一种2,4-二硝基氯苯的连续生产方法与流程



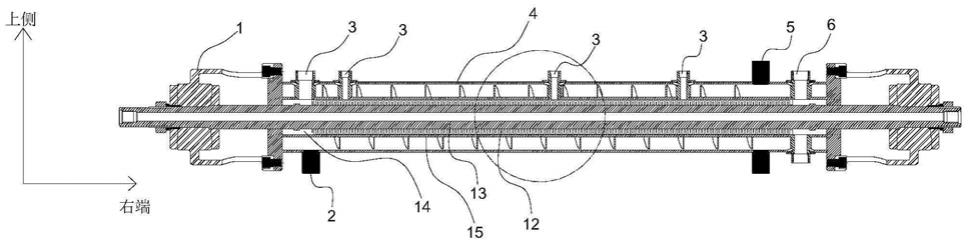
[0001]
本发明涉及生物医药领域,更具体地,涉及一种2,4-二硝基氯苯的连续生产方法。
背景技术:
[0002]
2,4-二硝基氯苯是一种重要的化工原料,其广泛应用于医药、农药、染料、炸药、化学助剂等领域。随着国内化工行业的不断发展,2,4-二硝基氯苯的市场需求也越来越大。2,4-二硝基氯苯的主要生产方式是传统的釜式硝化合成工艺,这种合成工艺是将氯苯与混酸按照一定的比加入反应釜中进行充分反应而得到产物,可分为“一步法合成”和“两步法合成”。“一步法合成”,是指在硝化釜中加入氯苯,然后在持续搅拌下,按摩尔比缓慢滴加混酸(h
2
so
4-hno
3
),加料时温度控制在55℃。加料完毕,逐渐升温到80~90℃,保持1h左右,待反应结束后静置分层,上层有机相用碱液和水洗至ph=7左右,然后冷却、结晶、干燥得到产品的方法。“两步法合成”,是指在硝化釜中加入氯苯,然后在持续搅拌下,按摩尔比缓慢滴加混酸(h
2
so
4-hno
3
),加料时温度控制在55℃。加料完毕,逐渐升温到65℃,保持3h,反应结束静置分层。上层有机相通入到二硝化反应釜中,在持续搅拌下缓慢滴加硝酸(hno
3
),加料完毕升温到80℃并维持1h,待反应结束后静置分层,上层有机相用碱液和水洗至ph=7左右然后冷却、结晶、干燥得到产品的合成方法。
[0003]
传统的间歇式硝化法采用釜式批量生产,生产技术较落后,反应速度慢,周期长,规模小,导致生产效率不高,反应条件控制不稳定,副反应复杂,产品品质低,混酸用量大,废酸和有机废液产量大,严重污染环境,不符合“绿色化学”的要求,且操作不当很容易引发爆炸事故,因此,硝化工艺的审批和生产受到了严重的制约。
[0004]
为了克服间歇式硝化法的缺点,连续硝化法的研究逐渐被重视起来。目前连续硝化反应装置主要有串联釜式、静态管式和循环回路式等类型。近几年备受关注的微化工技术,为现代绿色工业提供了新的方向,也逐渐成为新的研究热点。微反应系统的原理是将反应物料微量化、反应过程精细化、反应生产连续化,以高效传热为依托,保障稳定的反应环境;反应通道微细化的结构,保证高效的传质效率。
[0005]
中国专利“一种二硝基氯苯的合成方法及微反应器”(公开号:cn101544568,公开日2008.03.28)公开了一种二硝基氯苯的合成方法及微反应器该法以氯苯和硝酸/硫酸(n/s)的混合酸为起始反应物料,物料流由计量泵同步输入到微反应器中,并在反应通道内完成混合传质及反应过程。所用微通道反应器采取不锈钢平板结构,包括:固定压封板、微通道板、原料入口和产物出口及位于两块封板上的温控孔道与热偶测控插孔。这种微反应器和二硝基氯苯的合成方法基本实现了微反应合成二硝基氯苯,但由于这种微反应器内设置多条微通道,在反应过程中容易存在混合不均匀,换热效果相对较差以及容易产生返混现象,导致反应器不同位置反应速率不一致,令传质速度及产物收率受到影响。
技术实现要素:
[0006]
本发明旨在克服上述现有技术的至少一种缺陷(不足),提供一种2,4-二硝基氯苯
的连续生产方法,用于消除合成2,4-二硝基氯苯过程中局部返混,提供高效的传质优势,以提高2,4-二硝基氯苯的收率,容易实现工业化放大生产,且提供高效换热和微量连续化,实现了硝化工艺的稳定控制,减少副产物的产生。
[0007]
本发明采取的技术方案是:一种2,4-二硝基氯苯的连续生产方法,包括以下步骤:
[0008]
s1混酸配制:边搅拌边往硫酸内缓慢滴加硝酸,混合均匀后得混酸溶液。
