一种硅胶薄膜及其制备方法与流程



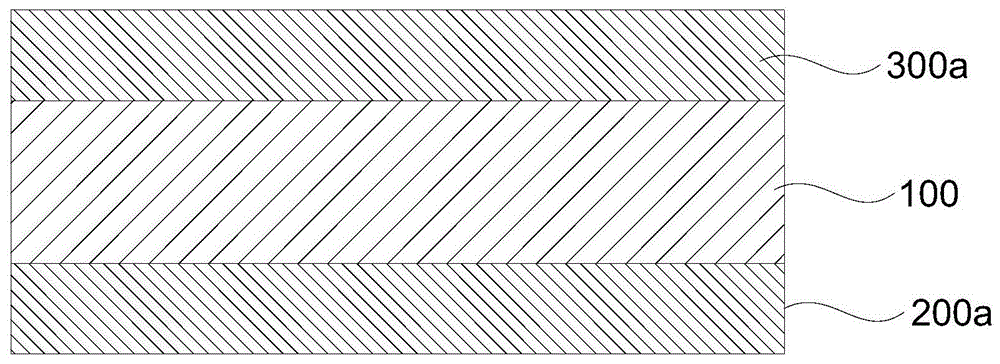
本发明属于薄膜
技术领域:
,尤其涉及一种硅胶薄膜及其制备方法。
背景技术:
:申请号为cn201820194863.0公开了一种tpu保护膜,其包括哑膜层、第一oca胶层、第一底涂层、tpu膜层、第二底涂层、第二oca胶层、透明pet层、高粘硅胶使用层和氟素膜保护层,所述哑膜层、第一oca胶层、第一底涂层、tpu膜层、第二底涂层、第二oca胶层、透明pet层、高粘硅胶使用层和氟素膜保护层按照从上至下的顺序依次贴合。该tpu保护膜的主要材质是tpu,tpu的耐温性能一般,只能耐130℃,限制了其应用。技术实现要素:本发明的目的在于提供一种硅胶薄膜及其制备方法,旨在解决现有技术中的tpu保护膜的主要材质是tpu,tpu的耐温性能一般的技术问题。为实现上述目的,本发明实施例提供的一种硅胶薄膜,包括一硅胶基层,所述硅胶基层包括按质量百分比计的以下原料:50~55%的聚硅氧烷;40~45%的vmq硅树脂;0.8~1%的铂金催化剂;4~6%的甲基氢聚硅氧烷;以及0.1~0.15%的炔醇。可选地,该硅胶薄膜还包括一功能涂层以及一胶粘层,所述功能涂层和所述胶粘层分别设于所述硅胶基层的正面和反面上;所述功能性涂层为自修复涂层、抗污涂层、抗指纹涂层、耐磨层、耐水解层、抗紫外线层或耐候层中的任意一种。可选地,所述自修复涂层包括按质量百分比计的以下原料:50~60%的丙烯酸酯以及40~50%的乙酸丁酯。可选地,所述胶粘层为第一压敏胶层,所述第一压敏胶层包括按质量百分比计的以下原料:30~40%的mq硅树脂;30~40%的甲苯;20~30%的聚硅氧烷;0.8~1%的铂金催化剂;以及1~2%的甲基氢聚硅氧烷。可选地,该硅胶薄膜还包括一第二压敏胶层和一第三压敏胶层,所述第二压敏胶层和所述第三压敏胶层分别设于所述硅胶基层的正面和反面。可选地,所述第二压敏胶层包括按质量百分比计的以下原料:97~98%的聚硅氧烷;0.8~1%的铂金催化剂;1~2%的甲基氢聚硅氧烷;以及0.1~0.15%的炔醇。可选地,所述第三压敏胶层包括按质量百分比计的以下原料:30~40%的mq硅树脂;30~40%的甲苯;20~30%的聚硅氧烷;0.8~1%的铂金催化剂;以及1~2%的甲基氢聚硅氧烷。为实现上述目的,本发明实施例上述的硅胶薄膜的制备方法,包括以下步骤:1)原料混合:按硅胶基层的原料配比称取聚硅氧烷、vmq硅树脂、铂金催化剂、甲基氢聚硅氧烷以及炔醇,混合均匀;2)加热固化:在氟素离型膜上涂布上述原料,经过具有七节烘干区的烘箱进行加热固化,每节烘干区的长度为3.5~4.5米,七节烘干区的温度依次为85~95℃,115~125℃,135~145℃,145~155℃,145~155℃,115~125℃以及95~105℃;机速5~8m/min;固化后形成所述硅胶基层,并在所述硅胶基层的表面上覆上第一pet膜。