一种防护涂层及其制备方法和应用与流程



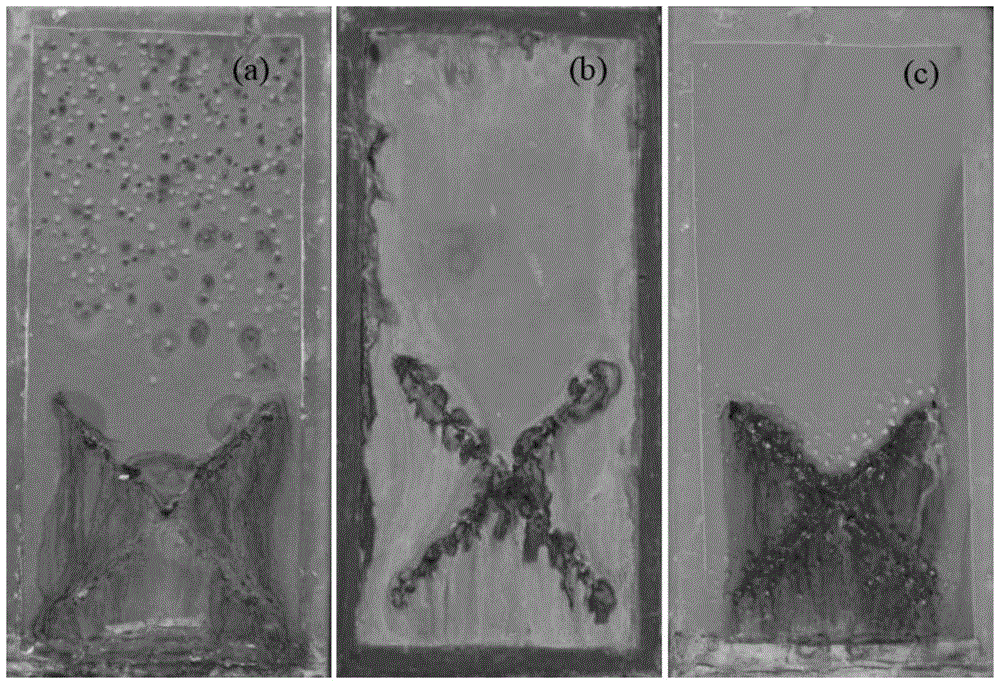
本申请属于钢铁防护的
技术领域:
,尤其涉及一种防护涂层及其制备方法和应用。
背景技术:
:有机涂层广泛应用于钢铁的防护,涂层与基体之间的附着力是其发挥保护作用的关键。随着服役时间的延长,有机涂层防护性能会逐步丧失,基体腐蚀生锈,需要对涂层进行再涂装。再涂装过程中,锈的存在会破坏新涂覆涂层与基体之间的附着。目前,传统工艺在涂覆涂层前,大多采用喷砂等方法对腐蚀表面进行除锈预处理,以保证有机涂层与基体间的附着力,然而除锈会带来严重的粉尘和噪声污染,并且受到构件结构及位置的极大限制。防止钢铁腐蚀的有效方法是向其表面涂装涂料。涂料耐腐蚀性能的强弱直接影响到钢铁使用寿命的长短。近些年来,人们对涂料进行了大量的研究,人们通过不同的方法对传统的涂料进行改性,以获得高性能的涂料。在众多改良涂料性能的技术中,纳米技术的出现,为涂料业的发展起到了推动作用。纳米粒子在涂料中的稳定存在是纳米技术在涂料业被广泛应用的关键。因为纳米材料表面效应的存在,使纳米颗粒与纳米颗粒之间容易碰撞,发生团聚现象,纳米粒子在涂料中不能稳定的存在,影响了纳米复合涂料的性能。所以在制备纳米复合涂料中,如何有效的将纳米粒子分散到涂料中是制备纳米涂料、保证纳米粒子在涂料中稳定存在的关键。但是,由于纳米颗粒在防护涂层浆料中不稳定,容易发生团聚现象,导致现有的含有纳米颗粒的防护涂层与基体的附着力较差,无法长时间提供防护作用。技术实现要素:有鉴于此,本申请公开了一种防护涂层及其制备方法,有效解决现有的含有纳米颗粒的防护涂层与基体的附着力较差,无法长时间提供防护作用的技术问题。本申请第一方面提供了一种防护涂层,包括:带锈液层、纳米环氧锌黄底漆层、纳米环氧云铁中间漆层和纳米氟碳面漆层;所述带锈液层设置在金属基材上,所述纳米环氧锌黄底漆层设置在所述带锈液层的表面,所述纳米环氧云铁中间漆层设置在所述纳米环氧锌黄底漆层的表面,所述纳米氟碳面漆层设置在所述纳米环氧云铁中间漆层的表面;所述带锈液层包括弱酸、钠盐、表面活性剂;其中,所述弱酸选自磷酸、单宁酸、醋酸、草酸、植酸及柠檬酸中的一种或多种,所述钠盐选自钼酸钠或/和植酸钠,所述表面活性剂选自十二烷基苯磺酸钠,异丙醇、叔丁醇、聚乙二醇、正丁醇和丙三醇中的一种或多种组成;所述纳米环氧锌黄底漆层包括环氧树脂、分散剂、磷酸锌、氧化铁黄、滑石粉、填料、混合溶剂和固化剂,其中,所述填料选自纳米铝粉、纳米锆粉和纳米二氧化硅中的一种或多种;所述纳米环氧云铁中间漆层包括环氧树脂、分散剂、滑石粉、云母氧化铁、填料、混合溶剂和固化剂,其中,所述填料选自纳米铝粉、纳米锆粉和纳米二氧化硅中的一种或多种;所述纳米氟碳面漆层包括氟碳树脂、消泡剂、聚酰胺蜡、混合溶剂、填料、溶剂和固化剂,其中,所述填料选自纳米铝粉、纳米锆粉和纳米二氧化硅中的一种或多种。需要说明的是,单宁酸在钼酸钠、柠檬酸促进作用下与锈层迅速反应形成带有微裂纹的单宁酸铁转化膜,通过机械互锁效应以及形成化学键增加了纳米环氧锌黄底漆层与转化膜的结合;同时混合醇促进单宁酸处理液渗透到锈层内部反应,不仅使锈层变得更加致密,也促进了转化膜与锈层的结合,可见,带锈液层对的单宁酸可与基体的锈层反应在表面形成带有微裂纹的单宁酸铁转化膜。并且部分处理液渗入多孔的内锈层中反应,增加了内锈层的致密性,提高了锈层的内聚力,有利于整个涂层体系附着力的提高。同时,从单宁酸与锈层的化学反应式出发,一个铁离子可以与三个单宁酸分子螯合,而单宁酸为大分子化合物也可以与多个铁离子反应,如此形成了网状的交织结构,这种结构一部分在表面的单宁酸转化膜内而另一部分却渗入到了内锈层,通过这种方式提高了单宁酸转化膜与锈层的结合。另外,当涂覆纳米环氧锌黄底漆层时,极易通过单宁酸转化膜的微裂纹渗透到内部,大量的微裂纹增大了涂层与转化膜的接触面积,有利于纳米环氧锌黄底漆层通过机械互锁效应牢固地与转化膜结合起来。而且单宁酸为多官能团化合物,形成的单宁酸铁转化膜中的活性官能团能够与纳米环氧锌黄底漆层中的活性官能团形成化学键,这也提高了转化膜与纳米环氧锌黄底漆层的结合。通过以上四个方面对附着力的促进,在单宁酸处理后纳米环氧锌黄底漆层/带锈结构钢涂层体系的附着力有了很大提升。作为优选,所述带锈液层具体包括:单宁酸5~20g/l;磷酸0~200g/l;钼酸钠1~4g/l;柠檬酸1~4g/l;混合醇5~20g/l;其中,所述混合混包括异丙醇和叔丁醇,所述异丙醇和所述叔丁醇的质量比为1:1;十二烷基苯磺酸钠0.5~5g/l。更为优选,所述带锈液层具体包括:单宁酸15g/l;磷酸50g/l;钼酸钠4g/l;柠檬酸1g/l;混合醇20g/l;其中,所述混合混包括异丙醇和叔丁醇,所述异丙醇和所述叔丁醇的质量比为1:1;十二烷基苯磺酸钠1g/l。本申请发现,单宁酸与磷酸的配合可以有效提高附着力,磷酸可为带锈液层提供合适的氢离子以及磷酸根离子浓度,有效地控制了带锈液层的浆料与锈层的反应速率,在转化膜中形成了有利于带锈液层的浆料渗透的狭小通道,增大了锈层转化程度,最终形成内聚力强的转化膜。另外,带有微裂纹及活性官能团的转化膜能与纳米环氧锌黄底漆层更好地结合。优选的,所述带锈液层的ph为2~5。