保护膜、显示模组、显示组件及显示装置的制作方法



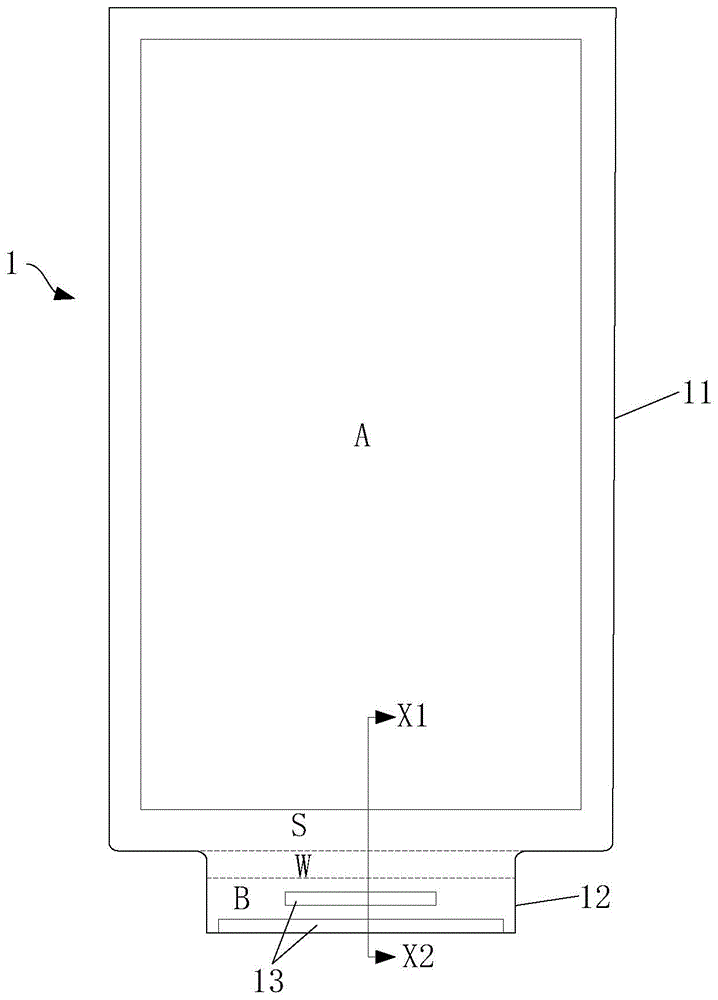
本申请涉及显示技术领域,特别涉及一种保护膜、显示模组、显示组件及显示装置。
背景技术:
有机发光二极管显示装置(organiclightemittingdisplay,oled)作为新型显示器件,在显示技术领域不断发展与应用,基于oled柔性的特点,柔性全面屏显示成为发展新趋势,引起人们极大关注。
目前柔性有机发光二极管显示基板(flexoled)的弯折处(padbending)的信号线是单层,为了提高该处抗弯折性能,采用喷涂mcl(metalcoatinglayer)对弯折处进行保护是目前oled屏幕厂商的主流方案。然而,喷涂mcl层会导致弯折侧的显示边框宽度较大,难以压缩,不利于窄边框的实现。
技术实现要素:
本申请公开了一种保护膜、显示模组、显示组件及显示装置,目的是提供一种针对柔性显示基板弯折区的保护方案,以减小显示基板弯折一侧边框的宽度,实现窄边框。
为达到上述目的,本申请提供以下技术方案:
一种保护膜,被配置为在母版切割之前贴附在柔性显示基板上,所述柔性显示基板包括显示区和位于显示区一侧的弯折区;所述保护膜包括:
基材层,被配置为覆盖在所述柔性显示基板的显示侧,且所述基材层在所述柔性显示基板上的投影与所述显示区和所述弯折区均有交叠;
第一胶层,位于所述基材层朝向所述柔性显示基板的一侧,被配置为覆盖所述柔性显示基板的显示区;所述第一胶层的粘性为0.5gf/inch-1.5gf/inch;
第二胶层,位于所述基材层朝向所述柔性显示基板的一侧,相对于所述第一胶层独立设置,被配置为覆盖所述柔性显示基板的弯折区;所述第二胶层为紫外光固化胶;所述第二胶层的粘性为3gf/inch-4gf/inch。
可选的,所述第一胶层靠近所述第二胶层的一侧边沿与所述第二胶层靠近所述第一胶层的一侧边沿之间的间距小于0.25mm。
可选的,所述第一胶层靠近所述第二胶层的一侧边沿与所述第二胶层靠近所述第一胶层的一侧边沿相接触。
可选的,所述第二胶层的厚度为60μm~120μm。
可选的,所述第一胶层为pu胶,所述第二胶层为亚克力胶。
一种显示模组,包括柔性显示基板和如上述任一项所述的保护膜;
所述保护膜贴附在所述柔性显示基板的显示侧;其中,所述第一胶层覆盖所述柔性显示基板的显示区,所述第二胶层覆盖所述柔性显示基板的弯折区。
可选的,所述第二胶层靠近所述显示区的一侧边沿与所述显示区靠近所述第二胶层的一侧边沿之间的距离为0.9mm-1.2mm。
可选的,所述柔性显示基板具有屏幕部和位于屏幕部一侧的绑定部,所述绑定部的宽度小于所述屏幕部;所述屏幕部包括所述显示区,所述绑定部包括所述弯折区;
所述第二胶层靠近所述显示区的一侧边沿与所述屏幕部和所述绑定部之间的分界线对齐。
可选的,所述显示区的面积占所述屏幕部的面积的比例为92.38%-92.48%。
一种显示组件,包括:
柔性显示基板,所述柔性显示基板包括显示区和位于显示区一侧的弯折区;
第二胶层,贴附于所述柔性显示基板的显示侧,覆盖所述弯折区,所述第二胶层为将如上述任一项所述的保护膜去除基材层和第一胶层之后所得到的胶层。
可选的,所述第二胶层靠近所述显示区的一侧边沿与所述显示区靠近所述第二胶层的一侧边沿之间的距离为0.9mm-1.2mm。
