一种环氧树脂涂料、超疏水性涂层及其制备方法与流程



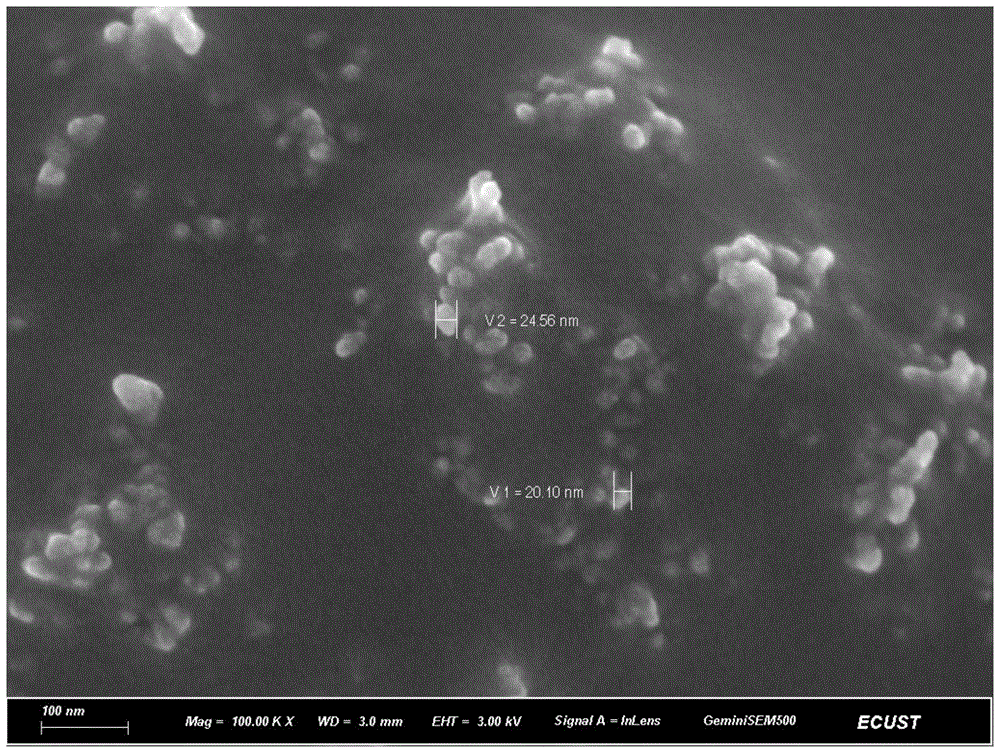
本发明涉及纳米涂料技术领域,具体涉及一种环氧树脂涂料、超疏水性涂层及其制备方法。
背景技术:
超疏水现象指物体表面与水的接触角大于150°而滚动角小于5°时的现象。因为超疏水现象对材料的防水、防冰和自清洁等性能具有很重要的意义,因而引起了研究者们极大的兴趣。
近年来,国内外超疏水性涂料的研究得到了飞速的发展,市场上已经出现了一些超疏水性涂料产品。但是采用已有超疏水性涂料得到的超疏水涂层存在附着力和耐磨性差等问题,且疏水效果耐久性差,导致其很难在实际生产中广泛使用。
技术实现要素:
本发明的目的在于提供一种环氧树脂涂料、超疏水性涂层及其制备方法,以本发明提供的环氧树脂涂料为主体材料制备的超疏水性涂层具有较好的附着力、耐磨性和持久的超疏水性。
为了实现上述发明目的,本发明提供以下技术方案:
本发明提供了一种环氧树脂涂料,按质量份数计,包括以下制备原料:
疏水改性环氧树脂50份;
微米级二氧化硅1~5份;
纳米级二氧化硅1~5份;
活性稀释剂25~50份。
优选地,所述疏水改性环氧树脂由环氧树脂经疏水试剂改性得到,所述疏水试剂包括端羟基聚二甲基硅氧烷、长链烷烃类化合物或有机氟类化合物。
优选地,所述环氧树脂与疏水试剂的质量比为100:(70~90)。
优选地,所述微米级二氧化硅的粒度为5~20μm。
优选地,所述纳米级二氧化硅的粒度为14~50nm。
优选地,所述活性稀释剂包括甲基丙烯酸缩水甘油酯、正丁基缩水甘油醚、烯丙基缩水甘油醚、5-乙基己基缩水甘油醚和丁二醇二缩水甘油醚中的一种或几种。
本发明提供了一种超疏水性涂层,按质量份数计,包括以下制备原料:
上述技术方案所述的环氧树脂涂料100份;
阳离子光引发剂3~5份;
自由基光引发剂3~5份;
光敏剂1~5份。
优选地,所述阳离子光引发剂包括三芳基锍六氟锑酸盐混合物或二苯基-(4-苯基硫)苯基锍六氟锑酸盐的丙烯酸酯溶液;
所述自由基光引发剂包括双(2,4,6-三甲基苯甲酰基)苯基氧化膦、2,4,6-三甲基苯甲酰基-乙氧基-苯基氧化膦或2-异丙基硫杂蒽酮;
所述光敏剂包括蒽、芘或苝。
本发明提供了上述技术方案所述超疏水性涂层的制备方法,包括以下步骤:
将环氧树脂涂料、阳离子光引发剂、自由基光引发剂和光敏剂混合,将所得混合物料涂覆到基底的表面形成湿膜,之后在紫外线照射条件下进行固化,在所述基底的表面形成超疏水性涂层。
优选地,所述固化采用的光源包括紫外汞灯或者紫外led灯,所述光源与湿膜的距离为15~30cm,光源照射的时间为5~20min。
