利用餐厨垃圾离心液连续发酵制备肥料的系统及方法与流程



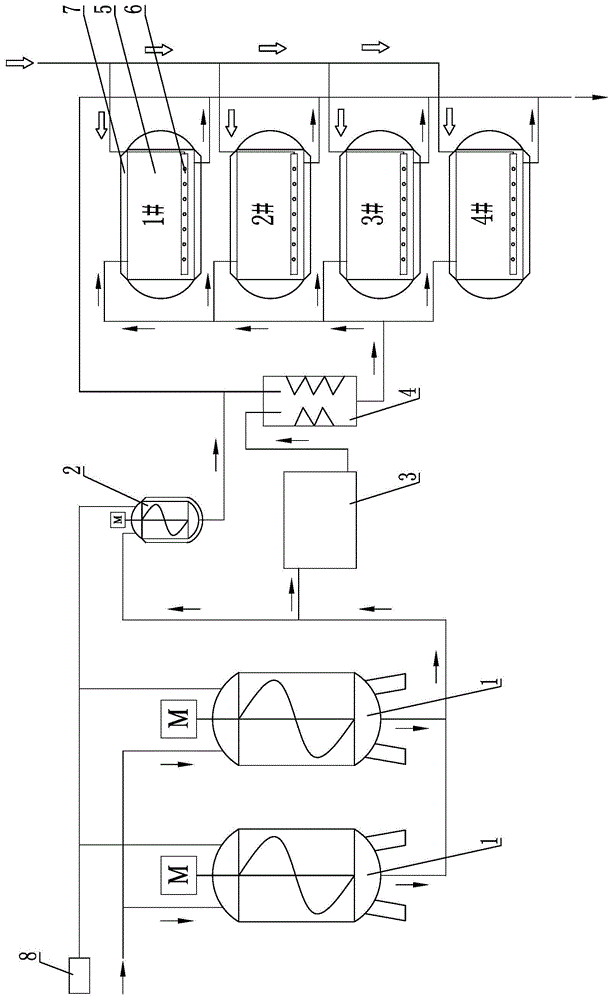
本发明涉及生活垃圾处理技术领域,尤其涉及一种利用餐厨垃圾离心液连续发酵制备肥料的系统及方法。
背景技术:
随着经济的不断发展,人们生活水平不断提高;在食品、副食品不断丰富的时代,厨房剩余物和餐后剩余物共同组成的餐厨垃圾日益增加。随意丢弃的餐厨垃圾不仅会腐烂发臭、滋生蚊蝇、传播疾病,而且对环境造成污染,因而逐渐成为一个难以忽视的污染源;对它的处理也日益受到重视。餐厨垃圾中含有大量有机物,具有一定的利用价值和经济价值,如果加以利用不仅可以对餐厨垃圾进行无害化处理,而且所得产物还可以成为有用的产品,使餐厨垃圾成为一种资源。餐厨垃圾经过分选、粉碎后进行分离,得到其中的餐厨垃圾离心液,然后对餐厨垃圾离心液进行发酵,生产微生物菌肥。
传统的餐厨垃圾离心液通过厌氧发酵的方式处理,具有缺点如下:1、设备投资费用高;2、产生可燃气体甲烷生成过程风险高;3、生物甲烷再利用成本高;4、厌氧发酵产生的沼液需要二次处理,处理成本高。为克服以上缺点,现有技术中提供一种新型方法,该方法采用定向接种好氧发酵,直接生成农业用液体微生物菌剂。然而,目前常见的好氧发酵方式主要为分级发酵,该分级发酵具有发酵效率低、发酵时间长、设备成本高、成品合格率低、工艺配套不合理等缺点,不利于发酵生产。
技术实现要素:
本发明所要解决的技术问题是提供一种发酵效率高、发酵时间短、设备成本低、成本合格率高、工艺配套合理、有利于发酵生产的利用餐厨垃圾离心液连续发酵制备肥料的系统及方法。
为解决上述技术问题,本发明的技术方案是:利用餐厨垃圾离心液连续发酵制备肥料的系统,包括至少一个配料罐,所述配料罐的出料端连接有种子罐,所述配料罐的出料端还连接有杀菌机,所述杀菌机的出料端连接有混合器且与所述混合器的进料端连接,所述种子罐的出料端连接至所述混合器的进料端,所述混合器的出料端连接有至少两个发酵罐,各所述发酵罐的出料端均连接至所述混合器的进料端。
作为优选的技术方案,各所述发酵罐内底部分别设置有用于提供灭菌空气的空气分布器,所述空气分布器通过管路连接至所述发酵罐外。
作为优选的技术方案,各所述发酵罐的外壁分别设置有用于为所述发酵罐提供保温的夹层水套。
利用餐厨垃圾离心液连续发酵制备肥料的方法,包括以下步骤:
a)菌悬液的制备:
a1)菌种活化:用特定培养基将需要繁殖的微生物菌液进行培养,在培养温度为35℃-37℃的条件下,培养时间为22h-26h,完成后镜检;
a2)菌种扩繁:然后对步骤a1)中培养后的微生物菌液进行扩量繁殖;
a3)菌悬液制备:重复步骤a1)、步骤a2)进行多次扩繁,制备菌悬液;
b)工业培养基的制备:
工业培养基的原料配比如下:葡萄糖粉45-55份,酵母浸粉0.8-1.2份,牛肉膏0.8-1.2份,蛋白胨0.8-1.2份,磷酸二氢钾15-25份,氢氧化钾4-6份,餐余离心液900-950份;将所需原料按照以上配比调配完成,制备微生物生产的工业培养基;
c)菌种培养:将步骤b)中制备好的工业培养基在95℃以上的条件下保温1.5h-2.5h,然后降温至35℃-45℃,向其内加入步骤a)中获得的菌悬液,在保温35℃-40℃的条件下,培养时间22h-26h,完成后镜检,制成增量用菌悬液;
d)发酵液增量:
