石墨载盘及具有其的MOCVD反应装置的制作方法



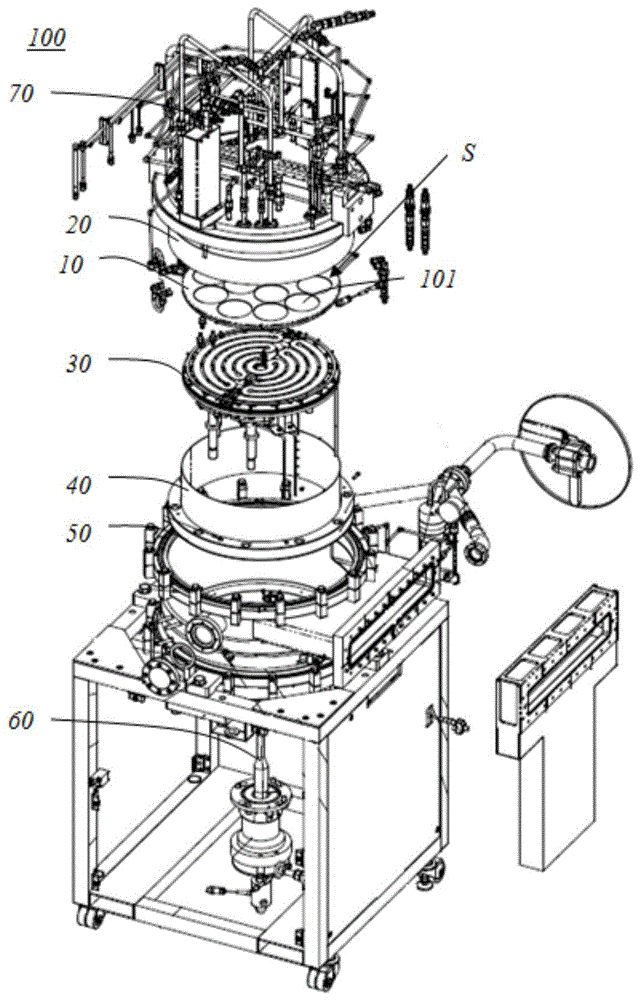
本发明涉及气相沉积领域,尤其涉及一种石墨载盘及具有其的mocvd反应装置。
背景技术:
mocvd(metal-organicchemicalvapordeposition,金属有机化合物化学气相沉积)是在气相外延生长(vapourphaseepitaxy,vpe)的基础上发展起来的一种新型气相外延生长技术。mocvd是制备化合物半导体外延材料的核心设备,以ⅲ族、ⅱ族元素的有机化合物和v、ⅵ族元素的氢化物等作为晶体生长源材料,以热分解反应方式在衬底上进行气相外延,主要用于生长各种ⅲ-v族、ⅱ-ⅵ族化合物半导体以及它们的多元固溶体的薄层单晶材料,涵盖了所有常见半导体,有着非常广阔的市场前景。
现有技术的mocvd反应装置一般包括:相对设置的喷淋头和石墨载盘,喷淋头用于提供反应气体,石墨盘内具有多个凹槽,每个凹槽内对应放置一片衬底,在石墨载盘的下方还有加热装置,以对石墨载盘进行加热,石墨载盘受热升温,能够以热辐射和热传导方式对衬底进行加热,在进行mocvd工艺时,反应气体自喷淋头的小孔进入石墨载盘上方的反应区域,衬底由于加热装置的热传导加热而具有一定的温度,该温度使得反应气体之间进行化学反应,从而在衬底表面沉积外延材料层。
现有的石墨载盘因为凹槽摆放位置的关系,产能及性能都存在缺陷,在目前led外延厂追求产能、提高性能的要求下,迫切需要一种新型石墨载盘,能够具有更高的单产及更好的性能。
技术实现要素:
本发明的目的在于提供一种石墨载盘及具有其的mocvd反应装置,其可以大大提高产能及芯片性能。
为实现上述发明目的之一,本发明一实施方式提供一种石墨载盘,所述石墨载盘呈圆形,且由所述石墨载盘中心朝向边缘的方向上,所述石墨载盘包括里圈区域、中圈区域及外圈区域,所述石墨载盘上设有若干用于承载4英寸衬底的凹槽,所述凹槽包括位于里圈区域的里圈凹槽、位于中圈区域的中圈凹槽及位于外圈区域的外圈凹槽,所述里圈区域设有6个里圈凹槽。
作为本发明一实施方式的进一步改进,所述石墨载盘还包括位于所述凹槽内的若干支撑件,于所述石墨载盘的厚度方向上,若干支撑件等高。
作为本发明一实施方式的进一步改进,所述中圈区域设有12个中圈凹槽,所述外圈区域设有18个外圈凹槽。
作为本发明一实施方式的进一步改进,所述凹槽为圆形凹槽。
作为本发明一实施方式的进一步改进,若干里圈凹槽的中心连成里圈中心线,若干中圈凹槽的中心线连成中圈中心线,所述中圈中心线与所述里圈中心线之间形成中间区域,所述中间区域包括对应若干里圈凹槽的第一区域、对应若干中圈凹槽的第二区域及对应剩余部分的交接区域,所述衬底用于成型外延片,对应所述里圈凹槽的外延片的工作电压为第一电压,对应所述中圈凹槽的外延片的工作电压为第二电压,所述第一电压与所述第二电压之间具有电压差,所述交接区域的面积与所述电压差之间为正相关。
作为本发明一实施方式的进一步改进,所述交接区域的面积不大于30000mm2。
作为本发明一实施方式的进一步改进,所述石墨大盘具有中心点,任意两个外圈凹槽之间具有外圈交接区,所述中心点至所述外圈交接区之间形成基准线,所述中心点与所述里圈凹槽的中心之间的第一连线与所述基准线之间的最小夹角为10°,所述中心点与所述中圈凹槽的中心之间的第二连线与所述基准线之间的最小夹角为5°,所述中心点与所述外圈凹槽的中心之间的第三连线与所述基准线之间的最小夹角为10°。
