一种环氧氯丙烷生产装置和工艺的制作方法



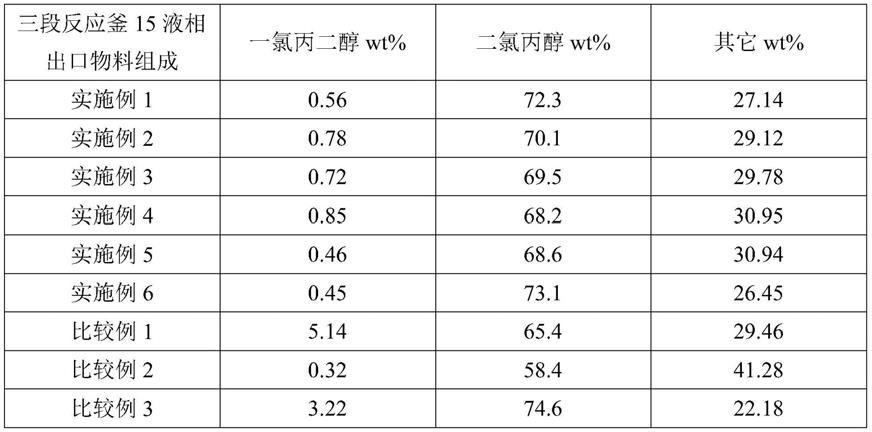
[0001]
本发明涉及化工生产技术领域,具体指一种环氧氯丙烷生产装置和工艺。
背景技术:
[0002]
环氧氯丙烷(别名表氯醇),化学名为1-氯-2,3-环氧丙烷,分子式为c
3
h
5
ocl,沸点115.2℃,凝固点-57.2℃,是一种易挥发、不稳定的无色液体,微溶于水,能与多种有机溶剂混溶。
[0003]
环氧氯丙烷是一种重要的有机化工原料和精细化工产品,是丙烯衍生物中的一个大品种产品,主要用于合成甘油、环氧树脂、氯醇橡胶、硝化甘油炸药等,也可用作纤维素酯、树脂和纤维素醚的溶剂;还是生产表面活性剂、增塑剂、稳定剂、胶粘剂和离子交换树脂的主要原料。在涂料、胶粘剂、增强材料、浇铸材料和电子层压制品等行业也有广泛的应用。此外,环氧氯丙烷还可用于合成表面活性剂、医药、农药、涂料、胶料、离子交换树脂等多种产品,以及用于生产化学稳定剂、化工染料和水处理剂等。
[0004]
目前环氧氯丙烷的生产方法主要是丙烯高温氯化法、醋酸丙烯酯法,此两种方法均以丙烯为原料,依赖石油能源的消费。随着石油能源的进一步价格上涨和资源短缺,丙烯的原料来源和价格均受市场的影响较大。由于国际上生物柴油的兴起,大量的副产甘油引发了甘油市场的过剩,而每生产10吨生物柴油约可产生1吨的副产物甘油。生物柴油副产的甘油市场供大于求,甘油法环氧氯丙烷成为新兴环氧氯丙烷生产技术近来被广泛关注。二氯丙醇,含2,3-二氯-1-丙醇和1,3-二氯-2-丙醇两种同分异构体,分子式为c
3
h
6
cl
2
o,沸点174℃,无色液体微有氯仿气味,是环氧氯丙烷的生产中间产品。二氯丙醇经过与ca(oh)
2
、naoh皂化反应后,二氯丙醇会环化生成最终产品环氧氯丙烷。
[0005]
如专利申请号为cn202010346652.6(公布号为cn111499598a)的发明专利《一种甘油法制备环氧氯丙烷生产工艺》公开了一种甘油法制备环氧氯丙烷生产工艺,将甘油、催化剂以及氯化氢加入到反应器中进行反应,使反应器中生成一氯丙二醇和水,一氯丙二醇在反应器中与氯化氢继续反应生成二氯丙醇,反应器中的原料在反应一段时间后,所得产物进入到反应精馏塔的内部,原料在反应精馏塔中反应并分离,氢氯化得到的二氯丙醇,送入预反应器与碱液进行环化反应,大部分液碱从预反应器进口加入,另一部分碱液通过进预反应器进料侧线加入,预反应器中的所得产物、剩余的1,2-二氯丙醇以及碱液进入到环化塔中,充分反应生成环氧氯丙烷,环化塔塔顶所得的产物送入第二精馏塔进一步分离,塔顶得到环氧氯丙烷。
[0006]
但是上述方案中,第一,第一精馏塔塔底的物料直接送入反应器中,一方面会导致混合不均匀,另一方面会导致物料中的重组分一起回到反应系统,增加蒸汽消耗;第二,反应精馏塔和第一精馏塔塔顶得到的二氯丙醇和氯化氢一起进入下游,在造成氯化氢浪费的同时还增加了皂化单元中碱液的消耗量。
技术实现要素:
[0007]
本发明所要解决的第一个技术问题是针对现有技术的现状,提供一种可以在稳定生产的同时有效回收精馏塔的轻组分回反应系统,并减小能耗的环氧氯丙烷生产装置。
[0008]
本发明所要解决的第二个技术问题是提供一种应用有上述环氧氯丙烷生产装置的环氧氯丙烷生产工艺。
[0009]
