一种后轮毂优化结构及其制作工艺的制作方法



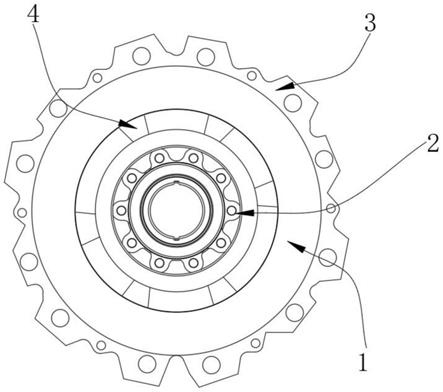
[0001]
本发明涉及轮毂制造技术领域,具体为一种后轮毂优化结构及其制作工艺。
背景技术:
[0002]
轮毂是轮胎内廓轮钢通过立柱连接的轮芯旋转部分,即支撑轮胎的中心装在轴上的金属部件。又叫轮圈、钢圈、轱辘、胎铃。轮毂根据直径、宽度、成型方式、材料不同种类繁多。轿车的轮毂轴承过去最多的是成对使用单列圆锥滚子或球轴承。随着技术的发展,轿车已经广泛的使用轿车轮毂单元。轮毂轴承单元的使用范围和使用量日益增长,已经发展到了第三代。第一代是由双列角接触轴承组成。第二代在外滚道上有一个用于将轴承固定的法兰,可简单的将轴承套到轮轴上用螺母固定。使得汽车的维修变的容易。第三代轮毂轴承单元是采用了轴承单元和防抱刹系统相配合。轮毂单元设计成有内法兰和外法兰,内法兰用螺栓固定在驱动轴上,外法兰将整个轴承安装在一起。在车轮行业目前使用率比较高主要是铝合金材质轮毂和钢材质轮毂,由于两种材质的轮毂各有自己的优点,所以目前都有一定的市场竞争力。现有的后轮毂材质为qt450-10,抗拉强度和屈服强度力度达不到要求,导致经常出现断裂的情况出现,同时现有的轮毂耐腐蚀性较差,容易受到外界腐蚀环境的影响,造成轮毂使用寿命变短,为此,提出一种后轮毂优化结构及其制作工艺。
技术实现要素:
[0003]
本发明的目的在于提供一种后轮毂优化结构及其制作工艺,以解决上述背景技术中提出的问题。
[0004]
为实现上述目的,本发明提供如下技术方案:一种后轮毂优化结构,包括胎圈座,所述胎圈座的外侧壁设置有轮缘,所述轮缘的外侧壁设置有轮辋,所述胎圈座的内侧壁设置有轮辐,所述轮辐的一端设置有车轮饰板。
[0005]
另外,本发明还提出了一种后轮毂优化结构的制作工艺,包括以下步骤:
[0006]
s1、准备铸铁原料,将原料放置于熔炼炉中炼化,加温至1350~1450℃,将铸铁熔炼为液体状态,盛放至熔炼铁液池备用;
[0007]
s2、对熔炼完成的铸铁液倒入精炼设备进行精炼,去除铸铁熔炼液中的碳杂质;
[0008]
s3、将液体转入锻造机中进行锻造制得坯料,锻造机设置壁厚厚度为7mm,锻造机第一次锻造的方式为将坯料置于温度为350~450℃的模具中进行锻造,并保温2.5~3.5h;
[0009]
s4、第二次锻造为等温淬火,将坯料从锻造机中取出,然后将加热的坯料放入温度为稍高于铸铁的ms点270~400℃的硝盐浴或碱浴中,保温30~60min使其完成贝氏体转变,使坯料从奥氏体转变为贝氏体,然后取出置于空气中冷却,获得毛坯;
[0010]
s5、使用x射线探伤设备对毛坯进行检测,观察毛坯是否带有缩松、针孔缺陷,并对毛坯的外观进行检测;
[0011]
s6、对毛坯进行热处理,加温至550~750℃,然后对毛坯保温存放;
[0012]
s7、将保温存放进行完毕热处理的毛坯移动至机加工区域,进行包括冲中心孔、粗
成型、旋压成型、冲风孔、精车档圈槽和冲螺纹孔的精车和精钻工序;
[0013]
s8、对进行完成机加工的后轮毂进行打磨工作,将冲型和钻孔处的毛边和毛刺打磨去除掉,使毛坯的表面更精细;
[0014]
s9、对轮毂进行动平衡检测和气密性试验;
[0015]
s10、对轮毂进行工序为除尘预处理、喷底粉、喷色漆和喷透明粉的涂装工艺流程。
[0016]
