一种抗滑低冰点型抗凝冰涂层及其制备方法与流程



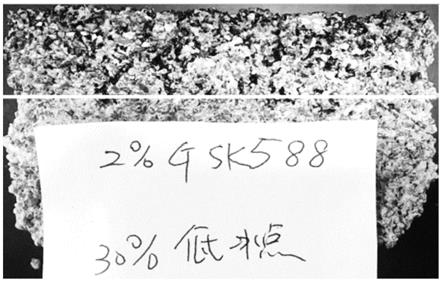
[0001]
本发明属于道路工程技术领域,具体涉及一种抗滑低冰点型抗凝冰涂层及其制备方法。
背景技术:
[0002]
我国广大的北方地区及南方山区道路冬季极易出现积雪结冰,降低了道路附着系数、车辆制动距离延长,且路面积雪遮挡了驾驶员视线,在弯道处极易发生交通事故,威胁人员生命财产安全,同时降低道路运输效率。传统的人工、机械清除冰雪、撒布融雪剂方法,被动不及时,费用高,易污染环境,造成路面损害。流体加热、电加热、热管加热等热力融冰雪技术施工复杂,造价高,维护不便。抗凝冰涂层技术由乳化沥青或者树脂材料作为基体材料,加入低冰点材料、外加剂共混形成,在入冬前喷洒到路面上,利用车辆荷载作用及其他其他外界作用,主动释放降低冰点的物质,减弱冰-路界面的粘结力,可以起到主动预防结冰的效果,施工方便、快捷,且可提高人工、机械除冰雪效率,减少对路面损伤,是一种经济、高效的技术手段,得到了广泛的关注。
[0003]
《一种融雪除冰乳液涂层及其施工方法》(cn110698986a)开发一种由水基胶粘剂、氟树脂乳液、ph调节剂、表面活性剂、增效剂组成的除冰乳液涂层。《一种长效疏水型抑冰涂层及其制备方法》(cn109233600a)开发了一种由聚氨酯、长效疏水抑冰剂和聚氨酯固化剂、水性环氧树脂和水性环氧树脂固化剂及石蜡粉组成了疏水性抑冰涂层。《一种路面融雪化冰涂层及其制备方法》(cn106867361b)开发了一种由环氧树脂、弹性改性剂、环氧活性稀释剂、融雪剂、消泡剂、分散剂、环氧固化剂、固化促进剂、偶联剂、磁铁粉等组成的具有微波辐射致热功能的融雪化冰涂层。《一种长效路面抗凝冰涂层材料及制备方法》(cn111138913a)开发了一种由橡胶粉、工业盐、碳酸钙、硬酸脂和环烷油组成的抗凝冰涂层。《一种环保型路面融冰雪涂层材料及其制备方法和使用方法》(cn102199398a)开发了一种由融雪物质、水性环氧树脂、乳化沥青和水性环氧树脂固化剂组成的环保型融冰雪涂层。这些产品大都采用乳化沥青或者环氧树脂作为载体,主要关注涂层的疏水效果、环保性能、融冰效果等,而忽略的涂层材料本身的渗透性能,导致涂层喷洒在路表面后,不能快速渗入裂缝及纹理中,导致路面抗滑性能急剧衰减,影响行车安全,特别是山区公路,长大下坡多,影响了涂层材料的推广应用。此外,由于低冰点材料颗粒比乳化沥青、环氧树脂大的多,加入后会影响体系的稳定,限制了低冰点材料颗粒的掺量,影响的抗凝冰效果。
[0004]
低冰点材料具有一定憎水作用且粒径大于乳化沥青,加入乳化沥青基体材料后,导致体系颗粒粒径大幅增加,超过一定量后,体系开始不稳定,粘度急剧增加而丧失工作性,涂层停留在沥青路面表面,无法渗入纹理结构中,导致路面抗滑性能急剧降低,威胁行车安全。
技术实现要素:
[0005]
针对现有技术中抗凝冰涂层渗透性和体系稳定性差,导致路面抗滑性能急剧降
低,威胁行车安全的问题,本发明提供一种抗滑低冰点型抗凝冰涂层及其制备方法,其目的在于:优化涂层渗透性及体系稳定性,在改善涂层渗透性的同时,提高低冰点材料的掺量,在涂层抗滑性能与抗凝冰效果之间取得平衡,兼顾长效性与安全性。
[0006]
本发明采用的技术方案如下:
[0007]
一种抗滑低冰点型抗凝冰涂层,包括乳化沥青、低冰点材料和润湿剂,所述乳化沥青、低冰点材料和润湿剂的质量比为1:0.2~0.4:0.02~0.03。
[0008]
作为优选,所述乳化沥青中各组分的质量百分比为:石油沥青40%~50%,水46.5%~58%,乳化剂2%~3%,ph助剂0%~0.5%。
[0009]
作为优选,所述石油沥青针入度分级60-80。
[0010]
作为优选,所述乳化剂为阳离子中裂型乳化剂。
[0011]
作为优选,所述ph助剂为盐酸、磷酸、甲酸或醋酸的一种。
