一种固定支架的制作方法



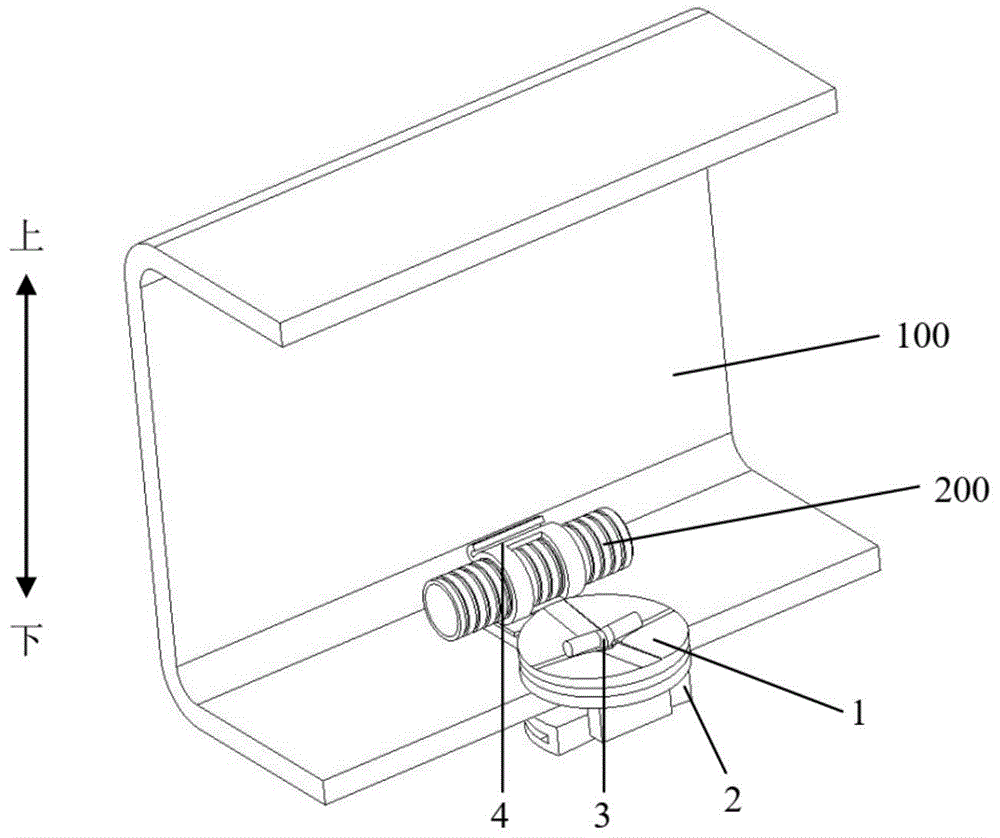
本实用新型涉及汽车零部件技术领域,尤其涉及一种固定支架。
背景技术:
目前,随着电气设备的应用逐渐增多,商用车用管线束也随之增多,固定支架主要用于将管线束固定在车架上。
传统商用车用固定支架多以普通支架通过连接孔与车架或被固定件连接,其主要的缺点为:1、车架必须开孔,固定支架位置固定,不易更改,布置灵活性差;但是,管线束最大的特点就是布置的多变性和灵活性,固定支架的布置位置千变万化,如果均采用传统的固定支架,需在实际样车出来前先确定好被固定件上孔的位置;2、实际车辆装配过程中,由于管线束为柔性连接,其装配的公差较大,与已知设定的传统固定支架的匹配程度较低,时常会遇到管线束无法正确装入既定固定支架里的现象,或者出现由于管线束固定位置变化多样,管线束得不到固定支架的有效固定的问题。
因此,亟需提出一种固定支架,能够解决车架上必须为固定支架开固定孔,使得固定支架固定位置过于固定,不灵活,不能与管线束理顺的灵活度匹配等问题,以适应管线束柔性布置,灵活性要求高,多变性高的特点,实现对管线束的有效固定。
技术实现要素:
本实用新型的目的在于提出一种固定支架,能够解决车架上必须为固定支架开固定孔,使得固定支架固定位置过于固定,不灵活,不能与管线束理顺的灵活度匹配等问题,以适应管线束柔性布置,灵活性要求高,多变性高的特点,实现对管线束的有效固定。
为达此目的,本实用新型采用以下技术方案:
一种固定支架,用于固定在车架上,包括:
第一夹板;
第二夹板,与所述第一夹板相对间隔设置,以配合形成夹持所述车架的夹口;
旋转夹紧杆,包括可转动的贯穿于所述第一夹板和所述第二夹板上的转轴部,和分别设于所述转轴部两端的第一抵靠部和第二抵靠部;
其中,所述第一夹板的远离所述第二夹板的一端的端面上形成有第一低位端面和第一高位端面,所述第一低位端面的上表面低于所述第一高位端面,且均能与所述第一抵靠部抵靠,所述第二夹板的远离所述第一夹板的一端能与所述第二抵靠部抵靠。
可选地,所述第二夹板的背对所述第一夹板的端面上形成有第二低位端面和第二高位端面;
其中,所述第一抵靠部压靠于所述第一高位端面上时,所述第二抵靠部能压靠于所述第二高位端面上;所述第一抵靠部压靠于所述第一低位端面上时,所述第二抵靠部能够压靠于所述第二低位端面上。
可选地,沿所述转轴部的轴线方向,所述第二高位端面上的各位置处到所述夹口的距离大于所述第二低位端面上各位置处到所述夹口的距离。
可选地,所述第一夹板包括:
主体部,正对于所述第二夹板,所述第一低位端面和所述第一高位端面形成于所述主体部背对所述第二夹板的端面上;
导向部,设置于所述主体部上,所述导向部上开设有沿所述转轴部的轴线方向延伸的导向滑槽,所述第二夹板的主体的一侧设置有导向块,所述导向块滑动插设于所述导向滑槽中,以用于限定所述第二夹板沿所述转轴部的轴线方向移动。
可选地,所述主体部包括:
第一夹紧部,正对所述第二夹板设置,所述第一夹紧部能够压靠于所述车架上;
第一抵接部,设置于所述第一夹紧部的背对所述夹口的一端上,所述第一抵接部的背对所述第一夹紧部的一端上形成有所述第一低位端面和所述第一高位端面;
其中,所述第一低位端面呈与所述转轴部的轴线相垂直的平面结构;所述第一高位端面呈与所述转轴部的轴线不相垂直的平面结构,且所述第一高位端面上各位置处到所述夹口的距离大于所述第一低位端面上的各位置处到所述夹口的距离。
