一种用于天然橡胶的铸造粉尘复合补强剂及其制备方法与流程



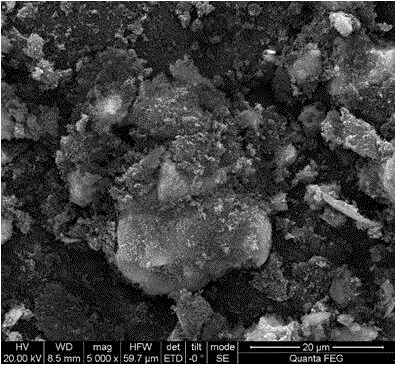
本发明属于固体废弃物资源回收利用和节能环保领域,具体涉及一种用于天然橡胶的铸造粉尘复合补强剂及其制备方法。
背景技术:
天然橡胶是重要的工业原料,广泛应用于生产轮胎、密封件、防震设备、传输带等。天然橡胶通常需要补强后才能使用,炭黑和白炭黑是最重要的橡胶补强填料,生产时需要消耗大量不可再生的一次性资源,加重全球资源紧缺的问题。因此,开发新的填料替换或部分替换炭黑与白炭黑,是解决资源危机的有效途径。
铸造粉尘是铸造车间收尘设备收集的细小粉末状颗粒废弃物,主要成分为二氧化硅,还含有少量的铝、钙、镁、铁、锰等元素的氧化物或它们之间形成的复杂多元氧化物。专利cn106220906b将铸造粉尘经过酸洗、磨细、偶联剂改性等加工处理过程后得到铸造粉尘填料用于天然橡胶的填充剂。但是这种铸造粉尘填充剂的补强效果不明显。由于铸造粉尘填充剂是一类性质不同于传统补强填充剂的新品种,当铸造粉尘对橡胶的补强效果不佳时,橡胶企业配方车间缺乏足够的耐心对其配方进行长期试验,不利于铸造粉尘补强剂的推广和应用。
同时,由于单一的铸造粉尘填充剂对天然橡胶的补强效果较差,铸造粉尘填充剂的补强效果往往难以达到橡胶企业的预期。所以在实际运用时常需要将铸造粉尘与其他高补强性填料进行复配,获得既能资源化利用铸造粉尘,又能减少高补强性填料的用量,还具有优异补强性的复合补强剂。复配最简单的方法是将铸造粉尘和其他的补强剂(如炭黑和白炭黑)分批次与天然橡胶进行混炼。但是该方法不但延长了混炼时间,还加重了粉尘污染,同样不利于铸造粉尘补强剂的推广应用。
技术实现要素:
本发明的目的在于提供一种用于天然橡胶的铸造粉尘复合补强剂及其制备方法,通过开发铸造粉尘在天然橡胶领域的应用,实现铸造粉尘的资源化,同时减少传统补强剂炭黑和白炭黑的用量。
本发明是这样来实现的:一种用于天然橡胶的铸造粉尘复合补强剂的制备方法,具体步骤为:
一、筛分:将铸造粉尘废弃物在电动振动筛中筛分,得到粒度小于100目的铸造粉尘;
二、除铁:将粒度小于100目的铸造粉尘使用干粉磁选机除去其中的铁粉;
三、酸洗:将100份除去铁粉的铸造粉尘在3000份浓度为10%的盐酸中机械搅拌2小时;
四、沉淀:将酸洗液静置24小时使固体沉淀,分离上次清液;将沉淀使用大量去离子水洗涤至中性;
五、一次粉磨:使用微粉磨机将酸洗后的铸造粉尘研磨至粒径达到300目以下;
六、混合:将粒度小于300目的铸造粉尘40~80份,白炭黑10~40份,炭黑10~40份,硅烷偶联剂1.5份在密封式机械搅拌机中混合2小时;
七、二次粉磨:将上一步混合好的复合粉料在微粉磨机中进一步研磨至粒径达到800目以下;
八、造粒:将二次粉磨后的复合粉料在圆盘造粒机中造粒,即得到颗粒状铸造粉尘复合补强剂。
利用上述方法制备的铸造粉尘复合补强剂改性的天然橡胶的补强性能比相同含量的铸造粉尘、白炭黑和炭黑填料分别添加到天然橡胶中进行补强的补强性能好。
有益效果:
1.本发明公开的铸造粉尘复合补强剂的制备方法简单,补强效果明显,复合补强剂对天然橡胶的改性效果优于相同含量的铸造粉尘、白炭黑和炭黑填料分别添加到天然橡胶中的补强效果,有利于在橡胶企业的快速推广;
