一种动车组轮对管理系统的制作方法



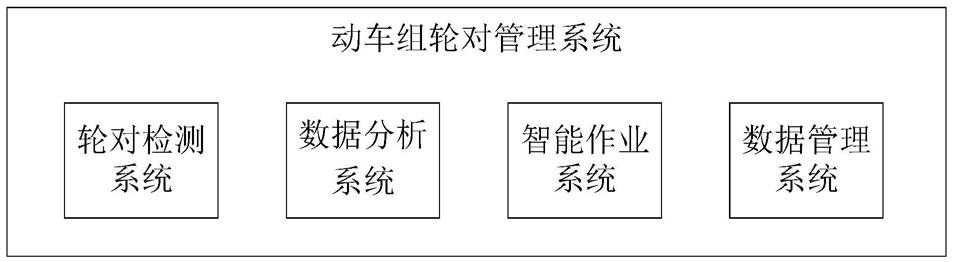
[0001]
本发明属于动车组检测领域,具体涉及一种动车组轮对管理系统。
背景技术:
[0002]
铁路是国民经济大动脉,关键基础设施和重大民生工程,是综合交通运输体系的骨干和主要交通方式之一,其中,crh系列高速动车组作为高速铁路主要的载运工具,保证和维护其安全运行显得十分的重要。轮对作为动车组的重要设备,其安全可靠的运行是动车组运营最基本的要素。一旦轮对出现故障,将严重影响高铁的安全。
[0003]
目前,国内对轮对的检测手段自动化程度较高,但由于轮对检测因素繁多,需要多种检测设备进行多级检测,现有检修手段下,动车组轮对检测一般分为四个主要部分,即正线检测、日常动态检测、定期在线检测及定期落轮检测。其中,正线检测主要为通过tads、twds、tpds在出入站完成轴承内外圈、滚子缺陷、车轮外形尺寸、车轮踏面状态、不圆度、轮轨作用的检测内容;日常动态检测主要为通过ly、le、风机及lb等在入段线咽喉处完成轮辋内部缺陷-擦伤-尺寸\受电弓压力、磨耗、中心线、车顶、车侧、车底、车轮踏面图像监视、风机异响、闸片磨耗、车轮外形、制动盘尺寸磨耗、不圆度、等效锥度的检测内容;定期在线检测主要为通过库内综合检修平台、lu、lhz、lx等在库内初级修检修线完成车底全景、关键部件可视、关键部件尺寸测量、轮辋轮辐缺陷-踏面图像、不圆度、三维测量、实心/空心车轴探伤、便携式缺陷复核等检测内容;定期落轮检测主要为通过la等设备在库内高级修检修线完成车轮车轴缺陷、车轮缺陷、车轴缺陷等检测内容。
[0004]
然而,虽然各检测设备具有高程度自动化,可以精确检测轮对特定检测内容,但各检测设备之间数据独立,多为信息孤岛,无法实现检测数据的互联互通,从而难以形成对轮对的全面质量分析与质量追踪。
技术实现要素:
[0005]
针对现有技术的以上缺陷或改进需求,本发明提供了一种动车组轮对管理系统,旨在解决由于各检测设备之间数据独立难以形成对动车组轮对的全面质量分析与质量追踪的技术问题。
[0006]
为实现上述目的,按照本发明的一个方面,提供了一种动车组轮对管理系统,该系统包括轮对检测子系统、数据分析子系统、智能作业子系统和数据管理子系统,其中,
[0007]
轮对检测子系统用于实现检测数据的采集,检测数据包括动车组轮对正线检测数据、日常动态检测数据、定期在线检测数据和定期落轮检测数据;
[0008]
数据分析子系统用于对检测数据进行数据分析,以获取动车组轮对的检测结果数据,检测结果数据包括现行运行状态和运行状态预判,将检测结果数据发送给智能作业子系统和数据管理子系统;
[0009]
智能作业子系统用于依据检测结果,结合检修作业流程数据库生成检修作业派工电子单以实现检修作业的派发,获取反馈的检修结果数据并发送给数据管理子系统;
[0010]
数据管理子系统用于依据轮对的状态类型建立对应的数据库,数据库的行以动车组的编号为主键,将每个动车组轮对的检测结果数据和检修结果数据以字段的形式存储。
[0011]
作为本发明的进一步改进,轮对检测子系统包括一个或多个正线检测设备,正线检测设备的类型包括列车滚动轴承早期故障轨边声学诊断模块、列车轮对尺寸动态检测模块和列车运行品质动态监测模块,列车滚动轴承早期故障轨边声学诊断模块用于实现动车轴承内外圈和滚子缺陷检测,列车轮对尺寸动态检测模块用于实现动车车轮外形尺寸检测,列车运行品质动态监测模块用于实现动车车轮踏面状态、不圆度和轮轨作业检测。
