一种DBC基板两面铜箔同时烧结时用的垫板及其制备方法与流程



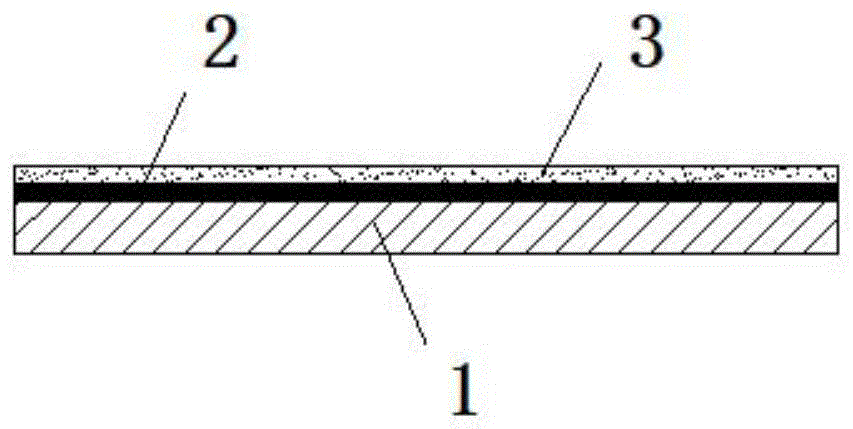
本发明涉及半导体技术领域,具体是dbc基板两面铜箔同时烧结时用的垫板及其制备方法。
背景技术:
为了提高双面覆铜陶瓷基板(dbc)烧结生产效率,dbc生产厂商都在开发两面铜箔同时烧结的工艺技术。两面铜箔同时烧结时需要用到专用烧结垫板,烧结时将第一片铜片先放在烧结垫板上,陶瓷板放在第一片铜片上面,再将第二片铜片放在陶瓷板上进行烧结。
目前制作烧结垫板的材料一般都选用铬镍铁合金(inconel)、镍镉合金等耐高温金属材料、sic陶瓷或者氧化铝陶瓷板上涂mgo粉末等材料。但用这些材料制成的烧结垫板在生产中存在一些问题:
1.耐高温金属材料容易与铜粘合在一起或在铜片表面留下接触痕迹,造成产品不良增加。
2.直接用sic陶瓷作为垫板时,则在与铜片接触后铜片表面容易出现烧结熔化现象,从而影响产品外观质量。
3.在氧化铝陶瓷垫板表面涂含有mgo粉的溶液,尽管mgo粉可起到与铜隔离作用且不会与铜粘合在一起,但与氧化铝板结合不牢,容易脱落。而脱落的粉末会污染烧结炉膛,影响产品烧结良率。同时由于mgo粉溶液是人工涂的,生产效率低。
技术实现要素:
针对现有技术存在的问题,本发明提供一种dbc基板两面铜箔同时烧结时用的垫板,以解决以上至少一个技术问题。
本发明还提供一种dbc基板两面铜箔同时烧结时用的垫板的制备方法,以解决以上至少一个技术问题。
为了达到上述目的,本发明提供了一种dbc基板两面铜箔同时烧结时用的垫板,其特征在于,包括从上至下依次设置的mgo烧结层、氧化铝溶射层以及sic陶瓷板;
所述mgo烧结层的厚度为1~10μm;
所述氧化铝溶射层的厚度为15~25μm;
所述sic陶瓷板的厚度为1mm~5mm。
进一步优选的,一种dbc基板两面铜箔同时烧结时用的垫板的制备方法,其特征在于,包括如下步骤,
步骤一,sic陶瓷板表面预处理,粗糙度ra为0.1~0.5μm;
步骤二,sic陶瓷板上熔射氧化铝粉,形成氧化铝溶射层;
步骤三,mgo溶液喷在氧化铝粉熔射层上,高温烧结,形成mgo烧结层。
进一步优选的,sic陶瓷板的长度为195mm~210mm,宽度为140mm~150mm。
进一步优选的,步骤一,sic陶瓷板精磨处理。
进一步优选的,步骤二,熔射温度为580℃~620℃。熔射时喷枪移动速度为3m/min~5m/min。
进一步优选的,步骤三中,mgo溶液是mgo粉以及酒精混合而成,所述mgo溶液浓度50%~70%。
进一步优选的,步骤三中,烧结温度为1050℃~1150℃;烧结时间为3小时;mgo层厚度为1~10μm。
进一步优选的,所述mgo烧结层的厚度为1~10μm;
所述氧化铝溶射层的厚度为15~25μm;
所述sic陶瓷板的厚度为1mm~5mm。
有益效果:本专利采用sic陶瓷板作为烧结垫板的基体材料,氧化铝溶射层以及mgo烧结层,可确保垫板不与铜片粘合在一起或在铜片表面留下接触痕迹、或使铜片熔化,同时mgo烧结层不易脱落而污染烧结炉膛,提高了产品的良率和生产效率。
mgo烧结层可起到覆铜陶瓷基板的铜片与sic陶瓷板的隔离作用,用mgo粉直接熔射在sic表面,虽结合力高,粉末不易脱落,但熔射工艺复杂,设备昂贵,生产成本高。而将mgo粉直接烧结在sic陶瓷板,粉末容易脱落会污染烧结炉膛。氧化铝粉熔射工艺简单、成本低,且与sic陶瓷板和mgo层结合力高,现把氧化铝粉熔射层作为sic陶瓷板和mgo层的过渡层为先将氧化铝粉熔射在sic表面,再将mgo粉烧结在氧化铝粉熔射层上,这样就解决了mgo粉熔射成本高,与sic陶瓷板烧结后粉末容易脱落的问题。
