聚硅氮烷改性环氧单组份防腐涂层料浆、涂层及制备方法与流程



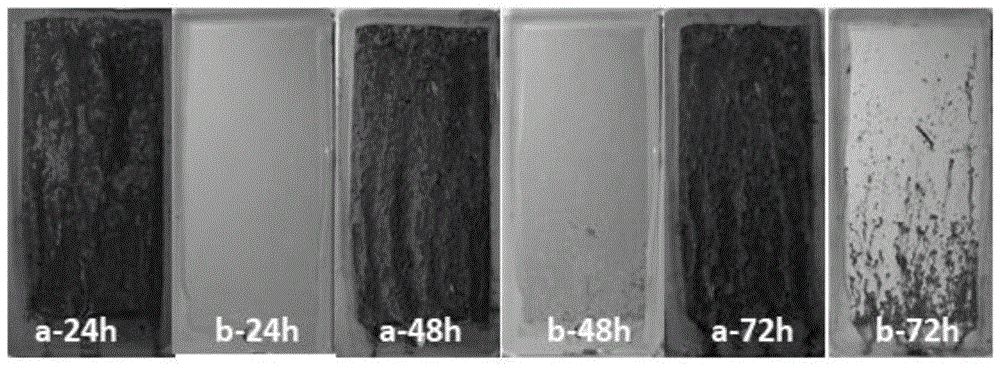
本发明属于防腐涂层技术领域,特别涉及一种聚硅氮烷改性环氧防腐单组份涂层料浆、涂层及制备方法。
背景技术:
热镀锌(galvanizing)也叫热浸锌和热浸镀锌,是一种有效的金属防腐方式,主要用于各行业的金属结构设施上。热镀锌过程是将除锈后的钢件浸入500℃左右熔化的锌液中,使钢件表面附着锌层,从而起到防腐的目的。热镀锌具体工艺流程为:成品酸洗-水洗-加助镀液-烘干-挂镀-冷却-药化-清洗-打磨-热镀锌完工。热镀锌具有加工高效、易转运、防护无死角、防腐性能好等特点,在石油化工、通信与电力、交通运输、建筑、机械制造和农业等领域得到了广泛应用。但是随着环保形势的日益严峻,热镀锌高能耗、高污染、高资源消耗的弊病受到全社会的关注,寻找可以替代热镀锌的金属防腐新方法迫在眉睫。
采用涂层防腐技术来保护金属是一种常规的、高效的方式,相较于热镀锌具有涂装工艺简单、过程中无需高温(锌槽温度500℃)和后期易修补等优势。因为涂层致密、与基材附着力高、屏蔽性能好等优点,环氧树脂类防腐涂料在行业内应用最广。但由于防腐性能要求,环氧防腐涂料一般采用含活泼氢的胺类固化剂,以双组份的形式使用;当二者混合后作为浸涂涂料使用时,其在常温下亦有可能发生交联固化反应,造成表面结皮或者凝胶现象,所以一般只能单次小批量应用;采用喷涂、刷涂或者辊涂的涂装方式,又很难对管件内壁或异形件等进行全方位无死角的防护。少数防腐涂料可大批量稳定的采用浸涂方式对工件进行全覆盖涂装,但涂料成膜物质大多为丙烯酸或有机硅类。以这些树脂体系的涂层作为底涂时具有机械性能差、影响后道涂层涂覆的天然缺陷。因此,常规防腐涂层技术不能实现涂覆方式、加工效率和防腐性能的统一,无法真正取代热镀锌工艺。
聚硅氮烷是一种以si-n为重复单元的有机聚合物,常添加无机氧化物和其他无机材料组成有机无机杂化聚合物,可作为陶瓷前驱体在较为温和的条件下裂解得到sic、si3n4或sicn陶瓷产物,又可作为热固性树脂广泛应用于固化剂、粘结剂、复合材料等领域。由于si-n键可与金属表面反应,形成类似硅烷表面处理技术中的si-o-me键,且该类聚合物形成的膜层致密,阻隔性能好,其作为防腐涂层的应用得到关注。专利cn201910968490.7公开了一种基于聚硅氮烷的锌铝防腐涂料。该涂料主要含有聚硅氮烷和锌铝粉,具有制备工艺简单、溶剂选择面广、浸涂效率高和耐蚀性好等优点,但聚硅氮烷固化物无机属性使得涂层内应力大,韧性和抗冲击性能欠佳,发生磕碰时涂层存在脱落风险。此外,所制备涂层中富含si-ch3或si-h等疏水基团,为后续涂料的涂装层间结合力带来不利影响。专利cn201610823332.9公开了一种环保的防腐蚀涂料。该涂料主要由玻璃鳞片、鲸蜡醇基硫酸钠、全氢聚硅氮烷、古马隆树脂、丙烯酸酯磷酸酯和马来酸酐接枝蜡乳液等组成。与现有的防腐蚀涂料相比,虽然具有抗腐蚀、防老化、耐高温、耐低温、延展性好和断裂伸长率高的优点,但是该涂层防腐体系中占主体的古马隆树脂等屏蔽性一般,更多依靠玻璃鳞片形成的片状阻隔,所以防腐性能一般。其次,全氢聚硅氮烷活性高,可转化成siox,使得涂层中n含量较少(<5%),当腐蚀介质水渗透进入涂层时,无足够的si-n基团与其发生水解反应,缓释作用较差。因此,在涂层发生局部破损时,基材短时间内很快发生锈蚀,对后期修补带来很大困难。