2.本发明采用机械研磨法,按照比例将铸造粉尘、白炭黑和炭黑在密闭式微粉磨机中充分研磨,不但可以细化铸造粉尘的颗粒尺寸,还能利用不同性质粉体之间的相互作用,使纳米级别的炭黑和白炭黑网络结构包覆在微米级铸造粉尘颗粒表面,形成特殊结构的铸造粉尘/白炭黑/炭黑复合补强剂;
3.特殊结构的复合补强剂与天然橡胶混炼时一次加入即可,缩短了混炼周期,减少了粉尘污染;
4.复合补强剂在研磨混合的过程中,硬度较大的铸造粉尘颗粒在不断被破碎细化的同时,对白炭黑和炭黑进行了强有力的分散,使得复合补强剂中的白炭黑和炭黑在混炼过程中更易于在天然橡胶中分散;
5.复合补强剂对天然橡胶的补强效果优于补强剂各组分单独分批次添加的补强效果。
附图说明
图1为实施例5中二次粉磨后得到的铸造粉尘/白炭黑/炭黑复合粉体的场发射扫描电子显微镜照片;
图2为未复合的原始铸造粉尘粉体的场发射扫描电子显微镜照片;
图3为实施例1-5和对比例1-5中天然橡胶混炼胶硫化后的性能测试统计图。
具体实施方式
下面对本发明的较佳实施例进行详细阐述,以使本发明的优点和特征能更易于被本领域技术人员理解,从而对本发明的保护范围做出更为清楚明确的界定。
实施例1
一、筛分:将铸造粉尘废弃物在电动振动筛中筛分,得到粒度小于100目的铸造粉尘;
二、除铁:将粒度小于100目的铸造粉尘使用干粉磁选机除去其中的铁粉;
三、酸洗:将100份除去铁粉的铸造粉尘在3000份浓度为10%的盐酸中机械搅拌2小时;
四、沉淀:将酸洗液静置24小时使固体沉淀,分离上次清液;将沉淀使用大量去离子水洗涤至中性;
五、一次粉磨:使用微粉磨机将酸洗后的铸造粉尘研磨至粒径达到300目以下;
六、混合:将粒度小于300目的铸造粉尘50份,白炭黑(m-5)25份;炭黑(vxc-72)25份;硅烷偶联剂(si-69)1.5份在密封式机械搅拌机中混合2小时;
七、二次粉磨:将上一步混合好的复合粉料在微粉磨机中进一步研磨至粒径达到800目以下;
八、造粒:将二次粉磨后的复合粉料在圆盘造粒机中造粒,即得到颗粒状铸造粉尘复合补强剂,标记为f50s25c25,其中f代表铸造粉尘,s代表白炭黑,c代表炭黑;50,25,25分别代表铸造粉尘、白炭黑和炭黑的质量份数(下同)。
复合补强剂的补强性能通过制备的天然橡胶复合材料的性能进行评价。
在开炼机中依次加入100份天然橡胶、2份硬脂酸、5份氧化锌、1份二硫化二苯并噻唑、1.2份二硫醇基苯并咪唑、50份复合补强剂f50s25c25、5份硫磺,充分混炼后停放3天得到混炼胶;将混炼胶在150℃,压力15mpa下硫化8分钟,得到天然橡胶复合材料。
其力学性能测试值列于图3中。
实施例2
一、筛分:将铸造粉尘废弃物在电动振动筛中筛分,得到粒度小于100目的铸造粉尘;
二、除铁:将粒度小于100目的铸造粉尘使用干粉磁选机除去其中的铁粉;
三、酸洗:将100份除去铁粉的铸造粉尘在3000份浓度为10%的盐酸中机械搅拌2小时;
四、沉淀:将酸洗液静置24小时使固体沉淀,分离上次清液;将沉淀使用大量去离子水洗涤至中性;
五、一次粉磨:使用微粉磨机将酸洗后的铸造粉尘研磨至粒径达到300目以下;