作为优选,所述纳米环氧锌黄底漆层具体包括a组分和b组分,所述a组分与所述b组分的质量比为1:1~10:1;所述a组分包括:所述b组分包括:混合溶剂30%-70%;固化剂30%-70%。优选的,所述a组分与所述b组分的质量比为5:1。其中,所述纳米铝粉、所述纳米锆粉和所述纳米二氧化硅至少一种的添加量不为0。作为优选,所述纳米环氧云铁中间漆层具体包括c组分和d组分,所述c组分与所述d组分的质量比为1:1~10:1;所述c组分包括:所述d组分包括:混合溶剂30%-70%;固化剂30%-70%。优选的,所述c组分与所述d组分的质量比为5:1。其中,所述纳米铝粉、所述纳米锆粉和所述纳米二氧化硅至少一种的添加量不为0。作为优选,所述纳米氟碳面漆层具体包括e组分和f组分,所述e组分与所述f组分的质量比为5:1~10:1;所述e组分:所述f组分:溶剂10%-50%;固化剂50%-90%。优选的,所述e组分与所述f组分的质量比为10:1。其中,所述纳米铝粉、所述纳米锆粉和所述纳米二氧化硅至少一种的添加量不为0。需要说明的是,本申请发现将纳米铝粉分别与环氧树脂体系和氟碳树脂体系混合制得的纳米环氧锌黄底漆层、纳米环氧云铁中间漆层和纳米氟碳面漆层的防腐蚀性能大大提高,腐蚀后的产物xps分析结果显示:al优先参加腐蚀反应,生成的产物为al2o3和alooh或al(oh)3,实现了牺牲阳极保护,从而保护了金属基体;将纳米锆粉分别与环氧树脂体系和氟碳树脂体系混合制得的纳米环氧锌黄底漆层、纳米环氧云铁中间漆层和纳米氟碳面漆层的防腐蚀性能大大提高;含有纳米二氧化硅的纳米环氧锌黄底漆层、纳米环氧云铁中间漆层和纳米氟碳面漆层的防腐蚀性能大大提高。具体的,所述b组分中的固化剂和所述d组分中的固化剂为聚酰胺固化剂,所述f组分中的固化剂为脂肪族聚异氰酸酯(六亚甲基二异氰酸酯三聚体),购买自德国拜尔公司n3390的固化剂。具体的,所述a组分和所述b组分的混合溶剂包括二甲苯和正丁醇,所述二甲苯和所述正丁醇的体积比为7:3;所述c组分和所述d组分的混合溶剂包括二甲苯和正丁醇,所述二甲苯和所述正丁醇的体积比为7:3;所述e组分的混合溶剂包括二甲苯和丁酯,所述二甲苯和所述丁酯的体积比为7:3,所述f组分的溶剂为醋酸丁酯。具体的,本申请的助剂包括消泡剂、流平剂和防沉剂中的一种或多种。本申请第二方面提供了一种防护涂层的制备方法,包括以下步骤:步骤1、制备所述带锈液层的浆料、所述纳米环氧锌黄底漆层的浆料、所述纳米环氧云铁中间漆层的浆料和所述纳米氟碳面漆层的浆料;步骤2、将所述带锈液层设置在金属基材上;步骤3、所述纳米环氧锌黄底漆层设置在所述带锈液层的表面;步骤4、将所述纳米环氧云铁中间漆层的浆料设置在所述纳米环氧锌黄底漆层的表面;步骤5,将所述纳米氟碳面漆层的浆料设置在所述纳米环氧云铁中间漆层的表面;其中,所述带锈液层的浆料包括弱酸、钠盐、表面活性剂;其中,所述弱酸选自磷酸、单宁酸、醋酸、草酸、植酸及柠檬酸中的一种或多种,所述钠盐选自钼酸钠或/和植酸钠,所述表面活性剂选自十二烷基苯磺酸钠,异丙醇、叔丁醇、聚乙二醇、正丁醇和丙三醇中的一种或多种组成;所述纳米环氧锌黄底漆层的浆料包括环氧树脂、分散剂、磷酸锌、氧化铁黄、滑石粉、填料、混合溶剂和固化剂,其中,所述填料选自纳米铝粉、纳米锆粉和纳米二氧化硅中的一种或多种;所述纳米环氧云铁中间漆层的浆料包括环氧树脂、分散剂、滑石粉、云母氧化铁、填料、混合溶剂和固化剂,其中,所述填料选自纳米铝粉、纳米锆粉和纳米二氧化硅中的一种或多种;所述纳米氟碳面漆层包括氟碳树脂、消泡剂、聚酰胺蜡、混合溶剂、填料、溶剂和固化剂,其中,所述填料选自纳米铝粉、纳米锆粉和纳米二氧化硅中的一种或多种。作为优选,所述纳米环氧锌黄底漆层的浆料的制备方法具体包括:1.1、将分散剂、混合溶剂和填料混合,制得纳米填料浆;其中,所述填料选自纳米铝粉、纳米锆粉和纳米二氧化硅中的一种或多种;1.2、将所述纳米填料浆与环氧树脂、磷酸锌、氧化铁黄和滑石粉混合,制得a组分;将混合溶剂和固化剂混合,制得b组分;1.3、将所述a组分和所述b组分混合,制得纳米环氧锌黄底漆层的浆料。其中,所述纳米环氧锌黄底漆层具体包括a组分和b组分,所述a组分与所述b组分的质量比为1:1~10:1;所述a组分包括:所述b组分包括:混合溶剂30%-70%;固化剂30%-70%。作为优选,所述纳米环氧云铁中间漆层的浆料的制备方法具体包括:2.1、将分散剂、混合溶剂和填料混合,制得纳米填料浆;其中,所述填料选自纳米铝粉、纳米锆粉和纳米二氧化硅中的一种或多种;2.2、将所述纳米填料浆与环氧树脂、云母氧化铁和滑石粉混合,制得c组分;将混合溶剂和固化剂混合,制得d组分;2.3、将所述c组分和所述d组分混合,制得纳米环氧云铁中间漆层的浆料。其中,所述纳米环氧云铁中间漆层具体包括c组分和d组分,所述c组分与所述d组分的质量比为1:1~10:1;所述c组分包括:所述d组分包括:混合溶剂30%-70%;固化剂30%-70%。作为优选,所述纳米氟碳面漆层的浆料的制备方法具体包括:3.1、将聚酰胺蜡、混合溶剂和填料混合,制得纳米填料浆;其中,所述填料选自纳米铝粉、纳米锆粉和纳米二氧化硅中的一种或多种;3.2、将所述纳米填料浆、氟碳树脂和消泡剂混合,制得e组分;将溶剂和固化剂混合,制得f组分;3.3、将所述e组分和所述f组分混合,制得纳米氟碳面漆层的浆料。