作为本发明一实施方式的进一步改进,任一里圈凹槽的中心与相邻的两个中圈凹槽的中心之间的连线呈正三角形。
作为本发明一实施方式的进一步改进,任一里圈凹槽与相邻的里圈凹槽或中圈凹槽均接触。
为实现上述发明目的之一,本发明一实施方式提供一种mocvd反应装置,包括如上中任意一项技术方案所述的石墨载盘、位于所述石墨载盘下方的加热装置、反应腔及源供给系统,所述石墨载盘位于所述反应腔内,所述源供给系统用于为反应腔提供反应气体。
与现有技术相比,本发明的有益效果在于:本发明一实施方式通过调整里圈凹槽的位置,使得里圈区域可以放置6个里圈凹槽,实现了4英寸外延生产的最大载片数,同时,可以有效改善现有石墨载盘技术在外延片生长过程中产生的圈位电压差异。
附图说明
图1是本发明一实施方式的mocvd反应装置示意图;
图2是本发明一实施方式的石墨载盘示意图;
图3是本发明一实施方式的石墨载盘另一示意图;
图4是本发明一实施方式的单个里圈凹槽对应的交界区域的面积与电压差之间的关系图。
具体实施方式
以下将结合附图所示的具体实施方式对本发明进行详细描述。但这些实施方式并不限制本发明,本领域的普通技术人员根据这些实施方式所做出的结构、方法、或功能上的变换均包含在本发明的保护范围内。
本申请的各个图示中,为了便于图示,结构或部分的某些尺寸会相对于其它结构或部分夸大,因此,仅用于图示本申请的主题的基本结构。
另外,本文使用的例如“上”、“上方”、“下”、“下方”等表示空间相对位置的术语是出于便于说明的目的来描述如附图中所示的一个单元或特征相对于另一个单元或特征的关系。空间相对位置的术语可以旨在包括设备在使用或工作中除了图中所示方位以外的不同方位。例如,如果将图中的设备翻转,则被描述为位于其他单元或特征“下方”或“之下”的单元将位于其他单元或特征“上方”。因此,示例性术语“下方”可以囊括上方和下方这两种方位。设备可以以其他方式被定向(旋转90度或其他朝向),并相应地解释本文使用的与空间相关的描述语。
结合图1,为本发明一实施方式的mocvd反应装置100的示意图。
这里的mocvd反应装置100以veecok868机型为例。
mocvd反应装置100包括石墨载盘10、挡板20、加热装置30、罩体40及集灰环50等。
在本实施方式中,石墨载盘10位于mocvd反应装置100的反应腔s内,石墨载盘10为石墨压制形成的石墨大盘,石墨载盘10上形成有承载衬底的若干凹槽101。
石墨载盘10呈圆形,石墨载盘10的中心固定于驱动轴60上以实现石墨载盘10的旋转,mocvd反应装置100还包括源供给系统70等结构,源供给系统70用于为反应腔s提供反应气体,石墨载盘10旋转可使得反应气体均匀沉积在各个衬底上。
在本实施方式中,挡板20呈中空环状,且挡板20环绕石墨载盘10设置,挡板20能够上下移动,从而能够充分的满足mocvd自动化生产的要求。
在mocvd设计中,其最重要的部分在于反应腔s内部流场及热场的设计,只有设计最合适的流场及热场才能使反应腔s内部的反应过程平稳进行,提高反应物源材料的利用率,并提高沉积薄膜的质量,在垂直式mocvd中,设置于石墨载盘10旁边的挡板20显得尤其重要,其直接影响石墨载盘10上方的流场分布,并且由于该挡板20离石墨载盘10很近,其对石墨载盘10表面的温场分布也具有一定程度的影响,挡板20可在生长过程中为反应腔s提供一个环绕型稳定的空间,气流经过反应腔s不会有气流乱串的现象发生。
加热装置30位于石墨载盘10下方,加热装置30用于为石墨载盘10加热以使得石墨载盘10保持在外延生长温度范围内,从而实现薄膜的成型,目前,普遍采用的加热方式是辐射加热,依靠加热装置30的热辐射使石墨载盘10升温。