[0009]
s2连续硝化:将氯苯和步骤s1配制的部分混酸溶液从平置的管式反应器的一端注入其反应腔,在垂直管式反应器轴向的搅拌柱的搅动下发生反应,混酸溶液和氯苯的注入推动反应腔中的混酸溶液和氯苯边混合反应边向管式反应器的另一端前进,将剩余混酸溶液从管式反应器中部注入反应腔,与反应腔中的混酸溶液和氯苯继续混合反应并前进至管式反应器另一端排出。
[0010]
s3收集产物:收集步骤s2排出的物料并将收集的物料进行冷却,萃取,洗涤有机相至中性后干燥得到所述2,4-二硝基氯苯。
[0011]
进一步地,氯苯、硝酸和硫酸的摩尔配比为氯苯:硝酸:硫酸=1:2~4:5~6。
[0012]
进一步地,硫酸的质量浓度为80~98wt%。
[0013]
优选地,硫酸的质量浓度为98wt%,硝酸的质量浓度为65wt%,氯苯、65wt%硝酸和98wt%硫酸的摩尔配比为氯苯:硝酸:硫酸=1:2.5:5。
[0014]
进一步地,在步骤s2中,反应温度为80~140℃。优选地,在步骤s2中,反应温度为110℃。优选地,反应温度由包绕反应腔的换热流体控制。
[0015]
在本技术方案中,通过换热流体包裹反应腔控制反应温度,能更好的进行换热,使反应腔内各个部分的温度梯度更小,有利于控制反应速度,防止局部反应过热。
[0016]
进一步地,在步骤s2中,反应时间为2~6min。优选地,在步骤s2中,反应时间为6min。
[0017]
进一步地,所述搅拌柱绕管式反应器轴向转动的转速为300r/min。优选地,所述搅拌柱绕管式反应器轴向转动的转速为200~400r/min。
[0018]
在传统的反应器中,一般设置挡板实现隔离反应前后的物料,以提高产率,但是挡板往往不利于传质,因此在本技术方案中,通过控制搅拌柱转速替代挡板实现隔离反应前后物料,从而既实现隔离又提供较大的比表面积利于传质,使隔离与传质的矛盾问题迎刃而解,进一步优化产品产率;而且垂直于转动轴上的搅拌柱在切向方向对物料进行搅拌,使物料混合更均匀且不会使物料产生向前或向后的推动力,有效避免物料产生返混现象。
[0019]
进一步地,在步骤s2中,将90%的混酸溶液从管式反应器的一端注入,剩余10%混酸溶液从管式反应器的中部注入。
[0020]
在本技术方案中,通过多位点注入混酸溶液,可以优化反应腔内局部体积配比,促进混合传质效果,从而优化物料用量配比,减少混酸溶液用量,符合“绿色化学”的要求,而且由于进行硝化反应时放出大量热量,与单位点注入混酸溶液相比,多位点注入混酸溶液可以分散反应热,促进换热效率,减少副产物,另外在工业放大化生产时,单位点注入混酸溶液容易使反应腔内部压力过大,长期使用容易损坏设备,而采用多位点进料尽量则可以避免上述问题,延长设备寿命。
[0021]
进一步地,在步骤s3中,用二氯甲烷、二氯乙烷、苯、氯仿中的任一种萃取溶剂进行萃取。
[0022]
进一步地,在步骤s3中,用氯化钙干燥。
[0023]
与现有技术相比,本发明的有益效果为:
[0024]
(1)氯苯和混酸溶液微量连续反应,实现了硝化工艺的稳定控制,生产更安全;
[0025]
(2)氯苯硝化时间短,提高生产效率;
[0026]
(3)垂直管式反应器轴向的搅拌柱搅拌反应物料,既实现隔离又利于传质,提高产品产率;
[0027]
(4)垂直于转动轴上的搅拌柱在切向方向对物料进行搅拌,物料混合更均匀,对物料无推动作用,有效避免物料产生返混现象;
[0028]
(5)换热流体包裹反应腔控制反应温度,传热效率高,有利于控制反应速度,避免局部反应过热;
[0029]
