到最大时,能够限制继续转动。
在上述实施例中,如图109所示,第三底座91沿纵向设有第五滑道911,第三滑动座92设有能够沿第五滑道911滑动的滑块922,具体的,如图110和图111所示,本实施例中,该第五滑道911为设于第三底座91的滑槽,第三滑动座92的边缘设有位于该滑槽内并可沿滑槽滑动的滑块922,或者,还可以将该滑槽设于第三底座91的上端面,第三滑动座92的下端面设有能够沿滑槽滑动的滑块922即可。当然,本实施例中,还可以将第五滑道911设置为沿纵向设置的条形孔或滑轨均可,在此不做具体限制。
当然,本实施例中,还可以将第五滑道911设于第三滑动座92,第三底座91能够沿第五滑道911滑动,由于第三底座91固设于轨面,因此第三滑动座92可相对于第三底座91滑动。而将第五滑道911设于第三底座91时,可保证该第三滑动座92的滑动连续性好。
另外,本实施例中,上述各部件之间的铰接连接均可采用销轴或圆销连接,并通过垫圈、开口销对销轴或圆销进行限位。
制动管防护装置
制动管是铁路车辆的一个重要部件,其在安装时需要在纵向上贯通车体,对于驮背车,由于托部4和本体部1存在反复的分离和安装的情形,制动管就有可能对托部的分离和安装产生干涉,一旦产生干涉,制动管就有可能被动作中的托部4损坏。
为此,本申请还涉及了一种翻转式的制动管防护装置,该制动管防护装置包括防护外壳和安装于防护外壳的制动管,在托部上升以准备和本体部相分离时,防护外壳可以在竖直面内沿横向外翻,以避免对托部4形成干涉,而在托部4下落以安装于本体部1时,防护外壳又可以沿横向内翻,以回复至原始位置,这样,能够较好地避免制动管与动作中的托部4产生干涉,同时,防护外壳也可以对制动管进行防护,能够防止制动管与地面接触而产生磨损泄露,对于驮背车的行车安全具有积极效果。
具体而言,请参考图74-81,图74为制动管防护装置的结构图,图75为图74中c处的放大图,图76为图74中d处的放大图,图77为图74中e处的放大图,图78为制动管防护装置在托部和本体部连接状态下的结构图,图79为图78中圈内部分的放大图,图80为制动管防护装置在托部和本体部分离状态下的结构图,图81为图80中圈内部分的放大图,图82为第一防护限位件和第二防护限位件设于支座的结构图,图83为第一枢接板的结构图,图84为第二枢接板的结构图,图85为防护隔板的结构图,图86为管吊座板的结构图,图87为管吊连接板结构图。
如图78所示,驮背车的车体通常包括本体部1和托部4,可以通过绕垂向旋转托部4或者沿横向平移托部4,使其与本体部1分离。制动管布置在托部4的横向外侧,绕垂向旋转托部4或者沿横向平移托部4时,为了规避制动管的干涉,需要先将托部44向上举升一段距离。为了缩短举升距离和保护制动管,本实用新型设计了一种制动管防护装置。
如图74所示,该制动管防护装置10包括防护壳体11,防护壳体11的壳腔用于容纳制动管。设置防护壳体11,一方面可以保护制动管,另一方面便于统一移动制动管。如图78所示,托部4与本体部1连接状态下,防护壳体11位于托部4的侧墙42的横向外侧。
如图74所示,该制动管防护装置10还包括防护连接件12,如图75所示,防护连接件12包括防护内端部12a、防护外端部12b以及位于两者之间的防护转接部12c。如图79所示,防护内端部12a位于托部4下侧,并与托部4抵接,具体可以与托部4的压板412d抵接;防护外端部12b位于防护内端部12a的横向外侧,并与本体部1转动连接,具体可以与本体部1的支座61转动连接。
如图79所示,托部4与本体部1连接过程中,托部4对防护内端部12a的抵压力逐渐增大,使防护内端部12a的受力逐渐大于防护外端部12b的重力,此时,防护连接件12绕与本体部1的转动连接位置转动(如图中箭头方向),从而带动防护壳体11向上并向内转动,使防护壳体11复位,最终到达图79所示位置。