可选的,所述柔性显示基板具有屏幕部和位于屏幕部一侧的绑定部,所述绑定部的宽度小于所述屏幕部;所述屏幕部包括所述显示区,所述绑定部包括所述弯折区;
所述第二胶层靠近所述显示区的一侧边沿与所述屏幕部和所述绑定部之间的分界线对齐。
可选的,所述显示区的面积占所述屏幕部的面积的比例为92.38%-92.48%。
一种显示装置,包括如上述任一项所述的显示组件。
附图说明
图1为本申请一实施例提供的一种柔性显示基板的结构示意图;
图2为本申请一实施例提供的一种显示模组沿图1中的x1-x2方向的截面结构示意图;
图3为本申请另一实施例提供的一种显示模组沿图1中的x1-x2方向的截面结构示意图;
图4为本申请一实施例提供的一种保护膜的截面结构示意图;
图5为本申请另一实施例提供的一种保护膜的截面结构示意图;
图6为本申请一实施例提供的一种显示组件沿图1中的x1-x2方向的截面结构示意图;
图7为相关技术中的一种显示模组沿图1中的x1-x2方向的截面结构示意图;
图8为本申请一实施例提供的一种显示组件的制备方法流程图;
图9为本申请一实施例提供的一种母版在贴附保护膜后的结构示意图。
具体实施方式
目前市场上,各大终端旗舰机都是超窄边框设计,全面屏的趋势已经深入人心,成为消费者宠儿。而目前柔性有机发光二极管显示器件绑定部弯折(flexoledpadbending)方案已成为超窄边框首选,但由于绑定部弯折区(padbending)布线密集且反折应力大,造成padbending区裂纹(crack)高发,严重制约着产品应用。针对上述问题,目前的应对方案是在弯折区喷涂保护层(mcl,metalcoatinglayer)。
发明人研究发现,尽管喷涂保护层(mcl)可以实现对padbending区的保护,但由于设备喷涂的精度及工艺的限制,mcl胶材的起始位置到均匀位置的过度范围比较大,喷涂的mcl层往往厚度均一性差,边缘锯齿严重,这些致使mcl胶材的喷涂范围较大,导致显示面板弯折区一侧的边框(paneldownborder)难以缩小。并且,目前flexoled的工艺流程为:在柔性基板的出光侧贴附上保护膜(tpf)→mcl喷涂→绑定工艺(fopbonding)→撕除上保护膜(tpf)→偏光片(pol)贴附,如图7所示,在pol贴附前需要剥离显示基板的上保护膜(tpf)2,为了避免喷涂的mcl胶材3与tpf2干涉(若mcl胶材3喷涂到tpf2上与tpf2干涉,撕除tpf2时将导致mcl胶材3剥离),mcl胶材3的喷涂边缘与tpf2边缘之间的距离d1一般需要≥0.3mm,因此mcl胶材3喷涂边缘与显示区a边缘的距离需要设置的比较大,这也使得弯折一侧的边框宽度(border)难以进一步压缩。鉴于上述问题,有效提升和改善对柔性显示基板的弯折区保护方式是非常有必要的。
具体的,本申请实施例提供一种保护膜、显示模组、显示组件及其制备方法、显示装置,目的是提供一种针对柔性显示基板弯折区的保护方案,以减小显示基板弯折区一侧边框的宽度,实现窄边框。
下面将结合本申请实施例中的附图,对本申请实施例中的技术方案进行清楚、完整地描述,显然,所描述的实施例仅仅是本申请一部分实施例,而不是全部的实施例。基于本申请中的实施例,本领域普通技术人员在没有做出创造性劳动前提下所获得的所有其他实施例,都属于本申请保护的范围。
如图1所示,常规的柔性显示基板1,具有屏幕部11和位于屏幕部11一侧的绑定部(舌部)12,绑定部12的宽度小于屏幕部11。以手机中的柔性显示基板为例,其绑定部12具体位于屏幕部11的下侧。
