一种表面皱褶的富氮纳米多孔碳微球及其制备方法与流程



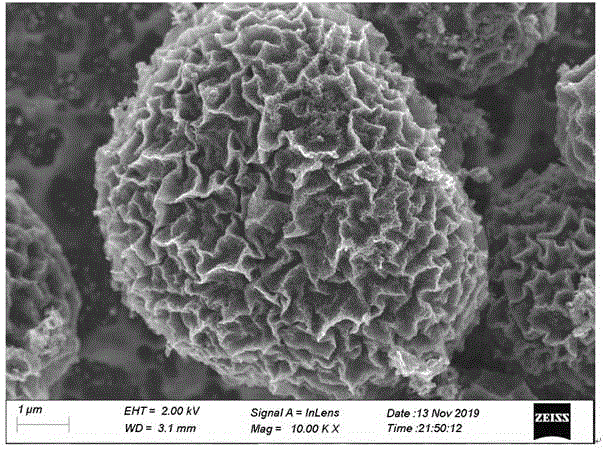
本发明属于碳材料技术领域,具体涉及一种表面皱褶的富氮纳米多孔碳微球及其制备方法。
背景技术:
多孔碳材料具有发达的孔隙、高的比表面积、高的化学稳定性、优良的耐热、耐酸碱及独特的电子传导性质,是现代工业中不可缺少的重要材料之一,广泛应用于催化剂载体、电极材料(燃料电池、锂硫电池、超级电容等)、吸附材料、储能材料和生物医药材料等方面。为了进一步改善多孔碳材料的性能,通常将杂原子(如n、b、s等)掺杂到多孔碳材料中,使得多孔碳材料的性能得到改进和提高。在众多的掺杂组分当中,氮是最受研究者们青睐的一种元素。氮原子上带有孤对电子,掺入多孔碳材料后会增加碳材料的电荷密度,增强碳材料的导电性。氮掺杂还可以改善碳材料的亲水性,提高其生物相容性。总之,氮掺杂的多孔碳材料比纯多孔碳材料具有更多优异的性质。
目前在多孔碳材料中引入氮的方法主要可以分为三种。第一种方法是由含氮前体,如三聚氰胺,聚吡咯,聚苯胺或其他含氮物质直接高温处理制得。这种方法制备的含氮碳材料通常孔隙少,比表面积低,氮含量有限。第二种方法是用含氮化合物如nh3,hcn,尿素或hno3对多孔碳在气相或液相中进行后处理。这种方法能够有效调控氮的形态和含量。但是这种方法往往需要先制备多孔炭,制备路线较长,工艺较复杂。第三种方法是热解含氮的树脂微球制备氮掺杂多孔碳微球的方法。这种方法所得碳微球中的孔以微孔为主,缺少介孔和大孔。
本发明提供了一种通过先制备包裹硬模板剂的蜜胺甲醛树脂微球,碳化后再移除硬模板剂的方式得到表面皱褶的富氮纳米多孔碳微球的方法。该方法将传统热解制备富氮碳微球的方法和硬模板制备纳米多孔碳的方法结合起来,加上独特的水相体系配方和条件控制,制备出了表面皱褶的富氮纳米多孔碳微球。
技术实现要素:
为解决现有技术的不足,本发明的目的在于提供制备表面皱褶的富氮纳米多孔碳微球的方法,包括以下步骤:
s1、将硬模板剂、三聚氰胺和甲醛加到水中得到分散均匀的混合基液;
s2、在不断搅拌下通过调节温度和ph值使步骤s1制得的混合基液中的三聚氰胺和甲醛发生聚合反应,得到包裹硬模板剂的蜜胺甲醛树脂微球沉淀物;
s3、将步骤s2制得的包裹硬模板剂的蜜胺甲醛树脂微球沉淀物分离后进行干燥处理;
s4、将步骤s3制得的干燥后的包裹硬模板剂的蜜胺甲醛树脂微球在惰性气体保护下进行高温碳化处理;
s5、用化学反应的方式脱除步骤s4制得的包裹硬模板剂的碳微球中的模板后,用去离子水洗至中性后干燥得到表面皱褶的富氮纳米多孔碳微球。
优选地,所述步骤s1中的硬模板剂选自无机纳米颗粒,颗粒粒径为1~1000nm。;
优选地,所述步骤s1中的混合基液中三聚氰胺和甲醛的质量比为0.1-10,更优选地,三聚氰胺和甲醛的质量比为1.4;
优选地,所述步骤s1中的混合基液中水占混合基液的质量分数为70%~90%;
优选地,所述步骤s1中的混合基液中硬模板剂占混合基液的质量分数为0.1%~20%;
