一种特种沙地轮胎及其耐磨检测装置的制作方法



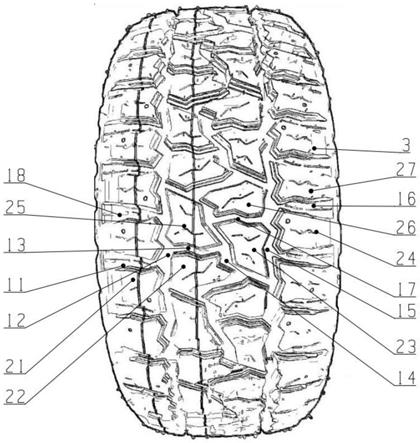
[0001]
本发明涉及车辆轮胎技术领域,具体地说,涉及一种特种沙地轮胎及其耐磨检测装置。
背景技术:
[0002]
全地形轮胎在沙丘地形上行驶时,因沙地颗粒较为松软,轮胎较难集结以提供相应的牵引力,从而造成轮胎行驶的操控性不佳的现象,特别是在前轮部位常发生操控反应过轻的现象。胎面花纹块横贯整个胎面宽度,为使轮胎发挥更好的牵引性也常于胎肩部采用曲面弧度的设计。此种胎面花纹结构的轮胎可使花纹块快速切入沙地以提升牵引性能,但在沙地上转弯行驶时,因轮胎的接地面积较低,胎面横向花纹沟较大,容易发生转弯时滑移过度而引起的转弯操控性不佳的问题,同时在轮胎直进行驶过程中,因为轮胎先接地端为光滑的曲面,也容易发生沙地颗粒无法有效集结,而产生直进牵引性能下降的问题,由于其结构特点的制约影响轮胎的使用性能。本发明在于克服全地形轮胎在结构制造所产生的缺点,提供一种特种沙地轮胎结构,该轮胎具有重量轻、制造成本低,在沙漠、沙地、海滩等松软地面上行驶更易通过的特点。
技术实现要素:
[0003]
为解决上述技术问题,本发明公开了一种特种沙地轮胎及其耐磨检测装置,特别是指在沙漠、海滩等松软地面上行驶轮胎,提高轮胎的转向性和横向刚性,使行驶更加平稳,具有强大的抓地性能,增加了车辆的刹车力、驱动力和牵引力,改善车辆的操控性和稳定性;其包括:
[0004]
胎体,所述胎体外圈形成有胎面,所述胎面边沿形成有胎肩,所述胎面和胎肩上设有若干个花纹块,所述花纹块以胎面周向轴左右两侧对称交错布置,所述花纹块包括设于所述胎面上沿轮胎周向分布的胎面花纹块组,及设于所述胎肩上沿轮胎周向分布的胎肩花纹块组,所述胎肩花纹块组的末端向胎侧延伸形成肩下花纹块。
[0005]
优选的,所述胎面花纹块组由若干个胎面花纹块组成,各胎面花纹块形成若干个花纹沟,所述胎面上从左到右依次开设有倾斜角度为5
°-
10
°
的第一花纹沟和第六花纹沟,倾斜角度为6
°-
10
°
的第二花纹沟和第五花纹沟,倾斜角度为 6
°-
10
°
的第三花纹沟和第七花纹沟,倾斜角度为6
°-
10
°
的第四花纹沟;所述胎肩与第二花纹沟之间限定出第一花纹块,所述第二花纹沟、第三花纹沟和第四花纹沟之间限定出第二花纹块,所述第二花纹沟、第四花纹沟、第五花纹沟限定出第三花纹块,所述第一花纹沟、第二花纹沟、第五花纹沟限定出第四花纹块,所述第二花纹沟、第三花纹沟、第四花纹沟之间限定出第五花纹块,所述第二花纹沟、第四花纹沟、第五花纹沟之间限定出第六花纹块。
[0006]
优选的,所述胎肩花纹块组包括若干个胎肩花纹块,长短和形状不同的两个胎肩花纹块在所述胎体肩部周向间隔分布,并且各胎肩花纹块之间沟槽边沿位置沿横向间隔设有沟底凸肋,所述胎肩花纹块周向两侧边为阶梯状设计,胎肩花纹块外端面由上端面与下
端面两个端面搭接形成;所述胎肩花纹块的末端向胎侧延伸形成肩下花纹块,肩下花纹块的厚度自肩下到肩下花纹块末端逐渐增厚,相邻的两行肩下花纹块在末端弯曲交叉,肩下花纹块末端向内开沟形成弧形沟槽,肩下花纹块的末端由高到低形成台阶。
[0007]
优选的,所述胎面花纹块设置为阶梯型块状结构,所述胎面花纹块下层面积大于所述胎面花纹块上层面积。
[0008]
优选的,所述第一花纹沟和第六花纹沟内分别设有两节长方形状弹性胶条,所述弹性胶条高度为锯齿状花纹沟深度的12%~14%,所述第一花纹块和第四花纹块上开设有气孔。
