一种新型全自动驾驶车辆可拆卸司机室间壁的制作方法



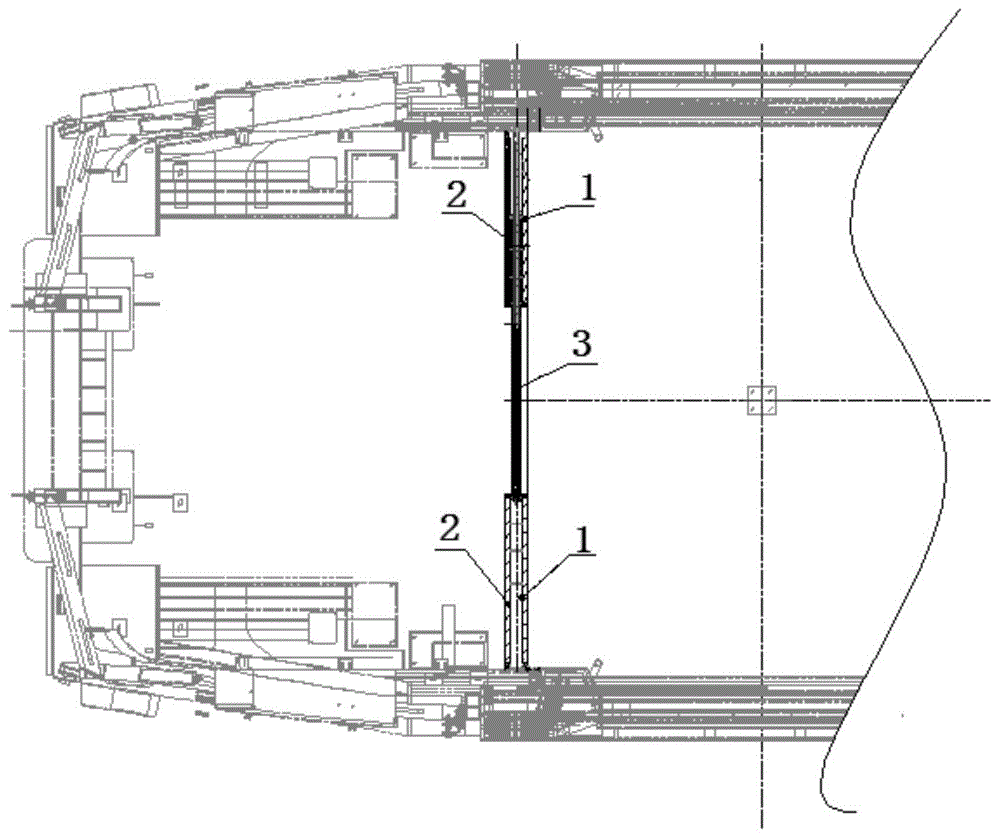
本发明属于轨道车辆司机室间壁结构,尤其是涉及一种全自动驾驶车辆的可灵活拆卸的司机室间壁。
背景技术:
现有全自动驾驶车辆在车辆运营之初,为保证车辆正常运行,需要配置司机,并为司机提供独有的空间,配置司机室间壁结构,司机室间壁结构多是无法现车拆除的“死间壁”。在后期实现全自动驾驶后,要保证司机室区域的通透性,需要拆除司机室间壁。拆除需要耗费大量的人力、物力,并且受到车上空间的限制,拆除工程艰巨。
发明目的
本发明的目的是提供一种可现车拆卸的司机室间壁,在不需要大量拆除车辆其它设备的情况下,方便快捷的拆除司机室间壁,且现车方便恢复周圈环境,保证司机室区域的通透性。
为实现上述发明目的,本发明提供一种新型全自动驾驶车辆可拆卸司机室间壁,包括客室侧间壁组成、司机室侧间壁组成、司机室间壁门、客室侧间壁顶板组成、司机室侧间壁顶板组成,其特征在于:客室侧间壁组成和司机室侧间壁组成两侧均与司机室内装侧墙之间为插接结构;客室侧间壁组成和司机室侧间壁组成与各自的间壁顶板组成在纵向中心线位置实现上下两处连接,其中,上部的连接均通过安装横梁用螺栓紧固件固定,安装横梁与连接在车顶滑槽上的连接件相连,下部的连接均通过间壁翻边用螺钉连接固定;客室侧间壁组成和司机室侧间壁组成的上部靠近两侧的位置与司机室车顶滑槽借助直角安装角铝用螺栓连接;客室侧间壁组成及司机室侧间壁组成与地板接口通过中间件及螺钉连接固定。
进一步地,客室侧间壁组成与司机室内装侧墙之间的插接结构是在司机室内装侧墙上连接一插接直角铝板,与插接直角铝板相对称设一直角挡缝板,客室侧间壁组成两侧连接端加工有水平平行的三个间隔且凸出于连接端端面的插板,插接直角铝板和直角挡缝板的其中一个直角边分别与司机室内装侧墙相贴合,另一直角边分别同时与客室侧间壁组成两侧的三个间隔且凸出的插板形成的插槽插接,安装拆卸方便,定位精准。
进一步地,所述的连接件是由两个相对互连的l型可调整角钢构成,两个l型可调整角钢通过上面开的连接孔实现高度调整,上面的l型可调整角钢的横边通过螺栓坚固件与车顶滑槽,下面的l型可调整角钢的横边与安装横梁连接。
进一步地,间壁翻边是在客室侧间壁组成和司机室侧间壁组成的加强骨架横梁上预埋螺套及用螺钉固定的角铝,角铝上焊接螺纹块,各自顶板组成在螺纹块对应位置开通过孔,用螺钉将各自顶板组成下部与客室侧间壁组成和司机室侧间壁组成连接固定。
进一步地,客室侧间壁组成与地板接口的连接方式是在客室侧间壁组成上连接一角铁,角铁的一面与地板贴合,通过螺钉固定连接,角铁的另一面与客室侧间壁组成贴合,通过螺栓连接固定。
进一步地,司机室侧间壁组成与地板接口的连接方式是在司机室侧间壁组成下面自带一方形管材,方形管材的底部延伸出一块连接板材,通过连接板材用螺钉与地板连接固定。