可选地,该硅胶薄膜的制备方法还包括以下步骤:3)制备第一压敏胶层:撕开所述硅胶基层表面上的所述第一pet膜,按第一压敏胶层的原料配比称取mq硅树脂、甲苯、聚硅氧烷、铂金催化剂以及甲基氢聚硅氧烷;将上述原料与乙酯以1:1.1~1.2的质量比混合稀释后制得第一稀释液,将所述第一稀释液涂布在所述硅胶基层表面上,然后经过具有七节烘干区的烘箱进行加热固化,每节烘干区的长度为3.5~4.5米,七节烘干区的温度依次为75~85℃,95~105℃,135~145℃,155~165℃,135~145℃,135~145℃以及115~125℃;机速15~25m/min;固化后形成所述第一压敏胶层,在所述胶粘层上覆上第二pet膜;4)制备自修复涂层:撕开所述硅胶基层表面上的氟素离型膜,按自修复涂层的原料配比称取丙烯酸酯和乙酸丁酯,将上述原料混合后涂布在所述硅胶基层上,然后经过具有七节烘干区的烘箱进行加热固化,每节烘干区的长度为3.5~4.5米,七节烘干区的温度依次为55~65℃,75~85℃,95~105℃,115~125℃,95~105℃以及75~85℃;机速15~20m/min;固化后形成所述自修复涂层,在所述胶粘层上覆上第三pet膜,制得所述硅胶薄膜。可选地,该硅胶薄膜的制备方法还包括以下步骤:5)制备第二压敏胶层:撕开所述硅胶基层表面上的所述第一pet膜,按第二压敏胶层的原料配比称取聚硅氧烷、铂金催化剂、甲基氢聚硅氧烷以及炔醇;将上述原料与乙酯以1:1.4~1.6的质量比混合稀释后制得第二稀释液,将所述第二稀释液涂布在所述硅胶基层表面上,然后经过具有七节烘干区的烘箱进行加热固化,每节烘干区的长度为3.5~4.5米,七节烘干区的温度依次为75~85℃,95~105℃,135~145℃,155~165℃,135~145℃,135~145℃以及115~125℃;机速15~25m/min;固化后形成所述第二压敏胶层,在所述第二压敏胶层上覆上第四pet膜;6)制备第三压敏胶层:撕开所述硅胶基层表面上的氟素离型膜,按第三压敏胶层的原料配比称取mq硅树脂、甲苯、聚硅氧烷、铂金催化剂以及甲基氢聚硅氧烷;将上述原料与乙酯以1:1.1~1.2的质量比混合稀释后制得第三稀释液,将所述第三稀释液涂布在所述硅胶基层表面上,然后经过具有七节烘干区的烘箱进行加热固化,每节烘干区的长度为3.5~4.5米,七节烘干区的温度依次为75~85℃,95~105℃,135~145℃,155~165℃,135~145℃,135~145℃以及115~125℃;机速15~25m/min;固化后形成所述第三压敏胶层,在所述第三压敏胶层上覆上第五pet膜,制得所述硅胶薄膜。本发明实施例提供的硅胶薄膜及其制备方法中的上述一个或多个技术方案至少具有如下技术效果之一:1、该硅胶薄膜包括一硅胶基层,基于该硅胶基层具有透明性好,柔韧性好,无毒无味,生理惰性,热化学性能好(可耐200℃高温),抗撕裂性能好,伸长率好,弹性好和防震性能好等特点,该硅胶基层为基于铂金硫化体系的有机硅成膜液态胶,固化后无低分子析出,表面平整度好,薄膜膜性佳,干爽度高;2、该硅胶薄膜的制备方法步骤简单,所需设备少,制得的硅胶基层表面平整度好,薄膜膜性佳。附图说明为了更清楚地说明本发明实施例中的技术方案,下面将对实施例或现有技术描述中所需要使用的附图作简单地介绍,显而易见地,下面描述中的附图仅仅是本发明的一些实施例,对于本领域普通技术人员来讲,在不付出创造性劳动性的前提下,还可以根据这些附图获得其他的附图。图1为本发明实施例提供的硅胶薄膜的结构示意图。图2为本发明实施例提供的硅胶薄膜的另一结构示意图。具体实施方式下面详细描述本发明的实施例,所述实施例的示例在附图中示出,其中自始至终相同或类似的标号表示相同或类似的元件或具有相同或类似功能的元件。下面通过参考附图描述的实施例是示例性的,旨在用于解释本发明的实施例,而不能理解为对本发明的限制。