(6)多位点注入混酸溶液,减少混酸溶液用量,工艺环保,还可以分散反应热,促进换热效率,减少副产物,提高产品产率,延长设备寿命。
附图说明
[0030]
图1为本发明2,4-二硝基氯苯的连续生产所采用的管式反应器的轴向剖视图。
[0031]
图2为本发明2,4-二硝基氯苯的连续生产所采用的管式反应器的轴向剖视图的局部放大图。
[0032]
附图中标记为:1-旋转动力组件;2-换热流体进口;3-原料进料口;4-换热夹套;5-换热流体出口;6-反应产物出料口;12-搅拌柱;13-中空转动轴;14-反应腔;15-反应器壳体。
具体实施方式
[0033]
本发明附图仅用于示例性说明,不能理解为对本发明的限制。为了更好说明以下实施例,附图某些部件会有省略、放大或缩小,并不代表实际产品的尺寸;对于本领域技术人员来说,附图中某些公知结构及其说明可能省略是可以理解的。
[0034]
如图1和图2所示,本发明的一种2,4-二硝基氯苯的连续生产方法采用的所述管式反应器平置,包括反应器壳体15、设于反应器壳体内的中空转动轴13、用于连接中空转动轴13与反应器壳体15的旋转动力组件1以及设于反应器壳体外壁面上的进出料口组件,在反应器壳体15外还设置换热部件;所述的中空转动轴13外壁面上垂直设有若干搅拌柱12;所述的反应器壳体15内壁面与中空转动轴13的外壁面之间形成反应腔14。
[0035]
进出口组件包括多个原料进料口3和反应产物出料口6,多个进料口可以实现多位点进料,分批分散进料,用于促进混合传质效果,优化物料配比,减轻内部压力;中空转动轴13用于内部换热,换热部件包括换热夹套4、换热流体入口2和换热流体出口5,所述的换热流体入口2布置在换热夹套4的下侧左端,所述的换热流体出口5布置在换热夹套4的上侧右端,使用时换热流体从换热流体入口2注入,从换热流体出口排出,使换热流体包裹反应腔,进行外部换热,换热流体流向为从第一个原料进料口2至反应产物出料口6,这样的流向适应连续反应的放热规律,更有利于反应换热,从而更好控制反应温度,反应空间内外双面换热,使反应腔内各个部分的温度梯度更小,具有非常高的传热效率,有利于控制反应速度,防止局部反应过热;旋转动力组件1固定中空转动轴13并为其提供转动动力,中空转动轴13
用于带动搅拌柱12,搅拌柱12垂直设置于中空转动轴13的外壁面,可随着中空转动轴13的转动在切向方向对物料进行搅拌,使物料混合更均匀,搅拌柱12与中空转动轴13外壁面垂直,在切向方向对物料进行搅拌,不会使物料产生向前或向后的推动力,物料主要由新物料不断注入而产生的推动力进行推动,以消除物料的返混现象,通过控制搅拌柱12转速可以替代传统不利于传质的隔离挡板,实现对反应物料隔离的同时又利于传质,以进一步提高产物的产率。
[0036]
本发明提出的一种2,4-二硝基氯苯的连续生产方法,包括以下步骤:
[0037]
s1混酸配制:根据摩尔配比和物料浓度,称取物料;边搅拌边往硫酸内缓慢滴加硝酸,混合均匀后得混酸溶液。
[0038]
s2连续硝化:反应器提前预热,反应温度控制在80~140℃,用恒流泵将氯苯从平置的管式反应器的左端第一个原料进料口3注入其反应腔14后,用另一恒流泵将步骤s1配制的90%的混酸溶液从平置的管式反应器的左端第一个原料进料口3注入其反应腔14,在垂直管式反应器轴向的搅拌柱12的搅动下发生反应,搅拌转速控制在200~400r/min,混酸溶液和氯苯的注入推动反应腔14中的混酸溶液和氯苯边混合反应边向管式反应器反应产物出料口6前进,用恒流泵将剩余10%的混酸溶液从管式反应器中间的第三个原料进料口3注入反应腔14,与反应腔14中的混酸溶液和氯苯继续混合反应并前进,在反应器内停留2~6min后,反应腔14内物料前进至管式反应器的反应产物出料口6排出。