d1)将步骤c)中获得的增量用菌悬液与步骤b)中制备好的工业培养基按照1:1~2比例混合进行发酵,在保温35℃-40℃条件下灭菌通氧,培养时间7h-9h,完成后镜检,得到菌悬液发酵产物;
d2)将上一步骤中获得的菌悬液发酵产物作为新的增量用菌悬液,与步骤b)中制备好的工业培养基按照1:1~2比例混合进行发酵,在保温35℃-40℃条件下灭菌通氧,培养时间7h-9h,完成后镜检,得到菌悬液发酵产物;
d3)重复步骤d2),制成成品发酵液;
e)连续发酵:
e1)将步骤d)中获得的成品发酵液分成两部分,一部分成品发酵液进入后储罐内;
e2)将步骤e1)中的剩余另一部分成品发酵液作为连续发酵用菌悬液,继续与步骤b)中制备好的工业培养基按照1:1~2比例混合进行发酵,在保温35℃-40℃条件下灭菌通氧,培养时间7h-9h,完成后镜检,制成新的成品发酵液;
e3)将e2)中获得的新的成品发酵液继续分成两部分,按照步骤e1)、步骤e2)循环重复上述过程,循环使用发酵完成的成品发酵液与步骤b)中制备好的工业培养基混合发酵;
f)产品后储熟化:进入后储罐内的成品发酵液进行后储熟化,形成成品。
作为优选的技术方案,a)菌悬液的制备:
a1)菌种活化:将保存的甘油管放置在灭菌的超净工作台上,让其恢复至室温,用灭菌的移液枪取1ml的菌液加入到100ml无菌的营业肉汤培养基中,恒温振荡培养箱,在培养温度为35℃-37℃的条件下,培养时间为24h,完成后镜检;
a2)菌种扩繁:将100ml培养完成的培养基再次倒入灭菌的1000ml无菌的营养肉汤培养基中,恒温振荡培养箱,在培养温度为35℃-37℃的条件下,培养时间为24h,完成后镜检;
a3)菌悬液制备:重复步骤a1)、步骤a2)再次扩繁,制备10kg菌悬液。
作为优选的技术方案,b)工业培养基的制备:工业培养基的原料配比如下:葡萄糖粉50份,酵母浸粉1份,牛肉膏1份,蛋白胨1份,磷酸二氢钾20份,氢氧化钾5份,离心液900-950份;将所需原料按照以上配比调配完成,制备微生物生产的工业培养基。
作为优选的技术方案,c)菌种培养:将步骤b)中制备好的工业培养基在95℃以上的条件下保温2h,然后降温至35℃-45℃,向其内加入步骤a)中获得的菌悬液,在保温35℃-40℃的条件下,培养时间24h,完成后镜检,制成增量用菌悬液。
作为优选的技术方案,d)发酵液增量:
d1)将步骤c)中获得的增量用菌悬液与步骤b)中制备好的工业培养基按照1:1比例混合进行发酵,在保温40℃条件下灭菌通氧,培养时间8h,完成后镜检,得到菌悬液发酵产物;
d2)将上一步骤中获得的菌悬液发酵产物作为新的增量用菌悬液,与步骤b)中制备好的工业培养基按照1:1比例混合进行发酵,在保温40℃条件下灭菌通氧,培养时间8h,完成后镜检,得到菌悬液发酵产物;
d3)重复步骤d2),制成成品发酵液。
作为优选的技术方案,e)连续发酵:
e1)将步骤d)中获得的成品发酵液分成两部分,一部分成品发酵液进入后储罐内;
e2)将步骤e1)中的剩余另一部分成品发酵液作为连续发酵用菌悬液,继续与步骤b)中制备好的工业培养基按照1:1比例混合进行发酵,在保温40℃条件下灭菌通氧,培养时间8h完成后镜检,制成新的成品发酵液;
e3)将e2)中获得的新的成品发酵液继续分成两部分,按照步骤e1)、步骤e2)循环重复上述过程,循环使用发酵完成的成品发酵液与步骤b)中制备好的工业培养基混合发酵。
作为优选的技术方案,采用血球计数板进行镜检。
由于采用了上述技术方案,本发明的有益效果是:
1、本发明可以有效提高发酵效率,缩短发酵时间;现有技术中主要采用分级发酵,发酵时间为24t,发酵罐按照10%接种量,每个10t发酵罐每天会生产成品9t,4个10t发酵罐每天最多生产成品36t;而本发明连续发酵法发酵时间为8h,4个10t发酵罐在一个8h发酵周期内可以生产成品15t,如果发酵24h,每天可以生产成品45t,因此,与传统发酵方法相比,且生产效率提高250份。
2、本发明的设备成本降低,与传统分级发酵相比,可以至少减少3个0.1t的发酵罐、3个1t的发酵罐,成本增加1t/h的uht灭菌机和普通的管道混合器,设备成本综合降低120份。
3、本发明提高成品的合格率,传统的发酵过程一般是按照10%的接种量进行混合培养,接种量低了容易造成微生物培养物的杂菌感染(优势种群占的比例),而连续发酵法的接种量在50%,不但提高发酵效率,而且通过比较高的优势种群占比,减少有害杂菌的生长和繁殖,提高成品的合格率。
4、与前部工艺的配套性更合理,前部的生产也是连续式的生产,传统的工艺需要大量储存罐放置前部工艺产生的过滤液,不但造成了大量设备的投入,而且过滤液随着放置时间的增加,液体本身的微生物大量繁殖,不利于发酵生产;而连续发酵减少了过滤液的存储时间,配置更加合理。
5、定向接种好氧发酵可以直接生成合格产品,无废弃物全部是产品;生产过程中无可燃气体,安全性高;并且发酵过程产生的少量气体(非可燃)集中收集处理,安全环保。
附图说明
以下附图仅旨在于对本发明做示意性说明和解释,并不限定本发明的范围。其中:
图1是本发明实施例的系统结构原理图;
图2是本发明实施例的工艺方法流程图;
图中:1-配料罐;2-种子罐;3-uht杀菌机;4-混合器;5-发酵罐;6-空气分布器;7-夹层水套;8-cpi清洗装置。
具体实施方式
下面结合附图和实施例,进一步阐述本发明。在下面的详细描述中,只通过说明的方式描述了本发明的某些示范性实施例。毋庸置疑,本领域的普通技术人员可以认识到,在不偏离本发明的精神和范围的情况下,可以用各种不同的方式对所描述的实施例进行修正。因此,附图和描述在本质上是说明性的,而不是用于限制权利要求的保护范围。
参见图1,利用餐厨垃圾离心液连续发酵制备肥料的系统,包括至少一个配料罐1,所述配料罐1的出料端连接有一个种子罐2,所述配料罐1的出料端还连接有uht杀菌机3,所述uht杀菌机3的出料端连接有混合器4且与所述混合器4的进料端连接,所述种子罐2的出料端连接至所述混合器4的进料端,所述混合器4的出料端连接有至少两个发酵罐5,各发酵罐5的进料端均连接至所述混合器4的出料端,且各发酵罐5的出料端均连接至所述混合器4的进料端,每个所述发酵罐5内底部分别设置有空气分布器6,各个空气分布器6通过管路连接至罐外,灭菌空气通过管路进入各个发酵罐5内,然后通过空气分布器6排入发酵罐5内实现有氧发酵;各发酵罐5的外壁上分别设置有夹层水套7,用于为所述发酵罐5提供保温。本系统还包括cpi清洗装置8,通过管路与各个罐体连通,用于对罐体以及管路清洗,cpi清洗装置8为本领域普通工程技术人员所公知的,在此不再赘述。
在本实施例中,设置有两个配料罐1,所述配料罐1为10t发酵罐,所述配料罐1用于制备工业培养基;所述种子罐2为1t发酵罐,所述种子罐2用于菌种培养,所述种子罐2外也设置有夹层水套,用于为种子罐升温、降温、保温;所述uht杀菌机3用于灭菌;所述混合器4用于将物料按照比例混合并排出;在本实施例中,所述发酵罐5设置有两个,所述发酵罐5为10t发酵罐,分别为1#发酵罐和2#发酵罐。所述混合器4为管道混合器,为本领域普通工程技术人员所公知的,在此不再赘述。所述空气分布器也为本领域普通工程技术人员所公知的,在此不再赘述。