屏幕部11具有显示区a和围绕该显示区a设置的周边区s。周边区s用于布线,例如栅极驱动电路。
绑定部12具有电连接区b和弯折区w,弯折区w位于电连接区b靠近显示区a的一侧,电连接区b设有连接结构13,用于与驱动ic(integratedcircuitchip)和/或柔性电路板(fpc,flexibleprintedcircuit)电连接;而弯折区w用于将电连接区b和与电连接区b电连接的驱动ic和/或fpc翻转至柔性显示基板1的背侧(背离显示侧的一侧)。
具体的,本申请实施例提供了一种保护膜,该保护膜被配置为在母版切割之前贴附在柔性显示基板的显示侧。如图1至图3所示,所述柔性显示基板1包括显示区a和位于显示区a一侧的弯折区w;如图4和图5所示,所述保护膜2包括基材层20,第一胶层21和第二胶层22。如图1至图3所示,所述保护膜2中:
基材层20被配置为覆盖在所述柔性显示基板1的显示侧,且所述基材层20在所述柔性显示基板1上的投影与所述显示区a和所述弯折区w均有交叠。
第一胶层21位于所述基材层20朝向所述柔性显示基板1的一侧,被配置为覆盖所述柔性显示基板1的显示区a;所述第一胶层21的粘性为0.5gf/inch-1.5gf/inch。
第二胶层22位于所述基材层20朝向所述柔性显示基板1的一侧,相对于所述第一胶层21独立设置,被配置为覆盖所述柔性显示基板1的弯折区w;所述第二胶层22为紫外光固化胶;所述第二胶层22的粘性为3gf/inch-4gf/inch。
上述保护膜2,用于在母版切割之前贴附在柔性显示基板1的显示侧,以对柔性显示基板1进行保护,且该保护膜2可以在进行偏光片贴合工艺之前剥离,以使得柔性显示基板1可以继续进行后续的贴合工艺。
具体的,该保护膜2的基材层20不仅覆盖柔性显示基板1的显示区a,而且覆盖柔性显示基板1的弯折区w;并且,该保护膜2包括两部分胶层,即第一胶层21和第二胶层22;其中,第一胶层21覆盖显示区a,其粘性较小,大概为0.5gf/inch-1.5gf/inch,第一胶层21主要用于将基材层20与柔性显示基板1的主体贴附在一起,在撕除保护膜2时该第一胶层21将随基材层20剥离;第二胶层22覆盖弯折区w,其粘性较大,大概为3gf/inch-4gf/inch,第二胶层22具体采用紫外光固化胶,经紫外固化后可以与柔性显示基板1黏附固定在一起,在撕除保护膜2时不会随基材层20剥离(如图6所示为撕除保护膜后第二胶层22粘附在柔性显示基板1上的状态),进而第二胶层22最终将贴附在柔性显示基板1上以形成mcl(metalcoatinglayer),对柔性显示基板1的弯折区w起到保护作用。
综上所述,采用上述保护膜2,能够实现在柔性显示基板1的弯折区w贴附形成mcl胶层(第二胶层22)。相对于通过喷涂工艺形成的mcl(如图7所示为喷涂mcl胶材3),贴附的mcl胶层的均匀性及精度更容易管控,采用较小的贴附面积即可以保证对弯折区w的有效覆盖和保护,进而可以减小弯折区w边沿至显示区a边沿的距离,如图2和图3所示;并且,由于本申请中的mcl胶层(第二胶层22)随保护膜(tpf)2一起贴附,相对于喷涂mcl工艺,该贴附方式不用考虑mcl胶材(第二胶层22)与保护膜2的避让,因此,mcl胶层(第二胶层22)的边沿与显示区a边沿的距离可以缩小,如图2和图3所示,从而可以实现对显示区a至弯折区w之间距离的进一步压缩,以减小边框(border),实现显示基板在弯折区w一侧的窄边框或者超窄边框。