[0012]
作为优选,所述低冰点材料含有无机或有机融雪抑冰成分,粒径小于0.075mm,经过憎水处理,具有缓释作用。
[0013]
作为优选,所述润湿剂为硅醇类非离子表面活性剂。
[0014]
一种抗滑低冰点型抗凝冰涂层的制备方法,包括以下步骤:
[0015]
s1:将乳化剂、水按比例配制成皂液;
[0016]
s2:用ph助剂将皂液的ph值调整为2~4之间,并加热至50~60℃;
[0017]
s3:按照比例称取石油沥青,并将石油沥青加热至140~145℃;
[0018]
s4:将皂液加入胶体磨中,然后加入140~145℃的石油沥青与皂液混合,混合物经高速剪切80~90s后得到乳化沥青;
[0019]
s5:待乳化沥青冷却后,按比例加入润湿剂,搅拌2~5min,得到高渗透乳化沥青;
[0020]
s6:按比例称取低冰点材料,分两到三次加入高渗透乳化沥青中,每次加入低冰点材料后搅拌2~5min,得到抗滑低冰点型抗凝冰涂层。
[0021]
综上所述,由于采用了上述技术方案,本发明的有益效果是:
[0022]
1.通过优选阳离子乳化剂及其掺量、固含量,调整乳化沥青体系粒径和粘度,确定高渗透乳化沥青配方,使乳化沥青体系的粒径、粘度更小,降低乳液液滴之间的摩阻力,从而具有更优异的渗透性,提高路面抗滑性能,保证行车安全。
[0023]
2.加入聚醚硅醇类非离子润湿剂,动、静态表面张力极低,含双羟基,不参与体系的化学反应,降低乳化沥青体系表面能,使乳化沥青能快速润湿低冰点材料,从而稳定共存,硅醇类非离子润湿剂化学性质为惰性,耐酸碱性强,使低冰点材料、沥青、水体系更加稳定,在维持涂层渗透性同时,有效提高低冰点材料掺量、降低路面的冰点,提高涂层的耐久性能,兼顾施工性、抗滑安全性及抗凝冰效果。
[0024]
3.优化配方后的涂层渗透深度大,喷涂在路表面后摩擦系数更大、冰点更低,兼顾抗滑安全性及抗凝冰效果。
附图说明
[0025]
本发明将通过例子并参照附图的方式说明,其中:
[0026]
图1是实施例2的接触角;
[0027]
图2是实施例6的接触角;
[0028]
图3是实施例7的接触角;
[0029]
图4是实施例8的接触角;
[0030]
图5是添加润湿剂后的渗透深度;
[0031]
图6是不添加润湿剂的渗透深度。
具体实施方式
[0032]
为使本申请实施例的目的、技术方案和优点更加清楚,下面将结合本申请实施例中附图,对本申请实施例中的技术方案进行清楚、完整地描述,显然,所描述的实施例仅仅是本申请一部分实施例,而不是全部的实施例。通常在此处附图中描述和示出的本申请实施例的组件可以以各种不同的配置来布置和设计。因此,以下对在附图中提供的本申请的实施例的详细描述并非旨在限制要求保护的本申请的范围,而是仅仅表示本申请的选定实施例。基于本申请的实施例,本领域技术人员在没有做出创造性劳动的前提下所获得的所有其他实施例,都属于本申请保护的范围。
[0033]
下面结合图1~图6对本发明作详细说明。
[0034]
实施例1
[0035]
称取水488g、乳化剂10g、盐酸2g,充分混合并加热至55℃制得皂液。将皂液倒入胶体磨中,然后称取温度为142.5℃的70号石油沥青500g,倒入胶体磨中与皂液进行混合,混合物经高速剪切85s后得到乳化沥青,主要技术指标见表1。
[0036]
实施例2
[0037]
称取水478g,乳化剂20g,盐酸2g,充分混合并加热至55℃制得皂液。将皂液倒入胶体磨中,然后称取温度为142.5℃的70号石油沥青500g,倒入胶体磨中与皂液进行混合,混合物经高速剪切85s后得到乳化沥青,主要技术指标见表1。
[0038]
实施例3
[0039]
称取水468g,乳化剂30g,盐酸2g,充分混合并加热至55℃制得皂液。将皂液倒入胶体磨中,然后称取温度为142.5℃的70号石油沥青500g,倒入胶体磨中与皂液进行混合,混合物经高速剪切85s后得到乳化沥青,主要技术指标见表1。
