一种金刚石颗粒涂层油漆制备方法与流程



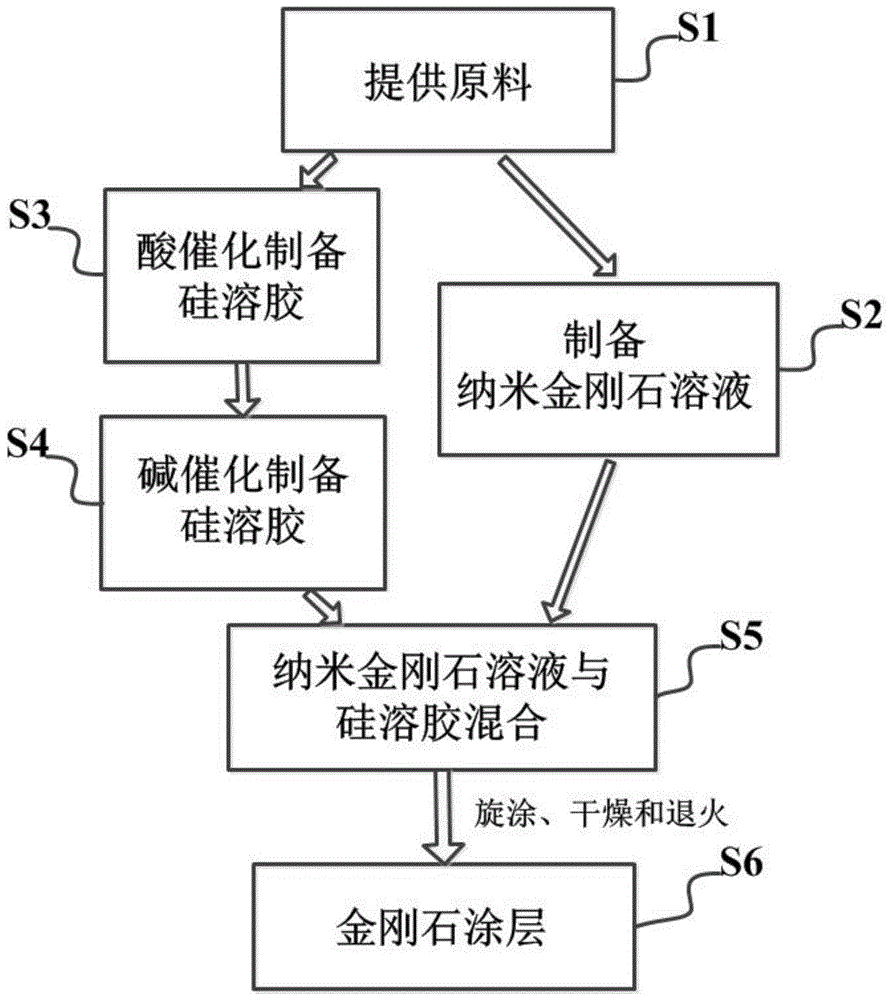
本发明涉及涂层油漆技术领域,尤其涉及一种金刚石颗粒涂层油漆制备方法。
背景技术:
涂层油漆电极和抗菌涂层油漆在我们的日常生活一直扮演着重要的角色。目前,在物理、化学、材料和医药等领域得到了较为广泛的应用。
金刚石涂层油漆凭借着耐磨性、和高热导率等特性在涂层油漆和涂层油漆领域具有广泛的应用前景。除此之外,金刚石拥有负电子亲和势和表面功能化的潜力。负电子亲和势的金刚石表面可释放大量电子可对带电荷的细菌产生一定程度的抑制作用;退火处理的金刚石表面可产生活性含氧基团,这些基团可促进金刚石和细菌结构组分的相互作用,也可达到抗菌的作用。因此,金刚石具有很好的抗菌性能。
其次,在制备金刚石涂层油漆的方法中,主要利用cvd、pvd法等方法制备。但这些方法成本较高,不易大规模工业化生产。然而,树脂和粘结剂法凭借着操作简单,成本低和易于规模生产等优势,成为涂层油漆制备领域行之有效的产业技术方法之一。
技术实现要素:
本发明的目的是为了解决现有技术中存在的缺点,而提出的一种金刚石颗粒涂层油漆制备方法。
为了实现上述目的,本发明采用了如下技术方案:
一种金刚石颗粒涂层油漆,包括表面功能化的金刚石颗粒粉、树脂前体、粘结剂、溶剂、催化剂和稳定剂等;一种金刚石颗粒涂层油漆制备方法包括以下步骤:
s1:先将金刚石颗粒表面层进行等离子体处理,在表面层掺杂n、s元素,实现负电子亲和能表面结构功能化;
s2:提供表面功能化的金刚石颗粒粉、硅溶胶前体、溶剂、去离子水、酸催化剂、碱催化剂、稳定剂和目标载体;
s3:将所述表面功能化的金刚石颗粒粉在50-900℃的温度下退火处理3~6h,退火后的金刚石粉加入溶剂超声处理30min,形成浓度为1~3g/l的稳定分散的金刚石溶液;
s4:将所述硅溶胶前体、溶剂、去离子水以1:3.5~4:1的摩尔比混合,所述酸催化剂调节溶液ph值至2~4,室温搅拌的时间是1~2.5h,初步得到硅溶胶;
s5:在所述硅溶胶中补加所述溶剂、去离子水和碱催化剂,使硅溶胶前体、溶剂、去离子水的最终摩尔配比为1:8~9:4,所述碱催化剂调节溶液ph值至7左右,室温搅拌1~2h;
s6:在所述硅溶胶中添加1%~10%(质量分数)的稳定剂,室温搅拌1~5h,得到最终的硅溶胶;
s7:在所述硅溶胶中加入5%~10%(质量分数)的所述金刚石溶液,继续室温搅拌1h,得到金刚石涂层油漆剂;
s8:将所述涂层油漆剂以1500r/min的速度参数在旋涂机上旋涂于所述目标载体上,旋涂时间为30s,冷冻干燥24h后以350~400℃的温度在空气中退火1h,从而得到所述金刚石涂层油漆。
优选的,其中所述硅溶胶前体选自包括正硅酸甲酯、正硅酸乙酯、正硅酸四乙酯、正硅酸丙酯、甲基三乙氧基硅烷或异氰酸丙基三乙氧基硅烷的任一种或多种,所述酸催化剂选自包括盐酸、硝酸、草酸或柠檬酸的任一种或多种,所述稳定剂选自包括聚乙烯醇、二月桂酸二丁基锡或丙三醇的任一种或多种,所述目标载体选自包括玻璃、金属、陶瓷和塑料等任一种或多种。