[0012]
作为本发明的进一步改进,轮对检测子系统包括一个或多个日常动态检测设备,日常动态检测设备的类型包括列车轮辋检测设备、列车图像监视设备、列车轴温红外检测设备和列车外形尺寸检测设备,列车轮辋检测设备用于实现动车轮辋内部缺陷、擦伤缺陷和尺寸缺陷的检测,列车图像监视设备用于实现动车车顶、车侧和车底图像监视,列车轴温红外检测设备用于实现动车轴温、风机异响、闸片磨耗的检测,列车外形尺寸检测设用于实现动车车轮外形、制动盘尺寸磨耗、不圆度、等效锥度的检测。
[0013]
作为本发明的进一步改进,轮对检测子系统包括一个或多个定期在线检测设备,定期在线检测设备的类型包括库内综合检修平台设备、列车移动式轮辋轮辐探测模块、空心轴探伤模块和便携式轮辋轮辐探测仪,库内综合检修平台设备用于实现动车车底全景、关键部件可视和关键部件尺寸测量的检测,列车移动式轮辋轮辐探测模块用于实现动车轮辋轮辐缺陷、踏面图像、不圆度和三维测量,空心轴探伤模块用于实现动车实心车轴和空心车轴探伤的检测,便携式轮辋轮辐探测仪用于实现动车便携式缺陷复核检测。
[0014]
作为本发明的进一步改进,轮对检测子系统包括固定式轮辋轮辐探测模块,固定式轮辋轮辐探测模块用于实现包括车轮车轴缺陷三级修检测的定期落轮检测。
[0015]
作为本发明的进一步改进,每个设备设置有对应的上位机,上位机与路局服务器连接,路局服务器设置有轮对检测子系统、数据分析子系统、智能作业子系统和数据管理子系统的控制软件。
[0016]
作为本发明的进一步改进,系统还设置有与各个运用所对应的调度室服务器,调度室服务器用于汇总对应运用所的检修数据,并将该检修数据上传至所述路局服务器。
[0017]
作为本发明的进一步改进,上位机获取对应设备上传的轮对指标的具体数值,依据内部存储与其检测指标所对应的寿命曲线图获取对应的轮对指标状态;
[0018]
数据分析子系统获取各个设备的轮对指标状态,依据各个设备的轮对指标状态进行现行运行状态和运行状态预判。
[0019]
作为本发明的进一步改进,轮对指标状态类型包括轴承状态、轮对外形尺寸状态、踏面状态、内部缺陷、制动盘状态、可视状态和车轴状态的一种或多种。
[0020]
作为本发明的进一步改进,检修作业流程数据库包括关于轮对轴承状态、轮对外形尺寸状态、踏面状态、内部缺陷、制动盘状态、可视状态和车轴状态的规范化检修作业流程说明。
[0021]
总体而言,通过本发明所构思的以上技术方案与现有技术相比,具有以下有益效果:
[0022]
本发明的一种动车组轮对管理系统,其覆盖了对动车组轮对的正线检测、日常动态检测、定期在线检测及定期落轮检测作业的全部检修作业范围需求,并实现数据的共享,
真正实现轮对的全方位检测。其检测全面,且监测及分析过程实现自动化,智能化,监测结果更加准确和快速。同时,其上升到路局层面的监测数据共享摆脱了以往轮对检测过程中对动车组轮对的数据孤立、不成体系的状况,使路局所属动车组的轮对,实现全生命过程周期的跟踪式检测和寿命管理,使轮对的状态管理更加准确、及时。相比于现阶段各个检测设备独立、检测仍需大量人工复检的状况,该系统大大提高了轮对日常检修效率和轮对的全寿命管理水平。
附图说明
[0023]
图1为本发明实施例的一种动车组轮对管理系统的示意图;
[0024]
图2为本发明实施例的上位机设置方式的示意图;
[0025]
图3为本发明实施例的数据上传方式的示意图。
具体实施方式
[0026]