本发明提供了一种环氧树脂涂料,按质量份数计,包括以下制备原料:疏水改性环氧树脂50份;微米级二氧化硅1~5份;纳米级二氧化硅1~5份;活性稀释剂25~50份。本发明提供的环氧树脂涂料中,疏水改性环氧树脂作为基体树脂,具有较低的表面能和一定的疏水性,而且环氧基团含量较多,不仅能够提高涂料后期的固化速率、缩短固化时间,还能够提高涂层对基底的附着力;微米级二氧化硅和纳米级二氧化硅能够在涂层表面形成类荷叶效应的微纳米凸起(也可称为微纳米二级粗糙结构),使涂层具有较好的超疏水效果,具体的,在实际使用过程中,水滴与涂层表面的微纳米凸起之间会形成空气通道,导致水滴与涂层表面的实际接触面积降低,从而使水滴容易从涂层表面滚落,起到超疏水作用;同时,微米级二氧化硅和纳米级二氧化硅的添加还可以使涂层具有较好的附着力和耐磨性;活性稀释剂既能使微米级二氧化硅和纳米级二氧化硅更好地分散在疏水改性环氧树脂中,又有利于涂层的交联固化,无需使用可挥发性溶剂如丙酮、乙酸乙酯等,绿色环保。
以本发明提供的环氧树脂涂料为主体材料,配以阳离子光引发剂、自由基光引发剂和光敏剂,能够在紫外线照射条件下固化形成超疏水性涂层,所述超疏水性涂层具有较好的附着力、耐磨性和持久的超疏水性;同时,该固化方式节能环保,适合工厂流水线高速生产工作以及室外大面积施工操作。
附图说明
图1为实施例1制备的超疏水性涂层的场发射扫描电子显微镜图(高倍率);
图2为实施例1制备的超疏水性涂层的场发射扫描电子显微镜图(低倍率);
图3为本发明中耐磨性能测试的示意图。
具体实施方式
本发明提供了一种环氧树脂涂料,按质量份数计,包括以下制备原料:
疏水改性环氧树脂50份;
微米级二氧化硅1~5份;
纳米级二氧化硅1~5份;
活性稀释剂25~50份。
在本发明中,按质量份数计,所述环氧树脂涂料的制备原料包括疏水改性环氧树脂50份。在本发明中,所述疏水改性环氧树脂优选由环氧树脂经疏水试剂改性得到。在本发明中,所述疏水改性环氧树脂的制备方法,优选包括以下步骤:
将环氧树脂与活性稀释剂混合,在搅拌条件下加热至110~130℃,维持温度恒定,向所得混合物料中加入催化剂和疏水试剂,保温反应1.5~2.5h,得到疏水改性环氧树脂。
在本发明中,制备所述疏水改性环氧树脂的过程中,所述环氧树脂优选包括双酚a型环氧树脂或双酚s型环氧树脂;所述活性稀释剂优选包括甲基丙烯酸缩水甘油酯(gma)或甲基丙烯酸四氢呋喃甲酯;所述疏水试剂优选包括端羟基聚二甲基硅氧烷(htpdms)、长链烷烃类化合物或有机氟类化合物,更优选为端羟基聚二甲基硅氧烷;所述催化剂优选包括二月桂酸二丁基锡;所述环氧树脂、活性稀释剂和疏水试剂的质量比优选为100:(40~60):(70~90),更优选为100:50:80;所述催化剂采用本领域技术人员熟知的用量即可。
在本发明中,制备所述疏水改性环氧树脂的过程中,所述搅拌的速率优选为1800~2200r/min;本发明优选向环氧树脂与活性稀释剂的混合物料中依次加入催化剂和疏水试剂,其中,所述催化剂的加入方式优选为滴加,所述疏水试剂优选分批加入。在本发明的实施例中,具体是用胶头滴管向环氧树脂与活性稀释剂的混合物料中逐滴加入催化剂,3~5min后用恒压漏斗每隔25~35min加入8~12g疏水试剂,至所有疏水试剂加入完毕后,在110~130℃条件下保温反应1.5~2.5h,得到疏水改性环氧树脂。在本发明中,在所述反应过程中,优选补加活性稀释剂以控制体系具有适宜的粘度;本发明对于体系的具体粘度不作特殊限定,保证反应顺利进行即可。