优选地,所述步骤s2中,调节ph至1-7,温度升高到60-90℃。
优选地,所述步骤s3中干燥温度为20-200℃,时间为0.1h-100h。
优选地,所述步骤s4中的碳化在500℃~1500℃下进行,且碳化过程在保护气氛中进行,所述保护气氛为氮气、氦气、氩气或它们的混合气体的气氛。
优选地,所述步骤s5中脱除模板的方法为通过化学反应将模板转化为可溶性物质。
本发明的优点如下:
本发明将传统热解制备富氮碳微球的方法和硬模板制备纳米多孔碳的方法结合起来,加上独特的水相体系配方和条件控制,制备出了表面皱褶的富氮纳米多孔碳微球。相较于传统的热解含氮树脂微球制备氮掺杂多孔碳微球的方法,该方法所得碳微球表面皱褶,内部包含大量孔径可调的纳米孔(模板剂造的孔),应用前景更好。本发明选取的溶剂为水,原料价格低廉,具有环保和成本优势。由于该方法所得碳微球表面呈皱褶状,可以在表面负载更多的催化剂,同时也可以增强其吸附能力,因此在催化剂载体和吸附材料等方面也有广阔的应用前景。同时,该材料含氮量非常高,由于氮对多硫化物吸附能力较强,且内部有许多纳米孔可以负载更多的硫,在锂硫电池正极材料有良好的应用前景。
附图说明
图1是本发明的实施例1制备的表面皱褶的富氮纳米多孔碳微球的整体sem图;
图2是本发明的实施例1制备的表面皱褶的富氮纳米多孔碳微球的局部sem图;
图3是本发明的实施例2制备的表面皱褶的富氮纳米多孔碳微球的孔径分布图。
图4是本发明的实施例3制备的表面皱褶的富氮纳米多孔碳微球的so2吸附曲线。
具体实施方式
以下结合附图和具体实施例对本发明作具体的介绍。
实施例1:在搅拌下将1.5g二氧化硅颗粒(粒径10nm)、14g三聚氰胺和10g甲醛加入200ml水中,升温至60℃后继续搅拌3h,然后调节ph至3,继续搅拌1h后降至室温,得到大量白色沉淀。通过离心方式分离出沉淀,然后将沉淀物放在烘箱中100℃下干燥1h。干燥完成后将包裹纳米二氧化硅的蜜胺甲醛树脂在氩气气氛中1000℃碳化处理2h得到包裹纳米二氧化硅的碳微球。将干燥后的包裹纳米二氧化硅的碳微球放入1000ml的10%hf水溶液中浸泡5h除去二氧化硅颗粒,将产物离心分离出,用去离子水洗涤至中性后,干燥得到表面皱褶的富氮纳米多孔碳微球。本实施例制备的碳微球的直径为1-100µm,比表面积为537m2/g,氮含量为16wt%。
实施例2:在搅拌下将50g碳酸钙颗粒(粒径30nm)、20g三聚氰胺和10g甲醛加入250ml水中,升温至70℃后继续搅拌3h,然后调节ph至1,继续搅拌1h后降至室温,得到大量白色沉淀。通过离心方式分离出沉淀,然后将沉淀物放在烘箱中50℃下干燥3h。干燥完成后将包裹纳米碳酸钙的蜜胺甲醛树脂在氩气气氛中800℃碳化处理2h得到包裹纳米碳酸钙的碳微球。将干燥后的包裹纳米碳酸钙的碳微球放入1000ml的10%hcl水溶液中浸泡5h除去碳酸钙颗粒,将产物离心分离出,用去离子水洗涤至中性后,干燥得到表面皱褶的富氮纳米多孔碳微球。本实施例制备的碳微球的直径为1-100µm,比表面积为486m2/g,氮含量为20wt%。
