环保型耐高温粉末涂料及其制备方法与流程



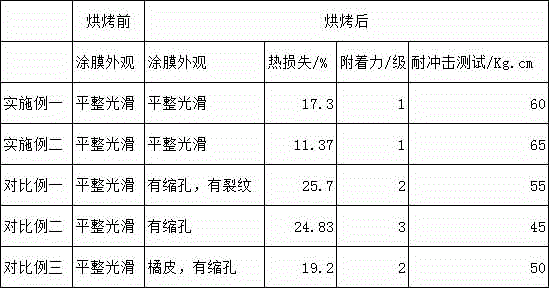
本发明涉及粉末涂料制备技术领域,尤其涉及环保型耐高温粉末涂料及其制备方法。
背景技术:
粉末涂料是一种以固体树脂和颜料、填料及助剂等组成的固体粉末状合成树脂涂料。和普通溶剂型涂料及水性涂料不同,它的分散介质不是溶剂和水,而是空气。它具有无溶剂污染,100%成膜,能耗低的特点。粉末涂料有热塑性和热固性两大类。
粉末涂料在喷涂后使用过程中,当温度过高时,粉末涂层内的作为流平剂使用的助剂容易挥发,从而影响涂层在高温时的使用性能,而且粉末涂层在长时间高温状态时,物理性能受影响较为严重,高温状态受影响的还包括在对热氧抑制上,都不能达到理想水平。
技术实现要素:
本发明所要解决的技术问题,是针对上述存在的技术不足,提供了环保型耐高温粉末涂料及其制备方法,采用含硅丙烯酸酯作为流平剂使用,实现了在持续高温状态时,相较传统流平剂减少了挥发流失,解决了由于流平剂大量挥发流失从而影响涂层机械性能的问题;采用有机硅树脂、复合抗氧化剂与含硼玻璃粉配合,实现了涂层在高温状态依然保持较好的机械性能,解决了在粉末涂料涂料在高温状态时机械性能较差的问题;采用由硅微粉、锰铁黑、消光钡、滑石粉所组成的颜填料,实现了在高温时,颜料里挥发损失较少,也避免了由于颜填料的挥发从而污染环境的问题。
为解决上述技术问题,本发明所采用的技术方案是:该粉末涂料包括下列重量份的原料配比组成:有机硅树脂30-40份、环氧树脂10-15份、取代双氰胺10-20份、含硼玻璃粉8-20份、颜填料5-20份、复合抗氧化剂1-5份、含硅丙烯酸酯0.1-5份、硅烷偶联剂0.5-1份;
所述含硼玻璃粉由以下重量份的原料配比组成:玻璃粉80-90份、氮化硼1-5份、氧化硼1-5份;
所述颜填料为硅微粉、锰铁黑、消光钡中至少两种混合后,然后再添加相同重量份的滑石粉混合而成;
所述复合抗氧剂由以下重量份的原料配比组成:抗氧剂101030-40份、抗氧剂16810-20份、抗氧剂107620-30份;
该粉末涂料是通过以下步骤制得的:
a、首先在混合器内加入玻璃粉、氮化硼、氧化硼、将其混合均匀为含硼玻璃粉;
b、然后再在混合器中加入有机硅树脂、环氧树脂、取代双氰胺、与混合均匀后的含硼玻璃粉,低速混合3分钟,高速混合2分钟;低速混合转速为120r/min,高速混合转速为600r/min;
c、然后再在混合器内加入颜填料、复合抗氧化剂、含硅丙烯酸酯、硅烷偶联剂,高速混合6分钟,高速混合转速为600r/min;
d、将步骤c中混合好的混合材料,放入双螺杆挤出机中进行挤出,挤出机熔融挤出1区温度设定为155-165℃,挤出机熔融挤出2区温度为183-186℃;
e、将步骤d中挤出的混合物经对辊压片机进行压片并冷却,然后经过初步破碎、acm粉碎、筛选得到最终粉末涂料产品。
进一步优化本技术方案,该粉末涂料包括下列重量份的原料配比组成:有机硅树脂35份、环氧树脂15份、取代双氰胺15份、含硼玻璃粉12份、颜填料12份、复合抗氧化剂3份、含硅丙烯酸酯2份、硅烷偶联剂0.8份;
所述含硼玻璃粉由以下重量份的原料配比组成:玻璃粉90份、氮化硼2.5份、氧化硼2.5份;
所述颜填料为硅微粉、锰铁黑、消光钡中至少两种混合后,然后再添加相同重量份的滑石粉混合而成;
所述复合抗氧剂由以下重量份的原料配比组成:抗氧剂101040份、抗氧剂16810份、抗氧剂107630份;
该粉末涂料是通过以下步骤制得的:
a、首先在混合器内加入玻璃粉、氮化硼、氧化硼、将其混合均匀为含硼玻璃粉;
b、然后再在混合器中加入有机硅树脂、环氧树脂、取代双氰胺、与混合均匀后的含硼玻璃粉,低速混合3分钟,高速混合2分钟;低速混合转速为120r/min,高速混合转速为600r/min;
c、然后再在混合器内加入颜填料、复合抗氧化剂、含硅丙烯酸酯、硅烷偶联剂,高速混合6分钟,高速混合转速为600r/min;
d、将步骤c中混合好的混合材料,放入双螺杆挤出机中进行挤出,挤出机熔融挤出1区温度设定为155-165℃,挤出机熔融挤出2区温度为183-186℃;
e、将步骤d中挤出的混合物经对辊压片机进行压片并冷却,然后经过初步破碎、acm粉碎、筛选得到最终粉末涂料产品。
进一步优化本技术方案,所述玻璃粉为350目。
进一步优化本技术方案,步骤e中所述的压片机,压片厚度为2.5-2.8mm。
进一步优化本技术方案,步骤e中所述筛选通过振动筛实现,筛选颗粒在280-320之间的为最终产品。