本发明提供一种硅胶薄膜,包括一硅胶基层100,所述硅胶基层100包括按质量百分比计的以下原料:50~55%的聚硅氧烷;40~45%的vmq硅树脂;0.8~1%的铂金催化剂;4~6%的甲基氢聚硅氧烷以及0.1~0.15%的炔醇。该硅胶薄膜包括一硅胶基层100,基于该硅胶基层100具有透明性好,柔韧性好,无毒无味,生理惰性,热化学性能好(可耐200℃高温),抗撕裂性能好,伸长率好,弹性好和防震性能好等特点,该硅胶基层100为基于铂金硫化体系的有机硅成膜液态胶,固化后无低分子析出,表面平整度好,薄膜膜性佳,干爽度高。本发明的硅胶薄膜还包括一功能涂层200a以及一胶粘层300a,所述功能涂层200a和所述胶粘层300a分别设于所述硅胶基层100的正面和反面上;所述功能性涂层为自修复涂层、抗污涂层、抗指纹涂层、耐磨层、耐水解层、抗紫外线层或耐候层中的任意一种。所述功能性涂层可以赋予硅胶薄膜相应的功能。入抗污涂层使其具有抗污功能,抗指纹涂层可以使其具有抗指纹功能。基于所述硅胶基层100可以生产出各种功能的硅胶薄膜。本发明的所述自修复涂层包括按质量百分比计的以下原料:50~60%的丙烯酸酯以及40~50%的乙酸丁酯。所述自修复涂层具有自修复功能,则该硅胶薄膜是一种自修复薄膜。本发明的所述胶粘层300a为第一压敏胶层,所述第一压敏胶层包括按质量百分比计的以下原料:30~40%的mq硅树脂;30~40%的甲苯;20~30%的聚硅氧烷;0.8~1%的铂金催化剂以及1~2%的甲基氢聚硅氧烷。本发明的硅胶薄膜还包括一第二压敏胶层200b和一第三压敏胶层300b,所述第二压敏胶层200b和所述第三压敏胶层300b分别设于所述硅胶基层100的正面和反面。所述第三压敏胶层300b的粘性大于所述第二压敏胶层200b的粘性。通过在硅胶薄膜上涂布压敏胶,可作为包装保护膜或贴屏保护膜。本发明的所述第二压敏胶层200b包括按质量百分比计的以下原料:97~98%的聚硅氧烷;0.8~1%的铂金催化剂;1~2%的甲基氢聚硅氧烷以及0.1~0.15%的炔醇。本发明的所述第三压敏胶层300b包括按质量百分比计的以下原料:30~40%的mq硅树脂;30~40%的甲苯;20~30%的聚硅氧烷;0.8~1%的铂金催化剂以及1~2%的甲基氢聚硅氧烷。本发明还提供上述的硅胶薄膜的制备方法,包括以下步骤:1)原料混合:按硅胶基层100的原料配比称取聚硅氧烷、vmq硅树脂、铂金催化剂、甲基氢聚硅氧烷以及炔醇,混合均匀;2)加热固化:在氟素离型膜上涂布上述原料,经过具有七节烘干区的烘箱进行加热固化,每节烘干区的长度为3.5~4.5米,七节烘干区的温度依次为85~95℃,115~125℃,135~145℃,145~155℃,145~155℃,115~125℃以及95~105℃;机速5~8m/min;固化后形成所述硅胶基层100,并在所述硅胶基层100的表面上覆上第一pet膜。本发明的硅胶薄膜的制备方法还包括以下步骤:3)制备第一压敏胶层:撕开所述硅胶基层100表面上的所述第一pet膜,按第一压敏胶层的原料配比称取mq硅树脂、甲苯、聚硅氧烷、铂金催化剂以及甲基氢聚硅氧烷;将上述原料与乙酯以1:1.1~1.2的质量比混合稀释后制得第一稀释液,将所述第一稀释液涂布在所述硅胶基层100表面上,然后经过具有七节烘干区的烘箱进行加热固化,每节烘干区的长度为3.5~4.5米,七节烘干区的温度依次为75~85℃,95~105℃,135~145℃,155