其中,所述纳米氟碳面漆层具体包括e组分和f组分,所述e组分与所述f组分的质量比为5:1~10:1;所述e组分:所述f组分:溶剂10%-50%;固化剂50%-90%。需要说明的是,本申请发现先将a组分的填料制成纳米填料浆后,例如分别制成纳米二氧化硅浆、纳米铝浆或纳米锆浆,在分别与纳米环氧锌黄底漆层、纳米环氧云铁中间漆层和纳米氟碳面漆层的其他成分混合,使得纳米填料能分散更均匀,纳米填料的分散状态有助于涂层性能的提高。优选的,a组分的纳米二氧化硅浆中二氧化硅的固含量为18%;c组分纳米二氧化硅浆中二氧化硅的固含量为18%;a组分的纳米铝浆中铝粉的固含量为50%;c组分的纳米铝浆中铝粉的固含量为50%;a组分的纳米锆粉浆中纳米锆粉的含量为10%,c组分的纳米锆粉浆中纳米锆粉的含量为10%。具体的,a组分、c组分和e组分的纳米二氧化硅的粒径为20nm。具体的,a组分的磷酸锌的粒径为325目,a组分的氧化铁黄为325目,a组分的滑石粉的粒径为600目;c组分的云母氧化铁的粒径为400目,c组分的滑石粉的粒径为800目。优选的,所述带锈液层的浆料的ph为2~5。本申请第三方面公开了所述防护涂层或所述制备方法制得的防护涂层在防止金属基体腐蚀中的应用。具体的,所述金属基体为钢材或镀锌钢。本申请的防护涂层,包括:带锈液层、纳米环氧锌黄底漆层、纳米环氧云铁中间漆层和纳米氟碳面漆层,首先,带锈液层带锈处理基材可直接在一定锈蚀表面上施工,通过带锈液层浆料与锈层反应形成转化膜,然后再依次涂覆纳米环氧锌黄底漆层、纳米环氧云铁中间漆层和纳米氟碳面漆层。本申请的纳米环氧锌黄底漆层是防护涂层的第一层,用于增加其他涂料的附着力,增加防护涂层的丰满度以及纳米氟碳面漆层的使用寿命,使纳米氟碳面漆层更好的展现其本身的特性,阻止涂料渗透过毛细孔被吸收,还可以封闭基材的碱性物质向上层渗透,减少纳米氟碳面漆层的用量;本申请的纳米环氧云铁中间漆层具有较好的防腐蚀能力和附着力,可提高纳米氟碳面漆层的涂装效果和涂膜整体的耐腐蚀能力,并能延长使用寿命,纳米环氧云铁中间漆层具有坚牢的结合力,水汽渗透率低,是优良的屏蔽型防护涂料,适用于钢结构中间涂层。本申请的纳米氟碳面漆层中氟碳树脂分子连上的氟碳键能够抵抗紫外线的降解作用,表现出极其优异的耐久性、耐紫外线及耐候性,使纳米氟碳面漆层长久完美如新,减少现场工况重复维护的要求,降低劳动强度,节约维护费用。实验测得,本申请的防护涂层的结合力高,寿命长,防腐时间超过15年。附图说明为了更清楚地说明本申请实施例或现有技术中的技术方案,下面将对实施例或现有技术描述中所需要使用的附图作简单地介绍。图1为本申请实施例提供的实施例1、实施例2的纳米环氧锌黄底漆层和对比例1的对照防护涂层a的盐雾试验结果图;图2为本申请实施例提供的实施例1、实施例2的纳米环氧锌黄底漆层和对比例1的对照防护涂层a和对照防护涂层b的氙灯老化的色差△e结果图;图3为本申请实施例提供的实施例1、实施例2的纳米环氧锌黄底漆层和对比例1的对照防护涂层a和对照防护涂层b的氙灯老化的失光率结果图;图4为本申请实施例提供的不同磷酸浓度的带锈液层浆料对纳米环氧锌黄底漆层与带锈结构钢之间的附着力影响图;图5为本申请实施例提供的直接添加纳米二氧化硅制得的纳米环氧锌黄底漆层浆料,和将纳米二氧化硅制成纳米二氧化硅浆后制得的纳米环氧锌黄底漆层浆料的tem图,其中,(a)为直接添加纳米二氧化硅制得的对照组浆料,(b)为将纳米二氧化硅制成纳米二氧化硅浆后制得的试验组浆料。具体实施方式本申请提供了一种防护涂层及其制备方法,有效解决现有的含有纳米颗粒的防护涂层与基体的附着力较差,无法长时间提供防护作用的技术缺陷。下面将对本申请实施例中的技术方案进行清楚、完整地描述,显然,所描述的实施例仅仅是本申请一部分实施例,而不是全部的实施例。基于本申请中的实施例,本领域普通技术人员在没有做出创造性劳动前提下所获得的所有其他实施例,都属于本申请保护的范围。本申请的防护涂层表征:(1)涂层附着力涂层附着力测试采用的仪器是由美国delelsko公司生产的positestat-a全自动拉拔式附着力检测仪。测试的具体过程为:首先为了保证附着力测试铝柱与环氧涂层间能够更好地结合,用400#的砂纸对环氧涂层以及测试铝柱表面进行轻轻地打磨使其变得粗糙,然后用无水酒精洗去表面的污染物后吹干,并用快固ab胶粘剂(a与b的体积比为1:1)将涂层表面与拉伸铝柱(直径20mm)粘接起来,在室温下放置24h以保证粘接剂完全固化。为了避免在测试过程中测试面积以外的环氧涂层对测试面积内的涂层附着力产生影响,在测试前先用直径20mm的圆形刀片沿着测试铝柱周围将测试面积内外的涂层分离。接着依照iso4624-2002测量把涂层从基体上拉开时所需的临界附着强度,该值就是涂层与金属的附着力。每组实验选取6个平行样,平均值即为最终的附着力结果。(2)宏观照片本文中宏观形貌照片都采用尼康公司生产的nikond3100型数码相机。(3)盐雾试验盐雾试验采用江苏淮安市中亚试验设备有限公司ywx/q系列试验盐雾腐蚀试验箱进行试验,盐雾测试依据gb/t1771-2007标准进行。试验温度为35±2℃,5%nacl溶液连续喷雾。评价起泡面积使用百分格板,微泡:肉眼仅可看见;小泡:肉眼明显可见,直径在0.5mm以下;中泡:直径0.6~1mm;大泡:直径1.1mm以上。