进一步地,司机室侧间壁组成与司机室内装侧墙之间的插接结构是在司机室内装侧墙上安装一侧墙插接角铝,侧墙插接角铝与连接客室侧间壁组成的插接直角铝板相对设置,司机室侧间壁组成两侧连接端加工有水平平行的三个间隔且凸出于连接端端面的插板,侧墙插接角铝的其中一个直角边与司机室内装侧墙相贴合,另一直角边与司机室侧间壁组成两侧的三个间隔且凸出的插板形成的插槽插接,三个插板形成两个插槽,便于根据需求调整空间大小,拆卸方便,定位精准。
进一步地,整个司机室间壁为变截面司机室间壁,为司机室间壁门上部机构提供安装活动空间。
本发明通过客室侧间壁组成和司机室侧间壁组成与司机室内装侧墙之间的插接结构,以及客室侧间壁组成和司机室侧间壁组成与地板、各自顶板组成及车顶的螺栓连接,实现了可拆卸的司机室间壁功能,安装便捷,拆除方便,省时省力,且可现车进行,拆除后现车即可修复原司机室间壁安装位置的环境。
附图说明
图1是本发明司机室间壁布置图;
图2是司机室间壁客室侧视图;
图3是司机室间壁司机室侧视图;
图4是客室侧间壁组成与侧墙的插接结构示意图;
图5是客室侧间壁组成与地板固定结构示意图;
图6是客室侧间壁组成车顶连接结构示意图;
图7是客室侧间壁组成与其顶板组成安装接口示意图;
图8安装横梁接口示意图;
图9是司机室侧间壁组成与侧墙的插接结构示意图;
图10是司机室侧间壁组成与地板接口结构示意图。
具体实施方式
参照图1-图3,本发明整个司机室间壁为变截面司机室间壁,在距离地板面1910mm以下间壁厚度为100mm,在距离地板面1910mm以上至2123mm范围内间壁厚度为200mm,为司机室间壁门上部机构提供安装活动空间。具体结构包括客室侧间壁组成1、司机室侧间壁组成2、司机室间壁门3、客室侧间壁顶板组成4、司机室侧间壁顶板组成5。
参照图4,客室侧间壁组成与司机室内装侧墙之间为插接结构,是在司机室内装侧墙6上连接一插接直角铝板101,与插接直角铝板101相对称设一直角挡缝板105,客室侧间壁组成两侧连接端加工有水平平行的三个间隔且凸出于连接端端面的插板102、103、104,插接直角铝板101和直角挡缝板105的其中一个直角边分别与司机室内装侧墙6相贴合,另一直角边分别同时与客室侧间壁组成两侧的三个间隔且凸出的插板形成的插槽插接,该插接结构安装拆卸方便,定位精准。
参照图5,客室侧间壁组成1与地板7接口的连接是在客室侧间壁组成1上连接一角铁,角铁的一面106与地板7贴合,通过螺钉107固定连接,角铁的另一面108与客室侧间壁组成1贴合,通过螺栓109连接固定,螺钉及螺栓的连接使得安装拆卸都极为简单、方便。
参照图2、图6,客室侧间壁组成1与司机室车顶的连接是在靠近间壁组成的两端,通过在客室侧间壁组成上部连接一直角安装角铝110,通过直角安装角铝110和t型螺栓111及螺母112与车顶滑槽8连接固定。
参照图2、图3、图7、图8,客室侧间壁组成1和司机室侧间壁组成2与各自的顶板组成4、5上部的连接是在中心线位置通过螺栓113固定在安装横梁114上,安装横梁通过两个相对互连的l型可调整角钢123、124用螺栓紧固件125与车顶滑槽8连接固定,方便调整;下部的连接是通过各自间壁组成自带间壁翻边用螺钉连接固定。