为了使本发明的目的、技术方案及优点更加清楚明白,以下结合附图及实施例,对本发明进行进一步详细说明。应当理解,此处所描述的具体实施例仅仅用以解释本发明,并不用于限定本发明。
[0027]
此外,下面所描述的本发明各个实施方式中所涉及到的技术特征只要彼此之间未构成冲突就可以相互组合。下面结合具体实施方式对本发明进一步详细说明。
[0028]
图1为本发明实施例的一种动车组轮对管理系统的示意图。如图1所示,本发明的动车组轮对管理系统,整体组成包括轮对检测系统、数据分析系统、智能作业系统及数据管理系统。轮对管理系统包含硬件检测设备和软件数据分析及管理系统两大方面,硬件检测设备包含实现动车组轮对正线检测、日常动态检测、定期在线检测、定期落轮检测各阶段全面的技术指标测量的检测设备及其所需的数据服务器,软件数据分析及管理系统主要包含对检测设备检测到的轮对原始状态数据进行专家系统分析及数据管理的各个系统,此外还包含配合人工复检及人工作业的作业管理系统。
[0029]
可选的,轮对检测系统包括一个或多个正线检测设备,正线检测设备的类型包括滚动轴承早期故障轨边声学诊断模块(tads设备)、轮对尺寸动态检测模块(twds设备)和列车运行品质动态监测模块(tpds设备),其中,tads设备进行轴承内外圈、滚子缺陷检测,twds设备实现车轮外形尺寸检测,tpds设备实现车轮踏面状态、不圆度及轮轨作业检测。三项设备位于车站出入站线上,均通过网线连接至设备控制室内的各自上位机,上位机通过无线传输连接至所属运用所或动车段的调度室服务器。
[0030]
可选的,轮对检测子系统包括一个或多个日常动态检测设备,日常动态检测设备的类型包括列车轮辋检测设备(ly设备)、列车图像监视设备(le设备)、列车轴温红外检测设备(th设备)和列车外形尺寸检测设备(lb设备),其中,ly进行轮辋内部缺陷、擦伤缺陷、尺寸缺陷的检测,le主要实现车顶、车侧、车底图像监视,th主要实现轴温、风机异响、闸片磨耗的检测。lb主要实现车轮外形、制动盘尺寸磨耗、不圆度、等效锥度的检测。这四项设备涵盖了轮对日常动态检测的主要检测指标,四项设备均通过网线连接至设备控制室内的各自上位机,上位机通过光纤连接至调度室服务器。
[0031]
可选的,轮对检测子系统包括一个或多个定期在线检测设备,定期在线检测设备
的类型包括库内综合检修平台设备、列车移动式轮辋轮辐探测模块(lu设备)、空心轴探伤模块(lhz设备)和便携式轮辋轮辐探测仪(lx设备),库内综合检修平台实现车底全景、关键部件可视、关键部件尺寸测量,lu实现轮辋轮辐缺陷、踏面图像、不圆度及三维测量,lhz实现实心、空心车轴探伤,lx实现便携式缺陷复核。四项设备位于检修库内,前三项设备通过网线传输方式将检测数据传输至各自上位机,第四项设备通过无线传输方式将检测数据传输至上位机,四项设备上位机均通过光纤连接至调度室服务器。
[0032]
可选的,轮对检测子系统包括固定式轮辋轮辐探测模块(la设备),la设备用于实现包括车轮车轴缺陷三级修检测的定期落轮检测。
[0033]
图2为本发明实施例的上位机设置方式的示意图。如图2所示,可选的,以上每项设备物理上均为设备——上位机——路局服务器的物理连接模式,每项设备之间为并联关系,互不干扰,以保证物理结构的简单化,并能够充分发挥每项设备的具体功能,路局服务器设置有轮对检测子系统、数据分析子系统、智能作业子系统和数据管理子系统的控制软件。
[0034]