[0039]
s3收集产物:收集步骤s2排出的物料并将收集的物料进行冷却,萃取,洗涤有机相至中性后干燥得到所述2,4-二硝基氯苯。
[0040]
实施例1
[0041]
在本实施例中,按照上述方法的步骤进行2,4-二硝基氯苯的连续生产,选用质量浓度为65wt%的硝酸、85wt%的硫酸配制混酸溶液,氯苯、硝酸和硫酸的摩尔配比为氯苯:硝酸:硫酸=1:2.5:5;在步骤s2中,反应温度控制在130℃,控制搅拌转速在200r/min,反应物料在反应器内停留2min。
[0042]
所得产物用气相色谱分析后得目标产物2,4-二硝基氯苯含量53.71%,硝基氯苯总含量44.45%,二硝基氯苯副产物1.16%。
[0043]
实施例2
[0044]
在本实施例中,按照上述方法的步骤进行2,4-二硝基氯苯的连续生产,选用质量浓度为65wt%的硝酸、85wt%的硫酸配制混酸溶液,氯苯、硝酸和硫酸的摩尔配比为氯苯:硝酸:硫酸=1:4:5.5;在步骤s2中,反应温度控制在130℃,控制搅拌转速在400r/min,反应物料在反应器内停留6min。
[0045]
所得产物用气相色谱分析后得目标产物2,4-二硝基氯苯含量83.71%,硝基氯苯总含量14.45%,二硝基氯苯副产物2.69%。
[0046]
实施例3
[0047]
在本实施例中,按照上述方法的步骤进行2,4-二硝基氯苯的连续生产,选用质量浓度为65wt%的硝酸、90wt%的硫酸配制混酸溶液,氯苯、硝酸和硫酸的摩尔配比为氯苯:硝酸:硫酸=1:2:5.5;在步骤s2中,反应温度控制在130℃,控制搅拌转速在200r/min,反应物料在反应器内停留2min。
[0048]
所得产物用气相色谱分析后得目标产物2,4-二硝基氯苯含量77.81%,硝基氯苯
总含量18.85%,二硝基氯苯副产物2.58%。
[0049]
实施例4
[0050]
在本实施例中,按照上述方法的步骤进行2,4-二硝基氯苯的连续生产,选用质量浓度为65wt%的硝酸、90wt%的硫酸配制混酸溶液,氯苯、硝酸和硫酸的摩尔配比为氯苯:硝酸:硫酸=1:3.5:5.5;在步骤s2中,反应温度控制在130℃,控制搅拌转速在400r/min,反应物料在反应器内停留2min。
[0051]
所得产物用气相色谱分析后得目标产物2,4-二硝基氯苯含量88.61%,硝基氯苯总含量8.90%,二硝基氯苯副产物2.77%。
[0052]
实施例5
[0053]
在本实施例中,按照上述方法的步骤进行2,4-二硝基氯苯的连续生产,选用质量浓度为65wt%的硝酸、90wt%的硫酸配制混酸溶液,氯苯、硝酸和硫酸的摩尔配比为氯苯:硝酸:硫酸=1:3.5:5.5;在步骤s2中,反应温度控制在130℃,控制搅拌转速在300r/min,反应物料在反应器内停留3min。
[0054]
所得产物用气相色谱分析后得目标产物2,4-二硝基氯苯含量92.26%,硝基氯苯总含量3.45%,二硝基氯苯副产物2.89%。
[0055]
实施例6
[0056]
在本实施例中,按照上述方法的步骤进行2,4-二硝基氯苯的连续生产,选用质量浓度为65wt%的硝酸、98wt%的硫酸配制混酸溶液,氯苯、硝酸和硫酸的摩尔配比为氯苯:硝酸:硫酸=1:2.5:5;在步骤s2中,反应温度控制在130℃,控制搅拌转速在200r/min,反应物料在反应器内停留2min。
[0057]
所得产物用气相色谱分析后得目标产物2,4-二硝基氯苯含量90.10%,硝基氯苯总含量6.24%,二硝基氯苯副产物3.15%。