如图81所示,托部4与本体部1分离过程中,托部4对防护内端部12a的抵压力逐渐减小,使防护内端部12a的受力逐渐小于防护外端部12b的重力,此时,防护连接件12在重力的作用下绕与本体部1的转动连接位置转动(如图中箭头方向),从而带动防护壳体11向下并向外转动,使防护壳体11的高度位置下降,最终到达图81所示位置。这里,在对制动管防护装置10进行安装时,可以对其重心位置进行调整,使得其重心可以分布在旋转中心的横向外侧,如此,一旦制动管防护装置10与托部4的连接解除,即可以产生如上形式的转动。
由于防护壳体11的高度位置下降,所以仅需要将托部4向上举升较短的距离即可规避防护壳体11对托部4的干涉,使托部4能够顺利进行绕垂向的旋转或沿横向的平移。
综上,托部4与本体部1分离过程中,防护壳体11能够自动向下并向外转动,以避让托部4,有效缩短了托部4的举升距离;托部4与本体部1连接过程中,防护壳体11能够自动复位。举升距离的缩短以及防护壳体11的自动避让和自动复位,使托部4与本体部1的分离效率和连接效率得以提升。
进一步的,该制动防护装10还可以设置第一防护限位件13(参见图79和图82),第一防护限位件13固定于本体部1,具体可以固定在支座61上,当防护壳体11向下并向外转动到极限位置时,防护连接件12与第一防护限位件13抵触,这样,可以防止防护壳体11过渡向下转动导致不易复位的风险。图中,第一防护限位件13为块体,实际实施时,其结构和形状可以根据需要调整,不局限于块体。
进一步的,该制动管防护装置10还可以设置磁性件14(参见图74),当防护壳体11位于所述托部4的横向外侧时,防护壳体11通过磁性件14与托部4的侧墙42磁力吸合。这样可以缓解制动防护装置的随车振动,利于提升制动防护装置10的寿命。
图示方案中,磁性件14可拆卸地固定在防护壳体11的上表面,具体可以螺栓螺母固定。将磁性件14固定在防护壳体11的上表面,可以保证在防护壳体11复位过程中防护壳体11所受的磁性力的方向与防护壳体11复位方向基本一致,从而使磁性力能够协助防护壳体11复位。使磁性件14与防护壳体11可拆卸固定,便于磁性件14的更换。
更进一步的,该制动管防护装置10还可以设置第二防护限位件15(参见图81和图82),当防护壳体11复位到托部4的横向外侧时,防护连接件12与第二防护限位件15抵触。设置磁性件14时,当托部4向上移动时,在磁性力的作用下,防护连接件12存在随之向上移动的趋势,通过设置第二防护限位件15,能够防止防护连接件12随托部4向上移动。图中,第二防护限位件15为块体,实际实施时,其结构和形状可以根据需要调整,不局限于块体。
图示方案中(参见图75),防护连接件12包括第一枢接板121、第二枢接板122和枢接转轴123。第一枢接板121和第二枢接板122沿纵向间隔排布。如图79所述,第二枢接板122相比第一枢接板121更靠近托部4。支座61位于第一枢接板121和第二枢接板122之间,枢接转轴123依次穿过第一枢接板121、支座61上的安装孔612和第二枢接板122,将三者连在一起,实现了防护连接件12与本体部1的转动连接。该结构连接可靠性高,当然,实际实施时,并不局限于该结构。
图示方案中,枢接转轴123的一端设有限位头(图中不可见),另一端设有径向孔,限位销1231穿于其径向孔内,第一枢接板121和第二枢接板122位于限位头和限位销1231之间,这样可以对枢接转轴123起到轴向限位作用,能够进一步提升防护连接件12与本体部1的连接可靠性。
图示方案中,防护连接件12还包括防护滚轮125,防护滚轮125可转动地连于第二枢接板122。如图79所示,第二枢接板122伸到压板412d下侧,使防护滚轮125的外周面与压板412d的下表面抵接,从而实现防护连接件12与托部4的抵接。通过设置防护滚轮125,可以缓解防护连接件12与托部4抵接过程中的磨损。