本发明解决上述第一个技术问题所采用的技术方案为:一种环氧氯丙烷生产装置,包括有依次相连接的甘油氯化单元、二氯丙醇精制单元和二氯丙醇皂化单元,其特征在于:所述的二氯丙醇精制单元包括有
[0010]
解析塔,底部安装有第一再沸器,顶部安装有第一冷凝器,其液相入口连通所述甘油氯化单元的物料出口;
[0011]
精馏塔,底部安装有第二再沸器,顶部安装有第二冷凝器,其液相入口连通所述解析塔的液相出口,底部具有供重组分排出的第一液相出口,侧部具有供轻组分排出的第二液相出口,该第二液相出口连通所述二氯丙醇皂化单元的物料入口;
[0012]
第一分层罐,其液相入口连通所述精馏塔的第一液相出口,具有供重组分排出的第一液相出口以及供轻组分排出的第二液相出口,所述第一分层罐的第二液相出口连通所述甘油氯化单元的物料入口;以及
[0013]
二氯丙醇回收塔,其液相入口连通所述第一分层罐的第一液相出口。
[0014]
优选地,所述的甘油氯化单元包括有
[0015]
原料储罐,用于储存甘油催化剂溶液;
[0016]
预反应塔,其液相入口连通所述原料储罐的物料出口,顶部具有供尾气排出的气相出口;
[0017]
一段反应釜,其液相入口连通所述预反应塔的液相出口,其气相入口连通外接的氯化氢管路;
[0018]
二段反应釜,其液相入口连通所述预反应塔的液相出口以及所述一段反应釜的液相出口,其气相入口连通外接的氯化氢管路以及所述一段反应釜的气相出口;以及
[0019]
三段反应釜,其液相入口连通所述预反应塔的液相出口以及所述二段反应釜的液相出口,其气相入口连通外接的氯化氢管路以及所述二段反应釜的气相出口,其气相出口连通所述预反应塔的气相入口;
[0020]
所述解析塔的液相入口连通所述三段反应釜的液相出口;
[0021]
所述第一分层罐的第二液相出口连通所述一段反应釜、二段反应釜和三段反应釜的液相入口。
[0022]
上述甘油氯化单元中,预反应塔的液相出口连通各反应釜的液相入口,这样,首次开车预反应塔的物料可以进所有反应釜,开车操作方便;另外,上一级反应釜的物料进入下一级,可以有效提高下一级反应釜中甘油和氯化氢之间的反应效率。
[0023]
进一步,所述解析塔的气相出口连通所述预反应塔的气相入口。由于解析塔的气相出口连通预反应塔的气相入口,第一,预计能回收200nm
3
/h的氯化氢,减少1t/h石灰乳消耗(15wt%浓度);第二,能够减小后续解析塔和皂化塔的负荷;第三,能够极大降低皂化塔中一氯丙二醇的含量。
[0024]
进一步,所述的二氯丙醇精制单元还包括有
[0025]
甘油吸收器,其液相入口连通所述原料储罐的物料出口,其气相入口连通所述精馏塔的气相出口,其液相出口连通所述预反应塔的液相入口;以及
[0026]
第一冷却器,其气相入口连通所述甘油吸收器的气相出口,其液相出口连通所述第一分层罐的液相入口。
[0027]
上述甘油吸收器能吸收精馏塔尾气中的部分有机物和氯化氢,由于甘油吸收器的液相出口连通预反应塔的液相入口,可以方便回收氯化氢和甘油;
[0028]
第一冷却器冷却下来的有机物回收至第一分层罐,可以有效回收精馏塔尾气中的二氯丙醇。
[0029]
再进一步,所述的二氯丙醇精制单元还包括有
[0030]
喷射器,其气相入口连通所述第一冷却器的气相出口;以及
[0031]
碱洗塔,其气相入口连通所述第一冷却器的气相出口,顶部的气相出口连接有第一真空泵。