(4)氙灯老化试验氙灯老化试验以氙弧灯作为辐照光源。试验样品安装于试验箱内,保证试验样品的试验条件一致,能自动控制辐照度、黑板温度、箱体空气温度和箱内相对湿度。氙灯老化试验依据gb/t32088-2015标准进行。(5)透射电镜(transmissionelectronmicroscopy,tem)采用jem-2100f透射电子显微镜(日本电子株式会社)测试纳米锆粉的粒径,测试时加速电压为200kv。(6)涂层的力学性能包括铅笔硬度、冲击强度、附着力(划圈法、拉开法)以及柔韧性。此外还有涂层的光泽和测试涂层厚度。主要的测试指标依据的标准如下:1)涂层的光泽依据gb1743-79;2)涂层的厚度测量依据gb1764-79;3)涂层的铅笔硬度依据gb/t6739-2006;4)涂层的冲击强度依据gb/t20624.2-2006;5)色漆和清漆漆膜的划格试验gb/t9286-1998;6)涂层的柔韧性依据gb/t1731-1993;7)涂层拉开法附着力测定依据gb/t5210-2006。其中,以下实施例所用原料或试剂均为市售或自制,分散剂购买自德国毕克公司byk110的分散剂;b组分和d组分的固化剂为聚酰胺,购买自江苏三木公司,型号为650;环氧树脂,购买自江苏三木公司的75%e20溶液;f组分的固化剂购买自德国拜尔公司,型号为n3390;聚酰胺蜡购买自天津环琦化工有限公司,其型号是ultra;消泡剂购买自德国毕克公司,其型号为byk065;氟碳树脂购买自日本大金公司,其型号为gk570。实施例1本申请实施例提供了第一种防护涂层,其具体制备方法包括:1、制备带锈液层的浆料、纳米环氧锌黄底漆层的浆料、纳米环氧云铁中间漆层的浆料和纳米氟碳面漆层的浆料。带锈液层的浆料包括:单宁酸15g/l;磷酸50g/l;钼酸钠4g/l;柠檬酸1g/l;混合醇20g/l;其中,混合混包括异丙醇和叔丁醇,异丙醇和叔丁醇的质量比为1:1。纳米环氧锌黄底漆层的浆料包括:1.1、按照混合溶剂:分散剂:纳米铝粉为44:1:4的质量比,将分散剂、混合溶剂和纳米铝粉混合,制得纳米铝粉浆;按照混合溶剂:分散剂:纳米锆粉为44:1:4的质量比,将分散剂、混合溶剂和纳米锆粉混合,制得纳米锆粉浆;按照混合溶剂:分散剂:纳米二氧化硅为44:1:4的质量比,将分散剂、混合溶剂和纳米二氧化硅混合,制得纳米二氧化硅浆;1.2、将纳米铝粉浆、纳米锆粉浆、纳米二氧化硅浆、环氧树脂、磷酸锌、氧化铁黄和滑石粉混合,制得a组分;其中,环氧树脂在a组分的质量分数为50%、磷酸锌在a组分的质量分数为20%、氧化铁黄在a组分的质量分数为1%、滑石粉在a组分的质量分数为26%、纳米铝浆在a组分的质量分数为1%、纳米锆浆在a组分的质量分数为1%和纳米二氧化硅浆在a组分的质量分数为1%混合;将混合溶剂和聚酰胺混合,制得b组分;其中,混合溶剂在b组分的质量分数为40%,聚酰胺在b组分的质量分数为60%;1.3、按照a组分:b组分为5:1的质量比,将a组分和b组分混合,制得纳米环氧锌黄底漆层的浆料。纳米环氧云铁中间漆层的浆料包括:2.1、按照混合溶剂:分散剂:纳米铝粉为90:1:5的质量比,将分散剂、混合溶剂和纳米铝粉混合,制得纳米铝粉浆;按照混合溶剂:分散剂:纳米锆粉为90:1:5的质量比,分散剂、混合溶剂和纳米锆粉混合,制得纳米锆粉浆;按照混合溶剂:分散剂:纳米二氧化硅为90:1:5的质量比,分散剂、混合溶剂和纳米二氧化硅混合,制得纳米二氧化硅浆;2.2、将纳米铝粉浆、纳米锆粉浆、纳米二氧化硅浆、环氧树脂、云母氧化铁和滑石粉混合,制得c组分;其中,环氧树脂在c组分的质量分数为50%、滑石粉在c组分的质量分数为30%、云母氧化铁在c组分的质量分数为17%、纳米铝粉浆在c组分的质量分数为1%、纳米锆粉浆在c组分的质量分数为1%和纳米二氧化硅浆在c组分的质量分数为1%混合;将混合溶剂和聚酰胺混合,制得d组分;其中,混合溶剂在d组分的质量分数为60%,聚酰胺在d组分的质量分数为40%;2.3、按照c组分:d组分为5:1的质量比,将c组分和d组分5:1混合,制得纳米环氧云铁中间漆层的浆料。纳米氟碳面漆层的浆料包括:3.1、按照聚酰胺蜡:混合溶剂:纳米铝粉为1:70:2的质量比,将聚酰胺蜡、混合溶剂和纳米铝粉混合,制得纳米铝粉浆;按照聚酰胺蜡:混合溶剂:纳米锆粉为1:70:2的质量比,将聚酰胺蜡、混合溶剂和纳米锆粉混合,制得纳米锆粉浆;按照聚酰胺蜡:混合溶剂:纳米二氧化硅为1:70:2的质量比,将聚酰胺蜡、混合溶剂和纳米二氧化硅混合,制得纳米二氧化硅浆;3.2、将纳米填料浆、氟碳树脂和消泡剂混合,制得e组分;氟碳树脂在e组分的质量分数为80%、消泡剂在e组分的质量分数为0.5%、聚酰胺蜡在e组分的质量分数为0.5%、纳米铝粉浆在e组分的质量分数为17%、纳米锆粉浆1%和纳米二氧化硅浆在e组分的质量分数为1%;将醋酸丁酯和n3390的固化剂混合,制得f组分;其中,醋酸丁酯在f组分的质量分数为10%,n3390的固化剂在f组分的质量分数为90%;3.3、按照e组分:f组分为10:1的质量比,将e组分和f组分混合,制得纳米氟碳面漆层的浆料。a组分、b组分、c组分、d组分和e组分的混合溶剂包括二甲苯和正丁醇,二甲苯和正丁醇的体积比为7:3。