图示方案中(参见图75),设有固定轴124,固定轴124的一端固定于第二枢接板122,具体可以焊接固定,固定轴124的另一端固定有挡圈(图中未示出),防护滚轮125可转动地套在固定轴124外周并位于挡圈和第二枢接板122之间,挡圈和第二枢接板122可以防止防护滚轮125脱离固定轴124。
图示方案中(参见图74和图75),防护壳体11的前端和后端不设置端板,防护壳体11的前端和后端由防护连接件12封挡,这样利于制动管防护装置10的轻量化。详细的,防护壳体11的前端由块第一枢接板121和一块第二枢接板122封挡,后端由另一块第一枢接板121和另一块第二枢接板122封挡,第一枢接板121和第二枢接板122上均设有供制动管穿过的防护过孔12d。图中(参见图83和图84),第一枢接板121和第二枢接板122上各设有两个防护过孔12d,两个防护过孔12d沿上下方向错开排布。实际实施时,防护过孔12d的数量和排布方式均不局限于此。
图示方案中(参见图74),防护壳体11包括c形防护梁111、多块防护封板112和多组管吊组件113。各防护封板112封挡固定在c形梁的开口侧,具体可以焊接固定,各防护封板112沿c形防护梁111的长度方向(即纵向)相互间隔,使相邻防护封板112之间形成安装口,该安装口用于安装管吊组件113。
具体的,如图76和图77所示,每组管吊组件113包括两块防护隔板1131和两块管吊座板1132。两块防护隔板1131固定在c形防护梁111的内部,具体可以焊接固定,两块防护隔板1131沿c形防护梁111的长度方向(即纵向)相互间隔。两块管吊座板1132一一对应地固定于两块防护隔板1131并位于两块防护隔板1131之间。另外,图77中,还设有管吊连接板1133。
具体的,如图85所示,防护隔板1131上设有供制动管穿过的管孔,制动管依次穿过各防护隔板1131上的管孔,这样,可以降低制动管在防护壳体11内的晃动,利于提升保护效果和缓解行车振动。
具体的,如图86所示,管吊座板1132上设有供螺纹紧固件穿过的座孔。如图87所示,管吊连接板1133上设有供螺纹紧固件穿过的连接孔。图76中,两管吊座板1132的座孔对齐,以便螺纹紧固件依次穿过两管吊座板1132,图77中,管吊连接板1133的连接孔与管吊座板1132的座孔对齐,以便螺纹紧固件依次穿过管吊连接板1133和管吊座板1132。
图示方案中(参见图74),共设有三组管吊组件113,两侧的管吊组件113的结构相同(图76所示结构),中间的管吊组件比两侧的管吊组件多设置了一块管吊连接板1133。
制动管20位于防护壳体11内的部分为刚性管、位于防护壳体11外的管段为柔性管,刚性管的两端分别与两条柔性管连通,柔性管与刚性管连通的一端设有法兰接头201,柔性管通过法兰接头201固定于制动管防护装置10。具体的方案中,第一枢接板121设有法兰连接孔,法兰接头201固定在第一枢接板121上(参见图79)。这种制动管能够适应防护壳体11的频繁翻转、不易折断、可靠性高。
具体的,刚性管可以是一整节管,也可以由多节刚性管段通过法兰或者快装接头连接而成。每条柔性管可以是一整节管,也可以由多节柔性管段通过法兰或者快装接头连接而成。
以上仅是本实用新型的优选实施方式,应当指出,对于本技术领域的普通技术人员来说,在不脱离本实用新型原理的前提下,还可以做出若干改进和润饰,这些改进和润饰也应视为本实用新型的保护范围。
起点商标作为专业知识产权交易平台,可以帮助大家解决很多问题,如果大家想要了解更多知产交易信息请点击 【在线咨询】或添加微信 【19522093243】与客服一对一沟通,为大家解决相关问题。
此文章来源于网络,如有侵权,请联系删除