罩体40环绕加热装置30设置。
这里,罩体40为钼罩,罩体40可以起到保护加热装置30的作用,罩体40可以避免反应产生的杂质进入加热装置30的底部,当有气流通入时,由于罩体40的阻挡作用,可以稳定气流。
集灰环50上设置有若干排气孔,生长的气流及反应后的化合物通过集灰环50中排气孔排出反应腔s,残留杂质滞留在集灰环50内。
参图2,为本发明一实施方式的石墨载盘10的示意图。
由石墨载盘10中心朝向边缘的方向上,石墨载盘10包括里圈区域10a、中圈区域10b及外圈区域10c。
石墨载盘10上设有若干用于承载4英寸衬底的凹槽101。
凹槽101为圆形凹槽101。
凹槽101包括位于里圈区域10a的里圈凹槽101a、位于中圈区域10b的中圈凹槽101b及位于外圈区域10c的外圈凹槽101c。
里圈区域10a设有6个里圈凹槽101a。
中圈区域10b设有12个中圈凹槽101b。
外圈区域10c设有18个外圈凹槽101c。
本实施方式可以提高产能,同时提高成型的芯片性能。
在本实施方式中,石墨载盘10还包括位于凹槽101内的若干支撑件,于石墨载盘10的厚度方向上,若干支撑件等高,也就是说,当衬底设置于凹槽101中时,若干衬底等高。
在本实施方式中,若干内圈凹槽101a邻接设置,若干中圈凹槽101b邻接设置,若干外圈凹槽101c邻接设置,且对应的内圈凹槽101a、中圈凹槽101b及外圈凹槽101c邻接设置。
这里,“邻接设置”是指凹槽101之间尽可能靠近设置,仅需保证相邻的凹槽101之间不导通即可。
石墨大盘10具有中心点a,任意两个外圈凹槽101c之间具有外圈交接区,中心点a至外圈交接区之间形成基准线l。
这里,相邻的外圈凹槽101c大致呈相切形式分布,外圈交接区即为相邻两个外圈凹槽101c的交界点。
中心点a与里圈凹槽101a的中心之间的第一连线l1与基准线l之间的最小夹角α1为10°,中心点a与中圈凹槽101b的中心之间的第二连线l2与基准线l之间的最小夹角α2为5°,中心点a与外圈凹槽101c的中心之间的第三连线l3与基准线l之间的最小夹角α3为10°。
这里,由于存在多条基准线l、第一连线l1、第二连线l2及第三连线l3,“最小夹角”定义为最邻近的两根线之间的夹角。
任一里圈凹槽101a的中心与相邻的两个中圈凹槽101b的中心之间的连线呈正三角形。
任一里圈凹槽101a与相邻的里圈凹槽101a或中圈凹槽101b均接触。
也就是说,里圈101a凹槽与相邻的里圈凹槽101a或中圈凹槽101b之间均处于相切状态。
可以看到,本实施方式的若干凹槽101之间是紧密配合的,可以大大提高产能。
本实施方式通过调整里圈凹槽101a的位置,使得里圈区域10a可以放置6个里圈凹槽101a,实现了4英寸外延生产的最大载片数,即此时石墨载盘10可以同时承载36片4英寸的衬底,同时,可以有效改善现有石墨载盘技术在外延片生长过程中产生的圈位电压差异。
具体的,结合图3,若干里圈凹槽101a的中心连成里圈中心线11a,若干中圈凹槽101b的中心线连成中圈中心线11b。
中圈中心线11b与里圈中心线11a之间形成中间区域12,中间区域12包括对应若干里圈凹槽101a的第一区域12a、对应若干中圈凹槽101b的第二区域12b及对应剩余部分的交接区域12d。