另外,常规喷涂mcl工艺中,mcl使用针管喷涂,至少需要四次以上的连续喷涂,耗能高,且喷涂时对padbending有二次损伤;而且mcl胶需要两次uv固化,首道喷涂需要先固化,直到整个涂覆完成后在统一固化,uv固化时间较长。然而,本申请中,通过保护膜将mcl胶层贴附在柔性基板上的方案,不仅可以在工艺上省去一次uv固化,节约成本,而且还可以提高产品的信赖性;例如,mcl胶采用贴附工艺,可以避免喷涂损伤,其在母版切割形成柔性显示基板之前完成贴附,可以依靠刚性基板(glass基材)提供支撑,从而大大降低padbendingcrack风险;而且,因为保护膜(tpf)的基材层延伸覆盖到padbending区,进而还可以大大提高柔性显示基板在后续运输过程中的信赖性,进一步降低crack的风险。
具体的,柔性显示基板的弯折区一般包括柔性衬底以及位于柔性衬底上的多层材料层,例如无机材料层和金属走线层等。具体的,本申请中,在弯折区上贴附mcl(metalcoverlayer,金属覆盖层)胶层,可以对弯折区部分的无机材料层和金属走线层的位置进行调节,以使无机材料层和金属走线层位于弯折区的中性层的位置,从而降低在弯折过程中,该弯折区部分的无机材料层和金属走线层发生断裂的可能性。
一些实施例中,如图4所示,所述保护膜2中,第一胶层21靠近所述第二胶层22的一侧边沿与所述第二胶层22靠近所述第一胶层21的一侧边沿之间的间距d小于0.25mm。
示例性的,如图5所示,所述保护膜2中,所述第一胶层21靠近所述第二胶层22的一侧边沿与所述第二胶层22靠近所述第一胶层21的一侧边沿相接触。
具体的,第一胶层21完全覆盖显示区a,其靠近弯折区w一侧的边沿可以位于周边区s上(如图2中所示),也可以与周边区s的边沿(屏幕部11和绑定部12之间的边界)对齐(如图3中所示)。第二胶层22完全覆盖弯折区w,其靠近显示区a一侧的边沿可以位于周边区s上(如图2中所示),也可以与周边区s的边沿(屏幕部11和绑定部12之间的边界)对齐(如图3中所示)。
例如,如图3所示,所述第一胶层21靠近所述第二胶层22的一侧边沿与所述第二胶层22靠近所述第一胶层21的一侧边沿相接触,且均与周边区s的边沿(屏幕部11和绑定部12之间的边界)对齐。
常规的喷涂mcl工艺中,如图7所示,喷涂的mcl胶材3的边沿与保护膜2的边沿之间的间距d1一般要大于0.3mm,如0.3mm-0.4mm,因此,显示区a和弯折区w之间的间距需要设置的比较大,即位于显示区a和弯折区w之间的周边区s的宽度较大。本申请中,如图2和图3所示,mcl胶层(第二胶层22)设置在保护膜2的基材层20上,与保护膜2同时贴附,第二胶层22的边沿与第一胶层21的边沿之间的间距很小,如小于0.25mm甚至可以为0(第二胶层22的边沿与第一胶层21边沿接触),进而,第一胶层21所覆盖的显示区a与第二胶层22所覆盖的弯折区w之间的间距可以设置的很小,即位于显示区a和弯折区w之间的周边区s的宽度较小,从而可以实现窄边框或超窄边框。
一些实施例中,所述第二胶层22的厚度为60μm~120μm。