与现有技术相比,本发明具有以下优点:1、采用含硅丙烯酸酯作为流平剂使用,有利的保证了当高温时,相较传统流平剂减少了挥发流失;2、采用在粉末涂料中添加的有机硅树脂、复合抗氧化剂与含硼玻璃粉相互配合,有利的保证了涂层在高温状态依然保持较好的机械性能;3、由硅微粉、锰铁黑、消光钡、滑石粉所组成的颜填料,此结构有利的保证了高温时,颜料里挥发损失较少,也避免了由于颜填料的挥发从而污染环境的问题。
附图说明
图1为环保型耐高温粉末涂料及其制备方法的实验结果对比图。
具体实施方式
为使本发明的目的、技术方案和优点更加清楚明了,下面结合具体实施方式并参照附图,对本发明进一步详细说明。应该理解,这些描述只是示例性的,而并非要限制本发明的范围。此外,在以下说明中,省略了对公知结构和技术的描述,以避免不必要地混淆本发明的概念。
具体实施方式:
实施例一
该粉末涂料包括下列重量份(kg)的原料配比组成:有机硅树脂35份、环氧树脂15份、取代双氰胺15份、含硼玻璃粉12份、颜填料12份、复合抗氧化剂3份、含硅丙烯酸酯2份、硅烷偶联剂0.8份;
所述含硼玻璃粉由以下重量份的原料配比组成:玻璃粉90份、氮化硼2.5份、氧化硼2.5份;
所述颜填料为硅微粉3份、锰铁黑3份,然后再添加滑石粉3份混合而成;
所述复合抗氧剂由以下重量份的原料配比组成:抗氧剂101040份、抗氧剂16810份、抗氧剂107630份;
该粉末涂料是通过以下步骤制得的:
a、首先在混合器内加入玻璃粉、氮化硼、氧化硼、将其混合均匀为含硼玻璃粉;
b、然后再在混合器中加入有机硅树脂、环氧树脂、取代双氰胺、与混合均匀后的含硼玻璃粉,低速混合3分钟,高速混合2分钟;低速混合转速为120r/min,高速混合转速为600r/min;
c、然后再在混合器内加入颜填料、复合抗氧化剂、含硅丙烯酸酯、硅烷偶联剂,高速混合6分钟,高速混合转速为600r/min;
d、将步骤c中混合好的混合材料,放入双螺杆挤出机中进行挤出,挤出机熔融挤出1区温度设定为160℃,挤出机熔融挤出2区温度为185℃;
e、将步骤d中挤出的混合物经对辊压片机进行压片并冷却,然后经过初步破碎、acm粉碎、筛选得到最终粉末涂料产品。
实施例二
该粉末涂料包括下列重量份(kg)的原料配比组成:有机硅树脂40份、环氧树脂10份、取代双氰胺10份、含硼玻璃粉10份、颜填料8份、复合抗氧化剂5份、含硅丙烯酸酯3份、硅烷偶联剂1份;
所述含硼玻璃粉由以下重量份的原料配比组成:玻璃粉90份、氮化硼2.5份、氧化硼2.5份;
所述颜填料为锰铁黑2份、消光钡2份,然后再添加滑石粉4份混合而成;
所述复合抗氧剂由以下重量份的原料配比组成:抗氧剂101040份、抗氧剂16810份、抗氧剂107630份;
采用与实施例一相同的制作步骤即可制得成品。
对比例一
在实施例一的配料比中,不再添加含硅丙烯酸酯、复合抗氧化剂,其他与实施例相同,即制得成品。
对比例二
在实施例二的配料比中,不再添加复合抗氧化剂,其他与实施例二相同,即可制得成品。
对比例三
在实施例二的配料比中,颜填料中不再添加锰铁黑、消光钡,其他与实施例二相同,即可制得成品。
效果验证
将实施例一、实施例二、对比例一、对比例二、对比例三的多种粉末涂料,采用静电喷涂法喷涂到冷轧板上,在温度为220℃的环境下固化30min,涂层厚度约为60-80μm。
耐热实验采用将固化完成后的冷轧板置于马弗炉中,在650℃下烘烤1h,取出后对冷轧板进行检测。
测得实验结果如说明书附图1所示,可以看出,按照本发明制备所得的实施例一的粉末涂料涂层,在经过烘烤后,获得了优于实施例一的技术效果,而相比较,对比例一的所得,由于不再添加含硅丙烯酸酯、复合抗氧化剂,从而影响了在烘烤后表面的外观,而且热损失较大,附着力也变差,不能取得较好的技术效果;对比例二的所得,不再添加复合抗氧化剂,由于相较于对比例一添加了含硅丙烯酸酯,没有了裂纹出现,但是仍然存在热损失较多和缩孔的问题,而且附着力与耐冲击性能也不理想;对比例三由于颜填料中不再添加锰铁黑、消光钡,从而使得颜填料在热损失过程中失去较多,也影响了涂膜的表面外观,与其他性能。
应当理解的是,本发明的上述具体实施方式仅仅用于示例性说明或解释本发明的原理,而不构成对本发明的限制。因此,在不偏离本发明的精神和范围的情况下所做的任何修改、等同替换、改进等,均应包含在本发明的保护范围之内。此外,本发明所附权利要求旨在涵盖落入所附权利要求范围和边界、或者这种范围和边界的等同形式内的全部变化和修改例。
起点商标作为专业知识产权交易平台,可以帮助大家解决很多问题,如果大家想要了解更多知产交易信息请点击 【在线咨询】或添加微信 【19522093243】与客服一对一沟通,为大家解决相关问题。
此文章来源于网络,如有侵权,请联系删除