技术实现要素:
鉴于以上分析,本发明旨在提供一种聚硅氮烷改性环氧单组份防腐涂层料浆、涂层及制备方法,至少能够解决以下技术问题之一:(1)现有的环氧树脂防腐涂料一般以双组份的形式使用,当混合配制成浸涂液时,应用过程中容易发生反应,造成浸涂液不稳定,影响后期使用;(2)现有的聚硅氮烷涂层的抗冲击性能欠佳,发生磕碰时涂层存在脱落风险;(3)现有的防腐涂层无法实现涂覆方式、加工效率和防腐性能的统一,无法替代热镀锌。
本发明的目的主要是通过以下技术方案实现的:
一方面,本发明提供了一种聚硅氮烷改性环氧单组份防腐涂层料浆,组分包括:聚硅氮烷改性环氧树脂、催化剂、填料和环保溶剂。
在一种可能的设计中,所述组分按质量百分比为:
其中,所述聚硅氮烷改性环氧树脂、所述催化剂、所述填料和所述环保溶剂的质量百分比之和为100%。
在一种可能的设计中,所述聚硅氮烷改性环氧树脂采用如下方法制备:将聚硅氮烷和环氧树脂按比例混合,在加热的状态下搅拌进行反应得到聚硅氮烷改性环氧树脂。
在一种可能的设计中,所述聚硅氮烷和所述环氧树脂的质量比为0.05~20。
在一种可能的设计中,所述聚硅氮烷的结构通式为:
其中,r1和r2相同或不同,r1和r2中至少有一个是活性基团-ch=ch2,另一个为-h、c1-c4烷基、-ch=ch2、-c6h5或-nh2中的一种,n是3~3000之间的整数。
在一种可能的设计中,所述环氧树脂包括双酚a环氧树脂、双酚f环氧树脂、溴化环氧树脂、酚醛环氧树脂和脂肪族环氧树脂中的一种或多种。
在一种可能的设计中,所述搅拌速度为100r/min~500r/min;所述搅拌时间为0.5h~8h;所述加热温度为40℃~220℃。
另一方面,本发明提供了一种聚硅氮烷改性环氧单组份防腐涂层料浆的制备方法,包括如下步骤:
步骤1、按照比例,将聚硅氮烷改性环氧树脂加入环保溶剂进行混合,在搅拌条件下加入催化剂和填料;
步骤2、待混合物均匀分散后,将其转入球磨罐中研磨均匀,得到聚硅氮烷改性环氧单组份防腐涂层料浆。
本发明还提供了一种聚硅氮烷改性环氧单组份防腐涂层,所述聚硅氮烷改性环氧单组份防腐涂层是通过将上述聚硅氮烷改性环氧单组份防腐涂层料浆涂覆到被保护基材表面后,经过中低温加热固化所得。
在一种可能的设计中,所述中低温加热固化的工艺参数为:加热温度为25~250℃,加热时间为0.1~4h。
与现有技术相比,本发明至少能实现以下技术效果之一:
(1)本发明的防腐涂层料浆的成膜物质采用聚硅氮烷改性环氧树脂,利用极性si-n键和环氧基团发生开环反应,生成一种主链含si-o-c、si-n-c的在常温下稳定的预聚物,侧链主要含有活泼的-ch=ch2、-h等其它基团;在加热条件下,侧链基团在催化剂的作用下发生加成反应,使得涂层交联密度明显增大,提供了高的阻隔屏蔽性。其次si-o键的引入增加了该聚合物的耐温性,使得在设计一种可中低温固化的单组份防腐涂层配方时,环氧树脂的种类和分子量的选择可以不受温度的限制,选择更加灵活多变;最后,当腐蚀介质h2o渗透进入涂层,会优先和主链上的si-n键发生水解反应,延缓了腐蚀介质渗透到基材的速度,具有本征缓释性能。因此,基于该改性树脂的涂层具有防腐性能优异、厚度易于调节、基材适用性强等特点,为防腐涂层的制备提供了新的材料选择。