[0040]
实施例4
[0041]
称取水578g,乳化剂20g,盐酸2g,充分混合并加热至55℃制得皂液。将皂液倒入胶体磨中,然后称取温度为142.5℃的70号石油沥青400g,倒入胶体磨中与皂液进行混合,混合物经高速剪切85s后得到乳化沥青,主要技术指标见表1。
[0042]
实施例5
[0043]
称取水378g,乳化剂20g,盐酸2g,充分混合并加热至55℃制得皂液。将皂液倒入胶体磨中,然后称取温度为142.5℃的70号石油沥青600g,倒入胶体磨中与皂液进行混合,混合物经高速剪切85s后得到乳化沥青,主要技术指标见表1。
[0044]
表1 高渗透乳化沥青实施例
[0045]
实施例平均粒径/μm粘度/(mpa
·
s)渗透深度/mm12.47426.755.822.11917.2512.932.09816.7517.0
41.8827.4224.955.67536.545.5
[0046]
从表1可以看出,对比实施例1~3,乳化剂的掺量增加,可以显著降低乳化沥青粒径分布范围及平均粒径(粒径测试采用济南润之rise-2002激光粒度仪测试),从而使乳化沥青的粘度降低,渗透性能提高。考虑经济性,优选乳化剂掺量2%~3%。
[0047]
从表1中还可以看出,对比实施例2、实施例4和实施例5,随着固含量(即石油沥青的含量)增加,乳化沥青粒径分布范围及平均粒径不段增大,特别是固含量由50%增加到60%时,平均粒径增大了1.7倍,粘度急剧增大,渗透性能大幅衰减。为保证渗透深度及涂层耐久性,固含量宜为40%~50%。
[0048]
实施例6
[0049]
称取水578g,乳化剂20g,盐酸2g,充分混合并加热至55℃制得皂液。将皂液倒入胶体磨中,然后称取温度为142.5℃的70号石油沥青400g,倒入胶体磨中与皂液进行混合,混合物经高速剪切85s后得到乳化沥青,冷却后,加入10g润湿剂,搅拌2min,得到高渗透乳化沥青,主要技术指标见表2。
[0050]
实施例7
[0051]
称取水578g,乳化剂20g,盐酸2g,充分混合并加热至55℃制得皂液。将皂液倒入胶体磨中,然后称取温度为142.5℃的70号石油沥青400g,倒入胶体磨中与皂液进行混合,混合物经高速剪切85s后得到乳化沥青。乳化沥青冷却后,加入20g润湿剂,搅拌2min,得到高渗透乳化沥青,主要技术指标见表2。
[0052]
实施例8
[0053]
称取水578g,乳化剂20g,盐酸2g,充分混合并加热至55℃制得皂液。将皂液倒入胶体磨中,然后称取温度为142.5℃的70号石油沥青400g,倒入胶体磨中与皂液进行混合,混合物经高速剪切85s后得到乳化沥青。乳化沥青冷却后,加入30g润湿剂,搅拌2min,得到高渗透乳化沥青,主要技术指标见表2。
[0054]
表2 润湿剂对乳化沥青影响
[0055]
实施例平均粒径/μm粘度/(mpa
·
s)接触角渗透深度/mm22.11917.2553.06512.962.11617.5016.87227.272.11820.2513.0731.482.11919.2511.63930.8
[0056]
对比实例2、实例6~8,可以看出,随着润湿剂掺量增加,乳化沥青粒径基本保持不变,粘度小幅增大,但乳化沥青接触角大大降低(采用广东艾斯瑞asr-705sb接触角测试仪测试接触角),即降低了乳化沥青的表面能。因此,将本发明的乳化沥青涂刷到路表面,可以快速润湿路面,从而大大增加了渗透深度,最大渗透深度可达30.8mm,与实施例2中不添加润湿剂相比,渗透深度增加了138.8%。
[0057]
加入润湿剂后,涂层体系的粘度大幅降低,涂层的渗透深度大幅增加,且随低冰点材料掺量增大,增加幅度越来越大,可有效增加低冰点材料掺量至40%。
[0058]
实施例9
[0059]
