雾化芯、雾化器及气溶胶产生装置的制作方法



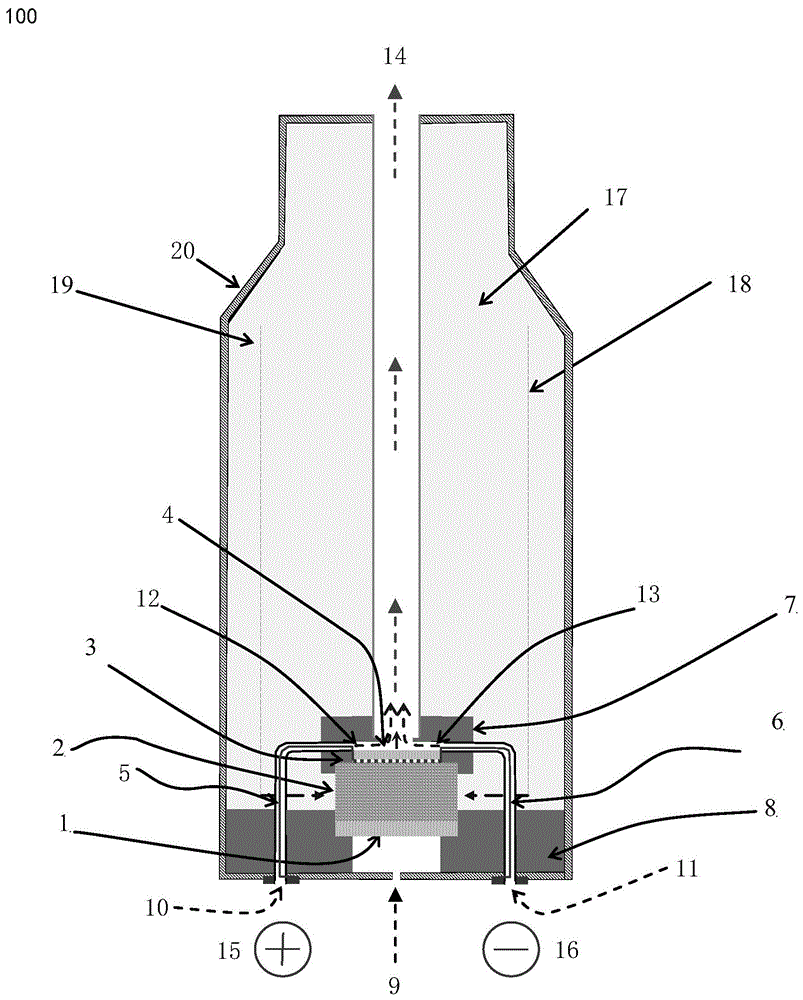
本发明实施例涉及烟具领域,尤其涉及一种雾化芯、包含该雾化芯的雾化器及包含该雾化器的气溶胶产生装置。
背景技术:
通过雾化芯加热雾化等手段,将含有尼古丁等的雾化液变成气溶胶的装置是一种模仿香烟的电子产品,有着与香烟近似的烟雾、味道和感觉。这种通过雾化产生的含尼古丁气溶胶不含普通香烟烟气中普遍存在的焦油等有害致癌物质,被认为是一种有利于传统烟民身体健康的香烟替代品。同时这种电子装置具有便携性好,不会产生明火,也不产生二手烟且环保的特点,受到很多吸烟人士的青睐。
气溶胶产生装置的加热雾化技术,目前广泛采用的主要有两类:1)以棉花或纤维束作为导油体,将电热丝缠绕其上直接加热烟油而使之雾化;2)以蜂窝陶瓷作为导油体,采用电热丝或电热带等方式加热而使烟油雾化。
棉花或纤维束的锁油能力有限,未使用的新品电子烟,放置一段时间以后,空气进口以及烟气出口常常可见渗漏出的烟油;以蜂窝陶瓷作为导油体的“陶瓷雾化芯”,业界采用的工艺其实质是将发热丝或发热带烧结在蜂窝陶瓷一侧表面或单侧覆以厚膜印刷发热带,作为单一元器件同时发挥吸油、锁油和雾化作用,其制造工艺较为复杂,这种雾化芯要满足吸油导油速率,需要足够的孔径和孔隙率,其结果是锁油能力不足。
另外,现有雾化器的结构中,雾化芯的雾化面通常与进气口直接连通,即大都采用直通式气道,吸满烟油的棉花或蜂窝陶瓷作为隔离体隔离雾化液和气溶胶。这种结构有利于提高雾化效率,但对棉花或蜂窝陶瓷的吸油、锁油能力要求极高,为了满足吸油能力,限于材料与工艺设计,现有的雾化器普遍存在漏油的问题,渗漏的雾化液(即烟油)在重力作用下从进气口漏出,污染传感器造成失灵,污染电源电极等,影响使用者的使用体验。另外,雾化效率与烟雾产量等也存在较大的提升空间。
技术实现要素:
为了解决现有技术中存在的漏油问题,以及雾化效率与烟雾产量不高的问题,本发明提供了一种雾化芯、包含该雾化芯的雾化器及包含该雾化器的气溶胶产生装置。
第一方面,本发明提供了一种雾化芯,该雾化芯包括:
雾化芯主体,所述雾化芯主体为多孔结构,用于传导雾化液和至少部分地储存雾化液,所述雾化芯主体具有第一表面,与所述第一表面相对的第二表面,以及与所述第一表面和第二表面相区别的吸液面,所述吸液面用于至少部分地与雾化液接触;
进气锁油层,设置于所述雾化芯主体的第一表面侧,所述进气锁油层具有进气面,该进气面远离所述第一表面设置并与空气接触,所述进气锁油层设置为允许空气经由所述进气面通过所述进气锁油层并至少部分地防止来自所述雾化芯主体的雾化液传导至进气面;
发热体,设置于所述雾化芯主体的第二表面侧,用于加热经由所述雾化芯主体传导的雾化液而生成气溶胶。
进一步的,所述雾化芯还包括气溶胶逸出层,设置于所述雾化芯主体的第二表面侧,所述气溶胶逸出层设置为允许所述气溶胶通过所述气溶胶逸出层并至少部分地防止来自所述雾化芯主体的雾化液通过该气溶胶逸出层。
或者,进一步包括气溶胶逸出层,设置为以低于所述雾化芯主体的速率传导所述雾化液,所述发热体设置于所述气溶胶逸出层远离所述雾化芯主体的一侧。