[0009]
优选的,所述第一花纹沟的沟槽尺寸由内至外逐渐变大。
[0010]
优选的,所述第一花纹块沿横向宽度下部开设有斜沟“~”字形刀槽和
“く”
花纹块,所述第二花纹块沿横向宽度倾斜方向上开设有“~”字形刀槽,刀槽周向沟长为45-50mm,沟宽为0.2mm-0.4mm,刀槽为陡坡状,所述第五花纹块沿横向宽度倾斜方向上开设有一个“~”和三个
“く”
字形刀槽,刀槽周向沟长为45-50mm,沟宽为0.2mm-0.4mm,刀槽为陡坡状。
[0011]
优选的,所述第一花纹块与第四花纹块,所述第二花纹块与第六花纹块、所述第三花纹块与第五花纹块结构相同,位置以胎面周向轴左右两侧对称交错布置。
[0012]
优选的,一种特种沙地轮胎耐磨检测装置,包括:
[0013]
底板;
[0014]
检测箱,所述检测箱固定连接于所述底板上方;
[0015]
检测台,所述检测台安装于所述检测箱内底部;
[0016]
控制箱,所述控制箱安装于所述检测箱上方;
[0017]
液压缸,所述液压缸竖直安装于所述检测箱上方,并且所述液压缸输出端向所述检测箱内部延伸,所述液压缸与所述控制箱电连接;
[0018]
液压杆,所述液压杆滑动连接于所述液压缸内部;
[0019]
横梁,所述横梁中心水平连接于所述液压杆上,所述横梁两端与所述检测箱侧壁内部滑动连接;
[0020]
u型架,所述u型架安装于所述横梁下方,所述u型架的横杆与所述立板转动连接,所述立板一侧安装有电机,所述电机输出端与所述横杆连接,所述横杆与轮胎连接;
[0021]
第一齿条,两个所述第一齿条分别安装于所述横梁两端靠近所述检测箱侧壁位置,所述检测台与所述第一齿条对应位置设有滑槽;
[0022]
第一齿轮,所述第一齿轮位于所述检测台上方,并且所述第一齿轮与所述第一齿条啮合;
[0023]
第二齿轮,所述第二齿轮与所述第一齿轮同轴设置,并且传动轴通过支架转动连接于所述检测台上;
[0024]
第二齿条,所述第二齿条滑动连接于所述检测台上方,并且所述第二齿条与所述第二齿轮啮合;
[0025]
夹板,所述夹板连接于所述第二齿条靠近所述检测台中心的一端,并且所述夹板与所述检测台滑动连接;
[0026]
耐磨组件,所述耐磨组件安装于所述检测台上方,并且所述耐磨组件设置于所述夹板之间,耐磨检测时所述耐磨组件与轮胎接触。
[0027]
优选的,所述耐磨组件包括:
[0028]
第一气缸,所述第一气缸转动连接于所述检测台上,所述第一气缸与所述控制箱电连接;
[0029]
转板,所述转板呈l型设置,所述转板转角处与所述第一气缸输出端连接;
[0030]
固定架,所述固定架转动连接与所述转板一端;
[0031]
耐磨检测板,所述耐磨检测板固定连接于所述固定架上方,并且所述耐磨检测板一端转动连接于所述检测台上;
[0032]
伸缩杆,所述伸缩杆转动连接于所述转板另一端与所述检测台之间;
[0033]
第二气缸,所述第二气缸转动连接于所述检测台上,所述第二气缸输出端转动连接于所述耐磨检测板下方,并且连接位置靠近所述耐磨检测板与所述检测台连接端,所述第二气缸与所述控制箱电连接。
附图说明
[0034]
为了更清楚地说明本发明具体实施方式或现有技术中的技术方案,下面将对具体实施方式或现有技术描述中所需要使用的附图作简单地介绍,显而易见地,下面描述中的附图是本发明的一些实施方式,对于本领域普通技术人员来讲,在不付出创造性劳动的前提下,还可以根据这些附图获得其他的附图。