称取水578g,乳化剂20g,盐酸2g,充分混合并加热至55℃制得皂液。将皂液倒入胶
体磨中,然后称取温度为142.5℃的70号石油沥青400g,倒入胶体磨中与皂液进行混合,混合物经高速剪切85s后得到乳化沥青。乳化沥青冷却后,加入100g低冰点材料搅拌5min得到抗凝冰涂层,主要技术指标见表3。
[0060]
实施例10
[0061]
称取水578g,乳化剂20g,盐酸2g,充分混合并加热至55℃制得皂液。将皂液倒入胶体磨中,然后称取温度为142.5℃的70号石油沥青400g,倒入胶体磨中与皂液进行混合,混合物经高速剪切85s后得到乳化沥青。乳化沥青冷却后,加入200g低冰点材料搅拌5min得到抗凝冰涂层,主要技术指标见表3。
[0062]
实施例11
[0063]
称取水578g,乳化剂20g,盐酸2g,充分混合并加热至55℃制得皂液。将皂液倒入胶体磨中,然后称取温度为142.5℃的70号石油沥青400g,倒入胶体磨中与皂液进行混合,混合物经高速剪切80s后得到乳化沥青。乳化沥青冷却后,加入20g润湿剂,搅拌2min,得到高渗透乳化沥青,然后向高渗透乳化沥青中加入100g低冰点材料搅拌5min得到抗凝冰涂层,主要技术指标见表3。
[0064]
实施例12
[0065]
称取水578g,乳化剂20g,盐酸2g,充分混合并加热至55℃制得皂液。将皂液倒入胶体磨中,然后称取温度为142.5℃的70号石油沥青400g,倒入胶体磨中与皂液进行混合,混合物经高速剪切85s后得到乳化沥青。乳化沥青冷却后,加入20g润湿剂,搅拌2min,得到高渗透乳化沥青,然后向高渗透乳化沥青中加入200g低冰点材料搅拌5min得到抗凝冰涂层,主要技术指标见表3。
[0066]
实施例13
[0067]
称取水578g,乳化剂20g,盐酸2g,充分混合并加热至55℃制得皂液。将皂液倒入胶体磨中,然后称取温度为142.5℃的70号石油沥青400g,倒入胶体磨中与皂液进行混合,混合物经高速剪切85s后得到乳化沥青。乳化沥青冷却后,加入20g润湿剂,搅拌2min,得到高渗透乳化沥青,然后向高渗透乳化沥青中加入300g低冰点材料搅拌5min得到抗凝冰涂层,主要技术指标见表3。
[0068]
实施例14
[0069]
称取水578g,乳化剂20g,盐酸2g,充分混合并加热至55℃制得皂液。将皂液倒入胶体磨中,然后称取温度为142.5℃的70号石油沥青400g,倒入胶体磨中与皂液进行混合,混合物经高速剪切85s后得到乳化沥青。乳化沥青冷却后,加入20g润湿剂,搅拌2min,得到高渗透乳化沥青,然后向高渗透乳化沥青中加入400g低冰点材料搅拌5min得到抗凝冰涂层,主要技术指标见表3。
[0070]
实施例15
[0071]
称取水578g,乳化剂20g,盐酸2g,充分混合并加热至55℃制得皂液。将皂液倒入胶体磨中,然后称取温度为142.5℃的70号石油沥青400g,倒入胶体磨中与皂液进行混合,混合物经高速剪切85s后得到乳化沥青。乳化沥青冷却后,加入20g润湿剂,搅拌2min,得到高渗透乳化沥青,然后向高渗透乳化沥青中加入500g低冰点材料搅拌5min得到抗凝冰涂层,主要技术指标见表3。
[0072]
实施例16
[0073]
称取水578g,乳化剂20g,盐酸2g,充分混合并加热至50℃制得皂液。将皂液倒入胶体磨中,然后称取温度为140℃的70号石油沥青400g,倒入胶体磨中与皂液进行混合,混合物经高速剪切80s后得到乳化沥青。乳化沥青冷却后,加入20g润湿剂,搅拌2min,得到高渗透乳化沥青,然后向高渗透乳化沥青中加入500g低冰点材料搅拌5min得到抗凝冰涂层。
[0074]
实施例17
[0075]