六、混合:将粒度小于300目的铸造粉尘50份,白炭黑(m-5)30份;炭黑(vxc-72)20份;硅烷偶联剂(si-69)1.5份在密封式机械搅拌机中混合2小时;
七、二次粉磨:将上一步混合好的复合粉料在微粉磨机中进一步研磨至粒径达到800目以下;
八、造粒:将二次粉磨后的复合粉料在圆盘造粒机中造粒,即得到颗粒状铸造粉尘复合补强剂,标记为f50s30c20。
复合补强剂的补强性能通过制备的天然橡胶复合材料的性能进行评价。
在开炼机中依次加入100份天然橡胶、2份硬脂酸、5份氧化锌、1份二硫化二苯并噻唑、1.2份二硫醇基苯并咪唑、50份复合补强剂f50s30c20、5份硫磺。充分混炼后停放3天得到混炼胶;将混炼胶在150℃,压力15mpa下硫化8分钟,得到天然橡胶复合材料。
其力学性能测试值列于图3中。
实施例3
一、筛分:将铸造粉尘废弃物在电动振动筛中筛分,得到粒度小于100目的铸造粉尘;
二、除铁:将粒度小于100目的铸造粉尘使用干粉磁选机除去其中的铁粉;
三、酸洗:将100份除去铁粉的铸造粉尘在3000份浓度为10%的盐酸中机械搅拌2小时;
四、沉淀:将酸洗液静置24小时使固体沉淀,分离上次清液;将沉淀使用大量去离子水洗涤至中性;
五、一次粉磨:使用微粉磨机将酸洗后的铸造粉尘研磨至粒径达到300目以下;
六、混合:将粒度小于300目的铸造粉尘50份,白炭黑(m-5)20份;炭黑(vxc-72)30份;硅烷偶联剂(si-69)1.5份在密封式机械搅拌机中混合2小时;
七、二次粉磨:将上一步混合好的复合粉料在微粉磨机中进一步研磨至粒径达到800目以下;
八、造粒:将二次粉磨后的复合粉料在圆盘造粒机中造粒,即得到颗粒状铸造粉尘复合补强剂,标记为f50s20c30。
复合补强剂的补强性能通过制备的天然橡胶复合材料的性能进行评价。
在开炼机中依次加入100份天然橡胶、2份硬脂酸、5份氧化锌、1份二硫化二苯并噻唑、1.2份二硫醇基苯并咪唑、50份复合补强剂f50s20c30、5份硫磺。充分混炼后停放3天得到混炼胶;将混炼胶在150℃,压力15mpa下硫化8分钟,得到天然橡胶复合材料。
其力学性能测试值列于图3中。
实施例4
一、筛分:将铸造粉尘废弃物在电动振动筛中筛分,得到粒度小于100目的铸造粉尘;
二、除铁:将粒度小于100目的铸造粉尘使用干粉磁选机除去其中的铁粉;
三、酸洗:将100份除去铁粉的铸造粉尘在3000份浓度为10%的盐酸中机械搅拌2小时;
四、沉淀:将酸洗液静置24小时使固体沉淀,分离上次清液;将沉淀使用大量去离子水洗涤至中性;
五、一次粉磨:使用微粉磨机将酸洗后的铸造粉尘研磨至粒径达到300目以下;
六、混合:将粒度小于300目的铸造粉尘50份,白炭黑(m-5)10份;炭黑(vxc-72)40份;硅烷偶联剂(si-69)1.5份在密封式机械搅拌机中混合2小时;
七、二次粉磨:将上一步混合好的复合粉料在微粉磨机中进一步研磨至粒径达到800目以下;
八、造粒:将二次粉磨后的复合粉料在圆盘造粒机中造粒,即得到颗粒状铸造粉尘复合补强剂,标记为f50s10c40。
复合补强剂的补强性能通过制备的天然橡胶复合材料的性能进行评价。
在开炼机中依次加入100份天然橡胶、2份硬脂酸、5份氧化锌、1份二硫化二苯并噻唑、1.2份二硫醇基苯并咪唑、50份复合补强剂f50s10c40、5份硫磺。充分混炼后停放3天得到混炼胶;将混炼胶在150℃,压力15mpa下硫化8分钟,得到天然橡胶复合材料。