优选的,所述金刚石颗粒的颗粒直径范围为1nm-100μm,在涂层油漆内的质量百分比含量为0.01%-99%。
优选的,所述的金刚石颗粒粉、树脂前体、粘结剂、溶剂、催化剂和稳定剂等按照比例均匀混合而成。
优选的,所述金刚石颗粒涂层油漆为水性或者油性中任意一种。
优选的,所述水性的金刚石颗粒涂层油漆的溶剂是水或者水溶性溶剂,在木材、金属、塑料等许多种亲水性固体表面附着。
优选的,所述油性的金刚石颗粒涂层油漆的溶剂是油溶性溶剂,在木材、金属、塑料等许多种亲油性固体表面附着。
本发明的有益效果为:
1、本发明采用树脂和粘结剂的方法制备涂层油漆,涂层油漆耐磨性好,抗菌性好,性能稳定,制备方法和工艺简单。
2、本发明采用树脂和粘结剂的方法制备涂层油漆,相较于pvd和cvd制备金刚石涂层油漆,本发明的成本低,适合规模生产。
附图说明
图1为本发明提出的一种金刚石颗粒涂层油漆及其制备方法的制备流程结构示意图。
具体实施方式
下面将结合本发明实施例中的附图,对本发明实施例中的技术方案进行清楚、完整地描述,显然,所描述的实施例仅仅是本发明一部分实施例,而不是全部的实施例。
参照图1,一种金刚石颗粒涂层油漆制备方法,其特征在于,包括以下步骤:
实施例1:
s1:先将金刚石颗粒表面层进行等离子体处理,在表面层掺杂n、s元素,实现负电子亲和能表面结构功能化;
s2:提供表面功能化的金刚石颗粒粉、硅溶胶前体、溶剂、去离子水、酸催化剂、碱催化剂和目标载体;
s3:将所述表面功能化的金刚石颗粒粉在50℃的温度下退火处理3h,退火后的金刚石粉加入溶剂超声处理30min,形成浓度为1g/l的稳定分散的金刚石溶液;
s4:将所述硅溶胶前体、溶剂、去离子水以1:3.5~4:1的摩尔比混合,所述酸催化剂调节溶液ph值至2,室温搅拌的时间是1h,初步得到硅溶胶;
s5:在所述硅溶胶中补加所述溶剂、去离子水和碱催化剂,使硅溶胶前体、溶剂、去离子水的最终摩尔配比为1:8~9:4,所述碱催化剂调节溶液ph值至7左右,室温搅拌1h;
s6:在所述硅溶胶中添加1%(质量分数)的稳定剂,室温搅拌1h,得到最终的硅溶胶;
s7:在所述硅溶胶中加入5%(质量分数)的所述金刚石溶液,继续室温搅拌1h,得到金刚石涂层油漆剂;
s8:将所述涂层油漆剂以1500r/min的速度参数在旋涂机上旋涂于所述目标载体上,旋涂时间为30s,冷冻干燥24h后以350℃的温度在空气中退火1h,从而得到所述金刚石涂层油漆。
实施例2:
s1:先将金刚石颗粒表面层进行等离子体处理,在表面层掺杂n、s元素,实现负电子亲和能表面结构功能化;
s2:提供表面功能化的金刚石颗粒粉、硅溶胶前体、溶剂、去离子水、酸催化剂、碱催化剂和目标载体;
s3:将所述表面功能化的金刚石颗粒粉在450℃的温度下退火处理5h,退火后的金刚石粉加入溶剂超声处理30min,形成浓度为12g/l的稳定分散的金刚石溶液;
s4:将所述硅溶胶前体、溶剂、去离子水以1:3.5~4:1的摩尔比混合,所述酸催化剂调节溶液ph值至3,室温搅拌的时间是1.5h,初步得到硅溶胶;
s5:在所述硅溶胶中补加所述溶剂、去离子水和碱催化剂,使硅溶胶前体、溶剂、去离子水的最终摩尔配比为1:8~9:4,所述碱催化剂调节溶液ph值至7左右,室温搅拌1.5h;