[0035]
图1为本发明结构示意图;
[0036]
图2为本发明胎面局部结构示意图;
[0037]
图3为本发明胎肩局部结构示意图;
[0038]
图4为本发明耐磨检测装置结构示意图;
[0039]
图5为本发明耐磨组件结构示意图。
[0040]
图中:1.胎体;2.胎面;3.胎肩;4.肩下花纹块;11.第一花纹沟;12.第二花纹沟;13.第三花纹沟;14.第四花纹沟;15.第五花纹沟;16.第六花纹沟;17.第七花纹沟;18.弹性胶条;21.第一花纹块;22.第二花纹块;23.第三花纹块;24. 第四花纹块;25.第五花纹块;26.第六花纹块;27.气孔;31.胎肩花纹块;32.沟底凸肋;51.底板;52.检测箱;53.检测台;54.控制箱;55.液压缸;56.液压杆;57.横梁;58.u型架;581.横杆;582.立板;583.电机;59.第一齿条;510.第一齿轮;511.第二齿轮;512.第二齿条;513.夹板;6.耐磨组件;61.第一气缸;62.转板;63.固定架;64.耐磨检测板;65.伸缩杆;66.第二气缸。
具体实施方式
[0041]
下面将结合附图对本发明的技术方案进行清楚、完整地描述,显然,所描述的实施例是本发明一部分实施例,而不是全部的实施例。基于本发明中的实施例,本领域普通技术人员在没有做出创造性劳动前提下所获得的所有其他实施例,都属于本发明保护的范围。
[0042]
实施例
[0043]
下面将结合附图对本发明做进一步描述。
[0044]
如图1-3所示,本实施例提供的一种特种沙地轮胎,包括:
[0045]
胎体1,所述胎体1外圈形成有胎面2,所述胎面2边沿形成有胎肩3,所述胎面2和胎肩3上设有若干个花纹块,所述花纹块以胎面2周向轴左右两侧对称交错布置,所述花纹块
包括设于所述胎面2上沿轮胎周向分布的胎面花纹块组,及设于所述胎肩3上沿轮胎周向分布的胎肩花纹块组,所述胎肩花纹块组的末端向胎侧延伸形成肩下花纹块4。
[0046]
本发明的工作原理为:
[0047]
本发明提供一种特种沙地轮胎,针对沙地轮胎需在沙漠、沙地、海滩等松软地使用等行驶的特点,将轮胎胎面花纹设置为越野花纹,海路比控制在0.60,所述胎面周向设置两道曲折形纵向花纹沟,横向花纹沟较宽并且延伸至肩部以下;所述胎面是由沿轮胎横向方向上延伸且沿轮胎周向开设的若干个横向花纹沟,和胎面周向中轴线上且沿胎周向方向延伸开设的花纹沟,相交叉划分的多个花纹块组成的,所述花纹块以胎面周向轴左右两侧对称交错布置;各花纹块包括沿轮胎周向分布的胎面花纹块组及沿轮胎周向分布的胎肩花纹块组,一长一短和形状不一样的两个胎肩花纹块在肩部周向间隔分布,并且在各胎肩花纹沟底沿横向间隔设有沟底凸肋;胎肩花纹块周向两侧边为阶梯状设计,并且胎肩花纹块外端面由上端面与下端面两个端面搭接形成;各花纹块组之间形成波浪状和不规则状的花纹沟;肩部花纹块的末端向胎侧延伸形成肩下花纹块,肩下花纹块的厚度自肩下到花纹块末端逐渐增厚,相邻的两行肩下花纹块在末端弯曲交叉,肩下花纹块末端向内开沟形成弧形沟槽,肩下花纹块的末端由高到低形成台阶,组成的特种沙地越野轮胎。
[0048]
本发明的有益效果为:
[0049]
本发明提供的一种特种沙地轮胎,通过建立计算机模型,模拟轮胎在沙漠、沙地、海滩等松软地的接地印痕的大小与形状,接地压强的高低与分布状况,花纹与松软路面的接触情况,设计出u型结构花纹沟及无向块状花纹块,提高了本特种沙地轮胎在松软路面通过率及排水、排泥、排沙石等功能,提高车辆的稳定性及快速转弯性能,同时提高了轮胎的操控性能。