其力学性能测试值列于图3中。
实施例5
一、筛分:将铸造粉尘废弃物在电动振动筛中筛分,得到粒度小于100目的铸造粉尘;
二、除铁:将粒度小于100目的铸造粉尘使用干粉磁选机除去其中的铁粉;
三、酸洗:将100份除去铁粉的铸造粉尘在3000份浓度为10%的盐酸中机械搅拌2小时;
四、沉淀:将酸洗液静置24小时使固体沉淀,分离上次清液;将沉淀使用大量去离子水洗涤至中性;
五、一次粉磨:使用微粉磨机将酸洗后的铸造粉尘研磨至粒径达到300目以下;
六、混合:将粒度小于300目的铸造粉尘50份,白炭黑(m-5)40份;炭黑(vxc-72)10份;硅烷偶联剂(si-69)1.5份在密封式机械搅拌机中混合2小时;
七、二次粉磨:将上一步混合好的复合粉料在微粉磨机中进一步研磨至粒径达到800目以下;从图1和图2中可以看出,经过该程度的二次粉磨后纳米级别的炭黑和白炭黑呈网络结构包覆在微米级铸造粉尘颗粒表面,白炭黑和炭黑得到了有效的分散,便于其在混炼过程中更好的分散在天然橡胶中,也能减少投料过程中的粉尘污染;
八、造粒:将二次粉磨后的复合粉料在圆盘造粒机中造粒,即得到颗粒状铸造粉尘复合补强剂,标记为f50s40c10。
复合补强剂的补强性能通过制备的天然橡胶复合材料的性能进行评价。
在开炼机中依次加入100份天然橡胶、2份硬脂酸、5份氧化锌、1份二硫化二苯并噻唑、1.2份二硫醇基苯并咪唑、50份复合补强剂f50s20c30、5份硫磺。充分混炼后停放3天得到混炼胶;将混炼胶在150℃,压力15mpa下硫化8分钟,得到天然橡胶复合材料。
其力学性能测试值列于图3中。
对比例1
一、筛分:将铸造粉尘废弃物在电动振动筛中筛分,得到粒度小于100目的铸造粉尘;
二、除铁:将粒度小于100目的铸造粉尘使用干粉磁选机除去其中的铁粉;
三、酸洗:将100份除去铁粉的铸造粉尘在3000份浓度为10%的盐酸中机械搅拌2小时;
四、沉淀:将酸洗液静置24小时使固体沉淀,分离上次清液;将沉淀使用大量去离子水洗涤至中性;
五、一次粉磨:使用微粉磨机将酸洗后的铸造粉尘研磨至粒径达到300目以下;
六、混合:将粒度小于300目的铸造粉尘100份,硅烷偶联剂(si-69)1.5份在密封式机械搅拌机中混合2小时;
七、二次粉磨:将上一步混合好的复合粉料在微粉磨机中进一步研磨至粒径达到800目以下;
八、造粒:将二次粉磨后的复合粉料在圆盘造粒机中造粒,即得到颗粒状铸造粉尘补强剂,标记为f,其中f代表铸造粉尘(下同)。
补强剂依次添加、逐步混炼时的补强性能通过制备的天然橡胶复合材料的性能进行评价。
在开炼机中依次加入100份天然橡胶、2份硬脂酸、5份氧化锌、1份二硫化二苯并噻唑、1.2份二硫醇基苯并咪唑、25份铸造粉尘补强剂f、12.5份白炭黑(m-5)、12.5份炭黑(vxc-72)、5份硫磺。充分混炼后停放3天得到混炼胶;将混炼胶在150℃,压力15mpa下硫化8分钟,得到天然橡胶复合材料。
其力学性能测试值列于图3中。
对比例2
步骤一到步骤八与对比例1相同。
补强剂依次添加、逐步混炼时的补强性能通过制备的天然橡胶复合材料的性能进行评价。