可选地,所述第一高位端面上开设有第一限位凹槽,所述第一限位凹槽能够容纳所述第一抵靠部,以限制所述转轴部转动。
可选地,所述第一低位端面上开设有第二限位凹槽,所述第二限位凹槽能够容纳所述第一抵靠部,以限制所述转轴部转动。
可选地,所述固定支架还包括:
零件固定件,用于承载待固定件;其中,所述第一夹板上设置有所述零件固定件,和/或,所述第二夹板上设置有所述零件固定件。
可选地,所述零件固定件包括:
夹箍本体部,设置于所述第一夹板上,所述夹箍本体部的侧壁上开设有一伸缩开口;
加强部,其一体成型的设置于所述夹箍本体部的伸缩开口的边缘上。
可选地,所述第一夹板、所述第二夹板和所述旋转夹紧杆中至少一个的材质为弹性材质。
本实用新型的有益效果为:
本实用新型的第二夹板与第一夹板间隔设置以形成夹持车架的夹口。旋转夹紧杆的转轴部可转动的贯穿于第一夹板和第二夹板上,转轴部两端分别设置有第一抵靠部和第二抵靠部。第一夹板的远离第二夹板的一端的端面上形成有第一低位端面和第一高位端面,第一低位端面的上表面低于第一高位端面,且均能与第一抵靠部抵靠,第二夹板的远离第一夹板的一端能与第二抵靠部抵靠。用户旋拧旋转夹紧杆,当第一抵靠部抵靠于第一高位端面上,第二抵靠部抵靠于第二夹板远离第一夹板的一端上时,夹口的口径减小,进而固定支架夹紧固定在车架上;用户旋拧旋转夹紧杆,当第一抵靠部转动到第一低位端面的位置上时,夹口的口径增大,进而固定支架松开车架。与现有的用于将待固定件固定在车架上的固定支架相比,本实用新型对固定支架在车架上的固定方式进行了改进,其无需在车架上开固定孔,采用螺栓紧固的方式进行固定,而是通过旋拧旋转夹紧杆的方式,便可使得固定支架灵活的夹紧在车架的不同位置上,实现固定支架在车架上的有效固定,操作方便。
附图说明
图1是本实用新型提供的固定支架在车架上的结构示意图;
图2是本实用新型提供的固定支架的剖面结构示意图;
图3是本实用新型提供的固定支架的第一夹板的结构示意图;
图4是本实用新型提供的固定支架的第二夹板的结构示意图。
图中:
100-车架;200-待固定件;
1-第一夹板;11-主体部;111-第一夹紧部;112-第一抵接部;1121-第一低位端面;1122-第一高位端面;1123-第一限位凹槽;12-导向部;121-导向滑槽;13-第一通孔;
2-第二夹板;21-第二抵接部;211-第二低位端面;212-第二高位端面;213-第三限位凹槽;22-第二夹紧部;23-导向块;24-第二通孔;
3-旋转夹紧杆;31-转轴部;32-第一抵靠部;33-第二抵靠部;
4-零件固定件;41-夹箍本体部;42-加强部。
具体实施方式
为使本实用新型解决的技术问题、采用的技术方案和达到的技术效果更加清楚,下面结合附图并通过具体实施方式来进一步说明本实用新型的技术方案。
在本实用新型的描述中,除非另有明确的规定和限定,术语“相连”、“连接”、“固定”应做广义理解,例如,可以是固定连接,也可以是可拆卸连接,或成一体;可以是机械连接,也可以是电连接;可以是直接相连,也可以通过中间媒介间接相连,可以是两个元件内部的连通或两个元件的相互作用关系。对于本领域的普通技术人员而言,可以具体情况理解上述术语在本实用新型中的具体含义。
在本实用新型中,除非另有明确的规定和限定,第一特征在第二特征之“上”或之“下”可以包括第一和第二特征直接接触,也可以包括第一和第二特征不是直接接触而是通过它们之间的另外的特征接触。而且,第一特征在第二特征“之上”、“上方”和“上面”包括第一特征在第二特征正上方和斜上方,或仅仅表示第一特征水平高度高于第二特征。第一特征在第二特征“之下”、“下方”和“下面”包括第一特征在第二特征正下方和斜下方,或仅仅表示第一特征水平高度小于第二特征。