[0050]
在一个实施例中,所述胎面花纹块组由若干个胎面花纹块组成,各胎面花纹块形成若干个花纹沟,所述胎面2上从左到右依次开设有倾斜角度为5
°-
10
°
的第一花纹沟11和第六花纹沟16,倾斜角度为6
°-
10
°
的第二花纹沟12和第五花纹沟15,倾斜角度为6
°-
10
°
的第三花纹沟13和第七花纹沟17,倾斜角度为 6
°-
10
°
的第四花纹沟14;所述胎肩3与第二花纹沟12之间限定出第一花纹块21,所述第二花纹沟12、第三花纹沟13和第四花纹沟14之间限定出第二花纹块22,所述第二花纹沟12、第四花纹沟14、第五花纹沟15限定出第三花纹块23,所述第一花纹沟11、第二花纹沟12、第五花纹沟15限定出第四花纹块24,所述第二花纹沟12、第三花纹沟13、第四花纹沟14之间限定出第五花纹块25,所述第二花纹沟12、第四花纹沟14、第五花纹沟15之间限定出第六花纹块26。
[0051]
在一个实施例中,所述胎肩花纹块组包括若干个胎肩花纹块31,长短和形状不同的两个胎肩花纹块31在所述胎体1肩部周向间隔分布,并且各胎肩花纹块31之间沟槽边沿位置沿横向间隔设有沟底凸肋32,所述胎肩花纹块31周向两侧边为阶梯状设计,胎肩花纹块31外端面由上端面与下端面两个端面搭接形成;所述胎肩花纹块31的末端向胎侧延伸形成肩下花纹块4,肩下花纹块4的厚度自肩下到肩下花纹块4末端逐渐增厚,相邻的两行肩下花纹块4在末端弯曲交叉,肩下花纹块4末端向内开沟形成弧形沟槽,肩下花纹块4的末端由高到低形成台阶。
[0052]
在一个实施例中,所述胎面花纹块设置为阶梯型块状结构,所述胎面花纹块下层面积大于所述胎面花纹块上层面积。
[0053]
在一个实施例中,所述第一花纹沟11和第六花纹沟16内分别设有两节长方形状弹性胶条18,所述弹性胶条18高度为锯齿状花纹沟深度的12%~14%,所述第一花纹块21和第四花纹块24上开设有气孔27。
[0054]
在一个实施例中,所述第一花纹沟11的沟槽尺寸由内至外逐渐变大。
[0055]
在一个实施例中,所述第一花纹块21沿横向宽度下部开设有斜沟“~”字形刀槽和
“く”
花纹块,所述第二花纹块22沿横向宽度倾斜方向上开设有“~”字形刀槽,刀槽周向沟长为45-50mm,沟宽为0.2mm-0.4mm,刀槽为陡坡状,所述第三花纹块23沿横向宽度倾斜方向上开设有一个“~”和三个
“く”
字形刀槽,刀槽周向沟长为45-50mm,沟宽为0.2mm-0.4mm,刀槽为陡坡状。
[0056]
在一个实施例中,所述第一花纹块21与第四花纹块21,所述第二花纹块 22与第六花纹块26、所述第三花纹块23与第五花纹块25结构相同,位置以胎面2周向轴左右两侧对称交错布置。
[0057]
上述技术方案的工作原理和有益效果为:
[0058]
在胎面上设置有沿轮胎横向方向上延伸的第一花纹块21和第二花纹块22,所述第一花纹块21凹进去,第二花纹块22凸出来,所述第一花纹块21和第二花纹块22同向两边都开设有一高一低缺边,起到缓冲作用并且提高了抓地性能,也就是说,使轮胎更容易适应路面,并且在行驶过程中吸收冲击并减小震动,从而提高车辆乘坐舒适性和操控性,同时减轻驾驶者的疲劳。
[0059]
所述第一花纹块21沿横向宽度下部开设有斜沟“~”字形刀槽和