(2)本发明提供的防腐涂层料浆在低温(<60℃)下成膜物质的结构和性能稳定,敞口放置不变质、可中低温烘烤固化成膜,完全适应批量工件浸泡涂装的加工方式。涂覆前,无需对基材进行特殊化学处理、等离子处理、火焰和热处理等;施工工艺简单、质量稳定可控;所制备涂层厚度调节范围宽、适应面广、附着力好、防腐性能优异,可作为一种浸涂液从工艺和性能等方面完全替代热镀锌。
(3)本发明提供的防腐涂层附着力好、柔韧性好、防腐性能优异。例如,当被保护基材为q235普通钢板时,厚度为2μm的涂层附着力0级,柔韧性1级,抗冲击性能50kg·cm,耐中性盐雾时间达72h;厚度为80μm的涂层附着力0级,柔韧性2级,抗冲击性能50kg.cm,耐中性盐雾时间达2000h。
(4)本发明的制备方法工艺简单、条件温和,利于大批量工业化生产,经济效益显著。
本发明的其他特征和优点将在随后的说明书中阐述,或者通过实施本发明而了解。本发明的目的和其他优点可通过在所写的说明书以及附图中所特别指出的来实现和获得。
附图说明
附图仅用于示出具体实施例的目的,而并不认为是对本发明的限制,在整个附图中,相同的附图标记表示相同的部件。
图1是实施例12的涂层耐盐雾测试图片,基材为q235钢板;其中a为空白样板的耐盐雾测试结果图片,b为涂覆防腐涂层的样板的耐盐雾测试结果图片;
图2是实施例13的涂层耐盐雾测试图片,基材为镀锌板;
图3是实施例14的涂层耐盐雾测试图片,基材为q235钢板;
图4是本发明的聚硅氮烷改性环氧树脂的过程中,红外光谱对原料和反应产物的结构分析结果;
图5是本发明的涂层固化时涂层与基材表面的活性羟基,涂层内部发生的双键加成反应。
具体实施方式
以下结合具体实施例对一种聚硅氮烷改性环氧单组份防腐涂层料浆、涂层及制备方法作进一步的详细描述,这些实施例只用于比较和解释的目的,本发明不限定于这些实施例中。
一方面,本发明提供了一种聚硅氮烷改性环氧单组份防腐涂层料浆,组分包括:聚硅氮烷改性环氧树脂、催化剂、填料和环保溶剂。
需要说明的是,聚硅氮烷改性环氧单组份防腐涂层料浆中,聚硅氮烷改性环氧树脂的含量过高会导致涂层料浆密度过低,在浸泡涂装时,工件出浸漆槽后表面涂料因为重力滴落速度过慢,影响加工效率;含量过低会导致防腐性能下降。因此,控制聚硅氮烷改性环氧单组份防腐涂层料浆中,各组分按质量百分比为:
其中,上述的聚硅氮烷改性环氧树脂、催化剂、填料和环保溶剂的质量百分比之和为100%。
优选的,各组分按质量百分比为:
其中,上述的聚硅氮烷改性环氧树脂、催化剂、防腐填料和环保溶剂的质量百分比之和为100%。
需要说明的是,上述聚硅氮烷改性环氧树脂是通过聚硅氮烷和环氧树脂化学反应获得的。聚硅氮烷和环氧树脂的质量比为0.05~20之间,优选为0.1~10。