~165℃,135~145℃,135~145℃以及115~125℃;机速15~25m/min;固化后形成所述第一压敏胶层,在所述胶粘层300a上覆上第二pet膜;4)制备自修复涂层:撕开所述硅胶基层100表面上的氟素离型膜,按自修复涂层的原料配比称取丙烯酸酯和乙酸丁酯,将上述原料混合后涂布在所述硅胶基层100上,然后经过具有七节烘干区的烘箱进行加热固化,每节烘干区的长度为3.5~4.5米,七节烘干区的温度依次为55~65℃,75~85℃,95~105℃,115~125℃,95~105℃以及75~85℃;机速15~20m/min;固化后形成所述自修复涂层,在所述胶粘层300a上覆上第三pet膜,制得所述硅胶薄膜。本发明的硅胶薄膜的制备方法还包括以下步骤:5)制备第二压敏胶层200b:撕开所述硅胶基层100表面上的所述第一pet膜,按第二压敏胶层200b的原料配比称取聚硅氧烷、铂金催化剂、甲基氢聚硅氧烷以及炔醇;将上述原料与乙酯以1:1.4~1.6的质量比混合稀释后制得第二稀释液,将所述第二稀释液涂布在所述硅胶基层100表面上,然后经过具有七节烘干区的烘箱进行加热固化,每节烘干区的长度为3.5~4.5米,七节烘干区的温度依次为75~85℃,95~105℃,135~145℃,155~165℃,135~145℃,135~145℃以及115~125℃;机速15~25m/min;固化后形成所述第二压敏胶层200b,在所述第二压敏胶层200b上覆上第四pet膜;6)制备第三压敏胶层300b:撕开所述硅胶基层100表面上的氟素离型膜,按第三压敏胶层300b的原料配比称取mq硅树脂、甲苯、聚硅氧烷、铂金催化剂以及甲基氢聚硅氧烷;将上述原料与乙酯以1:1.1~1.2的质量比混合稀释后制得第三稀释液,将所述第三稀释液涂布在所述硅胶基层100表面上,然后经过具有七节烘干区的烘箱进行加热固化,每节烘干区的长度为3.5~4.5米,七节烘干区的温度依次为75~85℃,95~105℃,135~145℃,155~165℃,135~145℃,135~145℃以及115~125℃;机速15~25m/min;固化后形成所述第三压敏胶层300b,在所述第三压敏胶层300b上覆上第五pet膜,制得所述硅胶薄膜。该硅胶薄膜的制备方法步骤简单,所需设备少,制得的硅胶基层100表面平整度好,薄膜膜性佳。为了进一步理解本发明,下面结合实施例对本发明提供的硅胶薄膜的制备方法进行详细说明,本发明的保护范围不受以下实施例的限制。在以下实施例中,所采用的原料均为市售产品。此外,以下实施例所采用的烘箱具有七节烘干区,每节烘干区的长度均为4米。实施例1~8中的硅胶基层100的原料配比请见表1。实施例1~4中的第一压敏胶层和实施例5~8中的第三压敏胶层300b的原料配比请见表2(第一压敏胶层和第三压敏胶层300b的原料配比相同)。实施例1~4中的自修复涂层的原料配比请见表3。实施例5~8中的第二压敏胶层200b的原料配比请见表4。