[0058]
实施例7
[0059]
在本实施例中,按照上述方法的步骤进行2,4-二硝基氯苯的连续生产,选用质量浓度为65wt%的硝酸、98wt%的硫酸配制混酸溶液,氯苯、硝酸和硫酸的摩尔配比为氯苯:硝酸:硫酸=1:2.5:5;在步骤s2中,反应温度控制在110℃,控制搅拌转速在300r/min,反应物料在反应器内停留4min。
[0060]
所得产物用气相色谱分析后得目标产物2,4-二硝基氯苯含量94.08%,硝基氯苯总含量3.24%,二硝基氯苯副产物1.13%。
[0061]
实施例8
[0062]
在本实施例中,按照上述方法的步骤进行2,4-二硝基氯苯的连续生产,选用质量浓度为65wt%的硝酸、98wt%的硫酸配制混酸溶液,氯苯、硝酸和硫酸的摩尔配比为氯苯:硝酸:硫酸=1:2.5:5;在步骤s2中,反应温度控制在110℃,控制搅拌转速在300r/min,反应物料在反应器内停留6min。
[0063]
所得产物用气相色谱分析后得目标产物2,4-二硝基氯苯含量97.30%,硝基氯苯总含量0.84%,二硝基氯苯副产物1.71%。
[0064]
实施例9
[0065]
在本实施例中,按照上述方法的步骤进行2,4-二硝基氯苯的连续生产,选用质量浓度为65wt%的硝酸、98wt%的硫酸配制混酸溶液,氯苯、硝酸和硫酸的摩尔配比为氯苯:
硝酸:硫酸=1:2.5:5;在步骤s2中,反应温度控制在90℃,控制搅拌转速在300r/min,反应物料在反应器内停留6min。
[0066]
所得产物用气相色谱分析后得目标产物2,4-二硝基氯苯含量78.25%,硝基氯苯总含量19.24%,二硝基氯苯副产物2.03%。
[0067]
实施例10
[0068]
在本实施例中,按照上述方法的步骤进行2,4-二硝基氯苯的连续生产,选用质量浓度为65wt%的硝酸、80wt%的硫酸配制混酸溶液,氯苯、硝酸和硫酸的摩尔配比为氯苯:硝酸:硫酸=1:2.5:6;在步骤s2中,反应温度控制在80℃,控制搅拌转速在400r/min,反应物料在反应器内停留6min。
[0069]
所得产物用气相色谱分析后得目标产物2,4-二硝基氯苯含量91.24%,硝基氯苯总含量5.35%,二硝基氯苯副产物1.67%。
[0070]
实施例11
[0071]
在本实施例中,按照上述方法的步骤进行2,4-二硝基氯苯的连续生产,选用质量浓度为65wt%的硝酸、80wt%的硫酸配制混酸溶液,氯苯、硝酸和硫酸的摩尔配比为氯苯:硝酸:硫酸=1:2:5;在步骤s2中,反应温度控制在140℃,控制搅拌转速在400r/min,反应物料在反应器内停留3min。
[0072]
所得产物用气相色谱分析后得目标产物2,4-二硝基氯苯含量62.85%,硝基氯苯总含量32.38%,二硝基氯苯副产物3.52%。
[0073]
以上所述实施例的各技术特征可以进行任意的组合,为使描述简洁,未对上述实施例中各个技术特征所有可能的组合都进行描述,然而,只要这些技术特征的组合不存在矛盾,都应当认为是本说明书所记载的范围。
[0074]
显然,本发明的上述实施例仅仅是为清楚地说明本发明技术方案所作的举例,而并非是对本发明的具体实施方式的限定。凡在本发明权利要求书的精神和原则之内所作的任何修改、等同替换和改进等,均应包含在本发明权利要求的保护范围之内。
起点商标作为专业知识产权交易平台,可以帮助大家解决很多问题,如果大家想要了解更多知产交易信息请点击 【在线咨询】或添加微信 【19522093243】与客服一对一沟通,为大家解决相关问题。
此文章来源于网络,如有侵权,请联系删除



tips