[0032]
上述甘油吸收器、第一冷却器和碱洗塔可以除掉不凝气中的大部分氯化氢,防止因不凝气过多而影响精馏塔真空度,同时尾气中夹杂的酸性不凝气会腐蚀第一真空泵,影响二氯丙醇的质量和产量的稳定性;
[0033]
喷射泵可将蒸汽以很高的速度由喷嘴喷出,在真空室形成低压,使精馏塔顶部气体依次进入真空室、混合室、皂化塔,喷射的蒸汽可供皂化塔反应使用,同时喷射器可以减少下述第一真空泵的负荷或在第一真空泵故障时部分代替第一真空泵,保障精馏塔的稳定运行。
[0034]
进一步,所述的二氯丙醇皂化单元包括有
[0035]
碱液罐,用于储存碱液;
[0036]
皂化塔,具有对应于第二块塔板设置的物料入口以及对应于第一块塔板设置的热水入口,所述皂化塔的物料入口连通所述精馏塔的第二液相出口以及所述碱液罐的物料出口,皂化塔的热水入口连通外接的热水管路;
[0037]
第三冷凝器,其气相入口连通所述皂化塔的气相出口,其气相出口连接有第二真空泵;
[0038]
第二分层罐,其液相入口连通所述第三冷凝器的液相出口,具有供重组分排出的第一液相出口以及供轻组分排出的第二液相出口,所述的第二液相出口连通所述皂化塔的回流入口;以及
[0039]
粗环氧氯丙烷储罐,其物料入口连通所述粗环氧氯丙烷储罐的第一液相出口。
[0040]
一般皂化塔进料采用第一块塔板进料,此处采用第二块塔板进料,第一块塔板为热水洗涤,具有以下优点:第一、皂化塔易结垢,增加热水冲洗口可以避免结垢现象;第二、如果从第一块塔板进料会使进来的物料直接被二氯丙醇蒸汽汽提上去,导致二氯丙醇受污染,如果从第三块甚至更下方的塔板进料,会对反应效率和收率产生影响,而从第二块塔板进料可以有效避免上述问题;第三、第一块塔板进热水洗涤,第二块塔板进料,且两个进口互不影响,相比原先第一块塔板进料的方式具有开车效率更高的优势。
[0041]
再进一步,所述的二氯丙醇皂化单元还包括有
[0042]
闪蒸罐,其液相入口连通所述皂化塔的液相出口;
[0043]
第二冷却器,其液相入口连通所述闪蒸罐的液相出口,其液相出口连接至氯化钙
预处理单元;以及
[0044]
第四冷凝器,其气相入口连通所述闪蒸罐的气相出口,其气相出口连接有第三真空泵,其液相出口连接至污水处理单元。
[0045]
皂化塔液相出口排出的氯化钙母液固含量大,用冷却器冷却极易堵塞,此处通过真空闪蒸冷却,从而保证系统稳定运行。
[0046]
本发明解决上述第二个技术问题所采用的技术方案为:一种应用有上述环氧氯丙烷生产装置的环氧氯丙烷生产工艺,包括有以下步骤:
[0047]
第一步,甘油氯化:原料储罐中的甘油催化剂溶液送入预反应塔中与来自各反应釜未反应完的氯化氢以及解析塔解析出来的氯化氢进行预反应,反应后的料液同时送入一段反应釜、二段反应釜和三段反应釜中,氯化氢管路将氯化氢送入各反应釜,一段反应釜的料液进入二段反应釜,二段反应釜的料液进入三段反应釜,三段反应釜反应完毕的粗二氯丙醇送入解析塔,一段反应釜未反应完的氯化氢进入二段反应釜,二段反应釜未反应完的氯化氢进入三段反应釜,三段反应釜未反应完的氯化氢送入预反应塔;
[0048]
第二步,二氯丙醇精制:解析塔对粗二氯丙醇进行解析,解析出来的气相送入预反应塔,解析后的粗二氯丙醇送入精馏塔,从精馏塔出来的重组分进入第一分层罐,第一分层罐分层后的重部分送往二氯丙醇回收塔回收其中的二氯丙醇,分层后的轻组分则返回各反应釜重新反应,精馏塔侧线出料为精二氯丙醇;