具体的,上述聚硅氮烷改性环氧树脂采用如下方法制备:将聚硅氮烷和环氧树脂按上述比例进行混合,在加热的状态下搅拌进行反应得到聚硅氮烷改性环氧树脂。
需要说明的是,上述聚硅氮烷的结构通式为:
其中,r1和r2相同或不同,r1和r2中至少有一个是活性基团-ch=ch2,另一个为-h、c1-c4烷基、-ch=ch2、-c6h5或-nh2中的一种,n是3~3000之间的整数。
具体的,r1为-ch=ch2,r2为-ch3;即聚硅氮烷为含乙烯基的聚硅氮烷。这是因为-ch=ch2在催化剂和加热的条件下可发生加成反应,极大提高了聚硅氮烷防腐涂层的致密度,有利于涂层防腐性能的提高。
具体的,为了保证聚硅氮烷具有较好的成膜性能,控制n为10~40之间的整数。
具体的,上述环氧树脂包括双酚a环氧树脂、双酚f环氧树脂、溴化环氧树脂、酚醛环氧树脂、脂肪族环氧树脂中的一种或多种。
具体的,上述催化剂选自金属类催化剂、过氧化物类催化剂和/或偶氮类催化剂中的至少一种。
所述金属类催化剂可以为有机锡催化剂、钯类催化剂、铂类催化剂或铑类催化剂中的一种或多种;所述有机锡催化剂可以为二丁基锡二月桂酸脂、辛酸亚锡、二甲基锡或三苯基锡等中的一种或多种;所述钯类催化剂选自钯/碳、氯化钯、丙酸钯、乙酸钯或四(三苯基膦)钯等中的一种或多种;所述铂类催化剂选自铂/碳、氯铂酸、铂/碳酸钙、顺式二(三苯基膦)二氯化铂、二(亚磷酸三苯酯)二氯化铂或四(三苯基膦)铂等中的一种或多种;所述铑类催化剂选自顺式二(三苯基膦)二氯化铑、二(三苯基膦)羰基氯化铑、三(三苯基膦)氯化铑或四(三苯基膦)铑等中的一种或多种。
所述的过氧化物类催化剂可以为过氧化环己酮、过氧化二苯甲酰、过氧化二异丙苯或过氧化二叔丁基等中的一种或多种。
所述的偶氮类催化剂可以为偶氮二异丁腈、偶氮二异庚腈、偶氮二异丁酸二甲酯或偶氮异丁氰基甲酰胺等中的一种或多种。
具体的,上述环保溶剂为一种无毒或者低毒,可生物降解的、低挥发的溶剂。包括多元醇醚酯、丙二醇二甲醚、丙二醇二丁醚、十二碳醇酯、乙二醇丁醚醋酸酯、二丙二醇甲醚醋酸酯、二乙二醇乙醚乙酸酯、n,n-二乙基甲酰胺、乙二醇二乙酸酯、二乙二酸甲醚乙酸酯、丙二醇甲醚乙酸酯中的一种或多种。
需要说明的是,经过深入研究,为了保证聚硅氮烷改性环氧防腐单组份涂层料浆在进行涂装时具备较好的成膜性能,控制上述聚硅氮烷改性环氧树脂中聚硅氮烷和环氧树脂的质量比为0.1~10;优选的,聚硅氮烷和环氧树脂的质量比为0.25~4。
具体的,控制上述聚硅氮烷和环氧树脂反应的搅拌速度为100r/min~500r/min,如150r/min、200r/min、250r/min、300r/min、350r/min、400r/min、450r/min等;搅拌时间为0.5h~8h,加热温度为40℃~220℃,如80℃、100℃、120℃、140℃、160℃、180℃、210℃等。优选的,加热温度为100℃~150℃。