实施例3:在搅拌下将10g二氧化硅颗粒(粒径50nm)、14g三聚氰胺和10g甲醛加入150ml水中,升温至80℃后继续搅拌3h,然后调节ph至4,继续搅拌1h后降至室温,得到大量白色沉淀。通过离心方式分离出沉淀,然后将沉淀物放在烘箱中200℃下干燥0.5h。干燥完成后将包裹纳米二氧化硅的蜜胺甲醛树脂在氮气气氛中600℃碳化处理2h得到包裹纳米二氧化硅的碳微球。将干燥后的包裹纳米二氧化硅的碳微球放入1000ml的20%naoh水溶液中90℃下浸泡24h除去二氧化硅颗粒,将产物离心分离出,用去离子水洗涤至中性后,干燥得到表面皱褶的富氮纳米多孔碳微球。本实施例制备的碳微球的直径为1-100µm,比表面积为432m2/g,氮含量为29wt%。
实施例4:在搅拌下将20g氧化锌颗粒(粒径200nm)、14g三聚氰胺和10g甲醛加入300ml水中,升温至90℃后继续搅拌3h,然后调节ph至7,继续搅拌1h后降至室温,得到大量白色沉淀。通过离心方式分离出沉淀,然后将沉淀物放在烘箱中30℃下干燥100h。干燥完成后将包裹纳米硫化锌的蜜胺甲醛树脂在氮气气氛中500℃碳化处理2h得到包裹纳米硫化锌的碳微球。将干燥后的包裹纳米硫化锌的碳微球放入1000ml的20%h2so4水溶液中浸泡5h除去硫化锌颗粒,将产物离心分离出,用去离子水洗涤至中性后,干燥得到表面皱褶的富氮纳米多孔碳微球。本实施例制备的碳微球的直径为1-100µm,比表面积为236m2/g,氮含量为30wt%。
产品表征和性能检测
由图1的sem图可见:实施例1制备的表面皱褶的富氮纳米多孔碳微球呈球形,直径在1-100微米,分散性好,表面呈皱褶状。
由图2的sem图可见:实施例1制备的表面皱褶的富氮纳米多孔碳微球包含了大量10纳米左右的米孔,该孔是由硬模板剂造成的。
由图3的孔径分布图可见:实施例2制备的表面皱褶的富氮纳米多孔碳微球的孔径主要分布在30nm(模板尺寸)左右。
由图4的so2吸附曲线图可见:实施例3制备的表面皱褶的富氮纳米多孔碳微球对so2吸附量高达81.2mg/g。
在本说明书的描述中,参考术语“一个实施例”、“一些实施例”、“示例”、“具体示例”、或“一些示例”等的描述意指结合该实施例或示例描述的具体特征、结构、材料或者特点包含于本发明的至少一个实施例或示例中。在本说明书中,对上述术语的示意性表述不一定指的是相同的实施例或示例。而且,描述的具体特征、结构、材料或者特点可以在任何的一个或多个实施例或示例中以合适的方式结合。
以上显示和描述了本发明的基本原理、主要特征和优点。本行业的技术人员应该了解,上述实施例不以任何形式限制本发明,凡采用等同替换或等效变换的方式所获得的技术方案,均落在本发明的保护范围内。
起点商标作为专业知识产权交易平台,可以帮助大家解决很多问题,如果大家想要了解更多知产交易信息请点击 【在线咨询】或添加微信 【19522093243】与客服一对一沟通,为大家解决相关问题。
此文章来源于网络,如有侵权,请联系删除