本发明采用疏水改性环氧树脂作为基体树脂,具有较低的表面能和一定的疏水性,与微米级二氧化硅和纳米级二氧化硅界面结合效果好,而且环氧基团含量较多,不仅能够提高涂料后期的固化速率、缩短固化时间,还能够提高涂层对基底的附着力。
在本发明中,以所述疏水改性环氧树脂的质量份数为基准,所述环氧树脂涂料的制备原料包括微米级二氧化硅1~5份,优选为2~4份。在本发明中,所述微米级二氧化硅的粒度优选为5~20μm,更优选为5~15μm。本发明对于所述微米级二氧化硅的来源没有特殊的限定,采用本领域技术人员熟知的市售商品即可;在本发明的实施例中,所述微米级二氧化硅优选购自德国赢创工业集团,具体是采用d10型号(初始平均粒径为6.5μm)和d17型号(初始平均粒径为10μm)的微米级二氧化硅。
在本发明中,以所述疏水改性环氧树脂的质量份数为基准,所述环氧树脂涂料的制备原料包括纳米级二氧化硅1~5份,优选为2~4份。在本发明中,所述纳米级二氧化硅的粒度优选为14~50nm,更优选为14~40nm。本发明对于所述纳米级二氧化硅的来源没有特殊的限定,采用本领域技术人员熟知的市售商品即可;在本发明的实施例中,所述纳米级二氧化硅优选购自德国赢创工业集团,具体是采用r202型号(初始平均粒径为14nm)和ry50型号(初始平均粒径为40nm)的纳米级二氧化硅。
本发明中微米级二氧化硅和纳米级二氧化硅能够在涂层表面形成类荷叶效应的微纳米凸起,使涂层具有较好的超疏水效果,具体的,在实际使用过程中,水滴与涂层表面的微纳米凸起之间会形成空气通道,导致水滴与涂层表面的实际接触面积降低,从而使水滴容易从涂层表面滚落,起到超疏水作用;同时,微米级二氧化硅和纳米级二氧化硅的添加还可以使涂层具有较好的附着力和耐磨性。本发明优选通过控制微米级二氧化硅和纳米级二氧化硅的添加量以及粒度,有利于提高涂层的附着力、耐磨性和超疏水性。
在本发明中,以所述疏水改性环氧树脂的质量份数为基准,所述环氧树脂涂料的制备原料包括活性稀释剂25~50份,优选为25~35份;在本发明中,此处所述活性稀释剂的添加量不包括制备疏水改性环氧树脂时采用的活性稀释剂。在本发明中,所述活性稀释剂优选包括甲基丙烯酸缩水甘油酯、正丁基缩水甘油醚、烯丙基缩水甘油醚、5-乙基己基缩水甘油醚和丁二醇二缩水甘油醚中的一种或几种,更优选为甲基丙烯酸缩水甘油酯。在本发明中,制备环氧树脂涂料所用活性稀释剂的种类可以与制备疏水改性环氧树脂所用活性稀释剂的种类相同,也可以不相同。
在本发明中,活性稀释剂既能使微米级二氧化硅和纳米级二氧化硅更好地分散在疏水改性环氧树脂中,又有利于涂层的交联固化,无需使用可挥发性溶剂如丙酮、乙酸乙酯等,绿色环保。尤其如果以甲基丙烯酸缩水甘油酯作为活性稀释剂,所述甲基丙烯酸缩水甘油酯同时带有双键和环氧基团,有利于保证固化过程中阳离子型紫外光固化反应和自由基型紫外光固化反应顺利进行,进而提高涂料的固化速率、缩短固化时间。