进一步地,所述发热体设置为位于所述气溶胶逸出层和所述雾化芯主体的第二表面之间。
进一步地,所述发热体基本上是二维的形状。
进一步地,所述气溶胶逸出层和/或所述进气锁油层为多孔结构,所述气溶胶逸出层和/或所述进气锁油层的平均孔径小于所述雾化芯主体的平均孔径。
进一步地,所述气溶胶逸出层和/或所述进气锁油层为多孔结构,所述气溶胶逸出层和/或所述进气锁油层的孔隙率小于所述雾化芯主体的孔隙率。
进一步地,所述气溶胶逸出层、所述进气锁油层和所述雾化芯主体至少一个采用陶瓷材料。
进一步地,所述进气锁油层、所述雾化芯主体、所述发热体和所述气溶胶逸出层是分离的,通过叠置形成所述雾化芯。
进一步地,所述进气锁油层、所述雾化芯主体、所述发热体和所述气溶胶逸出层中至少两者固定为一体形成所述雾化芯,所述固定通过粘接或烧结。
进一步地,所述发热体为多孔结构,包含电连通的导电网络。
进一步地,所述发热体包括具有开孔的金属加热片。
进一步地,所述金属加热片包括镍铬合金或者铁铬铝合金加热片。
进一步地,所述雾化芯主体,所述进气锁油层和/或所述气溶胶逸出层的横截面包括长方形,圆角长方形,正方形,圆角正方形或者圆形,所述金属加热片具有与其所接触表面相适应的形状。
进一步地,所述发热体包括采用导电浆料,通过厚膜印刷的方式印制在所述雾化芯主体的第二表面或所述气溶胶逸出层表面的导电轨迹。
进一步地,所述雾化芯主体具有开口在所述吸液面上的盲孔或通孔,以导引所述雾化液进入所述雾化芯主体内部,减少雾化液传导距离。
本发明将进气锁油层和发热体分别设置在雾化芯主体的两侧,并将发热体侧设置为面向出气口,进气锁油层与空气接触,这样能够实现降低漏油几率的效果。原因在于:进气锁油层允许空气通过,而一定程度上防止经由雾化芯主体传导的雾化液通过进气锁油层,由此降低了雾化液渗漏的几率,同时,发热体位于另一侧,由于需要传导足够的雾化液,并使产生的大量烟雾持续顺利地吸走,因而发热体侧需要相对更开放的出口,在这种情况下,难以保证雾化液的渗漏,而发明通过将发热体侧设置为面向出气口,这样在通常状态下,雾化液的所承受的重力方向朝向雾化芯主体内部,因此,在重力作用下雾化液将倾向于保留在雾化芯主体中,从而降低了漏油的几率。
对于进气锁油层,可选地,所述进气锁油层为多孔结构,例如,陶瓷多孔结构或有机多孔结构。为了能够起到锁油的作用,一种考虑是,使所述进气锁油层的孔隙率和/或平均孔径小于所述雾化芯主体的;另一种考虑是,使进气锁油层具有比所述雾化芯主体更高的疏油性能,例如,采用特氟龙材料制备进气锁油层,或例如在进气锁油层表面沉积疏油层,由此降低雾化液通过的几率或速率。
气溶胶逸出层提供进一步的锁油能力,优选地,气溶胶逸出层具有例如,陶瓷多孔结构或有机多孔结构。该多孔结构的孔隙率和/或平均孔径小于所述雾化芯主体,由此产生更优化的锁油能力,降低雾化液传导速率,进而降低从雾化侧漏油的几率,相对的,为了防止导油速率不足导致的气溶胶产生量不足或干烧,所述气溶胶逸出层的孔隙率和/或平均孔径需大于所述进气锁油层。可以理解的是,接近所述雾化芯主体的孔隙率和/或平均孔径,使得导油速率提高,进而提高气溶胶产生量,但是相应降低锁油性能,增大漏油几率,反之,相对所述雾化芯主体的孔隙率和/或平均孔径,越小的孔隙率和/或平均孔径,越优化的锁油性能,但是相应地降低导油速率,降低气溶胶产生量,降低口感。