具体的,为了增加涂层的致密度,上述填料包括纳米填料、常规无机填料和颜料中的一种或多种。纳米填料选自纳米sio2、纳米al2o3、纳米tio2、纳米zno、纳米zro2、纳米ti粉中的一种或多种,粒径≤800nm,如700nm、600nm、500nm、400nm、300nm、100nm、80nm等;常规无机填料选自锌粉、铝粉、磷酸锌、三聚磷酸铝、二硫化钼、硫酸钡、碳酸钙、滑石、云母中的一种或多种,粒径325~3000目,如500目、800目、1000目、1500目、2000目等;颜料选自氧化铁红、炭黑和氧化铬绿中的一种或多种。
另一方面,本发明提供了一种上述聚硅氮烷改性环氧单组份防腐涂层料浆的制备方法,包括如下步骤:
步骤1、按照比例,将聚硅氮烷改性环氧树脂加入环保溶剂进行混合,在搅拌条件下加入催化剂和填料;
步骤2、待混合物均匀分散后,将其转入球磨罐中研磨均匀,得到聚硅氮烷改性环氧防腐涂层浆料。
需要说明的是,上述步骤1中,为了方便搅拌,先将聚硅氮烷改性环氧树脂加入环保溶剂进行分散,在搅拌条件下加入催化剂和填料。
具体的,上述步骤1中,搅拌速度为500r/min~3000r/min,搅拌时间为0.5h~1h。
本发明还提供了一种聚硅氮烷改性环氧单组份防腐涂层,聚硅氮烷改性环氧单组份防腐涂层是通过将上述聚硅氮烷改性环氧单组份防腐涂层料浆涂覆到被保护基材表面后,经过中低温加热固化所得。
具体的,上述涂覆方式为辊涂、喷涂或浸涂等方式。
为了进一步提高涂层的质量,攻克拐角、空隙和凹凸不平的难刷部位,提高效率,涂覆方式可以为喷涂,喷涂压力为0.3~0.6mpa,喷幅宽度为10~18cm,喷涂间距为20~30cm。
为了减少设备投资,提高涂料的利用率,减少损耗,并且尽可能的保证拐角、空隙和凹凸不平的难刷部位的涂层质量,实现批量的流水线生产;涂覆方式为浸涂,浸涂时间为5~20s,提拉速度为1~4m/min,如2m/min、3m/min。
具体的,控制上述中低温加热固化的工艺参数为:加热温度为25~250℃,如50℃、80℃、100℃、130℃、170℃、200℃、230℃等,加热时间为0.1~4h。优选的,加热温度为120~180℃,加热时间为0.1~1h。
考虑到聚硅氮烷改性环氧防腐涂层的涂层太薄,在批量处理工件时无法覆盖粗糙度较大的工件表面;涂层太厚,加热固化后内应力集中存在开裂风险。因此,控制涂层的厚度为2~100μm。优选的,涂层的厚度为2~50μm。
需要说明的是,上述聚硅氮烷与环氧树脂发生的化学反应通式如下所示。
需要说明的是,在聚硅氮烷改性环氧树脂的过程中,为了更加清晰地判断聚硅氮烷和环氧树脂发生了化学反应,优选常温,100℃,120℃,140℃四个反应温度,各反应0.5h。采用红外光谱对原料和反应产物的结构进行分析,结果如图4所示,由图4可以看出,915cm-1对应的环氧基团中c-o伸缩振动峰强度随着加热温度的升高逐渐减弱。3390cm-1对应的n-h峰,随着加热温度的升高半峰宽变宽,说明生成了-oh基团。由此说明,环氧树脂和聚硅氮烷在加热状态下发生了开环反应,而非简单的物理混合。
需要说明的是,涂层固化时涂层与基材表面的活性羟基,涂层内部发生的双键加成反应如图5所示。