作为本技术方案的进一步优选的:在s9中,气密性检测包括水压试验和氦气质谱漏气试验。
[0017]
作为本技术方案的进一步优选的:在s1中,熔炼炉为塔式炉、感应炉、倾转炉、固定炉中的一种。
[0018]
作为本技术方案的进一步优选的:在s2中,铸铁熔炼液的精炼方法为通入管路法、钟罩压入法和精炼机。
[0019]
作为本技术方案的进一步优选的:在s3中,第一次锻造的成型工艺分为金属型重力铸造、低压铸造、挤压铸造和旋压工艺。
[0020]
作为本技术方案的进一步优选的:在s4中,经过等温淬火处理后的轮毂毛坯材质标准为qtd1050-6。
[0021]
作为本技术方案的进一步优选的:在s10中,轮毂涂装前的预处理工序为水洗处理、酸洗处理、碱洗处理和磷化。
[0022]
与现有技术相比,本发明的有益效果是:本发明通过对产品结构优化及工艺的优化,使用等温淬火工艺,材料由以前qt450-10的标准提升到qtd1050-6的标准,性能极大的提高,提高了车轮轮毂的抗拉强度及屈服强度、延伸率,同时通过将轮毂的厚度设置为7mm,使轮毂的重量减轻,通过对产品的表面进行涂装,使产品具有较好的耐腐蚀性和防磨效果,维持轮毂的使用寿命。
附图说明
[0023]
图1为本发明的结构示意图;
[0024]
图2为本发明的侧视图。
[0025]
图中:1、胎圈座;2、车轮饰板;3、轮缘;4、轮辐;5、轮辋。
具体实施方式
[0026]
下面将结合本发明实施例中的附图,对本发明实施例中的技术方案进行清楚、完整地描述,显然,所描述的实施例仅仅是本发明一部分实施例,而不是全部的实施例。基于本发明中的实施例,本领域普通技术人员在没有做出创造性劳动前提下所获得的所有其他实施例,都属于本发明保护的范围。
[0027]
实施例一
[0028]
请参阅图1-2,本发明提供一种技术方案:一种后轮毂优化结构,包括胎圈座1,胎圈座1的外侧壁设置有轮缘3,轮缘3的外侧壁设置有轮辋5,胎圈座1的内侧壁设置有轮辐4,轮辐4的一端设置有车轮饰板2。
[0029]
另外,本发明还提出了一种后轮毂优化结构的制作工艺,包括以下步骤:
[0030]
s1、准备铸铁原料,将原料放置于熔炼炉中炼化,加温至1350℃,将铸铁熔炼为液
体状态,盛放至熔炼铁液池备用;
[0031]
s2、对熔炼完成的铸铁液倒入精炼设备进行精炼,去除铸铁熔炼液中的碳杂质;
[0032]
s3、将液体转入锻造机中进行锻造制得坯料,锻造机设置壁厚厚度为7mm,锻造机第一次锻造的方式为将坯料置于温度为350℃的模具中进行锻造,并保温2.5h;
[0033]
s4、第二次锻造为等温淬火,将坯料从锻造机中取出,然后将加热的坯料放入温度为稍高于铸铁的ms点270℃的硝盐浴中,保温30min使其完成贝氏体转变,使坯料从奥氏体转变为贝氏体,然后取出置于空气中冷却,获得毛坯;
[0034]
s5、使用x射线探伤设备对毛坯进行检测,观察毛坯带有缩松、针孔缺陷,并对毛坯的外观进行检测;
[0035]
s6、对毛坯进行热处理,加温至550℃,然后对毛坯保温存放;
[0036]
s7、将保温存放进行完毕热处理的毛坯移动至机加工区域,进行包括冲中心孔、粗成型、旋压成型、冲风孔、精车档圈槽和冲螺纹孔的精车和精钻工序;
[0037]
s8、对进行完成机加工的后轮毂进行打磨工作,将冲型和钻孔处的毛边和毛刺打磨去除掉,使毛坯的表面更精细;
[0038]
s9、对轮毂进行动平衡检测和气密性试验;
[0039]