本发明对于所述环氧树脂涂料的制备方法没有特殊的限定,将疏水改性环氧树脂、微米级二氧化硅、纳米级二氧化硅和活性稀释剂混合均匀即得到所述环氧树脂涂料。本发明对于各制备原料的加料顺序以及混合方式没有特殊的限定,能够保证各制备原料混合均匀即可;在本发明的实施例中,具体是将微米级二氧化硅和纳米级二氧化硅搅拌混合均匀,之后加入疏水改性环氧树脂和活性稀释剂,搅拌混合均匀,得到环氧树脂涂料。
本发明提供了一种超疏水性涂层,按质量份数计,包括以下制备原料:
上述技术方案所述的环氧树脂涂料100份;
阳离子光引发剂3~5份;
自由基光引发剂3~5份;
光敏剂1~5份。
在本发明中,按质量份数计,所述超疏水性涂层的制备原料包括上述技术方案所述的环氧树脂涂料100份。本发明以上述技术方案所述环氧树脂涂料为主体材料制备超疏水性涂层,能够保证所述超疏水性涂层具有较好的附着力、耐磨性和持久的超疏水性。
在本发明中,以所述环氧树脂涂料的质量份数为基准,所述超疏水性涂层的制备原料包括阳离子光引发剂3~5份,优选为3~4份。在本发明中,所述阳离子光引发剂优选包括三芳基锍六氟锑酸盐混合物或二苯基-(4-苯基硫)苯基锍六氟锑酸盐的丙烯酸酯溶液,其中,所述二苯基-(4-苯基硫)苯基锍六氟锑酸盐的丙烯酸酯溶液中二苯基-(4-苯基硫)苯基锍六氟锑酸盐的质量浓度优选为50%。
在本发明中,以所述环氧树脂涂料的质量份数为基准,所述超疏水性涂层的制备原料包括自由基光引发剂3~5份,优选为3~4份。在本发明中,所述自由基光引发剂包括双(2,4,6-三甲基苯甲酰基)苯基氧化膦、2,4,6-三甲基苯甲酰基-乙氧基-苯基氧化膦或2-异丙基硫杂蒽酮。
本发明利用阳离子光引发剂和自由基光引发剂配合使用,能够同时结合二者的优势,具体的,自由基光引发剂有利于提高固化速度,且光源匹配性好;阳离子光引发剂在固化过程中没有表面氧阻聚现象、涂层的收缩率小,且固化反应只要开始,即便撤掉紫外光源,固化反应还会持续进行。本发明采用阳离子光引发剂和自由基光引发剂混合固化体系,弥补了单一光引发剂的缺陷,提高了紫外光固化的应用优势。
在本发明中,以所述环氧树脂涂料的质量份数为基准,所述超疏水性涂层的制备原料包括光敏剂1~5份,优选为2~4份。在本发明中,所述光敏剂优选包括蒽、芘或苝。本发明利用光敏剂吸收光能跃迁至激发态,通过能量转移给光引发剂(即阳离子光引发剂和自由基光引发剂),光引发剂接受能量后由基态跃迁至激发态,产生活性中间体,引发聚合反应,得到超疏水性涂层。
本发明提供了上述技术方案所述超疏水性涂层的制备方法,包括以下步骤:
将环氧树脂涂料、阳离子光引发剂、自由基光引发剂和光敏剂混合,将所得混合物料涂覆到基底的表面形成湿膜,之后在紫外线照射条件下进行固化,在所述基底的表面形成超疏水性涂层。
本发明对于所述环氧树脂涂料、阳离子光引发剂、自由基光引发剂和光敏剂混合时各制备原料的加料顺序以及混合方式没有特殊的限定,能够将各制备原料混合均匀即可。
在本发明中,所述基底优选包括铝质基底、铁质基底、木质基底、玻璃钢基底或塑料基底;在本发明中,所述基底的表面具体是指基底上需要涂覆混合物料(即环氧树脂涂料、阳离子光引发剂、自由基光引发剂和光敏剂混合所得物料)形成超疏水性涂层的表面。