参见图2,利用餐厨垃圾离心液连续发酵制备肥料的方法,包括以下步骤:
a)菌悬液的制备:
a1)菌种活化(以枯草芽孢杆菌为例):将从冰箱保存的甘油管放置在灭菌的超净工作台上,让其恢复至室温,用灭菌的移液枪取1ml的菌液加入到100ml无菌的营业肉汤培养基中(通过gb/t7489.6中方法配置),恒温振荡培养箱,在培养温度为35℃-37℃的条件下,培养时间为24h,完成后镜检(血球计数板);
a2)菌种扩繁:将100ml培养完成的培养基再次倒入灭菌的1000ml无菌的营养肉汤培养基中(通过gb/t7489.6中方法配置),恒温振荡培养箱,在培养温度为35℃-37℃的条件下,培养时间为24h,完成后镜检(血球计数板);
a3)菌悬液制备:重复步骤a1)、步骤a2)再次扩繁,制备10kg菌悬液。
b)工业培养基的制备:
工业培养基的原料配比如下:葡萄糖粉50份,酵母浸粉1份,牛肉膏1份,蛋白胨1份,磷酸二氢钾20份,氢氧化钾5份,离心液900-950份;将所需原料按照以上配比在所述配料罐1中调配完成,制备微生物生产的工业培养基。在整个系统发酵过程中,按照该配比不对配制工业培养基。
c)菌种培养:
在所述种子罐2中加入步骤b)中制备好的工业培养基,在95℃以上的条件下保温2h,然后降温至35℃-45℃,无菌操作向其内加入步骤a)中获得的10kg菌悬液,在保温35℃-40℃的条件下,培养时间24h,完成后镜检(血球计数板),制成1t增量用菌悬液。
d)发酵液增量:
d1)发酵启动,所述配料罐1内制备好的工业培养基经过所述uth杀菌机调整流速为1000kg/h,在所述混合器4中与所述种子罐2的1t增量用菌悬液流速1000kg/h按照1:1比例混合进入1#发酵罐中发酵,向发酵罐5的夹层水套7中通入40℃的循环水对发酵罐5进行保温,并且通过管路由空气分布器6向发酵罐5通入灭菌空气,通入量为500l/h,培养时间8h,完成后镜检(血球计数板),得到2t菌悬液发酵产物;
d2)将1#发酵罐中的2t菌悬液发酵产物作为新的增量用菌悬液,所述配料罐1内制备好的工业培养基经过所述uth杀菌机,在所述混合器4中与所述1#发酵罐中2t菌悬液发酵物按照1:1比例混合进入2#发酵罐中发酵,向发酵罐5的夹层水套7中通入40℃的循环水对发酵罐5进行保温,并且通过管路由空气分布器6向发酵罐5通入灭菌空气,通入量为500l/h,培养时间8h,完成后镜检(血球计数板),得到4t菌悬液发酵产物;
d3)重复步骤d2),将2#发酵罐中的4t菌悬液发酵产物作为新的增量用菌悬液,所述配料罐1内制备好的工业培养基经过所述uth杀菌机,在所述混合器4中与所述2#发酵罐中4t菌悬液发酵物按照1:1比例混合进入1#发酵罐中发酵,重复上述步骤,制成8t成品发酵液。
e)连续发酵:
e1)正常生产,将步骤d)中获得的8t成品发酵液分成两部分,一部分成品发酵液进入后储罐内;
e2)将步骤e1)中的剩余另一部分成品发酵液作为连续发酵用菌悬液,继续与所述配料罐1内制备好的工业培养基按照1:1比例混合进行发酵,发向发酵罐5的夹层水套7中通入40℃的循环水对发酵罐5进行保温,并且通过管路由空气分布器6向发酵罐5通入灭菌空气,通入量为500l/h,培养时间8h,完成后镜检(血球计数板),制成新的成品发酵液;