这里,第一区域12a为里圈凹槽101a位于中间区域12的部分,第二区域12b为中圈凹槽101b位于中间区域12的部分,交接区域12d为中间区域12除去第一区域12a、第二区域12b之后的区域,交接区域12d即为里圈凹槽101a与中圈凹槽101b之间未设置凹槽101的区域。
里圈中心线11a围设形成的圆形面积为s1,位于里圈中心线11a围设形成的区域内部的里圈凹槽101a的面积为s2,中圈中心线11b围设形成的圆形面积为s3,位于中圈中心线11b围设形成的区域内部的中圈凹槽101b的面积为s4,每个里圈凹槽101a的面积为s5。
交接区域12d的面积定义为s,那么,此时交接区域12d的面积s=s3-s4-6*s5-s1+s2。
承载于凹槽101中的衬底后续用于成型外延片,即通过源供给系统70提供的反应气体在衬底上沉积各种薄膜层而形成外延片。
实际操作中,源供给系统70由上至下提供反应气体,石墨载盘10旋转而使得反应气体沉积在各个衬底上,此时,交接区域12d也会产生大量沉积物,大量的沉积物会影响反应腔s内部的流场,即气流的速度、方向等均会受到影响,导致沉积在各个衬底上的薄膜层质量受影响,例如薄膜层的厚度、均匀度等会偏离理想值。
而外延片最终用于形成二极管芯片,由于各个外延片的成型过程出现差异,导致同一个批次长出来的外延片呈现出不同的电性水平,进而使得芯片良率差,或者无法出货等。
具体的,由于各个外延片的成型过程出现差异,会导致外延片的工作电压也出现差异,例如,对应里圈凹槽101a的外延片的工作电压为第一电压v1,对应中圈凹槽101b的外延片的工作电压为第二电压v2,第一电压v1与第二电压v2之间具有电压差v=v1-v2,电压差v即为圈位电压差异,交接区域12d的面积s与电压差v之间为正相关。
具体的,结合图4,单个里圈凹槽101a对应的交界区域12d的面积s’,s’=s/6。
单个里圈凹槽101a对应的交界区域12d的面积s’与电压差v之间具有关系式:
y=5e-10x2-3e-06x-0.0193;
其中,x为单个里圈凹槽101a对应的交界区域12d的面积s’,y为中圈凹槽101b及里圈凹槽101a处成型的外延片的电压差v。
在本实施方式中,通过调整里圈凹槽101a的位置,里圈区域10a放置有6个里圈凹槽101a,可以使得交接区域的面积s不大于30000mm2,即此时s’不大于5000mm2,那么,此时的电压差v可以控制在0.01v以下。
也就是说,本实施方式可以有效改善现有石墨载盘技术在外延片生长过程中产生的圈位电压差异,进而提高芯片良率。
综上所述,本发明通过调整里圈凹槽101a的位置,使得里圈区域10a可以放置6个里圈凹槽101a,实现了4英寸外延生产的最大载片数,即此时石墨载盘10可以同时承载36片4英寸的衬底,同时,可以有效改善现有石墨载盘技术在外延片生长过程中产生的圈位电压差异。
应当理解,虽然本说明书按照实施方式加以描述,但并非每个实施方式仅包含一个独立的技术方案,说明书的这种叙述方式仅仅是为清楚起见,本领域技术人员应当将说明书作为一个整体,各实施方式中的技术方案也可以经适当组合,形成本领域技术人员可以理解的其他实施方式。
上文所列出的一系列的详细说明仅仅是针对本发明的可行性实施方式的具体说明,它们并非用以限制本发明的保护范围,凡未脱离本发明技艺精神所作的等效实施方式或变更均应包含在本发明的保护范围之内。
起点商标作为专业知识产权交易平台,可以帮助大家解决很多问题,如果大家想要了解更多知产交易信息请点击 【在线咨询】或添加微信 【19522093243】与客服一对一沟通,为大家解决相关问题。
此文章来源于网络,如有侵权,请联系删除