在开炼机中依次加入100份天然橡胶、2份硬脂酸、5份氧化锌、1份二硫化二苯并噻唑、1.2份二硫醇基苯并咪唑、25份铸造粉尘补强剂f、15份白炭黑(m-5)、10份炭黑(vxc-72)、5份硫磺。充分混炼后停放3天得到混炼胶;将混炼胶在150℃,压力15mpa下硫化8分钟,得到天然橡胶复合材料。
其力学性能测试值列于图3中。
对比例3
步骤一到步骤八与对比例1相同。
补强剂依次添加、逐步混炼时的补强性能通过制备的天然橡胶复合材料的性能进行评价。
在开炼机中依次加入100份天然橡胶、2份硬脂酸、5份氧化锌、1份二硫化二苯并噻唑、1.2份二硫醇基苯并咪唑、25份铸造粉尘补强剂f、10份白炭黑(m-5)、15份炭黑(vxc-72)、5份硫磺。充分混炼后停放3天得到混炼胶;将混炼胶在150℃,压力15mpa下硫化8分钟,得到天然橡胶复合材料。
其力学性能测试值列于图3中。
对比例4
步骤一到步骤八与对比例1相同。
补强剂依次添加、逐步混炼时的补强性能通过制备的天然橡胶复合材料的性能进行评价。
在开炼机中依次加入100份天然橡胶、2份硬脂酸、5份氧化锌、1份二硫化二苯并噻唑、1.2份二硫醇基苯并咪唑、25份铸造粉尘补强剂f、5份白炭黑(m-5)、20份炭黑(vxc-72)、5份硫磺。充分混炼后停放3天得到混炼胶;将混炼胶在150℃,压力15mpa下硫化8分钟,得到天然橡胶复合材料。
其力学性能测试值列于图3中。
对比例5
步骤一到步骤八与对比例1相同。
补强剂依次添加、逐步混炼时的补强性能通过制备的天然橡胶复合材料的性能进行评价。
在开炼机中依次加入100份天然橡胶、2份硬脂酸、5份氧化锌、1份二硫化二苯并噻唑、1.2份二硫醇基苯并咪唑、25份铸造粉尘补强剂f、20份白炭黑(m-5)、5份炭黑(vxc-72)、5份硫磺。充分混炼后停放3天得到混炼胶;将混炼胶在150℃,压力15mpa下硫化8分钟,得到天然橡胶复合材料。
其力学性能测试值列于图3中。
由图3可知,实施例1-5是以复合补强剂为填料制备的样品;对比例1-5是以铸造粉尘填充剂、白炭黑和炭黑为填料,分别添加到天然橡胶中制备的样品。其中,实施例1和对比例1中三种填料的含量相同;实施例2和对比例2中三种填料的含量相同;实施例3和对比例3中三种填料的含量相同;实施例4和对比例4中三种填料的含量相同;实施例5和对比例5中三种填料的含量相同。将相应的实施例和对比例的力学性能进行对比可以发现,当补强剂含量和各组成成分相同时,实施例的拉伸强度和撕裂强度均明显高于相应对比例;实施例的断裂伸长率和邵尔a硬度与相应对比例相比,无明显差异。因此,力学性能测试结果表明,通过机械研磨制备的铸造粉尘、白炭黑和炭黑三元复合填充剂的补强性能优于单一的铸造粉尘、白炭黑和炭黑分别依次添加的补强性能。
以上所述仅为本发明的实施例,并非因此限制本发明的专利范围,凡是利用本发明说明书及附图内容所作的等效结构或等效流程变换,或直接或间接运用在其他相关的技术领域,均同理包括在本发明的专利保护范围内。
起点商标作为专业知识产权交易平台,可以帮助大家解决很多问题,如果大家想要了解更多知产交易信息请点击 【在线咨询】或添加微信 【19522093243】与客服一对一沟通,为大家解决相关问题。
此文章来源于网络,如有侵权,请联系删除


