陶瓷复合雾化器及其制造方法与流程



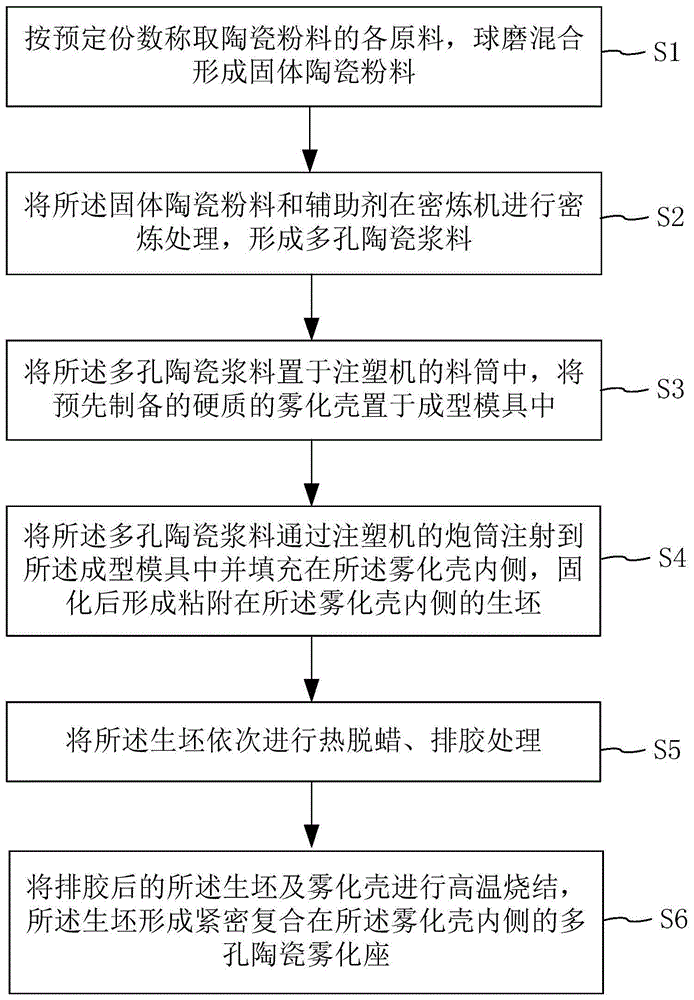
本发明涉及电子烟技术领域,尤其涉及一种陶瓷复合雾化器及其制造方法。
背景技术:
目前市场中,电子烟的陶瓷雾化器的主要形式为金属印刷线路陶瓷雾化芯和金属贴合陶瓷雾化芯,主要工艺为热压铸注浆成型和干压成型两种工艺路线。基于产品的特殊形貌及产品型号功能和成本的需要,干压工艺制备陶瓷雾化芯仅有个别厂家,且该工艺仅能采用厚膜印刷发热形式,综合成本高、良率低,不具有明显的竞争力。电子烟陶瓷雾化芯主流生产工艺,多采用热压铸注浆成型工艺,在不同型号雾化器生产过程中,具有相对较简单工艺流程,尤其在金属贴合发热形式的陶瓷雾化芯结构中,具有很高的生产良率和低成本优势,但热压铸工艺过程,生产工序中需要采用氧化铝埋粉处理,若生产环节处理不稳定,容易出现陶瓷雾化器粉体附着现象,同时,陶瓷雾化芯结构的低强度造成的装配破损容易导致烟弹漏油问题。
技术实现要素:
本发明要解决的技术问题在于,针对上述提出的现有技术缺陷,提供一种低成本、高良率的陶瓷复合雾化器的制造方法及制得的陶瓷复合雾化器。
本发明解决其技术问题所采用的技术方案是:提供一种陶瓷复合雾化器的制造方法,包括以下步骤:
s1、按预定份数称取陶瓷粉料的各原料,球磨混合形成固体陶瓷粉料;
s2、将所述固体陶瓷粉料和辅助剂在密炼机进行密炼处理,形成多孔陶瓷浆料;
s3、将所述多孔陶瓷浆料置于注塑机的料筒中,将预先制备的硬质的雾化壳置于成型模具中;
s4、将所述多孔陶瓷浆料通过注塑机的炮筒注射到所述成型模具中并填充在所述雾化壳内侧,固化后形成粘附在所述雾化壳内侧的生坯;
s5、将所述生坯依次进行热脱蜡、排胶处理;
s6、将排胶后的所述生坯及雾化壳进行高温烧结,所述生坯形成紧密复合在所述雾化壳内侧的多孔陶瓷雾化座。
优选地,步骤s1中,所述陶瓷粉料包括原料及其质量份数如下:硅质或铝质的玻璃相陶瓷粉0~99份、碳化硅粉0~99份、高岭土粉0~50份、磷酸盐1~10份、钠盐1~5份以及钾盐1~5份。
优选地,步骤s2中,所述辅助剂包括石蜡、高密度聚乙烯、低密度聚乙烯以及十八酸;
在所述多孔陶瓷浆料中,所述固体陶瓷粉料所占百分比为50-80%,所述石蜡所占百分比分别为8-20%,所述高密度聚乙烯和低密度聚乙烯所占百分比均为1-15%,所述十八酸所占百分比为1-5%。
优选地,步骤s2中,所述密炼处理的温度为160℃-180℃。
优选地,步骤s4中,所述炮筒的温度为120℃-160℃。
优选地,步骤s5中,将所述生坯置于40℃-80℃的白电油中进行热脱蜡处理。
优选地,步骤s6中,所述高温烧结的温度为600℃~1500℃。
优选地,步骤s3还包括:将发热件置于成型模具中并位于所述雾化壳的一端。
本发明还提供一种陶瓷复合雾化器,采用以上任一项所述的制造方法制得;所述陶瓷复合雾化器包括多孔陶瓷雾化座、紧密包覆在所述多孔陶瓷雾化座外侧的硬质的雾化壳;所述多孔陶瓷雾化座的内部中空,形成容置烟液的储液腔。
优选地,所述陶瓷复合雾化器还包括嵌设在所述多孔陶瓷雾化座上的发热件。