s10、对轮毂进行工序为除尘预处理、喷底粉、喷色漆和喷透明粉的涂装工艺流程。
[0040]
本实施例中,具体的:在s9中,气密性检测包括水压试验和氦气质谱漏气试验;水压试验是在≥0.4mpa的气压下保压30s,通过目测观察水中铝轮毂漏气时的气泡来检验铝轮毂的漏气情况,氦气质谱漏气试验是利用氦气质谱分析的原理,能够快速自动检测氦气的泄漏情况,优选为氦气质谱漏气试验。
[0041]
本实施例中,具体的:s1中,熔炼炉优选为塔式炉。
[0042]
本实施例中,具体的:在s2中,铸铁熔炼液的精炼方法优选为精炼机。
[0043]
本实施例中,具体的:在s3中,第一次锻造的成型工艺优选为金属型重力铸造。
[0044]
本实施例中,具体的:在s4中,经过等温淬火处理后的轮毂毛坯材质标准为qtd1050-6。
[0045]
本实施例中,具体的:在s10中,轮毂涂装前的预处理工序为水洗处理、酸洗处理、碱洗处理和磷化。
[0046]
实施例二
[0047]
请参阅图1-2,本发明提供一种技术方案:一种后轮毂优化结构,包括胎圈座1,胎圈座1的外侧壁设置有轮缘3,轮缘3的外侧壁设置有轮辋5,胎圈座1的内侧壁设置有轮辐4,轮辐4的一端设置有车轮饰板2。
[0048]
另外,本发明还提出了一种后轮毂优化结构的制作工艺,包括以下步骤:
[0049]
s1、准备铸铁原料,将原料放置于熔炼炉中炼化,加温至1400℃,将铸铁熔炼为液体状态,盛放至熔炼铁液池备用;
[0050]
s2、对熔炼完成的铸铁液倒入精炼设备进行精炼,去除铸铁熔炼液中的碳杂质;
[0051]
s3、将液体转入锻造机中进行锻造制得坯料,锻造机设置壁厚厚度为7mm,锻造机第一次锻造的方式为将坯料置于温度为400℃的模具中进行锻造,并保温3h;
[0052]
s4、第二次锻造为等温淬火,将坯料从锻造机中取出,然后将加热的坯料放入温度为稍高于铸铁的ms点350℃的硝盐浴中,保温45min使其完成贝氏体转变,使坯料从奥氏体
转变为贝氏体,然后取出置于空气中冷却,获得毛坯;
[0053]
s5、使用x射线探伤设备对毛坯进行检测,观察毛坯带有缩松、针孔缺陷,并对毛坯的外观进行检测;
[0054]
s6、对毛坯进行热处理,加温至650℃,然后对毛坯保温存放;
[0055]
s7、将保温存放进行完毕热处理的毛坯移动至机加工区域,进行包括冲中心孔、粗成型、旋压成型、冲风孔、精车档圈槽和冲螺纹孔的精车和精钻工序;
[0056]
s8、对进行完成机加工的后轮毂进行打磨工作,将冲型和钻孔处的毛边和毛刺打磨去除掉,使毛坯的表面更精细;
[0057]
s9、对轮毂进行动平衡检测和气密性试验;
[0058]
s10、对轮毂进行工序为除尘预处理、喷底粉、喷色漆和喷透明粉的涂装工艺流程。
[0059]
本实施例中,具体的:在s9中,气密性检测包括水压试验和氦气质谱漏气试验;水压试验是在≥0.4mpa的气压下保压30s,通过目测观察水中铝轮毂漏气时的气泡来检验铝轮毂的漏气情况,氦气质谱漏气试验是利用氦气质谱分析的原理,能够快速自动检测氦气的泄漏情况,优选为氦气质谱漏气试验。
[0060]
本实施例中,具体的:s1中,熔炼炉优选为感应炉。
[0061]
本实施例中,具体的:在s2中,铸铁熔炼液的精炼方法优选为精炼机。
[0062]
本实施例中,具体的:在s3中,第一次锻造的成型工艺优选为金属型重力铸造。
[0063]