[0049]
第三步,二氯丙醇皂化:自精馏塔输送来的精二氯丙醇进入二氯丙醇皂化单元进行皂化制得环氧氯丙烷。
[0050]
优选地,自所述氯化氢管路送入所述一段反应釜、二段反应釜和三段反应釜中的氯化氢的比率为8:1:1~5:5:0。
[0051]
将合适比率的氯化氢分别送入一段反应釜、二段反应釜和三段反应釜中,可以确保三段反应釜中一氯丙二醇含量小于1%,减少皂化塔氯化钙母液一氯丙二醇和cod的含量。
[0052]
优选地,所述解析塔的操作压力0.15~0.30mpa,所述解析塔的气相出口通过自流管路连通所述预反应塔的气相入口,所述解析塔的液相出口通过第一管路连通所述精馏塔的液相入口,该第一管路为自流管路。
[0053]
通过提高解析塔的操作压力可以让解析塔中三元共沸物中的氯化氢更多地解析出来,但是操作压力过大会导致回收的一氯丙二醇变少,使得一氯丙二醇会和二氯丙醇一起进入精馏塔,因此需要合理控制解析塔的操作压力;
[0054]
另外,将解析塔的操作压力控制在0.15~0.30mpa,还起到了额外的作用:一方面,可以保证解析塔解析出氯化氢可以自流回收至预反应塔,减小能耗;另一方面,因为解析塔正压,精馏塔负压,解析塔的物料可以自流去精馏塔,减小能耗。
[0055]
与现有技术相比,本发明的优点在于:第一,精馏塔物料直接回反应釜混合不均匀,有了第一分层罐,可以起到稳定生产的作用同时减少重组分回反应系统,减少蒸汽消耗,使反应釜中催化剂含量比较均匀,反应速度更加平稳;第二,下层物料可以间断进二氯丙醇回收塔回收,不用连续运行,也可以降低蒸汽消耗。
附图说明
[0056]
图1为本发明环氧氯丙烷生产装置的实施例的结构示意图;
[0057]
图2为图1中甘油氯化单元的结构示意图;
[0058]
图3为图1中二氯丙醇精制单元的结构示意图;
[0059]
图4为图1中二氯丙醇皂化单元的结构示意图。
具体实施方式
[0060]
以下结合附图实施例对本发明作进一步详细描述。
[0061]
如图1至图4所示,为本发明环氧氯丙烷生产装置的一个优选实施例。
[0062]
如图1所示,环氧氯丙烷生产装置包括有依次相连接的甘油氯化单元1、二氯丙醇精制单元2和二氯丙醇皂化单元3。
[0063]
其中,如图2所示,甘油氯化单元1包括有原料储罐11、预反应塔12、一段反应釜13、二段反应釜14和三段反应釜15。
[0064]
具体地,原料储罐11用于储存甘油催化剂溶液;
[0065]
预反应塔12的顶部具有液相入口和气相出口,底部具有气相入口和液相出口;预反应塔12的液相入口连通原料储罐11的物料出口,预反应塔12的气相出口连接至尾气吸收单元121;本实施例中,预反应塔12采用pvdf泰勒花环作为填料,可以耐酸性物料的腐蚀,增加反应接触面积,确保设备稳定运行;在预反应塔12中,原料储罐11中混合好的甘油和催化剂与解析塔21和各反应釜未反应完的氯化氢进行初步反应,接着送入各反应釜中与氯化氢进行进一步的反应,物料最后送入解析塔21中除去未反应完的氯化氢;
[0066]
一段反应釜13、二段反应釜14和三段反应釜15的顶部均具有液相入口和气相出口,底部均具有气相入口和液相出口;
[0067]