“く”
花纹块,所述第二花纹块22沿横向宽度倾斜方向上开设有“~”字形刀槽,刀槽周向沟长为45-50mm,沟宽为0.2mm-0.4mm,刀槽为陡坡状,所述第三花纹块 23沿横向宽度倾斜方向上开设有一个“~”和三个
“く”
字形刀槽,刀槽周向沟长为45-50mm,沟宽为0.2mm-0.4mm,刀槽为陡坡状。所述第一花纹块21 与第四花纹块21,所述第二花纹块22与第六花纹块26、所述第三花纹块23与第五花纹块25结构相同,只是在分布位置上是相对的。通过上述结构设计,由于各个花纹块上开设的刀槽形状、大小、长度、方向、角度、位置不一致,在轮胎滚动接地时,各边界对沙漠、沙地、海滩等松软地路等路面的切割作用力也是多方向的且多样的,这样可以快速穿透沙漠、沙地、海滩等松软地等路面,可减小花纹块的蠕动和生热,降低轮胎噪声、振动和滞后损失,提高轮胎的高速行驶性能、乘坐舒适性、操控稳定性和抓地性能。
[0060]
轮胎使用的花纹块包括:蝴蝶状花纹块、梯形状花纹块、箭状花纹块、刀尖状花纹块和条状花纹块,所述箭状花纹块的箭头部分朝向胎肩,箭状花纹块、刀尖状花纹块和条状花纹块之间形成的花纹沟,有利于切割、穿透沙漠、沙地、海滩等松软地等路面;蝴蝶状花纹块、梯形状花纹块可以使轮胎不容易被沙地、泥地、松软地给包住,令沙地、泥地、松软地失去附着力,防止车辆陷在砂石、泥地里动弹不得,此外蝴蝶状花纹块、梯形状花纹块还能提供一种向上“浮力”,提高车辆脱困能力,有效提升牵引;箭状花纹块,能够提升肩部刚性,保证在沙地路面操控自如。
[0061]
由于花纹块设计为“无向块状”,以胎面周向中轴线在胎面左右两侧对称交错布置,因此胎面左右两侧的花纹沟均对称交错设置,从而避免在胎面左右两侧(以周向中轴线划分左右两侧)花纹块完全对称一致设计时,在轮胎滚动过程中,轮胎同一部位接地时左右两侧的花纹块撞击噪音的频率一致,导致产生共振和轮胎滚动噪音增大的问题;各个花纹
沟设计成具有不同倾斜角度以及交错设置,使得形成的花纹块呈多样化,轮胎滚动接地时各个沟槽和花纹块产生的空气噪音均不一致,杜绝共振现象,降低噪音;另外各个沟槽的边界和不同位置、形状的花纹块会产生不同的应力,对沙漠、沙地、海滩等松软地等地行驶时提供多样化的抓地力,乘坐舒适性和操控稳定性,使得轮胎更容易抓地,增加抓地力。
[0062]
所述特种沙地轮胎,整体花纹块设计为蝴蝶状花纹块和梯形状花纹块,更适于沙地越野车的性能要求,设计时将海路比控制在0.60,流畅的横向花纹沟槽,保证排沙时的畅通无阻和超强的操控性能,所述蝴蝶状花纹块设计时,主行驶面花纹沟深度较浅且以纵向花纹沟为主,横向花纹沟宽度较小,可减小花纹块的蠕动和生热,降低轮胎噪声、振动和滞后损失,提高轮胎的高速行驶性能、乘坐舒适性和操控稳定性。通过上述结构设计,所述特种沙地轮胎的花纹块粗壮有力,使轮胎在转向性、横向刚性更强,行驶更平稳,具有强大的越野性能,增加车辆的刹车力、驱动力和牵引力,改善车辆操控性能和稳定性能。
[0063]
花纹块之间设置有不同形状、大小、长度、方向、角度、位置的花纹沟和弹性胶条,在轮胎滚动接地时,由于各边界对沙漠、沙地、海滩等松软地等路面的切割作用力也是多方向的且多样的,花纹沟里会粘附沙石和泥巴等,包住花纹沟形成一个光滑圆形,使车子陷在砂石和泥巴里动弹不得,而弹性胶条受到轮胎滚动接地力产生回弹力,会把粘附在花纹沟里沙石和泥巴及时排出来,从而提高抓地力和操控稳定性能及快速转弯性能的提升,还起到保护轮胎的作用,能够延长轮胎使用寿命。