本发明的陶瓷复合雾化器,将多孔陶瓷雾化座以注射成型复合在硬质的外壳内侧形成一体,避免了热压铸成型埋粉烧结工序导致的残留粉体现象,实现了低成本、高良率的雾化器的生产;通过雾化壳的高硬度和高强度承受外部压力,避免多孔陶瓷雾化座因受力导致的结构损害,有效防止漏油现象出现。
另外,通过陶瓷粉料的原料选择结合注射成型解决了大颗粒陶瓷粉料在该工艺中胶料分离的技术难点。
附图说明
下面将结合附图及实施例对本发明作进一步说明,附图中:
图1是本发明一实施例的陶瓷复合雾化器的制造流程图;
图2是本发明一实施例的陶瓷复合雾化器的结构示意图;
图3是图2所示陶瓷复合雾化器的分解结构示意图。
具体实施方式
为了对本发明的技术特征、目的和效果有更加清楚的理解,现对照附图详细说明本发明的具体实施方式。
参考图1,本发明一实施例的陶瓷复合雾化器的制造方法,可包括以下步骤:
s1、按预定份数称取陶瓷粉料的各原料,球磨混合形成固体陶瓷粉料。
其中,陶瓷粉料包括原料及其质量份数如下:硅质或铝质的玻璃相陶瓷粉0~99份、碳化硅粉0~99份、高岭土粉0~50份、磷酸盐1~10份、钠盐1~5份以及钾盐1~5份。
将称取的各原料加入到球磨机中,以干法球磨方式将各原料混合均匀。混合时间可为24小时,也可根据实际需要增减。
s2、将固体陶瓷粉料和辅助剂在密炼机进行密炼处理,形成多孔陶瓷浆料。
辅助剂包括石蜡、高密度聚乙烯、低密度聚乙烯以及十八酸。
在多孔陶瓷浆料中,固体陶瓷粉料所占百分比为50-80%,石蜡所占百分比分别为8-20%,高密度聚乙烯和低密度聚乙烯所占百分比均为1-15%,十八酸所占百分比为1-5%。
密炼处理的温度为160℃-180℃,优选170℃。
s3、将多孔陶瓷浆料置于注塑机的料筒中,将预先制备的硬质的雾化壳置于成型模具中。
其中,雾化壳可以采用但不限于氧化铝基、氧化锆基及铝硅基等陶瓷材料制成,也可以是金属材料制成。
该步骤s3还可包括将预先制成的发热件置于成型模具中并位于雾化壳的一端。
s4、将多孔陶瓷浆料通过注塑机的炮筒注射到成型模具中并填充在雾化壳内侧,固化后形成粘附在雾化壳内侧的生坯,发热件嵌设在生坯上。
炮筒的温度为120℃-160℃,可优选140℃,保证浆料有良好的流动性。
多孔陶瓷浆料在成型模具中可以通过自然冷却成型为生坯。
s5、将生坯依次进行热脱蜡、排胶处理。
生坯附着在雾化壳的内侧,因此生坯连带雾化壳一起进行热脱蜡和排胶处理。
热脱蜡处理优选在白电油中进行,生坯连带雾化壳置于40℃-80℃的白电油中实现热脱蜡。热脱蜡时间可为5小时,或根据实际情况增减。
完成热脱蜡后,将生坯连带雾化壳进行排胶处理。排胶温度可为500℃,时间可为15小时。
通过热脱蜡和排胶处理,去除生坯中石蜡及聚乙烯等的辅助剂。
s6、将排胶后的生坯及雾化壳进行高温烧结,生坯形成紧密复合在雾化壳内侧的多孔陶瓷雾化座。
具体地,将排胶后的生坯及雾化壳放入烧结炉中进行高温烧结,高温烧结的温度为600℃~1500℃;烧结温度可优选700℃。
生坯经烧结后形成多孔陶瓷雾化座。多孔陶瓷雾化座的内部中空,形成用于储存烟液的储液腔。
对于上述步骤s3中发热件也放置于成型模具内,在步骤s5的热脱蜡、排胶处理以及步骤s6的高温烧结中,发热件同生坯及雾化壳一起。在高温烧结后,发热件嵌设在多孔陶瓷雾化座上。