一段反应釜13的液相入口连通预反应塔12的液相出口,一段反应釜13的气相入口连通外接的氯化氢管路10;本实施例中,一段反应釜13的数量至少为两台,且各一段反应釜13之间相互并联设置,一台运行,一台备用;
[0068]
二段反应釜14的液相入口连通预反应塔12的液相出口以及一段反应釜13的液相出口,二段反应釜14的气相入口连通外接的氯化氢管路10以及一段反应釜13的气相出口;
[0069]
三段反应釜15的液相入口连通预反应塔12的液相出口以及二段反应釜14的液相出口,三段反应釜15的气相入口连通外接的氯化氢管路10以及二段反应釜14的气相出口,三段反应釜15的气相出口连通预反应塔12的气相入口。
[0070]
上述甘油氯化单元1中,预反应塔12的液相出口连通各反应釜的液相入口,这样,首次开车预反应塔12的物料可以进所有反应釜,开车操作方便;另外,上一级反应釜的物料进入下一级,可以有效提高下一级反应釜中甘油和氯化氢之间的反应效率。
[0071]
如图3所示,二氯丙醇精制单元2包括有解析塔21、精馏塔22、甘油吸收器23、第一冷却器24、喷射器25、碱洗塔26、第一分层罐27和二氯丙醇回收塔28。
[0072]
具体地,解析塔21的底部安装有第一再沸器211,解析塔21的顶部安装有第一冷凝器212,解析塔21的液相入口连通三段反应釜15的液相出口,解析塔21顶部的气相出口通过自流管路连通预反应塔12的气相入口;本实施例中,解析塔21采用pvdf泰勒花环作为填料,可以使设备更将稳定运行;
[0073]
现有的方案中,通常会将解析塔塔顶的气体冷凝后直接通入皂化塔,冷凝液主要成分为含有一氯丙二醇和二氯丙醇的氯化氢水溶液中,其通入皂化塔会增加碱液用量,提高皂化塔负荷,而且一氯丙二醇进入氯化钙水溶液,会降低皂化水的品质,影响进一步回收利用,本实施例中,由于解析塔21的气相出口连通预反应塔12的气相入口,第一,预计能回收200nm
3
/h的氯化氢,减少1t/h石灰乳消耗(15wt%浓度);第二,能够减小后续解析塔和皂化塔的负荷;第三,能够极大降低皂化塔中一氯丙二醇的含量;
[0074]
精馏塔22的底部安装有第二再沸器221,精馏塔22的顶部安装有第二冷凝器222,精馏塔22的液相入口连通解析塔21底部的液相出口,精馏塔22的底部具有供重组分排出的第一液相出口,精馏塔22的侧部具有供轻组分排出的第二液相出口,精馏塔22的顶部具有供尾气排出的气相出口;具体地,解析塔21的液相出口分别通过第一管路223和第二管路224连通至精馏塔22的液相入口,第一管路223为自流管路,第二管路224上安装有能将物料从解析塔21的液相出口输送到精馏塔22的液相入口的第一输送泵225;第二再沸器221通过第一循环管路226和第二循环管路227连接在精馏塔22的底部,第一循环管路226采用虹吸自循环管路,第二循环管路227上安装有能将物料从第二循环管路227的入口输送到第二循环管路227的出口的循环泵228,这样,精馏塔22的第二再沸器221可以依靠虹吸自循环减少能耗,实际应用时,先期用循环泵228强制循环,后期将根据实际情况选择何种循环,节能降耗(每小时可以节省90kw);
[0075]
甘油吸收器23的液相入口连通原料储罐11的物料出口,甘油吸收器23的气相入口连通精馏塔22的气相出口,甘油吸收器23的液相出口连通预反应塔12的液相入口;上述甘油吸收器23能吸收精馏塔22尾气中的部分有机物和氯化氢,由于甘油吸收器23的液相出口连通预反应塔12的液相入口,可以方便回收氯化氢和甘油;