附图说明
图1为本发明一种dbc基板两面铜箔同时烧结时用的垫板的一种示意图。
1为sic陶瓷板,2为氧化铝溶射层,3为mgo烧结层。
具体实施方式
下面结合附图对本发明做进一步的说明。
参见图1,一种dbc基板两面铜箔同时烧结时用的垫板,包括从上至下依次设置的mgo烧结层3、氧化铝溶射层2以及sic陶瓷板1;mgo烧结层3的厚度为1~10μm;氧化铝溶射层2的厚度为15~25μm;sic陶瓷板1的厚度为1mm~5mm。
一种dbc基板两面铜箔同时烧结时用的垫板的制备方法,包括如下步骤,
步骤一,sic陶瓷板1精磨处理,粗糙度ra为0.1~0.5μm;sic陶瓷板的长度为195mm~210mm,宽度为140mm~150mm。sic陶瓷板的厚度为1mm~5mm。
步骤二,sic陶瓷板1上熔射氧化铝粉,形成氧化铝溶射层2;熔射温度为580℃~620℃。氧化铝溶射层的厚度为15~25μm。熔射时喷枪移动速度为3m/min~5m/min。
溶射工艺参数:电流500-600a,电压55v-65v,主气流量35-50l/min,次气流量4-10l/min,送粉量20-60g/min,溶射距离100-150mm;主气为氩气,次气为氢气,主气与次气混合作为溶射气体。
步骤三,配制mgo溶液,mgo溶液是mgo粉以及酒精混合而成,mgo溶液浓度50%~70%;
mgo溶液喷在氧化铝粉熔射层上,高温烧结,形成mgo烧结层3;
烧结温度为1050℃~1150℃;烧结时间为3小时;mgo烧结层厚度为1~10μm。
具体实施例1为
一种dbc基板两面铜箔同时烧结时用的垫板的制备方法,包括如下步骤,
步骤一,sic陶瓷板精磨处理,粗糙度ra为0.1~0.5μm;sic陶瓷板的长度为195mm~210mm,宽度为140mm~150mm。sic陶瓷板的厚度为2mm~3mm。
步骤二,sic陶瓷板上熔射氧化铝粉,形成氧化铝溶射层;熔射温度为580℃~620℃。氧化铝溶射层的厚度为18μm~20μm。熔射时喷枪移动速度为3m/min~5m/min。
步骤三,配制mgo溶液,mgo溶液是mgo粉以及酒精混合而成,mgo溶液浓度55%~60%,mgo溶液喷在氧化铝粉熔射层上,高温烧结,形成mgo烧结层;
烧结温度为1050℃~1150℃;烧结时间为3小时;mgo烧结层厚度为3μm~5μm。
有益效果:本专利采用sic陶瓷板作为烧结垫板的基体材料,氧化铝溶射层以及mgo烧结层,可确保垫板不与铜片粘合在一起或在铜片表面留下接触痕迹、或使铜片熔化,同时mgo烧结层不易脱落而污染烧结炉膛,提高了产品良率5%以上并同时提高生产效率。
mgo烧结层可起到覆铜陶瓷基板的铜片与sic陶瓷板的隔离作用,用mgo粉直接熔射在sic表面,虽结合力高,粉末不易脱落,但熔射工艺复杂,设备昂贵,生产成本高。而将mgo粉直接烧结在sic陶瓷板,粉末容易脱落会污染烧结炉膛。氧化铝粉熔射工艺简单、成本低,且与sic陶瓷板和mgo层结合力高,现把氧化铝粉熔射层作为sic陶瓷板和mgo层的过渡层为先将氧化铝粉熔射在sic表面,再将mgo粉烧结在氧化铝粉熔射层上,这样就解决了mgo粉熔射成本高,与sic陶瓷板烧结后粉末容易脱落的问题。
以上仅是本发明的优选实施方式,应当指出,对于本技术领域的普通技术人员来说,在不脱离本发明原理的前提下,还可以做出若干改进和润饰,这些改进和润饰也应视为本发明的保护范围。
起点商标作为专业知识产权交易平台,可以帮助大家解决很多问题,如果大家想要了解更多知产交易信息请点击 【在线咨询】或添加微信 【19522093243】与客服一对一沟通,为大家解决相关问题。
此文章来源于网络,如有侵权,请联系删除