s6:在所述硅溶胶中添加3%(质量分数)的稳定剂,室温搅拌1h,得到最终的硅溶胶;
s7:在所述硅溶胶中加入8%(质量分数)的所述金刚石溶液,继续室温搅拌1h,得到金刚石涂层油漆剂;
s8:将所述涂层油漆剂以1500r/min的速度参数在旋涂机上旋涂于所述目标载体上,旋涂时间为30s,冷冻干燥24h后以375℃的温度在空气中退火1h,从而得到所述金刚石涂层油漆。
实施例3:
s1:先将金刚石颗粒表面层进行等离子体处理,在表面层掺杂n、s元素,实现负电子亲和能表面结构功能化;
s2:提供表面功能化的金刚石颗粒粉、硅溶胶前体、溶剂、去离子水、酸催化剂、碱催化剂和目标载体;
s3:将所述表面功能化的金刚石颗粒粉在900℃的温度下退火处理6h,退火后的金刚石粉加入溶剂超声处理30min,形成浓度为1~3g/l的稳定分散的金刚石溶液;
s4:将所述硅溶胶前体、溶剂、去离子水以1:3.5~4:1的摩尔比混合,所述酸催化剂调节溶液ph值至4,室温搅拌的时间是2.5h,初步得到硅溶胶;
s5:在所述硅溶胶中补加所述溶剂、去离子水和碱催化剂,使硅溶胶前体、溶剂、去离子水的最终摩尔配比为1:8~9:4,所述碱催化剂调节溶液ph值至7左右,室温搅拌2h;
s6:在所述硅溶胶中添加5%(质量分数)的稳定剂,室温搅拌5h,得到最终的硅溶胶;
s7:在所述硅溶胶中加入10%(质量分数)的所述金刚石溶液,继续室温搅拌1h,得到金刚石涂层油漆剂;
s8:将所述涂层油漆剂以1500r/min的速度参数在旋涂机上旋涂于所述目标载体上,旋涂时间为30s,冷冻干燥24h后以400℃的温度在空气中退火1h,从而得到所述金刚石涂层油漆。
本发明,结合上述所述的实施例1-3,可以得知本发明实施例3得到的涂层油漆耐磨性好,抗菌性好,性能稳定。
在本发明的描述中,需要理解的是,术语“中心”、“纵向”、“横向”、“长度”、“宽度”、“厚度”、“上”、“下”、“前”、“后”、“左”、“右”、“竖直”、“水平”、“顶”、“底”、“内”、“外”、“顺时针”、“逆时针”等指示的方位或位置关系为基于附图所示的方位或位置关系,仅是为了便于描述本发明和简化描述,而不是指示或暗示所指的设备或元件必须具有特定的方位、以特定的方位构造和操作,因此不能理解为对本发明的限制。
此外,术语“第一”、“第二”仅用于描述目的,而不能理解为指示或暗示相对重要性或者隐含指明所指示的技术特征的数量。由此,限定有“第一”、“第二”的特征可以明示或者隐含地包括一个或者更多个该特征。在本发明的描述中,“多个”的含义是两个或两个以上,除非另有明确具体的限定。
以上所述,仅为本发明较佳的具体实施方式,但本发明的保护范围并不局限于此,任何熟悉本技术领域的技术人员在本发明揭露的技术范围内,根据本发明的技术方案及其发明构思加以等同替换或改变,都应涵盖在本发明的保护范围之内。
起点商标作为专业知识产权交易平台,可以帮助大家解决很多问题,如果大家想要了解更多知产交易信息请点击 【在线咨询】或添加微信 【19522093243】与客服一对一沟通,为大家解决相关问题。
此文章来源于网络,如有侵权,请联系删除