表1实施例1、5实施例2、6实施例3、7实施例4、8聚硅氧烷(%)5552.45550vmq硅树脂(%)4041.454045铂金催化剂(%)0.810.870.88甲基氢聚硅氧烷(%)4.1544炔醇(%)0.10.150.130.12表2表3实施例1实施例2实施例3实施例4丙烯酸酯(%)60505557乙酸丁酯(%)40504543表4实施例5实施例6实施例7实施例8聚硅氧烷(%)97989797.6铂金催化剂(%)10.850.880.8甲基氢聚硅氧烷(%)1.9121.5炔醇(%)0.10.150.120.1实施例1本实施例提供的硅胶薄膜的制备方法,包括以下步骤:1)原料混合:按硅胶基层100的原料配比称取聚硅氧烷、vmq硅树脂、铂金催化剂、甲基氢聚硅氧烷以及炔醇,混合均匀;2)加热固化:在氟素离型膜上涂布上述原料,经过具有七节烘干区的烘箱进行加热固化,七节烘干区的温度依次为85℃,115℃,135℃,145℃,145℃,115℃以及95℃;机速5m/min;固化后形成所述硅胶基层100,并在所述硅胶基层100的表面上覆上第一pet膜。3)制备第一压敏胶层:撕开所述硅胶基层100表面上的所述第一pet膜,按第一压敏胶层的原料配比称取mq硅树脂、甲苯、聚硅氧烷、铂金催化剂以及甲基氢聚硅氧烷;将上述原料与乙酯以1:1.1的质量比混合稀释后制得第一稀释液,将所述第一稀释液涂布在所述硅胶基层100表面上,然后经过具有七节烘干区的烘箱进行加热固化,七节烘干区的温度依次为75℃,95℃,135℃,155℃,135℃,135℃以及115℃;机速15m/min;固化后形成所述第一压敏胶层,在所述胶粘层300a上覆上第二pet膜;4)制备自修复涂层:撕开所述硅胶基层100表面上的氟素离型膜,按自修复涂层的原料配比称取丙烯酸酯和乙酸丁酯,将上述原料混合后涂布在所述硅胶基层100上,然后经过具有七节烘干区的烘箱进行加热固化,七节烘干区的温度依次为55℃,75℃,95℃,115℃,95℃以及75℃;机速15m/min;固化后形成所述自修复涂层,在所述胶粘层300a上覆上第三pet膜,制得所述硅胶薄膜。实施例2本实施例提供的硅胶薄膜的制备方法,包括以下步骤:1)原料混合:按硅胶基层100的原料配比称取聚硅氧烷、vmq硅树脂、铂金催化剂、甲基氢聚硅氧烷以及炔醇,混合均匀;2)加热固化:在氟素离型膜上涂布上述原料,经过具有七节烘干区的烘箱进行加热固化,七节烘干区的温度依次为90℃,120℃,140℃,150℃,150℃,120℃以及100℃;机速6m/min;固化后形成所述硅胶基层100,并在所述硅胶基层100的表面上覆上第一pet膜。3)制备第一压敏胶层:撕开所述硅胶基层100表面上的所述第一pet膜,按第一压敏胶层的原料配比称取mq硅树脂、甲苯、聚硅氧烷、铂金催化剂以及甲基氢聚硅氧烷;将上述原料与乙酯以1:1.15的质量比混合稀释后制得第一稀释液,将所述第一稀释液涂布在所述硅胶基层100表面上,然后经过具有七节烘干区的烘箱进行加热固化,七节烘干区的温度依次为80℃,100℃,140℃,160℃,140℃,140℃以及120℃;机速20m/min;固化后形成所述第一压敏胶层,在所述胶粘层300a上覆上第二pet膜;4)制备自修复涂层:撕开所述硅胶基层100表面上的氟素离型膜,按自修复涂层的原料配比称取丙烯酸酯和乙酸丁酯,将上述原料混合后涂布在所述硅胶基层100上,然后经过具有七节烘干区的烘箱进行加热固化,七节烘干区的温度依次为60℃,80℃,100℃,120℃,100℃以及80℃;机速17m/min;固化后形成所述自修复涂层,在所述胶粘层300a上覆上第三pet膜,制得所述硅胶薄膜。