称取水578g,乳化剂20g,盐酸2g,充分混合并加热至60℃制得皂液。将皂液倒入胶体磨中,然后称取温度为145℃的70号石油沥青400g,倒入胶体磨中与皂液进行混合,混合物经高速剪切90s后得到乳化沥青。乳化沥青冷却后,加入20g润湿剂,搅拌5min,得到高渗透乳化沥青,然后向高渗透乳化沥青中加入500g低冰点材料搅拌2min得到抗凝冰涂层。
[0076]
表3 润湿剂对涂层影响
[0077]
实施例粘度/(mpa
·
s)摆值降低率/%渗透深度/mm冰点/℃935.7530.610.1-3.310920.342.54.7-6.0112724.121.4-3.31248.7522.919.6-6.01361.2511.917.8-10.014135.38.315.8-11.115350.129.612.4-11.1
[0078]
从表3中可以看出,对比实例2、实例9~15,不掺加润湿剂时,随着低冰点材料掺量增加,涂层粘度急剧增大,渗透深度快速减小,残留在路表宏观纹理构造中的涂层越多,导致摆值快速下降,20%掺量时,30℃粘度达到0.9pa
·
s,无法通过喷洒方式施工,采用涂刷施工也非常困难,均匀性难以保证,且摆值下降了42.5%,抗滑性能大大降低,不利于行车安全;加入润湿剂后,由于润湿剂对整个体系表面张力的降低,随着低冰点材料掺量增加,粘度增长幅度大幅缩小,渗透深度小幅减小,在50%掺量时仍可渗透12.4mm,摆值降低率先不断减小,而后又开始增大,40%掺量时,下降比例最小,这是因为低冰点材料可在一定程度上增加摩擦系数,但掺量50%时,涂层的渗透性下降过大,会有一部分残留在纹理构造中,对抗滑不利;相同掺量下,掺入润湿剂摆值下降比例小于不掺,且随着低冰点掺量增加,融雪抑冰成分增多,涂层的冰点不断降低,而后趋于稳定,大大改善了抗凝冰的效果。抗滑低冰点型抗凝冰涂层低冰点材料掺量40%时,仍然可以采用喷洒法施工,均匀性更好,冰点可达-11.1℃,且具有优异抗滑性能,兼顾施工性、安全性和抗凝冰效果。涂层冰点测试方法参照jt/t 1239-2019进行。
[0079]
渗透性的评价方法为:
[0080]
步骤1:取水泥混凝土用标准砂,用1.18~2.36mm筛过筛,取1.18~2.36mm部分,烘干后按照砂、水泥、水重量比850:50:55的比例配置砂浆;
[0081]
步骤2:采用马歇尔击实30次后,击实面垫上与试模内径相同的油纸,应保持击实面平整;
[0082]
步骤3:表面用毛刷快速涂刷15g抗滑低冰点型抗凝冰涂层,放置两天后,将试件脱模;
[0083]
步骤4:采用切割机从试件中间切割成两部分,晾干,用钢尺测量乳化沥青渗透深
度,单位mm,保留小数点后一位。
[0084]
涂层抗滑性能测试方法为:
[0085]
步骤1:采用jtg f40 ac-13型级配中值,按照最佳沥青用量成型300mm
×
300mm
×
50mm尺寸车辙试件;
[0086]
步骤2:参照jtg 3450—2019 t0964方法,采用摆氏摩擦仪测试车辙板摆值,并进行温度修正,记为bpn
前
。
[0087]
步骤3:按照0.3kg/m2用量,在车辙试件表面均匀涂刷抗凝冰涂层材料,待涂层完全干固后,按照步骤2测试摆值,并进行温度修正,记为bpn
后
。
[0088]
步骤4:计算摆值降低率
△
bpn,计算公式如下:
[0089]
△
bpn=(bpn
前-bpn
后
)
×
100%/bpn
后
[0090]
以上所述实施例仅表达了本申请的具体实施方式,其描述较为具体和详细,但并不能因此而理解为对本申请保护范围的限制。应当指出的是,对于本领域的普通技术人员来说,在不脱离本申请技术方案构思的前提下,还可以做出若干变形和改进,这些都属于本申请的保护范围。
起点商标作为专业知识产权交易平台,可以帮助大家解决很多问题,如果大家想要了解更多知产交易信息请点击 【在线咨询】或添加微信 【19522093243】与客服一对一沟通,为大家解决相关问题。
此文章来源于网络,如有侵权,请联系删除



tips