[0076]
第一冷却器24的气相入口连通甘油吸收器23的气相出口;第一冷却器24冷却下来的有机物回收至第一分层罐27,可以有效回收精馏塔22尾气中的二氯丙醇;
[0077]
喷射器25的气相入口连通第一冷却器24的气相出口;喷射泵25可将蒸汽以很高的速度由喷嘴喷出,在真空室形成低压,使精馏塔22顶部气体依次进入真空室、混合室、皂化塔,喷射的蒸汽可供皂化塔32反应使用,同时喷射器25可以减少下述第一真空泵261的负荷或在第一真空泵261故障时部分代替第一真空泵261,保障精馏塔22的稳定运行。
[0078]
碱洗塔26的气相入口连通第一冷却器24的气相出口,碱洗塔26顶部的气相出口连接有第一真空泵261;甘油吸收器23、第一冷却器24和碱洗塔26可以除掉不凝气中的大部分氯化氢,防止因不凝气过多而影响精馏塔22真空度,同时尾气中夹杂的酸性不凝气会腐蚀第一真空泵261,影响二氯丙醇的质量和产量的稳定性;
[0079]
第一分层罐27的液相入口连通精馏塔22的第一液相出口以及第一冷却器24的液相出口,第一分层罐27具有供重组分排出的第一液相出口以及供轻组分排出的第二液相出口,第一分层罐27的第二液相出口连通至一段反应釜13、二段反应釜14和三段反应釜15的液相入口;具体地,第一分层罐27的液相入口与精馏塔22的第一液相出口之间的管路上安装有能将物料从精馏塔22的第一液相出口输送到第一分层罐27的液相入口的第二输送泵271;
[0080]
上述第一分层罐27第一液相出口和第二液相出口排出的物料组成相似,但比例不同,其中第二液相出口排出的物料中催化剂和二元酸酯的含量更高;第一分层罐27作用主
要有以下两个:第一,精馏塔22物料直接回反应釜混合不均匀,有了第一分层罐27,可以起到稳定生产的作用同时减少重组分回反应系统,减少蒸汽消耗,使反应釜中催化剂含量比较均匀,反应速度更加平稳;第二,下层物料可以间断进二氯丙醇回收塔28回收,不用连续运行,也可以降低蒸汽消耗;
[0081]
二氯丙醇回收塔28,其液相入口连通第一分层罐27的第一液相出口;本实施例中,二氯丙醇回收塔28年可以回收760吨dch,效益明显。
[0082]
如图4所示,二氯丙醇皂化单元3包括有碱液罐31、皂化塔32、第三冷凝器33、第二分层罐34、粗环氧氯丙烷储罐35、闪蒸罐36、第二冷却器37和第四冷凝器38。
[0083]
碱液罐31用于储存碱液;本实施例中,碱液为氢氧化钙;
[0084]
皂化塔32具有对应于第二块塔板设置的物料入口以及对应于第一块塔板设置的热水入口,皂化塔32的物料入口连通精馏塔22的第二液相出口以及碱液罐31的物料出口,皂化塔32的热水入口连通外接的热水管路30;具体地,皂化塔32的物料入口与精馏塔22的第二液相出口之间的管路上安装有能将物料从精馏塔22的第二液相出口输送到皂化塔32的物料入口的第三输送泵321;
[0085]
一般皂化塔进料采用第一块塔板进料,此处采用第二块塔板进料,第一块塔板为热水洗涤,具有以下优点:第一、皂化塔32易结垢,增加热水冲洗口可以避免结垢现象;第二、如果从第一块塔板进料会使进来的物料直接被二氯丙醇蒸汽汽提上去,导致二氯丙醇受污染,如果从第三块甚至更下方的塔板进料,会对反应效率和收率产生影响,而从第二块塔板进料可以有效避免上述问题;第三、第一块塔板进热水洗涤,第二块塔板进料,且两个进口互不影响,相比原先第一块塔板进料的方式具有开车效率更高的优势;