在本实施例的描述中,术语“上”、“下”、“左”、“右”等方位或位置关系为基于附图所示的方位或位置关系,仅是为了便于描述和简化操作,而不是指示或暗示所指的装置或元件必须具有特定的方位、以特定的方位构造和操作,因此不能理解为对本实用新型的限制。此外,术语“第一”、“第二”仅仅用于在描述上加以区分,并没有特殊的含义。
如图1-3所示,本实施例提出了一种固定支架,固定支架固定在车架100上,固定支架主要包括第一夹板1、第二夹板2和旋转夹紧杆3。第二夹板2与第一夹板1相对间隔设置,以配合形成夹持车架100的夹口,车架100上凸设有呈板状的侧壁,实际使用时,夹口用于夹紧于车架200的侧壁边缘处。其中,旋转夹紧杆3包括可转动的贯穿于第一夹板1和第二夹板2上的转轴部31,转轴部31的一端上设置有能够抵靠于第一夹板1远离第二夹板2的一端的第一抵靠部32,转轴部31的另一端上设置有能够抵靠于第二夹板2远离第一夹板1的一端的第二抵靠部33;第一夹板1的远离第二夹板2的一端的端面上形成有第一低位端面1121和第一高位端面1122,第一低位端面1121的上表面低于第一高位端面1122,且均能与第一抵靠部32抵靠;旋拧旋转夹紧杆3的转轴部31,当第一抵靠部32压靠于第一高位端面1122上,且第二抵靠部33压靠于第二夹板2远离第一夹板1的一端上时,夹口的口径能减小以夹紧车架200的侧壁边缘处;当第一抵靠部32转动至第一低位端面1121的位置上时,夹口的口径增大以松开车架200的侧壁边缘处。
此外,为了使得第二夹板2能够相对第一夹板1进行稳定的靠近或者远离运动。如图2-4所示,本实施例中,第一夹板1包括主体部11和导向部12。主体部11正对于第二夹板2,第一低位端面1121和第一高位端面1122形成于主体部11背对第二夹板2的端面上;导向部12设置于主体部11上,导向部12上开设有沿转轴部31的轴线方向延伸的导向滑槽121,第二夹板2的主体的一侧设置有导向块23,导向块23滑动插设于导向滑槽121中,以用于限定第二夹板2沿转轴部31的轴线方向移动。
而对于第一低位端面1121和第一高位端面1122的具体结构,如图2-3所示,沿转轴部31的轴线方向,第一高位端面1122上的各位置处到夹口的距离大于第一低位端面1121上的各位置处到夹口的距离。更进一步地,主体部11包括第一夹紧部111和第一抵接部112。第一夹紧部111正对第二夹板2设置,第一夹紧部111能够压靠于车架上;第一抵接部112设置于第一夹紧部111的背对夹口的一端上,第一低位端面1121和第一高位端面1122形成于第一抵接部112的背对第一夹紧部111的一端上;其中,第一低位端面1121呈与转轴部31的轴线相垂直的平面结构;第一高位端面1122呈与转轴部31的轴线不相垂直的平面结构,且第一高位端面1122上各位置处到夹口的距离大于第一低位端面1121上的各位置处到夹口的距离。具体而言,如图2-3所示,本实施例中,第一抵接部112为类似半圆板状结构,且有两个第一抵接部112,两个第一抵接部112相互一体成型为圆板状结构,两个第一抵接部112的第一低位端面1121共同形成于两个第一抵接部112相连的位置,圆板状结构的中部位置开设有第一通孔13,转轴部31穿设于第一通孔13中。如图2所示,沿夹口的开口端向夹口的内部的方向,本实施例的其中一个第一抵接部112上的各位置沿转轴部31的轴线方向上到夹块的距离逐渐减小,进而实现该第一抵接部112的倾斜设置,另一个第一抵接部112则以共同形成第一低位端面1121的连接位置为对称部位进行对称设置,两个第一抵接部112配合形成圆板状结构。