e3)将e2)中获得的新的成品发酵液继续分成两部分,按照步骤e1)、步骤e2)循环重复上述过程,循环使用发酵完成的成品发酵液与步骤b)中制备好的工业培养基混合发酵。
f)产品后储熟化:进入后储罐内的成品发酵液进行后储熟化,形成成品。
g)一个月进行一次cpi清洗,保证发酵过程正常进行。
在本实施例中设置有两个发酵罐5,当然可以为3个、4个或更多,当发酵罐5数量更多时,其连续发酵效果越高,当然发酵罐5数量更多成本较高,因此发酵罐5的数量选择根据实际需要进行选择,属于本领域普通工程技术人员所公知的,在此不再赘述;当发酵罐5设置为4个时,参见图1,分别为1#发酵罐、2#发酵罐、3#发酵罐、4#发酵罐,每个发酵罐5均为10t容量,当1#发酵罐内有5t成品发酵液时,通过所述混合器4进行1:1混合进入2#发酵罐内,经过8h发酵后形成10t成品发酵液,其中5t成品发酵液进入后储罐内,剩余5t成品发酵液;当1#发酵罐进入2#发酵罐内时,1#发酵罐内空置,可以用于接收3#发酵罐的发酵液,而当3#发酵罐空置时可以用于接收4#发酵罐内的发酵液,因此一个8h发酵周期内会同时会有3个发酵罐作业,仅有一个发酵罐空置,发酵效率得到大大提高,发酵时间有效缩短。
相对于传统发酵的优势:
1、本发明可以有效提高发酵效率,缩短发酵时间;现有技术中主要采用分级发酵,发酵时间为24t,发酵罐按照10%接种量,每个10t发酵罐每天会生产成品9t,4个10t发酵罐每天最多生产成品36t;而本发明连续发酵法发酵时间为8h,4个10t发酵罐在一个8h发酵周期内可以生产成品15t,如果发酵24h,每天可以生产成品45t,因此,与传统发酵方法相比,且生产效率提高250份。
2、本发明的设备成本降低,与传统分级发酵相比,可以至少减少3个0.1t的发酵罐、3个1t的发酵罐,成本增加1t/h的uht灭菌机和普通的管道混合器,设备成本综合降低120份。
3、本发明提高成品的合格率,传统的发酵过程一般是按照10%的接种量进行混合培养,接种量低了容易造成微生物培养物的杂菌感染(优势种群占的比例),而连续发酵法的接种量在50%,不但提高发酵效率,而且通过比较高的优势种群占比,减少有害杂菌的生长和繁殖,提高成品的合格率。
4、与前部工艺的配套性更合理,前部的生产也是连续式的生产,传统的工艺需要大量储存罐放置前部工艺产生的过滤液,不但造成了大量设备的投入,而且过滤液随着放置时间的增加,液体本身的微生物大量繁殖,不利于发酵生产;而连续发酵减少了过滤液的存储时间,配置更加合理。
5、定向接种好氧发酵可以直接生成合格产品,无废弃物全部是产品;生产过程中无可燃气体,安全性高;并且发酵过程产生的少量气体(非可燃)集中收集处理,安全环保。
以上显示和描述了本发明的基本原理、主要特征及本发明的优点。本行业的技术人员应该了解,本发明不受上述实施例的限制,上述实施例和说明书中描述的只是说明本发明的原理,在不脱离本发明精神和范围的前提下,本发明还会有各种变化和改进,这些变化和改进都落入要求保护的本发明范围内。本发明要求保护范围由所附的权利要求书及其等效物界定。
起点商标作为专业知识产权交易平台,可以帮助大家解决很多问题,如果大家想要了解更多知产交易信息请点击 【在线咨询】或添加微信 【19522093243】与客服一对一沟通,为大家解决相关问题。
此文章来源于网络,如有侵权,请联系删除