2、将带锈液层的浆料涂覆在带锈结构钢材上;测定带锈液层的浆料与带锈结构钢材的附着力,带锈结构钢与带锈液层的附着力达到5.7。3、将步骤1制得的纳米环氧锌黄底漆层的浆料涂覆在干燥后的带锈液层的表面;测定带锈液层与纳米环氧锌黄底漆层的附着力,纳米环氧锌黄底漆层与带锈液层的附着力达到18;4、将步骤1制得的纳米环氧云铁中间漆层的浆料涂覆在干燥后的纳米环氧锌黄底漆层的表面;5,将步骤1制得的纳米氟碳面漆层的浆料涂覆在干燥后的纳米环氧云铁中间漆层的表面。实施例2本申请实施例提供了第二种防护涂层,其具体制备方法包括:1、制备带锈液层的浆料、纳米环氧锌黄底漆层的浆料、纳米环氧云铁中间漆层的浆料和纳米氟碳面漆层的浆料。带锈液层的浆料包括:单宁酸15g/l;磷酸50g/l;钼酸钠4g/l;柠檬酸1g/l;混合醇20g/l;其中,混合混包括异丙醇和叔丁醇,异丙醇和叔丁醇的质量比为1:1。纳米环氧锌黄底漆层的浆料包括:1.1、按照混合溶剂:分散剂:纳米铝粉为44:1:4的质量比,将分散剂、混合溶剂和纳米铝粉混合,制得纳米铝粉浆;按照混合溶剂:分散剂:纳米锆粉为44:1:4的质量比,将分散剂、混合溶剂和纳米锆粉混合,制得纳米锆粉浆;按照混合溶剂:分散剂:纳米二氧化硅为44:1:4的质量比,将分散剂、混合溶剂和纳米二氧化硅混合,制得纳米二氧化硅浆;1.2、将纳米铝粉浆、纳米锆粉浆、纳米二氧化硅浆、环氧树脂、磷酸锌、氧化铁黄和滑石粉混合,制得a组分;其中,环氧树脂在a组分的质量分数为20%、磷酸锌在a组分的质量分数为30%、氧化铁黄在a组分的质量分数为5%、滑石粉在a组分的质量分数为15%、纳米铝浆在a组分的质量分数为10%、纳米锆浆在a组分的质量分数为10%和纳米二氧化硅浆在a组分的质量分数为10%混合;将混合溶剂和聚酰胺混合,制得b组分;其中,混合溶剂在b组分的质量分数为40%,聚酰胺在b组分的质量分数为60%;1.3、按照a组分:b组分为1:1的质量比,将a组分和b组分混合,制得纳米环氧锌黄底漆层的浆料。纳米环氧云铁中间漆层的浆料包括:2.1、按照混合溶剂:分散剂:纳米铝粉为90:1:5的质量比,将分散剂、混合溶剂和纳米铝粉混合,制得纳米铝粉浆;按照混合溶剂:分散剂:纳米锆粉为90:1:5的质量比,分散剂、混合溶剂和纳米锆粉混合,制得纳米锆粉浆;按照混合溶剂:分散剂:纳米二氧化硅为90:1:5的质量比,分散剂、混合溶剂和纳米二氧化硅混合,制得纳米二氧化硅浆;2.2、将纳米铝粉浆、纳米锆粉浆、纳米二氧化硅浆、环氧树脂、云母氧化铁和滑石粉混合,制得c组分;其中,环氧树脂在c组分的质量分数为20%、滑石粉在c组分的质量分数为30%、云母氧化铁在c组分的质量分数为35%、纳米铝粉浆在c组分的质量分数为5%、纳米锆粉浆在c组分的质量分数为5%和纳米二氧化硅浆在c组分的质量分数为5%混合;将混合溶剂和聚酰胺混合,制得d组分;其中,混合溶剂在d组分的质量分数为60%,聚酰胺在d组分的质量分数为40%;2.3、按照c组分:d组分为1:1的质量比,将c组分和d组分混合,制得纳米环氧云铁中间漆层的浆料。纳米氟碳面漆层的浆料包括:3.1、按照聚酰胺蜡:混合溶剂:纳米铝粉为1:70:2的质量比,将聚酰胺蜡、混合溶剂和纳米铝粉混合,制得纳米铝粉浆;按照聚酰胺蜡:混合溶剂:纳米锆粉为1:70:2的质量比,将聚酰胺蜡、混合溶剂和纳米锆粉混合,制得纳米锆粉浆;按照聚酰胺蜡:混合溶剂:纳米二氧化硅为1:70:2的质量比,将聚酰胺蜡、混合溶剂和纳米二氧化硅混合,制得纳米二氧化硅浆;3.2、将纳米填料浆、氟碳树脂和消泡剂混合,制得e组分;氟碳树脂在e组分的质量分数为68%、消泡剂在e组分的质量分数为1%、聚酰胺蜡在e组分的质量分数为1%、纳米铝粉浆在e组分的质量分数为20%、纳米锆粉浆5%和纳米二氧化硅浆在e组分的质量分数为5%;将醋酸丁酯和n3390的固化剂混合,制得f组分;其中,醋酸丁酯在f组分的质量分数为50%,n3390的固化剂在f组分的质量分数为50%;3.3、按照e组分:f组分为5:1的质量比,将e组分和f组分混合,制得纳米氟碳面漆层的浆料。a组分、b组分、c组分、d组分和e组分的混合溶剂包括二甲苯和正丁醇,二甲苯和正丁醇的体积比为7:3。2、将带锈液层的浆料涂覆在带锈结构钢材上;测定带锈液层的浆料与带锈结构钢材的附着力,带锈结构钢与带锈液层的附着力达到5.7。3、将步骤1制得的纳米环氧锌黄底漆层的浆料涂覆在干燥后的带锈液层的表面;测定带锈液层与纳米环氧锌黄底漆层的附着力,纳米环氧锌黄底漆层与带锈液层的附着力达到11;4、将步骤1制得的纳米环氧云铁中间漆层的浆料涂覆在干燥后的纳米环氧锌黄底漆层的表面;5,将步骤1制得的纳米氟碳面漆层的浆料涂覆在干燥后的纳米环氧云铁中间漆层的表面。对比例1本申请对比例提供了第一种对照防护涂层,对照防护涂层不含有纳米铝粉、纳米锆粉和纳米二氧化硅:现有常规的涂层为中山牌丙烯酸配套漆,中山牌丙烯酸配套漆的底漆成分包括:环氧树脂、丙烯腈、聚氨酯和溶剂,中山牌丙烯酸配套漆的中间漆成分包括:环氧树脂、丙烯腈、云母氧化铁、聚氨酯和溶剂,中山牌丙烯酸配套漆的面漆成分包括:甲苯、氯化聚丙烯、甲基丙烯酸二甲胺乙酯、甲基丙烯酸甲酯、丙烯酸丁酯、苯乙烯和沤氮二异丁氰,标记为对照防护涂层a。现有常规的涂层为中山牌醇酸漆,中山牌醇酸漆包括200号溶剂油和树脂标记为对照防护涂层b。