与现有的用于将待固定件200固定在车架100上的固定支架相比,本实施例对固定支架在车架100上的固定方式进行了改进,其无需在车架100上开固定孔,然后采用螺栓紧固的方式进行固定,而是通过旋拧旋转夹紧杆3的方式来将固定支架夹紧固定在车架100上。当第一抵靠部32压靠于第一高位端面1122上,且第二抵靠部33压靠于第二夹板2远离第一夹板1的一端上时,夹口的口径减小,便可使得固定支架灵活的夹紧在车架100的不同位置上,进而实现固定支架在车架100上的有效固定,操作简单方便。当第一抵靠部32转动至第一低位端面1121的位置上时,夹口的口径增大,进而松开车架100,便可取下固定支架或者调整固定支架的位置,使用灵活方便。
进一步地,为了将待固定件200固定在固定支架上。如图1-2所示,本实施例中,固定支架还包括用于承载待固定件200的零件固定件4。其中,第一夹板1上设置有零件固定件4。在其它实施例中,也可以同时在第二夹板2上设置一个零件固定件4,或者仅在第二夹板2上设置一个零件固定件4。具体而言,本实施例中,零件固定件4为管线束固定件,其用于将管线束固定在固定支架上。其中,零件固定件4包括夹箍本体部41和加强部42。夹箍本体部41设置于第一夹板1上,夹箍本体部41的侧壁上开设有一伸缩开口(图中未标识),管线束贯穿固定在夹箍本体部41上;加强部42为加强筋结构,其一体成型的设置于夹箍本体部41的伸缩开口的边缘上,进而起到强化伸缩开口的硬度的作用。
需要说明的是,在其它实施例中,零件固定件4也可以根据实际需求设计为用于承载各种不同的待固定件的其它结构,例如可以是与待固定件采用螺栓紧固连接的连接板,或者是和待固定件进行插接连接插接板,待固定件上设置有插块,零件固定件4上设置有插槽,插槽和插块配合插接,进而将待固定件固定连接在零件固定件4上。本实施例的固定支架能够适应管线束柔性布置,灵活性要求高,多变性高的特点,实现对管线束的有效固定。
同理,如图2和图4所示,本实施例中,第二夹板2的结构与第一夹板1的结构原理基本相同。具体而言,第二夹板2的背对第一夹板1的端面上形成有第二低位端面211和第二高位端面212,沿转轴部31的轴线方向,第二高位端面212上的各位置处到夹口的距离大于第二低位端面211上各位置处到夹口的距离,进而保证第二抵靠部33抵压于第二高位端面212上时能够促进夹口的口径的减小,来夹紧车架100。其中,当第一抵靠部32压靠于第一高位端面1122上时,第二抵靠部33压靠于第二高位端面212上;第一抵靠部32压靠于第一低位端面1121上时,第二抵靠部33能够压靠于第二低位端面211上,由于第二夹板2设计了第二低位端面211和第二高位端面212,同时第一夹板1上设计了第一低位端面1121和第一高位端面1122,当第一抵靠部32压靠于第一高位端面1122上时,第二抵靠部33同步压靠于第二高位端面212上,进而能够使得夹口的口径缩小的更小,进而产生更大的夹紧力,使得夹紧更加稳定可靠。