实施例3本实施例提供的硅胶薄膜的制备方法,包括以下步骤:1)原料混合:按硅胶基层100的原料配比称取聚硅氧烷、vmq硅树脂、铂金催化剂、甲基氢聚硅氧烷以及炔醇,混合均匀;2)加热固化:在氟素离型膜上涂布上述原料,经过具有七节烘干区的烘箱进行加热固化,七节烘干区的温度依次为92℃,122℃,142℃,152℃,152℃,122℃以及102℃;机速7m/min;固化后形成所述硅胶基层100,并在所述硅胶基层100的表面上覆上第一pet膜。3)制备第一压敏胶层:撕开所述硅胶基层100表面上的所述第一pet膜,按第一压敏胶层的原料配比称取mq硅树脂、甲苯、聚硅氧烷、铂金催化剂以及甲基氢聚硅氧烷;将上述原料与乙酯以1:1.17的质量比混合稀释后制得第一稀释液,将所述第一稀释液涂布在所述硅胶基层100表面上,然后经过具有七节烘干区的烘箱进行加热固化,七节烘干区的温度依次为82℃,102℃,142℃,162℃,142℃,142℃以及122℃;机速22m/min;固化后形成所述第一压敏胶层,在所述胶粘层300a上覆上第二pet膜;4)制备自修复涂层:撕开所述硅胶基层100表面上的氟素离型膜,按自修复涂层的原料配比称取丙烯酸酯和乙酸丁酯,将上述原料混合后涂布在所述硅胶基层100上,然后经过具有七节烘干区的烘箱进行加热固化,七节烘干区的温度依次为62℃,82℃,102℃,122℃,102℃以及82℃;机速18m/min;固化后形成所述自修复涂层,在所述胶粘层300a上覆上第三pet膜,制得所述硅胶薄膜。实施例4本实施例提供的硅胶薄膜的制备方法,包括以下步骤:1)原料混合:按硅胶基层100的原料配比称取聚硅氧烷、vmq硅树脂、铂金催化剂、甲基氢聚硅氧烷以及炔醇,混合均匀;2)加热固化:在氟素离型膜上涂布上述原料,经过具有七节烘干区的烘箱进行加热固化,七节烘干区的温度依次为95℃,125℃,145℃,155℃,155℃,125℃以及105℃;机速8m/min;固化后形成所述硅胶基层100,并在所述硅胶基层100的表面上覆上第一pet膜。3)制备第一压敏胶层:撕开所述硅胶基层100表面上的所述第一pet膜,按第一压敏胶层的原料配比称取mq硅树脂、甲苯、聚硅氧烷、铂金催化剂以及甲基氢聚硅氧烷;将上述原料与乙酯以1:1.2的质量比混合稀释后制得第一稀释液,将所述第一稀释液涂布在所述硅胶基层100表面上,然后经过具有七节烘干区的烘箱进行加热固化,七节烘干区的温度依次为85℃,105℃,145℃,165℃,145℃,145℃以及125℃;机速25m/min;固化后形成所述第一压敏胶层,在所述胶粘层300a上覆上第二pet膜;4)制备自修复涂层:撕开所述硅胶基层100表面上的氟素离型膜,按自修复涂层的原料配比称取丙烯酸酯和乙酸丁酯,将上述原料混合后涂布在所述硅胶基层100上,然后经过具有七节烘干区的烘箱进行加热固化,七节烘干区的温度依次为65℃,85℃,105℃,125℃,105℃以及85℃;机速20m/min;固化后形成所述自修复涂层,在所述胶粘层300a上覆上第三pet膜,制得所述硅胶薄膜。实施例5本实施例提供的硅胶薄膜的制备方法,包括以下步骤:1)原料混合:按硅胶基层100的原料配比称取聚硅氧烷、vmq硅树脂、铂金催化剂、甲基氢聚硅氧烷以及炔醇,混合均匀;2)加热固化:在氟素离型膜上涂布上述原料,经过具有七节烘干区的烘箱进行加热固化,七节烘干区的温度依次为85℃,115℃,135℃,145℃,145℃,115℃以及95℃;机速5m/min;固化后形成所述硅胶基层100,并在所述硅胶基层100的表面上覆上第一pet膜。