实施例3本申请实施例为测定实施例1和实施例2的纳米环氧锌黄底漆层、对比例1的对照防护涂层的附着力,包括:1、采用拉开法测定实施例1和实施例2的纳米环氧锌黄底漆层,和对比例1的对照防护涂层的附着力,结果如表1所示。表1实施例1和实施例2的纳米环氧锌黄底漆层,和对比例1的对照防护涂层的附着力对比试验编号附着力平均值(mpa)实施例118.5实施例211.8对比例17.92、对实施例1和实施例2的纳米环氧锌黄底漆层,和对比例1的对照防护涂层a的底漆进行盐雾试验,结果如图1所示,图1为本申请实施例提供的实施例1、实施例2的纳米环氧锌黄底漆层和对比例1的对照防护涂层a的底漆的盐雾试验结果图。从图1可知,盐雾试验2000小时后,可以看到对比例1的对照防护涂层a的底漆划叉处被腐蚀产物充满,划叉附近锈迹斑斑。没有划叉的部位严重出现锈点,说明对比例1的对照防护涂层a的底漆缺陷较多,盐雾和盐水从缺陷的部位渗透到基体,基体被腐蚀。而实施例1和实施例2的纳米环氧锌黄底漆层只在划叉两侧处有锈蚀,其余样板表面没有锈点,涂层表面均匀,缺陷少。3、对实施例1和实施例2的纳米氟碳面漆,和对比例1的对照防护涂层a和对照防护涂层b进行氙灯老化试验,结果如图2~3所示,图2为本申请实施例提供的实施例1、实施例2的纳米氟碳面漆和对比例1的对照防护涂层a和对照防护涂层b的氙灯老化的色差△e结果图,图3为本申请实施例提供的实施例1、实施例2的纳米氟碳面漆和对比例1的对照防护涂层a和对照防护涂层b的氙灯老化的失光率结果图,其中,a为对比例1的对照防护涂层a,b为对比例1对照防护涂层b,i为实施例1的纳米氟碳面漆层,k为实施例2的纳米氟碳面漆层。从图2中可以看出,耐氙灯老化1500h后,各种涂层的色差都有一定的升高,对比例1的对照防护涂层a和对照防护涂层b色差变化△e为5.66和3.58,实施例1的纳米环氧锌黄底漆层i和实施例2的纳米氟碳面漆层k的△e变化1.76和2.04,实施例1和实施例2的纳米氟碳面漆层比现有常用对比例1的对照防护涂层a和对照防护涂层b的色差变化都小,说明实施例1和实施例2的涂层的耐候性较好。从失光率曲线图3中可以看出,现有常用对比例1的对照防护涂层a和对照防护涂层b的失光都很严重,而实施例1和实施例2的纳米氟碳面漆层失光现象较轻,耐候性很好。实施例4本申请实施例提供了不同带锈液层配方的附着力测试,过程如下:按照表2的方案制备带锈液层的浆料,然后将带锈液层的浆料进行附着力测试,结果如表3所示。表2编号单宁酸(g/l)na2moo4(g/l)柠檬酸(g/l)异丙醇/叔丁醇(1:1)(g/l)温度(℃)实验1511520实验25221025实验35331530实验45442035实验510121535实验610212030实验71034525实验810431020实验915132025实验1015241520实验1115311035实验121542530实验1320141030实验142023535实验1520322020实验1620411525表3编号结合力(mpa)实验12.36±0.22实验22.89±0.49实验31.83±0.65实验44.22±0.22实验51.94±0.48实验62.70±0.47实验72.80±0.51实验82.11±0.20实验93.27±0.64实验102.76±0.34实验113.70±0.70实验121.95±0.50实验132.36±0.21实验142.39±0.56实验152.22±0.33实验163.42±0.44从表3可知,随着单宁酸浓度的增加,或者处理温度的升高,附着力都呈现先下降再上升继而再下降的变化,当单宁酸浓度为15g/l、处理温度为25℃时达到各自的附着力最大值。而处理温度在35℃时的附着力数值与25℃时很接近,但是从实际施工条件考虑,25℃更适合。附着力随着钼酸钠以及混合醇的浓度增加时基本呈现上升的趋势,在钼酸钠浓度为4g/l、混合醇浓度为20g/l时达到各自的附着力最大值。柠檬酸对附着力的影响规律为:随着柠檬酸浓度的升高附着力先下降后上升,在浓度为1g/l达到最大值。本申请实施例的带锈液层的浆料优选配方,包括单宁酸15g/l、钼酸钠4g/l、柠檬酸1g/l、混合醇20g/l(混合混包括异丙醇和叔丁醇,异丙醇和所述叔丁醇的质量比为1:1)、处理温度25℃。没有带锈液层的浆料处理带锈结构钢,纳米环氧锌黄底漆层与带锈结构钢的附着力为1.93mpa。上述配方的带锈液层的浆料处理带锈结构钢之后,纳米环氧锌黄底漆层与带锈结构钢的附着力为5.97mpa,可见单宁酸15g/l、钼酸钠4g/l、柠檬酸1g/l、混合醇20g/l(混合混包括异丙醇和叔丁醇,异丙醇和所述叔丁醇的质量比为1:1)、处理温度25℃的带锈液层的浆料可提高纳米环氧锌黄底漆层与带锈结构钢之间的附着力。实施例5本申请实施例提供了含有磷酸的带锈液层配方的附着力测试,过程如下:1、本申请实施例的带锈液层的浆料,包括单宁酸15g/l、钼酸钠4g/l、柠檬酸1g/l、混合醇20g/l(混合混包括异丙醇和叔丁醇,异丙醇和所述叔丁醇的质量比为1:1)、处理温度25℃,制得基础液,基础液的ph为2.58。