本领域技术人员可以在本发明的启示下进行调整,并获得最优化性能。作为一种选择,优选地,进气锁油层的孔隙率为40-50%、平均孔径为20-30μm,厚度为0.5-1.5mm;优选地,雾化芯主体的孔隙率为60-90%、平均孔径40-100μm,厚度为2-4mm;优选地,气溶胶逸出层的孔隙率70-80%、平均孔径20-70μm,厚度为0.3-1mm。进一步地,为满足经由发热片产生的雾化气溶胶的快速逸出条件,气溶胶逸出层的厚度优选控制在0.5mm以下。
所述雾化芯主体可以为均匀的多孔结构,具有常规可选的孔隙率和/或平均孔径,以满足足够导油速率需求;所述雾化芯主体也可以具有开口在其吸油面上的通孔或盲孔,开孔或盲孔将进一步降低雾化液到发热体的传导距离,进一步提高雾化液传导效率。
所述进气锁油层,所述雾化芯主体,所述发热体,可选地所述气溶胶逸出层可以采用叠层的形式组合形成所述雾化芯,也可以至少部分地固定成一体形成所述雾化芯,所述固定可以是粘接或烧结。可以理解的是,叠层的形式组合形成所述雾化芯对于各个部分的批量加工,降低成本有利,可以分别批量自动化生产各部分,自动化裁切,并在后期装配。可以理解的是,至少部分地固定成一体形成所述雾化芯,具有较复杂的工艺,但有利于后期装配,降低装配难度。
所述烧结,例如可以是将所述进气锁油层,所述雾化芯主体,所述发热体,可选地所述气溶胶逸出层由坯体成型直接结合在一起,经脱胶、孔隙成型工序,整体烧制而成。
可选的发热体基本上是二维的形状,二维的形状可以容易地固定在多孔体的表面,例如雾化芯主体或气溶胶逸出层的表面,多孔体的所述表面优选基本上是平的。
发热体优选是金属发热片,例如,优选由镍铬合金或者铁铬铝合金电致发热片材制造。可以理解的是,金属发热片的厚度越小,其电阻值越大,反之,金属发热片的厚度越大,其电阻值越小。金属发热片通常在其上形成开孔图案,以调整电阻,可以理解的是,开孔面积百分比越大,电阻值越大,反之,开孔面积百分比越小,电阻值越小。作为选择,金属发热片厚度优选采用30-80μm,开孔面积百分率优选为50-70%。开孔具有2个目的:1)降低发热片的导电面积(体积),提高宏观电阻;优选地,将发热片的整体电阻值控制在1-2ω范围之内;2)使烟油能够通过发热片,吸收热量,转化为蒸气逸出。
金属发热片适应所述雾化芯主体和/或气溶胶逸出层的形状,可以是例如,长方形,圆角长方形,正方形,圆角正方形,圆形。金属发热片上供烟油和蒸气通过的孔洞形状,为确保发热均匀,以方形为宜,如图7-图9所示。
30-80μm厚的金属片材,其强度一般不足以支持直接覆盖在蜂窝陶瓷表面使用,尤其是在开有大面积孔洞的条件下,容易变形、甚至破裂。因此,优选地将这种超薄多孔合金发热片夹在雾化芯主体和气溶胶逸出层之间,一方面可以确保超薄发热片的结构完整,另一方面也可以利用蜂窝陶瓷的绝热特性来限制热量的扩散,从而提高电源的能量利用率,并提升热量向雾化液传递的效率。