本发明提供的聚硅氮烷改性环氧单组份防腐涂层的表面含有少量活泼的si-n极性基团,si-n极性基团的中心原子为电负性较大的n原子,含有孤对电子,当金属(例如fe)有空轨道时,能够提供孤对电子给金属的空轨道,形成配位键吸附于金属表面,改变金属表面的双电层结构,提高金属离子化过程的活化能;同时,在腐蚀环境下si-n水解产生氨气,使得金属表面形成弱碱性环境,进一步延缓了金属表面的腐蚀。此外,相比于常规树脂,环氧树脂屏蔽性好;相比于聚硅氮烷,环氧树脂韧性好。因此,利用聚硅氮烷化学接枝改性环氧树脂,固化后可形成一种具有高屏蔽性和高韧性的阻隔膜,由此得到一种兼具阻隔和缓释作用的双功能防腐涂层,在性能上实现对热镀锌的替代。此外,聚硅氮烷侧链si-h和-ch3等烷基基团决定主链si-n的活泼性,可选择不同活性的聚硅氮烷对环氧树脂进行改性,得到一种在温度低于60℃环境下,结构和性能稳定的聚硅氮烷改性环氧树脂预聚物,复配高沸点低挥发性的环保型溶剂、催化剂和填料,制得的防腐涂层料浆可作为一种单组份防腐浸涂液,在车间敞开环境下对工件进行浸泡涂装加工,对各大型件或异形件进行无死角、全覆盖保护,在工艺上实现对热镀锌的替代。
具体的,上述聚硅氮烷改性环氧防腐涂层在基底上的附着力为0级。
示例性的,当被保护基材为q235普通钢板时,厚度为2μm的涂层附着力0级,柔韧性1级,抗冲击性能50kg.cm,耐中性盐雾时间达72h;厚度为80μm的涂层附着力0级,柔韧性2级,抗冲击性能50kg.cm,耐中性盐雾时间达2000h。
与现有技术相比,本发明的防腐涂层料浆的成膜物质采用聚硅氮烷改性环氧树脂,将聚硅氮烷和环氧树脂的优势相结合,一方面利用聚硅氮烷特殊的化学结构,赋予所制备涂层优异的附着力、高的致密性以及本征缓释性能;另一方面,环氧树脂具有成本低、屏蔽性好、韧性可调节空间大等优势。因此,基于该改性树脂的涂层具有防腐性能优异、厚度易于调节、基材适用性强等特点,为防腐涂层的制备提供了新的材料选择。
本发明提供的防腐涂层料浆在低温(<60℃)下成膜物质的结构和性能稳定,敞口放置不变质、可中低温烘烤固化成膜,完全适应批量工件浸泡涂装的加工方式。涂覆前,无需对基材进行特殊化学处理、等离子处理、火焰和热处理等;施工工艺简单、质量稳定可控;所制备涂层厚度调节范围宽、适应面广、附着力好、防腐性能优异,可作为一种浸涂液从工艺和性能等方面完全替代热镀锌。例如,当被保护基材为q235普通钢板时,厚度为2μm的涂层附着力0级,柔韧性1级,抗冲击性能50kg.cm,耐中性盐雾时间达72h;厚度为80μm的涂层附着力0级,柔韧性2级,抗冲击性能50kg.cm,耐中性盐雾时间达2000h。
下面结合具体实施例,进一步阐述本发明。下述方法如无特别说明均为常规方法,下述原材料如无特别说明均能从公开商业途径获得。
下述实施例中所用的聚硅氮烷(opz118)采用公开的氨解方法合成,具体为:共氨解二甲基二氯硅烷、甲基乙烯基二氯硅烷、甲基三氯硅烷,所得聚硅氮烷为淡黄色液体,数均分子量900,粘度:20000cps。
下述实施例中,涂层厚度采用德国(elcometer)测厚仪(型号:b600)进行测量;附着力按照gb/t9286-1998进行测试;耐盐雾时间按照gb/t1771-2007进行测试。
聚硅氮烷改性环氧树脂及其制备:
实施例1
本实施例提供了一种聚硅氮烷改性环氧树脂1,采用如下方法制备:
称取50质量份的聚硅氮烷opz118、50质量份的环氧树脂e51混合搅拌,速度为200r/min,反应温度为100℃,反应时间为1h。即得,备用。
实施例2
本实施例提供了一种聚硅氮烷改性环氧树脂2,采用如下方法制备:
称取80质量份的聚硅氮烷opz118、20质量份的环氧树脂e51混合搅拌,速度为200r/min,反应温度为120℃,反应时间为1h。即得,备用。
实施例3
本实施例提供了一种聚硅氮烷改性环氧树脂3,采用如下方法制备:
称取20质量份的聚硅氮烷opz118、80质量份的环氧树脂e51混合搅拌,速度为300r/min,反应温度为140℃,反应时间为2h。即得,备用。
实施例4(即对比例)
本实施例提供了一种聚硅氮烷改性环氧树脂4,采用如下方法制备:
称取20质量份的聚硅氮烷opz118、80质量份的环氧树脂e51常温混合搅拌,速度为300r/min。即得,备用。
聚硅氮烷改性环氧防腐涂层料浆及其制备:
实施例5
本实施例提供了一种聚硅氮烷改性环氧防腐涂层料浆1,采用如下方法制备:
称取16质量份的聚硅氮烷改性环氧树脂1,64质量份的丙二醇丁醚、9.97质量份的纳米tio2和10质量份的磷酸锌,在800r/min的转速下搅拌1h后移置球磨罐中研磨均匀即得,备用。其中,催化剂为:二丁基锡二月桂酸脂,添加量为0.03质量份。
实施例6
本实施例提供了一种聚硅氮烷改性环氧防腐涂层料浆2,采用如下方法制备:
称取16质量份的聚硅氮烷改性环氧树脂1,64质量份的十二碳醇酯、9.97质量份的纳米sio2和10质量份的云母粉,在1200r/min的转速下搅拌0.8h后移置球磨罐中研磨均匀即得,备用。其中,催化剂为:过氧化环己酮,添加量为0.03质量份。
实施例7
本实施例提供了一种聚硅氮烷改性环氧防腐涂层料浆3,采用如下方法制备:
称取10质量份的聚硅氮烷改性环氧树脂2,80质量份的丙二醇甲醚乙酸酯、9.97质量份的纳米zno,在1200r/min的转速下搅拌0.8h后移置球磨罐中研磨均匀即得,备用。其中,催化剂为:偶氮二异丁腈,添加量为0.03质量份。
实施例8
本实施例提供了一种聚硅氮烷改性环氧防腐涂层料浆4,采用如下方法制备:
称取20质量份的聚硅氮烷改性环氧树脂2、40质量份的丙二醇甲醚乙酸酯、4.97质量份的纳米sio2、5质量份的铝粉和30质量份的片状锌粉,在2000r/min的转速下搅拌0.5h后移置球磨罐中研磨均匀即得,备用。其中,催化剂为:氯铂酸,添加量为0.03质量份。
实施例9(即对比例)
本实施例提供了一种聚硅氮烷改性环氧防腐涂层料浆5,采用如下方法制备:
称取10质量份的聚硅氮烷改性环氧树脂4,80质量份的丙二醇甲醚乙酸酯、9.97质量份的纳米zno,在1200r/min的转速下搅拌0.8h后移置球磨罐中研磨均匀即得,备用。其中,催化剂为:偶氮二异丁腈,添加量为0.03质量份。
聚硅氮烷改性环氧防腐涂层及其制备、性能测试:
实施例10
采用喷涂法将聚硅氮烷改性环氧防腐涂层料浆1涂覆到表面洁净的q235钢板(150*70*0.8mm)表面,喷涂工艺为:压力为0.5mpa,喷幅宽度为18cm,喷涂间距为20cm。