2、将步骤1的基础液添加不同量磷酸,使得磷酸在基础液的浓度分别为:0g/l、10g/l、20g/l、30g/l、40g/l、50g/l、75g/l、100g/l、150g/l和200g/l,分别测定不同浓度磷酸的带锈液层的浆料处理带锈结构钢后,纳米环氧锌黄底漆层与带锈结构钢之间的附着力,结果如图4所示,图4为本申请实施例提供的不同磷酸浓度的带锈液层浆料对纳米环氧锌黄底漆层与带锈结构钢之间的附着力影响图。由图4可以看出,在磷酸浓度升高的初期,附着力随着磷酸浓度的升高而不断上升;在磷酸浓度为50g/l时附着力达到最大值11.63mpa,这个值远远高于不作带锈液层处理的1.93mpa以及步骤1基础液处理的5.97mpa;当磷酸浓度大于50g/l后,附着力开始急剧下降;到浓度升高到150g/l与200g/l甚至分别下降到了1.45mpa、0.99mpa,这比不作带锈液层处理的1.93mpa还要小很多。表明在单宁酸的带锈液层的浆料中加入适量磷酸可以显著提高附着力,高的磷酸浓度反而会降低附着力。3、将步骤1的基础液添加磷酸后,磷酸浓度为50g/l,制得优选带锈液层的浆料,由于磷酸的加入,优选带锈液层的浆料的ph降至0.38;将步骤1的基础液添加盐酸后,制得ph为0.38的对比浆料1;将步骤1的基础液添加磷酸后,磷酸浓度为50g/l,制得优选带锈液层的浆料,然后采用氢氧化钠将优选带锈液层的浆料的ph值调节至2.58,制得ph为2.58的对比浆料2。为了消除磷酸根的影响,选择了不加磷酸而用盐酸溶液将优选带锈液层的浆料ph调节到0.38实验条件;为了消除ph的影响,选择了加入50g/l磷酸到优选带锈液层的浆料中用氢氧化钠溶液将ph调节到2.58实验条件。将上述优选带锈液层的浆料、对比浆料1和对比浆料2处理带锈结构钢后,测定纳米环氧锌黄底漆层与带锈结构钢之间的附着力,结果如图5所示,图5为ph及磷酸根对纳米环氧锌黄底漆层与带锈结构钢的附着力影响(误差棒为标准差)。从图5可知,在优选带锈液层的浆料中加入50g/l磷酸提高附着力是在氢离子和磷酸根共同作用下,有效地控制了优选带锈液层的浆料与锈层的反应速率,形成了具有一些狭小通道转化膜结构,有利于优选带锈液层的浆料渗透到内锈层发生反应,最终增大了对锈层的转化程度,形成了整体较为致密的转化膜,这层致密转化膜保证了其内聚力。同时转化膜表面带有微裂纹和许多活性官能团,有利于与纳米环氧锌黄底漆层通过机械互锁以及化学键作用牢固结合起来。实施例6本申请实施例提供了纳米环氧锌黄底漆层浆料的附着力试验,具体步骤如下:纳米环氧锌黄底漆层的浆料包括:1.1、按照混合溶剂:分散剂:纳米铝粉为44:1:4的质量比,将分散剂、混合溶剂和纳米铝粉混合,制得纳米铝粉浆;按照混合溶剂:分散剂:纳米锆粉为44:1:4的质量比,将分散剂、混合溶剂和纳米锆粉混合,制得纳米锆粉浆;按照混合溶剂:分散剂:纳米二氧化硅为44:1:4的质量比,将分散剂、混合溶剂和纳米二氧化硅混合,制得纳米二氧化硅浆;1.2、将纳米铝粉浆、纳米锆粉浆、纳米二氧化硅浆、环氧树脂、磷酸锌、氧化铁黄和滑石粉混合,制得a组分;其中,环氧树脂在a组分的质量分数为50%、磷酸锌在a组分的质量分数为20%、氧化铁黄在a组分的质量分数为1%、滑石粉在a组分的质量分数为26%、纳米铝浆在a组分的质量分数为1%、纳米锆浆在a组分的质量分数为1%和纳米二氧化硅浆在a组分的质量分数为1%混合;将混合溶剂和聚酰胺混合,制得b组分;其中,混合溶剂在b组分的质量分数为40%,聚酰胺在b组分的质量分数为60%;混合溶剂包括二甲苯和正丁醇,二甲苯和正丁醇的体积比为7:3;1.3、按照a组分:b组分为5:1的质量比,将a组分和b组分混合,制得纳米环氧锌黄底漆层的浆料。2、制备对照组:制备步骤与本实施例的纳米环氧锌黄底漆层的浆料的制备方法类似,区别在于,本实施例的对照组不添加纳米铝粉、纳米锆粉和纳米二氧化硅。3、测定步骤1和步骤2的实验组和对照组的附着力(采用拉开法测定),结果如表4所示。表4组别两块板平均值(mpa)对照组5.3实验组11.84、测定本实施例的纳米环氧锌黄底漆层的浆料的物理化学性能,结果如表7所述。从表4可知,本申请实施例的纳米环氧锌黄底漆层的力学性能和对基体的附着力均很好。实施例7本申请实施例为纳米环氧云铁中间漆层的浆料的制备方法具体包括:纳米环氧云铁中间漆层的浆料包括:2.1、按照混合溶剂:分散剂:纳米铝粉为90:1:5的质量比,将分散剂、混合溶剂和纳米铝粉混合,制得纳米铝粉浆;按照混合溶剂:分散剂:纳米锆粉为90:1:5的质量比,分散剂、混合溶剂和纳米锆粉混合,制得纳米锆粉浆;按照混合溶剂:分散剂:纳米二氧化硅为90:1:5的质量比,分散剂、混合溶剂和纳米二氧化硅混合,制得纳米二氧化硅浆;2.2、将纳米铝粉浆、纳米锆粉浆、纳米二氧化硅浆、环氧树脂、云母氧化铁和滑石粉混合,制得c组分;其中,环氧树脂在c组分的质量分数为50%、滑石粉在c组分的质量分数为30%、云母氧化铁在c组分的质量分数为17%、纳米铝粉浆在c组分的质量分数为1%、纳米锆粉浆在c组分的质量分数为1%和纳米二氧化硅浆在c组分的质量分数为1%混合;将混合溶剂和聚酰胺混合,制得d组分;其中,混合溶剂在d组分的质量分数为60%,聚酰胺在d组分的质量分数为40%;混合溶剂包括二甲苯和正丁醇,二甲苯和正丁醇的体积比为7:3;2.3、按照c组分:d组分为5:1的质量比,制得纳米环氧云铁中间漆层的浆料。