3)制备第二压敏胶层200b:撕开所述硅胶基层100表面上的所述第一pet膜,按第二压敏胶层200b的原料配比称取聚硅氧烷、铂金催化剂、甲基氢聚硅氧烷以及炔醇;将上述原料与乙酯以1:1.4的质量比混合稀释后制得第二稀释液,将所述第二稀释液涂布在所述硅胶基层100表面上,然后经过具有七节烘干区的烘箱进行加热固化,七节烘干区的温度依次为75℃,95℃,135℃,155℃,135℃,135℃以及115℃;机速15m/min;固化后形成所述第二压敏胶层200b,在所述第二压敏胶层200b上覆上第四pet膜;4)制备第三压敏胶层300b:撕开所述硅胶基层100表面上的氟素离型膜,按第三压敏胶层300b的原料配比称取mq硅树脂、甲苯、聚硅氧烷、铂金催化剂以及甲基氢聚硅氧烷;将上述原料与乙酯以1:1.1的质量比混合稀释后制得第三稀释液,将所述第三稀释液涂布在所述硅胶基层100表面上,然后经过具有七节烘干区的烘箱进行加热固化,七节烘干区的温度依次为75℃,95℃,135℃,155℃,135℃,135℃以及115℃;机速15m/min;固化后形成所述第三压敏胶层300b,在所述第三压敏胶层300b上覆上第五pet膜,制得所述硅胶薄膜。实施例6本实施例提供的硅胶薄膜的制备方法,包括以下步骤:1)原料混合:按硅胶基层100的原料配比称取聚硅氧烷、vmq硅树脂、铂金催化剂、甲基氢聚硅氧烷以及炔醇,混合均匀;2)加热固化:在氟素离型膜上涂布上述原料,经过具有七节烘干区的烘箱进行加热固化,七节烘干区的温度依次为90℃,120℃,140℃,150℃,150℃,120℃以及100℃;机速6m/min;固化后形成所述硅胶基层100,并在所述硅胶基层100的表面上覆上第一pet膜。3)制备第二压敏胶层200b:撕开所述硅胶基层100表面上的所述第一pet膜,按第二压敏胶层200b的原料配比称取聚硅氧烷、铂金催化剂、甲基氢聚硅氧烷以及炔醇;将上述原料与乙酯以1:1.5的质量比混合稀释后制得第二稀释液,将所述第二稀释液涂布在所述硅胶基层100表面上,然后经过具有七节烘干区的烘箱进行加热固化,七节烘干区的温度依次为80℃,100℃,140℃,160℃,140℃,140℃以及120℃;机速20m/min;固化后形成所述第二压敏胶层200b,在所述第二压敏胶层200b上覆上第四pet膜;4)制备第三压敏胶层300b:撕开所述硅胶基层100表面上的氟素离型膜,按第三压敏胶层300b的原料配比称取mq硅树脂、甲苯、聚硅氧烷、铂金催化剂以及甲基氢聚硅氧烷;将上述原料与乙酯以1:1.15的质量比混合稀释后制得第三稀释液,将所述第三稀释液涂布在所述硅胶基层100表面上,然后经过具有七节烘干区的烘箱进行加热固化,七节烘干区的温度依次为80℃,100℃,140℃,160℃,140℃,140℃以及120℃;机速20m/min;固化后形成所述第三压敏胶层300b,在所述第三压敏胶层300b上覆上第五pet膜,制得所述硅胶薄膜。实施例7本实施例提供的硅胶薄膜的制备方法,包括以下步骤:1)原料混合:按硅胶基层100的原料配比称取聚硅氧烷、vmq硅树脂、铂金催化剂、甲基氢聚硅氧烷以及炔醇,混合均匀;2)加热固化:在氟素离型膜上涂布上述原料,经过具有七节烘干区的烘箱进行加热固化,七节烘干区的温度依次为92℃,122℃,142℃,152℃,152℃,122℃以及102℃;机速7m/min;固化后形成所述硅胶基层100,并在所述硅胶基层100的表面上覆上第一pet膜。