本发明的制造方法中,通过上述步骤s1-s6,获得陶瓷复合雾化器的雾化壳组件,该雾化壳组件由雾化壳及多孔陶瓷雾化座复合为一体形成。通过发热件通电发热后,可将多孔陶瓷雾化座内的烟液加热雾化形成烟雾。
如图1、2所示,上述制造方法制得的一实施例的陶瓷复合雾化器,用于电子烟,其可包括多孔陶瓷雾化座10以及硬质的雾化壳20。
多孔陶瓷雾化座10的内部中空,形成容置烟液的储液腔(未图示)。雾化壳20紧密包覆在多孔陶瓷雾化座10的外侧,起到外围密封的作用,还提高雾化芯的结构强度。
具体地,多孔陶瓷雾化座10在结构上可包括支撑板11以及侧板12,侧板12围接在支撑板11的外周上,形成一端封闭、相对另一端开放的筒状的多孔陶瓷雾化座10。侧板12与支撑板11围成的空间形成储液腔。支撑板11位于多孔陶瓷雾化座10的一侧且为封闭侧,与支撑板11相对的多孔陶瓷雾化座10的另一侧开放,形成与储液腔相连通的进液口,烟液通过该进液口进入储液腔中。
多孔陶瓷雾化座10的外周形状可以是椭圆形、圆形或多边形等各种形状,其内部的储液腔也可以是多种形状。
雾化壳20可以采用但不限于氧化铝基、氧化锆基及铝硅基等陶瓷材料制成,也可以是金属材料制成。本实施例中,雾化壳20为相对两端开放的筒状结构,紧密包覆在多孔陶瓷雾化座10的侧板12外侧,与多孔陶瓷雾化座10复合形成一体。雾化壳20的外周形状对应其所包覆的多孔陶瓷雾化座10的外周形式设置。
本发明的陶瓷复合雾化器还包括发热件30,嵌设在多孔陶瓷雾化座10上,用于通电发热,热量传导至多孔陶瓷雾化座10,从而对烟液进行加热雾化。
多孔陶瓷雾化座10的一表面上设有与发热件30相适配的限位槽110,发热件30容置在限位槽110内。本实施例中,限位槽110设置在支撑板11背向储液腔的表面上。
在限位槽110内,发热件30的下表面和侧面分别与限位槽110的底面和侧面相贴合。发热件30可以通过紧配合固定在限位槽110内。
进一步地,为防止发热件30从多孔陶瓷雾化座10上脱离,发热件30上还可以设有至少一个向储液腔内延伸的倒钩33。对应倒钩33的位置及数量,限位槽110的底面设有贯通至储液腔的通孔120,从而倒钩33可穿过通孔120置于储液腔中。倒钩33的端部可以勾挂在支撑板11朝向储液腔的表面上,防止发热件30从限位槽110中脱出。
限位槽110和通孔120均在多孔陶瓷雾化座10成型时形成在其上。
发热件30进一步可包括相间隔的两个电极触点31、连接在两个电极触点31之间的发热线路32。两个电极触点31分别用于与电子烟的正极和负极连接导通。发热线路32可以是直线状、波浪状、u形状等各种形状的发热条。
倒钩33一体形成在电极触点31和发热线路32中至少一处上。
本发明的陶瓷复合雾化器使用时,安装在电子烟中,形成电子烟的烟弹的雾化模块,将烟液加热形成烟雾。
以上所述仅为本发明的实施例,并非因此限制本发明的专利范围,凡是利用本发明说明书及附图内容所作的等效结构或等效流程变换,或直接或间接运用在其他相关的技术领域,均同理包括在本发明的专利保护范围内。
起点商标作为专业知识产权交易平台,可以帮助大家解决很多问题,如果大家想要了解更多知产交易信息请点击 【在线咨询】或添加微信 【19522093243】与客服一对一沟通,为大家解决相关问题。
此文章来源于网络,如有侵权,请联系删除