[0086]
第三冷凝器33的气相入口连通皂化塔32顶部的气相出口,第三冷凝器33的气相出口连接有第二真空泵331;
[0087]
第二分层罐34的液相入口连通第三冷凝器33的液相出口,第二分层罐34具有供重组分排出的第一液相出口以及供轻组分排出的第二液相出口,第二液相出口连通皂化塔32的回流入口;具体地,皂化塔32的回流入口与第二分层罐34的第二液相出口之间的管路上安装有能将物料从第二分层罐34的第二液相出口输送到皂化塔32的回流入口的第四输送泵322;
[0088]
粗环氧氯丙烷储罐35的物料入口连通粗环氧氯丙烷储罐35的第一液相出口;
[0089]
闪蒸罐36的液相入口连通皂化塔32的液相出口;具体地,闪蒸罐36的液相入口与皂化塔32的液相出口之间的管路上安装有能将物料从皂化塔32的液相出口输送到闪蒸罐36的液相入口的第五输送泵361;皂化塔32液相出口排出的氯化钙母液固含量大,用冷却器冷却极易堵塞,此处通过真空闪蒸冷却,从而保证系统稳定运行;
[0090]
第二冷却器37的液相入口连通闪蒸罐36的液相出口,第二冷却器37的液相出口连接至氯化钙预处理单元371;以及
[0091]
第四冷凝器38的气相入口连通闪蒸罐36的气相出口,第四冷凝器38的气相出口连接有第三真空泵381,第四冷凝器38的液相出口连接至污水处理单元382。
[0092]
本发明还提供了一种应用有上述环氧氯丙烷生产装置的环氧氯丙烷生产工艺。
[0093]
实施例1:
[0094]
第一步,甘油氯化:控制预反应塔12操作压力为50kpa,原料储罐11中的甘油催化
剂溶液送入预反应塔12中与来自各反应釜未反应完的氯化氢以及解析塔21解析出来的氯化氢进行预反应,反应后的料液同时送入一段反应釜13、二段反应釜14和三段反应釜15中,氯化氢管路10将氯化氢以6:4:0的比率分别送入一段反应釜13、二段反应釜14和三段反应釜15,一段反应釜13的料液利用压力差进入二段反应釜14,二段反应釜14的料液利用压力差进入三段反应釜15,三段反应釜15反应完毕的粗二氯丙醇送入解析塔21,一段反应釜13未反应完的氯化氢进入二段反应釜14,二段反应釜14未反应完的氯化氢进入三段反应釜15,三段反应釜15未反应完的氯化氢送入预反应塔12;
[0095]
第二步,二氯丙醇精制:控制解析塔21的操作压力为0.25mpa,解析塔21对粗二氯丙醇进行解析,解析出来的气相送入预反应塔12,解析后的粗二氯丙醇送入精馏塔22,精馏塔22顶部气相出口排出的不凝气经甘油吸收器23降膜吸收后,气相进入第一冷却器24进一步冷凝,液相则送入预反应塔12;第一冷却器24冷凝后的气相分为两部分,一部分通过喷射器25抽出,一部分进入碱洗塔26后经第一真空泵261抽出,冷凝后的液相流进入第一分层罐27;从精馏塔22出来的重组分同样进入第一分层罐27,第一分层罐27分层后的重部分送往二氯丙醇回收塔28回收其中的二氯丙醇,分层后的轻组分则返回各反应釜重新反应;精馏塔22侧线出料为精二氯丙醇;
[0096]