发热体也可以是涂层发热体,例如,采用真空溅射、真空镀膜等技术途径,将多孔超薄合金发热片直接覆盖在气溶胶逸出层,使合金元素以原子态的方式紧密附着在多孔陶瓷材料上形成发热体,优选地,发热体覆盖在气溶胶逸出层朝向出气通道的材料面,构成另一种形式的复合多孔发热片。
发热体也可以是内建在所述气溶胶逸出层的导电网络,由此,所述气溶胶逸出层整体形成所述发热体,加热并导出雾化后的气溶胶。
发热体也可以采用导电浆料,通过厚膜印刷的方式,将导电轨迹印制在气溶胶逸出层朝向出气通道的材料面形成发热体。
此外,还可以不包括气溶胶逸出层,将多孔超薄合金发热片直接覆盖在雾化芯主体朝向出气通道的材料面,可供优选的技术途径包括真空溅射、真空镀膜等方式,使合金元素以原子态的方式紧密附着在蜂窝陶瓷吸油体材料的表层,构成另一种形式的复合多孔发热片。或者,采用导电浆料,通过厚膜印刷的方式,将优选图案的导电轨迹印制在雾化芯主体朝向出气通道的材料面。可以理解的是,这种方式,优选地要提高雾化芯主体的锁油能力,例如采用降低雾化芯主体的孔隙率、减小雾化芯主体的微孔直径等技术措施,否则,烟油容易渗漏流出,可选地,优选增加开口在吸油面的通孔或盲孔,消除或降低由此带来的导油效率劣化。
第二方面,本发明还提供了一种雾化器,其包括:
外壳,所述外壳内形成有存储雾化液的储液仓,所述储液仓包括出口;所述外壳内沿所述外壳的纵长方向形成延伸的出气通道,包括入口和出气口,所述出气通道的出气口位于所述外壳的一端;
任意地本发明所公开的雾化芯;所述雾化芯收容于所述外壳内,储液仓的所述出口与雾化芯的所述吸液面连通;
至少一个进气通道,所述进气通道包括进气口和进气通道出口,所述进气通道出口与所述出气通道入口在所述发热体附近会和,形成连通的气流通道,由所述发热体加热产生的气溶胶经由所述气流通道被排出;
固定件,用于固定所述雾化芯与所述外壳,所述固定件上开设至少一个连通所述进气通道进气口的开口;
电极触点,电连接所述发热体,用于使电源供电给所述发热体。
进一步地,所述进气通道有两条,所述电极经由所述进气通道与所述发热体电连接。
进一步地,所述电极采用所述进气通道与所述发热体电连接。
此外,第三方面,本发明提供一种气溶胶产生装置,包括:
电源组件和雾化器,所述电源组件用于给所述雾化器提供电能,所述电源组件与所述雾化器电连接,所述雾化器为本发明公开的任意的雾化器。
进一步地,所述电源组件与所述雾化器电连接为可拆卸地电连接。
与现有技术相比,本发明所提供的雾化器、将发热体的一侧面向出气通道设置,并设置至少一个进气通道,使进气通道出口与外壳上形成的出气通道入口在所述发热体附近汇合,形成连通的气流通道,由此,在用户吸食所述气溶胶时,发热体附近的气流通道将会形成负压,此时,进气锁油层的进气面与空气接触,空气可以通过进气面进入进气锁油层,在雾化芯主体的第一表面侧附近的气压接近大气压,也就是说,由于用户吸食,在雾化芯主体的第一、第二表面两侧形成气压差,该气压差将有利于促进雾化芯主体内吸收并储存的雾化液向发热体传导,进而提高雾化效率。
进气通道的设计,隔离了雾化液与外界的直接连通,进一步降低了漏油的几率。
附图说明
一个或多个实施例通过与之对应的附图中的图片进行示例性说明,这些示例性说明并不构成对实施例的限定,附图中具有相同参考数字标号的元件表示为类似的元件,除非有特别申明,附图中的图不构成比例限制。