将样板置于120℃烘箱干燥1h,取出即得防腐涂层。该涂层厚度12μm。附着力0级,柔韧性1级,抗冲击50kg.cm,耐盐雾时间为336h。
实施例11
采用喷涂法将聚硅氮烷改性环氧防腐涂层料浆2喷涂到表面洁净的铝板(150mm*70mm*0.8mm)表面,喷涂工艺为:压力为0.4mpa,喷幅宽度为15cm,喷涂间距为25cm。
将样板置于170℃烘箱干燥0.3h,取出即得防腐涂层。该涂层厚度10μm。附着力0级,柔韧性1级,抗冲击50kg.cm,耐盐雾时间为1500h。
实施例12
采用浸涂法将聚硅氮烷改性环氧防腐涂层料浆3涂覆到表面洁净的q235钢板(150*70*0.8mm)表面,具体为将q235钢板浸没在溶液中10s,然后以2m/min的提拉速度取出钢板;待溶剂挥发30min后,加热固化,160℃固化0.5h。得到的防腐涂层厚度为2μ,采用划格法测试的涂层附着力为0级,柔韧性1级,抗冲击50kg.cm,耐盐雾时间为72h。
实施例13
采用浸涂的方式将聚硅氮烷改性环氧防腐涂层料浆3涂覆在表面洁净的镀锌板(150*70*0.8mm)表面,具体为,将镀锌板浸没在溶液中10s,然后以2m/min的提拉速度取出;待溶剂挥发30min后,加热固化,180℃固化0.5h。得到的防腐涂层厚度为3μm。采用划格法测试的涂层附着力为0级,耐中性盐雾240h后,镀锌板表面划叉处保持完好,其余部位不发生腐蚀,而无涂层的对比样板腐蚀严重。
实施例14
采用浸涂法将聚硅氮烷改性环氧防腐涂层料浆4涂覆到表面洁净的q235钢板(150*70*0.8mm)表面,具体为将q235钢板浸没在溶液中10s,然后以2m/min的提拉速度取出钢板,待溶剂挥发后,在150℃烘箱干燥0.8h,取出即得防腐涂层。该涂层厚度50μm,附着力0级,柔韧性1级,抗冲击50kg.cm,耐盐雾时间为2000h。
实施例15(即对比例)
采用浸涂法将聚硅氮烷改性环氧防腐涂层料浆5涂覆到表面洁净的q235钢板(150*70*0.8mm)表面,具体为将q235钢板浸没在溶液中10s,然后以2m/min的提拉速度取出钢板;待溶剂挥发30min后,加热固化,160℃固化0.5h得到防腐涂层。该涂层表面发粘,厚度无法准确测试,附着力4级,耐盐雾1h即发生锈蚀。
图1是实施例12的涂层耐盐雾测试图片,基材为q235钢板;其中a为空白样板的耐盐雾测试结果图片,b为涂覆防腐涂层的样板的耐盐雾测试结果图片;图2是实施例13的涂层耐盐雾测试图片,基材为镀锌板;图3是实施例14的涂层耐盐雾测试图片,基材为q235钢板。由图1-图3可以看出本发明的聚硅氮烷改性环氧单组份防腐涂层比空白样板的耐盐雾时间长,防腐效果好。
以上所述,仅为本发明较佳的具体实施方式,但本发明的保护范围并不局限于此,任何熟悉本技术领域的技术人员在本发明揭露的技术范围内,可轻易想到的变化或替换,都应涵盖在本发明的保护范围之内。
起点商标作为专业知识产权交易平台,可以帮助大家解决很多问题,如果大家想要了解更多知产交易信息请点击 【在线咨询】或添加微信 【19522093243】与客服一对一沟通,为大家解决相关问题。
此文章来源于网络,如有侵权,请联系删除