2、制备对照组:制备步骤与本实施例的纳米环氧云铁中间漆层的浆料的制备方法类似,区别在于,本实施例的对照组不添加纳米铝粉、纳米锆粉和纳米二氧化硅。3、测定步骤1和步骤2的实验组和对照组的附着力(采用拉开法测定),结果如表5所示。表5组别两块板平均值(mpa)对照组5.7实验组11.14、测定本实施例的纳米环氧云铁中间漆层的浆料的物理化学性能,结果如表7所述。从表5可知,本实施例的纳米环氧云铁中间漆层力学性能和对基体的附着力均很好。实施例8本申请实施例为纳米氟碳面漆层的浆料的制备方法具体包括:纳米氟碳面漆层的浆料包括:3.1、按照聚酰胺蜡:混合溶剂:纳米铝粉为1:70:2的质量比,将聚酰胺蜡、混合溶剂和纳米铝粉混合,制得纳米铝粉浆;按照聚酰胺蜡:混合溶剂:纳米锆粉为1:70:2的质量比,将聚酰胺蜡、混合溶剂和纳米锆粉混合,制得纳米锆粉浆;按照聚酰胺蜡:混合溶剂:纳米二氧化硅为1:70:2的质量比,将聚酰胺蜡、混合溶剂和纳米二氧化硅混合,制得纳米二氧化硅浆;3.2、将纳米填料浆、氟碳树脂和消泡剂混合,制得e组分;氟碳树脂在e组分的质量分数为80%、消泡剂在e组分的质量分数为0.5%、聚酰胺蜡在e组分的质量分数为0.5%、纳米铝粉浆在e组分的质量分数为17%、纳米锆粉浆1%和纳米二氧化硅浆在e组分的质量分数为1%;将醋酸丁酯和n3390的固化剂混合,制得f组分;其中,醋酸丁酯在f组分的质量分数为10%,n3390的固化剂在f组分的质量分数为90%;3.3、按照e组分:f组分为10:1的质量比,将e组分和f组分混合,制得纳米氟碳面漆层的浆料。2、制备对照组:制备步骤与本实施例的纳米氟碳面漆层的浆料的制备方法类似,区别在于,本实施例的对照组不添加纳米铝粉、纳米锆粉和纳米二氧化硅。3、测定步骤1和步骤2的实验组和对照组的性能测试,结果如表6所示。表6组别厚度(μm)铅笔硬度柔韧性(mm)附着力(级)冲击强度(kg·cm)对照组24±2h1150实验组23±2h10504、测定本实施例的纳米氟碳面漆层的浆料的物理化学性能,结果如表7所述。从表6可知,本实施例的纳米氟碳面漆层的附着力为最高级0级,而现有常规的面漆附着力为1级。表7检测项目实施例6的实验组实施例7的实验组实施例8的实验组粘度(涂4杯25℃)446918干燥时间(h)表干0.312.5干燥时间(h)实干4.55.58.5厚度(μm)28±234±224±2光泽(60°)1.5±14.7±3155±5铅笔硬度h2hhb附着力(级)111柔韧性(mm)211冲击强度(kg·cm)505050实施例9本申请实施例为采用不同方法添加纳米二氧化硅在纳米环氧锌黄底漆层浆料中的分散试验,具体包括:1、纳米环氧锌黄底漆层的浆料试验组。制备包括:1.1、按照混合溶剂:分散剂:纳米二氧化硅为44:1:4的质量比,将分散剂、混合溶剂和纳米二氧化硅混合,制得纳米二氧化硅浆;1.2、将纳米二氧化硅浆、环氧树脂、磷酸锌、氧化铁黄和滑石粉混合,制得a组分;其中,环氧树脂在a组分的质量分数为50%、磷酸锌在a组分的质量分数为20%、氧化铁黄在a组分的质量分数为1%、滑石粉在a组分的质量分数为26%、纳米二氧化硅浆在a组分的质量分数为1%混合;将混合溶剂和聚酰胺混合,制得b组分;其中,混合溶剂在b组分的质量分数为40%,聚酰胺在b组分的质量分数为60%;混合溶剂包括二甲苯和正丁醇,二甲苯和正丁醇的体积比为7:3;1.3、按照a组分:b组分为5:1的质量比,将a组分和b组分混合,制得纳米环氧锌黄底漆层的浆料。2、制备对照组:制备步骤与本实施例的纳米环氧锌黄底漆层的浆料的制备方法类似,区别在于,本实施例的对照组的纳米二氧化硅不制成纳米二氧化硅浆,而是将纳米二氧化硅与其余组分直接混合,制得对照组浆料。3、对步骤1的试验组浆料和步骤2的对照组浆料进行扫描电镜分析,结果如图5所示。图5为本申请实施例提供的直接添加纳米二氧化硅制得的纳米环氧锌黄底漆层浆料,和将纳米二氧化硅制成纳米二氧化硅浆后制得的纳米环氧锌黄底漆层浆料的tem图,其中,(a)为直接添加纳米二氧化硅制得的对照组浆料,(b)为将纳米二氧化硅制成纳米二氧化硅浆后制得的试验组浆料。从图5可知,纳米二氧化硅制成纳米二氧化硅浆后制成的纳米环氧锌黄底漆层浆料中的纳米粒子具有均匀的分散,团聚体非常少;而直接加入纳米二氧化硅粉制成的对照组浆料中的纳米粒子分散不均匀,团聚体非常多;这是由于纳米二氧化硅制成纳米二氧化硅浆后,纳米二氧化硅原有的团聚体被打碎,由超分散剂的溶液润湿后形成吸附层,形成稳定分散的纳米二氧化硅浆,纳米二氧化硅浆与纳米环氧锌黄底漆层浆料其他原料混合后,由于超分散剂的锚固作用,使纳米二氧化硅粒子表面的吸附层不会受到纳米环氧锌黄底漆层浆料其他原料的破坏,进而使纳米二氧化硅粒子能在纳米环氧锌黄底漆层浆料中分散稳定,成膜后仍能保持良好的分散状态。以上所述仅是本申请的优选实施方式,应当指出,对于本
技术领域:
的普通技术人员来说,在不脱离本申请原理的前提下,还可以做出若干改进和润饰,这些改进和润饰也应视为本申请的保护范围。当前第1页1 2 3 
起点商标作为专业知识产权交易平台,可以帮助大家解决很多问题,如果大家想要了解更多知产交易信息请点击 【在线咨询】或添加微信 【19522093243】与客服一对一沟通,为大家解决相关问题。
此文章来源于网络,如有侵权,请联系删除



tips