图1是包含本发明雾化芯的雾化器的总体结构示意图;
图2是图1中雾化器的局部结构示意图,分离构造的多孔陶瓷进气锁油层、多孔陶瓷雾化芯主体、发热体以及多孔陶瓷气溶胶逸出层,由密封固定件i和密封固定件ii连接在一起。
图3是图2的构件分解示意图,进气锁油层、雾化芯主体、发热片以及气溶胶逸出层呈四段分离的状态。
图4是正方形横截面结构的四段分离式多孔陶瓷雾化芯的构造示意图。
图5是长方形横截面结构的四段分离式多孔陶瓷雾化芯的构造示意图。
图6是圆形横截面结构的四段分离式多孔陶瓷雾化芯的构造示意图。
图7是方型多孔超薄合金发热片的导线引出方式。
图8是长方型多孔超薄合金发热片的导线引出方式。
图9是圆形多孔超薄合金发热片的导线引出方式。
图10是本发明的电子烟的示意图。
附图标号说明:
1-进气锁油层
2-雾化芯主体
3-发热体
4-气溶胶逸出层
5,6-连接发热体与电极触点的导线
7-密封固定件i
8-密封固定件ii
9-空气接触口
10-进气通道i
11-进气通道ii
12-进气通道出口i
13-进气通道出口ii
14-出气通道及出气口
15,16-电极触点(分别连接电源正极,负极)
17-储油仓
18,19-储油仓内雾化液流动方向
20-外壳
100-雾化器
200-电源组件。
具体实施方式
为了便于理解本发明,下面结合附图和具体实施方式,对本发明进行更详细的说明。需要说明的是,当元件被表述“固定于”另一个元件,它可以直接在另一个元件上、或者其间可以存在一个或多个居中的元件。当一个元件被表述“连接”另一个元件,它可以是直接连接到另一个元件、或者其间可以存在一个或多个居中的元件。本说明书所使用的术语“上”、“下”、“左”、“右”、“内”、“外”以及类似的表述只是为了说明的目的。
除非另有定义,本说明书所使用的所有的技术和科学术语与属于本发明的技术领域的技术人员通常理解的含义相同。本说明书中在本发明的说明书中所使用的术语只是为了描述具体的实施方式的目的,不是用于限制本发明。本说明书所使用的术语“和/或”包括一个或多个相关的所列项目的任意的和所有的组合。
本说明书所揭露的雾化液可以为烟油、液态的药物成分或其它加热易挥发的芳香类物质。
下面结合附图对本发明做详细的描述,所做描述仅为理解本发明的发明构思,本发明不限于所描述的范围。
如图1所示,为本发明的一种实施方式所提供的雾化器,该雾化器主要包括外壳20,所述外壳20内形成有存储雾化液的储液仓17,所述储液仓包括出口(未示出);所述外壳20内沿所述外壳的纵长方向形成延伸的出气通道和出气口14,包括入口,所述出气通道的出气口位于所述外壳的一端;
参考图2和图3,该雾化器还包括雾化芯,包括进气锁油层1,雾化芯主体2,发热体3和气溶胶逸出层4,所述雾化芯主体2为多孔结构,用于传导雾化液和至少部分地储存雾化液,所述雾化芯主体具有第一表面,与所述第一表面相对的第二表面,以及与所述第一表面和第二表面相区别的吸液面,所述吸液面用于至少部分地与雾化液接触;所述进气锁油层1设置于所述雾化芯主体的第一表面侧,所述进气锁油层具有进气面,该进气面远离所述第一表面设置并与空气接触,所述进气锁油层1设置为允许空气经由所述进气面通过所述进气锁油层并至少部分地防止来自所述雾化芯主体的雾化液传导至进气面;所述发热体3设置于所述雾化芯主体的第二表面侧,用于加热经由所述雾化芯主体传导的雾化液而生成气溶胶。