3)制备第二压敏胶层200b:撕开所述硅胶基层100表面上的所述第一pet膜,按第二压敏胶层200b的原料配比称取聚硅氧烷、铂金催化剂、甲基氢聚硅氧烷以及炔醇;将上述原料与乙酯以1:1.55的质量比混合稀释后制得第二稀释液,将所述第二稀释液涂布在所述硅胶基层100表面上,然后经过具有七节烘干区的烘箱进行加热固化,七节烘干区的温度依次为82℃,102℃,142℃,162℃,142℃,142℃以及122℃;机速22m/min;固化后形成所述第二压敏胶层200b,在所述第二压敏胶层200b上覆上第四pet膜;4)制备第三压敏胶层300b:撕开所述硅胶基层100表面上的氟素离型膜,按第三压敏胶层300b的原料配比称取mq硅树脂、甲苯、聚硅氧烷、铂金催化剂以及甲基氢聚硅氧烷;将上述原料与乙酯以1:1.17的质量比混合稀释后制得第三稀释液,将所述第三稀释液涂布在所述硅胶基层100表面上,然后经过具有七节烘干区的烘箱进行加热固化,七节烘干区的温度依次为82℃,102℃,142℃,162℃,142℃,142℃以及122℃;机速22m/min;固化后形成所述第三压敏胶层300b,在所述第三压敏胶层300b上覆上第五pet膜,制得所述硅胶薄膜。实施例8本实施例提供的硅胶薄膜的制备方法,包括以下步骤:1)原料混合:按硅胶基层100的原料配比称取聚硅氧烷、vmq硅树脂、铂金催化剂、甲基氢聚硅氧烷以及炔醇,混合均匀;2)加热固化:在氟素离型膜上涂布上述原料,经过具有七节烘干区的烘箱进行加热固化,七节烘干区的温度依次为95℃,125℃,145℃,155℃,155℃,125℃以及105℃;机速8m/min;固化后形成所述硅胶基层100,并在所述硅胶基层100的表面上覆上第一pet膜。3)制备第二压敏胶层200b:撕开所述硅胶基层100表面上的所述第一pet膜,按第二压敏胶层200b的原料配比称取聚硅氧烷、铂金催化剂、甲基氢聚硅氧烷以及炔醇;将上述原料与乙酯以1:1.6的质量比混合稀释后制得第二稀释液,将所述第二稀释液涂布在所述硅胶基层100表面上,然后经过具有七节烘干区的烘箱进行加热固化,七节烘干区的温度依次为85℃,105℃,145℃,165℃,145℃,145℃以及125℃;机速25m/min;固化后形成所述第二压敏胶层200b,在所述第二压敏胶层200b上覆上第四pet膜;4)制备第三压敏胶层300b:撕开所述硅胶基层100表面上的氟素离型膜,按第三压敏胶层300b的原料配比称取mq硅树脂、甲苯、聚硅氧烷、铂金催化剂以及甲基氢聚硅氧烷;将上述原料与乙酯以1:1.2的质量比混合稀释后制得第三稀释液,将所述第三稀释液涂布在所述硅胶基层100表面上,然后经过具有七节烘干区的烘箱进行加热固化,七节烘干区的温度依次为85℃,105℃,145℃,165℃,145℃,145℃以及125℃;机速25m/min;固化后形成所述第三压敏胶层300b,在所述第三压敏胶层300b上覆上第五pet膜,制得所述硅胶薄膜。以上所述仅为本发明的较佳实施例而已,并不用以限制本发明,凡在本发明的精神和原则之内所作的任何修改、等同替换和改进等,均应包含在本发明的保护范围之内。当前第1页1 2 3 
起点商标作为专业知识产权交易平台,可以帮助大家解决很多问题,如果大家想要了解更多知产交易信息请点击 【在线咨询】或添加微信 【19522093243】与客服一对一沟通,为大家解决相关问题。
此文章来源于网络,如有侵权,请联系删除



tips