本发明对于所述涂覆的方式没有特殊的限定,采用本领域技术人员熟知的涂覆方式即可,具体如刷涂、喷涂或者浸涂;在本发明中,所述湿膜的厚度优选为0.5~2mm,更优选为1~1.5mm。
在本发明中,所述固化采用的光源优选包括紫外汞灯或者紫外led灯,所述紫外汞灯优选为高压紫外汞灯;所述光源与湿膜的距离优选为15~30cm,更优选为20~25cm;所述光源照射的时间优选为5~20min,更优选为10~15min。在本发明中,所述固化优选在室温条件下进行,即不需要额外的加热或降温。本发明在紫外线照射条件下进行固化,节能环保,不仅适合工厂流水线高速生产工作,而且也适合室外大面积施工操作,同时所得超疏水性涂层具有较好的附着力、耐磨性和持久的超疏水性。
下面将结合本发明中的实施例,对本发明中的技术方案进行清楚、完整地描述。显然,所描述的实施例仅仅是本发明一部分实施例,而不是全部的实施例。基于本发明中的实施例,本领域普通技术人员在没有做出创造性劳动前提下所获得的所有其他实施例,都属于本发明保护的范围。
实施例1
将100g双酚a型环氧树脂和50g甲基丙烯酸缩水甘油酯(gma)加入到配有电动搅拌器、恒温加热套和冷凝回流装置的四口烧瓶中,维持转速2000r/min,加热至120℃,维持温度恒定,用胶头滴管逐滴加入5滴催化剂二月桂酸二丁基锡,5min后用恒压漏斗每隔0.5h加入10g羟基聚二甲基硅氧烷(htpdms),共计加入80g,加入完毕后在120℃条件下保温反应2h(反应过程中需要补加gma,保证四口烧瓶中体系粘度适宜);待反应完成后,取出反应物冷却至室温,得到疏水改性环氧树脂;
将微米级二氧化硅(购自德国赢创工业集团)和纳米级二氧化硅(购自德国赢创工业集团)搅拌混合均匀,之后加入疏水改性环氧树脂和gma,搅拌混合均匀,得到环氧树脂涂料;其中,所述环氧树脂涂料中各组分添加量以及二氧化硅粒度见表1;
将所述环氧树脂涂料与阳离子光引发剂(三芳基锍六氟锑酸盐混合物,添加量为环氧树脂涂料质量的3%)、自由基光引发剂(双(2,4,6-三甲基苯甲酰基)苯基氧化膦,添加量为环氧树脂涂料质量的3%)和光敏剂(蒽,添加量为环氧树脂涂料质量的3%)搅拌混合均匀,将所得混合物料刷涂到基底(具体为玻璃)的单面,形成1mm厚的湿膜,之后在室温、紫外灯照射条件下进行固化(以高压紫外汞灯为光源,光源与湿膜的距离为20cm,照射时间为15min),得到超疏水性涂层,厚度为1mm。
实施例2~4
参照实施例1的方法制备超疏水性涂层,其中,制备环氧树脂涂料时各组分添加量以及二氧化硅粒度列于表1中。
表1实施例1~4制备环氧树脂涂料时各组分添加量以及二氧化硅粒度
对比例1
按照实施例1的方法制备涂层,不同之处在于,在制备环氧树脂涂料的过程中省略掉微米级二氧化硅。
对比例2
按照实施例1的方法制备涂层,不同之处在于,在制备环氧树脂涂料的过程中省略掉纳米级二氧化硅。
对比例3
按照实施例1的方法制备涂层,不同之处在于,在制备环氧树脂涂料的过程中省略掉微米级二氧化硅和纳米级二氧化硅。
对比例4
按照实施例1的方法制备涂层,不同之处在于,不对双酚a型环氧树脂进行改性处理,直接将所述双酚a型环氧树脂作为原料与其它原料(即微米级二氧化硅、纳米级二氧化硅和gma)混合制备环氧树脂涂料,并进一步以此环氧树脂涂料为原料制备涂层。