图3为本发明实施例的数据上传方式的示意图。如图3所示,可选的,数据分析系统是对检测设备采集的初始数据进行数据分析从而对动车组轮对现行状态进行判断及预测的系统。该系统包含各设备上位机的本设备分析系统、段所内调度室服务器中的轮对状态分析系统;数据判断系统则是将各个数据指标状态是否进行需要检修及现存的状态节点(占轮对该指标完好状态的百分比及一般情况下该指标的状态曲线节点)的判断显示,并将结果传递至调度室服务器内。其主要流程为:
[0035]
各个硬件设备针对各自的检测内容,检测到本设备所负责的轮对指标的具体数值。
[0036]
该数值通过网线传递至上位机后,各个设备的上位机针对检测到的具体数据进行数据分析,分析轮对的指标状态,进行百分制分数评定,具体评分方式为——各个设备上位机内部存储有轮对对于该设备检测指标所对应的寿命曲线图,寿命曲线的横坐标为寿命时间,纵坐标为该指标检测数值,以需检修的检测数值点为临界点,此处即为60分;该数值以上,根据横坐标进行等区间打分,分别为60分至100分。
[0037]
上位机将数据及评分通过光纤(正线检测设备通过无线)传递至调度室服务器中,调度室服务器根据各个设备的轮对指标状态,针对轴承状态、轮对外形尺寸状态、踏面状态、内部缺陷、制动盘状态、可视状态及车轴状态7部分,进行评级判断,分为运行良好”、“运行正常”、“运行较差”及“需检修”四个等级,若评定结果为“合格”或“不合格”,则激活智能作业系统。七部分进行评级判断的原理为:服务器内部存储专家评分系统,具体原理为先期组织技术专家,对各个检测设备的各项检测单元的检测分数对上述七部分性能的影响因子进行评估,打出百分比,各个检测设备针对该部分的百分比之和为1。将各个设备的检测分数
×
各自的影响因子即为该部分的综合诊断分数,分数按85至100、70至85及60-70分依次为“运行良好”、“运行正常”、“运行较差”,60分以下为“需检修”。
[0038]
智能作业系统包含检修作业流程数据库,作业派班系统及人工数据回填系统。若该系统激活,则由管理人员在作业派班系统中指定作业人员对需要复检或维修的轮对检测内容进行作业指派,同时作业派班系统从检修作业流程数据库(该数据库包含规范化的轮对轴承状态、轮对外形尺寸状态、踏面状态、内部缺陷、制动盘状态、可视状态及车轴状态7
部分检修作业流程说明)中提取所需的作业流程说明派发至作业人员。作业人员于派班系统中接收作业任务,根据作业流程说明进行检修作业操作,作业完成后利用手持检测设备将该项轮对指标的新职回填至人工数据回填系统,该系统将对新的轮对数据进行模拟分析(模拟检测设备上位机-服务器的过程),并将数据更新至调度室服务器中。
[0039]
数据管理系统搭建至路局服务器网络,主要架构为大型数据库,分为轮对轴承状态、轮对外形尺寸状态、踏面状态、内部缺陷、制动盘状态、可视状态及车轴状态7个小数据库,每个小数据库的行均以该路局所辖动车组的编号为主键,将每个动车组的轮对的检测记录及检修记录均为字段存储起来。这些数据是由路局内所辖各个运用所的检修数据最终汇总至该运用所的调度室服务器后,调度室服务器再将轮对状态结果上传至路局服务器中,最终实现路局所辖动车轮对的检测状态全记录的。
[0040]
本领域的技术人员容易理解,以上所述仅为本发明的较佳实施例而已,并不用以限制本发明,凡在本发明的精神和原则之内所作的任何修改、等同替换和改进等,均应包含在本发明的保护范围之内。
起点商标作为专业知识产权交易平台,可以帮助大家解决很多问题,如果大家想要了解更多知产交易信息请点击 【在线咨询】或添加微信 【19522093243】与客服一对一沟通,为大家解决相关问题。
此文章来源于网络,如有侵权,请联系删除



tips