具体的,本申请中,保护膜上的第二胶层可以通过印刷工艺形成在基材层上,并可以通过构图限定其形状范围,因此,相对于直接在柔性显示基板1在通过喷涂形成的mcl胶层,其可以实现厚度的均一性及减薄,从而有利于弯折区窄边框的实现,以进一步提升产品的窄边框效果。并且,上述第二胶层的厚度设置,可以使无机材料层和金属走线层位于弯折区的中性层的位置,从而有效降低弯折过程中无机材料层和金属走线层发生断裂的可能性。
一些实施例中,所述第一胶层21为非紫外光固化胶(uv固化胶)。第二胶层22为紫外光固化胶。在对第二胶层22进行uv光固化时,uv光对第一胶层21无影响。
示例性的,所述第一胶层21为pu胶,所述第二胶层22为亚克力胶。具体的,第二胶层22进行uv固化后,弯折性能好,并与柔性显示基板1的粘附力可以达到13.3n/mm2。
一些实施例中,如图4和图5所示,本申请实施例的保护膜2还可以包括设置在第一胶层21和第二胶层22背离基材层20一侧的离型膜24。在贴附保护膜2之前,将该离型膜24撕除。
具体的,本申请实施例还提供一种显示模组,如图2和图3所示,该显示模组包括柔性显示基板1和上述任一项所述的保护膜2。
具体的,所述保护膜2贴附在所述柔性显示基板1的显示侧;其中,所述第一胶层21覆盖所述柔性显示基板1的显示区a,所述第二胶层22覆盖所述柔性显示基板1的弯折区w。
一些实施例中,如图3所示,所述柔性显示基板1具有屏幕部11和位于屏幕部11一侧的绑定部12,所述绑定部12的宽度小于所述屏幕部11;所述屏幕部11包括所述显示区a,所述绑定部12包括所述弯折区w。
示例性的,所述第二胶层22靠近所述显示区a的一侧边沿与所述屏幕部11和所述绑定部12之间的分界线对齐。
示例性的,所述第二胶层22靠近所述显示区a的一侧边沿与所述显示区a靠近所述第二胶层22的一侧边沿之间的距离为0.9mm-1.2mm。
例如,如图3所示,第二胶层22靠近所述显示区a的一侧边沿与屏幕部11和所述绑定部12之间的分界线对齐,第二胶层22靠近所述显示区a的一侧边沿与所述显示区a靠近所述第二胶层22的一侧边沿之间的距离即是位于屏幕部11和绑定部12之间的周边区s的宽度,该宽度为0.9mm-1.2mm,相对于常规喷涂mcl方案中的柔性显示基板1的周边区s宽度(如图7所示)可以缩小0.25mm-0.4mm,实现了对窄边框的进一步压缩,有利于提高屏占比,提升全屏显示效果。
示例性的,本申请实施例的柔性显示基板1中,所述显示区a的面积占所述屏幕部11的面积的比例为92.38%-92.48%。具体的,该柔性显示基板1应用于手机产品,可以使得手机产品的屏占比大概提高0.12%-0.28%。例如,针对6.18寸的手机产品,常规的屏占比一般为92.18%左右,而应用本申请柔性显示基板1的手机产品的屏占比可以达到92.43%左右。
当然,本申请中第一胶层21和第二胶层22的边缘位置并不限于上述实施例;例如,如图2所示,第二胶层22的边沿与第一胶层21的边沿也可以不与屏幕部和绑定部12之间的分界线对齐,而是位于周边区s上;并且,第二胶层22的边沿与第一胶层21的边沿之间也可以具有一定间距,该间距小于0.25mm。
具体的,如图2和图3所示,本申请实施例提供的显示模组,还可以包括与电连接区b连接的ic芯片4,fpc(图中未示出),以及位于柔性显示基板1背侧的膜层5等,背侧膜层5与弯折区w无交叠,以提高弯折可靠性。
本申请实施例还提供一种显示组件,如图6所示,该显示组件包括:
柔性显示基板1,所述柔性显示基板1包括显示区a和位于显示区a一侧的弯折区w;
第二胶层22,贴附于所述柔性显示基板1的显示侧,覆盖所述弯折区w,所述第二胶层22为将上述任一项所述的保护膜2去除基材层20和第一胶层21之后所得到的胶层。
具体的,本申请实施例提供的显示模组(如图2和图3所示)为在柔性显示基板1的显示侧贴附保护膜2之后,且在剥离保护膜2之前(在进行偏光片贴合工艺之前)的一种模组形态。而本申请实施例提供的显示组件(如图6所示)可以是将显示模组的保护膜剥离之后所得到的组件产品。
具体的,本申请实施例提供的显示组件可以是进行偏光片和/或玻璃盖板贴合工艺之后的组件产品,即该显示组件还可以包括偏光片和玻璃盖板等层结构。
如图6所示,一些实施例中,所述柔性显示基板1具有屏幕部11和位于屏幕部11一侧的绑定部12,所述绑定部12的宽度小于所述屏幕部11;所述屏幕部11包括所述显示区a,所述绑定部12包括所述弯折区w。
示例性的,本申请实施例提供的显示组件中,所述第二胶层22靠近所述显示区a的一侧边沿与所述屏幕部11和所述绑定部12之间的分界线对齐。
示例性的,所述第二胶层22靠近所述显示区a的一侧边沿与所述显示区a靠近所述第二胶层22的一侧边沿之间的距离为0.9mm-1.2mm。
例如,如图6所示,第二胶层22靠近所述显示区a的一侧边沿与屏幕部11和所述绑定部12之间的分界线对齐,第二胶层22靠近所述显示区a的一侧边沿与所述显示区a靠近所述第二胶层22的一侧边沿之间的距离即是位于屏幕部11和绑定部12之间的周边区s的宽度,该宽度为0.9mm-1.2mm,相对于常规喷涂mcl方案中的柔性显示基板1的周边区s宽度(如图7所示)可以缩小0.25mm-0.4mm,实现了对窄边框的进一步压缩,有利于提高屏占比,提升全屏显示效果。
示例性的,本申请实施例的柔性显示基板1中,所述显示区a的面积占所述屏幕部11的面积的比例为92.38%-92.48%。具体的,该柔性显示基板1应用于手机产品,可以使得手机产品的屏占比大概提高0.12%-0.28%。例如,针对6.18寸的手机产品,常规的屏占比一般为92.18%左右,而应用本申请柔性显示基板1的手机产品的屏占比可以达到92.43%左右。
具体的,上述图6所示的显示组件为图3所示的显示模组在撕除保护膜2后所得到的组件形态。具体的,本申请中第一胶层21和第二胶层22的边缘位置并不限于上述图6中所示。例如,本申请的显示组件也可以是图2所示的显示模组在撕除保护膜2后所得到的组件形态,此时,第二胶层22的边沿与第一胶层21的边沿不与屏幕部和绑定部12之间的分界线对齐,而是位于周边区s上;并且,第二胶层22的边沿与第一胶层21的边沿之间具有一定间距,该间距小于0.25mm。
具体的,本申请实施例还提供一种显示装置,该显示装置包括如上述任一项所述的显示组件。
具体的,本申请实施例提供的显示组件中,柔性显示基板可以为oled基板。本申请实施例提供的显示装置可以为手机、平板电脑、笔记本、个人数字助理(personaldigitalassistant,pda)、车载电脑等。本发明实施例对上述显示装置的具体形式不做特殊限制。
具体的,本申请实施例还提供一种显示组件的制备方法,如图8所示,该方法包括以下步骤:
步骤101,制备如上述任一项所述的保护膜(如图4和图5中所示的保护膜2);
步骤102,在柔性显示基板上贴附所述保护膜,对所述保护膜的第二胶层进行紫外光固化(如图2和图3所示);