对实施例1~4制备的超疏水性涂层进行表征,具体如下:
图1和图2为实施例1制备的超疏水性涂层的场发射扫描电子显微镜(fesem)图,图1中,v1=20.10nm,v2=24.56nm;图2中v2=11.00μm。由图1和图2可知,微米级纳米二氧化硅在涂层中呈半包埋状,形成微米级凸起,纳米级二氧化硅隐没在微米级纳米二氧化硅之间,可以同时形成微米级凸起和纳米级乳突;微米级纳米二氧化硅和纳米级二氧化硅在涂层中形成微纳米二级粗糙结构,能够起到类荷叶效应,达到涂层超疏水的目的。
实施例2~4制备的超疏水性涂层的场发射扫描电子显微镜图与图1和图2类似,其制备的超疏水性涂层均具有微纳米二级粗糙结构,且所述超疏水性涂层中微米级凸起上分布着纳米级乳突。
将实施例1~4和对比例1~4制备的涂层进行性能测试,具体如下:
(1)耐磨性能测试的实验方法为:如图3所示,在涂层上铺设150目的砂布,然后在砂布上放置200g砝码,轻轻匀速拉动砝码一个来回(单次有效长度为20cm,即一个来回的长度共计40cm)记为一个磨损周期,测试磨损前和35个磨损周期后涂层的接触角,以此比较磨损前后涂层的性能差异;
(2)硬度采用bevs1301铅笔硬度计,按《gb/t6739-86》规定的方法进行测试;
(3)附着力采用bevs2202型划格器,按《gb/t9286-98》规定的方法进行测试。
性能测试结果列于表2中。
表2实施例1~4和对比例1~4制备的涂层的性能测试结果
由表2可知,本发明以疏水改性环氧树脂作为基体树脂,通过添加微米级二氧化硅和纳米级二氧化硅能够使涂层具有较好的超疏水效果、附着力和耐磨性;
其中,由实施例1和对比例1可知,未添加微米级二氧化硅的涂层的耐磨性较差,而加入微米级二氧化硅后会使涂层的耐磨性明显提高,这是因为微米级二氧化硅的加入,能够形成微米级凸起,是提高涂层耐磨性的关键点;虽然纳米级二氧化硅在形成纳米级乳突的同时也会聚集形成微米级凸起,但在使用过程中,纳米级二氧化硅形成的微米级凸起容易被磨散,导致耐磨性变差;
由实施例1和对比例2可知,未添加纳米级二氧化硅的涂层的疏水效果较差,而加入纳米级二氧化硅后会使涂层的疏水效果明显提高,这是因为纳米级二氧化硅是构建微纳米粗糙结构的基础,可以有效提高涂层超疏水效果;
由实施例1和对比例3可进一步得知微米级二氧化硅和纳米级二氧化硅对于改善涂层超疏水效果及耐磨性有重要作用;
由实施例1和对比例4可知,用疏水改性环氧树脂作为基体树脂制备的涂层具有更强的疏水性。
以上所述仅是本发明的优选实施方式,应当指出,对于本技术领域的普通技术人员来说,在不脱离本发明原理的前提下,还可以做出若干改进和润饰,这些改进和润饰也应视为本发明的保护范围。
起点商标作为专业知识产权交易平台,可以帮助大家解决很多问题,如果大家想要了解更多知产交易信息请点击 【在线咨询】或添加微信 【19522093243】与客服一对一沟通,为大家解决相关问题。
此文章来源于网络,如有侵权,请联系删除