所述气溶胶逸出层4设置于所述雾化芯主体2的第二表面侧,参考图4,图5,图6,所述雾化芯的各组成可以是长方形,正方形,圆形。参考图7,图8,图9,所述发热体为二维片状发热体,其具有方形开孔。所述方形开孔仅为优选示例,也可以为长方形,圆形或椭圆形等其他形状,只要其目的是为了电阻值大小和均匀性的控制。雾化芯收容于所述外壳20内,储液仓17的所述出口与雾化芯的所述吸液面连通,使用情况下,储油仓内雾化液大致沿雾化液流动方向18,19通过储液仓17的所述出口和雾化芯的所述吸液面吸入雾化芯;
该雾化器还包括两个进气通道10,11,进气通道包括进气口和进气通道出口12,13,所述进气通道出口12,13与所述出气通道入口在所述发热体3附近汇合,形成连通的气流通道,由所述发热体3加热产生的气溶胶经由出气通道及出气口14被排出;
该雾化器还包括密封固定件7,8,用于固定所述雾化芯与所述外壳20,所述密封固定件上开设至少一个连通所述进气通道进气口的开口;
两个电极触点15,16,通过导线5,6电连接所述发热体3,用于使电源供电给所述发热体3。所述电极触点15,16分别经由所述进气通道10,11与所述发热体3电连接。
所述雾化器还具有使雾化芯的进气锁油层1的进气面接触空气用的空气接触口9,通过空气接触口9,雾化芯中进气锁油层的进气面与空气连通,气压保持接近1个环境大气压,雾化器在使用时,通过使用者的吸食动作,在进气通道出口12,13与出气通道入口交汇点发热体3附近,产生负压,压力传递方向如图2,图3中中间箭头所示,在该压力差的驱动下,雾化芯中的雾化液产生向发热体传导的动力,促进了雾化液的雾化效果。
进一步,本实施例中的雾化芯主体中的吸液面区别于第一表面和第二表面,雾化器在使用时,通过使用者的吸食动作,在进气通道出口12,13与出气通道入口交汇点发热体3附近产生负压,雾化液从吸液面传导至第二表面以提供给发热体,而通过进气锁油层进入的空气经过第一表面导入至吸液面而进入储液腔内,从而保证储液腔内的气压平衡,空气通过雾化芯导入储液腔的路径和雾化液通过雾化芯传递至发热体的路径互不干扰,进一步提高了雾化液的传递效率。
需要说明的是,本发明的说明书及其附图中给出了本发明的较佳的实施例,但是,本发明可以通过许多不同的形式来实现,并不限于本说明书所描述的实施例,这些实施例不作为对本发明内容的额外限制,提供这些实施例的目的是使对本发明的公开内容的理解更加透彻全面。并且,上述各技术特征继续相互组合,形成未在上面列举的各种实施例,均视为本发明说明书记载的范围;进一步地,对本领域普通技术人员来说,可以根据上述说明加以改进或变换,而所有这些改进和变换都应属于本发明所附权利要求的保护范围。
起点商标作为专业知识产权交易平台,可以帮助大家解决很多问题,如果大家想要了解更多知产交易信息请点击 【在线咨询】或添加微信 【19522093243】与客服一对一沟通,为大家解决相关问题。
此文章来源于网络,如有侵权,请联系删除