[0064]
相较于普通轮胎,所述特种沙地轮胎中各花纹沟较宽,花纹沟深度也较深,且花纹沟设置为u型结构,赋予了轮胎更强的切割作用力,从而提高抓地力、操控稳定性及快速转弯性能,同时由于花纹沟设计u型结构提高了轮胎刚性,赋予了轮胎超强抓地力及操控稳定性和牵引性能,使轮胎更具有优异的排沙、泥巴性能,又能防止石子夹在花纹沟内,整个花纹横纵向花纹沟相通,有效降低行驶时带来的噪音。
[0065]
胎肩部花纹块的末端向胎侧延伸形成肩下花纹块,肩下花纹块的厚度自肩下到花纹块末端逐渐增厚,相邻的两行肩下花纹块在末端弯曲交叉,肩下花纹块末端向内开沟形成弧形沟槽,肩下花纹块的末端由高到低形成台阶;在胎肩以下至水平轴以上胎侧区域设置不规则几何形状的突起,分为三种高度错落排列,可以降低噪声和防止沙地等路面的尖锐物体刺破胎侧,起到保护轮胎的作用,能够延长轮胎使用寿命和降低轮胎噪声。
[0066]
在胎面宽度上设置的倾斜角度比较低,通过对弧长、半径的设计使得胎面接地宽度达到最优设计,达到最大的接地面积,配合胎面花纹结构,有效提升了轮胎的操控性能。
[0067]
如图4、5所示,在一个实施例中,一种特种沙地轮胎耐磨检测装置包括:
[0068]
底板51;
[0069]
检测箱52,所述检测箱52固定连接于所述底板51上方;
[0070]
检测台53,所述检测台53安装于所述检测箱52内底部;
[0071]
控制箱54,所述控制箱54安装于所述检测箱52上方;
[0072]
液压缸55,所述液压缸55竖直安装于所述检测箱52上方,并且所述液压缸55输出端向所述检测箱52内部延伸,所述液压缸55与所述控制箱54电连接;
[0073]
液压杆56,所述液压杆56滑动连接于所述液压缸55内部;
[0074]
横梁57,所述横梁57中心水平连接于所述液压杆56上,所述横梁57两端与所述检测箱52侧壁内部滑动连接;
[0075]
u型架58,所述u型架58安装于所述横梁57下方,所述u型架58的横杆581与所述立板582转动连接,所述立板581一侧安装有电机583,所述电机 583输出端与所述横杆581连接,所述横杆581与轮胎连接;
[0076]
第一齿条59,两个所述第一齿条59分别安装于所述横梁57两端靠近所述检测箱52侧壁位置,所述检测台53与所述第一齿条59对应位置设有滑槽;
[0077]
第一齿轮510,所述第一齿轮510位于所述检测台53上方,并且所述第一齿轮510与所述第一齿条59啮合;
[0078]
第二齿轮511,所述第二齿轮511与所述第一齿轮510同轴设置,并且传动轴通过支架转动连接于所述检测台53上;
[0079]
第二齿条512,所述第二齿条512滑动连接于所述检测台53上方,并且所述第二齿条512与所述第二齿轮511啮合;
[0080]
夹板513,所述夹板513连接于所述第二齿条512靠近所述检测台53中心的一端,并且所述夹板513与所述检测台53滑动连接;
[0081]
耐磨组件6,所述耐磨组件6安装于所述检测台53上方,并且所述耐磨组件6设置于所述夹板513之间,耐磨检测时所述耐磨组件6与轮胎接触。
[0082]
上述技术方案的工作原理和有益效果为:
[0083]