本实施例中,具体的:在s4中,经过等温淬火处理后的轮毂毛坯材质标准为qtd1050-6。
[0064]
本实施例中,具体的:在s10中,轮毂涂装前的预处理工序为水洗处理、酸洗处理、碱洗处理和磷化。
[0065]
实施例三
[0066]
请参阅图1-2,本发明提供一种技术方案:一种后轮毂优化结构,包括胎圈座1,胎圈座1的外侧壁设置有轮缘3,轮缘3的外侧壁设置有轮辋5,胎圈座1的内侧壁设置有轮辐4,轮辐4的一端设置有车轮饰板2。
[0067]
另外,本发明还提出了一种后轮毂优化结构的制作工艺,包括以下步骤:
[0068]
s1、准备铸铁原料,将原料放置于熔炼炉中炼化,加温至1450℃,将铸铁熔炼为液体状态,盛放至熔炼铁液池备用;
[0069]
s2、对熔炼完成的铸铁液倒入精炼设备进行精炼,去除铸铁熔炼液中的碳杂质;
[0070]
s3、将液体转入锻造机中进行锻造制得坯料,锻造机设置壁厚厚度为7mm,锻造机第一次锻造的方式为将坯料置于温度为450℃的模具中进行锻造,并保温3.5h;
[0071]
s4、第二次锻造为等温淬火,将坯料从锻造机中取出,然后将加热的坯料放入温度为稍高于铸铁的ms点400℃的碱浴中,保温60min使其完成贝氏体转变,使坯料从奥氏体转变为贝氏体,然后取出置于空气中冷却,获得毛坯;
[0072]
s5、使用x射线探伤设备对毛坯进行检测,观察毛坯带有缩松、针孔缺陷,并对毛坯的外观进行检测;
[0073]
s6、对毛坯进行热处理,加温至750℃,然后对毛坯保温存放;
[0074]
s7、将保温存放进行完毕热处理的毛坯移动至机加工区域,进行包括冲中心孔、粗成型、旋压成型、冲风孔、精车档圈槽和冲螺纹孔的精车和精钻工序;
[0075]
s8、对进行完成机加工的后轮毂进行打磨工作,将冲型和钻孔处的毛边和毛刺打磨去除掉,使毛坯的表面更精细;
[0076]
s9、对轮毂进行动平衡检测和气密性试验;
[0077]
s10、对轮毂进行工序为除尘预处理、喷底粉、喷色漆和喷透明粉的涂装工艺流程。
[0078]
本实施例中,具体的:在s9中,气密性检测包括水压试验和氦气质谱漏气试验;水压试验是在≥0.4mpa的气压下保压30s,通过目测观察水中铝轮毂漏气时的气泡来检验铝轮毂的漏气情况,氦气质谱漏气试验是利用氦气质谱分析的原理,能够快速自动检测氦气的泄漏情况,优选为氦气质谱漏气试验。
[0079]
本实施例中,具体的:s1中,熔炼炉优选为固定炉。
[0080]
本实施例中,具体的:在s2中,铸铁熔炼液的精炼方法优选为钟罩压入法。
[0081]
本实施例中,具体的:在s3中,第一次锻造的成型工艺优选为金属型重力铸造。
[0082]
本实施例中,具体的:在s4中,经过等温淬火处理后的轮毂毛坯材质标准为qtd1050-6。
[0083]
本实施例中,具体的:在s10中,轮毂涂装前的预处理工序为水洗处理、酸洗处理、碱洗处理和磷化。
[0084]
尽管已经示出和描述了本发明的实施例,对于本领域的普通技术人员而言,可以理解在不脱离本发明的原理和精神的情况下可以对这些实施例进行多种变化、修改、替换和变型,本发明的范围由所附权利要求及其等同物限定。
起点商标作为专业知识产权交易平台,可以帮助大家解决很多问题,如果大家想要了解更多知产交易信息请点击 【在线咨询】或添加微信 【19522093243】与客服一对一沟通,为大家解决相关问题。
此文章来源于网络,如有侵权,请联系删除
相关标签: 汽车轮毂



tips