步骤103,对所述柔性显示基板进行绑定工艺;
步骤104,将所述保护膜的基材层和第一胶层从所述柔性显示基板上撕除(如图6所示为撕除保护膜后的形态)。
一些实施例中,步骤102,在柔性显示基板上贴附所述保护膜,具体包括:
如图9所示,在母版10上贴附所述保护膜(包括基材层20,第一胶层21和第二胶层22)。具体的,所述母版10包括多个所述柔性显示基板1;所述保护膜可以是覆盖整张母版10的保护膜,保护膜的基材层20上具有多对第一胶层21和第二胶层22的图案,每对第一胶层21和第二胶层22对应覆盖一个柔性显示基板1。
在步骤102之后,还可以包括以下步骤:
对所述母版10进行单元切割,以获得所述柔性显示基板1。具体的,切割母版10时同时将保护膜的基材层20切割开,以使得切割后的每块保护膜与柔性显示基板1一一对应。
一些实施例中,步骤101,制备如上述任一项所述的保护膜;具体可以包括:
提供与母版10尺寸大致相同的保护膜基材层20;
在基材层20上依次制备第一胶层21和第二胶层22。
示例性的,第一胶层21为非紫外光固化胶,第二胶层22为紫外光固化胶。在对第二胶层22(mcl胶)进行uv光固化时,uv光对第一胶层21无影响。例如,所述第一胶层21为pu胶,所述第二胶层22为亚克力胶。
示例性的,第二胶层22的厚度为60μm~120μm。第二胶层22(mcl胶层)可以通过印刷工艺形成在保护膜的基材层20上,并可以通过构图限定其形状范围;相对于直接在显示基板上通过喷涂形成的mcl胶材,第二胶层22可以实现厚度的均一性及减薄。
具体的,常规喷涂mcl工艺中,mcl使用针管喷涂,至少需要四次以上的连续喷涂,耗能高,且喷涂时对padbending有二次损伤;而且mcl胶需要两次uv固化,首道喷涂需要先固化,直到整个涂覆完成后在统一固化,uv固化时间较长。然而,本申请中,将mcl胶层制备在上保护膜(tpf)上,并通过tpf将mcl胶层贴附在柔性基板上,该方案一方面可以在工艺上省去一次uv固化,节约成本,另一方面还可以提高产品的信赖性,例如,集成mcl胶采用贴附工艺,可以避免喷涂损伤,其在母版切割形成柔性显示基板之前完成贴附,可以依靠刚性基板(glass基材)提供支撑,从而大大降低padbendingcrack风险;而且,因为保护膜(tpf)的基材层延伸覆盖到padbending区,进而还可以大大提高柔性显示基板在后续运输过程中的信赖性,进一步降低crack的风险。
需要说明的是,本公开的一些实施例中,保护膜,显示组件和显示装置还可以包括其他的结构,这可以根据实际需求而定,本公开的实施例对此不作限制。关于本公开实施例提供的各部分结构的尺寸和材料选择并不限于上述实施例,可以根据实际需要进行改动,此处不再赘述。再者,本申请附图只是示意图,图中各部分结构的尺寸和比例并不代表各结构的实际尺寸比例。
显然,本领域的技术人员可以对本申请实施例进行各种改动和变型而不脱离本申请的精神和范围。这样,倘若本申请的这些修改和变型属于本申请权利要求及其等同技术的范围之内,则本申请也意图包含这些改动和变型在内。
起点商标作为专业知识产权交易平台,可以帮助大家解决很多问题,如果大家想要了解更多知产交易信息请点击 【在线咨询】或添加微信 【19522093243】与客服一对一沟通,为大家解决相关问题。
此文章来源于网络,如有侵权,请联系删除