间壁翻边是在客室侧间壁组成和司机室侧间壁组成的加强骨架横梁116上预埋螺套117及用螺钉121固定的角铝115,角铝上焊接螺纹块120。各自顶板组成在螺纹块120对应位置开通过孔,用螺钉119及垫片118将各自顶板组成下部与客室侧间壁组成和司机室侧间壁组成连接固定。
参照图9,司机室侧间壁组成2与司机室内装侧墙6之间的插接结构是在司机室内装侧墙上安装一侧墙插接角铝201,侧墙插接角铝与连接客室侧间壁组成的插接直角铝板101相对设置,司机室侧间壁组成两侧连接端加工有水平平行的三个间隔且凸出于连接端端面的插板202,侧墙插接角铝201的其中一个直角边与司机室内装侧墙6相贴合,另一直角边与司机室侧间壁组成两侧的三个间隔且凸出的插板202形成的插槽插接,三个插板形成两个插槽,便于根据需求调整空间大小,拆卸方便,定位精准。
参照图10,司机室侧间壁组成2与地板接口通过司机室侧间壁自带方形管材205及螺钉203连接固定,方形管材205的底部延伸出一块连接板材204,通过连接板材204与地板7连接固定。
安装过程:
整个司机室间壁安装主要分为5大部分,安装顺序为两侧的客室侧间壁组成1→客室侧间壁顶板组成4→司机室间壁门3→两侧的司机室侧间壁组成2→司机室侧间壁顶板组成5,客室侧间壁组成与侧墙的接口为插接结构;与地板接口固定是在地板上提前预埋钢板,司机室侧间壁组成底部安装可现车扎钉,操作方便;与车顶接口滑槽型材用t型螺栓紧固件连接固定;客室侧间壁顶板组成4上部与安装横梁连接,通过安装横梁与客室侧间壁组成1连接,下部通过客室侧间壁组成1自带间壁翻边上钉固定。安装司机室间壁门。司机室侧间壁组成2与侧墙为插接结构;顶部固定同客室侧间壁组成;司机室侧间壁顶板组成5的安装方式与客室侧间壁顶板组成4安装方式相同。
拆卸过程:
在全自动驾驶车辆全面实现全自动,不需要司机值守情况下,该司机室间壁结构即可拆除,拆除过程中,优先拆除司机室顶板,其次从司机室侧开始,分别按司机室侧间壁顶板组成5→两侧的司机室侧间壁组成2→司机室间壁门3→客室侧间壁顶板组成4→两侧的客室侧间壁组成1的顺序拆除,完成司机室间壁的拆除,此操作省时省力,操作便捷。
整个司机室间壁结构方便安装,方便拆卸,后续维护工作量小,仅需要将司机室间壁结构拆除后,现车补修地板上钉点,保证外观美观即可,司机室内装侧墙插接条可现车拆除,封堵上钉点;仅需要对司机室顶板加改,即可满足司机室间壁拆除后的修复工作。能够实现全自动驾驶车辆的间壁的快速拆除,实现整个客室司机室的贯通。
起点商标作为专业知识产权交易平台,可以帮助大家解决很多问题,如果大家想要了解更多知产交易信息请点击 【在线咨询】或添加微信 【19522093243】与客服一对一沟通,为大家解决相关问题。
此文章来源于网络,如有侵权,请联系删除