进一步地,当第一抵靠部32转动到第一高位端面1122上之后,为了固定第一抵靠部32的位置,防止转轴部31转动,进而使得第一抵靠部32偏位。如图3所示,本实施例中,第一高位端面1122上开设有第一限位凹槽1123,第一限位凹槽1123能够容纳第一抵靠部32,以限制转轴部31转动,进而避免了第一抵靠部32偏位而导致夹紧失效的问题。其中,如图3所示,本实施例中的第一限位凹槽1123的端部通向第一高位端面1122沿转轴部31的轴线方向相距夹口的距离最远的位置,第一限位凹槽1123穿过两个第一抵接部112一体形成的圆饼状结构的中心位置,第一通孔13位于圆饼状结构的中心位置处。
同理,当第一抵靠部32转动到第一低位端面1121上之后,为了固定第一抵靠部32的位置,防止转轴部31转动进而使得第一抵靠部32偏位。如图3所示,第一低位端面1121上开设有第二限位凹槽(图中未标识),第二限位凹槽开设于第一低位端面1121的整个端面上,第二限位凹槽能够容纳第一抵靠部32,以限制转轴部31转动。其中,本实施例中的第二限位凹槽与第一限位凹槽1123相垂直,第一通孔13位于第二限位凹槽的中间位置。
而除了通过在第一高位端面1122上开设第一限位凹槽1123以及在第一低位端面1121上开设第二限位凹槽来限位第一抵靠部32之外。当完成对旋转部31的旋拧后,为了也能够限制第二抵靠部33的位置,以防止其发生移动偏位。如图2和图4所示,本实施例中,在第二高位端面212上开设有第三限位凹槽213,第三限位凹槽213能够容纳第二抵靠部33,以限制转轴部31转动,进而避免了第二抵靠部33的偏位。具体而言,第二夹板2上开设有第二通孔24,贯穿第一通孔13的转轴部31同时贯穿第二通孔24。本实施例中的第三限位凹槽213的一端通向第二高位端面212沿转轴部31的轴线方向相距夹口的距离最远的一端,第三限位凹槽213的另一端通向第二高位端面212沿转轴部31的轴线方向相距夹口的距离最近的一端,且经过第二通孔24,进而当第二抵靠部33转到第二高位端面212上时,可以通过第三限位凹槽213来防止第二抵靠部33的移动偏移。
同样的,如图2和图4所示,第二低位端面211上开设有第四限位凹槽(图中未标识),第四限位凹槽开设于第二低位端面211的整个端面上,第四限位凹槽能够容纳第二抵靠部33,以限制转轴部31转动。具体而言,本实施例中的第四限位凹槽与第三限位凹槽213相垂直,第二通孔24位于第二限位凹槽的中间位置处,进而当第二抵靠部33转到第二低位端面211上时,可以通过第四限位凹槽213来防止第二抵靠部33的移动偏移。需要说明的是,本实施例中的旋转夹紧杆3呈工字型形状,在其它实施例中,旋转夹紧杆3也可以呈c字型形状,旋转夹紧杆3的材质为弹性材质,本实施例为弹性橡胶材质,其他实施例也可以是弹性硅胶材质,同时第一夹板1和第二夹板2也可以是弹性橡胶材质,弹性橡胶材质的第一夹板1、第二夹板2和旋转夹紧杆3能够发生弹性形变,进而能够通过旋拧旋转夹紧杆3的方式使得第一夹板1和第二夹板2形成的夹口夹紧于车架100的侧壁边缘上。需要说明的是,第一夹板1、第二夹板2和旋转夹紧杆3中至少一个零件的材质为弹性材质也能实现第一夹板1和第二夹板2形成的夹口夹紧于车架100的侧壁边缘的效果。
以上内容仅为本实用新型的较佳实施例,对于本领域的普通技术人员,依据本实用新型的思想,在具体实施方式及应用范围上均会有改变之处,本说明书内容不应理解为对本实用新型的限制。
起点商标作为专业知识产权交易平台,可以帮助大家解决很多问题,如果大家想要了解更多知产交易信息请点击 【在线咨询】或添加微信 【19522093243】与客服一对一沟通,为大家解决相关问题。
此文章来源于网络,如有侵权,请联系删除