第三步,二氯丙醇皂化:自精馏塔22输送来的精二氯丙醇与由碱液罐31来的碱液混合后进入皂化塔32的第二块塔板上,热水管路30的热水进入皂化塔32的第一块塔板进行冲洗;在皂化塔32内生成的环氧氯丙烷随汽提蒸汽蒸出后进入第三冷凝器33,冷凝后的不凝气由第二真空泵331抽出,冷凝液进入第二分层罐34;冷凝液在第二分层罐34中分层分离,分层后的重组分为粗环氧氯丙烷,送往粗环氧氯丙烷储罐35等待进一步精制,分层后的轻组分为水,送回皂化塔32;皂化塔32的釜液送入闪蒸罐36,闪蒸后的液相送入第二冷却器37冷却后送往氯化钙预处理单元371,闪蒸后的气相送入第四冷凝器38,冷凝后的不凝气由第三真空泵381抽出,冷凝液送至污水处理单元382;
[0097]
对三段反应釜15液相出口物料进行检测,记录一氯丙二醇、二氯丙醇的含量。
[0098]
实施例2:
[0099]
与实施例1的不同之处在于:第一步中,氯化氢管路10将氯化氢以8:1:1的比率分别送入一段反应釜13、二段反应釜14和三段反应釜15。
[0100]
实施例3:
[0101]
与实施例1的不同之处在于:第一步中,氯化氢管路10将氯化氢以6:3:1的比率分别送入一段反应釜13、二段反应釜14和三段反应釜15。
[0102]
实施例4:
[0103]
与实施例1的不同之处在于:第一步中,氯化氢管路10将氯化氢以5:5:0的比率分别送入一段反应釜13、二段反应釜14和三段反应釜15。
[0104]
实施例5:
[0105]
与实施例1的不同之处在于:第二步中,解析塔21的操作压力为0.15mpa;
[0106]
实施例6:
[0107]
与实施例1的不同之处在于:第二步中,解析塔21的操作压力为0.30mpa;
[0108]
比较例1:
[0109]
与实施例1的不同之处在于:第一步中,氯化氢管路10将氯化氢以5:3:2的比率分
别送入一段反应釜13、二段反应釜14和三段反应釜15。
[0110]
比较例2:
[0111]
与实施例1的不同之处在于:第二步中,解析塔21的操作压力为50kpa;
[0112]
比较例3:
[0113]
与实施例1的不同之处在于:第二步中,解析塔21的操作压力为0.35mpa;
[0114]
上述所有实施例和比较例的性能测试结果如表1所示。
[0115][0116]
由表1可以看出:
[0117]
(1)从实施例1~4和比较例1可以看出,将合适比率的氯化氢分别送入一段反应釜13、二段反应釜14和三段反应釜15中,可以确保三段反应釜15中一氯丙二醇含量小于1%,减少皂化塔氯化钙母液一氯丙二醇和cod的含量;
[0118]
(2)从实施例1、实施例5、实施例6、比较例2和比较例3可以看出,通过提高解析塔21的操作压力可以让解析塔21中三元共沸物中的氯化氢更多地解析出来,但是操作压力过大会导致回收的一氯丙二醇变少,使得一氯丙二醇会和二氯丙醇一起进入精馏塔22,因此需要合理控制解析塔21的操作压力;
[0119]
另外,将解析塔21的操作压力控制在0.15~0.30mpa,还起到了额外的作用:一方面,可以保证解析塔解析出氯化氢可以自流回收至预反应塔,减小能耗;另一方面,因为解析塔正压,精馏塔负压,解析塔的物料可以自流去精馏塔,减小能耗。
起点商标作为专业知识产权交易平台,可以帮助大家解决很多问题,如果大家想要了解更多知产交易信息请点击 【在线咨询】或添加微信 【19522093243】与客服一对一沟通,为大家解决相关问题。
此文章来源于网络,如有侵权,请联系删除



tips