轮胎耐磨检测时,将轮胎安装于所述u型架58的的横杆581上,启动所述液压缸55,所述液压缸55动作,推动所述液压杆56向下运动,带动所述横梁 57和u型架58同步向下运动,当轮胎到达检测位置与所述耐磨组件6接触后,启动所述电机583,带动所述横杆581和轮胎高速转动,所述轮胎和耐磨检测板 64发生摩擦,从而实现轮胎的耐磨检测,所述横梁57下降的同时,所述第一齿条510同步向下运动,带动所述第一齿轮510转动,所述第二齿轮511随之同步转动,从而带动所述第二齿条512水平运动,所述夹板513在所述第二齿条 512的作用下向中间靠拢,将所述耐磨检测板64夹紧;所述检测箱52箱板采用静音结构,所述底板51内部设有液压升降滚轮。
[0084]
通过上述结构设计,有效实现轮胎的耐磨检测,检测过程中将耐磨检测板 64夹紧,防止轮胎检测过程中由于轮胎或耐磨检测板64安装不平衡,导致的耐磨检测板64侧偏,保证检测过程中轮胎受力的一致性,从而提高检测准确性,同时,减少检测过程中的噪音,并且能够实现检测装置的快速移动,提高了耐磨检测装置的适用性。
[0085]
在一个实施例中,所述耐磨组件6包括:
[0086]
第一气缸61,所述第一气缸62转动连接于所述检测台53上,所述第一气缸61与所述控制箱54电连接;
[0087]
转板62,所述转板62呈l型设置,所述转板62转角处与所述第一气缸61 输出端连接;
[0088]
固定架63,所述固定架63转动连接与所述转板62一端;
[0089]
耐磨检测板64,所述耐磨检测板64固定连接于所述固定架63上方,并且所述耐磨检测板64一端转动连接于所述检测台53上;
[0090]
伸缩杆65,所述伸缩杆65转动连接于所述转板62另一端与所述检测台53 之间;
[0091]
第二气缸66,所述第二气缸66转动连接于所述检测台53上,所述第二气缸66输出端转动连接于所述耐磨检测板64下方,并且连接位置靠近所述耐磨检测板64与所述检测台
53连接端,所述第二气缸66与所述控制箱54电连接
[0092]
上述技术方案的工作原理和有益效果为:
[0093]
启动所述第一气缸61动作,将所述第一气缸61滑杆伸出,驱动所述转板 62向上运动,所述转板62带动所述固定架63向上运动,从而驱动所述耐磨检测板64实现转动,所述伸缩杆65连接于所述转板62和检测台53之间,所述伸缩杆65随转板62运动二伸长,对所述转板62进行支撑,当所述耐磨检测板 64发生侧偏时,通过所述第二气缸66动作对所述耐磨检测板64位置进行微调。
[0094]
通过上述结构设计,通过固定架63和转板62将第一气缸61和耐磨检测板 64连接,所述固定架63有效保证了连接强度,提高角度调整时所述耐磨检测板64的转动稳定性,将所述耐磨检测板64连接时的应力集中位置向两侧转移,防止中间位置应力集中导致的局部变形,降低安装方式对检测结果的影响,同时对所述耐磨检测板64位置能进行微调,有助于消除侧偏误差,有效实现了不同坡度轮胎磨损状态的模拟检测,提高装置可靠性。
[0095]
显然,上述实施例仅仅是为清楚地说明所作的举例,而并非对实施方式的限定。对于所属领域的普通技术人员来说,在上述说明的基础上还可以做出其它不同形式的变化或变动。这里无需也无法对所有的实施方式予以穷举。而由此所引伸出的显而易见的变化或变动仍处于本发明创造的保护范围之中。
起点商标作为专业知识产权交易平台,可以帮助大家解决很多问题,如果大家想要了解更多知产交易信息请点击 【在线咨询】或添加微信 【19522093243】与客服一对一沟通,为大家解决相关问题。
此文章来源于网络,如有侵权,请联系删除



tips